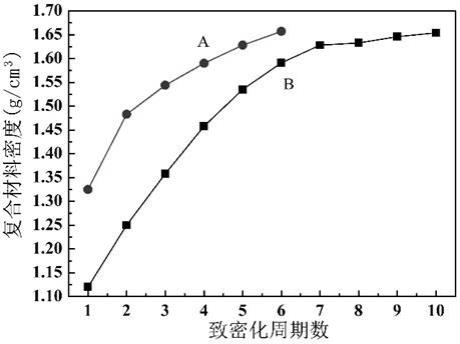
1.本发明属于耐高温透波复合材料制备技术领域,具体涉及一种石英纤维增强石英基复合材料及其制造方法,即一种sio
2f
/sio2复合材料及其制造方法。
背景技术:
2.耐高温透波材料是一类广泛用于导弹、空天飞机、运载火箭和可重复使用飞行器上的多功能介质材料,主要用于制造各种飞行器上的天线罩和天线窗结构件,其作用是实现电磁波的高效传输和有效通讯,保护内部制导系统,是集“透波
‑
承载
‑
放热”于一体的结构
‑
功能构件。
3.随着飞行器飞行速度的不断提高,对天线罩、窗所用材料的耐温性提出更高要求。飞行速度在4ma以上飞行器的天线罩、窗一般采用浇注熔融石英(scfs)或石英纤维增强石英基复合材料(sio
2f
/sio2)制造。其中,sio
2f
/sio2具有更好的韧性和抗热震性能,加工性优异,并能承受更高的热力联合载荷状态。
4.目前,虽然采用sio
2f
/sio2制造天线罩、窗已被广泛研究,但是由于其制造成本较高,应用推广受到限制。sio
2f
/sio2目前主要以溶胶
‑
凝胶工艺制造,其过程主要分为:
①
石英纤维预制件的成型;
②
纤维预制件的表面处理;
③
利用硅溶胶对纤维预制件进行浸渍;
④
溶胶的干燥
‑
凝胶化;
⑤
高温煅烧,以及步骤
③‑⑤
的重复循环以实现致密化。造成sio
2f
/sio2制造成本高的原因是致密化效率低,通常需要步骤
③‑⑤
循环十几次甚至几十次,并且中途要进行多次消除致密“壳层”的加工工序,制品才能达到所需密度。
5.目前,稳定储存的市售硅溶胶的固含量通常为≤25%,低的固含量导致单周期致密化效率低。韩爽(稀有金属材料与工程,韩爽,等,2009,38:458
‑
461.)等通过对市售硅溶胶常压下加热蒸发的方法,对硅溶胶进行浓缩,获得了固含量为30%
‑
37%的硅溶胶,进而先用低浓度硅溶胶浸渍纤维预制件,再用高浓度浸渍,并以微波干燥方式进行干燥和凝胶化,为获得密度大于1.65g/cm3的制品,致密化周期仍在10次以上。徐道新(3d sio
2f
/sio2复合材料的制备与性能研究,徐道新,硕士论文,2017.)等采用ph>9的碱性硅溶胶对编织件进行浸渍,虽然所用硅溶胶浓度达到40%
‑
50%,但碱性硅溶胶对石英纤维产生损伤,并且其钠离子含量较高(0.4%),会对产品透波性能产生影响。造成致密化效率低的另一原因是,随着致密化的进行,供sio2胶团向制品内部渗入的通道会逐渐变少,变窄。高浓度硅溶胶一般由大尺寸的胶团组成,sio2胶团颗粒越大越难继续向半成品内部渗透,密度很难继续增长,甚至达不到产品密度要求。
6.因此,开展石英纤维增强石英基复合材料的高效制造方法的研究很有必要。
技术实现要素:
7.本发明针对需要提高sio
2f
/sio2制备过程中致密化效率,从而降低sio
2f
/sio2产品制备成本的问题,提供了一种石英纤维增强石英基复合材料及其制造方法,即一种sio
2f
/sio2复合材料及其制造方法。
8.本发明的目的通过以下技术方案来实现:本发明采用减压旋转蒸发的方法对市售酸性硅溶胶进行浓缩,得到不同浓度的浓缩硅溶胶。相比于市售硅溶胶的浓度,本发明将浓缩硅溶胶按一定浓度范围划分为高浓度和中浓度两个档次,并通过工艺设计,在不同致密化周期中,采用不同浓度档次硅溶胶的组合浸渍方案,从而减少了制备过程中的致密化周期,实现了sio
