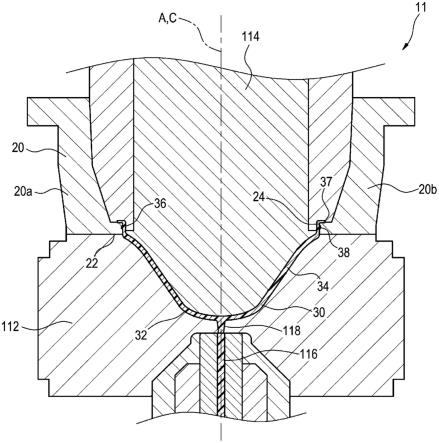
1.本发明涉及用于制造树脂广口容器的制造方法和制造设备以及树脂广口容器。
背景技术:
2.专利文献1公开了一种由片材形成的杯形聚酯容器。专利文献2公开了一种通过冷型坯式双轴拉伸吹塑成型法制造的塑料广口容器。专利文献3公开了一种通过拉伸和吹塑成型聚对苯二甲酸乙二醇酯(pet)成型的包装杯型容器。
3.引文列表
4.专利文献
5.专利文献1:jp2004-115064a
6.专利文献2:jp2004-010061a
7.专利文献3:jp2004-352332a
技术实现要素:
8.技术问题
9.在由片材成型广口容器的方法中,片材的成本通常较高,并且在真空成型或压制成型之后需要进行后处理(比如修整)。此外,在采用片材的成型方法中,容器本身很可能会被刮伤,从而难以成型具有优异外观的广口容器。此外,在通过冷型坯式双轴拉伸吹塑成型法成型广口容器的方法中,虽然在外表面上会产生一些摩擦划痕,但是可以制造在外观上优于上述方法的广口容器。然而,成本增加了。
10.另一方面,在热型坯式拉伸吹塑成型法(isbm法)中,可以在一个制造步骤中进行容器预制件的注射成型和该预制件的拉伸吹塑成型。如果在isbm法中可以缩短制造时间,则可以提供具有优异外观的容器,同时降低成本。如在wo2019/078358中所公开的,存在一种在注射成型步骤中在高温下使预制件脱模的方法,作为用于缩短isbm法中的制造时间的手段。然而,已经发现,在通过isbm法制造广口容器的情况下,在注射成型步骤中,当预制件从注射腔模具或注射芯模具中脱模时,预制件很可能会从颈部模具中脱离。
11.本发明的一个目的是提供一种能够有利地制造广口容器的用于制造树脂广口容器的制造方法和制造设以及一种新型树脂广口容器。
12.问题解决方案
13.根据本发明的一个方面的用于制造树脂广口容器的制造方法是一种用于制造树脂广口容器的热型坯式制造方法,至少包括:注射成型步骤:注射成型树脂有底预制件,所述树脂有底预制件包括第一底部、与所述第一底部相连的第一本体部以及在与所述第一底部相反侧具有与所述第一本体部相连的圆柱形广口的第一唇部,所述第一唇部包括设置在位于与所述第一本体部相反侧的边缘处并向外突出的凸缘部;以及吹塑成型步骤:吹塑成型所述注射成型的预制件,以制成树脂广口容器,其中,在所述注射成型步骤中,将熔融树脂注射到所述预制件形状的空间中,以注射成型所述预制件,所述空间通过合模注射芯模
具、注射腔模具和唇部模具而形成,使得在比所述凸缘部更靠近所述第一本体部的所述第一唇部的外周部上形成向外突出的突出部,并且包括所述突出部的所述第一唇部由包括凹部的所述唇部模具保持以使所述预制件从注射成型模具中脱模,所述凹部构造为与所述突出部接合。
14.根据本发明的一个方面的用于制造树脂广口容器的制造设备是一种用于制造树脂广口容器的热型坯式制造设备,该制造设备至少包括:注射成型部,其构造为注射成型树脂有底预制件,所述预制件包括第一底部、与所述第一底部相连的第一本体部以及在与所述第一底部相反侧具有与所述第一本体部相连的圆柱形广口的第一唇部,所述第一唇部包括设置在位于与所述第一本体部相反侧的边缘处并向外突出的凸缘部;以及吹塑成型部,其构造为吹塑成型已注射成型的所述预制件,以制成树脂广口容器,其中,所述注射成型部构造为将熔融树脂注射到所述预制件形状的空间中以注射成型所述预制件,所述空间通过合模注射芯模具、注射腔模具和唇部模具而形成,其中,所述唇部模具包括唇部外围限定部,所述唇部外围限定部构造为限定除所述凸缘部之外的所述预制件的第一唇部的外周部,并且其中,所述唇部外围限定部包括凹部,所述凹部构造为在比所述凸缘部更靠近所述第一本体部的第一唇部的外周部上限定向外突出的突出部。
