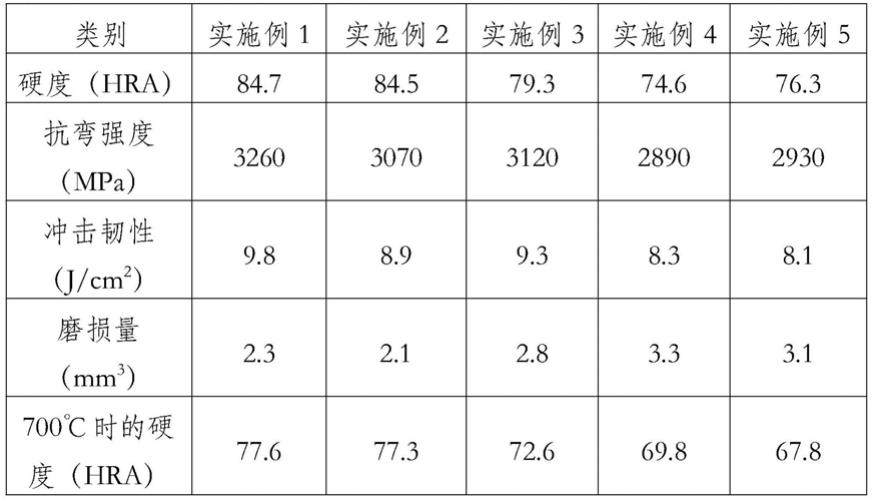
1.本发明涉及金属材料制造领域,具体来说涉及一种通过金属间化合物和碳氮化物共同实现强硬化的粉末冶金高速钢。
背景技术:
2.高速工具钢作为工具材料距今己有近百年的历史。由于其高硬度、高耐磨等特点,使得其至今仍在加工领域具有非常重要的意义。高速钢常用于制备丝锥、模具、钻头、刀具等切割设备。高速钢优异的切削性能主要来源于马氏体基体强化与碳化物二次硬化相平衡的结果。从化学成分来看,高速钢是一种含大量强碳化物形成元素(c、w、mo)的高性能工具钢。其硬质碳化物类型主要包括:mc(2100
‑
2800hv)、m2c(1800
‑
2250hv)、m6c(1800
‑
2250hv)和m7c3(1890
‑
2060hv)等。mc作为先共晶相可呈颗粒状弥散分布在马氏体基体中,其它类型碳化物均为共晶反应产物呈网状分布在后凝固的枝晶间区域。这类粗大网状一次碳化物在后续锻造、热处理过程难以消除,容易引起应力集中,使得加工过程产生裂纹,严重影响高速钢的寿命。为了获得弥散分布硬质碳化物(特别是高硬度mc相),有研究采用热处理或添加少量合金元素等方法促进网状亚稳相m2c高温分解成弥散mc,这样的方式不仅会增加加工工序导致成本上升,同时热加工引起的带状碳化物会破坏材料的各向异性,这使得高速钢刀具在使用过程中力学性能受到限制。
3.与此同时,粉末冶金技术在高速钢中的应用,可以有效细化组织,得到碳化物均匀分布,组织均匀的高速钢。与传统铸造高速钢相比,粉末冶金高速钢具有更好的力学性能。但是粉末冶金加工工艺处理后的材料依然存在合金中有害元素偏聚的问题而影响材料的力学性能。
技术实现要素:
4.本部分的目的在于概述本发明的实施例的一些方面以及简要介绍一些较佳实施例。在本部分以及本技术的说明书摘要和发明名称中可能会做些简化或省略以避免使本部分、说明书摘要和发明名称的目的模糊,而这种简化或省略不能用于限制本发明的范围。
5.鉴于上述高速钢的现状,提出了本发明。
6.因此,本发明其中一个目的是,进一步提升高速钢的硬度及耐磨性。通过复合稀土元素的添加,使合金的组织更加均匀,利用稀土元素能吸附有害元素的特性,减少有害元素在合金组织中的偏聚,起到一种净化钢液的作用。由于合金组织更加均匀,材料的硬度及耐磨性得到了明显的提升。
7.为解决上述技术问题,本发明提供了如下技术方案:一种复合稀土增强粉末冶金高速钢及其制备方法,其特征在于:
8.在粉末冶金的基础上向高速钢原料中添加复合稀土元素,得到复合稀土增强粉末冶金高速钢。
9.作为本发明所述复合稀土增强粉末冶金高速钢的制备方法的优选方案,其中:所
述原料,为si、mn、cr、mo、w、fe;所述复合稀土元素,为ce、y、la、nd等稀土元素中的两种或多种。
10.作为本发明所述复合稀土增强粉末冶金高速钢的制备方法的优选方案,其中:所述原料及复合稀土元素,其质量百分比为:si<0.5%、mn<0.5%、cr:4~8%、mo:3~6%、w:7~12%、re:0.1~0.3%,余量为fe。
11.作为本发明所述复合稀土增强粉末冶金高速钢的制备方法的优选方案,其中:所述原料及复合稀土元素,其质量百分比为:si:0.25%、mn:0.30%、cr:4~5%、mo:3~4%、w:8~10%、re:0.25%,余量为fe。
