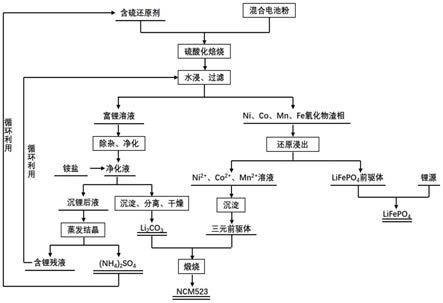
1.本发明涉及锂离子电池回收技术领域,特别涉及一种废旧电池正极材料资源化的处理方法。
背景技术:
2.锂离子电池具有能量密度大、循环寿命长和安全性能高等优点,而被广泛应用于新能源汽车和3c电子消费产品等多个领域。随着下游市场需求增大和锂离子电池技术的不断发展,其产量和报废量均呈现快速增长的趋势,至2025年我国退役电池将累计高达134.5gwh,如何有效回收处理废旧锂离子电池是全社会面临的迫切问题。磷酸铁锂电池的使用寿命一般在5年左右,三元电池的使用寿命一般为6年左右。
3.目前动力电池回收利用主要是梯次利用和再生利用,其中再生利用已经形成一定规模,2020年市场规模达到24亿元,预计到2025年,我国废旧动力电池再生利用市场规模将达到260亿元。近年来,钴、锂、镍等稀有金属的市场价持续暴涨,分别达到48.4万元/t、117.5万元/t和15万元/t(价格均来自于上海有色网2021年12月21日报价)。因此,回收废旧锂离子电池中的金属材料,在资源利用和经济效益方面具有重要意义。
4.在对废旧锂离子电池的回收过程中最有价值之处在于对锂离子电池中的钴、镍、锰、锂等金属的回收。现有的电池回收行业往往是多种正极粉的混合回收,而不是单一的磷酸铁锂或者三元电池,如何实现混合型废旧锂离子电池正极粉中锂、钴、镍、锰和铁的有效分离与资源化回收利用仍是研究的难点。
技术实现要素:
5.本发明要解决的技术问题是提供一种废旧电池正极材料资源化的处理方法,以提高废旧锂离子电池的回收效果。该处理方法采用火法焙烧 湿法浸出,回收流程短、过程清洁、副产品可循环利用,降低有价金属高效回收和资源化利用成本,适用于混合型废旧锂离子电池。为了解决上述问题,本发明提供的技术方案如下:
6.本发明的一种废旧电池正极材料资源化的处理方法,所述处理方法包括以下步骤:
7.s1,将废旧电池正极材料粉末与含硫还原剂进行球磨混合,然后硫酸化焙烧,得到焙烧产物;
8.s2,将步骤s1得到的所述焙烧产物进行水浸,然后过滤分离得到富锂浸出液和过渡金属氧化物渣相;
9.s3,对步骤s2所述富锂浸出液进行除杂净化处理,再加入碳酸铵和氨水进行沉锂反应,分离得到li2co3和沉锂后液,将所述沉锂后液进行蒸发结晶,得到硫酸铵产物和含锂残液;
10.s4,对步骤s2所述过渡金属氧化物渣相进行酸浸,得到含有mn
2
、ni
2
、co
2
的浸出液以及主要成分为铁的浸出残渣,向所述浸出液中加入锰盐、镍盐、钴盐中的至少一种,在
惰性气氛保护下加入碱溶液进行共沉淀反应,经分离干燥后得到镍钴锰三元前驱体材料;
11.s5,将步骤s4所述镍钴锰三元前驱体材料与步骤s3得到的li2co3混合后研磨、煅烧得到ncm523;其中,“ncm523”中的n代表镍、c代表钴、m代表锰,“523”为质量比,即镍、钴、锰的质量比为5︰2︰3。
12.s6,在步骤s4得到的主要成分为铁的浸出残渣中加入锂源后煅烧得到lifepo4。其中,锂源为碳酸锂。
13.进一步地,步骤s1中所述废旧电池正极材料是limno2,linio2,licoo2、lncm、lnca和lifepo4中的至少一种;步骤s1中所述含硫还原剂为硫磺、亚硫酸盐和硫化物中的至少一种;且所述含硫还原剂中硫与所述废旧电池正极材料中锂的摩尔比为(0.5-2):1。其中,硫化物主要为碱金属硫化物、多硫化物等。