2f
/sio2的高效制备。
9.一种石英纤维增强石英基复合材料的制造方法,具体包括以下步骤:1)纤维预制件的准备:制备纤维体积分数为35%
‑
50%的纤维预制件,将得到的纤维预制件采用多次丙酮浸泡,烘干去除纤维表面的浸润剂和杂质,备用;2)以固含量≤25%、粘度小于10mpa
·
s、激光粒度仪测出的平均胶团粒度≤50nm的市售酸性硅溶胶为原料,采用旋转蒸发仪进行减压浓缩,得到固含量为30%
‑
47%、半透明、室温下储存48小时后粘度仍≤50mpa
·
s的硅溶胶;3)将上步骤得到的固含量为30%
‑
47%的硅溶胶划分为高浓度硅溶胶和中浓度硅溶胶:40%<高浓度硅溶胶≤47%,粘度≤40mpa
·
s,激光粒度仪测出的平均胶团粒度≤350nm;30%≤中浓度硅溶胶≤40%,粘度≤20mpa
·
s,激光粒度仪测出的平均胶团粒度≤150nm;4)对步骤1)得到的纤维预制件进行“真空浸渍
‑
凝胶化
‑
烧成”的致密化循化操作,在真空浸渍工序中,前1
‑
2循环周期用高浓度硅溶胶浸渍,第3
‑
4循环周期用中浓度硅溶胶浸渍,以后用市售酸性硅溶胶浸渍;重复“真空浸渍
‑
凝胶化
‑
烧成”的致密化循化操作,直至制品密度满足要求,得到石英纤维增强石英基复合材料。
10.本发明中:步骤1)所述的制备纤维体积分数为35%
‑
50%的纤维预制件,是根据复材制品图纸,采用2d、2.5d、穿刺、铺层缝合、3d编织、缠绕等多种成型方式制备纤维体积分数为35%
‑
50%的纤维预制件。
11.步骤2)所述的市售酸性硅溶胶,其ph为2
‑
4。
12.步骤2)所述的采用旋转蒸发仪进行减压浓缩,是对旋转蒸发仪进行抽真空,并保持真空度为6
×
10
‑2mpa,对容器内硅溶胶进行水浴加热,加热温度为40℃
‑
60℃,容器旋转速度设定为50
‑
150转/分钟。
13.步骤4)所述的“真空浸渍
‑
凝胶化
‑
烧成”的致密化循化操作,操作步骤如下:a.将步骤1)得到的纤维预制件放入浸渍罐中,抽真空至6
×
10
‑2mpa,灌入不同浓度的硅溶胶,在真空条件下预制件在硅溶胶中浸泡2
‑
24h,停止抽真空,打开浸渍罐进气阀,放入空气至大气压,打开浸渍罐,取出浸渍后的纤维预制件,沥干多余的硅溶胶;b.将浸有硅溶胶的纤维预制件放入烘箱内,在200℃烘干2h,排除溶剂,并使硅溶胶凝胶化;c.将样品放入马弗炉中,在800℃下烧成1h。
14.本发明还涉及采用上述制造方法得到的一种石英纤维增强石英基复合材料。
15.与现有技术相比,本发明具有以下优点:1、本发明所述的一种石英纤维增强石英基复合材料的制造方法,采用的减压旋转蒸发的浓缩方式处理原料,设备简单,操作简单,原料广泛,无需进行化学合成或处理等复
杂操作,与现有技术中常压下的加热蒸发相比,减压旋转蒸发的效率提高500%以上,更适合sio
2f
/sio2复合材料工业化生产的需要。
16.2、本发明所述的一种石英纤维增强石英基复合材料的制造方法,在减压条件下,可以将蒸发温度降低,减轻蒸发过程中溶胶颗粒因受热导致的团聚,浓缩到相同浓度后,减压旋转蒸发所得固含量为30%
‑
47%的硅溶胶中胶团尺寸更小,储存稳定性更好。
