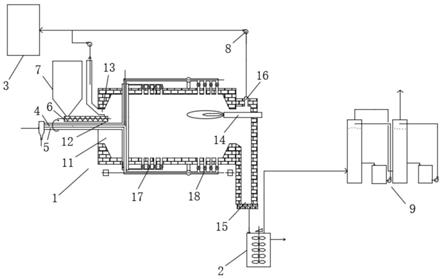
1.本发明涉及钒酸钠的制备技术领域,具体涉及一种以钒精渣为原料制备钒酸钠的方法及装置。
背景技术:
2.钒是一种十分重要的战略物资,在钢铁、电子、化工、宇航、原子能、航海、建筑、体育、医疗、电源、陶瓷等在国民经济和国防中占有十分重要的位置。
3.目前,从钒精渣中提取钒酸钠一般是将钒原料进行研磨后,再与添加复合添加剂混合后,在含氧气体以及750~950℃条件下于回转窑中高温焙烧反应制得溶于水的钒酸钠盐,再经浸取提钒得到;
4.例如,专利申请号为201710386380.0的中国专利申请公开了一种由含钒原料制备钒酸钠的富氧焙烧方法,具体公开了将含钒原料研磨至粒径小于120μm,与复合添加剂混合后,放置于由填充料组成的反应混合物料床上并注入含氧气体,在温度为750
‑
950℃的回转窑中,通过热焰气体直接加热反应;其中,复合添加剂为比例为40~60:20~40:10~30的氯化钠、硫酸钠和碳酸钠;然而,该方法在钒酸钠制备过程中焙烧温度较高,需要较高的能源,同时该方法使得钒原料中的钒转化率较低,其最高钒转化率仅仅为95.3%;此外,由于现有技术提钒效率较低,使得钒尾渣中钒含量较高,因此,现有技术中制备得到的钒尾渣需要多次作为原料进行焙烧除钒,进而增加了能耗。
技术实现要素:
5.本发明的目的在于提供一种以钒精渣为原料制备钒酸钠的方法及装置,该方法能够充分促进钒精渣中的钒转化为钒酸钠,可有效提高钒转化率;此外,该方法还能够有效降低反应温度,降低能耗。
6.为了实现本发明的上述目的,特采用以下技术方案:
7.本发明第一方面提供一种以钒精渣为原料制备钒酸钠的方法,所述方法包括如下步骤:
8.(a)将钒精渣烘干磨细并去除金属铁,得到钒精渣物料,再将钒精渣物料和钠盐附加剂混合,得到混合物料,其中,钒精渣物料中mfe的含量不大于5%;
9.(b)将混合物料在旋转翻料以及喷吹空气的条件下进行预氧化处理,得到预氧化物料;
10.(c)将预氧化物料在旋转翻料以及喷吹氧气的条件下进行高温焙烧,得到熟料,其中,高温焙烧温度为620~720℃;
11.(d)将未经冷却的熟料进行浸取提钒,即得所述钒酸钠。
12.优选地,所述钒精渣物料与钠盐附加剂的质量比为1∶(0.07~0.3)。
13.优选地,所述钒精渣物料的目粒度不低于120目。
14.优选地,所述钠盐附加剂由氯化钠和碳酸钠组成,所述氯化钠与碳酸钠的质量比
为1∶(0.4~2)。
15.优选地,所述预氧化处理温度为150~600℃,时间为0.5~4h。
16.优选地,所述步骤(b)中,旋转翻料的转速为0.4~1.2r/min;喷吹空气的压力为0.01~1.6mpa,并且每吨混合物料按照0.5~50m3/h的喷吹量进行喷吹空气。
17.优选地,所述高温焙烧时间为20~60min。
18.优选地,所述步骤(c)中,旋转翻料的转速为0.4~1.2r/min;喷吹氧气的压力为0.01~1.6mpa,并且每吨预氧化物料按照0.5~10m3/h的喷吹量进行喷吹氧气。
19.本发明第二方面提供一种基于上述方法生产钒酸钠的装置,所述装置包括回转窑,以及分别与所述回转窑连接的浸取装置和烟气净化系统;
20.所述回转窑的一端设置有进气口、进料口和第一出气口,另一端设置有燃烧器、出料口和第二出气口,所述回转窑侧壁上且靠近所述进料口的端部设置有第一喷气嘴,且远离所述进料口的端部设置有第二喷气嘴,所述第一喷气嘴通过所述进气口与空气管路连接,所述第二喷气嘴通过所述进气口与氧气管路连接;所述进料口通过螺旋传输器与生料仓连接,所述第一出气口和第二出气口经引风机分别与所述烟气净化系统连接,所述出料口与所述浸取装置连接。
21.优选地,所述浸取装置包括电机、减速机、浸取罐和搅拌桨;
22.所述电机通过所述减速机与所述搅拌桨连接,所述搅拌桨位于所述浸取罐内;