15.根据本发明的一个方面的树脂广口容器是一种树脂广口容器,包括:底部;本体部,其与所述底部相连;以及唇部,其在与所述底部相反侧具有与所述本体部相连的圆柱形广口,其中,所述唇部包括设置在与位于所述底部相反侧上的边缘处并向外突出的凸缘部以及设置在比所述凸缘部更靠近所述本体部的唇部的外周部上并向外突出的突出部,并且其中,所述唇部的外径是所述广口容器的最大直径。
16.本发明的有益效果
17.根据本发明,可以提供能够有利地制造广口容器的用于制造树脂广口容器的制造方法和制造设备以及新型树脂广口容器。
附图说明
18.图1是示出根据一个实施方式的用于制造树脂广口容器的制造设备的示意图。
19.图2a是示出了根据该实施方式的用于制造树脂广口容器的制造设备所设置的唇部模具的视图。
20.图2b是图2a所示的区域b的局部放大图。
21.图3是示出了根据该实施方式的树脂广口容器的预制件的视图。
22.图4是示出了根据该实施方式的用于制造树脂广口容器的制造设备的注射成型部的视图。
23.图5是示出了根据该实施方式的温度调节部的视图。
24.图6是示出了根据该实施方式的吹塑成型部的视图。
25.图7是示出了根据该实施方式的树脂广口容器的视图。
具体实施方式
26.下文将结合附图描述本发明的一个实施方式。需要注意的是,为了方便描述,附图所示的每个构件的尺寸可以与每个实际构件的尺寸不同。
27.首先,将结合附图1描述用于制造树脂广口容器的制造设备10。图1是制造设备10的功能框图。
28.如图1所示,制造设备10是热型坯式设备,包括用于制造树脂广口容器预制件的注射成型部11、用于调节所制造的预制件的温度的温度调节部12、用于吹塑成型预制件以制造容器的吹塑成型部(吹塑装置的一个实例)13以及用于取出所制造的容器的取出部14。构造为供应作为原材料的树脂材料的注射装置15连接到注射成型部11。
29.注射成型部11、温度调节部12、吹塑成型部13和取出部14设置在围绕输送装置16旋转预定角度(在本实施方式中为90度)的位置。输送装置16包括旋转板或类似的部件。输送装置16构造为通过图2a和图2b所示的附接到输送装置16的唇部模具20来支撑预制件或广口容器(这将在后面描述),并且随着旋转板的旋转将预制件或广口容器输送到每个部件。
30.这里,将结合图2a和图2b来描述唇部模具20。图2a是通过用沿着唇部模具20的中心轴线a的平面截取唇部模具20而获得的剖视图,而图2b是图2a中区域b的局部放大图。唇部模具20构造为能够结合两个拼合模具20a、20b的打开和关闭操作(例如,在图2a中的左右方向上的移动)来支撑或释放预制件或广口容器。在两个拼合模具20a、20b闭合的状态下,唇部模具20具有大致圆柱形的形状。唇部模具20具有保持部22,该保持部22构造为在关闭状态下保持预制件或广口容器的唇部。
31.这里将结合图3来描述由本实施方式的制造设备10成型的预制件30。图3是通过用沿着预制件30的中心轴线c的平面截取预制件30而获得的剖视图。预制件30是树脂有底模制产品,包括第一底部32、与第一底部32相连的第一本体部34以及在与第一底部32相反侧具有与第一本体部34相连的圆柱形广口的第一唇部36。第一唇部36的直径d可以例如为65mm以上且110mm以下,优选地为80mm以上且95mm以下。第一唇部36是由唇部模具20的保持部22保持的部位(参见图2a)。第一唇部36在中心轴线c的方向上的长度l1可以例如为8.0mm以上且15mm以下。与唇部模具20保持接触的第一唇部36在中心轴线c的方向上的长度l2较短,并且可以例如为4.0mm以上且7.0mm以下或者约为5mm(4.5mm以上且5.5mm以下)。此外,第一唇部36和第一本体部34的外形在俯视图或水平横截面中均为圆形。此外,预制件30在中心轴线c的方向上的长度l可以例如为30mm以上且60mm以下,并且可以比第一唇部的直径d短。
