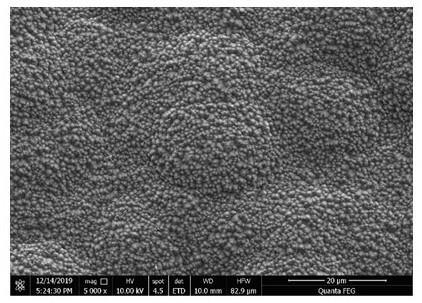
一种石墨基座表面用sic复合涂层及其制备方法
技术领域
1.本发明属于半导体技术领域,具体涉及一种石墨基座表面用sic复合涂层及其制备方法。
背景技术:
2.石墨基座是mocvd设备中的核心零部件之一,是衬底基片的承载体和发热体,直接决定薄膜材料的均匀性和纯度。然而,在实际生产过程中会有腐蚀性气体的产生和金属有机物的残留,这会使石墨基座产生腐蚀掉粉现象,大大降低石墨基座的使用寿命,同时掉落的石墨粉体也会对芯片造成污染,成为限制mocvd设备应用范围和阻碍半导体行业发展的首要问题之一。
3.表面涂层技术是解决上述问题的有效手段之一。sic因其高的热力学稳定性、优异的导热性、高的电子迁移率、抗氧化、耐冲刷等一系列优异性能,结合cvd法良好的覆盖性和可控性,cvd-sic涂层成为石墨基座表面用防护涂层的理想选择。然而,sic涂层和石墨基体之间较大的热膨胀系数差异导致涂层在热循环过程中易产生裂纹甚至脱落,从而失去对基体的保护作用。
4.为了解决这一问题,梯度涂层、复合涂层以及引入第二相增韧涂层等技术被大量研究,然而这些技术仍存在制造成本过高、工艺复杂、涂层与基体之间热膨胀系数失配缓解不明显、涂层厚度不足、涂层表面粗糙度过大等缺点,无法满足石墨基座的应用需求以及工业化生产。
技术实现要素:
5.针对现在技术中存在的不足之处,本发明的目的在于提供一种石墨基座表面用sic复合涂层及其制备方法,所制备的复合涂层与基体结合强度高,抗热疲劳性能好,同时本发明方法还具有设备工艺简单、制造成本较低、涂层无明显分层、涂层高纯、涂层厚度可控、sic外涂层致密且呈单晶型等优点。
6.为实现上述发明目的,本发明采用的技术方案是,一种石墨基座表面用sic复合涂层,由pyc/sic过渡层和sic外涂层组成;所述pyc/sic过渡层的厚度为5~15 μm;所述sic外涂层的厚度为75~100 μm。
7.优选的,所述sic外涂层的表面粗糙度低于2.5 μm。
8.本发明还提供了一种石墨基座表面用sic复合涂层的制备方法,利用化学气相沉积法制备并且进气口和出气口分别位于沉积室的下端和上端;布气盘贴合沉积室内壁放置于进气口上方150 mm处;制备步骤如下:a.对石墨基座进行预处理,然后放入沉积室中,并记录其位置;b.合炉后进行除杂处理;c.pyc/sic过渡层的制备:将炉温升至1350~1500 ℃,然后通入ch4和n2,保持炉内压力为4~10 kpa,沉积时间为20~60 h,在石墨基座表面制备疏松热解碳,其中,n2的流量为
3~10 l/min,ch4的流量为3~10 l/min;随后在沉积温度为1400~1550 ℃,沉积压力为0.5~5 kpa条件下,按照h2/sicl4体积比为5~30通入h2和sicl4气体,沉积0.2~1 h,对疏松热解碳进行封孔处理,同时在其表面生成一层sic涂层,其中,h2的流量为8~12 l/min;d.sic外涂层的制备:将炉温降至1100-1250 ℃,然后通入mts-h2前驱体体系,h2/mts摩尔比为10~20,沉积压力为0.5~10 kpa,沉积时间为3~7 h,在步骤c制备的pyc/sic过渡层表面沉积形成sic外涂层,其中,mts的流量为400~480 g/h;e.沉积结束后,再次升/降温至1200~1400 ℃,保温1~2 h,以缓慢释放复合涂层中的热应力和界面应力;f.随炉冷却至室温,取出石墨基座。
9.较好地,所述pyc/sic过渡层的厚度为5~15 μm;所述sic外涂层的厚度为70~100 μm。
10.较好地,所述sic外涂层的表面粗糙度低于2.5 μm。
11.较好地,沉积过程中,石墨基座位于化学气相沉积室的恒温区中,距布气盘的高度为250~650 mm。
