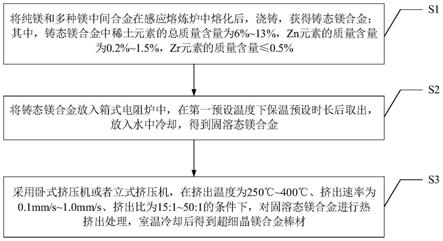
1.本发明涉及镁合金制造技术领域,尤其涉及一种超细晶镁合金棒材的制备方法。
背景技术:
2.镁合金是目前工程应用中密度最低的金属结构材料,在减重需求迫切的航空航天、交通运输、电子器件等领域具有广阔的应用前景。
3.与常见的铝、铁等立方结构金属材料不同,镁合金具有典型的密排六方(hcp)晶体结构。hcp结构的晶体对称性差,室温下各个潜在滑移系和孪晶系的临界分切应力差别大,这使得其在室温条件下可开动的滑移系的数量不足(通常仅有基面滑移),从而导致其室温强度和塑性均远低于常见的铝合金。通常,通过变形加工可以改善铸态金属的力学性能,然而,镁合金在变形过程中很容易形成较强的基面织构,这导致其存在显著的力学性能各向异性,这也进一步限制了其作为高性能结构材料的广泛应用。
4.根据经典的hall
‑
petch关系,通过晶粒细化可以显著提升金属材料的力学性能,尤其当晶粒尺寸细化到超细晶范畴(d<1μm)时,材料的强度可获得大幅的提升。然而,镁合金熔点低、变形加工困难,现有的超细晶镁合金制备技术还主要依赖于剧烈塑性变形等方法,如高压扭转、等通道转角挤压和多向锻造等。例如,申请号cn201210516981.6,名称为“一种超细晶镁合金薄板的高成材率加工方法”的专利,公开了镁合金等通道挤压后进行轧制加工,得到超细晶镁合金板材的方法,但这些工艺制备流程复杂,通常需要多个道次的挤出和轧制才能实现组织的细化,并且所制备的样品通常为短棒状或者薄片状样品,无法实现大尺寸超细晶镁合金的高效率连续制备,此外,通过剧烈塑性变形技术制备的超细晶镁合金通常含有高密度位错等结构缺陷,这使得其塑性变形能力较差,无法满足工程上对材料强度和塑性的匹配需求。申请号201610589439.1,名称为“一种小变形量制备大块纳米晶镁合金的方法”的专利公开了一种利用室温冷轧变形和后续低温短时热处理工艺制备纳米晶(40
‑
100nm)mg
‑
ag合金的方法,该方法只适用于特定的合金成分,并且所制备材料的屈服强度较低,只有120mpa。申请号202010873447.5,名称为“一种超细晶的变形镁合金材料及其制备方法”的专利公开了一种通过简单的反挤压方法制备超细晶高稀土含量(稀土含量质量比>13%)镁合金的专利,实施例给出的平均晶粒尺寸均为5
‑
6μm,并不是国际上广泛认可的超细晶组织(d<1μm)。
5.因此,迫切需要发展一种工艺流程简单的、可连续制备低织构超细晶镁合金的方法。
技术实现要素:
6.有鉴于此,本发明提供了一种超细晶镁合金棒材的制备方法,用以发展一种工艺流程简单的、可连续制备低织构超细晶镁合金的方法。
7.本发明提供的一种超细晶镁合金棒材的制备方法,包括如下步骤:
8.s1:将纯镁和多种镁中间合金在感应熔炼炉中熔化后,浇铸,获得铸态镁合金;其
中,所述铸态镁合金中稀土元素的总质量含量为6%~13%,zn元素的质量含量为0.2%~1.5%,zr元素的质量含量≤0.5%;
9.s2:将所述铸态镁合金放入箱式电阻炉中,在第一预设温度下保温预设时长后取出,放入水中冷却,得到固溶态镁合金;
10.s3:采用卧式挤压机或者立式挤压机,在挤出温度为250℃~400℃、挤出速率为0.1mm/s~1.0mm/s、挤出比为15:1~50:1的条件下,对所述固溶态镁合金进行热挤出处理,室温冷却后得到超细晶镁合金棒材。
11.在一种可能的实现方式中,在本发明提供的上述超细晶镁合金棒材的制备方法中,在执行步骤s3后,还包括如下步骤:
12.s4:将所述超细晶镁合金棒材在第二预设温度下进行时效处理。