12.作为本发明所述复合稀土增强粉末冶金高速钢的制备方法的优选方案,其中:
13.依照配方取得相应质量分数的原料及复合稀土元素粉末混合均匀,并配入成型剂及炭黑,经球磨后干燥,再通过模压得到压坯,将压坯进行真空烧结,烧结冷却后得到烧结坯;
14.保护气氛下,将得到的烧结坯预热保温后进行热加工,控制道次变形量和压缩比,热变形结束后再退火处理,随炉冷却至室温,得到热加工后样品;
15.将热加工后样品预热后进行固溶处理,固溶处理快速冷却后得到固溶态样品,再进行深冷处理,待回温至室温后进行等温时效处理,即得到成品。
16.作为本发明所述复合稀土增强粉末冶金高速钢的制备方法的优选方案,其中:所述成型剂为聚乙烯、硬脂酸或石蜡中一种,添加量为8~15wt%;所述炭黑,添加量为1~2wt%;
17.作为本发明所述复合稀土增强粉末冶金高速钢的制备方法的优选方案,其中:
18.所述球磨为湿式球磨,采用行星球磨机混合粉末,其中,湿磨介质为无水乙醇,保护气氛为氩气,球料比为4~5:1,球磨机转速为180~200r/min,球磨时间为40~50h,经68~75℃真空干燥后过筛,获得待压料;
19.所述模压为双向模压,其中,模压压力为140~160mpa;
20.所述真空烧结,其中,温度为1300~1500℃,烧结时间为2~3h。
21.作为本发明所述复合稀土增强粉末冶金高速钢的制备方法的优选方案,其中:
22.所述预热保温后进行热加工,其中,预热温度为1150~1200℃,保温时间为30min,保护气氛为发生炉煤气;
23.所述热加工为热锻、轧制、旋锻中的任一种;
24.所述热变形,其中,道次变形量为5%,压缩比为70%;
25.所述退火处理,其中,退火温度为800~870℃,退火时间为2~3h。
26.作为本发明所述复合稀土增强粉末冶金高速钢的制备方法的优选方案,其中:所述将热加工后样品预热,其预热方式为箱式电阻炉预热,预热温度为220~280℃,预热时间为15~20min;
27.作为本发明所述复合稀土增强粉末冶金高速钢的制备方法的优选方案,其中:
28.所述固溶处理,其处理方式为盐浴固溶,固溶温度为1150~1200℃,固溶时间为15~30min,固溶后冷却方式为油冷;
29.所述深冷处理,其处理方式为深冷箱深冷,其深冷温度为
‑
100~
‑
80℃,深冷时间为2~4h;
30.所述时效处理,其处理方式为电阻炉处理,时效温度为550~680℃,处理次数为2次,时效保温时间为2.5小时。本发明的有益效果:
31.本发明方案制备的复合稀土增强粉末冶金高速钢,成品中合金的晶粒明显细化,碳化物的形态由未变质处理的连续网状变为断续网状和颗粒状,改善了合金中共晶碳化物的不均匀度,合金中非金属夹杂物总量普遍减少,夹杂物尺寸变小。具有优异的力学性能及出色的耐磨性,有着高的硬度(70~85hra)、高的抗弯强度(2800~3300mpa)和冲击韧性(8.1~9.8j/cm2)。
32.本发明添加的复合稀土元素在高速钢中有良好的净化与细化晶粒的作用,会产生良好的净化作用和脱硫、脱磷、脱氧效果。稀土元素在晶界和奥氏体的富集可以有效地改善晶界,减少碳化物的偏析,降低其热稳定性使其加热易于溶解,从而产生较好的固溶强化效果,大大增加了高速钢的强度。与添加稀土元素相比,添加复合稀土能使高速钢具有更好的硬度、抗弯强度、冲击韧性和更少的磨损量,达到更好的使用效果。