17.3、本发明所述的一种石英纤维增强石英基复合材料的制造方法,随着致密化过程的进行,采用先高浓度硅溶胶,后低浓度硅溶胶的组合方案,提高致密化效率。在致密化过程前期,纤维预制件中空隙主要为纤维间搭接形成的,尺寸在几微米至几十微米,即使sio2胶团尺寸在几百纳米,胶团也能在负压作用下向预制件内部渗透;随着致密化过程的进行,纤维预制件中的通道变少、变窄,这时采用所含胶团尺寸较小的浓度较低的硅溶胶进行浸渍,可以保证胶团能够顺利地向内部渗透,避免难以制备高密度复合材料的问题。
附图说明
18.图1是本发明实施例1和对比例1制备sio
2f
/sio2过程中密度随致密化周期的变化曲线图(a是实施例1,b是对比例1);图2是本发明实施例2和对比例2制备sio
2f
/sio2过程中密度随致密化周期的变化曲线图(a是实施例2,b是对比例2);图3是采用常压加热蒸发和减压旋转蒸发两种浓缩方式得到的42%硅溶胶粘度随时间的变化的图(a是常压加热蒸发,b是减压旋转蒸发);图4是采用激光粒度仪测得固含量为25%市售酸性硅溶胶中胶团尺寸分布曲线图;图5是采用激光粒度仪测得固含量为42%硅溶胶常压加热蒸发后胶团尺寸分布曲线图;图6是采用激光粒度仪测得固含量为42%硅溶胶减压旋转蒸发后胶团尺寸分布曲线图;图7是采用激光粒度仪测得固含量为35%硅溶胶常压加热蒸发后胶团尺寸分布曲线图;图8是采用激光粒度仪测得固含量为35%硅溶胶减压旋转蒸发后硅溶胶中胶团尺寸分布曲线图。
具体实施方式
19.以下通过实施例进一步详细描述本发明,但这些实施例不应认为是对本发明的限制。下面将结合本发明实施例中的附图,对本发明实施例中的技术方案进行清楚、完整地描述,显然,所描述的实施例仅仅是本发明的一部分实施例,而不是全部的实施例。基于本发明中的实施例,本领域普通技术人员在没有做出创造性劳动前提下所获得的所有其他实施例,都属于本发明保护的范围。
20.另外,本发明各个实施例之间的技术方案可以相互结合,但是必须是以本领域普通技术人员能够实现为基础,当技术方案的结合出现相互矛盾或无法实现时应当认为这种技术方案的结合不存在,也不在本发明要求的保护范围之内。
21.实施例1:
一种石英纤维增强石英基复合材料的制造方法,包括以下步骤:1)纤维预制件的准备:采用2.5d编织的方式制备石英纤维平板作为预制件,其纤维体积分数为35%,长宽高分别为100mm
×
100mm
×
20mm;sio
2f
/sio2复合材料平板的密度要求为1.65g/cm3;将石英纤维预制件置于丙酮中浸泡,每次浸泡时间为10h,然后在烘箱内100℃进行烘干2h,去除纤维表面的浸润剂和杂质,重复“浸泡
‑
烘干”3次,每次浸泡更换新的丙酮;2)将2kg固含量为25%、ph=2、粘度小于10mpa
·
s的市售酸性硅溶胶,倒入旋转蒸发仪配套的烧瓶中,将烧瓶与旋转蒸发仪连接,抽真空至6
×
10
‑2mpa,检查气密性,旋转蒸发仪气密性正常条件下,接通低温冷却液循环泵,向旋转蒸发仪的冷凝器中通入
‑
10℃的乙醇,持续抽真空,开启旋转蒸发仪的水浴加热,将烧瓶中硅溶胶加热至45℃,同时,开启烧瓶旋转装置,旋转速度设定为50转/分钟,对硅溶胶进行浓缩。控制浓缩时间,分别获得固含量为42%的高浓度硅溶胶(粘度≤40mpa
·
s,激光粒度仪测出的平均胶团粒度≤350nm)和固含量为35%的中浓度硅溶胶(粘度≤20mpa
·
