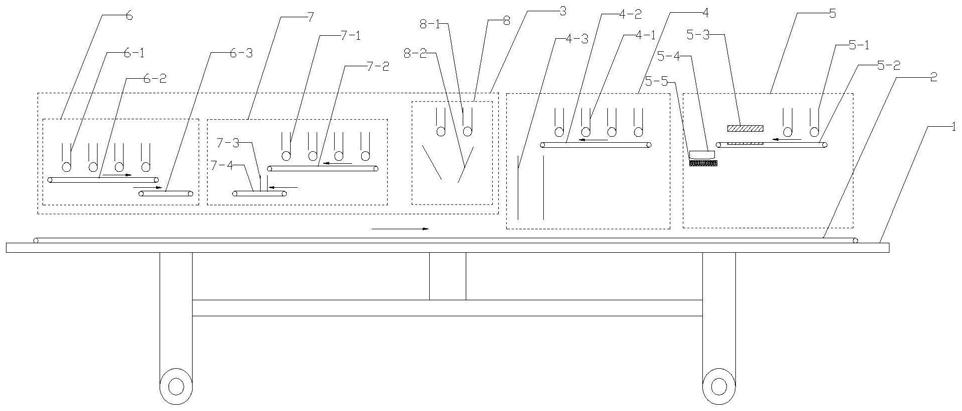
1.本发明涉及一种瓷质砖及其生产方法,具体涉及一种具有通体石材纹理且易加工的瓷质砖及其生产方法。
背景技术:
2.我国建筑陶瓷行业经过几十年的发展,生产制造水平取得了非常大的提升,产品质量和装饰水平已经能与国外先进国家媲美。在陶瓷砖装饰技术方面,发展历程主要经历了三个阶段:即丝网平版印刷装饰、胶辊印花装饰和数码喷墨印花装饰。其中,数码喷墨印花装饰是一种非接触式的数字印刷技术,可印刷不规则面、不需要实物制版,转版简单,生产重复性好,通过直接在坯体上喷印,提高了印花的精度,将传统丝网与胶辊印花的60-100dpi分辨率一次性上升至360dpi甚至更高,同时实现了多变图案造型运用的可行性,更可以在3d立体的凹凸砖面上进行喷墨,因此,生产出来的瓷砖形象更逼真,更贴近自然。
3.虽然,数码喷墨印刷装饰解决了陶瓷砖表面花色不够逼真的问题,但是,陶瓷砖后期深加工如磨边、开槽、倒角等会有显露的底坯纹理、质地及色泽与表面反差较大,装饰效果不协调,露底不美观的问题。在实现具有通体石材纹理方面,中国专利cn201910066018.4公开了一种通体无釉大理石瓷砖及其制造方法,通过多管自由布料结合干燥抛坯的方式赋予瓷砖通体纹理,但为了保护表面纹理,还需要在喷墨装饰后增加透明耐磨保护材料作保护层,且多管自由布料容易导致纹理随机性过大,使得坯体纹理与喷墨纹理难以完全匹配,而使用干燥抛坯工序后,由于抛磨深度不同,呈现的纹理也不同,所以干燥抛坯工序的增加也给纹理控制带来了较大的难度。
4.瓷砖属于脆性陶瓷材料,尤其是吸水率不大于0.5%的瓷质砖,虽然,辊道窑高温快速烧成制度赋予了瓷质砖良好的致密度和破坏强度,但快烧制度也使得瓷质砖内部热应力分布不均匀,在后期因装修而切割加工过程中,容易因应力集中而发生切割裂、开孔裂、开槽裂等缺陷。因此,解决应力集中问题,改善瓷质砖的切割裂、开孔裂、开槽裂等后期加工缺陷是建筑陶瓷行业亟待解决的问题。
技术实现要素:
5.为了解决陶瓷砖后期深加工如磨边、开槽、倒角等会有显露的底坯纹理、质地及色泽与表面反差较大,装饰效果不协调,露底不美观的问题,以及解决瓷质砖的切割裂、开孔裂、开槽裂等后期加工缺陷问题,本发明提供一种具有通体石材纹理且易加工的瓷质砖的生产方法。
6.本发明的另一目的是提供一种用该生产方法生产的具有通体石材纹理且易加工的瓷质砖。
7.为实现第一个发明目的,本发明采用的技术方案是这样的:一种具有通体石材纹理且易加工的瓷质砖的生产方法,包括如下步骤:a、按常规方法制备具有通体石材纹理且易加工的瓷质砖用坯体粉料组,该坯体粉
料组由四种不同化学组成的坯体粉料构成:第一材质粉料、第二材质粉料、第三材质粉料和第四材质粉料;其中,所述第一材质粉料的化学组成以重量百分比计为:sio
2 65%~68%,al2o
3 18~22%,cao 2.5~3.5%,mgo 0.1~1%,k2o 2~3%,na2o 1.5~2.5%,zno 0.1%~1%,fe2o
3 ≤1%,tio
2 ≤0.3%,il≤5%,所述第二材质粉料的化学组成以重量百分比计为:sio
2 67%~70%,al2o
3 17~20%,cao 0~1%,mgo 9~13%,k2o 1~2%,na2o 0.5~1.5%,zno 0.1%~1%,fe2o
3 ≤0.7%,tio
2 ≤0.2%,il≤5%,所述第三材质粉料的化学组成以重量百分比计为:sio
2 68%~73%,al2o
3 3~7%,cao 18~23%,mgo 0.1~1%,k2o 0~0.3%,na2o 0~0.3%,fe2o
3 ≤1%,tio
2 ≤0.5%,il≤3%,所述第四材质粉料的化学组成以重量百分比计为:sio
2 68%~71%,al2o
3 13~17%,cao 0.5~2%,mgo 0.1~1%,k2o 3~5%,na2o 4~6%,zno 0.1%~1%,fe2o
3 ≤1%,tio
2 ≤0.5%,il≤5%,备用;b、布料:采用数字化通体布料系统对步骤a制备的具有通体石材纹理且易加工的瓷质砖用坯体粉料组进行布料,形成通体坯体粉料层;c、成型:将步骤b布料形成的通体坯体粉料层推入模腔,压制成型,形成具有通体石材纹理且易加工的瓷质砖坯体;d、坯体干燥:对步骤c成型后的具有通体石材纹理且易加工的瓷质砖坯体按照常规方法进行干燥;e、纹理识别:采用纹理采集器对步骤d干燥后的坯体纹理进行识别,并向数字喷墨印刷机发送网络信号;f、喷墨装饰:制备渗透喷墨墨水组,包括渗透墨水1、渗透墨水2、渗透墨水3、渗透墨水4、渗透墨水5、渗透墨水6以及渗透墨水7;所述渗透墨水1为铁离子着色的组合物,所述渗透墨水2为铬离子和钛离子复合着色的组合物,所述渗透墨水3为钴离子着色的组合物,所述渗透墨水4为铁离子和钴离子复合着色的组合物,所述渗透墨水5为铬离子和锡离子复合着色的组合物,所述渗透墨水6为铬离子着色的组合物,所述渗透墨水7为金离子着色的组合物;数字喷墨印刷机接收到步骤e纹理采集器发送过来的网络信号,进而调出相应石材纹理喷墨图稿,再将该渗透喷墨墨水组按相应的石材纹理喷墨图稿对位喷印在步骤e纹理识别后的具有通体石材纹理且易加工的瓷质砖坯体表面;g、烧成:将步骤f喷墨装饰后的具有通体石材纹理且易加工的瓷质砖坯体置于辊道窑中烧成,烧成温度为1150~1250℃,烧成周期为60~150min,得到具有通体石材纹理且易加工的瓷质砖烧结体;h、退火:在辊道窑尾部连接有退火窑,将步骤g烧成后的具有通体石材纹理且易加工的瓷质砖烧结体置于退火窑中进行退火处理,退火最高温度为550~750℃,退火周期为40~100min,得到具有通体石材纹理且易加工的瓷质砖半成品;i、磨边和抛光:利用常规的磨边和抛光加工设备,对步骤h退火得到的具有通体石材纹理且易加工的瓷质砖半成品进行磨边和抛光处理,制得一种具有通体石材纹理且易加工的瓷质砖成品。
