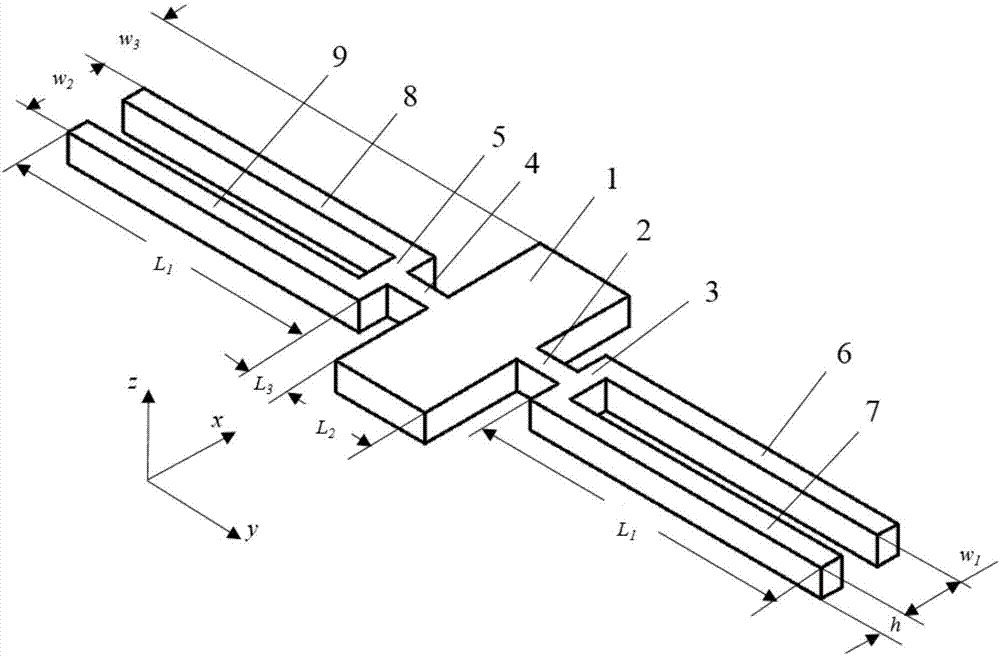
本发明涉及mems(microelectromechanicalsystems,微型机械电子系统)传感器领域,更具体地说,涉及一种基于面内谐振的mems黏密度传感器芯片及其制备方法。
背景技术:
:随着mems(microelectromechanicalsystems,微型机械电子系统)技术的发展,mems黏密度传感器作为一种能够同时测量流体黏度和密度的多功能传感器,其具有的微型化、集成化、功耗低和准确度高等优点使其在工业、医疗、化工和生物等诸多领域得到日渐广泛的应用。对基于谐振原理的黏密度传感器而言,按照谐振器件在流体中振动方式的不同可分为面外振动和面内振动,对面外振动而言,谐振器件与周围流体存在压缩力,所受阻尼为压膜阻尼,而做面内振动的谐振器件与周围流体为剪切力,所受阻尼为滑膜阻尼,因而在高黏度流体中,基于面外振动的黏密度传感器所受的阻尼力会显著增加,成为其黏密度测量范围、准确度和稳定度等测量性能下降的重要原因。为实现黏密度传感器在高黏度流体中的准确测量,诸多研究学者及相关结构对面内振动展开了研究,目前主要的面内振动方式有:振子的平行于芯片平面的摆动以及振子在宽度和长度方向的延伸振动,但是许多面内结构在提高黏密度传感器芯片品质因子的同时,使谐振频率显著降低,尚不能满足对高黏度流体同时获得较高精度、灵敏度的黏度和密度测量需要。技术实现要素:为解决现有技术中存在的问题,本发明的目的在于提供一种基于面内谐振的mems黏密度传感器芯片及其制备方法,本发明通过实现硅微谐振梁结构的面内振动,将与流体间的压膜阻尼替代为滑膜阻尼,降低黏密度传感器芯片在流体环境中所受的阻尼力,提高传感器芯片的品质因子并具有较高的谐振频率,提高黏密度传感器对黏度和密度的测量精度与灵敏度等测量性能,能够有效解决现有技术中存在mems黏密度传感器对高黏度流体测量精度低的技术难题。为了实现上述目的,本发明采用如下的技术方案:一种基于面内谐振的mems黏密度传感器芯片,其特征在于,包括硅基底和硅微谐振梁结构,硅基底上开设有窗口,硅微谐振梁结构设置在窗口内并与窗口连接;硅微谐振梁结构包括振子、弹性连接梁、弹性固支梁以及导线;弹性连接梁包括第一弹性连接梁、第二弹性连接梁、第三弹性连接梁和第四弹性连接梁;弹性固支梁包括第一弹性固支梁、第二弹性固支梁、第三弹性固支梁和第四弹性固支梁;第一弹性连接梁和第二弹性连接梁相互垂直并组成t型梁结构,第一弹性连接梁的一端与振子相连,另一端与第二弹性连接梁的中部连接,第二弹性连接梁的两端分别与第一弹性固支梁和第二弹性固支梁的端部相连,第一弹性固支梁和第二弹性固支梁相互平行,均与第二弹性连接梁垂直;第三弹性连接梁和第四弹性连接梁相互垂直并组成t型梁结构,第三弹性连接梁与第一弹性连接梁对称设置在振子两侧,第三弹性连接梁的一端与振子相连,另一端与第四弹性连接梁的中部连接,第四弹性连接梁的两端分别与第三弹性固支梁和第四弹性固支梁的端部相连,第三弹性固支