s,激光粒度仪测出的平均胶团粒度≤150nm),都是半透明、室温下储存48小时后粘度仍≤50mpa
·
s,备用;3)对步骤1)得到的纤维预制件进行“真空浸渍
‑
凝胶化
‑
烧成”的致密化循化操作,按照第1周期用固含量为42%高浓度硅溶胶浸渍;第2和第3循环周期用固含量为35%中浓度硅溶胶浸渍,以后用市售酸性硅溶胶(粘度≤10mpa
·
s,激光粒度仪测出的平均胶团粒度≤50nm)浸渍,直至制品密度满足要求,致密化操作步骤如下:a.将纤维预制件放入浸渍罐中,抽真空至6
×
10
‑2mpa,灌入不同浓度的硅溶胶,在真空条件下预制件在硅溶胶中浸泡8h,停止抽真空,打开浸渍罐进气阀,放入空气至大气压,打开浸渍罐,取出浸渍后的纤维预制件,沥干多余的硅溶胶;b.将浸有硅溶胶的纤维预制件放入烘箱内,在200℃烘干2h,排除溶剂,并使硅溶胶凝胶化;c.将样品放入马弗炉中,在800℃下烧成1h;至此,完成一个“真空浸渍
‑
凝胶化
‑
烧成”的致密化周期;按照所设计不同浓度硅溶胶组合浸渍方案,反复执行步骤a
‑
c,致密化过程进行到第6周期时,sio
2f
/sio2复合材料密度达到1.65 g/cm3,如图1中a所示。
22.实施例2:一种石英纤维增强石英基复合材料的制造方法,包括以下步骤:1)纤维预制件的准备:采用铺层缝合的方式制备石英纤维平板作为预制件,其纤维体积分数为50%,长宽高分别为100mm
×
100mm
×
20mm;sio
2f
/sio2复合材料平板的密度要求为1.75g/cm3;将石英纤维预制件置于丙酮中浸泡,每次浸泡时间为10h,然后在烘箱内100℃进行烘干2h,去除纤维表面的浸润剂和杂质,重复“浸泡
‑
烘干”3次,每次浸泡更换新的丙酮;2)将2kg固含量为20%、ph=4、粘度小于10mpa
·
s的市售酸性硅溶胶,倒入旋转蒸发仪配套的烧瓶中,将烧瓶与旋转蒸发仪连接,抽真空至6
×
10
‑2mpa,检查气密性,旋转蒸发仪气密性正常条件下,接通低温冷却液循环泵,向旋转蒸发仪的冷凝器中通入
‑
30℃的乙醇,持续抽真空,开启旋转蒸发仪的水浴加热,将烧瓶中硅溶胶加热至60℃,同时,开启烧瓶旋转装置,旋转速度设定为100转/分钟,对硅溶胶进行浓缩,分别获得固含量为47%的高浓度
硅溶胶(粘度≤40mpa
·
s,激光粒度仪测出的平均胶团粒度≤350nm)和固含量为30%的中浓度硅溶胶(粘度≤20mpa
·
s,激光粒度仪测出的平均胶团粒度≤150nm),都是半透明、室温下储存48小时后粘度仍≤50mpa
·
s,备用;3)对步骤1)得到的纤维预制件进行“真空浸渍
‑
凝胶化
‑
烧成”的致密化循化操作,按照第1周期和第2周期用固含量为47%的高浓度硅溶胶浸渍;第3和第4循环周期用固含量为30%的中浓度硅溶胶浸渍,以后用固含量为20%的市售酸性硅溶胶(粘度≤10mpa
·
s,激光粒度仪测出的平均胶团粒度≤50nm),直至制品密度满足要求,致密化操作步骤如下:a.将纤维预制件放入浸渍罐中,抽真空至6
×
10
‑2mpa,灌入不同浓度的硅溶胶,在真空条件下预制件在硅溶胶中浸泡15h,停止抽真空,打开浸渍罐进气阀,放入空气至大气压,打开浸渍罐,取出浸渍后的纤维预制件,沥干多余的硅溶胶;b.将浸有硅溶胶的纤维预制件放入烘箱内,在200℃烘干2h,排除溶剂,并使硅溶胶凝胶化;c.将样品放入马弗炉中,在800℃下烧成1h;至此,完成一个“真空浸渍