8.以上步骤中,凡未加特别说明的,都采用现有技术中的常规控制手段。
9.为完成第二个发明目的,采用的是按上述步骤生产的具有通体石材纹理且易加工的瓷质砖。
10.进一步地,步骤a中所述第一材质粉料、第二材质粉料和第四材质粉料中均含有1%
~8%的无定形二氧化硅。
11.进一步地,步骤a中所述第三材质粉料中含有0.5%~2%的二氧化锡。
12.进一步地,步骤b中所述数字化通体布料系统包括智能化软件控制系统和通体布料装置;所述通体布料装置包括机架、第一传输皮带、线条形成系统、补粉系统和粒子形成系统;所述线条形成系统包括粗线条形成系统、中等线条形成系统和细线条形成系统;所述粗线条形成系统包括位于第一传输皮带前进方向起始端的粗线条布料料斗,位于粗线条布料料斗下方的第一分传输皮带,以及位于第一分传输皮带下方的第二分传输皮带;所述中等线条形成系统包括沿第一传输皮带前进方向第二分传输皮带前端的雕刻皮带、紧贴雕刻皮带表面的刮粉料斗,以及位于刮粉料斗上方的第三分传输皮带和第三分传输皮带上方的中等线条布料料斗;所述细线条形成系统包括沿第一传输皮带前进方向第三分传输皮带前端的倾斜挡板和倾斜挡板上方的细线条布料料斗;所述补粉系统包括沿第一传输皮带前进方向倾斜挡板前端的刮平料斗,刮平料斗上方的第四分传输皮带,以及第四分传输皮带上方的补粉料斗;所述粒子形成系统包括沿第一传输皮带前进方向的第四分传输皮带前端的筛网、紧贴筛网的刮皮、刮皮上方的沿第一传输皮带前进方向的第五分传输皮带,在第五分传输皮带上依次分布有顶压装置和粒子粉料布料料斗;所述粗线条形成系统和中等线条形成系统在垂直于第一传输皮带方向上的宽度小于第一传输皮带。
13.步骤b中所述数字化通体布料系统的工作过程是这样的:首先,通过智能化软件控制系统输入数字化石材纹理图稿,并按数字化石材纹理图稿驱动通体布料装置进行布料,之后,通体布料装置中的粗线条布料料斗依次下料,在第一分传输皮带上形成粉料层,粉料层随着第一分传输皮带的传动,掉落到第二分传输皮带上,第二分传输皮带再沿着垂直于第一传输皮带前进方向做摆动运动下料,将粉料甩到第一传输皮带上,由于第一传输皮带是一直在沿着前进方向运动,使得下到第一传输皮带上的粉料呈不规则弧线状分布,在第一传输皮带上形成弧线状的粗线条,当承载有粗线条粉料的第一传输皮带运动至中等线条形成系统下方时,中等线条布料料斗开始下料,通过叠层下料的方式在第三分传输皮带上形成粉料料层,该粉料料层随着第三分传输皮带运动下落至刮粉料斗中,通过刮粉料斗与雕刻皮带的相互作用,由雕刻皮带将雕刻皮带凹陷处的粉料输送至第一传输皮带上粗线条粉料的间隙处,所述刮粉料斗与雕刻皮带在下料过程中也是沿着垂直于第一传输皮带前进方向做摆动运动,在第一传输皮带上形成不规则的弧线状分布,由于雕刻皮带设计成一定宽度的凹陷条纹,使得凹陷处的粉料在第一传输皮带上形成的弧形粉料宽度要小于粗线条布料系统形成的弧形粉料,当承载有粗线条粉料层和中等线条粉料层的第一传输皮带运动至细线条形成系统下方时,细线条布料料斗开始间歇下料,粉料下落至倾斜挡板上,再滑落至第一传输皮带上粗线条粉料层和中等线条粉料层的间隙处,之后,承载有粗线条粉料层、中等线条粉料层和细线条粉料层的第一传输皮带运动至补粉系统的下方时,补粉料斗开始下料,依次下落至第四分传输皮带上形成叠层粉料层,再下落至刮平料斗,通过刮平料斗将补粉粉料施布在第一传输皮带上粗线条粉料层、中等线条粉料层和细线条粉料层的空隙处,完成补粉操作,之后,第一传输皮带将完成补粉操作后的粉料层输送至粒子形成系统的下方,粒子粉料布料料斗开始下料,下落至第五分传输皮带上,之后,第五分传输皮带将粉料运送至顶压装置处,顶压装置开始工作,对粉料进行预压,形成具有一定密实程度的粉块,粉块随着第五分传输皮带运动,下落至带有刮皮的筛网上,之后,刮皮沿着垂直于第一
传输皮带运动方向进行来回运动,将粉块挤压通过筛网,通过筛网挤压形成与筛网孔径大小一致的粒子,粒子下落至第一传输皮带上已经补粉完成的粉料层上,由于粒子本身有一定的重量,加之筛网与第一传输皮带具有一定的高度差,使得粒子在重力作用下,嵌入补粉完成的粉料层,形成最终的具有一定纹理的坯体粉料料层,随后,通过第一传输皮带将具有一定纹理坯体粉料料层送入压机模腔中反压成型。
14.进一步地,所述通体布料装置中的第二分传输皮带、刮粉料斗与雕刻皮带均沿着垂直于第一传输皮带前进方向做摆动运动,第二分传输皮带的摆动频率低于刮粉料斗和雕刻皮带,第二分传输皮带的摆动步调与刮粉料斗和雕刻皮带不一致。