12.较好地,步骤c和e中,升温速率为3~6 ℃/min。
13.较好地,步骤c和d中,sicl4和mts需处于一个恒温环境,所以将其放置在恒温水浴挥发容器中,设置温度恒定为40 ℃;通过鼓泡h2的方式将sicl4和mts分别带入沉积室中,同时h2还作为反应过程中的稀释气体。
14.较好地,步骤a中,对所述石墨基座进行预处理的步骤为:将所述石墨基座先在酒精中进行超声波处理10 min,然后用去离子水冲洗10 min,最后放入烘箱在110 ℃恒温条件下烘干30 min。
15.较好地,步骤b中,所述除杂处理的步骤为:装炉完毕后关闭炉门,开启真空泵使炉内压力抽至200 pa以下后关闭真空泵,随后往沉积炉内快速通入n2气,当炉内压力达到90 kpa以上后停止充n2气,再次开启真空泵抽真空至200 pa以下。
16.相较于现有技术,本发明的优点和有益效果如下:本发明方法采用下进气和在进气口上方设置布气盘的方式,使气体在沉积室中均匀分布,从而制备出厚度均匀的涂层;过渡层中的热解碳与石墨基座的热膨胀系数相近,两者之间具有良好的结合强度;同时过渡层中含有热解碳和残余孔隙可有效减小涂层制备过程中产生的界面应力及热应力;过渡层中的sic与pyc形成钉扎状界面结合以及牢固的化学结合;同时以过渡层表面的sic为基底同质外延生长cvd-sic外涂层,大大提高了sic外涂层与石墨基座的结合能力;本发明方法制备的sic外涂层高纯,致密无分层,几乎为(111)晶型,表面粗糙度低于2.5 μm等;本发明方法使用设备工艺简单、制造成本较低,具有广阔的工业化应用前景。
附图说明
17.图1为本发明中具有sic复合涂层的石墨基座的结构示意图;附图标记为:1、石墨基座;2、pyc/sic过渡层;3、sic外涂层;图2为实施例1中经化学气相沉积后制备的sic外涂层表面形貌sem图;图3为实施例1中经化学气相沉积后制备的sic外涂层的xrd衍射图谱。
具体实施方式
18.为使本发明要解决的技术问题、技术方案和优点更加清楚,下面将结合附图及具体实施例进行详细描述。应理解,以下实施例仅用于说明本发明而非用于限制本发明的范围。
19.实施例1如图1所示,本发明提供一种石墨基座表面用sic复合涂层,包括石墨基座1,pyc/sic过渡层2和sic外涂层3;利用化学气相沉积法制备并且进气口和出气口分别位于沉积室的下端和上端,布气盘贴合沉积室内壁放置于进气口上方150 mm处;制备步骤如下:a.将石墨基座先在酒精中进行超声波处理10 min,然后用去离子水冲洗10 min,最后放入烘箱在110 ℃恒温条件下烘干30 min,之后放入沉积室的恒温区中,距布气盘的高度为450 mm;b.装炉完毕后关闭炉门,开启真空泵使炉内压力抽至200 pa以下后关闭真空泵,随后往沉积炉内快速通入n2气,当炉内压力达到90 kpa以上后停止充n2气,再次开启真空泵抽真空至200 pa以下;c.以4 ℃/min的升温速率将炉温升至1450 ℃,然后通入ch4和n2,n2的流量为6 l/min,ch4的流量为4 l/min,保持炉内压力为6 kpa,沉积时间为25 h,在石墨基座表面制备疏松热解碳;随后在沉积温度为1450 ℃,沉积压力为0.5 kpa,按照h2/sicl4体积比为20通入h2和sicl4气体,h2的流量为8 l/min,沉积时间为0.3 h,对疏松热解碳进行封孔处理,同时在其表面生成一层sic涂层,本实施例制备的pyc/sic过渡层的厚度为6.2 μm;d.将炉温降至1150 ℃,然后通入mts-h2前驱体体系,h2/mts摩尔比为15,沉积压力为2 kpa,沉积时间为4 h,在步骤c制备的pyc/sic过渡层表面沉积形成sic外涂层,其中,mts的流量为440 g/h,本实施例制备的sic外涂层的厚度为82.37 μm;e.沉积结束后,使炉温升至1200 ℃,保温1 h,以缓慢释放复合涂层中的热应力和界面应力;f.随炉冷却至室温,取出石墨基座。
