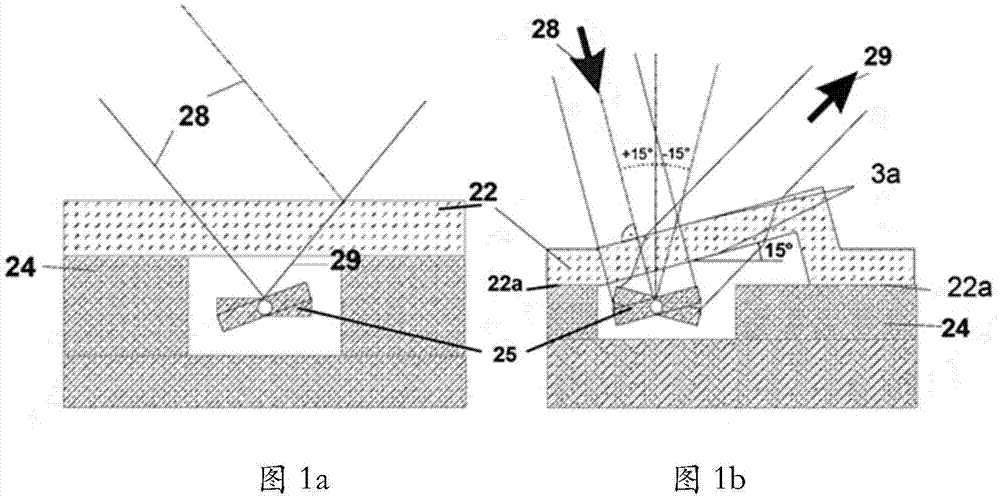
本发明涉及一种用于生产光学部件、尤其用于包封微系统的盖的方法,该光学部件尤其必须实现光学功能。
用于包封通常布置在载体衬底上的微系统(例如moems、mems)的盖通常至少提供免于污染物的保护且同时不影响微系统的机械和/或光学功能。如果微系统的功能不仅仅限于在载体衬底中运动或平行于载体衬底运动,而是也提供垂直于载体衬底面的运动,则盖通常必须确保微系统有相应的运动自由度。这需要例如确保光学功能区域的高表面质量的结构化工艺。
背景技术:
如果微系统将执行光学功能或者如果将光学测量微系统的某些参数或物理变量,例如通过干涉仪或通过视频序列分析来确定偏转(auslenkung),则通常需要光学透明盖(图1a)。
wo2004/1068665描述了一种用于moems的晶片级封装方法,其提供由玻璃制成的盖。不过,在包封处理之前,分离具有moems的载体晶片。将由此得到的分开(separaten)的未包封芯片(die)放置在新衬底上,进行固定、保持接触并紧接着进行包封。可以使用已知的压印和蚀刻方法和/或通过使用例如硅制成的隔垫(abstandshaltern)形成盖中的凹陷(vertiefungen)。
在us6146917中,描述了一种用于mems/moems的晶片级封装方法,其中,由硅或玻璃制成的设有凹陷的盖晶片通过熔接或阳极键合连接到载体晶片,由此得到气密密封的壳体。可以通过使用koh溶液的湿法化学蚀刻在由硅制成的盖晶片中形成所需的50-150μm深的凹陷。
在us2005/0184304中,提出一种用于包封经过表面微机械加工的微镜阵列的晶片级封装方法。由玻璃制成的盖晶片具有用作光学窗口的凹陷,并且所述凹陷也可以具有相应涂层(vergütungsschichten)。盖晶片中的凹陷可以具有大于100μm的深度并且通过例如蚀刻、铸造或压印的常用成形方法或通过使用隔垫来形成。
所列的所有文献具有共同特征,即盖的光学窗口呈现为平行于载体衬底、具体为载体晶片的衬底面(载体衬底面)并且由此平行于布置在其上的mems/moems。此外,在现有技术中描述了多种盖,其具有由呈现为相对于载体衬底面倾斜的光学窗口所界定的凹陷。
如在wo2007/069165和us7,948,667中所述,可以通过倾斜光学窗口实现反射消除(reflexionsausblendung)(图1b)。
根据us2007/0024549a1,也可以制造具有倾斜光学窗口的盖,其能够进行晶片级包封。盖的成形或所需凹陷的实现分别使用已知的压印和成形方法进行。
这样的成形方法的示例包括玻璃深拉和毛坯压制。具体而言,毛坯压制也用于生产光学部件,例如,透镜;(见网页http://www.aixtooling.de/index.html?content=/deutsch/aktuelles/aktuelles.html上的文章berndbresseler的″mikroproduktion-derwerkzeugbaualsmaβderdinge″和网页http://www.rpoptics.com/precision%20glass%20molding%20technical%20brief_2.pdf上的文章johndeeganrochesterprecisionoptics的″precisionglassmoldingtechnicalbrief″。
具有扁平或面平行表面的光学部件,例如镜子、或部分透射性镜子以及分束器(见文献chuanpu,zuhuazhuandyu-hwalo的″surfacemicromachinedintegratedopticpolarizationbeamsplitter″;ieeephotonicstechnologyletters,vol.10,no.7,july1998andlihy.linandevanl.goldstein的″micro-electro-mechanicalsystems(mems)forwdmoptical-crossconnectnetworks″,ieee1999)通常通过微系统技术由硅生产。例如,因此斜交镜可以通过例如使用koh的各向异性湿法化学蚀刻处理来实现(见文献jenq-yangchang、chih-mingwang、chien-chiehlee、hsi-fushihandmount-learnwu的″realizationoffree-spaceopticalpickupheadwithstackedsi-basedphaseelements″;ieeephotonicstechnologyletters)。
在文献kyounggsikyu、daesunglee、umakrishnamoorthy,namkyoopark和olavsolgaard的″micromachinedfouriertransformspectrometeronsiliconopticalbenchplatform″;sensorsandactuatorsa130-131(2006)523-530中,微光学分束器和斜交镜也通过各种蚀刻方法来生产,其中,涉及光学功能表面的高质量、具体为微小粗糙度。可以通过koh湿法化学蚀刻采用硅获得均方根表面粗糙度小于20nm的表面。但是,这样的表面仅能在具有由硅的晶体结构预先确定的特定倾斜角度的标准硅晶片中实现。
基于玻璃(例如硼硅酸盐玻璃)通过蚀刻方法生产光学元件通常导致表面的粗糙度不符合光学应用的要求(参见文献xinghuali、takashiabe、masayoshiesashi″deepreactiveionetchingofpyrexglassusingsf6plasma″,sensors和actuatorsa87,2001,pp.139-145和ciprianiliescu、kwonglucktan、francise.h.tay、jianminmiao″deepwetanddryetchingofpyrexglass:areview″)。
在de102008012384和wo2013/079131中另外描述了一种用于生产光学部件、具体为具有倾斜光学窗口的盖的方法。通过使用强化元件和通过玻璃流,充当光学窗口的区域可以以保护和稳定的方式倾斜,由此可以实现高质量倾斜或移位的光学窗口。该方法的缺点在于,玻璃衬底的结构化与相对高材料花费联系在一起,因为玻璃衬底的不同区域设置为用于力吸收、变形和光学窗口。
技术实现要素:
因此,本发明的目的是克服现有技术的缺点并且提供用于生产具有移位的和/或倾斜的区域以及高表面质量的光学部件、尤其盖的成本有利的且灵活的方法。
根据本发明,该目的通过根据权利要求1所述的用于生产光学部件、尤其盖的方法实现。从属权利要求教导有利的改进方案。
根据权利要求1所述的本发明的方法用于生产光学部件,其中,一个或多个区域或表面、尤其必须满足光学功能的表面被设置成相对于所生产的光学部件或在设置光学部件的应用中使用的部件的参照区域或参照表面倾斜和/或移位,其中参照区域或参照表面尤其也满足光学功能。尤其使,根据本发明的方法可应用在晶片级,由此可并行地生产多个光学部件。
尤其是,光学部件具有至少一个光学元件,例如光学窗口、反射镜或半透明反射镜、分束器、棱镜、透镜和/或干涉滤光器;或光学部件由至少一个光学元件构成。
光学窗口的用于使应用的辐射入射到光学窗口中和/或再次耦合出的表面是光学窗口的透射表面。
根据本发明的方法例如可用于生产具有一个或多个光学窗口的盖,盖用于包封微系统,微系统尤其具有光学功能并且通常施加或布置在载体衬底上。通常,作为载体衬底使用硅晶片,通过表面微机械或体积微机械工艺在硅晶片上生产待包封的微系统(例如mems、moems)。
根据本发明的依照权利要求1所述的用于生产一个或多个光学部件、尤其微光学部件的方法具有以下方法步骤:
–提供变形元件和载体;
–使变形元件与载体接触,由此在变形元件和载体之间形成第一接触表面,
–在变形元件上施加功能元件,使得在功能元件和变形元件之间形成第二
接触表面,第二接触表面至少部分地与第一接触表面重叠,使得通过变形
元件的形成在两个接触表面的重叠区域之间的区域形成为变形区域,
–对变形区域的至少一部分进行加热且使之变形,使得功能元件至少部分
地偏转、尤其移位和/或倾斜,
–在将功能元件施加在变形元件上的步骤中和/或在对变形区域加热和变
形的步骤中,连接功能元件与变形元件。
变形元件是用于生产光学部件的中心元件。通过使变形元件或变形区域的变形,可改变功能元件相对于其初始位置或相对于载体的取向或位置,而不使功能元件经受变形。由此例如可以获得功能元件的高光学质量。功能元件的偏转至少部分地由变形元件或变形区域的变形引起并且不是仅仅通过整个变形元件和/或载体的位置的改变而引起的。
此外,可通过变形元件的变形选择性地改变其初始形状并且实现期望的最终形状。
尤其是,变形元件是衬底,由此可并行地生产多个光学部件,或变形元件是结构元件,由此可提供具有特殊几何结构、例如呈框架形式(框架状结构)的变形元件。