15.进一步地,所述通体布料装置中的粒子形成系统为间歇式运动。
16.进一步地,步骤f中所述渗透喷墨墨水组的粘度为25~35mpa
·
s,50ml流速杯测试流速为11~15s,比重为0.88~0.92g/cm3,表面张力为23~29mn/m。
17.进一步地,步骤f中所述渗透喷墨墨水组的颜色并不是固定不变的,会在不同体系的坯体粉料中呈现不同的颜色;对于第一材质粉料、第二材质粉料和第四材质粉料来说,渗透墨水1呈现铁红色、渗透墨水2呈现黄色、渗透墨水3呈现海碧蓝色、渗透墨水4呈现黑色、渗透墨水5呈现淡黄色、渗透墨水6呈现黄绿色,以及渗透墨水7呈现粉红色;对于第三材质粉料来说,渗透墨水1呈现黄色、渗透墨水2呈现黄灰色、渗透墨水3呈现海碧蓝色、渗透墨水4呈现蓝色、渗透墨水5呈现玫瑰红色、渗透墨水6呈现绿色,以及渗透墨水7呈现粉红色;对于第一材质粉料、第二材质粉料和第四材质粉料来说,虽然7种渗透墨水在这3种材质粉料中的发色色调一致,但发色的饱和度并不同,对于渗透墨水1、渗透墨水2、渗透墨水3、渗透墨水4、渗透墨水5和渗透墨水6来说,发色饱和度由高到底的排序为:第四材质粉料>第一材质粉料>第二材质粉料;对于渗透墨水7来说,发色饱和度由高到底的排序为:第二材质粉料>第四材质粉料>第一材质粉料。
18.同一渗透墨水在不同体系的坯体粉料中会呈现不同的颜色,主要是指色相的不同,也可称之为色调的不同,色相是指颜色的相貌,是颜色彼此区别的最主要的基本特征,表示颜色质的区别。渗透墨水在坯体粉料中着色,原位反应形成对光具有选择性吸收的着色化合物,进而形成对不同波长光的反射辐射作用,形成不同的颜色。如渗透墨水5为铬离子和锡离子复合着色的组合物,在第一材质粉料、第二材质粉料和第四材质粉料中呈现淡黄色,这是由于铬离子在钾钠体系中与氧化钛原位反应形成铬-钛黄色固溶体所致;而渗透墨水5在第三材质粉料中呈现玫瑰红色,这是由于第三材质粉料中的氧化钙和氧化硅,与渗透墨水5中的锡离子原位反应形成了锡榍石(casnsio5),渗透墨水5中的铬离子在氧化气氛中形成cr2o3,并固溶于锡榍石晶格中,使得第三材质粉料与渗透墨水5的原位反应呈现出玫瑰红色,且会随着锡榍石含量增加,其玫瑰红色的饱和度增强。
19.同一体系坯体粉料与不同渗透墨水作用,也会呈现不同的颜色。主要也是色相的区别,以第一材质粉料为例,渗透墨水1呈现铁红色,是由于渗透墨水1中的铁离子在氧化气氛中原位反应形成氧化铁,第一材质粉料中的无定形sio2再包裹在氧化铁表面,稳定氧化铁的发色,形成铁红色;渗透墨水2呈现黄色,是由于渗透墨水2中的铬离子与第一材质粉料中的氧化钛原位反应形成铬-钛固溶体,呈现出黄色;渗透墨水3呈现海碧蓝色,是由于渗透墨水3中的钴离子与第一材质粉料中的氧化铝和氧化锌原位反应形成钴-铝-锌固溶体,呈现海碧蓝颜色;渗透墨水4中的铁离子和钴离子原位反应形成铁-钴固溶体,呈现黑色;渗透
墨水5呈现淡黄色,是由于渗透墨水5中少量的铬离子与第一材质粉料中的氧化钛原位反应形成了少量铬-钛固溶体,呈现出淡黄色;渗透墨水6呈现黄绿色,是由于渗透墨水6中具有大量的铬离子,一部分铬离子与第一材质粉料中的氧化钛原位反应形成了铬-钛固溶体,呈现出黄色,多余的铬离子则在氧化气氛中原位反应形成绿色的氧化铬,因而,最终呈现出复合发色,即黄绿色;渗透墨水7呈现粉红色,主要是由于渗透墨水7中的金胶体粒径为40nm左右,对530nm波长的光具有最大的吸收能力而呈现出粉红色。
20.同一渗透墨水在不同体系的坯体粉料中也会呈现相同的颜色,但颜色的饱和度不同。即不同材质粉料对同一渗透墨水发色的色相相同,但颜色的饱和度不同。饱和度是指颜色的纯洁性,即反射光线或透射光线接近光谱色的程度,也称为纯度或彩度。颜色的饱和度取决于坯体粉料表面选择性反射光谱辐射的能力。坯体粉料对光谱某一较窄波段的反射率高,而对其他波长的反射率低或没有反射,表明它有较高的选择性反射的能力,则该颜色的饱和度较高,反之较低。为了更直观地对比色相相同,而饱和度不同的差异,在本技术实际应用过程中会采用cie标准色度系统,即cie 1976 l a b 色彩空间作为国际通用的色彩测量标准。其中,l表示颜色的明度(0为黑色,100为白色),色度a为绿色和红色之间的位置(-100~100),色度b表示蓝色和黄色之间的位置(-100~100)。以渗透墨水1为例,第一材质粉料、第二材质粉料和第四材质粉料分别与渗透墨水1作用,均呈现铁红色,但发色饱和度有差异,具体参照表1所示。
21.表1 不同材质粉料与渗透墨水1作用后的呈色色度值 第一材质粉料第二材质粉料第四材质粉料l46~46.545.5~4646.5~47a15.5~17.513.5~15.517.5~20b13~1412~1314~15从表1不难发现,对于渗透墨水1在坯体粉料上的呈色来说,发色饱和度由高到底的排序为:第四材质粉料>第一材质粉料>第二材质粉料。
22.进一步地,步骤i中所述具有通体石材纹理且易加工的瓷质砖成品的吸水率≤0.5%,破坏强度≥1300n,断裂模数≥40mpa,容重≤2.35g/cm3,膨胀系数为6.3~7
