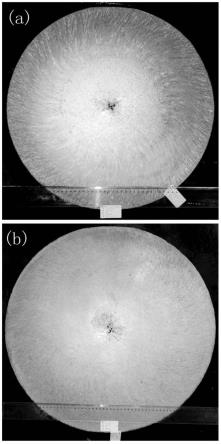
一种超超临界高压锅炉钢p92连铸大圆坯的生产工艺
技术领域
1.本发明属于p92钢冶炼技术领域,具体涉及一种超超临界高压锅炉钢p92连铸大圆坯的生产工艺。
背景技术:
2.电站锅炉受压部件用钢主要分为:碳钢、低合金cr-mo钢和奥氏体耐热钢三大系列。碳素、低合金cr-mo钢由于耐热性差、高温持久强度低,所以使用温度受到了很大的限制,因此在早期开发的超(超)临界机组中,大量使用了奥氏体钢,如tp304h、tp347h等。为缓解能源和环境危机,全球对能源和环保问题更加重视,大力发展蒸汽温度超过600℃的超超临界火力发电机组。当p91钢使用温度超过600℃时材料老化加速,p91已不能满足长期安全运行的要求。p92钢p92属于美标马氏体耐热钢,执行标准:astma335,在p91钢的基础上适当降低钼元素的含量,同时加入一定量的钨以将材料的钼当量提高,p92钢具有抗热疲劳性能好,导热系数高,热膨胀系数小等优点,整体性能优于奥氏体不锈钢,是可以部分替代奥氏体钢的候选材料之一,并可用于壁温≤625℃的主蒸汽管道。
3.现有p92连铸大圆坯生产工艺存在以下缺陷;(1)由于p92钢冶炼不合理导致化学成分未能有效控制、lf调合金成分压力较大,硫化物及氧化物等非金属夹杂掺杂在钢材中而使钢材性能降低。(2)p92钢提高了合金成分,连铸凝固过程中,铸坯表面温度回升大、热应力作用使铸坯中心部位撕开,形成中心裂纹,柱状晶发达柱状晶在铸坯中心相遇形成“搭桥”,进一步促进中心裂纹,中心裂纹变大,当晶桥下面的钢液凝固收缩时得不到上部钢液的补充时形成疏松或缩孔,凝固末端富集溶质元素被吸入到空穴中形成中心偏析,无法在后续工序中完全消除,低倍质量较差将严重钢材的冲击韧性、弯曲性能和抗疲劳强度。(3)退火阶段组织应力未能得到完全释放使退火后硬度升高,导致圆坯开裂风险,从而无法满足超超临界高压锅炉钢性能要求。
技术实现要素:
4.本发明旨在至少在一定程度上解决上述技术问题之一,本发明提供一种超超临界高压锅炉钢p92连铸大圆坯的生产工艺,通过电炉、lf精炼、vd、连铸、退火的设定形成一套完整的大规格高压锅炉钢连铸圆坯的生产工艺,有效控制中心裂纹、化学成分、降低组织及热应力,满足超超临界高压锅炉钢性能要求。
5.本发明解决其技术问题所采用的技术方案是:
6.一种超超临界高压锅炉钢p92连铸大圆坯的生产工艺,包括以下步骤:
7.s1、电炉炼钢:将铁水比≥85%的炼钢原料经电炉炼钢得到钢水;
8.钢种冶炼钢包选择:大小修包第一次不得使用在该钢种上,防止夹杂物、过热度、h等超标,钢包上一次不得盛装控ti或控s钢水,防止ti、s超标;
9.控制电炉出钢终点c:≤0.04%,出钢碳尽量低,防止合金及电机增碳导致成品碳超标;
10.控制电炉出钢目标p:≤0.005%,电炉出钢严禁下渣,有效控制钢水回p;
11.控制目标温度t≥1630℃,出钢温度控制较高,有利于合金融化,尤其是钨铁,减轻lf调合金成分压力;
12.出钢前打开底吹氩气,出钢过程中全程吹氩,前期大氩气搅拌,保证出钢铁水与合金充分接触融化合金化,后期视包内钢水翻腾情况调整氩气至正常或软吹,保证钢包液面有钢水翻滚,避免钢水大翻氧化钢液,出钢严禁下渣;
13.出钢过程中,每炉90-110t钢水中按顺序加入150-170kg铝、250-260kg金属锰、2000kg低碳铬铁(含碳0.15~0.50%)、300kg促净剂(cao53.5%,sio23.5%,al2o334.3%,mgo8.5%)和900kg石灰,前期初步合金化并充分脱氧,出钢结束后及时吊至lf工位;