32.第一唇部36具有环形凸缘部37,该环形凸缘部设置在位于与第一本体部34相反侧的边缘处并向外突出。预制件30具有环形突出部38,该环形突出部设置在比凸缘部37更靠近第一本体部34的第一唇部36的外周部上并向外突出。凸缘部37和突出部38沿着第一唇部的圆周方向形成。凸缘部37向外突出的长度可以比第一唇部36在中心轴线c的方向上的长度短。凸缘部37向外突出的长度l3可以例如为1.0mm以上且3.0mm以下,更优选地为1.5mm以上且2.5mm以下。突出部38向外突出的长度可以比凸缘部37向外突出的长度短。突出部38向外突出的长度l4可以例如为0.3mm以上且1.5mm以下,更优选地为0.4mm以上且0.6mm以下。
33.第一底部32的厚度th1可以为1.5mm以上且2.0mm以下。第一本体部34的厚度th2(第一本体部34的最大厚度)与第一底部32的厚度th1之比th2/th1可以为0.8以上且1.4以下,更优选地为0.95以上且1.25以下。在通过用沿着第一唇部36的中心轴线c的平面截取预制件30而获得的预制件30的横截面中(图3),第一本体部34相对于中心轴线c的倾角θ可以
为20
°
以上且70
°
以下,或者可以为30
°
以上且50
°
以下。预制件的横截面形状可以是大致三角形或大致梯形。
34.这里,回到图2a和图2b,再次描述唇部模具20。唇部模具20的保持部22具有唇部外围限定部24,该唇部外围限定部构造为当在注射成型部11中成型预制件30时限定除第一唇部36的凸缘部37之外的预制件30的外周部。唇部外围限定部24具有凹部26,该凹部构造为当在注射成型部11中成型预制件30时限定预制件30的突出部38。
35.随后,结合图4来描述注射成型部11。图4是示出了注射成型部11的一个方面的示意性剖视图。注射成型部11包括注射成型模具,该注射成型模具包括注射芯模具114和注射腔模具112。注射成型部11构造为经由流道116和浇口118将诸如聚酯基树脂(例如,pet:聚对苯二甲酸乙二醇酯)的合成树脂材料浇注到(通过将熔融树脂填充到)预制件30形状的空间中,以注射成型预制件30,其中该空间通过合模注射芯模具114、注射腔模具112和唇部模具20而形成。例如,5℃至20℃的冷却介质在注射芯模具114和注射腔模具112内流动,以在成型期间将这些模具保持在低温。
36.这里,结合图5来描述图1所示的温度调节部12。图5是示出了温度调节部12的一个方面的示意性剖视图。温度调节部12包括用于执行温度调节吹塑(冷却吹塑)的模具单元,该模具单元包括构造为容纳预制件30的腔模具(用于温度调节的腔模具)122和构造为以气密的方式接触预制件30并将空气送到预制件30内部的空气引入构件124。
37.腔模具122具有固定式(单一单元式)结构,该固定式结构构造为限定形状与由注射成型部11制成的预制件30大致相同的空间。例如20℃至100℃(更优选地60℃至90℃)的温度调节介质(冷却介质)在腔模具122内流动,以保持低温。