13.在一种可能的实现方式中,在本发明提供的上述超细晶镁合金棒材的制备方法中,步骤s2中,所述第一预设温度为495℃~520℃。
14.在一种可能的实现方式中,在本发明提供的上述超细晶镁合金棒材的制备方法中,步骤s2中,所述预设时长为6h~12h。
15.在一种可能的实现方式中,在本发明提供的上述超细晶镁合金棒材的制备方法中,步骤s4中,所述第二预设温度为170℃~230℃。
16.本发明提供的上述超细晶镁合金棒材的制备方法,通过综合优化铸态镁合金的成分和改进热挤出处理的工艺,利用热挤出处理过程中的动态再结晶和纳米第二相的动态析出原理,发展一种工艺步骤简单的、可连续制备大尺寸低织构超细晶镁合金的短流程方法,进而实现高强高韧且力学性能各向同性镁合金的可控制备。本发明提供的上述超细晶镁合金棒材的制备方法,工艺流程短,仅需要对镁合金进行一次热挤出处理即可获得超细晶组织,还可实现超细晶镁合金棒材的连续制备,生产效率高,适合大规模工业化生产。采用本发明提供的上述超细晶镁合金棒材的制备方法,可以获得尺寸均匀的等轴超细晶组织,晶粒的再结晶程度高,织构强度低,合金的力学性能接近各向同性。
附图说明
17.图1为本发明提供的一种超细晶镁合金棒材的制备方法的流程图;
18.图2为本发明实施例1所得的超细晶镁合金棒材的{0002}基面极图;
19.图3为本发明实施例1所得的超细晶镁合金棒材的透射电子显微照片;
20.图4为本发明实施例1所得的超细晶镁合金棒材的室温拉伸和压缩应力应变曲线;
21.图5为对比例1所得镁合金的{0002}基面极图;
22.图6为对比例1所得镁合金的电子背散射衍射晶界图。
具体实施方式
23.下面将结合本发明实施方式中的附图,对本发明实施方式中的技术方案进行清楚、完整的描述,显然,所描述的实施方式仅仅是作为例示,并非用于限制本发明。
24.本发明提供的一种超细晶镁合金棒材的制备方法,如图1所示,包括如下步骤:
25.s1:将纯镁和多种镁中间合金在感应熔炼炉中熔化后,浇铸,获得铸态镁合金;其中,铸态镁合金中稀土元素(gd、y、sm等)的总质量含量为6%~13%,zn元素的质量含量为
0.2%~1.5%,zr元素的质量含量≤0.5%;
26.步骤s1中的合金熔炼方法与常规的镁合金熔炼方法相同,在此不做赘述;熔炼后得到上述成分的铸态镁合金,可以形成高密度的纳米第二相颗粒(主要为lpso,β’,γ’相,等),这对抑制热变形过程中的晶粒长大十分重要;
27.s2:将铸态镁合金放入箱式电阻炉中,在第一预设温度下保温预设时长后取出,放入水中冷却,得到固溶态镁合金;
28.s3:采用卧式挤压机或者立式挤压机,在挤出温度为250℃~400℃、挤出速率为0.1mm/s~1.0mm/s、挤出比为15:1~50:1的条件下,对固溶态镁合金进行热挤出处理,室温冷却后得到超细晶镁合金棒材;
29.通过设计铸态镁合金的成分以及热挤出处理的条件,在热挤出处理过程中,挤出温度为250℃~400℃,挤出速率为0.1mm/s~1.0mm/s,挤出比为15:1~50:1,可以使原始粗大的晶粒发生动态再结晶,获得接近随机取向的完全再结晶超细晶组织;并且,在热挤出处理过程中还伴随着固溶元素的晶界偏聚以及高密度纳米第二相颗粒在晶界附近的动态析出,它们可有效钉扎晶界,使得动态再结晶超细晶组织在高温下得以保留;得到的低织构超细晶镁合金棒材中晶粒尺寸<2μm的再结晶晶粒占比应>80%,平均晶粒尺寸应≤1.5μm,宏观基面织构强度应≤3.0mrd(随机取向分布强度倍数),沿挤出方向的拉伸和压缩屈服强度比值应在0.9
‑
1.1范围内。