×
10-6
/℃。
23.进一步地,步骤h和步骤i的顺序可以调换,即对步骤g得到的具有通体石材纹理且易加工的瓷质砖烧结体进行磨边和抛光后,冷却静置,再进行退火处理。
24.本发明取得的有益效果如下:开发出四种材质粉料,通过数字化通体布料系统形成通体石材纹理,开发出渗透喷墨墨水组,利用同一材质粉料对不同渗透墨水发色色调的不同、不同材质粉料对同一渗透墨水发色色调的差异,以及不同材质粉料对同一渗透墨水发色色调相同但发色饱和度不同,在坯体表面形成色彩丰富而灵活多变的石材纹理,结合数字化通体布料系统形成的通体石材纹理,很好地解决了陶瓷砖后期深加工如磨边、开槽、倒角等会有显露的底坯纹理、质地及色泽与表面反差较大,装饰效果不协调,露底不美观的问题。同时,本发明通过具有石材纹理且易加工的瓷质砖用坯体粉料组的化学组成的开发,并配合相应的退火工艺,能够解决瓷质砖的切割裂、开孔裂、开槽裂等后期加工缺陷问题。
附图说明
25.图1是通体布料装置示意图;
其中,1——机架,2——第一传输皮带,3——线条形成系统,4——补粉系统,5——粒子形成系统,4-1——刮平料斗,4-2——第四分传输皮带,4-3——补粉料斗,5-1——粒子粉料布料料斗,5-2——第五分传输皮带,5-3——顶压装置,5-4——刮皮,5-5——筛网,6——粗线条形成系统,7——中等线条形成系统,8——细线条形成系统,6-1——粗线条布料料斗,6-2——第一分传输皮带,6-3——第二分传输皮带,7-1——中等线条布料料斗,7-2——第三分传输皮带,7-3——刮粉料斗,7-4——雕刻皮带,8-1——细线条布料料斗,8-2——倾斜挡板。
26.图2是粗线条形成系统和中等线条形成系统俯视图;其中,6-1——粗线条布料料斗,6-2——第一分传输皮带,6-3——第二分传输皮带,7-1——中等线条布料料斗,7-2——第三分传输皮带,7-3——刮粉料斗,7-4——雕刻皮带。
具体实施方式
27.下面将参考附图并结合实施例,来具体说明本发明。
28.实施例1如图1~2所示,本发明采用如下步骤实现:a、按常规方法制备具有通体石材纹理且易加工的瓷质砖用坯体粉料组,该坯体粉料组由四种不同化学组成的坯体粉料构成:第一材质粉料、第二材质粉料、第三材质粉料和第四材质粉料;其中,所述第一材质粉料的化学组成以重量百分比计为:sio
2 68%,al2o
3 18%,cao 3.5%,mgo 0.1%,k2o 3%,na2o 1.5%,zno 0.5%,fe2o
3 ≤1%,tio
2 ≤0.3%,il≤5%,所述第二材质粉料的化学组成以重量百分比计为:sio
2 67%%,al2o
3 20%,cao 0.1%,mgo 13%,k2o 1%,na2o 1.5%,zno 0.5%,fe2o
3 ≤0.7%,tio
2 ≤0.2%,il≤5%,所述第三材质粉料的化学组成以重量百分比计为:sio
2 73%,al2o
3 3%,cao 23%,mgo 0.1%,k2o 0.3%,na2o 0.1%,sno
2 2%,fe2o
3 ≤1%,tio
2 ≤0.5%,il≤3%,所述第四材质粉料的化学组成以重量百分比计为:sio
2 68%%,al2o
3 17%,cao 0.5%,mgo 1%,k2o 3%,na2o 6%,zno 0.5%,fe2o
3 ≤1%,tio
2 ≤0.5%,il≤5%,备用;所述第一材质粉料、第二材质粉料和第四材质粉料中均含有5%的无定形二氧化硅;b、布料:采用数字化通体布料系统对步骤a制备的具有通体石材纹理且易加工的瓷质砖用坯体粉料组进行布料,形成通体坯体粉料层;采用的数字化通体布料系统包括,智能化软件控制系统和通体布料装置;所述通体布料装置包括机架1、第一传输皮带2、线条形成系统3、补粉系统4和粒子形成系统5;所述线条形成系统3包括粗线条形成系统6、中等线条形成系统7和细线条形成系统8;所述粗线条形成系统6包括位于第一传输皮带2前进方向起始端的粗线条布料料斗6-1,位于粗线条布料料斗6-1下方的第一分传输皮带6-2,以及位于第一分传输皮带6-2下方的第二分传输皮带6-3;所述中等线条形成系统7包括沿第一传输皮带2前进方向第二分传输皮带6-3前端的雕刻皮带7-4、紧贴雕刻皮带7-4表面的刮粉料斗4-3,以及位于刮粉料斗4-3上方的第三分传输皮带7-2和第三分传输皮带7-2上方的中等线条布料料斗7-1;所述细线条形成系统8包括沿第一传输皮带2前进方向第三分传输皮带7-2前端的倾斜挡板8-2和倾斜挡板8-2上方的细线条布料料斗8-1;所述补粉系统4包括沿第一传输皮带2前进方向倾斜挡板8-2前端