38.空气引入构件124包括中空的杆构件124a和装配芯(用于温度调节的吹塑型芯构件)124b,该杆构件包括设置在其中的空气流通孔。杆构件124a容纳在装配芯124b中,以可以上下移动。杆构件124a的末端设有内部通气口126a,可以通过该通气口排出或吸入空气。对应于预制件30或广口容器40的厚度适当地设定空气的温度。装配芯124b构造为在空气引入构件124插入(气密接触)预制件30的情况下装配(紧密接触)至第一唇部36。从而,可以防止预制件30中的空气从第一唇部36向装配芯124b的外部泄漏。杆构件124a和装配芯124b之间的间隙是用于相对于预制件30供应/排出空气的空气流通路径。由装配芯124b的末端和杆构件124a形成的间隙构成外部通气口126b,空气可以通过该外部通气口排出或吸入。内部通气口126a和外部通气口126b可以分别用作吹气口和排气口。
39.需要注意的是,代替或结合上述方法,温度调节部12可以采用利用温度调节腔模具和温度调节芯模具(温度调节杆模)以及诸如各种红外加热器类型、red类型、电磁波加热类型等的温度调节装置夹住预制件的方法。需要注意的是,可以省略温度调节部12。例如,可以通过采用温度调节部12来改善广口容器的厚度分布。然而,从制造效率的角度来看,优选地采用一种方法,其中在预制件与上述温度调节腔模具接触的状态下,通过在预制件内部通入空气来同时冷却预制件的内部和外部。此外,当采用该方法时,优选地使外部温度调节腔模具的冷却强度高于内部空气的冷却强度。
40.这里,结合图6来描述图1所示的温度调节部12。图6是示出了吹塑成型部13的一个方面的示意性剖视图。吹塑成型部13包括拉伸杆132、吹塑芯模具134、吹塑腔模具136以及吹塑底模具138。吹塑成型部13构造为从吹塑芯模具134引入空气,以将预制件30膨胀成由
吹塑腔模具136和吹塑底模具138限定的形状,并在利用例如拉伸杆132拉伸注射成型的预制件30的同时形成广口容器。
41.随后,结合图7来描述由本实施方式的制造设备10成型的广口容器40。图7是广口容器40的侧视图。广口容器40是杯形容器,包括第二底部42、与第二底部42相连的第二本体部44以及在与第二底部42相反侧具有与第二本体部44相连的圆柱形广口的第二唇部(开口部)46。第二唇部46包括设置在位于与第二本体部44相反侧的边缘处并向外突出的环形凸缘部47以及设置在比凸缘部47更靠近第二本体部44的第二唇部46的外周部上并向外突出的环形突出部48。第二唇部46的凸缘部47的外径是广口容器40的最大直径。广口容器40与预制件30的垂直拉伸比(svr)可以大于或等于4.0且小于或等于6.0。广口容器40的第二唇部46的直径以及凸缘部47和突出部48的尺寸和形状分别与预制件30的第一唇部36的直径以及凸缘部37和突出部38的尺寸和形状相同。通过在吹塑成型步骤中拉伸预制件30的第一唇部36,广口容器40的第二唇部46的长度l1'可以大于第一唇部36的长度l1。在第二唇部46上形成有唇部模具20的分型线。更具体地,在第一唇部36和第二唇部46上形成有作为构成唇部模具20的拼合模具20a、20b的接触面的迹线在垂直方向上延伸的两条垂直线状分型线以及作为唇部模具20和注射腔模具112的接触面的迹线在圆周方向上延伸的一条环形分型线。这些分型线形成在唇部模具20的保持部22的范围内(预制件30的第一唇部36的长度l2的范围内)。此外,在第二底部42的下表面的中心区域上形成有从浇口118排出的熔融树脂的注射痕迹(横截面为圆形)。
42.随后,描述根据本实施方式的用于制造广口容器的制造方法。该制造方法是热型坯式方法,包括注射成型预制件30的注射成型步骤、将注射成型的预制件30的温度调节至适于吹塑成型的温度的温度调节步骤以及吹塑成型预制件30以成型广口容器40的吹塑成型步骤。
