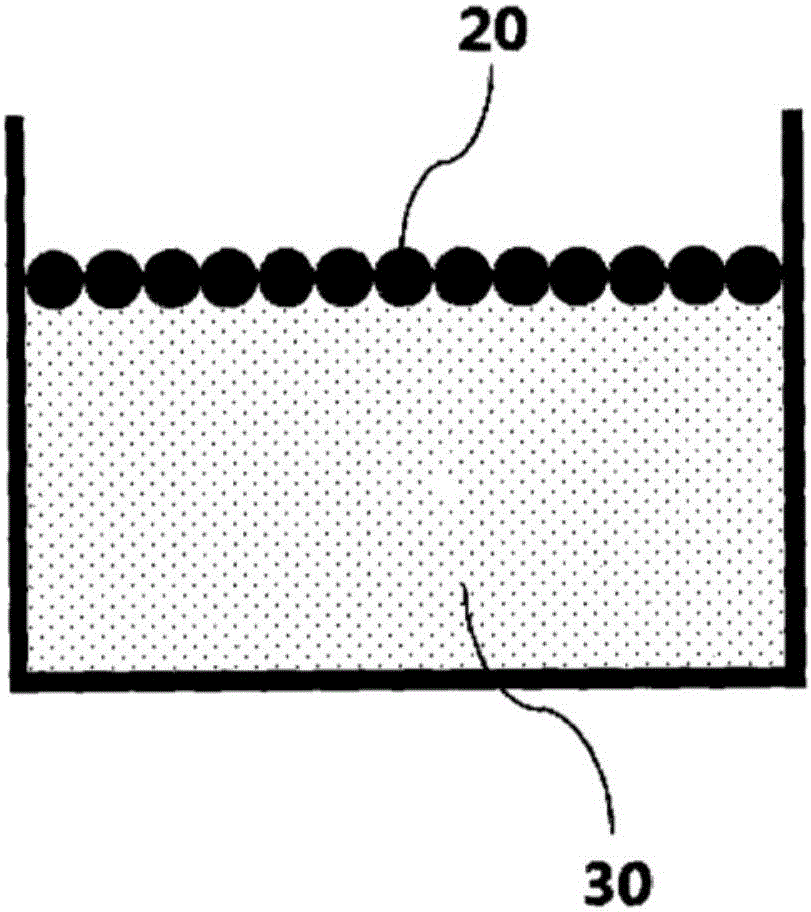
本发明涉及经济划算地制造金属网格薄膜的方法。
另外,本发明涉及利用上述方法来制造垂直对齐的GaAs(砷化镓)半导体纳米线阵列的方法。
详细地,本发明涉及采用具有对齐的纳米尺寸孔的金属薄膜作为阳极(anode),从外部施加电压或电流,将孔(h )注入到GaAs基板,湿法刻蚀具有结晶取向的半导体基板,从而大面积制造出直径和长度可控、具有宽表面积和高纵横比的垂直对齐的GaAs半导体纳米线阵列的方法。
背景技术:
近来,由于低维半导体纳米结构独特的物理特性和结构特性,关于利用低维半导体纳米结构作为半导体纳米线的高性能元件的研究正在活跃进行。相比于由硅(Si)或锗(Ge)等单一元素形成的单结晶半导体,由两种或多种元素形成的化合物半导体可利用多种元素的组合和组成比来实现符合目的的多种类半导体纳米元件。
其中,作为III-V族半导体的GaAs因具有比硅快达5倍的电子移动速度和简单的晶体管结构可制造很多高速集成电路。而且,GaAs可处理高达250GHz的高频带,且较少受到温度变化的影响,因而相比于硅具有运行噪声低的优点。最重要的是,GaAs由于具有直接带隙半导体特性,发光效率优异。因此,GaAs作为近期急剧增长的发光二极管或太阳能电池组件的材料广受瞩目。
因此,为了利用GaAs纳米线作为实际元件,必须对具有宽表面积和高纵横比的高品质的垂直对齐的GaAs半导体纳米线阵列进行较好的空间对齐,调节其密度,还需要均匀控制纳米线的直径和长度。
截止到目前的报道,GaAs纳米线的生长方法大致分类为自下向上法(Top-down)和自下向上法(Bottom-up)。
在所述自上向下法中,可利用分子束外延法(Molecular Beam Epitaxy,MBE)、金属有机化学气相沉积法(Metal Organic Chemical Vapor Deposition,MOCVD)等来生长GaAs纳米线。但是,在所述自上向下法中,在纳米线生长时会产生孪晶(twin)等缺陷,并且在基板上垂直对齐具有均匀长度和直径的纳米线也存在困难。而且,所述自下向上法可分为干法刻蚀和湿法刻蚀。反应离子刻蚀(RIE)作为干法刻蚀的典范,需要昂贵的设备、可能会在工艺中损坏材料并且导致表面不均匀及产生大量杂质,从而对物理及化学特性产生较大的影响,进而对元件设计产生变数,因此不适合。
另外,金属辅助化学刻蚀(Metal-assisted chemical etching)作为湿法刻蚀刻蚀的典范,目前已在硅纳米线制造上进行了最活跃的研究,金属辅助化学刻蚀刻蚀是将图形化(patterning)薄膜浸渍在含氧化剂的刻蚀液中,利金属作为催化剂刻蚀诱导自发性反应,从而在短时间内获得长度和直径可控的纳米线的方法。目前将这种方法利用于制造包含GaAs的III-V族半导体纳米线的研究范围正在逐渐扩大。
但是,对于包含GaAs的III-V族半导体基板,在将金属作为催化剂进行化学刻蚀时,垂直刻蚀的同时会发生侧面刻蚀,因此很难制造出具有均匀的直径和长度的纳米线,也很难制造出高纵横比的纳米线。
技术实现要素:
【技术问题】