23.所述浸取罐顶部设置有下料口、加水口和排气口,所述排气口连接有冷凝器,所述浸取罐侧壁的底部设置有进液口,上部设置有排液口。
24.优选地,所述浸取罐的侧壁设置有衬板。
25.与现有技术相比,本发明的有益效果至少包括:
26.在高温焙烧过程中,若mfe含量过高,则导致mfe与氧反应易造成局部高温而使得物料成团,进而影响钒精渣与氧的接触,从而降低钒转化率;本技术上述方法通过对钒精渣进行除铁处理,使得钒精渣中mfe含量不大于0.5%,再经预氧化处理以氧化未除尽的铁粉,使得在高温焙烧过程中消除了mfe与氧气反应,不会造成局部高温,进而避免物料成团,有效提高钒精渣与氧气接触面积,从而提高钒转化率。
27.本技术上述方法通过限定高温焙烧的环境以及温度,有效降低了反应温度,避免了现有焙烧温度(750~950℃)下副反应过多的问题,比如,在该温度下碳酸钠容易熔融,而且钒精渣中二氧化硅与纯碱进行反应(反应方程式如下na2co3 sio2→
na2sio3 co2),化学反应发生在784
‑
853c
°
之间,最高峰在835c
°
,容易形成液态玻璃体,反应物料已成团,导致钒精渣不易与氧气反应;此外,由于碳酸钠的熔点温度为851℃,而纯碱的熔融同样不利于钒精渣氧化反应。然而,本技术技术方案通过对高温焙烧环境以及温度(620~720℃)的限定,在高温焙烧过程中纯碱不会熔融、降低副反应(比如铬的氧化产物)并降低能耗,同时硅溶出率大大降低,进而降低了反应物料成团几率,提高了钒精渣与氧气反应接触面积,从而显著提高钒转化率和产量。
附图说明
28.为了更清楚地说明本发明具体实施方式或现有技术中的技术方案,下面将对具体实施方式或现有技术描述中所需要使用的附图作简单地介绍。在所有附图中,类似的元件
或部分一般由类似的附图标记标识。附图中,各元件或部分并不一定按照实际的比例绘制。
29.图1为本发明实施例中生产钒酸钠装置的结构示意图;
30.图2为本发明实施例中浸取装置的结构示意图;
31.图3为本发明回转窑上第一喷气嘴的分布图;
32.图4为本发明回转窑上第二喷气嘴的分布图。
具体实施方式
33.下面将结合实施例对本发明技术方案的实施例进行详细的描述。以下实施例仅用于更加清楚地说明本发明的技术方案,因此只作为示例,而不能以此来限制本发明的保护范围。
34.需要注意的是,除非另有说明,本技术使用的技术术语或者科学术语应当为本发明所属领域技术人员所理解的通常意义。
35.目前,现有以含钒物料制备钒酸钠过程中存在高温焙烧温度较高,需要较高的能源,能耗较高,同时现有方法使得钒原料中的钒转化率较低。
36.有鉴于此,本发明实施例提供一种以钒精渣为原料制备钒酸钠的方法,该方法包括如下步骤:
37.(a)将钒精渣烘干磨细并去除金属铁,得到钒精渣物料,再将钒精渣物料和钠盐附加剂混合,得到混合物料,其中,钒精渣物料中mfe的含量不大于0.5%;
38.(b)将混合物料在旋转翻料以及喷吹空气的条件下进行预氧化处理,得到预氧化物料;
39.(c)将预氧化物料在旋转翻料以及喷吹氧气的条件下进行高温焙烧,得到熟料,其中,高温焙烧温度为620~720℃;
40.(d)将未经冷却的熟料进行浸取提钒,即得所述钒酸钠。
41.研究表明,钒转化率随着钒精渣粒度的减小而增大,但钒精渣粒度减小到一定程度(120目~180目,相当于125~80μ)以后,转化率变化不大,但过细的钒渣粒度会导致磨料的能量消耗大、产量低且物粒飞扬损失大;另一方面,钒精渣粒度太细,表面活性大,在焙烧时炉料容易烧结,不利于钒的提取;进而在保障钒转化率的前提下为了降低能耗,在一实施方式中,本技术具体限定钒精渣物料的目粒度不低于120目;该目粒度的限定能够保障钒精渣中钒转化率并避免由于钒精渣粒度过细而产生的上述问题。
42.本发明上述高温焙烧过程中,若mfe含量过高,则导致mfe与氧反应易造成局部高温而使得物料成团,进而影响钒精渣与氧的接触,从而降低钒转化率;本技术上述方法通过对钒精渣进行除铁处理,使得钒精渣中mfe含量不大于0.5%,再经预氧化处理以氧化未除尽的铁粉,使得在高温焙烧过程中消除了mfe与氧气反应,不会造成局部高温,进而避免物料成团,有效提高钒精渣与氧气接触面积,从而提高钒转化率。