14.进一步地,步骤s1中所述硫酸化焙烧的焙烧温度为600℃-700℃,所述硫酸化焙烧的焙烧时间为60min-120min。
15.进一步地,步骤s2中对所述焙烧产物进行水浸所采用的水为超纯水、纯水或者去离子水,液固比为3-8ml/g,水浸温度为40℃-60℃,水浸时间为15min-30min。
16.进一步地,步骤s3中所述除杂净化处理采用化学沉淀法或者树脂吸附法,所述沉锂反应的温度为40℃-60℃。
17.进一步地,步骤s3中蒸发结晶后的所述含锂残液可在步骤s2中的水浸阶段循环使用,蒸发结晶后得到的硫酸铵产物可在步骤s1中的硫酸化焙烧阶段循环使用。
18.进一步地,步骤s4中对所述过渡金属氧化物渣相进行酸浸时,用硫酸或者盐酸作为浸出酸,用过氧化氢、硫代硫酸钠、抗坏血酸或者蔗糖作为还原剂;所述酸浸的温度为20℃-80℃、时间为10min-80min,所述酸浸的液固比为5-60ml/g,所述浸出酸浓度为0.5-2.5mol/l,所述还原剂浓度为1%-10%。
19.进一步地,步骤s4中向所述浸出液中加入锰盐、镍盐和钴盐时,调节金属离子比例为ni:co:mn=5:2:3。
20.进一步地,步骤s5中得到ncm523的煅烧温度为500℃-1000℃。
21.进一步地,步骤s6中,在主要成分为铁的浸出残渣中加入锂源时,控制铁、锂比例为1:1,得到lifepo4的煅烧温度为500℃-1000℃。
22.本发明提供的废旧电池正极材料资源化的处理方法的有益效果是:
23.通过对混合型废旧锂离子电池的水浸预提锂过程、沉碳酸锂过程,还原浸出过程、硫酸镍钴锰与铁渣分离过程、镍钴锰三元正极合成过程。可综合回收镍、钴、锰、锂、铁等多组分,有利于简化废旧电池活性材料的回收工艺。具体如下:(1)实现锂的高效回收利用且实现了硫酸铵以及水浸液的闭路循环;(2)不通过萃取提取有价金属,直接合成前驱体,实现了有价金属的资源化利用;(3)实现了磷酸铁锂的原位生成,简化回收工艺,适于工业化应用。
附图说明
24.为了更清楚地说明本发明实施例中的技术方案,下面将对实施例描述中所需要使用的附图作简单地介绍,显而易见地,下面描述中的附图仅仅是本发明的一些实施例,对于本领域普通技术人员来讲,在不付出创造性劳动的前提下,还可以根据这些附图获得其他
的附图。
25.图1是本发明废旧电池正极材料资源化的处理方法的工艺流程图。
具体实施方式
26.为了使本技术领域的人员更好地理解本发明实施例中的技术方案,并使本发明的上述目的、特征和优点能够更加明显易懂,下面结合附图对本发明的具体实施方式作进一步的说明。
27.在此需要说明的是,对于这些实施方式的说明用于帮助理解本发明,但并不构成对本发明的限定。此外,下面所描述的本发明各个实施方式中所涉及的技术特征只要彼此之间未构成冲突就可以相互结合。
28.实施例一
29.本实施例的一种废旧电池正极材料资源化的处理方法,参考图1,该处理方法包括以下步骤:
30.s1,将废旧电池正极材料粉末与含硫还原剂进行球磨混合,然后硫酸化焙烧,得到焙烧产物;
31.s2,将步骤s1得到的焙烧产物进行水浸,然后过滤分离得到富锂浸出液和过渡金属氧化物渣相;
32.s3,对步骤s2富锂浸出液进行除杂净化处理,再加入碳酸铵和氨水进行沉锂反应,分离得到li2co3和沉锂后液,将沉锂后液进行蒸发结晶,得到硫酸铵产物和含锂残液;
33.s4,对步骤s2过渡金属氧化物渣相进行酸浸,得到含有mn