14.s2、lf精炼:将步骤s1的钢水经lf精炼处理,lf精炼前期视炉渣流动情况补加0-100kg石灰或促净剂进行cao调渣,若补加渣料尽量在取第一个样之前完成;
15.钢水进站迅速造白渣,渣面采用硅铁粉 铝豆按质量比20:1组成的扩散脱氧剂扩散脱氧,冶炼中后期少量多批加入扩散脱氧剂以保持还原性气氛,扩散脱氧剂用量≥3.0kg/t;
16.lf精炼过程保持氩气通畅,lf精炼前期在1630℃以上分批次加入钨铁(few80-c),最后一批根据钨铁的量达到目标下限0.1%时谨慎添加,防止有未熔化的钨铁存在,冶炼前期不得加入硅铁合金,适当调大氩气搅拌,氩气流量为300-500nl/min,促进脱氧及合金化;
17.lf精炼中期加合金阶段均保持氩气中等氩气强度,氩气流量为200-300nl/min,lf精炼后期避免钢水翻滚氧化,氩气流量为100-200nl/min,通过此工艺合金成分得到精准控制;
18.s3、vd真空处理:将经步骤s2的钢水进vd站真空处理,控制最高真空度≤67pa,高真空保持时间≥10min,氮气软吹时间≥20min,去除钢水中的h,确保夹杂物充分上浮,提高钢水纯净度,控制a、b、c、d类夹杂在1.5级以内,ds类夹杂≤1.0级;破空后加入b铁(feb18c0.5b),每炉14kg,用于调质,且b铁用量少,在后期加入更精准;
19.s4、连铸:将经步骤s3的钢水通过连铸机全程保护浇铸防止二次氧化,选用较高的过热度浇注,过热度在30-45℃之间,高过热度降低钢水粘度,促进钢水流动性,有利于补缩,降低圆坯中心缩孔及中心裂纹等级;
20.采用两段水冷却配合结晶器电磁搅拌、铸流搅拌和末端电磁搅拌:
21.两段水冷却全部开启,一冷水流量为3600-5000l/min,一冷水快冷增加柱状晶比例使钢坯致密性更好,二冷水一区水流量为34-42l/min,二冷水二区水流量为7-58l/min,避免不合理的二冷配水使铸坯表面温度波动太大而出现温度回升、热应力引起中心裂纹现象,有效控制枝晶产生,有利于中心缩孔及中心裂纹处补充钢水;
22.结晶器电磁搅拌电流250-300a、频率为1-4hz,铸流搅拌电流为100-200a、频率为5-10hz,末端电磁搅拌电流为1000-1110a、频率为4-10hz,控制拉速为0.28m/min得到连铸大圆坯,采用三段电磁搅拌,有效控制低倍质量及中心偏析;
23.连铸大圆坯的最大直径最小规格控制的连铸大圆坯中心裂纹长度在40mm以内,的连铸大圆坯中心裂纹长度在65mm以内,的连铸大圆坯中心裂纹长度在70mm以内,的连铸大圆坯中心裂纹长度在90mm以内;
24.s5、缓冷退火:将步骤s4的连铸大圆坯在9机架矫直机矫直后被切割成圆坯定尺,
圆坯定尺直接装入台车炉进行热送退火,装炉前圆坯定尺表面温度≥550℃,缓冷退火程序为以≤80℃/h的速度升温至780
±
5℃、保温19-30h,后随炉冷却温降至450
±
5℃,后以≤40℃/h的速度温降至250℃后出炉得到连铸大圆坯,通过该工艺使连铸大圆坯经过完全退火,组织应力得到完全释放,硬度明显减低,硬度在230hbw以下,消除连铸圆坯组织应力及热应力,连铸圆坯切面无应力裂纹,避免了连铸圆坯开裂的风险,退火后的连铸大圆坯经精整、检测后入库,可以用于电站高压锅炉,通过穿管热处理后生产的大规格无缝管满足超超临界蒸汽管道对原材料性能的苛刻要求。