大量光学部件应至少在部分区域中、通常在其整个区域上对于应用中所使用的电磁辐射是可穿透的。对于大多数光学应用,要求对于使用的电磁辐射可穿透的区域具有尽可能高的透明性,从而例如实现激光束尽可能不对微系统具有影响。
相应地,变形元件优选至少在一个区域中包含玻璃和/或类玻璃材料,或者变形元件由玻璃和/或类玻璃材料构成。类玻璃材料根据本发明理解为尽管它们的化学组成不同于硅酸盐玻璃的化学组成,但是在其热力学性质(无定形结构、玻璃转变温度)方面与玻璃类似。示例包括在化学领域中已知的玻璃或有机玻璃(organischenvitroide),如聚甲基丙烯酸甲酯(pmma)、聚碳酸酯和聚苯乙烯。
合适的玻璃的示例为硅酸盐玻璃、尤其为硼硅酸盐玻璃,因为硼硅酸盐玻璃是耐化学的且耐高温的。硼硅酸盐玻璃对急剧的温度波动的耐热性和不敏感性是其热膨胀系数低的结果。另外,尤其在肉眼可见的波长范围中透射率非常高,超过了90%。
除了一个或多个变形元件之外,还提供至少一个载体,载体尤其是也在加热和变形期间至少局部地支撑变形元件并且确保稳定的力吸收。
载体尤其是衬底、优选硅晶片、或另一平坦支撑件(例如工具或台板(einwerkzeugodereinetischplatte)),其可容纳一个或多个变形元件且由此允许优化的串行和/或并行加工,由此可提高生产工艺的效率。
载体优选在至少一个区域中包括半导体材料或载体由半导体材料、尤其硅构成。因此,可使用半导体晶片、例如硅晶片作为载体,由此可以使用半导体技术、特别是硅技术的成熟且可良好控制的工艺。
载体、尤其载体的与变形元件进行接触的一个或多个区域、尤其具有非粘性釉,非粘性釉特别包含硅酸盐和氢氧化铝,和/或载体涂覆或包含有:特别耐高温的材料,尤其是石墨、氮化铝钛、氮化硼、碳化硅;贵金属,特别是铂;和/或贵金属合金,特别是铂-铟或铂-铱合金,或者载体或区域由以上这些材料构成。由于与变形元件、尤其是与玻璃连接的可能性低以及由此引起的磨损小,这种载体可以多次使用或者在较长的时段内使用(寿命更长)。
在另一实施例中,载体具有支撑结构,支撑结构将限制功能元件的至少一个区域和/或变形元件的至少一个区域使得功能元件的至少一个区域和/或变形元件的至少一个区域可偏转和/或可变形,从而辅助或实现功能元件的倾斜。由此,可确保有针对性地或差分的力吸收以及因此使工艺、尤其在生产所需的时间方面以及在光学部件的可重复生产方面进行优化。尤其在支撑结构与功能元件接触的情况下,作用在功能元件上的力可以直接通过支撑结构或载体吸收并且由此可使变形区域的区域有针对性地解除。
在另一方法步骤中,变形元件与载体接触,由此在变形元件和载体之间形成第一接触表面。
此外,功能元件如此施加到变形元件上,使得在功能元件和变形元件之间形成至少一个第二接触表面,第二接触表面至少部分地与第一接触表面重叠,从而通过变形元件的在两个接触表面的重叠区域之间形成的区域构成至少一个变形区域。
关于这两个方法步骤的时间顺序,可以在将功能元件施加到变形元件之前或之后使变形元件与载体接触。替代地,可以同时进行处理。
功能元件是用于生产光学部件的另一基础元件,其中,功能元件由此可以是生产的光学部件的组成部分且尤其可具有光学功能。
此外,当使用成形装置(例如冲压元件)时,功能元件可以保护变形元件或变形元件的一个或多个表面区域抵抗过度的机械应力或者防止与成形装置直接接触和/或防止将外部施加的力、例如基于压差传递或分配到变形区域。
此外,功能元件可以用作成型元件,其中,功能元件的一个或多个表面区域被成型到变形元件上或变形元件的一个或多个表面区域上。因此,例如可将功能元件的表面区域的结构或特性、例如粗糙度和/或平坦性传递到变形元件。
功能元件尤其是光学元件,例如光学窗口、反射镜、半透明反射镜、分束器、棱镜、透镜和/或干涉滤光器。这种光学元件例如可在该工艺之前单独生产并然后在该工艺中集成到需要生产的光学部件中。光学元件的生产和集成之间的分离允许对这两个工艺至少部分地独立优化且实现光学部件的高质量、尤其通过保持光学元件的光学质量来实现。
为了确保光学部件的高质量、尤其表面的高质量,功能元件的表面的至少一个区域、尤其用作透射表面和/或将与变形元件接触的区域尤其具有小于或等于25nm、优选小于或等于15nm、特别优选低小于或等于5nm的均方根表面粗糙度和/或尤其具有小于或等于180nm/mm、优选小于或等于100nm/mm的每测量长度上的平坦度偏差(相对平坦度偏差)。这例如可通过对该区域抛光来实现。
优选地,功能元件是具有至少两个透射表面的光学窗口,其中,透射表面构造成平坦的(平面的)和/或彼此平行。
为了满足光学质量要求,透射表面的每毫米的相对平坦度偏差优选地小于或等于应用中使用的电磁辐射的波长的四分之一,其中,特别优选使用的波长范围为从紫外线到红外线波长范围(例如,在约200nm至约15μm之间)。为了覆盖广泛的应用范围,透射表面优选地具有小于或等于180nm/mm、特别优选地小于或等于100nm/mm的相对平坦度偏差。
此外,透射表面优选地具有小于或等于10μm/mm的每测量长度的平面平行度偏差(相对平行度偏差)。通过这种表面特性,功能元件、尤其光学窗口为光学部件(例如盖)提供了最好的先决条件,该光学部件引起较小的偏差以及光学射束路径的较小光束扩张,这实现了光学信号的较小失真。
平坦度和平面度偏差以及均方根表面粗糙度(quadratische
此外,功能元件优选应具有均匀的材料结构,以避免对辐射的不期望的折射和/或偏转。
大量光学部件应至少在一个区域中、尤其其整体上对于在应用中使用的电磁辐射是可穿透的。相应地,功能元件至少在一个区域中包含玻璃和/或类玻璃材料或功能元件由玻璃和/或类玻璃材料构成。
合适的玻璃尤其是具有或不具有碱土添加剂的硅酸盐玻璃(例如硼硅酸盐玻璃),例如eagle
在另一实施例中,功能元件至少一个区域中包括半导体材料、尤其硅,或功能元件由半导体材料、尤其硅构成,由此可以使用半导体技术、特别是硅技术的成熟且可良好控制的工艺。此外,特别是硅在合适的抗反射的情况下对于红外辐射具有超过90%的透射率。
对于功能元件特别合适的材料是具有的热膨胀系数尽可能接近变形元件的材料的热膨胀系数或与其尽可能相同。优选地,变形元件的材料的热膨胀系数与功能元件的材料的热膨胀系数之差应小于或等于5ppm/k、特别优选小于或等于1ppm/k。由此,可以降低在冷却期间由于变形元件或变形区域的材料和功能元件的材料的不同程度的收缩而产生的机械应力,且机械应力会导致变形元件和/或功能元件或光学部件损坏。
在变形元件与载体接触时和/或在功能元件施加在变形元件上时,变形元件和载体或功能元件和变形元件优选地彼此连接,特别优选地形状锁合和/或材料锁合地连接、尤其通过粘接、焊接
在优选的实施方式中,通过以下方式实现在功能元件和变形元件之间的形状锁合连接,即:功能元件布置在变形元件的用于容纳功能元件的调节凹陷(einerjustiervertiefung)中。以相同方式,可通过将变形元件布置在载体的为此形成的调节凹陷中而建立变形元件和载体之间的形状锁合连接。在这种类型的布置中,无需额外的接合物质(例如粘结剂)或特殊的接合步骤(例如键合(bonden)),该额外的接合物质和特殊的接合步骤会损坏尤其功能元件和/或变形元件的表面质量。
在另一实施例中,通过阳极键合、直接键合、熔接、等离子体激活键合和/或热键合使变形元件与载体接触和/或将功能元件施加在变形元件上。尤其在半导体工业中,这些接合方法是通常使用的连接技术,该连接技术使连接稳定。这种连接步骤尤其在真空中进行,由此例如可减少在连接区域中、特别是在变形元件和载体和/或变形元件和功能元件之间的界面处的气穴和/或被捕获的颗粒,以及特别是减少功能元件和/或变形元件的界面区域中的由此产生的缺陷。
在将功能元件施加在变形元件上时,功能元件优选地与功能衬底分开或从功能衬底脱离,且尤其之后与变形元件接触或布置在变形元件上且尤其与其连接。
功能衬底尤其实施成平板或晶片,例如硅或玻璃晶片。由此,可由一个或多个功能衬底生产多个功能元件,并且可以减少或优化加工步骤,例如用于确保功能元件的期望强度或厚度。
优选地,分离方法是钻孔、锯切、铣削、激光切割或激光加工、折断(brechen)(可能先前具有裂纹)、喷砂和/或蚀刻。
通过在将功能元件布置在变形元件上之前进行的生产工艺,用于功能元件的原材料(功能衬底)可被更有效地使用。由此且通过节省与此相关联的其他步骤、例如涂料涂覆(lackaufbringung)、曝光、涂料结构化、移除涂料可降低生产成本。
在布置在变形元件上之前生产功能元件具有以下优点,即:可为后续的布置步骤提供由不同材料(例如由多个功能衬底)制成且具有不同大小(例如厚度)或形状以及具有不同特性(例如关于透明度、反射性或吸收能力)的功能元件。这使得生产最佳地且灵活地匹配的期望规格。
此外,在布置在变形元件上之前生产功能元件的情况下,变形元件的将不与功能元件接触或连接的区域少量地暴露于侵蚀性介质、例如蚀刻溶液,从而更好地保持该区域的高表面质量并且可保持用于后续的接触和/或连接步骤。
此外,可使用更复杂的功能元件或利用特殊的生产工艺制造功能元件(例如透镜、棱镜)。
功能元件在变形元件上的布置例如可借助真空处理器(真空抽吸器)、夹具(夹头)或拾取工具(真空抽吸器和夹具的组合)进行,这确保了变形元件或功能元件的位置上精确和精准的布置。