本发明的目的是克服现有技术中采用金属作为催化剂通过湿化学刻蚀GaAs半导体基板刻蚀制造GaAs半导体纳米线阵列的技术局限,从而提供了一种垂直对齐的具有均匀直径和长度的GaAs半导体纳米线阵列。
另外,本发明的目的是提供上述垂直对齐的具有均匀直径和长度的GaAs半导体纳米线阵列的大面积制造技术。
进一步,本发明的另一个目的是通过抑制侧面刻蚀来制造出具有均匀直径和高纵横比的纳米线,从而提供一种能够克服因普遍存在于III-V族半导体基板的侧面刻蚀效应导致的长度局限性的方法。
进一步,本发明的目的是不管GaAs基板的掺杂浓度及掺杂种类如何,提供一种制造垂直对齐的GaAs纳米线阵列的方法。
进一步,本发明的目的是不管基板的结晶取向是否与垂直对齐的GaAs纳米线不同,提供一种制造与基板具有相同取向的垂直对齐的GaAs纳米线阵列的方法。
进一步,本发明的目的是提供一种通过控制从具有一种结晶取向的GaAs基板制造出的GaAs纳米线的刻蚀方向,制造具有一种或多种结晶取向的GaAs纳米线阵列,和制造结晶取向周期性交替的锯形GaAs纳米线阵列,及制造多孔GaAs纳米线阵列的方法。
【技术方案】
为达成上述目的,本发明提供的GaAs纳米线阵列的制造方法包括:(a)在GaAs基板表面制作图形化金属网格的步骤;(b)在刻蚀液中通过对所述金属网格施加偏压湿法刻蚀所述GaAs基板刻蚀刻蚀的步骤。
根据本发明的一方面,所述步骤(a)还包括:(a1)在所述GaAs基板上生成有机粒子单层阵列的步骤;(a2)在所述有机粒子的单层阵列上沉积金属薄膜的步骤;(a3)通过移除所述有机粒子的单层阵列来制造所述金属网格的步骤。
另外,根据本发明的一方面,所述步骤(a1)还包括先预处理GaAs基板的步骤。
另外,根据本发明的一方面,在所述步骤(a2)之后,通过加热或在氧气氛围(空气、氧气或臭氧氛围)中进行等离子处理来收缩所述有机粒子单层阵列中的有机粒子,进而增加阵列和阵列之间的间距,以调整纳米线间的生成距离。
以下具体说明本发明的一方面。
本发明一方面提供的III-V族化合物半导体纳米线阵列的制造方法包括:(a)在III-V族化合物半导体基板表面制作图形化金属网格的步骤;(b)在刻蚀液中通过对所述金属网格施加偏压湿法刻蚀刻蚀GaAs基板刻蚀的步骤。
根据本发明的一方面,所述步骤(a)还包括:(a1)在所述GaAs基板上生成有机粒子单层阵列的步骤;(a2)在所述有机粒子单层阵列上沉积金属薄膜的步骤;(a3)通过移除所述有机粒子单层阵列来制造所述金属网格的步骤。
本发明一方面提供的III-V族化合物半导体纳米线阵列的制造方法可进一步包括,在步骤(a2)之后,通过加热或在空气、氧气或臭氧氛围中进行等离子处理来收缩有机粒子单层阵列中的有机粒子,进而增加阵列和阵列之间的间距。
根据本发明的一方面,所述金属网格的孔形状至少为圆形、椭圆形、正方形、矩形、纤维形及多边形中的一种。
根据本发明的一方面,,将所述金属网格作为阳极(anode)施加电压或电流。