‑
凝胶化
‑
烧成”的致密化周期;按照所设计不同浓度硅溶胶组合,反复执行步骤a
‑
c,致密化过程进行到第9周期时,sio
2f
/sio2复合材料密度达到1.75 g/cm3,如图2中a所示。
23.实施例3:一种石英纤维增强石英基复合材料的制造方法,包括以下步骤:1)纤维预制件的准备:采用2d穿刺的方式制备石英纤维平板作为预制件,其纤维体积分数为45%,长宽高分别为100mm
×
100mm
×
20mm;sio
2f
/sio2复合材料平板的密度要求为1.70g/cm3;将石英纤维预制件置于丙酮中浸泡,每次浸泡时间为10h,然后在烘箱内100℃进行烘干2h,去除纤维表面的浸润剂和杂质,重复“浸泡
‑
烘干”3次,每次浸泡更换新的丙酮;2)将2kg固含量为23%、ph=3、粘度小于10mpa
·
s的市售酸性硅溶胶,倒入旋转蒸发仪配套的烧瓶中,将烧瓶与旋转蒸发仪连接,抽真空至6
×
10
‑2mpa,检查气密性,旋转蒸发仪气密性正常条件下,接通低温冷却液循环泵,向旋转蒸发仪的冷凝器中通入
‑
10℃的乙醇,持续抽真空,开启旋转蒸发仪的水浴加热,将烧瓶中硅溶胶加热至40℃,同时,开启烧瓶旋转装置,旋转速度设定为150转/分钟,对硅溶胶进行浓缩,分别获得固含量为45%的高浓度硅溶胶(粘度≤40mpa
·
s,激光粒度仪测出的平均胶团粒度≤350nm)和固含量为40%的中浓度硅溶胶(粘度≤20mpa
·
s,激光粒度仪测出的平均胶团粒度≤150nm),都是半透明、室温下储存48小时后粘度仍≤50mpa
·
s,备用;3)对步骤1)得到的纤维预制件进行“真空浸渍
‑
凝胶化
‑
烧成”的致密化循化操作,按照第1周期用固含量为45%高浓度硅溶胶浸渍;第2和第3循环周期用固含量为40%中浓度硅溶胶浸渍,以后用固含量为23%的市售酸性硅溶胶(粘度≤10mpa
·
s,激光粒度仪测出的平均胶团粒度≤50nm)浸渍,直至制品密度满足要求,致密化操作步骤如下:a.将纤维预制件放入浸渍罐中,抽真空至6
×
10
‑2mpa,灌入不同浓度的硅溶胶,在真空条件下预制件在硅溶胶中浸泡2h,停止抽真空,打开浸渍罐进气阀,放入空气至大气压,打开浸渍罐,取出浸渍后的纤维预制件,沥干多余的硅溶胶;b.将浸有硅溶胶的纤维预制件放入烘箱内,在200℃烘干2h,排除溶剂,并使硅溶
胶凝胶化;c.将样品放入马弗炉中,在800℃下烧成1h;至此,完成一个“真空浸渍
‑
凝胶化
‑
烧成”的致密化周期;按照所设计不同浓度硅溶胶组合,反复执行步骤a
‑
c,致密化过程进行到第8周期时,sio
2f
/sio2复合材料密度达到1.70g/cm3。
24.实施例4:一种石英纤维增强石英基复合材料的制造方法,包括以下步骤:1)纤维预制件的准备:采用3d编织的方式制备石英纤维平板作为预制件,其纤维体积分数为50%,长宽高分别为100mm
×
100mm
×
20mm;sio
2f
/sio2复合材料平板的密度要求为1.80g/cm3;将石英纤维预制件置于丙酮中浸泡,每次浸泡时间为10h,然后在烘箱内100℃进行烘干2h,去除纤维表面的浸润剂和杂质,重复“浸泡
‑
烘干”3次,每次浸泡更换新的丙酮;2)将2kg固含量为22%、ph=3、粘度小于10mpa
·
s的市售酸性硅溶胶,倒入旋转蒸发仪配套的烧瓶中,将烧瓶与旋转蒸发仪连接,抽真空至6