43.结合图4来描述注射成型步骤。在注射成型步骤中,熔融树脂经由流道116和浇口118注射到通过合模注射芯模具114、注射腔模具112和唇部模具20而形成的预制件30形状的空间中。在预定时间过去之后,将注射芯模具114和唇部模具20拉起,以使预制件30从注射腔模具112中脱模。此时,预制件30的突出部38与唇部模具20的凹部26接合(参见图2b)。此外,唇部模具20的保持部22将预制件30的凸缘部37卡住。在这种状态下,第一唇部36由唇部模具20保持,并且预制件30从注射腔模具112脱模。这里,在熔融树脂注射完成到预制件30脱模的时间缩短的情况下,预制件30在高温状态下脱模。当在高温下从注射成型模具中脱模预制件30时,在注射成型模具中熔融树脂注射完成到预制件30脱模的冷却时间可以设定为例如0.0至1.5秒。需要注意的是,上述“熔融树脂的注射”指的是包括压力保持步骤的树脂填充步骤。树脂填充步骤的时间可以设定为例如2.5至4.5秒。此外,将脱模后的预制件30输送到温度调节步骤之前的预定时间可以设定为例如2.0至6.0秒的时间,在该时间内,例如,当在高温下使预制件30从注射成型模具脱模时,预制件30的外表面温度在脱模后快速上升且变成大约110℃以上且140℃以下。
44.在温度调节步骤中,在上述温度调节部12(图5)中将在注射成型步骤中成型的预制件30的温度调节到适合吹塑成型的温度。首先,将预制件30容纳在腔模具122的预制件形状的空间中。接着,将空气引入构件124插入(气密接触)容纳在腔模具122中的预制件30。随后,执行打开内部通气口126a以从内部通气口126a引入空气并将空气经由外部通气口126b
排放到预制件30的外部的冷却吹塑操作。此时,由于从内部通气口126a连续喷出空气,因此通过在预制件30中流动的空气的对流从内侧来对预制件30进行冷却。此外,由于预制件30与腔模具122连续接触,因此还从外侧对预制件进行冷却,同时对其进行温度调节,并且还减少了在注射成型过程中造成的温度不均。
45.需要注意的是,虽然可以省略温度调节步骤,但是例如通过采用温度调节部12可以改善广口容器的厚度分布。此外,在注射成型步骤中在高温下使预制件30脱模的情况下,可以在温度调节步骤中利用冷却空气等将预制件30冷却到预定温度,并且例如,预制件30的外表面温度可以从将预制件运送到温度调节部12中的时间开始降低大约30℃以上且50℃以下。通过在注射成型步骤中在高温下使预制件30脱模并在温度调节步骤中冷却预制件,可以在缩短循环时间的同时成型具有优异外观的广口容器40。此外,在温度调节步骤中,可以将构造为与预制件30的第一底部32的内表面接触的冷却杆件设置在杆构件124a的末端。
46.在吹塑成型步骤中,将预制件30容纳在由与广口容器40的形状相对应的吹塑腔模具136和吹塑底模具138限定的型腔中(参见图7),然后通过从吹塑芯模具134引入吹塑空气来使预制件30膨胀,同时可选地通过拉伸杆132拉伸预制件,以制成广口容器40(图6)。之后,从吹塑部件13的模具中释放广口容器40,并且将广口容器40输送到取出部14并取出。通过上述过程,制造出了广口容器40。需要注意的是,可以在本实施方式的制造方法中制造的广口容器不限于图7所示的特定广口容器40。
47.在本实施方式中描述的预制件30的第一唇部36和广口容器40的第二唇部46彼此对应,并且这些唇部在预制件30的中心轴线c的方向上的长度较短。因此,当在注射成型步骤中使预制件和广口容器从模具中脱模时,预制件和广口容器很可能会从唇部模具20中脱离。