在另一实施例中,至少一个功能元件在布置在变形元件上之前被布置在定位机构上。定位机构的放置、因此功能元件在定位机构上的传递和布置例如可借助真空处理器(真空抽吸器)、夹具(夹头)或拾取工具(真空抽吸器和夹具的组合)进行,这确保在定位机构上的位置方面的精确和精准地放置。
合适的定位机构是使功能元件的位置稳定或可调节的所有机构、装置和工具。该稳定明显方便了与其他方法步骤相关的操纵。由此例如在净化室条件下在大气压力下进行组装以及在另一净化室区域中在真空中进行后续的连接步骤,例如阳极键合。
作为定位机构,合适的是基于磁力或静电力作用的吸附衬底(
考虑到随后的连接步骤(例如,阳极键合),定位机构优选地设计成导电的。因此,定位机构尤其包含导电和/或半导电材料、例如硅,或由其构成。
作为合适的定位机构,可使用容纳衬底。这种容纳衬底具有至少一个凹口或凹陷(容纳凹陷),凹口或凹陷设计为用于容纳一个或多个功能元件且尤其侧向固定或受调节地保持功能元件。因为在这种情况下,基本上通过在容纳衬底和功能元件之间的形状锁合连接来确保调节,因此,容纳衬底可在将功能元件放置在变形元件上之后通过解除形状锁合连接而以简单方式被移除,从而为进一步的工艺步骤释放由此产生的布置。容纳衬底然后可再次用于下一个组装工艺且由此可重复使用,这继而降低了生产复杂度和生产成本。
此外或可替代地,可在变形元件上生产功能元件、例如光学窗口,使得至少一个功能层施加在变形元件上。功能层例如可借助沉积方法和/或通过使用功能衬底(例如硅晶片或玻璃衬底)来生产。在这种情况下,功能层与变形元件优选地连接、尤其材料锁合(例如借助键合、焊接、粘接或沉积),从而确保功能层和由此生产的功能元件的高位置稳定性。
适宜地,将功能层施加在变形元件上,使得降低或防止功能层相对于变形元件的移位和/或转动。
优选地,多晶硅层作为功能层尤其借助cvd、尤其热线cvd(hotwire-cvd)或pecvd或pvd、尤其溅射涂覆在变形元件上。因为在这些沉积工艺中工艺温度低于600℃、尤其在400℃和500℃之间,因此也可涂布温度敏感的变形元件。此外,功能层能以功能衬底的形式、例如硅晶片通过阳极键合和/或热键合施加在变形元件上或与其连接。尤其在半导体工业中,这些接合方法是通常使用的形成稳定连接的连接技术。
在涂覆了功能层之后,尤其通过钻孔、锯切、铣削、激光切割、折断、喷砂和/或蚀刻,来结构化功能层,以生产至少一个功能元件。
通过与功能衬底分离来生产的至少一个功能元件被布置在变形元件上或与变形元件连接,和/或通过对功能层进行结构化来生产一个或多个功能元件,使得功能元件通过尤其变形区域的随后变形而可偏转。此外,尤其通过布置或连接和/或结构化形成第二接触表面的形状并由此设定重叠区域。
前述用于将功能元件施加在变形元件上的实施例同样可应用于变形元件与载体的接触。相应地,变形元件可在接触之前生产(例如与变形衬底分离或从变形衬底中脱离),然后布置在载体上,和/或变形元件通过将变形层施加在载体上并且结构化变形层而生产。
变形元件以及功能元件的使用使得能够独立地生产这些元件并且因此能够将这些元件与尤其针对光学部件的工艺流程或者规格单独地匹配。由此,例如对于例如在加热和变形之后的加工(例如抛光步骤)不能接近或难以接近的表面、例如透射表面在生产相应的元件(例如功能元件)时实现高表面质量。
将第一层、第一区域或第一装置布置或施加在第二层、第二区域或第二装置“上”在此以及后面是指:第一层、第一区域或第一装置被直接以机械和/或电气接触布置或施加在第二层、第二区域或第二装置上。此外,也可指间接接触,即,另外的层、区域和/或装置布置在第一层、第一区域或第一装置和第二层、第二区域或第二装置之间。
在另一实施方式中,功能元件、变形元件和/或载体具有一个或多个凹陷和/或开口,凹陷和/或开口尤其借助于钻孔、锯切、铣削、激光切割、喷砂和/或蚀刻生产。根据本发明,孔也可以是开口。
在凹陷和/或开口的区域中,当使载体与变形元件接触和/或将功能元件施加在变形元件上之后,凹陷和/或开口能够在载体和变形元件之间、在功能元件和变形元件之间或在功能元件和载体之间产生距离,从而避免在该区域中的表面接触以及由此保持这些表面区域、尤其功能元件的表面质量(例如粗糙度方面)。这种接触也可尤其在加热和变形期间导致功能元件粘附在变形元件和/或载体上或变形元件粘附在载体上,并且防止或阻碍功能元件的由变形引起的偏转。
为了能够确保功能元件的由变形引起的尽可能无问题的偏转,优选功能元件的与形成重叠区域不相关的区域尤其在变形区域变形之前应该不与变形元件和/或载体直接或间接(例如通过一个或多个中间层)接触,以防止功能元件在这些区域中粘附在变形元件和/或载体上。
为了降低在接触情况下的粘附力,功能元件、变形元件和/或载体的表面或相应的表面区域可设置有不同的涂层和/或通过用于表面改型的方法(例如纳米纹理化)来制备。合适的涂层材料例如是铂、铂合金(例如铂-铱合金)、nialn、石墨和氮化硼。
此外,凹陷和/开口用于设定或影响变形区域的变形阻力。这例如可通过以下方式实现,即:凹陷和/或开口引起变形区域的表面增大或变形元件的邻近受变形影响的变形区域的区域的体积减小。
由此变形区域在凹陷和/或开口的区域中没有(变形区域具有至少部分地界定凹陷和/或开口的表面)或很小程度地与固体、尤其包括高粘性的液体、例如玻璃连接。由此,与随着在加热和变形期间在变形区域的塑性或粘性变形时发生的结构性材料移位产生的力没有或很小部分地被邻近变形区域的真空或材料(例如气体、液体、变形元件的区域)吸收。这使得可以分布有变形力的体积或表面减小以及因此降低变形阻力。
在本发明的情况下,变形阻力理解为是指反作用于变形区域的引起变形的力、即变形力(例如自身重力和/或从外部引入的力)的阻力。变形阻力由变形力与由其引起的变形速度的比例得出并且与粘度、尤其动态粘度以及与变形区域的变形力作用的表面或假想剖面面积成正比。
在另一实施例中,使载体与变形元件的接触和/或将功能元件施加在变形元件上,使得通过凹陷和/或开口在变形元件和载体之间、在变形元件和功能元件之间和/或在功能元件、变形元件和载体之间形成空腔,其中空腔尤其气密地密封。
除了确保在限定空腔的不同表面区域之间的距离以避免表面区域、尤其在加热和变形之前接触或粘附和/或为了使用光学部件的应用提供至少部分闭合的体积,可在空腔中尤其在加热和变形之前和/或期间产生低于或高于环境压力、尤其大气压力的压力。通过在空腔中的压力与环境压力之间的这种压差,可产生用于确保或有助于变形过程的力作用。
在加热和变形的步骤中环境压力或工艺压力对应于大气压力的情况下,在空腔中例如设定压力在约15mbar至约30mbar之间(负压)或在约1200mbar和约1600mbar之间(过压)。
通过使用合适的接合技术、例如键合,可尤其生产与环境气密密封的空腔。通过在特定的压力下进行该接合工艺,可在空腔中产生或设定该压力值。优选地,在连接工艺期间、例如在阳极键合期间,在温度为400℃下,压力在约10mbar至约20mbar之间或在约800mbar至约1000mbar之间。因为接下来的加热工艺通常在比接合工艺高得多的温度下进行(变形元件在加热和变形的步骤期间例如达到约700℃至约900℃之间的温度),因此在空腔中形成约15mbar至约30mbar或约1200mbar至约1600mbar的给定压力范围的压力。
因为在这种情况下空腔与环境气密地密封,因此,在没有例如为了运行真空泵或泵的其他能量引入的情况下,在较长时间上以及因此尤其为了变形或成形工艺而保持设定的压力值。
尤其是,通过在变形元件和载体之间的、其中设定有在加热期间产生相比于环境压力或工艺压力的过压或负压的压力的空腔,可实现将力作用到变形元件上,由此变形元件的至少一个区域或变形区域变形并且由此使功能元件偏转。在这种情况下,功能元件仅在变形工艺期间与变形区域或变形元件接触或连通的区域中被加载力作用。功能元件的其他区域、例如界定载体、变形元件和功能元件之间的空腔的表面区域不经受使变形区域变形的力作用,从而降低该区域的机械应力并且可特别好地保持其形状或表面质量(例如平坦度和平行性)。
通过使变形元件与载体形成接触,而在变形元件和载体之间形成第一接触表面或边界表面,并且通过将功能元件施加在变形元件上,而在功能元件和变形元件之间形成第二接触表面或边界表面,其中,第二接触表面至少部分地与第一接触表面重叠。变形元件的在两个接触表面的重叠区域之间形成的区域形成变形区域。
两个接触表面的重叠区域(以下称为重叠区域)尤其包括第一和第二接触表面的这样的区域,该区域的点与将其投影到相应的另一接触表面上的至少一个映射相关联,该映射在满足以下标准的情况下同样属于重叠区域,诸如点本身。所述点和其映射可通过相应的连接线连接,该连接线在变形元件的、或变形元件和与其接触的固体(例如包夹体)并且相应地未通过凹陷、开口或孔或空腔(例如真空、气体或液体)的整个长度延伸。点和其连接线满足上述标准的映射在下面称为点/映射对。
一个接触表面的一个点在另一接触表面上的投影尤其如此进行,即:使得在该点和其在另一接触表面上的映射之间的连接线描述了点和映射之间的最短连接或最短距离(下面称为最小投影)和/或借助正交投影将点映射到另一接触表面上。