梁和第四弹性固支梁相互平行,均与第四弹性连接梁垂直;第一弹性连接梁、第二弹性连接梁、第一弹性固支梁和第二弹性固支梁连接而成的整体与第三弹性连接梁、第四弹性连接梁、第三弹性固支梁和第四弹性固支梁连接而成的整体关于振子对称;第一弹性连接梁和第三弹性连接梁的中心线与振子的长度方向的中心线重合;第一弹性固支梁、第二弹性固支梁、第三弹性固支梁和第四弹性固支梁的另一端固定于硅基底的窗口的边缘上;导线包括对称设置的第一导线和第二导线,第一导线沿着第三弹性固支梁、第四弹性连接梁、振子的长度方向的中心线、第一弹性连接梁、第二弹性连接梁和第一弹性固支梁的路径设置;第二导线沿着第四弹性固支梁、第四弹性连接梁、振子的长度方向的中心线、第一弹性连接梁、第二弹性连接梁和第二弹性固支梁的路径设置。进一步的,所述振子为矩形截面质量块,振动方向为沿振子宽度方向的面内振动,且振动方向平行于传感器芯片,振子与被测流体间存在相互作用的剪切力。硅基底的形状为矩形,窗口为矩形窗口,窗口的与硅基底同心且对应边平行,硅微谐振梁结构设置在窗口的长度或宽度方向所对应的轴线上。振子为长方体结构,振子与窗口同心且对应边平行,长度为50~100μm,宽度为150~300μm,厚度为15~30μm;第一弹性连接梁和第三弹性连接梁的尺寸相同,长度为20~40μm,宽度为10~30μm,厚度为15~30μm;第一弹性固支梁、第二弹性固支梁、第三弹性固支梁和第四弹性固支梁的尺寸相同,长度为300~1000μm,宽度为10~20μm,厚度为15~30μm;第二弹性连接梁和第四弹性连接梁的尺寸相同,宽度为40~100μm,长度为10~40μm,厚度为15~30μm。所述硅基底为单晶硅。进一步的,第一导线和第二导线的两端均分别连接有焊盘,硅微谐振梁结构和硅基底上除焊盘对应的位置外均覆盖有氮化硅绝缘保护层,保障传感器芯片在腐蚀性、导电性等流体中仍可以实现黏密度的准确测量。一种基于面内谐振的mems黏密度传感器芯片的制备方法,其特征在于,包括以下步骤:步骤1),将硅基底的正面和背面均进行氧化,在硅片表面生成二氧化硅层;步骤2),再在步骤1)处理完的硅基底的正面旋涂一层光刻胶,再在导线与焊盘对应位置进行光刻,去除该位置的光刻胶,然后在硅基底表面溅射制作金属层,再进行剥离,使硅基底表面形成传感器芯片的导线和焊盘;步骤3),再在步骤2)处理完的硅基底的正面和背面制备厚一层氮化硅层;步骤4),再在步骤3)处理完的硅基底背面去除窗口对应区域的氮化硅层和二氧化硅层,使硅基底背面露出待腐蚀窗口,在待腐蚀窗口处刻蚀窗口对应的背腔,使硅基底上窗口所对应的区域形成一定厚度的薄膜,该薄膜的厚度为硅微谐振梁厚度;步骤5),再在步骤4)处理完的硅基底的正面旋涂光刻胶,再在焊盘对应位置进行光刻,露出氮化硅层,再刻蚀掉焊盘处对应的氮化硅,露出焊盘;步骤6),再在步骤5)处理完的硅基底的正面旋涂光刻胶,再在窗口所对应的区域中除了硅微谐振梁结构对应区域进行光刻,露出该区域的氮化硅层,再对该区域进行刻蚀,释放出硅微谐振梁结构,至此获得基于面内谐振的mems黏密度传感器芯片。