43.在一实施方式中,预氧化处理温度可以为150~600℃中任一数值的温度,时间可以为0.5~4h中任一数值。进一步地,为了更好的实现预氧化处理,在一实施方式中,旋转翻料的转速可以为0.4~1.2r/min中任一数值;喷吹空气的压力可以为0.01~1.6mpa中的任一数值,并且每吨混合物料可以按照0.5~50m3/h中的任一喷吹量进行喷吹空气。通过上述预氧化处理参数的控制,能够充分氧化钒精渣物料中剩余的铁粉。
44.本发明上述方法中对钠盐附加剂的种类不作具体限定,可以采用本领域常规的钠盐附加剂,例如,在一实施方式中,钠盐附加剂由氯化钠和碳酸钠组成,其中,氯化钠与碳酸钠的质量比为1∶(0.4~2)中的任一数值,具体可以为1∶0.4、1∶1、1∶2;更优选地,在其他实施方式中,氯化钠与碳酸钠的质量比为1∶(1.5~2)中任一数值;本发明上述钠盐附加剂中nacl是一种无氧酸的盐类,它不能直接与v2o5发生成盐反应。nacl必须先行分解成na2o、na2o再同v2o5生成可溶性的钒酸盐。而na2co3则不同,它是含氧配盐,在同v2o5反应时可以发生成盐反应(na2co3 v2o5=2navo3 co2);此外,nacl熔点低,单独用nacl作为焙烧钒精渣的附加剂时,焙烧温度不能提高到合理温度。同时在焙烧过程中,nacl还会大量挥发,由于nacl的大量挥发,炉料nacl含量相应减少,表现出附加剂量的不足,如果增大nacl的配入量,又易造成炉料中的烧结和大窑结圈,因此,全部采用nacl作为附加剂是不适宜的。但是由于nacl易挥发可起到疏松炉料、增大反应表面的作用,有利于钒渣反应,提高转化率。本技术上述实施方式中通过以na2co3为主,适量配入nacl,经两者复配显著提高了钒转化率。
45.在一实施方式中,钒精渣物料与钠盐附加剂的质量比为1∶(0.07~0.3)中的任一数值,具体可以为1∶0.07、1∶0.1或1∶0.3。通过上述原料配比的限定,能够更好的促进钒精渣中钒的转化。
46.本发明上述方法采用的焙烧温度仅仅为620~720℃,避免了现有焙烧温度(750~950℃)下副反应过多的问题,比如,在该温度(750~950℃)下碳酸钠容易熔融,而且钒精渣中二氧化硅与纯碱进行反应(反应方程式如下na2co3 sio2→
na2sio3 co2),化学反应发生在784
‑
853c
°
之间,最高峰在835c
°
,容易形成液态玻璃体,反应物料已成团,导致钒精渣不易与氧气反应;此外,由于碳酸钠的熔点温度为851℃,而纯碱的熔融被熔化,也同样不利于钒精渣氧化反应。然而,本技术技术方案通过对高温焙烧环境以及温度(620~720℃)的限定,在高温焙烧过程中纯碱不会熔融、降低副反应(比如铬的氧化产物)并降低能耗,同时硅溶出率大大降低,进而降低了反应物料成团几率,提高了钒精渣与氧气反应接触面积,从而显著提高钒转化率和产量。
47.在一实施方式中,高温焙烧时间可以为20~60min中的任一数值;旋转翻料的转速可以为0.4~1.2r/min中的任一数值;喷吹氧气的压力可以为0.01~1.6mpa中的任一数值,并且每吨预氧化物料可以按照0.5~10m3/h中的任一喷吹量进行喷吹氧气;通过上述高温焙烧参数的控制,实现了在620~720℃下促进钒精渣中钒的转化,同时减少副反应,提高钒转化率和产量。
48.在本发明中对浸取采用的溶液不作严格限制,可以采用本领域常规的浸取溶液;比如,可以采用水或钒酸钠的溶液;在一实施方式中,熟料与浸取溶液的质量比为1∶(0.1~100)中的任一数值,具体可以为1∶1、1∶10或1∶100。
