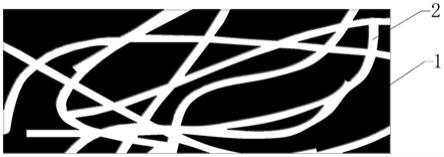
1.本发明涉及煤矸石综合利用技术领域,特别涉及一种地聚物轻质发泡材料的制备工艺。
背景技术:
2.目前我国煤研石综合利用的途径主要有煤研石发电、制作建筑材料、从煤研石中回收有用矿物、煤研石生产复合肥料等。但经过多年的实践证明煤矸石发电对环境有相当的污染,不利于环保;回收有价值的矿物会产生新的污染源,在某些地区因回收矿物所产生的性的污染源还属危废,对环境破坏程度更大,显然是得不偿失的;制作建筑材料因其中还有部分c以及c化合物导致所制备的建筑材料性能不高,应用场景有限,消纳量较低,社会效益不显著;至于生产复合肥,因煤矸石主题原材料中所含元素波动较大,生产工艺复杂,综合成本较高,使用量也较少;其他的领域如矿区回填等技术方案虽然也能消纳大量的煤矸石但附加值不高,经济效益不显著。
3.基于上述现状,目前市场上急需一种能打通全产业链、技术水平较高、综合利用率高、可大规模消纳煤矸石同时还具有较高附加值的技术应用,可产生较高的经济效益和社会效益的成熟技术。
4.对煤矸石化学成分进行分析可以发现去除可烧蚀成分后的产物具有较大的应用于绿色建筑材料的应用前景,基于此,提出了煤矸石可控热处理后制备绿色建筑材料(以地聚物为主要原材料)的综合利用方案和技术。利用热处理后的煤矸石制备以地聚物为主体材料的绿色建筑材料可广泛应用于装配式建筑、绿色装饰材料、防火保温建筑材料等领域。
技术实现要素:
5.本发明的目的是提供一种地聚物轻质发泡材料的制备工艺,该材料最终会形成不同于常见胶凝材料所制备的轻质材料,具有优良的机械性能和耐酸碱、耐火、耐高温等性能,成型材料耐久性优异、抗碳化优异等性能;在材料成型过程中该方法表现出成型快、生产制备过程中绿色环保、节能高效、相比制备胶凝材料可有效降低碳排放仅为普通胶凝材料的1/3~1/5,有利于大幅度降低建筑材料生产端的碳排放,有利于社会整体碳中和目标的尽快达成。
6.本发明的上述技术目的是通过以下技术方案得以实现的:一种地聚物轻质发泡材料的制备工艺,包括以下步骤:
7.s1:将热处理后的煤矸石中加入0.3
‑
0.5%的三乙醇胺进行粉磨后,得到煤矸石粉末;
8.s2:备发泡沫的制备:采用煤矸石粉末:发泡剂与助剂:碱金属氧化物:碱金属硅酸盐:水=100:0.6
‑
8:2
‑
12:6
‑
18:25
‑
60的比例进行混合,形成备发泡料;
9.s3:将s2中的备发泡料进行发泡成型,得到地聚物轻质发泡材料。
10.本发明的进一步设置为:所述步骤s2中,所述备发泡沫的配合比为:煤矸石粉末:
氢氧化钾:硅酸钠:水=100:8:21:0.8,混合均匀后得到备发泡沫。
11.本发明的进一步设置为:所述步骤s3中,按照备发泡沫:轻质填料=100:20的比例在搅拌机中进行混合均匀后,在搅拌条件下倒入模具中室温条件下成型,得到吸音降噪混凝土砌块。
12.本发明的进一步设置为:所述步骤s3中,按照备发泡料:铝粉=1:0.05的比例混合均匀后倒入模具进行发泡。发泡稳定后切块得到加气混凝土砌块。
13.本发明的进一步设置为:所述步骤s3中,按照备发泡料:双氧水:二氧化锰=100:10:2的比例混合均匀后再微波场中进行发泡及成型,微波功率为100%,微波时间为5min,成型后得到的发泡材料为泡沫陶瓷。
14.本发明的进一步设置为:所述步骤s3中,按照备发泡料:纤维素纤维:二氧化锰=100:3.5:0.5的比例混合均匀后放入微波场中进行微波处理,微波功率为70