如果针对一个点尤其需要两个投影(最小投影和正交投影)引起映射或存在更多个映射并且一个点引起多个点/映射对,则除了点以外,其点/映射对的所有映射都属于重叠区域。如果为一个点例如分配两个映射,相应存在点/映射对,即,点/映射1和点/映射2,则点以及映射1和映射2属于重叠区域。
尤其排除的是点的最小投影在另一接触表面的边缘上产生映射的点/映射对。这种点/映射对的点和映射不属于重叠区域。例如如果又存在点/映射1和点/映射2,其中,映射2是点在另一接触表面的边缘上的最小投影,则只有点和映射1(根据点/映射对,即点/映射1)属于重叠区域。
在另一实施方式中,仅包括其最小投影形成落在另一接触表面的边缘上的映射的点的接触表面与正交投影的结果无关而不属于重叠区域。
在本发明的情况下,变形区域尤其延伸到变形元件的由重叠区域定界且由点/映射对的连接线所经过的区域上,该连接线属于重叠区域。
根据现有技术的实施例,待变形的衬底具有执行不同功能的不同区域,例如:待偏转的功能区域,该区域在光学部件的应用范围中通常可满足光学功能(例如窗口);支撑区域,由载体支撑且因此允许在支撑区域和待变形的衬底的功能区域之间的相对运动;和变形区域,通过变形区域的形状变化确保功能区域的偏转。因为根据现有技术这些区域布置成侧向彼此相邻,因此待变形的衬底要求具有相应的横向尺寸。
通过将根据本发明的变形区域布置在功能元件和载体之间,可使所述区域的多个功能、尤其所有功能集中或组合在变形区域中,由此明显节省了材料以及降低了成本,因为要求变形元件具有较小横向尺寸或在变形元件的每横向尺寸上可生产多个光学部件。
在另一实施方式中,第一和/或第二接触表面或第一和/或第二接触表面的重叠区域和/或变形区域呈框架形式或框架形(例如呈圆环形式的接触表面),尤其在变形元件中围绕凹陷和/或开口或包围且优选闭合凹陷和/或开口。变形元件的这种框架形的、尤其闭合的重叠区域产生的区域还可用作连接表面,以便例如通过变形元件与一个或多个包封元件、尤其气密地闭合例如通过框架形的变形区域包围的凹陷和/或开口。由此例如可包封对运动自由度具有要求的mems或moems。
可有助于降低生产成本的另一空间或材料优化方案可通过以下方式实现,即:变形区域、尤其框架形的变形区域至少部分地限定变形元件中的凹陷和/或开口或尤其在变形元件和载体之间和/或在功能元件、变形元件和载体之间的空腔。这还使得变形区域具有如所述地影响变形阻力的表面。
变形区域的变形阻力的大小例如通过变形区域的所使用的材料、构型或形状和布置(例如变形区域是否邻近气体或固体)来确定。由此可通过变形区域的几何非对称性实现变形阻力的非对称性(阻力非对称性),该阻力非对称性可引起变形区域中的机械应力分布,机械应力分布引起局部不同的变形速度。由此可辅助或实现功能元件的由变形引起的倾斜。
在优选的实施方式中,框架形的变形区域的至少两个节段(框架节段)尤其在加热和变形期间具有不同大小的变形阻力,由此可辅助或实现功能元件的由变形引起的倾斜。
在另一实施方式中,形成两个或更多个变形区域,这两个或更多个变形区域与同一功能元件接触或由同一功能元件建立(begründet)并且优选围绕凹陷和/或开口径向相对地形成在变形元件中和/或至少部分地界定变形元件中的凹陷和/或开口。由此实现的空间或材料优化可有助于降低生产成本。
优选地,两个变形区域或两个变形区域中各有一个子区域(两个变形子区域)尤其在加热和变形期间具有不同大小的变形阻力,由此在加热和变形的步骤中可有助于或辅助功能元件的倾斜。
两个变形区域可为同一变形元件的区域且可通过变形元件的未用作变形区域的至少一个区域分开,或两个变形区域可分配给不同的变形元件。
将多个变形区域与一个功能元件结合使用、尤其多个变形元件的使用使得该方法变得灵活,因为变形区域或变形元件可单独构造。由此,通过例如使用不同材料和/或通过两个变形区域在几何结构上不同地构造,两个变形区域可具有不同大小的变形阻力,以便有助于或辅助功能元件在加热和变形的步骤中(在加热和变形期间)的倾斜。
在本发明的情况下,关于变形区域的结构以及几何考虑(geometrischenbetrachtungen)尤其涉及在变形元件成形之前或变形区域变形的工艺步骤之前的变形区域的形状。
通过变形区域的特殊构造,可有针对性地影响功能元件的偏转方式并且尤其有助于或辅助功能元件的倾斜。
因此,在另一实施例中,框架形的变形区域或两个变形区域形成为使得框架形变形区域的两个横截面区域的面积和/或两个变形区域的两个横截面区域的面积和/或整个横截面区域的面积大小不同,其中,横截面不是分配给两个变形区域的同一变形区域。
在下面使用的术语框架表面是指框架形的变形区域在减去变形区域的凹空(freistellung)之后的表面。这里,凹空是指假想除去所有的不属于框架形的变形区域的元件和区域。相应地,框架表面由实际表面(表面)和/或由通过减去而得到的通过从实际的边界表面(尤其在变形区域和载体或功能元件之间)和/或假想边界表面(尤其在变形区域和变形元件的与其毗邻的不属于变形区域的区域)中凹空而产生的表面组成。
框架形的变形区域的横截面尤其包括通过平缓闭合曲线界定的框架形的变形区域的所有点组,其中,曲线描述从框架表面的一个点开始在框架表面上延伸的至该点本身的最短连接(相应于曲线起始和终止于同一点),从而曲线仅包围属于框架形的变形区域但是不属于框架表面的点。因此,曲线的点是框架表面的包围在横截面区域中的唯一点。
并且/或者,框架形的变形区域的待比较的横截面尤其由框架形的变形区域的通过由框架形的变形区域的两个彼此正交的惯性主轴和/或体积主轴(在有均匀的质量分布的情况下的惯性主轴)限定的剖切平面的剖切得到,其中,仅考虑导致剖切两个接触表面的两个横截面区域的横截面。
两个变形区域的待比较的横截面尤其由这样的剖切平面通过两个变形区域的剖切得到,其中两个变形区域的两个体积重心位于该剖切平面上并且构造成使得两个接触表面被剖切并且两个横截面的面积总和最小。如果变形区域的剖切造成多个剖切表面,则其面积量相加,从而获得得到的可用于比较的横截面区域的面积。
总横截面区域是两个变形区域的横截面预期的总和,其中,横截面区域由通过先前(上面)限定的剖切平面对两个变形区域的剖切或由通过剖切平面朝其法向矢量的方向的平行移位产生的映射形成。
通过使剖切平面或横截面区域所在的平面沿由该平面的法向矢量给定的方向移动相同长度的无穷小距离,尤其限定无穷小的体积元件,以及因此限定框架形的变形区域的一个节段(框架节段)或变形区域的子区域(变形子区域),其中,在比较两个体积元件时,两个体积元件跨越相同长度的无穷小距离。
在另一实施方式中,变形区域具有一个表面,其中尤其框架形的变形区域的两个节段和/或两个变形区域和/或两个变形子区域具有面积大小不同的表面。变形区域的表面可通过对变形元件的结构化、尤其通过锯切和/或蚀刻生产或增大。由此影响或设定、尤其减小变形阻力。由此框架形的变形区域的两个节段和/或两个变形区域和/或两个变形子区域的表面的面积大小差异可通过锯切到变形元件中的不同深度实现。
根据另一实施方式,在同一工艺步骤中、尤其一个锯切步骤中对功能元件进行结构化且对变形元件进行结构化、尤其用于增大变形区域的表面。由此可节省工艺步骤且简化工艺。
在本发明的另一实施例中,第一和/或第二接触表面的界定或毗邻框架形的变形区域的两个节段和/或两个变形区域和/或两个变形子区域的相应区域的面积大小不同,由此可引起局部不同的变形阻力,以便实现或有助于功能元件的倾斜。
在另一实施例中,第一和/或第二框架形接触表面、尤其第一和/或第二接触表面的重叠的框架形区域的外边缘限定第一几何图形且内部边缘限定第二几何图形,其中,第一和第二几何图形彼此独立地分别从以下组中选出,所述组包括矩形、梯形、尤其等腰或直角梯形、圆形和三角形。
通过组合外边缘和内边缘的相应几何结构,可形成形状不同的接触表面或接触表面的重叠区域以及形状不同的变形区域,由此可设定局部不同的变形阻力。
由此,在示例性的实施例中,第一和/或第二接触表面的重叠的框架形区域的外边缘和内边缘分别通过矩形描述,矩形的周向中心不重叠,其中尤其描述内边缘的矩形的对称轴线和描述外边缘的矩形的对称轴线位于同一直线上。由此,相应框架形的重叠区域的两个相对支腿(schenkel)具有相同的面积且另两个相对支腿具有不同的面积,由此,变形区域或变形区域的变形阻力可设置成非对称的。
在另一实施例中,变形元件的一个区域设有稳定层,稳定层尤其局部地抵消变形元件或变形区域的变形。
尤其是,稳定层毗邻变形区域或遮盖变形区域的至少一部分表面。优选地,稳定层可毗邻框架形的变形区域的两个节段中的一个和/或两个变形区域或变形子区域中的一个和/或遮盖框架形的变形区域的两个节段中的一个的表面和/或两个变形区域或变形部分区域中的一个的表面。
由此,可增强或稳定变形元件或变形区域的多个区域,以便抵消这些区域的变形。结合变形元件的未设置稳定层的区域,由此可有助于或辅助功能元件的倾斜。