25.上述生产工艺的超超临界高压锅炉钢p92连铸大圆坯,其组成成分按质量分数计为:c:0.08~0.12%、si:0.20~0.40%、mn:0.30~0.50%、p≤0.013%、s:≤0.005%、cr:8.50~9.00%、v:0.15~0.25%、al:≤0.025%、ni:0.12~0.18%、nb:0.04~0.09%、mo:0.31~0.35%、w:1.55~1.75%、cu:≤0.10%、ti:≤0.008%、b:0.001~0.006%、h:≤1.5ppm、o:≤25ppm、n:0.050~0.065%,余量为fe和不可避免的杂质。
26.与现有技术相比,本发明的有益效果是:
27.(1)本发明电炉炼钢钢包选择防止夹杂物、过热度、h、ti、s等超标,出钢碳尽量低,有效控制钢水回p,高出钢温度减轻lf调合金成分压力,前期初步合金化并充分脱氧;lf精炼采用硅铁粉 铝豆扩散脱氧,中后期少量多批加入扩散脱氧剂以保持还原性气氛,在1630℃以上分批次加入钨铁保证钨铁熔化,氩气搅拌促进脱氧及合金化;vd真空处理确保夹杂物充分上浮,提高钢水纯净度,破空后加入b铁,使合金成分得到精准控制,夹杂物得到有效控制,a、b、c、d类夹杂在1.5级以内,ds类夹杂≤1.0级。
28.(2)本发明采用高过热度降低钢水粘度,促进钢水流动性,有利于补缩,降低圆坯中心缩孔及中心裂纹等级,采用合适参数的两段水冷却配合三段电磁搅拌,效控制枝晶产生,有利于中心缩孔及中心裂纹处补充钢水,使的连铸大圆坯中心裂纹长度分别在40mm、65mm、70mm、90mm以内,有效控制了中心裂纹、中心偏析和低倍质量,不但没增大且略有好转。
29.(3)缓冷退火阶段连铸大圆坯经过完全退火,组织应力得到完全释放,硬度明显减低在230hbw以下,消除连铸大圆坯组织应力及热应力,连铸大圆坯切面无应力裂纹,避免了连铸大圆坯开裂的风险。
30.综上,本发明通过炼钢工艺、连铸、退火工艺研究生产优质大圆坯,可以有效控制中心裂纹、化学成分、降低组织及热应力,用于电站高压锅炉,通过穿管热处理后生产的大规格无缝管满足超超临界蒸汽管道对原材料性能的苛刻要求。
附图说明
31.本发明的上述和/或附加的方面和优点从结合下面附图对实施例的描述中将变得明显和容易理解,其中:
32.图1是本发明实施例2和比较例1的低倍组织对比图。
33.图1(a)表示实施例2的低倍组织图;图1(b)表示比较例1的低倍组织图。
具体实施方式
34.下面详细描述本发明的实施例,所述实施例的示例在附图中示出,其中自始至终
相同或类似的标号表示相同或类似的元件或具有相同或类似功能的元件。下面通过参考附图描述的实施例是示例性的,旨在用于解释本发明,而不能理解为对本发明的限制。
35.实施例1:
36.为本发明所述一种超超临界高压锅炉钢p92连铸大圆坯的生产工艺的一种较佳实施方式,工艺包括将炼钢原料按如下步骤:电炉炼钢
→
lf精炼
→
vd真空处理
→
连铸
→
缓冷
→
退火
→
精整
→
检测
→
入库处理,得到规格的连铸大圆坯,以gb/t223标准检测成分,所述连铸大圆坯组成成分按质量分数(单位,wt%)计为c:0.09%、si:0.26%、mn:0.44%、p:0.009%、s:0.0015%、cr:8.8%、ni:0.15%、cu:0.02%、mo:0.32%、v:0.15%、nb:0.05%、ti:0.0016%、al:0.006%、w:1.59%、b:0.0016%、h:1.0ppm、o:27ppm、n:500ppm,余量为fe和不可避免的杂质。