的刮平料斗4-1,刮平料斗4-1上方的第四分传输皮带4-2,以及第四分传输皮带4-2上方的补粉料斗4-3;所述粒子形成系统5包括沿第一传输皮带2前进方向的第四分传输皮带4-2前端的筛网5-5、紧贴筛网5-5的刮皮5-4、刮皮5-4上方的沿第一传输皮带2前进方向的第五分传输皮带5-2,在第五分传输皮带5-2上依次分布有顶压装置5-3和粒子粉料布料料斗5-1;所述粗线条形成系统6和中等线条形成系统7在垂直于第一传输皮带2方向上的宽度小于第一传输皮带2;工作过程如下:首先,通过智能化软件控制系统输入数字化石材纹理图稿,并按数字化石材纹理图稿驱动通体布料装置进行布料,之后,通体布料装置中的粗线条布料料斗6-1依次下料,在第一分传输皮带6-2上形成粉料层,粉料层随着第一分传输皮带6-2的传动,掉落到第二分传输皮带6-3上,第二分传输皮带6-3再沿着垂直于第一传输皮带2前进方向做摆动运动下料,将粉料甩到第一传输皮带2上,由于第一传输皮带2是一直在沿着前进方向运动,使得下到第一传输皮带2上的粉料呈不规则弧线状分布,在第一传输皮带2上形成弧线状的粗线条,当承载有粗线条粉料的第一传输皮带2运动至中等线条形成系统7下方时,中等线条布料料斗7-1开始下料,通过叠层下料的方式在第三分传输皮带7-2上形成粉料料层,该粉料料层随着第三分传输皮带7-2运动下落至刮粉料斗7-3中,通过刮粉料斗7-3与雕刻皮带7-4的相互作用,由雕刻皮带7-4将雕刻皮带7-4凹陷处的粉料输送至第一传输皮带2上粗线条粉料的间隙处,所述刮粉料斗7-3与雕刻皮带7-4在下料过程中也是沿着垂直于第一传输皮带2前进方向做摆动运动,在第一传输皮带2上形成不规则的弧线状分布,由于雕刻皮带7-4设计成一定宽度的凹陷条纹,使得凹陷处的粉料在第一传输皮带2上形成的弧形粉料宽度要小于粗线条布料系统6形成的弧形粉料,当承载有粗线条粉料层和中等线条粉料层的第一传输皮带2运动至细线条形成系统8下方时,细线条布料料斗8-1开始间歇下料,粉料下落至倾斜挡板8-2上,再滑落至第一传输皮带2上粗线条粉料层和中等线条粉料层的间隙处,之后,承载有粗线条粉料层、中等线条粉料层和细线条粉料层的第一传输皮带2运动至补粉系统4的下方时,补粉料斗4-3开始下料,依次下落至第四分传输皮带4-2上形成叠层粉料层,再下落至刮平料斗4-1,通过刮平料斗4-1将补粉粉料施布在第一传输皮带2上粗线条粉料层、中等线条粉料层和细线条粉料层的空隙处,完成补粉操作,之后,第一传输皮带2将完成补粉操作后的粉料层输送至粒子形成系统5的下方,粒子粉料布料料斗5-1开始下料,下落至第五分传输皮带5-2上,之后,第五分传输皮带5-2将粉料运送至顶压装置5-3处,顶压装置5-3开始工作,对粉料进行预压,形成具有一定密实程度的粉块,粉块随着第五分传输皮带5-2运动,下落至带有刮皮5-4的筛网5-5上,之后,刮皮5-4沿着垂直于第一传输皮带2运动方向进行来回运动,将粉块挤压通过筛网5-5,通过筛网5-5挤压形成与筛网5-5孔径大小一致的粒子,粒子下落至第一传输皮带2上已经补粉完成的粉料层上,由于粒子本身有一定的重量,加之筛网5-5与第一传输皮带2具有一定的高度差,使得粒子在重力作用下,嵌入补粉完成的粉料层,形成最终的具有一定纹理的坯体粉料料层,随后,通过第一传输皮带2将具有一定纹理坯体粉料料层送入压机模腔中反压成型;c、成型:将步骤b布料形成的通体坯体粉料层推入模腔,压制成型,形成具有通体石材纹理且易加工的瓷质砖坯体;d、坯体干燥:对步骤c成型后的具有通体石材纹理且易加工的瓷质砖坯体按照常规方法进行干燥;
e、纹理识别:采用纹理采集器对步骤d干燥后的坯体纹理进行识别,并向数字喷墨印刷机发送网络信号;f、喷墨装饰:制备渗透喷墨墨水组,包括渗透墨水1、渗透墨水2、渗透墨水3、渗透墨水4、渗透墨水5、渗透墨水6以及渗透墨水7;所述渗透墨水1为铁离子着色的组合物,所述渗透墨水2为铬离子和钛离子复合着色的组合物,所述渗透墨水3为钴离子着色的组合物,所述渗透墨水4为铁离子和钴离子复合着色的组合物,所述渗透墨水5为铬离子和锡离子复合着色的组合物,所述渗透墨水6为铬离子着色的组合物,所述渗透墨水7为金离子着色的组合物;数字喷墨印刷机接收到步骤e纹理采集器发送过来的网络信号,进而调出相应石材纹理喷墨图稿,再将该渗透喷墨墨水组按相应的石材纹理喷墨图稿对位喷印在步骤e纹理识别后的具有通体石材纹理且易加工的瓷质砖坯体表面;g、烧成:将步骤f喷墨装饰后的具有通体石材纹理且易加工的瓷质砖坯体置于辊道窑中烧成,烧成温度为1250℃,烧成周期为60min,得到具有通体石材纹理且易加工的瓷质砖烧结体;h、退火:在辊道窑尾部连接有退火窑,将步骤g烧成后的具有通体石材纹理且易加工的瓷质砖烧结体置于退火窑中进行退火处理,退火最高温度为550℃,退火周期为100min,得到具有通体石材纹理且易加工的瓷质砖半成品;i、磨边和抛光:利用常规的磨边和抛光加工设备,对步骤h退火得到的具有通体石材纹理且易加工的瓷质砖半成品进行磨边和抛光处理,制得一种具有通体石材纹理且易加工的瓷质砖成品,成品的吸水率为0.1%,破坏强度为3000n,断裂模数为46mpa,容重为2.34g/cm3,膨胀系数为7
×
10-6
/℃。
29.实施例2如图1~2所示,本发明采用如下步骤实现:a、按常规方法制备具有通体石材纹理且易加工的瓷质砖用坯体粉料组,该坯体粉料组由四种不同化学组成的坯体粉料构成:第一材质粉料、第二材质粉料、第三材质粉料和第四材质粉料;其中,所述第一材质粉料的化学组成以重量百分比计为:sio
2 67%,al2o
3 20%,cao 3%,mgo 0.5%,k2o 2.5%,na2o 2%,zno 0.1%,fe2o
3 ≤1%,tio