33.本发明利用粉末冶金方法在高速钢中引入复合稀土,粉末冶金高速钢本身解决了一次碳化物粗大和偏析的问题,加入适量的复合稀土元素后可以进一步细化晶粒,减少夹杂,使烧结后的孔隙减少。且当原料中ce:y:la:nd=1:1:0.5:0.5时,所制得的高速钢性能最好。
34.整个技术方案流程简单,操作方便,技术可控,投入小,可满足工业生产需求。
具体实施方式
35.下面通过具体实施例进一步阐述本发明的技术方案。
36.为使本发明的上述目的、特征和优点能够更加明显易懂,下面结合说明书实施例对本发明的具体实施方式做详细的说明。
37.在下面的描述中阐述了很多具体细节以便于充分理解本发明,但是本发明还可以采用其他不同于在此描述的其它方式来实施,本领域技术人员可以在不违背本发明内涵的情况下做类似推广,因此本发明不受下面公开的具体实施例的限制。
38.其次,此处所称的“一个实施例”或“实施例”是指可包含于本发明至少一个实现方式中的特定特征、结构或特性。在本说明书中不同地方出现的“在一个实施例中”并非均指同一个实施例,也不是单独的或选择性的与其他实施例互相排斥的实施例。
39.本发明中所用原料粉末均为商用高纯度(>99.8%)和超细(平均粒径<5μm)粉末。
40.本发明对高速钢采用的性能测试的方法包括:hra洛氏硬度计测试其硬度;三点弯曲加载法测试其抗弯强度;使用电脑控制500j摆锤式冲击试验机测试其冲击性能;一定时间磨察磨损后测量其损失量。
41.实施例1
42.按质量分数为:si:0.25%、mn:0.30%、cr:4%、mo:3%、w:8%、re:0.25%(ce:y=1:1),余量为fe,配取粉末。将配取的原料粉末、9wt%成型剂石蜡、1.8wt%炭黑混合,放置于行星球磨机球磨罐中进行湿式球磨,球磨过程中球磨介质为无水乙醇,保护气体为氩气,球料比为5:1,转速为200r/min,球磨时间为40h。球磨结束后在75℃真空干燥箱中进行干燥,干燥并擦筛造粒后,将混合粉末通过160mpa压力下进行双向模压,得到压坯。将压坯放
置于真空烧结炉中进行烧结,最终烧结温度为1350℃,最高温阶段保温2小时,随炉冷却后得到烧结坯。将烧结坯在氮气保护的箱式炉中以1150℃预热,到温保温30min后进行自由锻,经过三个道次的热加工后达到70%的压缩比,冷却后得到热加工后样品。将热加工样品在箱式炉中以870℃退火2小时,冷却后在盐浴中进行固溶处理,固溶温度为1200℃,保温30min后通过油冷冷却到室温,随后在液氮深冷箱中进行3h的深冷处理,深冷处理温度为
‑
80℃。试样回温到室温后,在箱式炉中550℃下进行等温时效处理,保温时间为2.5小时,冷却后得到所需的复合稀土增强粉末冶金高速钢,具体性能如表1中所示。
43.实施例2
44.按质量分数为:si:0.25%、mn:0.30%、cr:5%、mo:4%、w:10%、re:0.25%(ce:y=1:1),余量为fe,配取粉末。将配取的原料粉末、9wt%成型剂石蜡、1.8wt%炭黑混合,放置于行星球磨机球磨罐中进行湿式球磨,球磨过程中球磨介质为无水乙醇,保护气体为氩气,球料比为5:1,转速为200r/min,球磨时间为40h。球磨结束后在75℃真空干燥箱中进行干燥,干燥并擦筛造粒后,将混合粉末通过160mpa压力下进行双向模压,得到压坯。将压坯放置于真空烧结炉中进行烧结,最终烧结温度为1350℃,最高温阶段保温2小时,随炉冷却后得到烧结坯。将烧结坯在氮气保护的箱式炉中以1150℃预热,到温保温30min后进行自由锻,经过三个道次的热加工后达到70%的压缩比,冷却后得到热加工后样品。将热加工样品在箱式炉中以870℃退火2小时,冷却后在盐浴中进行固溶处理,固溶温度为1200℃,保温30min后通过油冷冷却到室温,随后在液氮深冷箱中进行3h的深冷处理,深冷处理温度为