在加热和变形的步骤中对变形元件成形时或在变形区域的变形时,尤其利用例如变形区域或变形区域的材料的流动性能,例如该流动性能尤其在软化温度(softeningpoint)或固相线温度附近以及之上。这种成形、尤其也称为玻璃流动相对于其他成形或压制方法、例如玻璃深拉或玻璃压印(例如毛胚压制(beispielblankpressen))的优点尤其在于,尤其可实现这样的光学部件,其具有的衬底或晶片尺寸、尤其衬底或晶片直径大于或等于80mm、优选大于或等于150mm、特别优选大于或等于300mm;衬底侧的表面具有高表面质量、尤其较低表面粗糙度、较高表面平坦度和较高平行性。
尤其在由玻璃制成初始衬底时,通常例如借助玻璃深拉或玻璃压印生产的光学部件的表面粗糙度不令人满意。借助玻璃拉伸成形的衬底被粗糙化且例如不能满足对光学窗口的要求。
在毛胚压制的情况下,可生产的光学部件的最大尺寸(ausdehnungen)或大小明显受限。此外,该压制过程要求非常高质量的、耐受的以及昂贵的压制工具,这限制了灵活的生产。
在加热和变形的方法步骤中,变形区域中的至少一部分如此被加热和变形,即:使得功能元件至少部分地或局部地偏转,尤其移位、倾斜和/或转动(扭转)。
如果区域中的变形元件或变形区域、尤其第一和/或第二接触表面的区域中的变形区域被加热,则可通过与变形元件的接触而在变形元件的表面上成形例如具有较小的粗糙度和平坦偏差性的功能元件和/或载体的高质量表面区域。这具有的优点是,对在相应区域中的所提供的变形元件的表面质量的要求可更低且可消除可能必须的加工步骤,例如抛光。
为了实现这种塑铸(abformung)或尤其为了获得功能元件的形状及其表面特性,尤其功能元件和/或载体的材料的上冷却温度或固相线温度大于变形元件或变形区域的材料的上冷却温度或固相线温度,其中,在功能元件和/或载体的材料的相应的上冷却温度或固相线温度和变形元件或变形区域的材料的相应的上冷却温度或固相线温度之间的温度差应尽可能大、尤其大于等于100k。
如果功能元件和/或载体例如由硅构成且变形区域由硼硅酸盐玻璃构成,则为了形成差异,硅的固相线温度或熔化温度以及硼硅酸盐玻璃的上冷却温度是决定性的。
在有利的实施方式中,变形元件或变形区域的材料的软化温度或液相线温度在功能元件和/或载体的材料的软化温度或液相线温度之下、尤其在上冷却温度或固相线温度之下。由此可在保持功能元件和/或载体的形状的情况下实现有效的变形过程。
相应地,在加热和变形的步骤中,将变形区域、尤其整个变形区域或变形元件优选达到高于变形区域或变形元件的材料的上冷却温度或固相线温度之上以及功能元件和/或载体的材料的上冷却温度或固相线温度之下的温度。
材料或物质的固相线温度和液相线温度之间的温度区间称为熔融区间或熔融范围。例如,共晶合金和纯金属结合固相线温度和液相线温度。在这种情况下,固相线温度和液相线温度具有相同的称为熔点的值。
尤其变形区域的至少一部分、尤其整个变形区域或变形元件在加热和变形的步骤中达到变形区域或变形元件的材料的在软化温度-150℃和软化温度 100℃之间的温度。
尤其对于变形区域或变形元件使用玻璃或类玻璃材料,上冷却温度和软化温度是评估变形工艺的适用性的重要性质。
在上冷却温度之下,例如玻璃的粘度以及因此其变形阻力通常对于实施实际的变形工艺来说过高。在上冷却温度之上,粘度降低且变形性质改进。在软化温度的范围中,相应的材料具有特别有利的变形特性、尤其是在粘度方面。
在使用软化温度约为820℃的硼硅酸盐玻璃时,在加热和成形的步骤中例如在约700℃和约900℃之间的温度是适宜的。
对于每种玻璃来说,可设定通过上冷却温度和下冷却温度限定的冷却范围。该温度范围根据粘性限定,其中,上冷却温度是玻璃具有的粘度为1013或1013.3dpa·s时的温度。在下冷却温度处,粘度为1014.5dpa·s。
用于确定上冷却温度的确定方法是直接粘度确定法,该直接粘度确定法借助下面描述的利特尔顿方法作为拉丝方法使用,该方法仅寻求在1000g的丝线负荷下以0.136mm/min的速度延长的温度。此时粘度为1013或1013.3dpa·s。如果进一步冷却炉,则通过外推到0.0043mm/min的延长速度获得用于下冷却温度的值。
也称为利特尔顿温度或利特尔顿点的软化温度或软化点(softeningpoint)根据利特尔顿方法确定。对此,将直径为0.65mm至1.0mm且长度为22.9cm的材料丝(例如玻璃丝)悬挂到特定结构的炉中。在加热速度为5至10k/min时观察到从炉中悬出的丝下端。随着温度提高,丝在自重的情况下延长。延长率为1mm/min的温度称为利特尔顿温度。大部分玻璃或类玻璃材料在该温度下具有的粘度约为107.6dpa·s(scholze,horst″glas-natur,strukturundeigenschaften″,第3版,springerverlag,151页)。
优选地,在加热和变形期间保留或存留第一接触表面的重叠区域的至少一部分和第二接触表面的重叠区域的至少一部分,其中第一接触表面的重叠区域和第二接触表面的重叠区域尤其限定同一变形区域。
因此,变形元件和载体之间在重叠区域中的接触和功能元件和变形元件之间在重叠区域中的接触在加热和变形期间至少部分地未被解决,以便在加热和变形期间确保有效地将力传递到变形区域上和/或将功能元件和/或载体的一个或多个表面区域成型到变形元件上。
特别优选地,在加热和变形期间完全地或全部地保留或存留重叠区域。
加热和变形的步骤优选定时地进行或进行直至变形元件和/或功能元件接触偏转限制装置,该偏转限制装置例如限制由变形引起的期望的最大偏转。作为偏转限制装置例如可使用工具、功能元件和/或载体、尤其载体中凹陷的接合面。由此,可提高偏转的精确性或改进光学部件的可重复生产性。
在加热和变形的步骤中,变形区域的至少一部分通过力(变形力)变形,其中,该变形可超过变形区域而延伸到变形元件的不属于变形区域的区域上。尤其在毗邻变形区域的区域上,可基于与变形区域的材料耦合通过变形工艺来变形,因为在变形元件中由变形力引起的应力或速度分布可延伸超过变形区域。
变形区域的变形可优选通过功能元件和/或变形区域或变形元件的自身重力和/或通过从外部引入的力引起。
从外部引入的力或变形力可适宜地基于机械的、例如气动的和/或磁力的和/或电力的和/或压电的相互作用。
在另一实施例中,如上所述,从外部引入的力通过在功能元件的两个侧面、尤其相对的侧面之间的压差和/或通过在变形元件的两个侧面、尤其相对的侧面之间的压差引起。如即使在该力引入的方法中通过自重力变形时,变形元件和/或功能元件也不与另一物体、例如冲压工具接触,冲压工具可降低变形元件和/或功能元件的表面质量。因此,通过这种方式的力引入可保持或确保变形元件和/或功能元件的高表面质量。
此外,在这种情况下,进行加热和变形,直至通过变形区域或变形元件的变形引起的空腔体积改变导致空腔中的压力对应于环境压力。
特殊设计的成形装置也适合于引入变形力,其中,功能元件可起到保护功能,以尤其在加热和变形的步骤中避免成形装置与变形元件接触。成形装置与变形元件的接触可引起粘附,这在分离成形装置时会引起变形元件上的缺陷。
此外,功能元件可将通过成形装置局部引入的力以平面力作用分配到变形区域上。
除了变形力的作用点,例如变形区域或变形元件相对于所施加的变形力的变形阻力这样的特性对于如何使功能元件偏转是决定性的。
如已经所述地,功能元件在施加在变形元件上时可与其形成连接。此外或替代地,可行的是,功能元件在施加在变形元件上时布置在变形元件上,且在加热和变形的步骤中尤其通过热键合在功能元件和变形元件之间建立连接。
尤其是,如果在加热和变形期间在功能元件和变形元件之间产生连接,则可节省用于连接的额外的工艺步骤,该额外的工艺步骤尤其对于功能元件表现为额外的尤其热负荷且会不利地影响质量、尤其光学质量。此外,尤其可通过热键合确保功能元件的表面区域或表面结构有效地成型到变形元件上。
通过在功能元件和变形元件之间的连接,可确保元件、尤其元件的接触表面相对彼此的高位置稳定性,且由此保持以及获得和/或保持和/或产生接触表面的高表面质量。此外,通过连接可确保用于使变形区域或变形元件变形的有效的力传递。
通过功能元件与变形元件的连接、尤其粘合连接,即使在加热和变形之后也可确保元件彼此的稳定位置,从而在保持连接的情况下,可以生产可包括两个元件并由此例如可包括不同材料的光学部件,或从而可将连接的元件供应到与一个或多个成形装置无关的分离步骤、例如可选的蚀刻步骤。通过如此分开成形和分离步骤,也可在没有质量损失的情况下将具有复杂结构的变形元件与功能元件分离,该变形元件尤其具有大的形貌对比度(topografischekontraste)、例如狭窄的深凹槽结构或相对彼此成直角形成的表面。
尤其,如果至少一个功能元件不具有另外的功能,则该功能元件优选在下一方法步骤中至少部分地、优选完全地移除或与变形元件分离。
特别优选地,如此进行移除:使得功能元件可再次使用并且可多次使用,由此可以提高方法效率且可降低生产复杂性或生产成本。
这例如可通过以下方式实现,即:功能元件至少在与变形元件形成连接的区域中具有牺牲层,牺牲层在变形元件变形之后被移除以露出功能元件。可替代地,牺牲层可首先涂覆在变形元件上并且进行结构化,其中,功能元件之后在后续方法步骤中布置在牺牲层上并且因此布置在变形元件上或与牺牲层连接。一种优选的牺牲层包含硅、锗、氧化锌、钼和/或钨或由他们构成。对于这种经由牺牲层与变形元件连接的功能元件,可使用例如高熔点的或耐高温的玻璃(例如corningeagle
