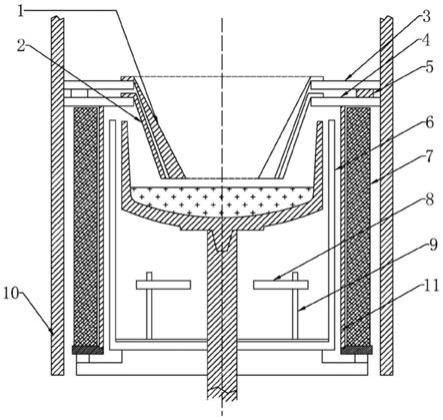
1.本发明涉及直拉法生长无位错单晶技术领域,特别涉及一种直拉法生长无位错锗单晶热场和生长工艺。
背景技术:
2.直拉法是1918年由切克劳斯基(czochralski)建立起来的一种晶体生长方法,简称cz法。直拉法是生长硅、锗以及化合物半导体等材料最普遍的生长方法。直拉法较其他方法具有更高的生长效率、更大的直径尺寸上限、更直观的生长过程观测、更可控的工艺条件,是产业化生产较为理想的单晶生长方式。但是对于不同的材料以及材料不同缺陷程度的要求,直拉单晶炉热场和工艺又有很大的区别。位错是存在于半导体材料中的一种典型缺陷,直接影响着半导体材料的电学性质,影响材料的最终使用。
3.在直拉生长工艺中,通过对热场温度梯度的调节,以及对晶体不同生长阶段工艺的控制,可以有效的控制晶体中的位错水平,实现降低位错甚至消除位错的目的。对于大部分采用直拉法工艺生长的半导体材料尤其是锗单晶而言,调节直拉单晶炉热场,控制热场中熔体的径向温度梯度非常小,纵向温度梯度适度,是获得低位错和无位错晶体的重要条件。
4.常见的直拉单晶炉热场系统中,通常采用单加热器和热屏的形式,通过降低埚位的方式实现晶体生长过程中较小的径向温度梯度,通过加装导流筒或者热屏的形式,调节热场中的纵向温度梯度。这种方法有较大的局限性,因为对于单加热器系统而言,埚位的降低非常有限,在装料量较大的情况下,过低的埚位,会因为坩埚底部离开加热器高温区域(一般在加热器中心稍偏上位置)而出现埚底结晶无法拉晶的情况。而对于采用主加热和底加热双加热形式的热场系统,虽然减小了液面附近的径向温度梯度,但是也会因为埚底的埚位,和主加热器与底加热器的配合下,热场中恒温区过长,熔体上方纵向温度梯度过小,晶体散热效率过低,而出现拉晶困难,拉速过低导致生长效率低下的问题。
技术实现要素:
5.鉴于传统直拉单晶炉热场所面临的径向和纵向温度调节较难平衡的情况,本发明的目的在于提供一种直拉法生长无位错锗单晶热场,通过直拉单晶炉内双加热器组合热场结构和热场上部紧贴炉壁的多层保温盖和多层楔形热屏结构组合的模式,实现温度梯度可调节的无位错锗单晶材料生长。
6.本发明的另一目的在于提供一种利用所述热场直拉法生长无位错锗单晶的生长工艺。
7.为实现上述目的,本发明采用以下技术方案:
8.一种直拉法生长无位错锗单晶热场,该热场的结构包括筒形主加热器和圆盘形底加热器,在主加热器外层依次设置有石墨保温桶、固化碳毡保温桶,在石墨保温桶和固化碳毡保温桶上端设有紧贴炉壁的多层保温盖,相邻的两层保温盖之间用石英块隔开;热屏悬
挂在保温盖上,并从保温盖朝向靠近单晶的方向延伸到熔体液面上方的位置;热屏采用多层结构设计,热屏的主体结构为喇叭形,靠近单晶的内层热屏采用上薄下厚的楔形结构,两层热屏之间具有间隙。
9.优选地,所述保温盖为两层结构,具有上保温盖和下保温盖;所述热屏具有两层结构,内层热屏悬挂于上保温盖,外层热屏悬挂在下保温盖上。
10.优选地,所述外层热屏厚度整体一致,为8-10mm;所述内热屏的上端厚度为5-6mm,下端厚度为20-22mm。
11.优选地,所述内层热屏与外层热屏之间的间距为10-15mm。
12.优选地,所述内层热屏和所述外层热屏的下端与熔体液面之间的距离相同,均小于10mm。
13.优选地,所述热屏高度为280-300mm,在热屏下端位置处,内层热屏的内径为190-200mm。
14.本发明所提供的直拉法生长无位错锗单晶热场,通过主加热和底加热器双加热形式实现更低的拉晶埚位,保证熔体足够小的径向温度梯度,通过紧贴炉壁的多层保温盖和多层楔形热屏组合进行熔体上部温度梯度调节,保证晶体纵向温度梯度适宜,避免出现因温度梯度过小而难以拉晶,或者温度梯度过大而产生新位错的情况,从而实现无位错锗单晶的拉制。