48.在本实施方式中描述的包括注射成型步骤和吹塑成型步骤的热型坯式制造方法中,注射成型预制件30,使得预制件30的第一唇部36包括突出部38,并且当从注射腔模具112中拔出预制件30时,预制件30的突出部38与唇部模具20的凹部26接合,从而可以防止预制件30的脱离(图2b和图4)。从而,可以适当地制造广口容器40。
49.此外,本实施方式中描述的广口容器40相对于预制件30在垂直方向上的拉伸比较大,因此本体部在垂直方向上的厚度分布可能会变得不均匀。此外,在广口容器40的第二底部42的注射成型过程中,可能会在浇口外围的部位中出现泛白(结晶)现象。
50.在热型坯式制造方法(其中在注射成型步骤中在高温下使预制件30脱模)(包括在本实施方式中描述的注射成型步骤、温度调节步骤以及吹塑成型步骤)中,注射成型预制件30,使得在通过沿着沿第一唇部36的中心轴线c的平面截取预制件30而获得的预制件30的横截面中第一底部32的厚度th1变为1.5mm以上或者第一底部32的厚度th1与第一本体部34的厚度th2之比变为0.8以上(参见图3)并且第一本体部34相对于中心轴线c的倾角为20
°
以上且70
°
以下(参见图3),并且在温度调节步骤中对其进行冷却。从而,可以改善通过高速isbm法制造的广口容器40在垂直方向上的厚度分布。此外,可以适当地减少在注射成型步骤中广口容器40在熔融树脂的浇口118外围的泛白现象,并且可以制造出外观更优异的广口容器(参见图4)。此外,广口容器40的第二底部42的可成形性(可转印性)也得到了改善。
51.事实上,根据发明人的判断,发现在预制件30的第一底部32的厚度th1为1.4mm并
且第一本体部34的厚度th2为2.0mm的情况下,广口容器40在浇口的外围出现轻微泛白现象。另一方面,在预制件30的第一底部32的厚度th1为1.8mm并且第一本体部34的厚度th2为2.0mm的情况下,广口容器40在浇口的外围几乎没有出现泛白现象,并且观察到高透明度。发明人认为上述结果的原因是浇口118和注射芯模具114的底部之间距离的增加减小了熔融树脂流入时的树脂阻力,并且还减小了剪切热的产生,同时抑制了成型后的预制件30的第一底部32处于异常高温状态。因此,减少了由于第一底部32的缓慢冷却而导致的泛白(结晶)。此外,发明人认为预制件30的第一本体部34比相关技术更厚,使得即使在通过高速isbm法的温度调节步骤冷却之后,在吹塑成型之前也能确保有足够的余热,这被认为能有效改善广口容器40的第二本体部44的厚度不均。
52.此外,在本实施方式中描述的广口容器40的成型中,可以通过使温度调节腔模或吹塑腔模具的型腔表面变粗糙来使广口容器40的内表面和外表面具有不同的表面粗糙度。从而,当使广口容器40彼此重叠或分离时,可以减小广口容器40之间的阻力,并且可以提高可操作性。
53.需要注意的是,本发明不限于上述实施方式,并且可以适当地对本发明进行自由修改和改进。此外,只要能够实现本发明,上述实施方式中每个元件的材料、形状、尺寸、数值、形式、数量、设置位置等可以是任意的且没有特别限制。
54.在下文中,列出了从上述实施方式及其修改中提取的方面。
55.[1]一种用于制造树脂广口容器的热型坯式制造方法,该制造方法至少包括:注射成型步骤:注射成型树脂有底预制件,该树脂有底预制件包括第一底部、与第一底部相连的第一本体部以及在与第一底部相反侧具有与第一本体部相连的圆柱形广口的第一唇部,该第一唇部包括设置在位于与第一本体部相反侧的边缘处并向外突出的凸缘部;以及吹塑成型步骤:吹塑成型注射成型的预制件,以制成树脂广口容器,其中,在注射成型步骤中,将熔融树脂注射到预制件形状的空间中,以注射成型预制件,该空间通过合模注射芯模具、注射腔模具和唇部模具而形成,使得在比凸缘部更靠近第一本体部的第一唇部的外周部上形成向外突出的突出部,并且包括突出部的第一唇部由包括凹部的唇部模具保持以使预制件从注射成型模具中脱模,该凹部构造为与突出部接合。