对于特定的应用,可有利的是,功能元件的一个部分或多个部分例如作为框架形的稳定结构或孔径结构(blendenstruktur)保留在变形元件上或成品光学部件上。
载体变形之后也优选被完全移除。但是在若干情况下,在载体上布置待包封的微系统,从而在连接元件和载体之间的连接仍然存在可能是适宜的。
在有利的实施方式中,变形元件和/或功能元件的至少一个区域设有至少一个精整涂层(veredlungsbeschichtung)、特别是设有抗反射涂层、抗静电涂层、反射涂层和/或吸收涂层和/或功能表面结构,由此可改进光学部件的功能性。
优选精整涂层是抗反射涂层,该抗反射涂层例如进一步降低了盖、尤其光学窗口上的反射性以及因此降低辐射损耗。这种抗反射涂层例如可通过由氟化镁和二氧化钛、或二氧化硅和二氧化钛构成的层系统实现。
此外,可使用使光学部件的电荷最小化的抗静电涂层。
适用于光学应用中的抗静电涂层的材料是ito(氧化铟锡),因为它在掺杂的情况下具有高导电性并且在宽波长范围内具有高透明度。
此外,可以有利的是,反射涂层、例如金属层作为精整涂层被涂布。该精整涂层可在结构化以空间上界定入射光(孔径功能(blendenfunktion))之后形成局部反射区域,例如或在光学窗口附近形成静态偏转镜。
此外优选精整涂层是吸收涂层,吸收涂层吸收特定波长或整个波长范围的电磁辐射。
在本发明的情况下,功能的表面结构是表面的在微米和/或纳米范围中的几何校正,由此可有针对性地影响特定的表性能。因此,通过优选使用结构尺寸低于应用中使用的辐射的波长的蛾眼结构(参见文献d.g.stavenga、s.foletti、g.palasantzas、k.arikawa的″lightonthemoth-eyecornealnipplearrayofbutterflies″,proceedingsoftheroyalsocietyb(2006)273,661-667,doi:10.1098/rspb.2005.3369,2005年12月6日在线公开),可以减小例如存在于玻璃表面和周围空气之间的边界层的折射率,这就是蛾眼结构适用于表面抗反射的原因。如果涂层被证明由于附着原因而不适用,则这种抗反射是特别有利的。
例如在变形元件成形之后,可借助于压印方法在变形元件的表面上产生蛾眼结构。然而,对在倾斜和/或移位的表面中的这种结构的压印是非常存在问题的。特别是在倾斜表面上,可以通过利用变形元件的流动特性来生产蛾眼结构。
因此,在优选的实施方式中,蛾眼结构作为功能表面结构产生,使得在功能元件布置在变形元件上和/或与变形元件接触之前,至少功能元件的与变形元件接触的区域设有蛾眼结构的凹模,并且在变形元件成形期间在功能元件布置在变形元件上和/或与变形元件接触之后,通过将功能元件中的凹模成形到变形元件的接触表面上、尤其透射表面(例如棱镜)上,而在变形元件的接触表面上产生蛾眼结构。在这种情况下,变形元件的材料流入通过功能元件中的凹模预定的模具中,由此形成相应的表面几何结构。变形元件的成形和蛾眼结构的产生也可在独立步骤中不同时间或连续进行。
在另一优选的实施例中,精整涂层如此生产,使得在功能元件布置在变形元件上和/或与变形元件接触之前,至少功能元件的与变形元件接触的区域设有精整涂层,然后通过在精整涂层和变形元件之间的连接建立在变形元件和功能元件之间的连接,或在功能元件布置在变形元件上和/或与变形元件接触之前在变形元件上涂布精整涂层,然后使功能元件布置在涂饰涂层上和/或与其连接,其中,在变形步骤之后,功能元件至少部分地被移除并且精整涂层保留在变形元件上。通过在变形元件变形之前将精整涂层涂布到变形元件上,可尤其在倾斜的光学区域、例如棱柱的透射面上实现精整涂层的各个层的厚度公差较小的均匀的精整涂层。在变形元件变形之后涂布精整涂层时,必须例如在倾斜的区域或表面上沉积各个层并且可以进行结构化,由此得出尤其在使用各向异性的沉积方法时,各个层的厚度的差异以及精整涂层以及因此光学部件的与位置相关的特性差异或光功能差异。
根据该实施例生产的宽带抗反射涂层可以例如基于由氧化硅和氮化硅构成的层序列。在这种情况下,首先将氧化硅层涂布到例如由硅构成的功能元件上。随后,将氮化硅层施加到氧化硅层上。此后,将由功能元件、氧化硅层和氮化硅层的层序列通过以下方式与变形元件连接,即:使氮化硅层与变形元件连接。在选择性地移除功能元件之后,保留由变形元件、氮化硅层和氧化硅层组成的层序列,并因此保留具有抗反射涂层的变形元件。可以替代地使用二氧化钛代替氮化硅。
由精整涂层和功能表面结构的组合,例如抗静电涂层和蛾眼结构的组合可以改善光学部件的功能性。
附图说明
不限制一般性的情况下,下面根据示例详细描述本发明。
图2-2d示出了借助根据本发明的方法生产的具有倾斜光学窗口3和使用其包封微镜25的盖阵列22;
图3a-3h示出了用于使玻璃晶片1结构化以便借助玻璃流动生产开口8a的实施例的步骤序列;
图4a-4i、图4k和图4m示出了用于根据本发明的方法用于不同形状的变形区域并且使用不同压力生产具有倾斜的或倾斜且移位的光学窗口3的盖阵列22的实施例的步骤序列;
图5a-5g示出了用于根据本发明的方法、使用用作载体5的工具5或具有通风通道23的支撑件(auflage)5生产具有倾斜的光学窗口3的盖阵列22的另一实施例的步骤序列;
图6a-6f和图7a-7e示出了用于根据本发明的方法使用力引入成型装置生产具有倾斜的光学窗口3的盖阵列22的其他实施例的步骤序列;
图8a-e示出了用于根据本发明的方法使用具有支持结构21的载体5生产具有倾斜的光学窗口3的盖阵列22的实施例的步骤序列;
图9a-9e示出了用于根据本发明的方法使用稳定层20生产具有倾斜的光学窗口3的盖阵列22的另一实施例的步骤序列;
图10a-10i、图11a-11f、图12a-12b和图13a-13f示出了用于根据本发明的方法使用、尤其在载体5和变形元件1之间的、一个或多个空腔12、13生产具有倾斜的或倾斜且移位的光学窗口3的盖阵列22的其他实施例的步骤序列;
图14a-14d示出了用于根据本发明的方法使用载体中的凹陷10生产具有倾斜且移位的光学窗口3的盖阵列22的另一实施例的步骤序列;
图15a-15d示出了用于根据本发明的方法使用变形元件1和功能元件2之间的空腔11生产具有倾斜且移位的光学窗口3的盖阵列22的另一实施例的步骤序列;
图16a-16f示出了用于根据本发明的方法使用两侧平坦的变形元件1生产棱镜或斜交镜22b的阵列的实施例的步骤序列;
图17a-17g示出了用于根据本发明的方法使用岛状变形元件1生产棱镜或斜交镜22b的阵列的实施例的步骤序列;
图18a-18b和图19a-19b示出了用于根据本发明的方法生产具有移位的光学窗口3的盖阵列22的其他实施例的步骤序列。
具体实施方式
图2示出了借助根据本发明的方法生产的具有倾斜光学窗口3的盖阵列22,其中,合适的盖阵列22可用于包封整个硅晶片24。
倾斜光学窗口3以二维阵列布置,并且通常相对于盖阵列22的环绕每个窗口3的接触表面22a具有在约5°至约20°之间、优选约15°的倾斜度。环绕每个倾斜的光学窗口3的接触表面22a以框架形状闭合并且呈平坦状。
在载体衬底或硅晶片24上设置对应尺寸的以框架形状闭合的平坦表面作为反接触表面,如图2a所示。由此允许相对于环境气密密封连接。
倾斜的光学窗口3在两侧设有由二氧化硅和氧化钛构成的层系统的抗反射涂层。
在盖阵列22接合到硅晶片24上之后,布置在硅晶片24上的接触衬垫27暴露出来并且芯片被分离出,由此形成通过盖22包封的微镜25,如图2a-2d所示。
图4a-4m示出了根据本发明的方法用于生产盖阵列或盖22的多个实施例的步骤序列,盖阵列或盖具有倾斜的或倾斜且移位的光学窗口3。在工艺开始时提供的变形元件1是由硼硅酸盐玻璃制成的玻璃晶片,玻璃晶片在两侧具有呈平面状且平行的衬底面1a、1b,并且该玻璃晶片的厚度在约500μm至约1000μm之间,在这种情况下为725μm。玻璃晶片1的两个晶片侧面或晶片面1a、1b被抛光,并且因此具有均方根表面粗糙度约为1至3nm的高表面质量。此外,玻璃晶片1具有矩形的(图4f)或梯形的(图4g)开口8a,开口通过喷砂或铣削工艺实现。
玻璃晶片1的一个侧面1b通过阳极键合连接到用作载体5的硅晶片5,其中,该工艺实现气密密封连接(图4b)。玻璃晶片1的另一侧面1a通过与厚度为850μm的作为功能层4的另一玻璃晶片4熔接或热键合而气密密封(图4c),另一玻璃晶片由耐高温的或更高熔点的玻璃或硅酸盐玻璃(例如corningeagle
在温度约为400℃且压力约为10至20mba或800至1000mbar的情况下连接两个玻璃晶片1、4。
另一玻璃晶片4在两侧具有平坦的面平行衬底面,其中,两个晶片侧面或晶片面被抛光且具有约为1至3nm的均方根表面粗糙度。
由于玻璃晶片1与硅晶片5并且与另一晶片4的连接,基于开口8a而在玻璃晶片1中形成气密密封空腔12(图4c)。