2 ≤0.3%,il≤5%,所述第二材质粉料的化学组成以重量百分比计为:sio
2 68%,al2o
3 19%,cao 0.5%,mgo 11%,k2o 1.5%,na2o 1%,zno 0.1%,fe2o
3 ≤0.7%,tio
2 ≤0.2%,il≤5%,所述第三材质粉料的化学组成以重量百分比计为:sio
2 71%,al2o
3 5%,cao 21%,mgo 0.5%,k2o 0.15%,na2o 0.15%,sno
2 1.5%,fe2o
3 ≤1%,tio
2 ≤0.5%,il≤3%,所述第四材质粉料的化学组成以重量百分比计为:sio
2 69%,al2o
3 15%,cao 1.3%,mgo 0.5%,k2o 4%,na2o 5%,zno 0.1%,fe2o
3 ≤1%,tio
2 ≤0.5%,il≤5%,备用;所述第一材质粉料、第二材质粉料和第四材质粉料中均含有1%的无定形二氧化硅;b、布料:采用数字化通体布料系统对步骤a制备的具有通体石材纹理且易加工的瓷质砖用坯体粉料组进行布料,形成通体坯体粉料层;采用的数字化通体布料系统包括,智能化软件控制系统和通体布料装置;所述通体布料装置包括机架1、第一传输皮带2、线条形成系统3、补粉系统4和粒子形成系统5;所述线条形成系统3包括粗线条形成系统6、中等线条形成系统7和细线条形成系统8;所述粗线条形成系统6包括位于第一传输皮带2前进方向起始端的粗线条布料料斗6-1,位于粗线条
布料料斗6-1下方的第一分传输皮带6-2,以及位于第一分传输皮带6-2下方的第二分传输皮带6-3;所述中等线条形成系统7包括沿第一传输皮带2前进方向第二分传输皮带6-3前端的雕刻皮带7-4、紧贴雕刻皮带7-4表面的刮粉料斗4-3,以及位于刮粉料斗4-3上方的第三分传输皮带7-2和第三分传输皮带7-2上方的中等线条布料料斗7-1;所述细线条形成系统8包括沿第一传输皮带2前进方向第三分传输皮带7-2前端的倾斜挡板8-2和倾斜挡板8-2上方的细线条布料料斗8-1;所述补粉系统4包括沿第一传输皮带2前进方向倾斜挡板8-2前端的刮平料斗4-1,刮平料斗4-1上方的第四分传输皮带4-2,以及第四分传输皮带4-2上方的补粉料斗4-3;所述粒子形成系统5包括沿第一传输皮带2前进方向的第四分传输皮带4-2前端的筛网5-5、紧贴筛网5-5的刮皮5-4、刮皮5-4上方的沿第一传输皮带2前进方向的第五分传输皮带5-2,在第五分传输皮带5-2上依次分布有顶压装置5-3和粒子粉料布料料斗5-1;所述粗线条形成系统6和中等线条形成系统7在垂直于第一传输皮带2方向上的宽度小于第一传输皮带2;工作过程如下:首先,通过智能化软件控制系统输入数字化石材纹理图稿,并按数字化石材纹理图稿驱动通体布料装置进行布料,之后,通体布料装置中的粗线条布料料斗6-1依次下料,在第一分传输皮带6-2上形成粉料层,粉料层随着第一分传输皮带6-2的传动,掉落到第二分传输皮带6-3上,第二分传输皮带6-3再沿着垂直于第一传输皮带2前进方向做摆动运动下料,将粉料甩到第一传输皮带2上,由于第一传输皮带2是一直在沿着前进方向运动,使得下到第一传输皮带2上的粉料呈不规则弧线状分布,在第一传输皮带2上形成弧线状的粗线条,当承载有粗线条粉料的第一传输皮带2运动至中等线条形成系统7下方时,中等线条布料料斗7-1开始下料,通过叠层下料的方式在第三分传输皮带7-2上形成粉料料层,该粉料料层随着第三分传输皮带7-2运动下落至刮粉料斗7-3中,通过刮粉料斗7-3与雕刻皮带7-4的相互作用,由雕刻皮带7-4将雕刻皮带7-4凹陷处的粉料输送至第一传输皮带2上粗线条粉料的间隙处,所述刮粉料斗7-3与雕刻皮带7-4在下料过程中也是沿着垂直于第一传输皮带2前进方向做摆动运动,在第一传输皮带2上形成不规则的弧线状分布,由于雕刻皮带7-4设计成一定宽度的凹陷条纹,使得凹陷处的粉料在第一传输皮带2上形成的弧形粉料宽度要小于粗线条布料系统6形成的弧形粉料,当承载有粗线条粉料层和中等线条粉料层的第一传输皮带2运动至细线条形成系统8下方时,细线条布料料斗8-1开始间歇下料,粉料下落至倾斜挡板8-2上,再滑落至第一传输皮带2上粗线条粉料层和中等线条粉料层的间隙处,之后,承载有粗线条粉料层、中等线条粉料层和细线条粉料层的第一传输皮带2运动至补粉系统4的下方时,补粉料斗4-3开始下料,依次下落至第四分传输皮带4-2上形成叠层粉料层,再下落至刮平料斗4-1,通过刮平料斗4-1将补粉粉料施布在第一传输皮带2上粗线条粉料层、中等线条粉料层和细线条粉料层的空隙处,完成补粉操作,之后,第一传输皮带2将完成补粉操作后的粉料层输送至粒子形成系统5的下方,粒子粉料布料料斗5-1开始下料,下落至第五分传输皮带5-2上,之后,第五分传输皮带5-2将粉料运送至顶压装置5-3处,顶压装置5-3开始工作,对粉料进行预压,形成具有一定密实程度的粉块,粉块随着第五分传输皮带5-2运动,下落至带有刮皮5-4的筛网5-5上,之后,刮皮5-4沿着垂直于第一传输皮带2运动方向进行来回运动,将粉块挤压通过筛网5-5,通过筛网5-5挤压形成与筛网5-5孔径大小一致的粒子,粒子下落至第一传输皮带2上已经补粉完成的粉料层上,由于粒子本身有一定的重量,加之筛网5-5与第一传输皮带2具有一定的高度差,使得粒子在