15.直拉无位错锗单晶的一般步骤为将籽晶浸入熔体后,进行缩颈、放肩、转肩、等径、收尾、停炉程序,而在单晶生长过程中需要在不同阶段配合相应的提拉速度以及温度变化曲线。然而,对于无位错锗单晶的生长而言,为了避免单晶生长过程中位错的产生,必须尽量减少单晶炉中热场温度的变化,保证单晶生长环境的稳定性,因此,本发明制定了与上述热场结构相配套的生长工艺方案,具体包括以下步骤:
16.(1)籽晶浸入:对于锗单晶而言,当晶体温度达到650℃-700℃之间时,就能够因应力作用而产生位错。因此籽晶浸入熔体前,需要分为四个烤晶悬停位置,使籽晶下端缓慢地从冷区浸入热区,分别为悬停在熔体上方1000mm-600mm、600mm-300mm、300mm-100mm、100mm-5mm位置,每个位置悬停时间为10min-20min,然后使籽晶浸入熔体1mm-5mm,充分熔接。
17.(2)缩颈:籽晶熔接完毕后,温度减低0℃-5℃,设定晶升0.1mm/min-0.2mm/min,持续30min-1h,然后继续降低温度,同时拉速逐步提升到0.5mm/min-1.2mm/min,缩颈直径为3mm-5mm,保持拉速稳定,缩颈长度控制在150mm-200mm之间。
18.(3)放肩:缩颈结束后,保持温度不变,将拉速降低至0.1mm/min-0.2mm/min,开始放肩,随着放肩长度和直径的增加,晶体散热量也会逐步增加,通过逐步提升拉速,保证晶体放肩角度稳定在60
°‑
90
°
,放肩过程中不进行温度调节。
19.(4)转肩:放肩直径距离目标直径相差3mm-5mm时,开始转肩,转肩时将放肩最终拉速提升10%-20%,使单晶逐步缓慢达到目标直径,转肩过程中不进行温度调节。
20.(5)等径:转肩结束后,微调晶升速度,保证单晶等径生长,等径过程中不进行温度调节。
21.(6)收尾:等径生长结束后,以等径最终拉速为基础,每生长10mm-15mm,晶升补偿为最终等径拉速的5%-8%,收尾长度最少为单晶直径1-1.2倍。
22.(7)停炉:单晶收尾完毕后,保持晶体位置不变,坩埚下降25-40mm,使加热器功率均匀缓慢降至0kw,降温过程时间为10-15小时。
23.本发明的有益效果在于:
24.本发明提出了一种主加热与底加热相互配合方式,上部加装紧贴炉壁的多层保温盖和多层楔形石墨热屏,保证埚位降低获得较小的径向温度梯度同时,不会出现埚底结晶现象,也不会出现因埚位较低,纵向梯度太小而出现难以拉晶的情况。同时通过调节熔体上方热屏层数,控制晶体纵向温度梯度适宜,保证单晶放肩等径过程中基本不需要进行温度调节,保证晶体生长过程中的温度环境稳定。
25.本发明采用上述热场系统和工艺相互配合的形式,大大减少了传统热场和工艺容易出现的无位错锗单晶断棱产生大量位错的几率。使用传统热场和工艺,在无位错锗单晶拉制过程中,尤其是更大尺寸的无位错锗单晶,常会因为熔体上部温度梯度调节不合理出现单晶结晶潜热释放不及时,出现单晶断棱,位错大量增殖问题。而通过本发明的热场结构,实现熔体上部温度的可调节,并通过多层上保温盖紧贴炉壁,以及多层热屏之间相互不接触,给单晶结晶潜热释放提供更好的温度梯度环境,更容易实现完整无位错锗单晶的拉制。
附图说明
26.图1为本发明的热场结构模型的结构示意图。
27.图2为本发明实施例1中所获得的无位错腐蚀坑图谱。
28.图3单晶断棱后的位错测试腐蚀坑图谱。
具体实施方式
29.下面结合附图和本发明的具体实施方式对本发明通作进一步说明。