在图3a-3h中示出了用于生产具有开口8a的玻璃晶片1的替代方案。对此,在第一步骤中,通过蚀刻、喷砂、钻孔、铣削和/或激光束加工在玻璃晶片1中产生辅助凹陷9(图3a)。通过使玻璃晶片1通过熔接与另一玻璃晶片4(图3b)连接或借助阳极键合与硅晶片5(图3c)连接,使玻璃晶片1中的辅助凹陷9被气密地密封,其中该另一玻璃晶片4在进一步工艺(verfahren)中代表功能元件2的基底并且相应地可用作功能衬底或功能层4,硅晶片5在进一步工艺中可用作载体5。替代地,代替在玻璃晶片1中形成辅助凹陷9,也可在硅晶片5中或另一玻璃晶片4中形成辅助凹陷9,以便在玻璃晶片1和硅晶片5或另一玻璃晶片4之间形成气密密封的空腔14。
在连接步骤中,在空腔14中产生约为800至1000mbar的压力。通过将由硼硅酸盐玻璃制成的玻璃晶片1加热到700℃以及因此加热到硼硅酸盐玻璃的软化温度的范围中的温度,玻璃晶片1变软或可流动。此外,将在空腔14中的压力提高到约1200至1600mbar。因为在大气压下进行加热,因此空腔14中的过压引起玻璃晶片1的变形(图3d、图3e)。通过研磨和抛光,使空腔14打开(图3f、图3g)并且在玻璃晶片1中产生开口8a。玻璃晶片1的被磨损的一侧之后与载体5或功能衬底4连接,从而封闭开口8a并且形成气密密封的空腔12(图3h)。
另一玻璃晶片4的用以产生例如可用作光学窗口3的多个功能元件2以及用于实现期望的变形区域15(图4d-玻璃晶片1的密点区域)的结构化借助锯切步骤进行,在锯切步骤中保留气密密封的空腔12(图4d)。对此,锯切另一玻璃晶片4,使得相应产生的功能元件2封闭空腔12(图4f和4g)。替代地,可如此生成功能元件2,使得相应产生的功能元件2封闭空腔12,空腔12根据图4f或图4g布置成列或竖直地布置。
此外,通过同一锯切步骤,对玻璃晶片1进行产生凹陷8b的结构化,由此设计、尤其框架形的、变形区域15且由此影响变形阻力。尤其变形区域15由此局部地设有另一表面区域17,从而减小变形区域15的这些表面区域的局部变形阻力(图4e)且在材料和时间消耗方面优化该工艺。
此外或替代地,可通过改变框架形的变形区域15的宽度来实现根据图4d的变形区域15的阻力非对称性。图4f和4g的俯视图示出了在锯切步骤之后在玻璃晶片1和功能元件2之间不同构造的第二接触表面7,其中,第二接触表面7的设计对于变形区域15的形状是决定性的。
为了确保期望的阻力非对称性,其中一个框架形的第二接触表面7的外边缘18和内边缘19分别通过矩形描述,它们的周向中心不重叠,其中,矩形内边缘19的对称轴线和矩形外边缘18的对称轴线位于同一直线上。由此框架形状的第二接触表面7的两个相对的支腿实施成宽度相同的并且另两个支腿实施成宽度不同(图4f)。
在根据图4g的实施方式中,其中一个框架形状的第二接触表面7的外边缘18通过矩形描述,而内边缘19通过等腰梯形描述。由此,框架形状的第二接触表面7的两个相对的支腿实施成锥形的并且另外两个支腿不是锥形的,在考虑到相应的载体5或相应成形的第一接触表面6的情况下,同样实现了变形区域15的阻力非对称性。
在接下来的方法步骤中,由玻璃晶片1、功能元件2和硅晶片5构成的层系统被加热。在使用由硼硅酸盐玻璃构成的、软化温度约为820℃的玻璃晶片1的情况下,将层系统加热到约700℃,由此玻璃晶片1变软并且开始流动。因为由硅酸盐玻璃(例如corningeagle
由于相比于接合工艺提高的温度,因此在空腔12中的压力从约10至20mbar提高到约20至30mbar,或从约800至1000mbar提高至约1200至1600mbar。相对于环境大气压力相应主导的负压或过压引起作用到玻璃晶片1、尤其变形区域15上的力,这引起玻璃晶片1或变形区域15的变形。
由于相应变形区域15的阻力非对称性,因此限定相应空腔12的功能元件2趋于倾斜(图4i-在空腔12中为过压;图4k-在空腔12中为负压)或趋于倾斜和移位(图4h和图4m-在空腔12中为过压)。在相应的功能元件2与偏转限定部(例如相邻的功能元件)接触时(图4m)或在空腔12中的压力通过引起变形已达到环境压力的值之后,变形步骤终止。
在另一步骤中,通过氢氧化钾(koh)中的湿法化学蚀刻从玻璃晶片1选择性地去除硅晶片5,并且将盖阵列22从成形的玻璃晶片1和功能元件2中分离,其中,分离工艺替代地也可在包封工艺之后进行,如图2a-2d所述。
在根据图5a-5g的另一示例性实施例中,代替硅晶片,使用具有通风通道23的工具或支撑件(einwerkzeugbeziehungsweiseeineauflage)作为载体5。在连接(verbinden)由硼硅酸盐玻璃制成的玻璃晶片1与另一玻璃晶片4(图5b)并且通过锯切步骤使两个玻璃晶片1、4结构化(图5c)以产生功能元件2以及以设计变形区域15之后,调整由玻璃晶片1和功能元件2构成的结构化玻璃晶片复合体使之与用作载体5的支撑件5接触,其中,支撑件5由石墨构成或者其中至少支撑件5的与结构化玻璃晶片复合体1、2接触的表面区域涂覆有石墨(图5d)。支撑件5的通风通道23匹配于结构化玻璃晶片复合体1、2的结构,从而通过结构化玻璃晶片复合体1、2和支撑件5封闭的每个空腔12与至少一个通风通道23连接(图5e)。在接下来的加热和变形期间,经由通风通道23借助真空泵在空腔12中产生低于环境压力(例如大气压力)的压力。通过由此实现作用到功能元件2或变形区域15上的力以及通过变形区域15的构造,产生作用到每个功能元件2上的合成扭矩,该合成扭矩与通过加热引起的玻璃晶片1的可流动硼硅酸盐玻璃结合,趋于使功能元件2在支撑件5的方向上倾斜或歪倾(neigenbeziehungsweiseverkippen)(图5f)。在达到期望的倾斜度之后,在空腔12中经由通风通道23设定环境压力,使得可从支撑件5移除成形的玻璃晶片复合体1、2(图5g)。支撑件5可重复用于另一工艺进程。
除了确保用于产生力作用的压差,也可经由成型装置30引入变形力,如图6a-6f和图7a-7e示出的那样。
图6a-6c示出了在使用硅晶片作为载体5的情况下的变型方案以及图6d-6f示出了在使用支撑件作为载体5的情况下的变型方案。成形装置30和支撑件5由在加热以及变形时尽可能较少粘附在结构化或成形的玻璃晶片复合体1、2上的材料、例如石墨构成或以该材料涂覆。通过对成形装置30的相应调节,可选择性地引入变形力,使得确保功能元件2或光学窗口3的倾斜。通过阻力非对称性的变形区域15(图6a-6c),可额外地辅助该倾斜。此外,可如此设计成形装置30,使得该成形装置同时用作止挡件,以便精确地实现光学窗口3的预定倾斜角度。可替代地,保持变形力直至达到功能元件2的期望倾斜度。在加热和变形之后,从成形的玻璃晶片复合体1、2除去成形装置30,从而可从支撑件5分离(图6f)成形的玻璃晶片复合体1、2或可以移除硅晶片5。
图7a-7e示出了具有楔形冲压元件31的成形装置30的应用。尤其冲压元件31的表面又由石墨制成或用石墨涂覆且允许基于其形状而将成形装置30自动对准放置到结构化玻璃晶片复合体1、2上。成型装置30又可用作止挡件,从而可精确地调节功能元件2的的倾斜角度。
在另一实施例中,冲压元件31具有倾斜的冲压表面,冲压表面具有对于光学窗口3期望的倾斜度。
根据图8a-8e的示例性实施例,由硼硅酸盐玻璃晶片1和功能元件2(例如光学窗口3)构成的结构化玻璃晶片复合体1、2(图8a)与支撑件5接触(图8b-8c),支撑件除了通风通道23之外还具有支撑结构21。在建立了接触之后,经由通风通道23借助真空泵在空腔12中设定低于环境压力的压力。通过将玻璃晶片1加热直至接近其软化温度,使该玻璃晶片1进入可流动的状态,使得通过由压差引起的力作用到结构化玻璃晶片复合体1、2上的力而使变形区域15变形。通过借助支撑结构21有针对性地局部支撑结构化玻璃晶片复合体1、2,可确保在功能元件2上的合成扭矩且可实现功能元件2相对于支撑件5或相对于功能元件2的初始位置的倾斜。
图9a-9e示出了用于生产具有倾斜的光学窗口3的盖阵列22的示例性实施例,其中通过使用稳定层20辅助功能元件2的倾斜。对此,由玻璃晶片1和另一玻璃晶片4构成的玻璃晶片复合体1、4在与作为载体5的硅晶片连接之后被结构化,使得在第一锯切步骤中,使另一玻璃晶片4的在加热和变形步骤中应尽可能少地偏转(图9a)的区域进行结构化。锯切切口形成为深至使得所产生的凹陷8c由玻璃晶片1部分地约束。然后,由此结构化的另一玻璃晶片4和凹陷8c利用由硅构成的稳定层20涂覆。可借助pvd或cvd方法沉积约1至5μm厚的硅层20。可替代地,锯切切口形成得深至使得另一玻璃晶片4的一部分作为稳定层保留。稳定层20通过其变形附加地抵消变形力并且此外稳定玻璃晶片1的由稳定层覆盖的区域。因为玻璃晶片1的该区域毗邻变形区域15且与该变形区域相互作用,因此以线形方式毗邻变形区域15的稳定层20附加地局部提高了变形区域15的变形阻力。
在另外的锯切步骤中,对玻璃晶片复合体1、4进行最终结构化以生产功能元件2或光学窗口3。变形区域15的通过该锯切步骤形成的区域不通过硅层20稳定(图9c),因为该区域旨在用于更大的偏转。由此确保在加热和变形期间功能元件2的倾斜(在空腔12中使用过压时的图9d)。硅层20还使得功能元件2稳定且固定在其位置中。通过使用稳定层20,可将变形区域15的旨在用于较小偏转且应因而具有较高变形阻力的区域设计成节省空间的(例如更窄)。