37.实施例2:
38.为本发明所述一种超超临界高压锅炉钢p92连铸大圆坯的生产工艺的一种较佳实施方式,工艺包括将炼钢原料按如下步骤:电炉炼钢
→
lf精炼
→
vd真空处理
→
连铸
→
缓冷
→
退火
→
精整
→
检测
→
入库处理,得到规格的连铸大圆坯,以gb/t223标准检测成分,所述连铸大圆坯组成成分按质量分数(单位,wt%)计为c:0.10%、si:0.24%、mn:0.45%、p:0.010%、s:0.0017%、cr:8.6%、ni:0.15%、cu:0.021%、mo:0.33%、v:0.16%、nb:0.05%、ti:0.0018%、al:0.007%、w:1.58%、b:0.0017%、h:1.0ppm、o:27ppm、n:520ppm,余量为fe和不可避免的杂质。
39.实施例3:
40.为本发明所述一种超超临界高压锅炉钢p92连铸大圆坯的生产工艺的一种较佳实施方式,工艺包括将炼钢原料按如下步骤:电炉炼钢
→
lf精炼
→
vd真空处理
→
连铸
→
缓冷
→
退火
→
精整
→
检测
→
入库处理,得到规格的连铸大圆坯,以gb/t223标准检测成分,所述连铸大圆坯组成成分按质量分数(单位,wt%)计为c:0.11%、si:0.28%、mn:0.42%、p:0.011%、s:0.0012%、cr:8.7%、ni:0.15%、cu:0.023%、mo:0.34%、v:0.17%、nb:0.05%、ti:0.0019%、al:0.009%、w:1.59%、b:0.0017%、h:1.2ppm、o:30ppm、n:590ppm,余量为fe和不可避免的杂质。
41.实施例4:
42.为本发明所述一种超超临界高压锅炉钢p92连铸大圆坯的生产工艺的一种较佳实施方式,工艺包括将炼钢原料按如下步骤:电炉炼钢
→
lf精炼
→
vd真空处理
→
连铸
→
缓冷
→
退火
→
精整
→
检测
→
入库处理,得到规格的连铸大圆坯,以gb/t223标准检测成分,所述连铸大圆坯组成成分按质量分数(单位,wt%)计为c:0.11%、si:0.28%、mn:0.43%、p:0.011%、s:0.0013%、cr:8.7%、ni:0.15%、cu:0.023%、mo:0.34%、v:0.17%、nb:0.05%、ti:0.0019%、al:0.009%、w:1.58%、b:0.0017%、h:1.2ppm、o:28ppm、n:590ppm,余量为fe和不可避免的杂质。
43.上述实施例1-4的生产工艺具体包括以下步骤:
44.s1、电炉炼钢:将铁水比≥85%的炼钢原料经电炉炼钢得到钢水;
45.钢种冶炼钢包选择:大小修包第一次不得使用在该钢种上,钢包上一次不得盛装控ti或控s钢水;控制电炉出钢终点c:≤0.04%;控制电炉出钢目标p:≤0.005%;控制目标温度t≥1630℃;出钢前打开底吹氩气,出钢过程中全程吹氩,前期大氩气搅拌,后期视包内
钢水翻腾情况调整氩气至正常或软吹,保证钢包液面有钢水翻滚,避免钢水大翻氧化钢液,出钢严禁下渣;
46.出钢过程中,每炉90-110t钢水中按顺序加入150-170kg铝、250-260kg金属锰、2000kg低碳铬铁(含碳0.15~0.50%)、300kg促净剂(cao53.5%,sio23.5%,al2o334.3%,mgo8.5%)和900kg石灰,前期初步合金化并充分脱氧,出钢结束后及时吊至lf工位;