‑
80℃。试样回温到室温后,在箱式炉中550℃下进行等温时效处理,保温时间为2.5小时,冷却后得到所需的复合稀土增强粉末冶金高速钢,具体性能如表1中所示。
45.实施例3
46.按质量分数为:si:0.25%、mn:0.30%、cr:6%、mo:4%、w:10%、re:0.25%(ce:y=1:1),余量为fe,配取粉末。将配取的原料粉末、9wt%成型剂石蜡、1.8wt%炭黑混合,放置于行星球磨机球磨罐中进行湿式球磨,球磨过程中球磨介质为无水乙醇,保护气体为氩气,球料比为5:1,转速为200r/min,球磨时间为45h。球磨结束后在70℃真空干燥箱中进行干燥,干燥并擦筛造粒后,将混合粉末通过150mpa压力下进行双向模压,得到压坯。将压坯放置于真空烧结炉中进行烧结,最终烧结温度为1400℃,最高温阶段保温2小时,随炉冷却后得到烧结坯。将烧结坯在氮气保护的箱式炉中以1150℃预热,保温30min后进行自由锻,经过三个道次的热加工后达到70%的压缩比,冷却后得到热加工后样品。将热加工样品在箱式炉中以840℃退火2小时,冷却后在盐浴中进行固溶处理,固溶温度为1200℃,保温15min后通过油冷冷却到室温,随后在液氮深冷箱中进行3h的深冷处理,深冷处理温度为
‑
80℃。试样回温到室温后,在箱式炉中600℃下进行等温时效处理,保温时间为2.5小时,冷却后得到所需的复合稀土增强粉末冶金高速钢,具体性能如表1中所示。
47.实施例4
48.按质量分数为:si:0.25%、mn:0.30%、cr:7%、mo:5%、w:7%、re:0.3%(ce:y=1:1),余量为fe,配取粉末。将配取的原料粉末、10wt%成型剂石蜡、1.5wt%炭黑混合,放置于行星球磨机球磨罐中进行湿式球磨,球磨过程中球磨介质为无水乙醇,保护气体为氩气,球料比为4:1,转速为180r/min,球磨时间为50h。球磨结束后在68℃真空干燥箱中进行干燥,干燥并擦筛造粒后,将混合粉末通过140mpa压力下进行双向模压,得到压坯。将压坯放
置于真空烧结炉中进行烧结,最终烧结温度为1500℃,最高温阶段保温2小时,随炉冷却后得到烧结坯。将烧结坯在氮气保护的箱式炉中以1200℃预热,到温保温30min后进行自由锻,经过三个道次的热加工后达到70%的压缩比,冷却后得到热加工后样品。将热加工样品在箱式炉中以800℃退火3小时,冷却后在盐浴中进行固溶处理,固溶温度为1150℃,保温30min后通过油冷冷却到室温,随后在液氮深冷箱中进行3h的深冷处理,深冷处理温度为
‑
90℃。试样回温到室温后,在箱式炉中630℃下进行等温时效处理,保温时间为2.5小时,冷却后得到所需的复合稀土增强粉末冶金高速钢,具体性能如表1中所示。
49.实施例5