根据本发明的一方面,所述金属网格包括不被所述刻蚀液腐蚀的金属刻蚀,包括银(Ag)、金(Au)、钯(Pd)或铂(Pt)。根据本发明的一方面,所述金属网格由具有两种或多种元素的合金形成或由两种或多种金属多层沉积形成。另外,所述金属网格还可通过利用有机粒子的制造方法以外的多种图形化(patterning)方法来制造。
另外,纳米线的长度通过湿法刻蚀的时间控制或通过施加偏压的大小控制。
另外,所述刻蚀液包括氢氟酸(HF)、盐酸(HCl)或硝酸(HNO3)。
另外,在所述湿法刻蚀步骤中,将纳米线的形状制造为垂直于所述基板或制造为锯形。另外,在所述湿法刻蚀步骤中,对所述基板施加偏压以诱导纳米线具有多孔性表面。
另外,在所述湿法刻蚀步骤中,纳米线的缩短长度取决于所述金属网格的孔尺寸的变化。
本发明中,所述III-V族化合物半导体可为GaAs。
以下说明关于本发明III-V族化合物半导体纳米线阵列的制造方法。
本发明(a1)步骤中的生成所述有机粒子单层阵列,原则上,在所述GaAs基板的全部区域生成所述有机粒子单层阵列,但根据需求也可在所述GaAs基板的部分区域生成所述有机粒子单层阵列,而且所述有机粒子单层阵列也可生成2层或3层等复数层,从而制造出非典型的而不一定是垂直型的GaAs纳米线。这些复数层根据需求可全部生成或仅部分生成,并且这些复数层可共混。在本发明中,对于该领域技术人员而言即使在生成单层阵列的情况下单层阵列仍会存在部分缺陷是显而易见的,因此概率上最优选地是以紧密堆积方式形成单层。
本发明中,对所述GaAs基板进行预处理有利于通过去除污染物质来保证生成纳米线的均匀性。预处理优选交替使用有机溶剂和离子水通过水洗进行。有机溶剂选用不损坏GaAs基板的溶剂,例如,丙酮、酮、乙醇、甲醇、乙醚、乙酸乙酯或四氢呋喃等,但并不仅限于此。预处理还可采用涡流或直流。也就是说,可采用多种方式进行预处理。
本发明提供的在所述GaAs基板上生成有机粒子单层阵列的方法中,所述有机粒子单层阵列通过将所述有机粒子以层形式分散在溶剂或水的表面上,然后转移至所述GaAs基板生成。转移可采用多种方式,例如,将GaAs基板投入至分散有机粒子的液态介质后,将GaAs基板从液态介质中缓慢提出,从而在GaAs基板表面上生成有机粒子单层阵列。所述液态介质可根据有机粒子的性质来自行选择,例如,液态介质可为上述预处理中使用的水或有机溶剂等,但并不仅限于此。
在本发明中,所述有机粒子的尺寸可为1nm~5000μm,优选为10nm~100μm,更优选为10nm~10μm,但并不仅限于此。所述有机粒子的种类可为聚苯乙烯粒子、聚甲基丙烯酸甲酯粒子、聚烯烃粒子、聚醋酸乙烯酯粒子、聚丁二烯粒子、交联丙烯酸粒子、环氧树脂粒子或其他橡胶粒子等,但并不仅限于此。由于聚苯乙烯粒子的密度低、浮游于水且商业化程度高,因此可优选聚苯乙烯粒子,但并不仅限于此。
另外,在本发明中,所述有机粒子可为圆形、椭圆形、正方形、矩形、纤维形及板状形等多种形状,因此本发明制造出的纳米线也可具有多种多样的形状。这是因为有机粒子的形状决定金属网格的孔形状,而金属网格的孔形状决定纳米线的形状。