在进行步骤1)之前,使用hf溶液对双面抛光的硅基底表面进行清洗,清洗后,硅片厚度为300~400μm。所述步骤1)中,生成的二氧化硅层的厚度为0.4~0.5μm。所述步骤3)中,采用lpcvd工艺在步骤3)处理完的硅基底的正面和背面制备厚为0.2~1.0μm的氮化硅层。所述步骤4)中,使用koh湿法工艺在待腐蚀窗口处刻蚀窗口对应的背腔。所述步骤6)中,释放出硅微谐振梁结构时的刻蚀过程采用感应耦合等离子刻蚀工艺。与现有技术相比,本发明具有如下有益效果:本发明一种基于面内谐振的mems黏密度传感器芯片至少具有以下优点:本发明的mems黏密度传感器芯片通过在硅基底上开设窗口,硅微谐振梁结构设置在窗口内并与窗口连接,硅微谐振梁结构包括振子、弹性连接梁、弹性固支梁以及导线,弹性连接梁为两个t型梁结构,两个t型梁结构对称设置在振子两侧,并分别通过对称的两根弹性固支梁与硅基底的窗口的边缘连接,导线设置为两根,两根导线对称布置在弹性连接梁和弹性固支梁上,并穿过振子宽度方向的轴线;本发明的mems黏密度传感器芯片在使用时,将其置于外界恒定磁场中,磁场方向与mems黏密度传感器芯片平面垂直;将布置于传感器芯片上的一根导线通入交变电流(如正弦交变电流),则该导线所在的两根弹性固支梁在恒定磁场中受交变洛伦兹力产生面内振动,振动方向沿振子宽度方向且与mems黏密度传感器芯片平面平行,导线所在的两根弹性固支梁通过t型梁结构带动振子做面内振动,同时带动另外一侧的弹性固支梁产生受迫振动,从而使另一根导线在磁场中切割磁感线产生感应电动势,改变通入电流的频率使浸入被测流体中的硅微谐振梁产生谐振,由输出感应电动势的幅值大小得到硅微谐振梁在流体中的谐振频率;硅微谐振梁结构在不同流体中具有不同的谐振频率和品质因子,依于此,能够实现mems黏密度传感器的流体黏度和密度测量;综上,本发明的mems黏密度传感器芯片基于面内振动方式,硅微谐振梁与流体间的阻尼类型为滑膜阻尼,阻尼力为剪切力,有利于降低硅微谐振梁在流体中的阻尼作用,提高mems黏密度传感器的品质因子;使用电磁激励、电磁检测的方式进行流体黏度、密度的准确测量,黏度测量精度优于±1%fs,密度测量精度优于±0.5%fs;因此能够实现高黏度流体的黏密度测量,且在非牛顿流体中仍具有良好的测量精度和灵敏度。本发明制备基于面内谐振的mems黏密度传感器芯片的过程中,通过先在硅基底的正面和背面生成二氧化硅层,使得后续形成的导线与硅基底,焊盘与硅基底之间能够电绝缘,能够防止导线通电时,硅基底发生导电现象,通过在二氧化硅层表面制备氮化硅层,氮化硅层作为化学绝缘层,能够提高传感器芯片的工作时的稳定性。附图说明图1为本发明的基于面内谐振的mems黏密度传感器芯片的结构示意图。图2为本发明的硅微谐振梁结构的结构示意图。图3为本发明的硅微谐振梁结构的comsol仿真效果图。图4为本发明的制备基于面内谐振的mems黏密度传感器芯片的工艺流程图。