30.较佳地,为了进一步提高低织构超细晶镁合金棒材的强度,在执行本发明提供的上述超细晶镁合金棒材的制备方法中的步骤s3后,还可以执行如下步骤:
31.s4:将超细晶镁合金棒材在第二预设温度下进行时效处理;通过纳米第二相的析出,进一步提高低织构超细晶镁合金棒材的强度。
32.在具体实施时,在执行本发明提供的上述超细晶镁合金棒材的制备方法中的步骤s2时,第一预设温度优选495℃~520℃范围。
33.在具体实施时,在执行本发明提供的上述超细晶镁合金棒材的制备方法中的步骤s2时,预设时长优选6h~12h范围。
34.在具体实施时,在执行本发明提供的上述超细晶镁合金棒材的制备方法中的步骤s4时,第二预设温度优选170℃~230℃范围。
35.下面通过三个具体的实施例和一个对比例对本发明提供的上述超细晶镁合金棒材的制备方法的具体实施和所得镁合金的微观组织和力学性能进行详细说明。
36.实施例1:
37.第一步:合金熔炼
38.将购买的纯镁和mg
‑
y、mg
‑
sm、mg
‑
zn、mg
‑
zr中间合金在常规镁合金感应熔炼炉中高温熔化后,浇铸,获得化学成分为mg
‑
6.5y
‑
4.5sm
‑
0.6zn
‑
0.3zr(质量百分比)的铸态镁合金。
39.第二步:固溶处理
40.将铸态镁合金放入温度为500℃的箱式电阻炉中,保温12h,然后取出放入水中快速冷却,得到固溶态镁合金。
41.第三步:热挤出处理
42.将固溶态镁合金加工成直径为50mm,高度为150mm的棒材,放入卧式挤压机进行热
挤出处理,挤出温度为350℃,挤出速率为0.75mm/s,挤出比为25:1,热挤出处理结束后,在空气中自然冷却,得到低织构超细晶镁合金棒材。
43.图2为实施例1所得的超细晶镁合金棒材的{0002}基面极图,其织构强度为1.38mrd。图3为实施例1所得的超细晶镁合金棒材的透射电子显微照片,全部为尺寸均匀的再结晶等轴晶粒,经统计测量其平均晶粒尺寸为0.93μm。图4为实施例1所得的超细晶镁合金棒材的室温拉伸(如图4所示的实线所示)和压缩(如图4所示的虚线所示)应力应变曲线(加载方向平行于挤出方向),其室温拉伸屈服强度和压缩屈服强度分别为378mpa和363mpa,拉伸断裂延伸率为12%,拉压屈服强度比值为1.04,展现出优异的强韧性和力学性能各向同性。
44.实施例2:
45.第一步:合金熔炼
46.将购买的纯镁和mg
‑
y、mg
‑
sm、mg
‑
zn、mg
‑
zr中间合金在常规镁合金感应熔炼炉中高温熔化后,浇铸,获得化学成分为mg
‑
5y
‑
3sm
‑
0.8zn
‑
0.5zr(质量百分比)的铸态镁合金。
47.第二步:固溶处理
48.将铸态镁合金放入温度为500℃的箱式电阻炉中,保温12h,然后取出放入水中快速冷却,得到固溶态镁合金。
49.第三步:热挤出处理
50.将固溶态镁合金加工成直径为50mm,高度为150mm的棒材,放入卧式挤压机进行热挤出处理,挤出温度为325℃,挤出速率为0.50mm/s,挤出比为25:1,热挤出处理结束后,在空气中自然冷却,得到低织构超细晶镁合金棒材。
51.实施例2所得的超细晶镁合金棒材的{0002}基面织构强度为1.58,平均晶粒尺寸为0.88μm,其室温拉伸和屈服强度分别为348mpa和341mpa,拉伸断裂延伸率为10%。拉压屈服强度比值为1.02,展现出优异的强韧性和力学性能各向同性。
52.实施例3:
53.第一步:合金熔炼
54.将购买的纯镁和mg
‑
gd、mg
‑
sm、mg
‑
zn、mg
‑
zr中间合金在常规镁合金感应熔炼炉中高温熔化后,浇铸,获得化学成分为mg
‑
6gd
‑