另外,在本发明中,在步骤(a2)之后,通过加热或在氧气氛围(空气、氧气或臭氧氛围)中进行等离子处理来收缩所述有机粒子单层阵列中的有机粒子,进而增加阵列和阵列之间的间距,以调整纳米线的生成距离。此步骤中有机粒子出现收缩现象的原因在于,经过等离子处理或加热处理后相互交联的或膨胀的有机粒子的体积会致密地收缩。由于在进行加热处理时不能熔融有机粒子,因此优选在等于或高于玻璃化转变温度且低于熔融温度的温度下进行热处理。
本发明的步骤(a2)中沉积金属薄膜时,可采用现有技术中的多种生成金属薄膜的方法或类似方法,因此不具体限定其方法。例如,可沉积制造纳米线阵列时作为电极的钯(Pd)、金(Au)、铂(Pt)或银(Ag),金属的沉积采用热沉积(thermal evaporation)、等离子沉积(plasma sputter)或电子束沉积(e-beam evaporation)。
以下说明本发明的步骤(a3)。本发明的步骤(a3)为沉积金属后去除有机粒子的步骤。一旦去除有机粒子,有机粒子在GaAs基板上的附着位置就会形成网格形状。有机粒子可采用溶解于溶剂的方式去除或置于至非溶剂中后通过超声波处理等方式物理去除,但并不仅限于一种方式。例如,在本发明选用聚苯乙烯粒子的例子时,GaAs基板被置于甲苯或三氯甲烷后进行超声波处理,以去除排列于GaAs基板表面的聚苯乙烯纳米粒子,进而制造出多孔金属网格。
当采用上述方式去除有机粒子后,根据金属薄膜的厚度与用于沉积金属薄膜的GaAs基板上的有机粒子的附着位置的高度间的偏差来形成网格。
根据本发明的一实施例,所述多孔金属网格的孔截面至少为圆形、椭圆形、正方形、矩形及正多边形中的一种形状。
另外,在本发明中使用的所述多孔金属网格的材料可为银(Ag)、金(Au)、钯(Pd)或铂(Pt),但并不仅限于此,也可包括不被特定刻蚀液腐蚀刻蚀的金属。
以下说明本发明一方面的步骤(b)。
步骤(b)的特征之处在于利用从步骤(a)获取的多孔金属网格来湿法刻蚀GaAs基板并生成纳米线。根据本发明的一方面,上述步骤(b)中,对所述多孔金属网格直接施加外部偏压,使与多孔金属网格底部接触的GaAs基板上形成孔(h ),并在刻蚀液中湿法刻蚀GaAs基板,从而通过自上而下的方式生成纳米线。
即与多孔金属网格接触的GaAs基板随着刻蚀降低,未与多孔金属网格接触的网格形状部分刻蚀刻蚀依旧不会刻蚀,这样就可生成纳米线形态。
本发明中,从外部施加的能源包括直流电流、电压、脉冲电流及脉冲电压。
此时,通过调节施加的氧化电压或氧化电流、刻蚀液的浓度及刻蚀时间可控制获得的GaAs纳米线的纵横比(=长度\直径)。
根据本发明的一方面,上述步骤(b)中使用的刻蚀液包括氢氟酸(HF)、盐酸(HCl)或硝酸(HNO3)等可刻蚀GaAs的所有溶液,因此并不具体限定。另外,本发明中使用的刻蚀液包括用去离子水稀释或用去离子水和无水乙醇(C2H5OH)的混合液稀释的刻蚀液,但并不仅限于此。
在本发明中,对所述金属薄膜施加的偏压在0.5mA~50mA的电流(电流密度:2.5mA/cm2~250mA/cm2)或0.2V~10V的电压范围内。
另外,在本发明中,所述偏压也可对掺杂的GaAs基板施加。本发明通过从外部施加直流电流或电压诱导GaAs基板的电化学刻蚀来制造GaAs纳米线,具有可在不管预定掺杂浓度或更高的掺杂浓度下以及在预定掺杂浓度或更高时具有的电特性的掺杂类型制造出纳米线的优点,并且一般还具有无需额外的掺杂工艺的优点因为所需掺杂浓度的晶片可直接刻蚀并不需要进行单独的掺杂工艺就可制造出具有所需电特性的GaAs基板刻蚀。