图中标号如下:1-振子,2-第一弹性连接梁,3-第二弹性连接梁,4-第三弹性连接梁,5-第四弹性连接梁,6-第一弹性固支梁,7-第二弹性固支梁,8-第三弹性固支梁,9-第四弹性固支梁,10-第一导线,11-第二导线,12-硅基底,12-1窗口,13-二氧化硅层,14-金属层,15-氮化硅层,16-焊盘。具体实施方式下面将结合附图,并通过实例,对本发明作进一步详细描述。如图1所示,本发明的基于面内谐振的mems黏密度传感器芯片,其特征在于,包括硅基底12、硅微谐振梁结构和导线,硅基底12上开设有窗口12-1,硅微谐振梁结构设置在窗口12-1内并与窗口12-1连接,硅基底12为单晶硅;硅微谐振梁结构包括振子1、弹性连接梁、弹性固支梁以及导线;弹性连接梁包括第一弹性连接梁2、第二弹性连接梁3、第三弹性连接梁4和第四弹性连接梁5;弹性固支梁包括第一弹性固支梁6、第二弹性固支梁7、第三弹性固支梁8和第四弹性固支梁9;第一弹性连接梁2和第二弹性连接梁3相互垂直并组成t型梁结构,第一弹性连接梁2的一端与振子1相连,另一端与第二弹性连接梁3的中部连接,第二弹性连接梁3的两端分别与第一弹性固支梁6和第二弹性固支梁7的端部相连,第一弹性固支梁6和第二弹性固支梁7相互平行,均与第二弹性连接梁3垂直;第三弹性连接梁4和第四弹性连接梁5相互垂直并组成t型梁结构,第三弹性连接梁4与第一弹性连接梁2对称设置在振子1两侧,第三弹性连接梁4的一端与振子1相连,另一端与第四弹性连接梁5的中部连接,第四弹性连接梁5的两端分别与第三弹性固支梁8和第四弹性固支梁9的端部相连,第三弹性固支梁8和第四弹性固支梁9相互平行,均与第四弹性连接梁5垂直;第一弹性连接梁2、第二弹性连接梁3、第一弹性固支梁6和第二弹性固支梁7连接而成的整体与第三弹性连接梁4、第四弹性连接梁5、第三弹性固支梁8和第四弹性固支梁9连接而成的整体关于振子1对称;第一弹性连接梁2和第三弹性连接梁4的中心线与振子1的长度方向的中心线重合;第一弹性固支梁6、第二弹性固支梁7、第三弹性固支梁8和第四弹性固支梁9的另一端固定于硅基底12的窗口12-1的边缘上;导线包括对称设置的第一导线10和第二导线11,第一导线10沿着第三弹性固支梁8、第四弹性连接梁5、振子1的长度方向的中心线、第一弹性连接梁2、第二弹性连接梁3和第一弹性固支梁6的路径设置;第二导线11沿着第四弹性固支梁9、第四弹性连接梁5、振子1的长度方向的中心线、第一弹性连接梁2、第二弹性连接梁3和第二弹性固支梁7的路径设置;第一导线10和第二导线11的两端均分别连接有焊盘16,硅微谐振梁结构和硅基底12上除焊盘16对应的位置外均覆盖有氮化硅绝缘保护层,保障传感器芯片在腐蚀性、导电性等流体中仍可以实现黏密度的准确测量。结合图2,本发明的硅基底12的形状为矩形,窗口12-1为矩形窗口,窗口12-1的与硅基底12同心且对应边平行,硅微谐振梁结构设置在窗口12-1的长度或宽度方向所对应的轴线上;振子1为矩形截面质量块,振子1与窗口12-1同心且对应边平行,长度为50~100μm,宽度为150~300μm,厚度为15~30微米;振动方向为沿振子宽度方向的面内振动,且振动方向平行于传感器芯片,振子与被测流体间存在相互作用的剪切力。