3sm
‑
0.5zn
‑
0.3zr(质量百分比)的铸态镁合金。
55.第二步:固溶处理
56.将铸态镁合金放入温度为510℃的箱式电阻炉中,保温12h,然后取出放入水中快速冷却,得到固溶态镁合金。
57.第三步:热挤出处理
58.将固溶态镁合金加工成直径为50mm,高度为150mm的棒材,放入卧式挤压机进行热挤出处理,挤出温度为335℃,挤出速率为0.65mm/s,挤出比为25:1,热挤出处理结束后,在空气中自然冷却,得到低织构超细晶镁合金棒材。
59.实施例3所得的超细晶镁合金棒材的{0002}基面织构强度为1.64,平均晶粒尺寸为0.98μm,其室温拉伸和屈服强度分别为377mpa和350mpa,拉伸断裂延伸率为10%。拉压屈服强度比值为1.08,展现出优异的强韧性和力学性能各向同性。
60.对比例1:
61.第一步:合金熔炼
62.将购买的纯镁和mg
‑
y、mg
‑
sm、mg
‑
zn、mg
‑
zr中间合金在常规镁合金感应熔炼炉中高温熔化后,浇铸,获得化学成分为mg
‑
6.5y
‑
4.5sm
‑
0.6zn
‑
0.3zr(质量百分比)的铸态镁合金。
63.第二步:固溶处理
64.将铸态镁合金放入温度为500℃的箱式电阻炉中,保温12h,然后取出放入水中快速冷却,得到固溶态镁合金。
65.第三步:热挤出处理
66.将固溶态镁合金加工成直径为50mm,高度为150mm的棒材,放入卧式挤压机进行热挤出处理,挤出温度为420℃,挤出速率为3.0mm/s,挤出比为25:1,热挤出处理结束后,在空气中自然冷却,得到本对比例样品。
67.图5为本对比例样品的{0002}基面极图,其织构强度为8.12mrd,图6为本对比例样品的电子背散射衍射晶界图,平均晶粒尺寸为7.88μm,室温拉伸和压缩屈服强度分别为269mpa和205mpa,其拉压屈服强度比值高达1.31,强度较低且力学性能各向异性明显。
68.对比例1所得镁合金的化学成分与实施例1相同,但由于热挤出工艺为传统的高温高速率热挤出,导致对比例1所得镁合金的晶粒组织粗大,基面织构较强,因而强度较低且力学性能各向异性明显。由此可见,本发明提供的上述超细晶镁合金棒材的制备方法,通过优化铸态镁合金的成分,满足铸态镁合金中稀土元素(gd、y、sm等)的总质量含量为6%~13%、zn元素的质量含量为0.2%~1.5%、zr元素的质量含量≤0.5%,并改进热挤出处理的工艺,满足挤出温度为250℃~400℃、挤出速率为0.1mm/s~1.0mm/s、挤出比为15:1~50:1的条件,可以获得低织构超细晶镁合金。
69.本发明提供的上述超细晶镁合金棒材的制备方法,通过综合优化铸态镁合金的成分和改进热挤出处理的工艺,利用热挤出处理过程中的动态再结晶和纳米第二相的动态析出原理,发展一种工艺步骤简单的、可连续制备大尺寸低织构超细晶镁合金的短流程方法,进而实现高强高韧且力学性能各向同性镁合金的可控制备。本发明提供的上述超细晶镁合金棒材的制备方法,工艺流程短,仅需要对镁合金进行一次热挤出处理即可获得超细晶组织,还可实现超细晶镁合金棒材的连续制备,生产效率高,适合大规模工业化生产。采用本发明提供的上述超细晶镁合金棒材的制备方法,可以获得尺寸均匀的等轴超细晶组织,晶粒的再结晶程度高,织构强度低,合金的力学性能接近各向同性。
70.显然,本领域的技术人员可以对本发明进行各种改动和变型而不脱离本发明的精神和范围。这样,倘若本发明的这些修改和变型属于本发明权利要求及其等同技术的范围之内,则本发明也意图包含这些改动和变型在内。
再多了解一些
本文用于企业家、创业者技术爱好者查询,结果仅供参考。