×
10
‑2mpa,检查气密性,旋转蒸发仪气密性正常条件下,接通低温冷却液循环泵,向旋转蒸发仪的冷凝器中通入
‑
30℃的乙醇,持续抽真空,开启旋转蒸发仪的水浴加热,将烧瓶中硅溶胶加热至50℃,同时,开启烧瓶旋转装置,旋转速度设定为80转/分钟,对硅溶胶进行浓缩,分别获得固含量为45%的高浓度硅溶胶(粘度≤40mpa
·
s,激光粒度仪测出的平均胶团粒度≤350nm)和固含量为32%的中浓度硅溶胶(粘度≤20mpa
·
s,激光粒度仪测出的平均胶团粒度≤150nm),都是半透明、室温下储存48小时后粘度仍≤50mpa
·
s,备用;3)对步骤1)得到的纤维预制件进行“真空浸渍
‑
凝胶化
‑
烧成”的致密化循化操作,按照第1周期和第2周期用固含量为45%高浓度硅溶胶浸渍;第3和第4循环周期用固含量为32%中浓度硅溶胶浸渍,以后用固含量为22%的市售酸性硅溶胶(粘度≤10mpa
·
s,激光粒度仪测出的平均胶团粒度≤50nm),直至制品密度满足要求,致密化操作步骤如下:a.将纤维预制件放入浸渍罐中,抽真空至6
×
10
‑2mpa,灌入不同浓度的硅溶胶,在真空条件下预制件在硅溶胶中浸泡24h,停止抽真空,打开浸渍罐进气阀,放入空气至大气压,打开浸渍罐,取出浸渍后的纤维预制件,沥干多余的硅溶胶;b.将浸有硅溶胶的纤维预制件放入烘箱内,在200℃烘干2h,排除溶剂,并使硅溶胶凝胶化;c.将样品放入马弗炉中,在800℃下烧成1h;至此,完成一个“真空浸渍
‑
凝胶化
‑
烧成”的致密化周期;按照所设计不同浓度硅溶胶组合,反复执行步骤a
‑
c,致密化过程进行到第10周期时,sio
2f
/sio2复合材料密度达到1.80g/cm3。
25.对比例1:一种石英纤维增强石英基复合材料的制造方法,和实施例1的区别在于所有致密化过程中均使用固含量为25%的市售酸性硅溶胶进行真空浸渍,具体包括以下步骤:1)纤维预制件的准备:采用2.5d编织的方式制备石英纤维平板作为预制件,其纤维体积分数为35%,长宽高分别为100mm
×
100mm
×
20mm;sio
2f
/sio2复合材料平板的密度要求为1.65g/cm3;
将石英纤维预制件置于丙酮中浸泡,每次浸泡时间为10h,然后在烘箱内100℃进行烘干2h,去除纤维表面的浸润剂和杂质,重复“浸泡
‑
烘干”3次,每次浸泡更换新的丙酮;2)采用固含量为25%、ph=2、粘度小于10mpa
·
s的市售酸性硅溶胶为原料对步骤1)得到的纤维预制件进行“真空浸渍
‑
凝胶化
‑
烧成”的致密化循化操作,直至制品密度满足要求,致密化操作步骤如下:a.将纤维预制件放入浸渍罐中,抽真空至6
×
10
‑2mpa,灌入不同浓度的硅溶胶,在真空条件下预制件在硅溶胶中浸泡8h,停止抽真空,打开浸渍罐进气阀,放入空气至大气压,打开浸渍罐,取出浸渍后的纤维预制件,沥干多余的硅溶胶;b.将浸有硅溶胶的纤维预制件放入烘箱内,在200℃烘干2h,排除溶剂,并使硅溶胶凝胶化;c.将样品放入马弗炉中,在800℃下烧成1h;至此,完成一个“真空浸渍
‑
凝胶化
‑
烧成”的致密化周期;为制备密度达到1.65g/cm3的sio
2f
/sio2复合材料,需要进行10个“真空浸渍
‑
凝胶化
‑
烧成”的致密化循环周期,其sio
2f