47.s2、lf精炼:将步骤s1的钢水经lf精炼处理,lf精炼前期视炉渣流动情况补加0-100kg石灰或促净剂进行cao调渣,若补加渣料尽量在取第一个样之前完成;
48.钢水进站迅速造白渣,渣面采用硅铁粉 铝豆按质量比20:1组成的扩散脱氧剂扩散脱氧,冶炼中后期少量多批加入扩散脱氧剂以保持还原性气氛,扩散脱氧剂用量≥3.0kg/t;
49.lf精炼过程保持氩气通畅,lf精炼前期在1630℃以上分批次加入钨铁(few80-c),第一批加1000kg,第二批加1000kg,第三批根据钨铁的量达到w成分目标下限0.1%时谨慎添加,防止有未熔化的钨铁存在,冶炼前期不得加入硅铁合金,适当调大氩气搅拌,氩气流量为300-500nl/min;lf精炼中期依据连铸大圆坯的目标成分加合金调质,均保持氩气中等氩气强度,氩气流量为200-300nl/min;lf精炼后期避免钢水翻滚氧化,氩气流量为100-200nl/min;
50.s3、vd真空处理:将经步骤s2的钢水进vd站真空处理,控制最高真空度≤67pa,高真空保持时间≥10min,氮气软吹时间≥20min;破空后加入b铁(feb18c0.5b),每炉14kg;
51.s4、连铸:将经步骤s3的钢水通过r17m连铸机全程保护浇铸防止二次氧化,采用两段水冷却配合结晶器电磁搅拌、铸流搅拌和末端电磁搅拌,控制拉速为0.28m/min,具体条件参数和按检测标准yb/t153检测的连铸坯中心裂纹均在长度如下表1所示:
[0052][0053]
由上表1表明,采用高过热度降低钢水粘度,促进钢水流动性,有利于补缩,降低圆坯中心缩孔及中心裂纹等级,采用合适参数的两段水冷却配合结晶器电磁搅拌、铸流搅拌和末端电磁搅拌,的连铸大圆坯中心裂纹长度在40mm以内,的连铸大圆坯中心裂纹长度在65mm以内,的连铸大圆坯中心裂纹长度在70mm以内,的连铸大圆坯中心裂纹长度在90mm以内,一冷水快冷增加柱状晶比例使钢坯致密性更好,二冷水控制铸坯表面温度波动和温度回升,降低热应力引起中心裂纹现象,有效控制枝晶产生,有利于中心缩孔及中心裂纹处补充钢水。
[0054]
s5、缓冷退火:将步骤s4的连铸大圆坯在9机架矫直机矫直后被切割成圆坯定尺,圆坯定尺直接装入台车炉进行热送退火,装炉前圆坯定尺表面温度≥550℃,缓冷退火程序为以≤80℃/h的速度升温至780
±
5℃、保温19-30h,后随炉冷却温降至450
±
5℃,后以≤40℃/h的速度温降至250℃后出炉得到连铸大圆坯,退火后的连铸大圆坯经精整、检测后入
库。
[0055]
将上述实施例1-4的通过连铸大圆坯取样锻打(锻比大于5),按gb/t10561检测夹杂物成分结果如下表2所示:
[0056]
种类aeabebcecdedds实施例1001.00000.51.01.0实施例2000.50000.51.01.0实施例3000.50000.51.00.5实施例4000.50000.51.00.5
[0057]
本发明电炉炼钢钢包选择防止夹杂物、过热度、h、ti、s等超标,出钢碳尽量低,有效控制钢水回p,高出钢温度减轻lf调合金成分压力;lf精炼采用硅铁粉 铝豆扩散脱氧,中后期少量多批加入扩散脱氧剂以保持还原性气氛,在1630℃以上分批次加入钨铁保证钨铁熔化,氩气搅拌促进脱氧及合金化;vd真空处理确保夹杂物充分上浮,提高钢水纯净度,破空后加入b铁,使合金成分得到精准控制,由上表2可知,夹杂物得到有效控制,a、b、c、d类夹杂在1.5级以内,ds类夹杂≤1.0级。