重力作用下,嵌入补粉完成的粉料层,形成最终的具有一定纹理的坯体粉料料层,随后,通过第一传输皮带2将具有一定纹理坯体粉料料层送入压机模腔中反压成型;c、成型:将步骤b布料形成的通体坯体粉料层推入模腔,压制成型,形成具有通体石材纹理且易加工的瓷质砖坯体;d、坯体干燥:对步骤c成型后的具有通体石材纹理且易加工的瓷质砖坯体按照常规方法进行干燥;e、纹理识别:采用纹理采集器对步骤d干燥后的坯体纹理进行识别,并向数字喷墨印刷机发送网络信号;f、喷墨装饰:制备渗透喷墨墨水组,包括渗透墨水1、渗透墨水2、渗透墨水3、渗透墨水4、渗透墨水5、渗透墨水6以及渗透墨水7;所述渗透墨水1为铁离子着色的组合物,所述渗透墨水2为铬离子和钛离子复合着色的组合物,所述渗透墨水3为钴离子着色的组合物,所述渗透墨水4为铁离子和钴离子复合着色的组合物,所述渗透墨水5为铬离子和锡离子复合着色的组合物,所述渗透墨水6为铬离子着色的组合物,所述渗透墨水7为金离子着色的组合物;数字喷墨印刷机接收到步骤e纹理采集器发送过来的网络信号,进而调出相应石材纹理喷墨图稿,再将该渗透喷墨墨水组按相应的石材纹理喷墨图稿对位喷印在步骤e纹理识别后的具有通体石材纹理且易加工的瓷质砖坯体表面;g、烧成:将步骤f喷墨装饰后的具有通体石材纹理且易加工的瓷质砖坯体置于辊道窑中烧成,烧成温度为1150℃,烧成周期为150min,得到具有通体石材纹理且易加工的瓷质砖烧结体;h、磨边和抛光:利用常规的磨边和抛光加工设备,对步骤g烧成得到的具有通体石材纹理且易加工的瓷质砖烧结体进行磨边和抛光处理,制得一种具有通体石材纹理且易加工的瓷质砖半成品;i、退火:在辊道窑尾部连接有退火窑,将步骤h磨边和抛光后的具有通体石材纹理且易加工的瓷质砖半成品置于退火窑中进行退火处理,退火最高温度为750℃,退火周期为40min,得到具有通体石材纹理且易加工的瓷质砖成品,成品的吸水率为0.2%,破坏强度为2600n,断裂模数为43mpa,容重为2.32g/cm3,膨胀系数为6.3
×
10-6
/℃。
30.实施例3如图1~2所示,本发明采用如下步骤实现:a、按常规方法制备具有通体石材纹理且易加工的瓷质砖用坯体粉料组,该坯体粉料组由四种不同化学组成的坯体粉料构成:第一材质粉料、第二材质粉料、第三材质粉料和第四材质粉料;其中,第一材质粉料的化学组成以重量百分比计为:sio
2 65%,al2o
3 22%,cao 2.5%,mgo 1%,k2o 2%,na2o 2.5%,zno 1%,fe2o
3 ≤1%,tio
2 ≤0.3%,il≤5%,所述第二材质粉料的化学组成以重量百分比计为:sio
2 70%,al2o
3 17%,cao1%,mgo 9%,k2o 2%,na2o 0.5%,zno 1%,fe2o
3 ≤0.7%,tio
2 ≤0.2%,il≤5%,所述第三材质粉料的化学组成以重量百分比计为:sio
2 68%%,al2o
3 7%,cao 18%,mgo 1%,k2o 0.1%,na2o 0.3%,sno
2 0.5%,fe2o
3 ≤1%,tio
2 ≤0.5%,il≤3%,所述第四材质粉料的化学组成以重量百分比计为:sio
2 71%,al2o
3 13%,cao 2%,mgo 0.1%,k2o 5%,na2o 4%,zno 1%,fe2o
3 ≤1%,tio
2 ≤0.5%,il≤5%,备用;所述第一材质粉料、第二材质粉料和第四材质粉料中均含有8%的无定形二氧化硅;b、布料:采用数字化通体布料系统对步骤a制备的具有通体石材纹理且易加工的
瓷质砖用坯体粉料组进行布料,形成通体坯体粉料层;采用的数字化通体布料系统包括,智能化软件控制系统和通体布料装置;所述通体布料装置包括机架1、第一传输皮带2、线条形成系统3、补粉系统4和粒子形成系统5;所述线条形成系统3包括粗线条形成系统6、中等线条形成系统7和细线条形成系统8;所述粗线条形成系统6包括位于第一传输皮带2前进方向起始端的粗线条布料料斗6-1,位于粗线条布料料斗6-1下方的第一分传输皮带6-2,以及位于第一分传输皮带6-2下方的第二分传输皮带6-3;所述中等线条形成系统7包括沿第一传输皮带2前进方向第二分传输皮带6-3前端的雕刻皮带7-4、紧贴雕刻皮带7-4表面的刮粉料斗4-3,以及位于刮粉料斗4-3上方的第三分传输皮带7-2和第三分传输皮带7-2上方的中等线条布料料斗7-1;所述细线条形成系统8包括沿第一传输皮带2前进方向第三分传输皮带7-2前端的倾斜挡板8-2和倾斜挡板8-2上方的细线条布料料斗8-1;所述补粉系统4包括沿第一传输皮带2前进方向倾斜挡板8-2前端的刮平料斗4-1,刮平料斗4-1上方的第四分传输皮带4-2,以及第四分传输皮带4-2上方的补粉料斗4-3;所述粒子形成系统5包括沿第一传输皮带2前进方向的第四分传输皮带4-2前端的筛网5-5、紧贴筛网5-5的刮皮5-4、刮皮5-4上方的沿第一传输皮带2前进方向的第五分传输皮带5-2,在第五分传输皮带5-2上依次分布有顶压装置5-3和粒子粉料布料料斗5-1;所述粗线条形成系统6和中等线条形成