‑
90%,微波场内保持真空度为0.03mpa,微波处理时间为16min,成型后的发泡材料为吸音板材。
15.本发明的进一步设置为:所述步骤s2中,按照煤矸石粉末:挤出剂助剂:氢氧化钾:硅酸钠:尾矿粉:水=100:0.008:10:26:150:50的比例混合均匀后通过炼泥
‑
真空炼泥
‑
挤出成型的过程加工成型形成a料,将挤出料a料与b料进行复合,所述b料组分为:煤矸石粉:硅酸钾:铝矾土尾矿粉:碳酸钙:二氧化锰:水=100:26:100:15:5:30的比例混合均匀,复合后上部为b料,下部为a料,将复合好的ab料放入微波场中进行成型加工,微波成型时间为40min,微波功率为85%,成型后的发泡材料为吸音降噪材料。
16.本发明的进一步设置为:所述步骤s2中,按照煤矸石粉末:挤出剂助剂:氢氧化钠:硅酸钾:硅灰:尾矿粉:水=100:0.012:10:12:8:120:30的比例混合均匀后通过炼泥
‑
真空炼泥
‑
注射成型的过程进行加工,并在微波条件下在注射成型模具中注射成型,微波时间为45min,微波强度为90%。
17.本发明的进一步设置为:所述纤维素纤维包括pva纤维、聚丙烯纤维、玄武岩纤维、耐碱玻璃纤维中的一种。
18.本发明的进一步设置为:所述轻质填料包括膨胀珍珠岩、eps颗粒、聚氨酯中空微球、中空玻璃微球中的一种
19.本发明的有益效果是:。
20.1、本发明的目的是提出一种利用热处理与机械活化后的煤矸石粉体材料用于制备一种地聚物轻质发泡材料,该材料最终会形成不同于常见胶凝材料所制备的轻质材料,具有优良的机械性能和耐酸碱、耐火、耐高温等性能,成型材料耐久性优异、抗碳化优异等性能;在材料成型过程中该方法表现出成型快、生产制备过程中绿色环保、节能高效、相比制备胶凝材料可有效降低碳排放仅为普通胶凝材料的1/3~1/5,有利于大幅度降低建筑材料生产端的碳排放,有利于社会整体碳中和目标的尽快达成。
21.2、使用煤矸石热处理后的粉体作为主体材料制备轻量化的地聚物材料,同时采用微波辅助加工的方法提高加工效率、提升产品品质与性能,并利用吸波物质吸收微波迅速产生高温的特点对易分解的纤维质物质进行分解,以产生利于吸声降噪的内部孔道网络系统。
22.3、本发明的板材可以通过浇筑、挤出、注射、模压等方式成型,在成型过程中可通过添加有机无机纤维、有机无机轻质填料等方法来调整功能与力学性能的协调。有机物纤
维可提高抗压、抗折强度、弯曲强度、弹性模量等力学强度的纤维;有机无机轻质填料用以调整保温隔热性能或吸音降噪性能的有机无机材料。同样也可以通过挤出、注射等工艺在微发泡的内腔中直接成型具有吸音降噪能力的结构形态或具有保温隔热性能的微细中空结构形态。
23.4、在本发明的技术方案中尤其需要重点说明的是具有开孔结构的孔道网络系统,首先,该系统是通过加入掺杂了吸波物质的纤维质材料,而纤维质材料在吸波物质的作用下在微波场中发生分解以气体的方式逸出,最终在材料中形成纵横交错的孔道网络;其次纤维质材料分解逸出的过程与材料骨架硬化成型的过程是同步的,否则不能形成孔道;再次,吸波物质的存在一方面使纤维质材料发生分解,另一方面促进地聚物材料在低温条件下发生低温陶瓷的合成反应;最后,开孔型的孔道系统可以将中高频、低频类声波增加消耗长度与时间,大幅度提高吸音降噪的效果,便于实现薄层吸音结构。
