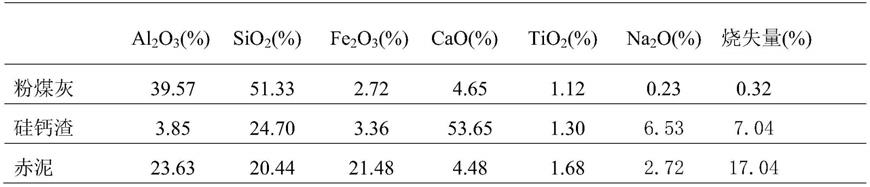
1.本发明涉及一种陶粒及其制备方法,具体涉及一种利用高铝粉煤灰制备的陶粒及其制备方法。
背景技术:
2.陶粒是一种人工轻集料,具有保温隔热性好、堆积密度低、耐高温耐腐蚀性好,抗冻等特点,被广泛应用于建材、水处理和环境等领域。传统的陶粒制备主要用到的是粘土和页岩,但是这两种矿物都属于自然资源,大量开采会对环境造成极大破坏。而且粘土和页岩制备的陶粒一般质量较轻,强度较低。
3.粉煤灰是电厂煤粉中粘土矿物随煤粉在锅炉中燃烧,经分解、烧结、熔融和冷却后形成的粉体物质。我国每年约产生5亿吨粉煤灰,粉煤灰大量堆存会带来严重的环境问题。
4.其中,内蒙古地区的粉煤灰具有高铝、高硅、低铁的特点,特别是内蒙古中西部地区,由于特殊的地质背景,该地区粉煤灰中氧化铝的含量均在35%以上,部分能达到50%,属于高铝粉煤灰。此类粉煤灰密度低、氧化铝含量高、储量丰富且活性较高,能够将其用于制备高强陶粒。
5.一般氧化铝含量在50%左右的高铝粉煤灰常被用来提取氧化铝,剩余残渣就则被称为硅钙渣,硅钙渣中含有氧化钙、氧化钠等,将硅钙渣与高铝粉煤灰掺杂进行陶粒的烧制时,有益于降低陶粒的烧结温度。此外,该地区周边还有堆积有铝土矿提取氧化铝排出的赤泥残渣,赤泥中氧化铁的含量比较高,且有一定的粘结性,能够将其用于对高铝粉煤灰造粒有益。如何粉煤灰、硅钙渣和赤泥较好的粘结成球是利用粉煤灰为主要原料生产高强陶粒亟待解决的问题。
技术实现要素:
6.本发明的目的在于提供一种利用高铝粉煤灰制备的陶粒及其制备方法,以解决现有技术中没有将粉煤灰、硅钙渣和赤泥用于制备高强度陶粒方法的技术问题。
7.为实现上述目的,本发明提供了以下技术方案:
8.本发明提供的一种利用高铝粉煤灰制备的高强陶粒,其特征在于:包括按照质量百分数计的70
‑
80%高铝粉煤灰、5
‑
15%赤泥和5
‑
15%硅钙渣。
9.进一步的,所述高铝粉煤灰各化学成分质量百分数如下:al2o3≥38:、sio2≥50%、fe2o3≥2%和cao≥2%。
10.进一步的,所述赤泥各化学成分质量百分数如下:20
‑
25%al2o3、15
‑
25%sio2、18
‑
25%fe2o3、1
‑
4%na2o和4
‑
6%cao;所述赤泥为铝土矿拜耳法提取氧化铝后剩余的残渣,且烧失量为15
‑
20%。
11.进一步的,所述硅钙渣各化学成分质量百分数如下:2.5
‑
6%al2o3、20
‑
30%sio2、1
‑
5%fe2o3、2
‑
10%na2o和45
‑
60%cao;所述硅钙渣为粉煤灰碱石灰烧结法提取氧化铝后剩余的残渣,且烧失量为5
‑
15%。
12.进一步的,选用的所述赤泥粒度<150μm,选用的所述硅钙渣粒度<150μm,所述粉煤灰粒度要求45μm筛余量小于45%。
13.本发明提供的一种利用高铝粉煤灰烧制权利要求1
‑
5所述高强陶粒的制备方法,其特征在于,包括以下步骤:
14.s1.预处理,将赤泥、硅钙渣进行处理,使其含水率降低至5%及以下;分别对赤泥、硅钙渣进行研磨并过筛;
15.s2.混合,将步骤s1中研磨并过筛后的赤泥、硅钙渣按配比与粉煤灰进行混合,并将混合的原料放入混料机混合均匀;
16.s3.制球,将混合好的原料加入圆盘造粒机中进行喷水造粒,制成5
‑
20mm的生料球体,且控制生料球的水分为10
‑
18%;
17.s4.烧制,将生料球进行高温烧制,从室温升温到500℃,保温10
‑
30min后,再逐渐升温到1150
‑
1280℃,保温5
‑
30min,总烧结时间为1
‑
4h,将烧制后的陶粒缓慢冷却到室温,得到成品。