在GaAs基板上制造出具有一种结晶取向的GaAs纳米线的刻蚀方向是可控的,从而使制造具有一种或多种结晶取向的GaAs纳米线阵列,和制造结晶取向周期性交替的锯形GaAs纳米线阵列,及制造多孔GaAs纳米线阵列成为可能。
也就是说,调节施加到金属薄膜上的直流电压或电流的尺寸及脉冲形态,可控制具有特定结晶取向的GaAs基板上制造出的纳米线的刻蚀方向,进而使制造具有一种结晶取向和一种或多种结晶取向的GaAs纳米线阵列,及制造结晶取向周期性交替的锯形GaAs纳米线阵列成为可能。
不仅如此,所述直流电流或电压并不施加在金属网格上,而是直接施加在GaAs基板上,使得制造多孔GaAs纳米线阵列成为可能。
【有益效果】
根据本发明提供的GaAs纳米线阵列的制造方法,不管GaAs基板的掺杂浓度及掺杂种类即可制造出GaAs纳米线阵列,因此无需额外的掺杂工艺,利用具有体现元件所需的掺杂浓度和种类的基板来直接制造出纳米线。
另外,不管基板的结晶取向是否与垂直对齐的GaAs纳米线不同,可制造出与基板具有相同取向的垂直对齐的GaAs纳米线阵列。
另外,控制从具有一种结晶取向的GaAs基板制造出的GaAs纳米线的刻蚀方向,从而使制造具有一种或多种结晶取向的GaAs纳米线阵列,和制造结晶取向周期性交替的锯形GaAs纳米线阵列,及制造多孔GaAs纳米线阵列成为可能。
与此同时,通过抑制侧面刻蚀来制造出具有均匀直径和高纵横比的纳米线,从而克服因普遍存在于III-V族半导体基板的侧面刻蚀效应导致的长度局限性。
附图说明
图1为本发明一实施例的GaAs半导体纳米线阵列的制造方法的流程图。
图2为示意本发明一实施例在去离子水表面生成聚苯乙烯纳米粒子单层阵列的截面图。
图3为示意本发明一实施例将聚苯乙烯纳米粒子单层阵列转移到GaAs基板上的方法的截面图。
图4为示意本发明一实施例减小聚苯乙烯纳米粒子尺寸的方法的截面图。
图5为示意本发明一实施例在GaAs基板上生成的聚苯乙烯纳米粒子单层阵列上沉积的金属薄膜的截面图。
图6为示意本发明一实施例去除聚苯乙烯的过程的截面图。
图7为示意本发明一实施例在GaAs基板上生成的多孔金属网格的扫描电子显微镜图(SEM)。
图8为示意本发明一实施例的GaAs纳米线阵列的制造方法的模式图。
图9为示意本发明一实施例通过湿法刻蚀n-型(100)GaAs基板制造的GaAs纳米线阵列的扫描电子显微镜照片。
图10为示意本发明一实施例通过湿法刻蚀n-型(111)GaAs基板制造的GaAs纳米线阵列的扫描电子显微镜照片。
图11为示意本发明一实施例通过湿法刻蚀p-型(100)GaAs基板制造的GaAs纳米线阵列的扫描电子显微镜照片。
图12为示意本发明一实施例通过湿法刻蚀n-型(100)GaAs基板制造的锯形GaAs纳米线阵列的扫描电子显微镜照片。
图13为示意本发明一实施例通过湿法刻蚀n-型(100)GaAs基板制造的多孔GaAs纳米线阵列的扫描电子显微镜照片。
具体实施方式