[0056]
[2]根据[1]所述的制造方法,进一步包括:温度调节步骤:在注射成型步骤和吹塑成型步骤之间,将注射成型的预制件的温度调节至适于吹塑成型的温度,其中,在注射成型步骤中,注射成型预制件,使得第一底部的厚度变为1.5mm以上或者第一底部的厚度与第一本体部的厚度之比变为0.8以上,并且注射成型预制件,使得在通过沿着沿第一唇部的中心轴线的平面截取预制件而获得的预制件的横截面中第一本体部相对于中心轴线的倾角变为20
°
以上且70
°
以下,并且其中在注射成型步骤中在高温下使预制件脱模,在温度调节步骤中将预制件冷却到适于吹塑成型的温度,并且在吹塑成型步骤中通过拉伸吹塑成型来制成树脂广口容器。
[0057]
[3]根据[1]或[2]所述的制造方法,其中,在吹塑成型步骤中,制造树脂广口容器,该树脂广口容器包括第二底部、与第二底部相连的第二本体部以及在与第二底部相反侧具有与第二本体部相连的圆柱形广口的第二唇部。
[0058]
[4]一种用于制造树脂广口容器的热型坯式制造设备,该制造设备至少包括:注射成型部,构造为注射成型树脂有底预制件,该树脂有底预制件包括第一底部、与第一底部相
连的第一本体部以及在与第一底部相反侧具有与第一本体部相连的圆柱形广口的第一唇部,该第一唇部包括设置在位于与第一本体部相反侧的边缘处并向外突出的凸缘部;以及吹塑成型部,构造为吹塑成型注射成型的预制件,以制成树脂广口容器,其中该注射成型部构造为将熔融树脂注射到预制件形状的空间中以注射成型预制件,该空间通过合模注射芯模具、注射腔模具和唇部模具而形成,其中唇部模具包括唇部外围限定部,该唇部外围限定部构造为限定除凸缘部之外的预制件的第一唇部的外周部,并且其中唇部外围限定部包括凹部,该凹部构造为在比凸缘部更靠近第一本体部的第一唇部的外周部上限定向外突出的突出部。
[0059]
[5]一种树脂广口容器,包括:底部;本体部,与底部相连;以及唇部,在与底部相反侧具有与本体部相连的圆柱形广口,其中该唇部包括设置在位于与底部相反侧上的边缘处并向外突出的凸缘部以及设置在比凸缘部更靠近本体部的唇部的外周部上并向外突出的突出部,并且其中唇部的外径是该广口容器的最大直径。
[0060]
本技术基于2020年4月27日提交的日本专利申请(日本专利申请第2020-078536号),其全部内容通过引用并入本文。此外,本文引用的所有参考文献的全部内容都并入本文。
[0061]
附图标记列表
[0062]
10:制造设备,11:注射成型部,12:温度调节部,13:吹塑成型部,14:取出部,15:注射装置,16:输送装置,20:唇部模具,22:保持部,24:唇部外围限定部,26:凹部,30:预制件,31:浇口痕迹,32:第一底部,34:第一本体部,36:第一唇部,37:凸缘部,38:突出部,40:广口容器,42:第二底部,44:第二本体部,46:第二唇部,112:注射腔模具,114:注射芯模具,116:流道,118:浇口,122:腔模,124:空气引入构件,124a:杆构件,124b:装配芯,126a:内部通气口,126b:外部通气口,132:拉伸杆,134:吹塑芯模具,136:吹塑腔模具,138:吹塑底模具
再多了解一些
本文用于创业者技术爱好者查询,仅供学习研究,如用于商业用途,请联系技术所有人。