30.本发明的直拉法生长无位错锗单晶热场的结构包括筒形主加热器和圆盘形底加热器,在主加热器外层依次设置有石墨保温桶、固化碳毡保温桶,在石墨保温桶和固化碳毡保温桶上端设有紧贴炉壁的多层保温盖,相邻的两层保温盖之间用石英块隔开;热屏悬挂在保温盖上,并从保温盖朝向靠近单晶的方向延伸到熔体液面上方的位置;热屏采用多层结构设计,热屏的主体结构为喇叭形,靠近单晶的内层热屏采用上薄下厚的楔形结构,两层热屏之间具有间隙。
31.如图1所示,作为本发明一种热场结构除了采用筒形主加热器6和底部圆盘形的底加热器8(采用石墨底电极9供电)的双加热器模式外,在热屏部分采用两层热屏,材料为石墨。靠近单晶为内层热屏1,靠近坩埚为外层热屏2,热屏的主体结构采用喇叭形,外层热屏2的上下厚度相同,厚度为8-10mm;内层热屏1采用上薄下厚的楔形结构,上端的厚度为5-6mm,下端的厚度为20-22mm;两层热屏间距即两层热屏之间的缝隙的宽度为10-15mm。保温盖采用两层保温盖,包括上保温盖3和下保温盖4,上保温盖3和下保温盖4之间用石英块5隔开,共同叠放在固化碳毡7和石墨保温桶11的顶部。上保温盖3和下保温盖4的外沿与炉壁10保持良好接触,便于热量通过水冷炉壁导走,热屏结构以及固定方式,特别是上保温盖和炉壁接触的情况对轴向温度梯度影响较大,变化幅度可超过5℃/cm以上。热屏高度280-300mm,内层热屏下端的内径为190-200mm。两层热屏离液面的距离相同,均小于10mm。
32.实施例1
33.该实施例中利用图1所示的热场结构拉制6英寸锗单晶,该热场结构中的各部分的尺寸数据为:
34.外层热屏厚度为10mm;内层热屏上端的厚度为6mm,下端的厚度为22mm;两层热屏之间的距离为15mm;热屏高度为300mm,内层热屏下端的内径为200mm。
35.具体拉制过程包括以下步骤:
36.(1)籽晶浸入:籽晶浸入熔体前,使籽晶缓慢从冷区浸入热区,分别为悬停在熔体上方600mm、300mm、100mm、5mm的位置,每个位置悬停时间为10min,然后使籽晶浸入熔体约5mm,充分熔接。
37.(2)缩颈:籽晶熔接完毕后,温度减低3℃,设定晶升0.1mm/min,持续1h,然后继续降低温度,同时拉速逐步提升到0.6mm/min,缩颈直径约5mm,保持拉速稳定,缩颈长度控制在200mm。
38.(3)放肩:缩颈结束后,保持温度不变,将拉速降低至0.1mm/min,开始放肩,随着放肩长度和直径的增加,晶体散热量也会逐步增加,通过逐步提升拉速,保证晶体放肩角度稳定在45
°
左右,放肩过程中不进行温度调节。
39.(4)转肩:放肩直径距离目标直径相差5mm时,开始转肩,转肩时将放肩最终拉速提升20%,使单晶逐步缓慢达到目标直径,转肩过程中不进行温度调节。
40.(5)等径:转肩结束后,微调晶升速度,保证单晶等径生长,等径过程中不进行温度调节。
41.(6)收尾:等径生长结束后,以等径最终拉速为基础,每生长10mm,晶升补偿0.05mm/min,收尾长度最少为单晶直径1.2倍。
42.(7)停炉:单晶收尾完毕后,保持晶体位置不变,坩埚下降25mm,使加热器功率均匀缓慢降至0kw,降温过程时间约10小时。
43.采用本发明热场和工艺拉制出的6英寸无位错锗单晶,通过肉眼观察单晶表面,发现单晶表面棱线清晰连贯,未出现断棱情况。切取头尾测试片,依据gb/t5252-2020,进行位错测试,如图2所示的图谱可以看出,单晶无位错。
44.而一般现有无位错锗单晶拉制工艺多为与热场相匹配的工艺参数。虽与本实施例相近,但是籽晶多不采用悬停分布进行熔接,同时因热场温度梯度的不同,很难很好的实现锗单晶结晶潜热释放,造成单晶在拉制过程中容易出现断棱情况,并且一但断棱,则会出现大量位错增殖情况。如图3所示的一例断棱后的位错测试腐蚀坑图谱,可以看出有大量的位错,无法获得无位错单晶。
再多了解一些
本文用于企业家、创业者技术爱好者查询,结果仅供参考。