[0058]
按照gb231-84《金属布氏硬度试验方法》测试退火后的连铸大圆坯硬度,结果如下表3所示:
[0059]
种类硬度值1/hbw硬度值2/hbw硬度值3/hbw平均硬度实施例1210200197202实施例2205213207208实施例3215207223215实施例4218210213214
[0060]
缓冷退火阶段在9机架矫直机矫直后≥550℃以≤80℃/h的速度升温至780
±
5℃、保温19-30h,后随炉冷却温降至450
±
5℃,后以≤40℃/h的速度温降至250℃后出炉,连铸大圆坯经过完全退火,组织应力得到完全释放,硬度明显减低,硬度在230hbw以下,消除连铸大圆坯组织应力及热应力,连铸大圆坯切面无应力裂纹,避免了连铸大圆坯开裂的风险。
[0061]
比较例1:通过电炉炼钢、lf精炼、vd真空处理、连铸、缓冷(热送退火)获得圆钢,其组成成分质量百分比的化学成分(单位,wt%):c:0.09%、si:0.31%、mn:0.44%、p:0.009%、s:0.001%、cr:8.5%、ni:0.16%、cu:0.03%、mo:0.93%、v:0.19%、nb:0.07%、ti:0.0019%、al:0.009%、w:0.005%、b:0.0005%、h:1.2ppm、o:30ppm、n:590ppm,其他为fe及残余元素。
[0062]
比较例2:通过电炉炼钢、lf精炼、vd真空处理、连铸、缓冷(热送退火)获得圆钢,其组成成分质量百分比的化学成分(单位,wt%):c:0.10%、si:0.30%、mn:0.43%、p:0.010%、s:0.0012%、cr:8.4%、ni:0.16%、cu:0.03%、mo:0.94%、v:0.19%、nb:0.072%、ti:0.0015%、al:0.007%、w:0.005%、b:0.0004%、h:1.2ppm、o:30ppm、n:590ppm,其他为fe及残余元素。
[0063]
按照gbt226标准进行低倍组织及缺陷酸蚀检验得到的附图1可知,本发明较比较例提高了合金成分,按常规多加合金后中心裂纹应该变大,但本发明通过电炉、lf精炼、vd、连铸、退火工艺的设定,形成一套完整的大规格高压锅炉钢连铸圆坯的生产工艺,有效控制
了中心裂纹、中心偏析和低倍质量,不但没增大,且略有好转。
[0064]
将实施例1-4与比较例1-2得到的连铸坯进一步加工成钢管,按照《金属材料室温拉伸试验工艺》gb/t228标准检测拉伸性能,按照《金属材料弯曲试验工艺》gb/t232标准检测弯曲性能,以金属材料夏比摆锤冲击试验工艺gbt229标准进行冲击试验,性能测试结果如下表4所示:
[0065][0066]
由上表可知,本发明通过优化的成分设计和通过炼钢工艺、连铸、退火工艺研究生产优质大圆坯,可以有效控制中心裂纹、化学成分、降低组织及热应力,提高了延伸强度r
p
、抗拉强度rm、冲击功kv2、晶粒度和在超过600℃使用时材料性能,用于电站高压锅炉,通过穿管热处理后生产的大规格无缝管满足超超临界蒸汽管道对原材料性能的苛刻要求。
[0067]
上文所列出的一系列的详细说明仅仅是针对本发明的可行性实施例的具体说明,它们并非用以限制本发明的保护范围,凡未脱离本发明技艺精神所作的等效实施例或变更均应包含在本发明的保护范围之内。
再多了解一些
本文用于企业家、创业者技术爱好者查询,结果仅供参考。