18.进一步的,步骤s4中所述由室温升温到500℃和再升温到1150
‑
1280℃的时间均为30
‑
60min。
19.进一步的,包括以下步骤:
20.s1.预处理,将赤泥、硅钙渣进行处理,使其含水率降低至5%及以下;分别对赤泥、硅钙渣进行研磨并过筛;
21.s2.混合,将步骤s1中研磨并过筛后的赤泥、硅钙渣按配比与粉煤灰进行混合,并将混合的原料放入混料机混合均匀;
22.s3.制球,将混合好的原料加入圆盘造粒机中进行喷水造粒,制成5
‑
20mm的生料球体,且控制生料球的水分为10
‑
18%;
23.s4.烧制,将生料球进行高温烧制,从室温升温到500℃,升温60min,保温30min,再从500℃升温到800℃,最后从800℃升温到1230℃,升温时间60min,保温30min,将烧制后的陶粒缓慢冷却到室温,得到成品。
24.进一步的,包括以下步骤:
25.s1.预处理,将赤泥、硅钙渣进行处理,使其含水率降低至5%及以下;分别对赤泥、硅钙渣进行研磨并过筛;
26.s2.混合,将步骤s1中研磨并过筛后的赤泥、硅钙渣按配比与粉煤灰进行混合,并将混合的原料放入混料机混合均匀;
27.s3.制球,将混合好的原料加入圆盘造粒机中进行喷水造粒,制成5
‑
20mm的生料球体,且控制生料球的水分为10
‑
18%;
28.s4.烧制,将生料球进行高温烧制,从室温升温到500℃,保温20min后,再从500℃升温到800℃,最后从800℃升温到1200℃,升温时间60min,保温20min,将烧制后的陶粒缓慢冷却到室温,得到成品。
29.基于上述技术方案,本发明实施例至少可以产生如下技术效果:
30.(1)本发明提供的一种利用高铝粉煤灰制备的陶粒及其制备方法,选用高铝粉煤灰为主要原料,充分利用其氧化铝含量高的优点制备出品质较好的高强陶粒,通过gbt17431.1
‑
2010《轻集料及其实验方法》中对轻集料的相关评估指标,对制备出的高强陶
粒进行了测试,制备出的高强陶粒强度达到12
‑
20mp,吸水率小于6%。
31.(2)本发明提供的一种利用高铝粉煤灰制备的陶粒及其制备方法,利用硅钙渣和赤泥为辅料,充分利用硅钙渣和赤泥辅料中的氧化铁和氧化钠的助熔作用,降低高强度陶粒的烧结温度。同时,利用硅钙渣和赤泥辅料具有的良好塑性,在造粒制作陶粒生料球过程中能有效的提高生料球的强度。
32.(3)本发明提供的一种利用高铝粉煤灰制备的陶粒及其制备方法,高铝粉煤灰的用量达到70%
‑
80%,不仅降低了粉煤灰的处理成本,解决了粉煤灰的堆存问题,而且为粉煤灰处理利用提供了一条新思路。同时配料中的硅钙渣和赤泥均属固废。该方法除了作为目标产物的高强度陶粒,提高了高强度陶粒制备过程中环境有益性。在生产出高强陶粒的同时,消耗了固废,环境效益显著。
具体实施方式
33.为使本发明的目的、技术方案和优点更加清楚,下面将对本发明的技术方案进行详细的描述。显然,所描述的实施例仅仅是本发明一部分实施例,而不是全部的实施例。基于本发明中的实施例,本领域普通技术人员在没有做出创造性劳动的前提下所得到的所有其它实施方式,都属于本发明所保护的范围。
34.实施例1
35.1.1原料
36.实施例1制备的高强度陶粒各原料质量百分数分别为:80%粉煤灰、12%赤泥、8%硅钙渣。
37.所述赤泥为铝土矿拜耳法提取氧化铝后剩余的残渣,且烧失量为15
‑
20%;所述硅钙渣为粉煤灰碱石灰烧结法提取氧化铝后剩余的残渣,且烧失量为5
‑
15%;赤泥粒度<150μm,选用的所述硅钙渣粒度<150μm,所述粉煤灰粒度要求45μm筛余量小于45%。
38.选取的高铝粉煤灰、赤泥和硅钙渣原料的各化学成分质量百分数如表1.