2
、ni
2
、co
2
的浸出液以及主要成分为铁的浸出残渣,向浸出液中加入锰盐、镍盐、钴盐中的至少一种,在惰性气氛保护下加入碱溶液进行共沉淀反应,经分离干燥后得到镍钴锰三元前驱体材料;
34.s5,将步骤s4镍钴锰三元前驱体材料与步骤s3得到的li2co3混合后研磨、煅烧得到ncm523;
35.s6,在步骤s4得到的主要成分为铁的浸出残渣中加入锂源后煅烧得到lifepo4。
36.优选地,步骤s1中废旧电池正极材料是limno2,linio2,licoo2、lncm、lnca和lifepo4中的至少一种;步骤s1中含硫还原剂为硫磺、亚硫酸盐和硫化物中的至少一种;且含硫还原剂中硫与废旧电池正极材料中锂的摩尔比为(0.5-2):1。步骤s1中硫酸化焙烧的焙烧温度为600℃-700℃,硫酸化焙烧的焙烧时间为60min-120min。
37.优选地,步骤s2中对焙烧产物进行水浸所采用的水为超纯水、纯水或者去离子水,液固比为3-8ml/g,水浸温度为40℃-60℃,水浸时间为15min-30min。
38.优选地,步骤s3中除杂净化处理采用化学沉淀法或者树脂吸附法,沉锂反应的温度为40℃-60℃。步骤s3中蒸发结晶后的含锂残液可在步骤s2中的水浸阶段循环使用,蒸发结晶后得到的硫酸铵产物可在步骤s1中的硫酸化焙烧阶段循环使用。
39.优选地,步骤s4中对过渡金属氧化物渣相进行酸浸时,用硫酸或者盐酸作为浸出酸,用过氧化氢、硫代硫酸钠、抗坏血酸或者蔗糖作为还原剂;酸浸的温度为20℃-80℃、时间为10min-80min,酸浸的液固比为5-60ml/g,浸出酸浓度为0.5-2.5mol/l,还原剂浓度为1%-10%。步骤s4中向浸出液中加入锰盐、镍盐和钴盐时,调节金属离子比例为ni:co:mn=5:2:3。
40.优选地,步骤s5中得到ncm523的煅烧温度为500℃-1000℃。
41.优选地,步骤s6中,在主要成分为铁的浸出残渣中加入锂源时,控制铁、锂比例为1:1,得到lifepo4的煅烧温度为500℃-1000℃。
42.实施例二
43.本实施例的一种废旧电池正极材料资源化的处理方法,包括以下步骤:
44.(1)将废旧电池正极材料粉末与含硫还原剂按n(s):n(li)=0.5:1充分混合后在600℃条件下进行硫酸化焙烧,焙烧时间60min,废旧电池正极材料被分解,锂离子从晶体结构中脱出。
45.(2)将焙烧产物分散于去离子水中进行水浸,其中,离子水与焙烧产物的液固比为3ml/g,水浸的温度为45℃,水浸的时间为15min,水浸完成后过滤分离后得到富锂浸出液和过渡金属氧化物渣相。将富锂浸出液取样稀释后,采用电感耦合等离子发射光谱仪分析测定其中锂元素的质量分数为16g/l。取过渡金属氧化物渣相的渣样,检测其中锂元素的质量分数小于0.1%,浸出率为97%。随后调节富锂浸出液的ph至8.5,待不再产生沉淀后进行固液分离,得到沉锂所需净化液。向净化液中加入过量的碳酸铵和氨水,在40℃下进行沉积碳酸锂备用。
46.(3)对过渡金属氧化物渣相进行酸浸,酸浸温度为25℃、时间为20min,液固比15ml/g,酸浓度1mol/l,还原剂用量4%。浸出后过滤得到co、li、mn、ni混合溶液和铁化合物残渣。调节浸出液中金属离子含量,之后沉淀金属离子,将酸回用,之后在600℃下将沉淀煅烧,研磨后得到合成ncm523材料。浸出后得到的铁化合物残渣中添加锂源,充分混合,600℃下煅烧,研磨后得到lifepo4材料。