本发明可通过多种变换获得多种实施例,其中将特定实施例示例于图中并做详细的说明。但是,这并不限定本发明的特定实施方式,应当理解为本发明包括属于本发明的思想及技术范围的所有变换、等同及替代。在说明本发明时,如果对相关公知技术的具体说明会混淆本发明的要旨的话,省略其详细说明。
第一、第二等用语可用于说明多种组成要素,但是上述多种组成要素并不限定于上述用语。上述用语仅用于将一个组成要素区别于其他组成要素。
本申请中使用的用语仅为了说明特定实施例,对本发明并不做限定。除文中明确指定外,单数的表达方式里包含复数的表达。在本申请中,“包括”或“种”等用语仅为了指定说明书中记载的特征、数字、步骤、组成要素、部件或其结合的存在,应当理解为并不提前排除一个或以上的其他特征、数字、步骤、组成要素、部件或其结合的存在或者附加可能性。
以下结合附图更详细地说明本发明,在参考附图进行说明时,相同或对应的组成要素赋予相同的附图标号,并省略对其进行重复说明。
首先利用图1阐述本发明提供的GaAs半导体纳米线阵列的制造方法。
首先,在去离子水的表面上生成具有六方紧密堆积结构(最紧密堆积的情况)的聚苯乙烯粒子单层阵列,继而将聚苯乙烯粒子单层阵列转移到GaAs基板上,通过氧等离子处理收缩聚苯乙烯粒子,继而通过惯用沉积方法来沉积金属薄膜,去除聚苯乙烯粒子。继而,将多孔金属网格作为阳极(anode),施加偏压,利用刻蚀液刻蚀GaAs基板与金属薄膜之间的接触面,作为GaAs基板与金属薄膜的非接触部分的网格部分不会被刻蚀,从而以自上而下的方式生成GaAs纳米线。
以下结合图2至图6,说明图7中制造金属网格的步骤。
根据本发明提供的GaAs纳米线阵列的制造方法,首先要制作多孔金属网格。
为制造多孔金属网格,如图2所示,聚苯乙烯纳米粒子(20)以单层分散在去离子水(30)中。继而,如图3所示,浸渍GaAs基板(10)并提出,从而在GaAs基板(10)表面生成聚苯乙烯纳米粒子单层阵列(20)。即,图3中所示的在去离子水表面以紧密堆积结构对齐的聚苯乙烯纳米粒子单层阵列从图2中去离子水(30)表面生成的聚苯乙烯纳米粒子单层阵列(20)转移至了GaAs基板(10)。除此转移方式以外还可选择多种手段,例如,旋涂(spin coating)或刮涂(knife coating)等,但并不仅限于此。
其次,如图4所示,通过氧等离子处理转移至GaAs基板表面的聚苯乙烯纳米粒子单层阵列可缩小聚苯乙烯纳米粒子的直径。
继而,如图5所示,在对齐有聚苯乙烯纳米粒子单层阵列(20)的GaAs基板上沉积金属。沉积金属的方法例如,热沉积(thermal evaporation)、等离子沉积(plasma sputter)或电子束沉积(e-beam evaporation)。
其次,如图6所示,将GaAs基板浸渍在甲苯或三氯甲烷中,去除聚苯乙烯纳米粒子单层阵列(20),从而制造出多孔金属网格(40)。
图7为根据本发明一实施例制造的多孔金属网格(40)的扫描电子显微镜照片。多孔金属网格的孔(50)是纳米(nm)至微米(μm)尺寸,并可根据聚苯乙烯纳米粒子的尺寸或氧等离子处理的时间来调整孔的尺寸,并且孔截面可为圆形、椭圆形、正方形、矩形及正多边形等多种形状。