最后,移除硅载体5(图9e)并且成形的玻璃晶片复合体1、2可直接地或在包封整个晶片之后被分开。
在图10a-13f中,示出了用于生产具有倾斜的或移位且倾斜的光学窗口3的盖阵列22的不同实施例的步骤序列,其中,在载体5和变形元件1之间具有空腔13,用于确保功能元件2和光学窗口3的期望的倾斜或移位且倾斜。
在载体5和变形元件1之间的一个或多个空腔13可通过以下方式形成:将由硼硅酸盐玻璃制成的玻璃晶片1和/或硅晶片5实施成具有一个或多个凹陷8b、10,在玻璃晶片1与硅晶片5接触或连接之后,凹陷包围(einschlieβen)一个或多个空腔13。玻璃晶片1和硅晶片5之间的连接通过熔接建立,由此可气密地密封空腔13并且由此能够设定可以与环境压力和空腔12中的压力不同的压力。空腔12中的压力之后可在连接另一玻璃晶片4与玻璃晶片1时被调节。
功能元件2、玻璃晶片1和硅晶片5之间的空腔12中的压力如此调节,即:使得在加热和变形的工艺步骤中空腔12中的压力对应于环境压力。由此,在空腔12和周围环境之间不存在将使功能元件2或光学窗口3受到机械负荷的压差。通过以此方式实现的功能元件2的机械负荷的降低,即使在加热和变形期间也可特别好地保持功能元件2的初始形状。引起变形的力作用通过空腔13和环境或空腔12之间的压差实现。因此在空腔13中的约100至200mbar的过压导致功能元件2以及因此光学窗口3根据图10d和图13d偏转,约100至200mbar的负压导致根据图10h和图13c的偏转。在空腔13中为过压的情况下,可在真空炉中进行加热和变形,其中,空腔12中的压力设定成与真空炉中的压力相同。在空腔13中为负压的情况下,可在炉中以及空腔12中在大气空气压力下进行加热和变形。图13e的结果通过研磨和/或抛光进行再加工,以便提供用于包封步骤的平面接触表面22a(图13f)。
在另一实施例中,相比于环境压力,在加热和变形期间,空腔13中为过压且空腔12中为负压,由此引起根据图10i的变形。
替代地,可通过使用具有一个或多个通风通道23和平衡通道23a的相应支撑件5调节所需的压差,如在图11d-11f中所示。平衡通道23a提供了空腔12与环境的连通,从而避免或减小压差或使压差最小化。经由通风通道23借助真空泵在空腔13中设定处于环境压力之下的压力。
如已所述地,在这些情况下,单独使用特殊成形装置30(没有基于压差引入力)(图11b)或与通过压差引入力结合使用该特殊成形装置30来辅助成形。
图12a-12b还示出了这样的示例性实施例,其中,使用玻璃晶片1和硅晶片5之间的不同配置的空腔13(其被作用有不同压力),以便实现功能元件2的局部不同程度的偏转以及功能元件2或光学窗口3的倾斜或倾斜且移位。
图14a-14d示出了根据本发明的方法使用载体5中的凹陷10产生具有倾斜且移位的光学窗口3的盖阵列22的另一实施例的步骤序列,其中,相比于环境压力,在空腔12中设定负压从而引入力并且引起变形。
图15a-15d示出了根据本发明的方法使用变形元件1(由硼硅酸盐玻璃制成的玻璃晶片)和功能元件2之间的空腔11产生具有倾斜且移位的光学窗口3的盖阵列22的另一示例性实施例的步骤序列。用于空腔11的基底是功能元件2,功能元件具有凹陷10a。通过在空腔11中设定相比于环境压力的过压,将功能元件2从玻璃晶体1推离(图15c)。除了空腔11,可以设置空腔13(图15d),由此可确保附加的由压力引起的力引入。
通过一个变形区域或多个变形区域15不同的设计(图15b),实现功能元件2的倾斜。在移除了硅晶片5之后,通过研磨和/或抛光打开空腔11或空腔13。
在修改的工艺变型中,可以不包括空腔11(图15b)。在这种情况下,可例如通过磁性相互作用而引入力。在变形区域15的变形阻力中的用于辅助功能元件2的倾斜的局部差异尤其通过以下方式被确保,即:在功能元件2和玻璃晶片1之间的接触仅在可将引入力从功能元件2传递到玻璃晶片1上以便实现期望变形的区域中引起连接。在玻璃晶片1和功能元件2之间未相互连接的接触区域中,通过变形区域15的变形解除功能元件2和玻璃晶片1之间的接触并且由此在功能元件2和玻璃晶片1之间产生空腔11;等同于图15c中的示意图,但是在功能元件2中没有凹陷10a。
图16a-16f示出了用于对平面玻璃晶片1的两侧进行结构化的示例性实施例,玻璃晶片1由厚度为725μm的硼硅酸盐玻璃制成,从而产生一个或多个棱镜或斜交镜。为了产生棱镜阵列,对具有平坦衬底表面1a、1b的玻璃晶片1的一个晶片侧面1a涂覆或沉积一个层序列,该层序列由两个厚度分别为200μm的硅层4a、4b和夹设在其间的厚度为1μm的氧化硅层4c构成。通过结构化层序列4a、4b、4c,产生功能元件2(图16b)。通过使用这种层序列,可改进用于产生功能元件2的结构化的精确性。替代地,可涂覆或沉积厚度为400μm的硅层作为功能层4且然后进行结构化。功能元件2可满足成形元件的功能以及保护和/或成型元件的功能。作为成形元件,这些功能元件2将引入的力传递或分配到玻璃晶片1,由此该玻璃晶片变形。作为保护元件,功能元件2可保持玻璃晶片1提供的高表面质量。另一方面,作为成型元件,可将功能元件2的高表面质量成型或传递到玻璃晶片1上。通过使由石英玻璃制成的成形装置30与结构化硅层4a接触,引入用于使玻璃晶片1变形的力(图16c)。通过两个硅层4a、4b的非对称的结构化,实现功能元件2的倾斜(图16d)。
此外,功能元件2可基于结构化而具有止挡件的功能,因为在实现功能元件2的期望倾斜时,成形装置30与结构化硅层4b接触并防止进一步倾斜(图16d)。
在移除成型装置30并移除功能元件2之后,结构化玻璃晶片1可用作棱镜阵列或分成多个棱镜。
在生产镜阵列的情况下,可在加热和变形之后在功能元件2上或结构化的玻璃晶片1上或其倾斜的透射面3a上沉积铝层作为反射层。
图17a-17g示出了根据本发明的方法产生一个或多个棱镜或斜交镜的另一示例性实施例。在由硼硅酸盐玻璃制成的具有凹陷8b的玻璃晶片1借助熔接而接合在硅晶片5上之后,凹陷8b在接下来的用于产生岛状结构1的锯切步骤中可防止锯32与硅晶片5接触,在锯切步骤中由玻璃晶片1生成各个岛状结构(图17a-17b)作为变形元件1。替代地,可在与硅晶片5连接之前产生岛状结构1(例如通过锯切)并且借助真空处理机布置在硅晶片5上。通过连接石英玻璃晶片4与岛状结构1(图17c)并且然后借助锯切对石英玻璃晶片4进行结构化,生产多个功能元件2(图17d),其中,替代地又可在与岛状结构1连接之前产生功能元件2。结果是,每个岛状结构1与功能元件2连接,但是也可使例如布置成一排或一列的多个岛状结构1与一个功能元件2连接。
借助成形装置30引入变形力(图17e),从而使功能元件2倾斜(图17f)。
如果功能元件2已设有可反射的精整涂层,则产生的光学部件例如可用作斜交镜。替代地,在移除功能元件2和/或硅晶片5之后,提供棱镜作为光学部件。
图18a-18b和图19a-19b示出了两个示例性实施例,这两个示例性实施例示出根据本发明的方法产生具有移位的光学窗口3的盖阵列22。
在两个示例中,又基于在空腔12的压力(在图18a-18b的示例中为过压和在图19a-19b的示例中为负压)与环境压力之间的压差,引入用于变形的力。通过变形区域15的阻力非对称设计,避免了由于硼硅酸盐玻璃晶片1的变形引起光学窗口3的倾斜并且实现了移位。
根据图19a-19b的实施例,不是在之前的连接步骤中进行,而是通过支撑件5中的通风通道23和通风凹陷23b调节空腔12中的压力,通风通道和通风凹陷改善表面通风,借助真空泵设定期望的压力。通过在支撑件5中的凹陷10,可设定光学窗口3的期望偏转,其中,支撑件5用作偏转限制部。由此可制成特别精确的光学部件。
附图标记列表
1变形元件
1a、1b变形元件的晶片侧面或衬底表面
2功能元件
3光学窗口
3a例如光学窗口或棱镜的透射表面
4功能衬底或功能层
4a、4b硅层
4c氧化硅层
5载体(例如硅衬底、石墨支撑件)
6第一接触表面
7第二接触表面
8a变形元件中的开口
8b变形元件中的凹陷
8c用于稳定层的凹陷
9辅助凹陷(behelfsvertiefung)
10载体中的凹陷
10a功能元件中的凹陷
11在功能元件或功能衬底/层和变形元件之间的空腔
12在功能元件或功能衬底/层、变形元件和载体之间的空腔
13在变形元件和载体之间的空腔
14基于辅助凹陷的空腔
15变形区域
16a第一接触表面的重叠区域
16b第二接触表面的重叠区域
17变形区域的表面积
18第二接触表面的外边缘
19第二接触表面的内边缘
20稳定层
21载体的支撑结构
22盖或盖阵列
22a盖或盖阵列的接触表面
22b棱镜或斜交镜的阵列
23通风通道或排风通道
23a平衡通道
23b通风凹陷
24载体衬底
25微镜
26微镜的悬挂部
27接触衬垫
28入射辐射
29偏转辐射
30成形装置
31例如具有直的、斜的、楔形的或锥形的冲压表面的冲压元件
32锯
33框架节段
本文用于企业家、创业者技术爱好者查询,结果仅供参考。