20.图2为本实施例中经化学气相沉积后制备的sic外涂层表面形貌sem图,从图中可以看出,sic外涂层表面由大小均匀的砂砾状晶粒组成,涂层表面致密,ra为1.52 μm。
21.图3为本实施例中经化学气相沉积后制备的sic外涂层的xrd衍射图谱,从图中可以观察到,涂层仅出现β-sic的衍射峰,几乎呈单晶型,无其它杂质峰的存在。
22.为验证涂层试样的抗热疲劳性能,进行了真空热循环实验:将涂层试样放入高温电阻炉之中,抽真空,加热至1000 ℃,保温20 min后随炉冷却至室温。发现sic复合涂层试样在经历331周期的热循环后表面出现涂层脱落现象,而单一sic涂层试样在经历84周期的热循环后表面出现涂层脱落现象。
23.实施例2本发明提供一种石墨基座表面用sic复合涂层,包括石墨基座1,pyc/sic过渡层2和sic外涂层3;利用化学气相沉积法制备并且进气口和出气口分别位于沉积室的下端和上端,布气盘贴合沉积室内壁放置于进气口上方150 mm处;制备步骤如下:a.将石墨基座先在酒精中进行超声波处理10 min,然后用去离子水冲洗10 min,最后放入烘箱在110 ℃恒温条件下烘干30 min,之后放入沉积室的恒温区中,距布气盘的
高度为450 mm;b.装炉完毕后关闭炉门,开启真空泵使炉内压力抽至200 pa以下后关闭真空泵,随后往沉积炉内快速通入n2气,当炉内压力达到90 kpa以上后停止充n2气,再次开启真空泵抽真空至200 pa以下;c.以5 ℃/min的升温速率将炉温升至1400 ℃,然后通入ch4和n2,n2的流量为6 l/min,ch4的流量为6 l/min,保持炉内压力为6 kpa,沉积时间为30 h,在石墨基座表面制备疏松热解碳;随后将炉温升至1450 ℃,按照h2/sicl4体积比为20通入h2和sicl4气体,h2的流量为10 l/min,控制沉积压力为3 kpa,沉积时间为0.5 h,对疏松热解碳进行封孔处理,同时在其表面生成一层sic涂层,本实施例制备的pyc/sic过渡层的厚度为6.86 μm;d.将炉温降至1150 ℃,然后通入mts-h2前驱体体系,h2/mts摩尔比为10,沉积压力为2 kpa,沉积时间为3 h,在步骤c制备的pyc/sic过渡层表面沉积形成sic外涂层,其中,mts的流量为440 g/h,本实施例制备的sic外涂层的厚度为72.27 μm;e.沉积结束后,使炉温升至1250 ℃,保温2 h,以缓慢释放复合涂层中的热应力和界面应力;f.随炉冷却至室温,取出石墨基座。
24.对涂层试样进行eds分析,发现制备的sic外涂层富碳,将导致涂层的抗氧化和抗腐蚀性能下降。
25.对涂层试样进行真空热循环实验,发现sic复合涂层试样在经历287周期的热循环后表面出现涂层脱落现象。
26.实施例3制备过程与实施例1基本相同,不同之处在于:步骤a中,石墨基座距布气盘的高度为650 mm;步骤c中,ch4的流量为3 l/min,h2/sicl4体积比为25。本实施例制备的pyc/sic过渡层的厚度为5.65 μm,sic外涂层的厚度为74.23 μm。
27.对涂层试样进行真空热循环实验,发现sic复合涂层试样在经历309周期的热循环后表面出现涂层脱落现象。
28.对比例1对比例1的制备过程与实施例1不同之处在于:省略了步骤d中sic外涂层的制备,产品中只含有pyc/sic过渡层。
29.由于涂层中有pyc的存在,单一pyc/sic涂层的抗氧化和抗腐蚀性能较差。
30.对涂层试样进行真空热循环实验,发现sic复合涂层试样在经历147周期的热循环后表面出现涂层脱落现象。
再多了解一些
本文用于企业家、创业者技术爱好者查询,结果仅供参考。