24.5、本发明中使用微波加热掺杂物料分解的同时进行低温陶瓷的合成过程能够通过调整微波强度以及掺杂物料的比例来进行准确调整的,例如同样采用掺杂了二氧化锰的纤维素纤维,当比例为0.2%(与地聚物材料的质量比),微波强度为100%,微波时间为4min条件下,所得产物为具有闭孔结构的保温隔热材料,而比例为3%(与地聚物质量比)、微波强度85%、微波时间为15min条件下所得产物为具有孔道直径为69 160μm的开孔型微细孔道系统,且该系统内部纵横交错,经检测其吸音效果十分明显。
25.本发明采用新颖的加工方法与工艺,实现了结构性吸音降噪系统与材料型吸音降噪系统或材料型保温隔热系统的结合,进而实现了多功能复合材料,可应用于多个领域以及不同的使用场合。在利用地聚物材料可低温合成陶瓷类材料的特点基础上合成制备了具有吸音降噪功能的轻质陶瓷材料和具有保温隔热性能的轻质陶瓷材料,可应用于交通、航天等高科技领域,具有相当高的附加值。
附图说明
26.为了更清楚地说明本发明实施例中的技术方案,下面将对实施例描述中所需要使用的附图作简单地介绍,显而易见地,下面描述中的附图仅仅是本发明的一些实施例,对于本领域普通技术人员来讲,在不付出创造性劳动的前提下,还可以根据这些附图获得其他的附图。
27.图1是本发明实施例四中的成型截面结构示意图。
28.图2是本发明实施例四吸音降噪测试结果图。
29.图3是本发明实施例五a料成型截面结构示意图。
30.图4是本发明实施例五复合ab料成型截面结构示意图。
31.图5是本发明实施例五吸音降噪测试结果图。
32.图6是本发明实施例六注射成型模具局部结构示意图。
33.图中,1、物料;2、孔道结构;3、a料;4、b料;5、注射成型模具。
具体实施方式
34.下面将结合具体实施例对本发明的技术方案进行清楚、完整地描述。显然,所描述的实施例仅仅是本发明的一部分实施例,而不是全部的实施例。基于本发明的实施例,本领
域普通技术人员在没有作出创造性劳动前提下所获得的所有其他实施例,都属于本发明保护的范围。
35.在实施例中,使用经微波热处理的煤矸石且二次粉磨后的比表面积为500m2/kg的粉末,配合比的比例为:煤矸石粉末:氢氧化钾:硅酸钠:水=100:8:21:0.8,以前述比例配置好“备发泡料”,后继.实施例中采用该“备发泡料”通过不同工艺以及添加轻质填料来实现材料的轻量化。
36.实施例一:将上述得到“备发泡料”与3m的中空玻璃微珠按照100:20的比例在搅拌机中进行混合,混合均匀后在搅拌条件下倒入模具中室温条件下成型,成型时间28天,模具尺寸为300*300*20。依据gb/t 5486
‑
2008《无机绝热制品试验方法》对其性能进行测试,具体测试数据如下:
37.表1
[0038][0039]
实施例二:将上述得到的“备发泡料”与铝粉按照1:0.05的比例混合均匀后倒入模具后进行发泡,发泡稳定后切割成标准样块进行测试,得到表2的检测结果:
[0040]
表2
[0041][0042]
由以上结果可以看出,该实施例1
‑
2产品可用于制备高性能加气混凝土砌块而无需使用蒸压设备以及蒸汽锅炉,提高了加气混凝土砌块生产的安全性,降低了生产的排放,节省了投资,提高了经济效益与环境效益。
[0043]
实施例三:将上述得到的“备发泡料”按照物料:双氧水:二氧化锰=100:10:2的比例混合均匀后在微波场中进行发泡及成型,微波功率为100%,微波时间为5min,成型过程中模具带有自锁保压装置以防止发泡过激导致物料溢出,成型后在室温条件下放置养护3天。测试依据为gb/t 33500