39.表1原料的各化学成分质量百分数
[0040][0041]
1.2制备方法
[0042]
s1.预处理,将赤泥、硅钙渣进行烘干处理,使其含水率降低至5%及以下;分别将赤泥、硅钙渣采用球磨机进行研磨,并将磨细后的赤泥、硅钙渣过100目筛;
[0043]
s2.混合,将步骤s1中研磨并过筛后的赤泥、硅钙渣按配比与粉煤灰进行混合,并将混合的原料放入混料机混合均匀;
[0044]
s3.制球,将混合好的原料加入圆盘造粒机中进行喷水造粒,制成5
‑
20mm的生料球体,且控制生料球的水分为10
‑
18%;
[0045]
s4.烧制,将生料球进行高温烧制,从室温升温到500℃,保温20min;再从500℃升温到800℃,升温时间20min;最后从800℃升温到1220℃,升温时间60min,保温20min,自然
冷却至室温,得到实施例1样品tl1。
[0046]
1.3陶粒硬度检测
[0047]
根据gbt17431.1
‑
2010《轻集料及其实验方法》中对轻集料的相关评估指标,对将制备出的实施例样品tl1分别进行容重、1h的吸水率、筒压强度、烧失率和表观密度进行检验,具体的指标如表2所示。
[0048]
表2陶粒性能指标
[0049][0050]
综上,本发明大量使用高铝粉煤灰粉煤灰,制得的陶粒吸水率低,且强度大幅提高,筒压强度12
‑
20mp,此外,本发明还充分利用了赤泥和硅钙渣的造孔、降低烧结温度以及粘结性能,使该工艺简单易行。本发明充分利用地区资源优势,配方全部使用固体废弃物,不仅不破坏自然环境,而且处置固废过程中不产生二次固废污染,环境意义巨大。
[0051]
所述高强陶粒的指标高于gbt17431.1
‑
2010《轻集料及其实验方法》中相应粒级陶粒的指标要求,堆积密度为800
‑
1100kg/m3,吸水率≤6%,筒压强度12
‑
20mp。
[0052]
实施例2
[0053]
2.1原料
[0054]
实施例2制备的高强度陶粒各原料质量百分数分别为:79%粉煤灰、11%赤泥、10%硅钙渣。
[0055]
所述赤泥为铝土矿拜耳法提取氧化铝后剩余的残渣,且烧失量为15
‑
20%;所述硅钙渣为粉煤灰碱石灰烧结法提取氧化铝后剩余的残渣,且烧失量为5
‑
15%;赤泥粒度<150μm,选用的所述硅钙渣粒度<150μm,所述粉煤灰粒度要求45μm筛余量小于45%。
[0056]
选取的高铝粉煤灰、赤泥和硅钙渣原料的各化学成分质量百分数如表3.