49.此外,为了更好的浸取熟料中的钒酸钠,通过将未经冷却的熟料直接进行浸取,能够使得浸取溶液的温度达到500~700℃,在该温度下能够更好的浸取熟料中的钒酸钠,并避免熟料中可溶性的偏钒酸盐放出氧生成不溶于水的钒青铜(nav6o
15
和na8v
24
o
63
),有利于提高钒的提取率。
50.本发明实施例还提供一种基于上述方法生产钒酸钠的装置,如图1、图2所示,该装置包括回转窑1,以及分别与回转窑1连接的浸取装置2和烟气净化系统3;
51.回转窑1的一端设置有进气口11、进料口12和第一出气口13,另一端设置有燃烧器
14、出料口15和第二出气口16,回转窑1侧壁上且靠近进料口12的端部设置有第一喷气嘴17,且远离进料口12的端部设置有第二喷气嘴18,第一喷气嘴17通过进气口11与空气管路4连接,第二喷气嘴18通过进气口11与氧气管路5连接,如图3、图4所示,在回转窑1的侧壁上分别设置有三排第一喷气嘴17和第二喷气嘴18,每排呈120
°
角,在回转窑1转动过程中,通过阀门控制第一喷气嘴17和第二喷气嘴18的开启和闭合,具体地,当第一喷气嘴17或第二喷气嘴18旋转到回转窑1内物料时,开启阀门,当第一喷气嘴17或第二喷气嘴18旋转到远离回转窑1内物料时,闭合阀门;进料口12通过螺旋传输器6与生料仓7连接,第一出气口13和第二出气口16经引风机8分别与烟气净化系统3连接,引风机8用于抽提回转窑1内部的气体,出料口15与浸取装置2连接;
52.浸取装置2包括电机21、减速机22、浸取罐23和搅拌桨24;
53.电机21通过减速机22与搅拌桨24连接,搅拌桨24位于浸取罐23内;
54.浸取罐23顶部设置有下料口25、加水口20和排气口26,排气口26连接有冷凝器9,冷凝器9用于冷凝从排气口26溢出的水蒸气,浸取罐23侧壁的底部设置有进液口27,上部设置有排液口28;浸取罐24的侧壁设置有衬板29。
55.此外,为了降低烟气中的氮氧化物的含量,在一实施方式中,燃烧器14采用的燃烧气体为天然气、煤气和氧气;通过采用纯氧燃烧器14而且无二次风,回转窑1两端的气体可以通过引风机8引入烟气净化系统3,进而使得回转窑1中烟气氮氧化物排放浓度低于20mg/nm3;而现有技术中回转窑1中进入大量二次空气,且燃烧器14燃烧气体后会产生氮氧化合物,造成烟气氮氧化物排放达到200mg/nm3。
56.以下特通过具体实施例对本发明的技术方案作进一步详细说明。
57.以下实施例采用的原料如下:
58.钒精渣:包括如下含量组分:v2o
5 13.5%、mfe 13%、tio
2 10.6%、mno 9.1%、sio
2 14%、p 0.28%、cao 4.6%、cr2o
3 8.2%;
59.氯化钠:市购得到;
60.碳酸钠:市购得到。
61.实施例1
62.本实施例为一种以钒精渣为原料制备钒酸钠的方法,该方法包括如下步骤:
63.(a)将钒精渣烘干磨细至目粒度不低于120目并经自动连续干式电磁除铁器去除金属铁,得到钒精渣物料,再将钒精渣物料和钠盐附加剂混合,得到混合物料,其中,钒精渣物料中mfe的含量为2.43%,钒精渣物料与钠盐附加剂的质量比为1∶0.07,钠盐附加剂由氯化钠和碳酸钠组成,氯化钠与碳酸钠的质量比为1∶1.5;
64.(b)将混合物料在0.4r/min旋转翻料以及0.5mpa喷吹空气条件下进行预氧化处理,得到预氧化物料,其中,预氧化处理温度为300~600℃,时间为0.5h,每吨混合物料按照20m3/h的喷吹量进行喷吹空气;
65.(c)将预氧化物料在0.4r/min旋转翻料以及0.5mpa喷吹氧气的条件下进行高温焙烧,得到熟料,其中,高温焙烧温度为680~720℃,高温焙烧时间为20min,每吨预氧化物料按照50m3/h的喷吹量进行喷吹氧气;
66.(d)将未经冷却的熟料直接与水混合进行浸取,再经提钒,得到钒酸钠,其中熟料与水的质量比为1∶10。
67.实施例2
68.本实施例为一种以钒精渣为原料制备钒酸钠的方法,该方法包括如下步骤:
69.(a)将钒精渣烘干磨细至目粒度不低于120目并经自动连续干式电磁除铁器去除金属铁,得到钒精渣物料,再将钒精渣物料和钠盐附加剂混合,得到混合物料,其中,钒精渣物料中mfe的含量为4.28%,钒精渣物料与钠盐附加剂的质量比为1∶0.3,钠盐附加剂由氯化钠和碳酸钠组成,氯化钠与碳酸钠的质量比为1∶2;
70.(b)将混合物料在1.2r/min旋转翻料以及1.6mpa喷吹空气条件下进行预氧化处理,得到预氧化物料,其中,预氧化处理温度为150~300℃,时间为4h,每吨混合物料按照50m3/h的喷吹量进行喷吹空气;
71.(c)将预氧化物料在1.2r/min旋转翻料以及1.6mpa喷吹氧气的条件下进行高温焙烧,得到熟料,其中,高温焙烧温度为620~680℃,高温焙烧时间为60min,每吨预氧化物料按照10m3/h的喷吹量进行喷吹氧气;
72.(d)将未经冷却的熟料直接与水混合进行浸取,再经提钒,得到钒酸钠,其中熟料与水的质量比为1∶100。
73.实施例3
74.本实施例为一种以钒精渣为原料制备钒酸钠的方法,该方法包括如下步骤:
75.(a)将钒精渣烘干磨细至目粒度不低于120目并经自动连续干式电磁除铁器去除金属铁,得到钒精渣物料,再将钒精渣物料和钠盐附加剂混合,得到混合物料,其中,钒精渣物料中mfe的含量为4.43%,钒精渣物料与钠盐附加剂的质量比为1∶0.1,钠盐附加剂由氯化钠和碳酸钠组成,氯化钠与碳酸钠的质量比为1∶1.8;
76.(b)将混合物料在1r/min旋转翻料以及1.0mpa喷吹空气条件下进行预氧化处理,得到预氧化物料,其中,预氧化处理温度为300~400℃,时间为2h,每吨混合物料按照30m3/h的喷吹量进行喷吹空气;
77.(c)将预氧化物料在1r/min旋转翻料以及1.0mpa喷吹氧气的条件下进行高温焙烧,得到熟料,其中,高温焙烧温度为650~700℃,高温焙烧时间为40min,每吨预氧化物料按照8m3/h的喷吹量进行喷吹氧气;
78.(d)将未经冷却的熟料直接与水混合进行浸取,再经提钒,得到钒酸钠,其中熟料与水的质量比为1∶50。
79.对比例1
80.本对比例为一种以钒精渣为原料制备钒酸钠的方法,该方法与实施例3中的方法基本相同,区别仅在于步骤(a)中经自动连续干式电磁除铁器去除金属铁后得到钒精渣物料中mfe的含量为6.67%。
81.对比例2
82.本对比例为一种以钒精渣为原料制备钒酸钠的方法,该方法与实施例3中的方法基本相同,区别仅在于步骤(c)中将喷吹氧气替换为喷吹空气。
83.对比例3
84.本对比例为一种以钒精渣为原料制备钒酸钠的方法,该方法与实施例3中的方法基本相同,区别仅在于步骤(d)中将熟料冷却至100℃后再与水混合进行浸取。
85.实验例
86.分别按照实施例3以及对比例1~3中的方法制备钒酸钠;分别计算钒精渣中钒转化率,钒精渣中铬的氧化率,钒尾渣带损,浸提后的钒尾渣中总钒含量;
[0087][0088][0089]
钒尾渣中的钒分为可溶性钒及不溶性钒,不溶性钒一般为未反应的钒,而带损是指钒尾渣带走的可溶性钒(即是钒酸钠),
[0090][0090][0091][0092]
计算结果如表1所示:
[0093]
表1不同方法制备钒酸钠的指标
[0094][0095]
由表1数据可知:
[0096]
本技术技术方方案通过特定工艺的限定,能够更好的提高钒转化率并降低铬的氧化率进而降低副反应,此外还能够有效降低钒尾渣带损,减少钒损失。
[0097]
最后应说明的是:以上各实施例仅用以说明本发明的技术方案,而非对其限制;尽管参照前述各实施例对本发明进行了详细的说明,本领域的普通技术人员应当理解:其依然可以对前述各实施例所记载的技术方案进行修改,或者对其中部分或者全部技术特征进行等同替换;而这些修改或者替换,并不使相应技术方案的本质脱离本发明各实施例技术方案的范围,其均应涵盖在本发明的权利要求和说明书的范围当中。
再多了解一些
本文用于企业家、创业者技术爱好者查询,结果仅供参考。