50.按质量分数为:si:0.25%、mn:0.30%、cr:8%、mo:6%、w:12%、re:0.3%(ce:y=3:5),余量为fe,配取粉末。将配取的原料粉末、15wt%成型剂石蜡、2wt%炭黑混合,放置于行星球磨机球磨罐中进行湿式球磨,球磨过程中球磨介质为无水乙醇,保护气体为氩气,球料比为4:1,转速为180r/min,球磨时间为50h。球磨结束后在68℃真空干燥箱中进行干燥,干燥并擦筛造粒后,将混合粉末通过140mpa压力下进行双向模压,得到压坯。将压坯放置于真空烧结炉中进行烧结,最终烧结温度为1300℃,最高温阶段保温3小时,随炉冷却后得到烧结坯。将烧结坯在氮气保护的箱式炉中以1200℃预热,到温保温30min后进行自由锻,经过三个道次的热加工后达到70%的压缩比,冷却后得到热加工后样品。将热加工样品在箱式炉中以800℃退火3小时,冷却后在盐浴中进行固溶处理,固溶温度为1150℃,保温30min后通过油冷冷却到室温,随后在液氮深冷箱中进行2h的深冷处理,深冷处理温度为
‑
100℃。试样回温到室温后,在箱式炉中680℃下进行等温时效处理,保温时间为2.5小时,冷却后得到所需的复合稀土增强粉末冶金高速钢,具体性能如表1中所示。
51.实施例6
52.按质量分数为:si:0.25%、mn:0.30%、cr:4%、mo:3%、w:8%、re:0.25%(ce:y:la:nd=1:1:0.25:0.5),余量为fe,配取粉末。将配取的原料粉末、9wt%成型剂石蜡、1.8wt%炭黑混合,放置于行星球磨机球磨罐中进行湿式球磨,球磨过程中球磨介质为无水乙醇,保护气体为氩气,球料比为5:1,转速为200r/min,球磨时间为40h。球磨结束后在75℃真空干燥箱中进行干燥,干燥并擦筛造粒后,将混合粉末通过160mpa压力下进行双向模压,得到压坯。将压坯放置于真空烧结炉中进行烧结,最终烧结温度为1350℃,最高温阶段保温2小时,随炉冷却后得到烧结坯。将烧结坯在氮气保护的箱式炉中以1150℃预热,到温保温30min后进行自由锻,经过三个道次的热加工后达到70%的压缩比,冷却后得到热加工后样品。将热加工样品在箱式炉中以870℃退火2小时,冷却后在盐浴中进行固溶处理,固溶温度为1200℃,保温30min后通过油冷冷却到室温,随后在液氮深冷箱中进行3h的深冷处理,深冷处理温度为
‑
80℃。试样回温到室温后,在箱式炉中550℃下进行等温时效处理,保温时间为2.5小时,冷却后得到所需的复合稀土增强粉末冶金高速钢,具体性能如表2中所示。
53.实施例7
54.按质量分数为:si:0.25%、mn:0.30%、cr:4%、mo:3%、w:8%、re:0.25%(ce:y:la:nd=1:1:0.5:0.5),余量为fe,配取粉末。将配取的原料粉末、9wt%成型剂石蜡、1.8wt%炭黑混合,放置于行星球磨机球磨罐中进行湿式球磨,球磨过程中球磨介质为无水乙醇,保护气体为氩气,球料比为5:1,转速为200r/min,球磨时间为40h。球磨结束后在75℃真空干燥箱中进行干燥,干燥并擦筛造粒后,将混合粉末通过160mpa压力下进行双向模压,
得到压坯。将压坯放置于真空烧结炉中进行烧结,最终烧结温度为1350℃,最高温阶段保温2小时,随炉冷却后得到烧结坯。将烧结坯在氮气保护的箱式炉中以1150℃预热,到温保温30min后进行自由锻,经过三个道次的热加工后达到70%的压缩比,冷却后得到热加工后样品。将热加工样品在箱式炉中以870℃退火2小时,冷却后在盐浴中进行固溶处理,固溶温度为1200℃,保温30min后通过油冷冷却到室温,随后在液氮深冷箱中进行3h的深冷处理,深冷处理温度为