/sio2复合材料密度随致密化周期次数的变化曲线见图1的b。
26.表明:实施例1比对比例1减少了4个循环周期,提高了sio
2f
/sio2复合材料的制备效率,降低了成本。
27.对比例2:一种石英纤维增强石英基复合材料的制造方法,和实施例2的区别在于所有致密化过程中均使用固含量为20%的市售酸性硅溶胶进行真空浸渍,具体包括以下步骤:1)纤维预制件的准备:采用铺层缝合的方式制备石英纤维平板作为预制件,其纤维体积分数为50%,长宽高分别为100mm
×
100mm
×
20mm;sio
2f
/sio2复合材料平板的密度要求为1.75g/cm3;将石英纤维预制件置于丙酮中浸泡,每次浸泡时间为10h,然后在烘箱内100℃进行烘干2h,去除纤维表面的浸润剂和杂质,重复“浸泡
‑
烘干”3次,每次浸泡更换新的丙酮;2)采用固含量为25%、ph=2、粘度小于10mpa
·
s的市售酸性硅溶胶为原料对步骤1)得到的纤维预制件进行“真空浸渍
‑
凝胶化
‑
烧成”的致密化循化操作,直至制品密度满足要求,致密化操作步骤如下:a.将纤维预制件放入浸渍罐中,抽真空至6
×
10
‑2mpa,灌入不同浓度的硅溶胶,在真空条件下预制件在硅溶胶中浸泡8h,停止抽真空,打开浸渍罐进气阀,放入空气至大气压,打开浸渍罐,取出浸渍后的纤维预制件,沥干多余的硅溶胶;b.将浸有硅溶胶的纤维预制件放入烘箱内,在200℃烘干2h,排除溶剂,并使硅溶胶凝胶化;c.将样品放入马弗炉中,在800℃下烧成1h;至此,完成一个“真空浸渍
‑
凝胶化
‑
烧成”的致密化周期;为制备密度达到1.75g/cm3的sio
2f
/sio2复合材料,需要进行16个“真空浸渍
‑
凝胶化
‑
烧成”的致密化循环周期,其sio
2f
/sio2复合材料密度随致密化周期次数的变化曲线见图2的b。
28.表明:实施例2比对比例2减少了7个循环周期,提高了sio
2f
/sio2复合材料的制备
效率,降低了成本。
29.对比例3:为表明与常压加热蒸发相比,减压旋转蒸发是更有效的硅溶胶浓缩方法。本对比例采用常压加热蒸发方式,制备实施例1中所获得的固含量为42%和35%的浓缩硅溶胶,并对浓缩效率,浓缩硅溶胶的稳定性,以及浓缩硅溶胶中胶团尺寸分布进行比较。
30.本对比例中,采取常压加热蒸发的方式获得浓缩硅溶胶,即将盛有固含量为25%的市售酸性硅溶胶的烧杯置于水浴锅中加热,加热温度为70℃,同时,将搅拌器放入硅溶胶中进行搅拌,搅拌速率为100转/分钟。
31.表1 两种硅溶胶浓缩方法对比:表1中列出了两种浓缩方式获得的42%硅溶胶的粘度和过程中溶剂蒸发速率。表明减压旋转蒸发的浓缩效率更高,且产物粘度较低,更适于后续浸渍的需要。
32.图3 为两种浓缩方式所得42%硅溶胶粘度随时间的变化,说明减压旋转蒸发所得浓缩硅溶胶具有更高的稳定性,这利于后续对纤维预制件长时间真空浸渍的需要。
33.表2 两种硅溶胶浓缩方法对比:图4
‑
图8和表2给出了两种浓缩方式所得固含量为42%和35%硅溶胶的胶团尺寸分布,该结果表明减压旋转蒸发所得浓缩硅溶胶中的胶团尺寸更小,更小的胶团利于其向纤维预制件内部渗透,避免复材制品在厚度方向上产生过大的密度梯度。
34.通过实施例和对比例的基本性能的比较,说明实施例的制造方法明显优于对比例。
再多了解一些
本文用于企业家、创业者技术爱好者查询,结果仅供参考。