‑
2017《外墙外保温泡沫陶瓷》,相应的测试结果见下表3:
[0044]
表3
[0045][0046]
由实施例三可以看出,该实施例产品可用于制备泡沫陶瓷,而对比实施例的工艺与泡沫陶瓷的常见艺可以看出,实施例的制备工艺远比常规泡沫陶瓷的制备工艺要简单、效率更高、更节能也更环保,节约了大量的陶瓷烧结时间,间接节省了产生大量的能源,降低了碳排放。
[0047]
实施例四:上述“备发泡料”与掺杂二氧化锰的纤维素纤维按照100:4(纤维素纤维:二氧化锰=7:1)的比例混合均匀后放入微波场中进行微波处理,微波功率为70
‑
90%根据温度进行调整,微波场内保持真空度为0.03mpa,微波处理时间为16min,成型后的内部结构如图1所示,图1中的白色部分为孔道结构,成型后进行吸音降噪测试结果如图2所示,
[0048]
实施例五:采用比表面积为500m/kg热处理并二次粉磨后的煤矸石粉末;将上述粉末与挤出助剂、氢氧化钾、硅酸钠、尾矿粉、水按照100:0.008:10:26:150:50的比例混合均匀后通过炼泥
‑
真空炼泥
‑
挤出成型的过程加工成型为a料,成型后的截面结构示意图如图3所示,图中灰色部分为上述物料,白色部分为中空结构,将a料挤出成型后与b料进行复合,b料组分为比表面积为500m2/kg的热处理并经二次粉磨的煤矸石粉100份、硅酸钾(模数=1.2)26份、铝矾土尾矿粉100份、掺杂了二氧化锰的碳酸钙(碳酸钙:二氧化锰=15::5)20份、水30份,将上述复合好的ab料放入微波场中进行成型加工,加工过程中使用微波加热,提高生产效率,微波成型加热时间为40min,微波功率为85%,复合后的ab料的界面示意图如4所示,上部分为b料,下部分为挤出结构a料,成型后放置至室温后进行吸音测试,测试结果如图5所示:
[0049]
在微波加热成型的条件下,ab料同时实现了低温陶瓷的合成过程,不仅在挤出结构中形成了尖劈结构复合空腔结构以实现结构吸音,同时复合了类泡沫陶瓷的材料,其中大量通孔实现了吸音降噪,类陶瓷的结构保证了主体结构的强度,最终得到了如图4所示的刚性吸音降噪材料。
[0050]
通过微波成型的方式实现了地聚物低温合成陶瓷的过程,同时实现了结构型吸音降噪材料与材料型吸音降噪材料的复核,通过本实施例予以展示了这一创新点。该方式大大节省了成型养护时间,节约了能源,提高了生产效率,大幅度提高了强度、吸声量、耐火极限以及降低了容重,得到了轻质高强的高性能吸音降噪材料。
[0051]
实施例六:采用比表面积为500m/kg热处理并二次粉磨后的煤矸石粉末;将上述粉末与挤出助剂、氢氧化钠、硅酸钾、硅灰、尾矿粉、水按照100:0.012:10:12:8:120:30的比例混合均匀后通过炼泥
‑
真空炼泥
‑
注射成型的过程加工成型,成型后的结构根据需要采用市面上认可的刚性吸音降噪结构即可。根据图6所设计结构设计注射成型模具,而后在微波条件下进行注射成型,微波时间为45min,微波强度为90%,
[0052]
如图6注射成型吸音板内部带有空腔,形成了类陶瓷刚性结构型吸音板,可用于内部装饰用,具有性能优异、防火防潮、吸音降噪等特点,加工过程中采用微波加热成型的低温陶瓷,远低于陶瓷加工动辄>900℃的环境和条件,使得对类似材料进行其他方面的改性
(如有机化改性)成为可能,最终制备的轻质高强、防火隔音的材料可用于军事、航天、防护等领域。
再多了解一些
本文用于企业家、创业者技术爱好者查询,结果仅供参考。