‑
80℃。试样回温到室温后,在箱式炉中550℃下进行等温时效处理,保温时间为2.5小时,冷却后得到所需的复合稀土增强粉末冶金高速钢,具体性能如表2中所示。
55.实施例8
56.按质量分数为:si:0.25%、mn:0.30%、cr:4%、mo:3%、w:8%、re:0.25%(ce:y:la:nd=1:1:0.75:0.5),余量为fe,配取粉末。将配取的原料粉末、9wt%成型剂石蜡、1.8wt%炭黑混合,放置于行星球磨机球磨罐中进行湿式球磨,球磨过程中球磨介质为无水乙醇,保护气体为氩气,球料比为5:1,转速为200r/min,球磨时间为40h。球磨结束后在75℃真空干燥箱中进行干燥,干燥并擦筛造粒后,将混合粉末通过160mpa压力下进行双向模压,得到压坯。将压坯放置于真空烧结炉中进行烧结,最终烧结温度为1350℃,最高温阶段保温2小时,随炉冷却后得到烧结坯。将烧结坯在氮气保护的箱式炉中以1150℃预热,到温保温30min后进行自由锻,经过三个道次的热加工后达到70%的压缩比,冷却后得到热加工后样品。将热加工样品在箱式炉中以870℃退火2小时,冷却后在盐浴中进行固溶处理,固溶温度为1200℃,保温30min后通过油冷冷却到室温,随后在液氮深冷箱中进行3h的深冷处理,深冷处理温度为
‑
80℃。试样回温到室温后,在箱式炉中550℃下进行等温时效处理,保温时间为2.5小时,冷却后得到所需的复合稀土增强粉末冶金高速钢,具体性能如表2中所示。
57.表1实施例1~5中样品力学性能、耐磨性及高温硬度性能测试结果
[0058][0059]
表2实施例6、7中样品力学性能、耐磨性及高温硬度性能测试结果
[0060][0061]
由表1和表2可看出,添加了复合稀土元素为ce、y、la、nd的高速钢比添加为ce、y、两种稀土元素的高速钢具有更高的硬度和抗弯强度,冲击韧性也更强,磨损量更少。且当ce:y:la:nd=1:1:0.5:0.5时,复合稀土增强的高速钢表现出了最好的性能。总体上来说,添加了ce、y、la、nd四种稀土元素的高速钢具有更好的使用效果。
[0062]
为了解决上述实际问题,改善高速钢的品质,本发明提供了一种复合稀土增强粉末冶金高速钢,钢中非金属夹杂物总量普遍减少,夹杂物尺寸变小,使钢的晶粒得到细化,并改善了钢的共晶碳化物不均匀度,以对钢基体进行强化。
[0063]
本发明通过上述对不同比例的复合稀土增强的高速钢进行性能测试,改善高速钢的品质,证明通过添加的稀土元素了ce、y、la和nd,且当ce:y:la:nd=1:1:0.5:0.5时使得成品中合金的晶粒明显细化,明显改善了合金中共晶碳化物的不均匀度,合金中非金属夹杂物总量普遍减少,夹杂物尺寸变小。使高速钢具有更好的硬度、抗弯强度、冲击韧性和磨损量,达到更好的使用效果。
[0064]
应说明的是,以上实施例仅用以说明本发明的技术方案而非限制,尽管参照较佳实施例对本发明进行了详细说明,本领域的普通技术人员应当理解,可以对本发明的技术方案进行修改或者等同替换,而不脱离本发明技术方案的精神和范围,其均应涵盖在本发明的权利要求范围当中。
再多了解一些
本文用于企业家、创业者技术爱好者查询,结果仅供参考。