其次,将GaAs基板(10)表面制造的多孔金属网格(40)作为阳极(anode),施加外部偏压,在刻蚀液中湿法刻蚀GaAs基板,从而生成GaAs半导体纳米线(60)。
图8为根据本发明一实施例利用多孔金属网格(40)制造GaAs半导体纳米线(60)的方法的示意图。在湿法刻蚀时,将多孔金属网格(40)作为阳极并施加偏压,从GaAs基板(10)吸收电子氧化位于GaAs基板(10)底部的多孔金属网格(40),从而在金属底部生成氧化层,并且通过湿法刻蚀中使用的刻蚀液来刻蚀氧化层。持续执行这样的氧化膜层的生成及刻蚀的循环反应,GaAs基板(10)只有与多孔金属网格(40)接触的区域才被选择性刻蚀并去除。刻蚀过程中,用于阳极的多孔金属网格(40)残存于GaAs基板(10)表面,从而持续刻蚀位于多空金属网格底部的GaAs基板,未刻蚀的多孔金属网格部位以自上而下的方式生成纳米线。
由此,多孔金属网格(40)的贯通孔(50)的直径转移为GaAs纳米线(60)的缩减直径,根据多孔金属网格(40)上生成的贯通孔(50)的数量来控制GaAs基板(10)上生成的纳米线(60)的数量,并且多孔金属网格(40)的贯通孔(50)的阵列转移为GaAs基板(10)上生成的GaAs纳米线(60)的阵列。另外,根据GaAs基板(10)的刻蚀深度来调节GaAs半导体纳米线(60)的长度,通过调节湿法刻蚀的时间及外部施加偏压的大小容易调节GaAs基板(10)的刻蚀深度。
湿式刻蚀中使用的刻蚀液包括氢氟酸(HF)、硫酸(H2SO4)、盐酸(HCl)或硝酸(HNO3)。另外,刻蚀液包括用去离子水或去离子水和无水乙醇(C2H5OH)的混合液稀释的刻蚀液。
图9至图11示出从与GaAs基板(10)的类型和结晶取向无关的基板中制造出垂直对齐的GaAs半导体纳米线阵列的照片。
详细地,图9为利用上述方法湿法刻蚀n-型(100)GaAs基板(10)生成的垂直对齐的GaAs纳米线(60)阵列的扫描电子显微镜照片,可以看出纳米线生成均匀。
图10为利用上述方法湿法刻蚀n-型(111)GaAs基板(10)生成的垂直对齐的GaAs纳米线(60)阵列的扫描电子显微镜照片。
图11为利用上述方法湿法刻蚀p-型(100)GaAs基板(10)生成的垂直对齐的GaAs纳米线(60)阵列的扫描电子显微镜照片。
另外,根据本发明的一实施例,利用上述方法湿法刻蚀GaAs基板(10)的步骤中,对多孔金属网格(40)施加的偏压形式是可控的,从而可制造出除垂直对齐的GaAs半导体纳米线(60)阵列以外的多种结构及结晶取向的GaAs半导体纳米线(60)阵列。图12为利用上述方法湿法刻蚀n-型(100)GaAs基板(10)时,根据多孔金属网格(40)制造的锯形GaAs纳米线(60)阵列的扫描电子显微镜照片。
更进一步,本发明的另一实施例中,利用上述湿法刻蚀方法,通过对多孔金属网格(40)施加偏压来生成垂直对齐的GaAs纳米线(60)阵列后,对GaAs基板施加偏压可制造出具有多孔性表面的垂直对齐的GaAs半导体纳米线(60)阵列。图13为通过上述方法制造出的具有多孔性表面的垂直对齐的GaAs半导体纳米线(60)阵列的扫描电子显微镜照片。