47.实施例三
48.本实施例的一种废旧电池正极材料资源化的处理方法,包括以下步骤:
49.(1)将废旧电池正极材料粉末与含硫还原剂按n(s):n(li)=1:1充分混合后在650℃条件下进行硫酸化焙烧,焙烧时间80min,废旧电池正极材料粉末被分解,锂离子从晶体结构中脱出。
50.(2)将焙烧产物分散于去离子水中进行水浸,其中,离子水与焙烧产物的液固比为5ml/g,水浸的温度为50℃,水浸的时间25min,浸出完成后过滤分离后得到富锂浸出液和过渡金属氧化物渣相。将富锂浸出液取样稀释后,采用电感耦合等离子发射光谱仪分析测定其中锂元素的质量分数为15.2g/l。取过渡金属氧化物渣相的渣样,检测其中锂元素的质量分数小于0.1%,浸出率为98.2%。随后调节富锂浸出液的ph至8.5,待不再产生沉淀后进行固液分离,得到沉锂所需净化液。向净化液中加入过量的碳酸铵和氨水,在55℃下进行沉积碳酸锂备用。
51.(3)对过渡金属氧化物渣相进行酸浸,酸浸温度为60℃,时间为60min,液固比40ml/g,酸浓度1.5mol/l,还原剂用量6%。浸出后过滤得到co、li、mn、ni混合溶液和铁化合物残渣。调节浸出液中金属离子含量,之后沉淀金属离子,将酸回用,之后在700℃下将沉淀煅烧,研磨后得到合成ncm523材料。浸出后得到的铁化合物残渣中添加锂源,充分混合,800℃下煅烧,研磨后得到lifepo4材料。
52.实施例四
53.本实施例的一种废旧电池正极材料资源化的处理方法,包括以下步骤:
54.(1)将废旧电池正极材料粉末与含硫还原剂按n(s):n(li)=2:1充分混合后在700℃条件下进行硫酸化焙烧,焙烧时间80min,废旧电池正极材料被分解,锂离子从晶体结构中脱出。
55.(2)将焙烧产物分散于去离子水中进行水浸,其中,离子水与焙烧产物的液固比为8ml/g,水浸的温度为60℃,浸出时间40min,浸出完成后过滤分离后得到富锂浸出液和过渡金属氧化物渣。将富锂浸出液取样稀释后,采用电感耦合等离子发射光谱仪分析测定其中锂元素的质量分数为16.8g/l。取过渡金属氧化物渣的渣样,检测其中锂元素的质量分数小于0.1%,浸出率为98.4%。随后调节富锂浸出液的ph至8.5,待不再产生沉淀后进行固液分离,得到沉锂所需净化液。向净化液中加入过量的碳酸铵和氨水,在55℃下进行沉积碳酸锂备用。
56.(3)对过渡金属氧化物渣相进行酸浸,酸浸温度为80℃,时间为40min,液固比50ml/g,酸浓度2.5mol/l,还原剂用量8%。浸出后过滤得到co、li、mn、ni混合溶液和铁化合物残渣。调节浸出液中金属离子含量,之后沉淀金属离子,将酸回用,之后在800℃下将沉淀煅烧,研磨后得到合成ncm523材料。浸出后得到的铁化合物残渣中添加锂源,充分混合,900℃下煅烧,研磨后得到lifepo4材料。
57.本说明书中的各个实施例均采用递进的方式描述,各个实施例之间相同相似的部分互相参见即可,每个实施例重点说明的都是与其它实施例的不同之处。
58.以上结合附图对本发明的实施方式作出详细说明,但本发明不局限于所描述的实施方式。对本领域的技术人员而言,在不脱离本发明的原理和精神的情况下对这些实施例进行的多种变化、修改、替换和变型均仍落入在本发明的保护范围之内。
再多了解一些
本文用于企业家、创业者技术爱好者查询,结果仅供参考。