第一弹性连接梁2和第三弹性连接梁4的尺寸相同,长度为20~40μm,宽度为10~30μm,厚度为15~30微米;第一弹性固支梁6、第二弹性固支梁7、第三弹性固支梁8和第四弹性固支梁9的尺寸相同,长度为300~1000μm,宽度为10~20μm,厚度为15~30μm,第二弹性连接梁和第四弹性连接梁的尺寸相同,长度为10~40μm,宽度为40~100μm,厚度为15~30μm。本发明的基于面内谐振的mems黏密度传感器芯片基于面内振动原理,使用电磁激励和电磁检测的方式实现流体的黏度和密度测量,与流体间存在剪切阻尼力,有利于减小与被测流体的阻尼作用,提高黏密度传感器的品质因子与测量精度。在使用时,该mems黏密度传感器芯片置于外界恒定磁场中,磁场方向与mems黏密度传感器芯片平面垂直;将布置于传感器芯片上的一根导线通入正弦交变电流,则该导线所在的两根弹性固支梁在恒定磁场中受交变洛伦兹力产生面内振动,振动方向沿振子1宽度方向且与mems黏密度传感器芯片平面平行,导线所在的两根弹性固支梁通过t型梁结构带动振子1做面内振动,同时带动另外一侧的弹性固支梁产生受迫振动,从而使另一根导线在磁场中切割磁感线产生感应电动势,改变通入正弦电流的频率使浸入被测流体中的硅微谐振梁产生谐振,由输出感应电动势的幅值大小得到硅微谐振梁在流体中的谐振频率;硅微谐振梁结构在不同流体中具有不同的谐振频率和品质因子,依于此,能够实现mems黏密度传感器的流体黏度和密度测量。结合图2进一步可知,硅微谐振梁结构中振子的振动方向为x方向,与被测流体间为剪切阻尼力,实现黏密度传感器芯片的面内振动。半功率法确定品质因子q为:其中,f为硅微谐振梁结构的谐振频率,δf是半功率峰宽(可以通过硅微谐振梁结构的谐振曲线拟合得到)。基于面内谐振的mems黏密度传感器芯片的测量工作方程满足:其中,ηf与ρf分别为待测流体的测量黏度和密度,c为常数,ff为硅微谐振梁在流体中的谐振频率,qf和qvac分别为硅微谐振梁在流体和真空环境中的品质因子。上式中,将ηf与ρf替换为待测液体的参考值,其它参数代入测试值,便可以计算出常数c。被测流体的密度ρf为:其中,f硅微谐振梁结构的本征频率,h、l和ρc分别为硅微谐振梁结构的厚度、长度和密度,w为振子的宽度,e为硅微谐振梁结构的杨氏模量,ffluid为硅微谐振梁结构在被测流体中的谐振频率。硅微谐振梁结构的设计尺寸参数为:其中,l1为弹性固支梁的长度,(w2-w1)为弹性固支梁宽度;l2为振子的长度;振子宽度w=w2 2w3;硅微谐振梁长度l=2l1 l2 2l3。结合图3,使用comsol有限元仿真软件对硅微谐振梁建立流固耦合仿真模型,得到如图所示的硅微谐振梁的面内振动仿真效果图。使用压力声学物理场模拟流体环境,硅微谐振梁结构为单晶硅材料,流体参数选用常见的醇类及烷类:乙醇、正庚烷、正己烷、正辛烷。