[0057]
表3原料的各化学成分质量百分数
[0058][0059]
2.2制备方法
[0060]
s1.预处理,将赤泥、硅钙渣进行烘干处理,使其含水率降低至5%及以下;分别将赤泥、硅钙渣采用球磨机进行研磨,并将磨细后的赤泥、硅钙渣过100目筛;
[0061]
s2.混合,将步骤s1中研磨并过筛后的赤泥、硅钙渣按配比与粉煤灰进行混合,并将混合的原料放入混料机混合均匀;
[0062]
s3.制球,将混合好的原料加入圆盘造粒机中进行喷水造粒,制成5
‑
20mm的生料球体,且控制生料球的水分为10
‑
18%;
[0063]
s4.烧制,将生料球进行高温烧制,从室温升温到500℃,保温20min;再从500℃升
温到800℃,升温时间15min;最后从800℃升温到1240℃,升温时间50min,保温18min,自然冷却至室温,得到实施例2样品tl2。
[0064]
2.3陶粒硬度检测
[0065]
根据gbt17431.1
‑
2010《轻集料及其实验方法》中对轻集料的相关评估指标,对将制备出的实施例样品tl2分别进行容重、1h的吸水率、筒压强度、烧失率和表观密度进行检验,具体的指标如表4所示。
[0066]
表4陶粒性能指标
[0067][0068]
实施例3
[0069]
2.1原料
[0070]
实施例2制备的高强度陶粒各原料质量百分数分别为:75%粉煤灰、14%赤泥、11%硅钙渣。
[0071]
所述赤泥为铝土矿拜耳法提取氧化铝后剩余的残渣,且烧失量为15
‑
20%;所述硅钙渣为粉煤灰碱石灰烧结法提取氧化铝后剩余的残渣,且烧失量为5
‑
15%;赤泥粒度<150μm,选用的所述硅钙渣粒度<150μm,所述粉煤灰粒度要求45μm筛余量小于45%。
[0072]
选取的高铝粉煤灰、赤泥和硅钙渣原料的各化学成分质量百分数如表5.
[0073]
表5原料的各化学成分质量百分数
[0074][0075]
3.2制备方法
[0076]
s1.预处理,将赤泥、硅钙渣进行烘干处理,使其含水率降低至5%及以下;分别将赤泥、硅钙渣采用球磨机进行研磨,并将磨细后的赤泥、硅钙渣过100目筛;
[0077]
s2.混合,将步骤s1中研磨并过筛后的赤泥、硅钙渣按配比与粉煤灰进行混合,并将混合的原料放入混料机混合均匀;
[0078]
s3.制球,将混合好的原料加入圆盘造粒机中进行喷水造粒,制成5
‑
20mm的生料球体,且控制生料球的水分为10
‑
18%;
[0079]
s4.烧制,将生料球进行高温烧制,从室温升温到500℃,保温20min;再从500℃升温到800℃,升温时间15min;最后从800℃升温到1240℃,升温时间50min,保温18min,自然冷却至室温,得到实施例3样品tl3。
[0080]
3.3陶粒硬度检测
[0081]
根据gbt17431.1
‑
2010《轻集料及其实验方法》中对轻集料的相关评估指标,对将制备出的实施例样品tl3分别进行容重、1h的吸水率、筒压强度、烧失率和表观密度进行检
验。
[0082]
综上,本发明大量使用高铝粉煤灰粉煤灰,制得的陶粒吸水率低,且强度大幅提高,筒压强度12
‑
20mp,此外,本发明还充分利用了赤泥和硅钙渣的造孔、降低烧结温度以及粘结性能,使该工艺简单易行。本发明充分利用地区资源优势,配方全部使用固体废弃物,不仅不破坏自然环境,而且处置固废过程中不产生二次固废污染,环境意义巨大。
[0083]
所述高强陶粒的指标高于gbt17431.1
‑
2010《轻集料及其实验方法》中相应粒级陶粒的指标要求,堆积密度为800
‑
1100kg/m3,吸水率≤6%,筒压强度12
‑
20mp。
[0084]
以上所述,仅为本发明的具体实施方式,但本发明的保护范围并不局限于此,任何熟悉本技术领域的技术人员在本发明揭露的技术范围内,可轻易想到变化或替换,都应涵盖在本发明的保护范围之内。因此,本发明的保护范围应以所述权利要求的保护范围为准。
再多了解一些
本文用于企业家、创业者技术爱好者查询,结果仅供参考。