系统7在垂直于第一传输皮带2方向上的宽度小于第一传输皮带2;工作过程如下:首先,通过智能化软件控制系统输入数字化石材纹理图稿,并按数字化石材纹理图稿驱动通体布料装置进行布料,之后,通体布料装置中的粗线条布料料斗6-1依次下料,在第一分传输皮带6-2上形成粉料层,粉料层随着第一分传输皮带6-2的传动,掉落到第二分传输皮带6-3上,第二分传输皮带6-3再沿着垂直于第一传输皮带2前进方向做摆动运动下料,将粉料甩到第一传输皮带2上,由于第一传输皮带2是一直在沿着前进方向运动,使得下到第一传输皮带2上的粉料呈不规则弧线状分布,在第一传输皮带2上形成弧线状的粗线条,当承载有粗线条粉料的第一传输皮带2运动至中等线条形成系统7下方时,中等线条布料料斗7-1开始下料,通过叠层下料的方式在第三分传输皮带7-2上形成粉料料层,该粉料料层随着第三分传输皮带7-2运动下落至刮粉料斗7-3中,通过刮粉料斗7-3与雕刻皮带7-4的相互作用,由雕刻皮带7-4将雕刻皮带7-4凹陷处的粉料输送至第一传输皮带2上粗线条粉料的间隙处,所述刮粉料斗7-3与雕刻皮带7-4在下料过程中也是沿着垂直于第一传输皮带2前进方向做摆动运动,在第一传输皮带2上形成不规则的弧线状分布,由于雕刻皮带7-4设计成一定宽度的凹陷条纹,使得凹陷处的粉料在第一传输皮带2上形成的弧形粉料宽度要小于粗线条布料系统6形成的弧形粉料,当承载有粗线条粉料层和中等线条粉料层的第一传输皮带2运动至细线条形成系统8下方时,细线条布料料斗8-1开始间歇下料,粉料下落至倾斜挡板8-2上,再滑落至第一传输皮带2上粗线条粉料层和中等线条粉料层的间隙处,之后,承载有粗线条粉料层、中等线条粉料层和细线条粉料层的第一传输皮带2运动至补粉系统4的下方时,补粉料斗4-3开始下料,依次下落至第四分传输皮带4-2上形成叠层粉料层,再下落至刮平料斗4-1,通过刮平料斗4-1将补粉粉料施布在第一传输皮带2上粗线条粉料层、中等线条粉料层和细线条粉料层的空隙处,完成补粉操作,之后,第一传输皮带2将完成补粉操作后的粉料层输送至粒子形成系统5的下方,粒子粉料布料料斗5-1开始下料,下落至第五分传输皮带5-2上,之后,第五分传输皮带5-2将粉料运送至顶压
装置5-3处,顶压装置5-3开始工作,对粉料进行预压,形成具有一定密实程度的粉块,粉块随着第五分传输皮带5-2运动,下落至带有刮皮5-4的筛网5-5上,之后,刮皮5-4沿着垂直于第一传输皮带2运动方向进行来回运动,将粉块挤压通过筛网5-5,通过筛网5-5挤压形成与筛网5-5孔径大小一致的粒子,粒子下落至第一传输皮带2上已经补粉完成的粉料层上,由于粒子本身有一定的重量,加之筛网5-5与第一传输皮带2具有一定的高度差,使得粒子在重力作用下,嵌入补粉完成的粉料层,形成最终的具有一定纹理的坯体粉料料层,随后,通过第一传输皮带2将具有一定纹理坯体粉料料层送入压机模腔中反压成型;c、成型:将步骤b布料形成的通体坯体粉料层推入模腔,压制成型,形成具有通体石材纹理且易加工的瓷质砖坯体;d、坯体干燥:对步骤c成型后的具有通体石材纹理且易加工的瓷质砖坯体按照常规方法进行干燥;e、纹理识别:采用纹理采集器对步骤d干燥后的坯体纹理进行识别,并向数字喷墨印刷机发送网络信号;f、喷墨装饰:制备渗透喷墨墨水组,包括渗透墨水1、渗透墨水2、渗透墨水3、渗透墨水4、渗透墨水5、渗透墨水6以及渗透墨水7;所述渗透墨水1为铁离子着色的组合物,所述渗透墨水2为铬离子和钛离子复合着色的组合物,所述渗透墨水3为钴离子着色的组合物,所述渗透墨水4为铁离子和钴离子复合着色的组合物,所述渗透墨水5为铬离子和锡离子复合着色的组合物,所述渗透墨水6为铬离子着色的组合物,所述渗透墨水7为金离子着色的组合物;数字喷墨印刷机接收到步骤e纹理采集器发送过来的网络信号,进而调出相应石材纹理喷墨图稿,再将该渗透喷墨墨水组按相应的石材纹理喷墨图稿对位喷印在步骤e纹理识别后的具有通体石材纹理且易加工的瓷质砖坯体表面;g、烧成:将步骤f喷墨装饰后的具有通体石材纹理且易加工的瓷质砖坯体置于辊道窑中烧成,烧成温度为1200℃,烧成周期为120min,得到具有通体石材纹理且易加工的瓷质砖烧结体;h、退火:在辊道窑尾部连接有退火窑,将步骤g烧成后的具有通体石材纹理且易加工的瓷质砖烧结体置于退火窑中进行退火处理,退火最高温度为550℃,退火周期为100min,得到具有通体石材纹理且易加工的瓷质砖半成品;i、磨边和抛光:利用常规的磨边和抛光加工设备,对步骤h退火得到的具有通体石材纹理且易加工的瓷质砖半成品进行磨边和抛光处理,制得一种具有通体石材纹理且易加工的瓷质砖成品,成品的吸水率为0.05%,破坏强度为3300n,断裂模数为45mpa,容重为2.33g/cm3,膨胀系数为6.5
×
10-6
/℃。
31.以上实施例仅用以说明本发明的技术方案而非对其限制,尽管参照较佳实施例对本发明进行了详细的说明,所属领域的普通技术人员应当理解。依然可以对发明的具体实施方式进行修改或者对部分技术特征进行等同替换,而不脱离本发明技术方案的精神,其均应涵盖在本发明请求保护的技术方案范围当中。
再多了解一些
本文用于企业家、创业者技术爱好者查询,结果仅供参考。