仿真结果为:流体谐振频率f(khz)品质因子q乙醇65.14242.34正庚烷66.05313.77正己烷66.25232.49正辛烷65.89218.92由仿真结果可以看出,本发明提出的一种基于面内谐振的mems黏密度传感器芯片具有较高的谐振频率和品质因子,有利于提高流体黏度、密度的测量范围和测量精度,实现高黏度流体的黏密度测量。结合图4,本发明的制备基于面内谐振的mems流体黏密度传感器芯片的制备工艺流程,包括如下步骤:步骤a),将n型(100)双面抛光硅片作为硅基底12使用hf溶液清洗干净,清洗后,硅基底12的厚度为300~400μm;步骤b),将步骤a)清洗后的硅基底12进行双面氧化,在硅基底12的正面和背面均生成厚度为0.4~0.5μm的二氧化硅层13;步骤c),将一薄层光刻胶(图中未示出)旋涂在步骤b)处理过的硅基底12的正面,通过光刻去除部分光刻胶,裸露出与导线和焊盘16相同的形状,然后再在硅基底12的表面溅射制作金属层14,再采用剥离(lift-off)工艺将其余光刻胶去除,则在硅基底12的正面形成传感器芯片的金属导线和焊盘;步骤d),采用lpcvd工艺在步骤c)处理完的硅基底12的正面和背面制备一层厚度为0.2~1.0μm的氮化硅层15,氮化硅层15作为化学惰性绝缘层,能够提高传感器芯片的稳定性;步骤e),再在步骤d)处理完的硅基底12背面去除窗口12-1对应区域的氮化硅15和二氧化硅层13,使硅基底12背面露出待腐蚀窗口,在待腐蚀窗口处使用koh湿法工艺刻蚀窗口12-1对应的背腔,刻蚀一定的深度,使硅基底12上窗口12-1所对应的区域形成一定厚度的薄膜,该薄膜的厚度为设计的硅微谐振梁厚度;步骤f),再在步骤e)处理完的硅基底12的正面旋涂光刻胶,再在焊盘对应位置进行光刻,露出氮化硅层15,并再刻蚀掉焊盘16处相应的氮化硅层,露出焊盘16,因此能够通过焊盘16实现电气连接,其余导线由氮化硅层保护,有利于实现导电和腐蚀性等流体的黏密度测量;步骤g),再在步骤f)处理完的硅基底12的正面旋涂光刻胶,再在窗口12-1所对应的区域中除了硅微谐振梁结构对应区域进行光刻,露出该区域的氮化硅层15,再采用感应耦合等离子(icp)刻蚀技术对该区域的氮化硅层15和二氧化硅层13进行刻蚀,释放出硅微谐振梁结构,至此获得基于面内谐振的mems黏密度传感器芯片。本发明制备的基于面内谐振的mems黏密度传感器芯片的主要技术指标如下:1、测量介质:牛顿和非牛顿流体;2、黏度测量范围:1mpa·s~100mpa·s;3、密度测量范围:100kg/m3~1500kg/m33、测量精度:黏度优于±1%fs,密度优于±0.5%fs;4、工作温度:-40℃~125℃;5、环境压力:≤100mpa。以上所述仅为本发明的一种实施方式,不是全部或唯一的实施方式,本领域普通技术人员通过阅读本发明说明书而对本发明技术方案采取的任何等效的变换,均为本发明的权利要求所涵盖。当前第1页12
再多了解一些
本文用于企业家、创业者技术爱好者查询,结果仅供参考。