以下通过实施例更详细地说明本发明。但是,这些实施例仅为了示意本发明,本发明的范围并不限定于这些实施例。
以下通过本发明的实施例具体说明本发明的实现例子。
【实施例1】图9的垂直型纳米线的生成方法。
GaAs基板的预处理
将iNexus公司的砷化镓n-型(100)基板、n-型(111)基板及p-型(100)基板依次用丙酮、乙醇和去离子水清洗并干燥以除去存在于基板表面的污染物,再利用氧等离子(氧:100sccm,等离子功率:300W,时间:20分钟)加大表面湿度。
聚苯乙烯纳米粒子单层阵列的制作
将Microparticles公司的聚苯乙烯纳米粒子(平均粒径250nm)与丙醇(C3H7OH)混合后,利用注射泵注射到装在烧杯中的去离子水的表面上,使具有六方紧密堆积结构的聚苯乙烯纳米粒子单层阵列均匀地形成在去离子水的表面上,再将预处理好的GaAs基板浸入后缓慢提出并使聚苯乙烯纳米粒子转移到GaAs基板上。
金属网格的制作
对转移到GaAs基板上以六方紧密堆积结构排列的聚苯乙烯纳米粒子单层阵列进行氧等离子处理(氧气:100sccm,等离子功率:300W,时间20分钟)以减少聚苯乙烯纳米粒子的尺寸,在制作纳米线阵列时沉积用作电极材料的钯(Pd)。沉积金属可通过等离子溅射(plasma sputtering)来实现。沉积金属后,将GaAs基板浸渍在甲苯中并进行超声波处理,从而完全去除GaAs基板表面对齐的聚苯乙烯纳米粒子并制造出多孔金属网格。
GaAs纳米线阵列的制作
将位于由上述方法获得的金属网格表面的GaAs基板浸渍在氢氟酸(HF)中,利用外部导线对金属网格施加电压或电流(0.5~50.0mA或0.2~10.0V),从而生成大面积垂直对齐的GaAs纳米线阵列。此时获得的GaAs纳米线的纵横比(=长度/直径)可通过调节施加的电压或电流、刻蚀液的浓度及刻蚀时间来控制。
【实施例2】图10的垂直型纳米线的生成方法
除将实施例1中的n-型(100)GaAs基板变更为n-型(111)GaAs基板之外,其他与上述实施例1相同。
【实施例3】图11的垂直型纳米线的生成方法
除将实施例1中n-型(100)GaAs基板变更为p-型(100)GaAs基板之外,其他与上述实施例1相同。
【实施例4】图12的垂直型纳米线的生成方法
使用与上述实施例1相同的n-型(100)GaAs基板并将电流的形式更换为脉冲电流之外,其他与上述实施例1相同。
【实施例5】图13的垂直纳米线的形成方法
采用与上述实施例1相同的方法生成垂直对齐的纳米线并将电流或电压的施加对象由金属网格更换为GaAs基板之外,其他与上述实施例1相同。
虽然以上详细记载了本发明内容的特定部分,但是本领域的技术人员应当理解,这些仅是举例说明,并不具体限定本发明的保护范围。本发明的保护范围由所附权利要求书及其等同范围来限定。
*对附图中主要部分的标记说明*
10:GaAs基板
20:聚苯乙烯纳米粒子单层阵列
30:去离子水
40:多孔金属网格
50:多孔金属网格的孔
60:GaAs半导体纳米线
本文用于企业家、创业者技术爱好者查询,结果仅供参考。