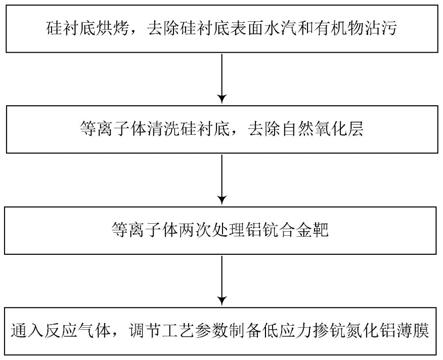
1.本发明涉及一种近零应力掺钪氮化铝薄膜制备方法,属于半导体制造技术领域。
背景技术:
2.随着5g产业的蓬勃发展,基于fbar(薄膜体声波谐振器)滤波器因其在较高频率工作时仍具有优异性能,成为研究的热点。氮化铝(aln)具有纵波声速大、与mems(微机电系统)工艺兼容且易于生产的优势,是fbar滤波器压电层的主流材料,但aln的机电耦合系数较低,滤波器可实现的带宽较窄,限制了aln薄膜的应用范围。掺钪(sc)氮化铝薄膜具有更高的压电系数且制备工艺与aln类似,是作为压电层的理想材料。
3.然而掺钪氮化铝常采用反应溅射的方法制备,工艺参数不当时,工艺过程中会在靶材表面生成掺钪氮化铝,随着工艺的继续进行,基片上掺钪氮化铝的制备速率不稳定,逐渐降低,严重时停止生长,即发生靶中毒现象。另外,掺钪氮化铝薄膜具有较大的应力,严重时会导致谐振器膜裂和脱落,器件性能失效。
技术实现要素:
4.为了解决上述背景中存在的技术问题,本发明提出了一种近零应力掺钪氮化铝薄膜制备方法。
5.本发明为解决其技术问题采用如下技术方案:
6.一种近零应力掺钪氮化铝薄膜制备方法,包括以下步骤:
7.a.将硅衬底传入烘烤腔进行除气烘烤,去除硅衬底表面水汽和有机物沾污;
8.b.对硅衬底进行预清洗,去除自然氧化层;
9.c.对溅射靶材进行预处理,获得稳定的掺钪氮化铝生长状态;
10.d.向腔体内通入高纯氩气和氮气,调节气体流量、直流功率、射频功率对掺钪铝靶进行溅射,在硅衬底上形成近零应力的掺钪氮化铝薄膜。
11.所述硅衬底厚度为400~725μm,直径为150~200mm。
12.所述溅射靶材为铝钪合金靶,铝材料纯度为>99.9%,钪原子比例为8~40%,靶材直径为344mm,厚度为14mm,靶基距为40~60mm。
13.步骤a中,所述将硅衬底传入烘烤腔,烘烤温度为200~300℃,烘烤时间为30~90s。
14.步骤b中,所述将硅衬底进行预清洗,预清洗时间为30~120s。
15.步骤c中,所述对溅射靶材进行两次等离子体处理:
16.第一次等离子体处理通入气体为高纯氩气,流量为40~80sccm,直流功率为5000~8000w,处理时间为30~120s;
17.第二次等离子体处理通入气体为高纯氩气和氮气,氩气流量为25~40sccm,氮气流量为80~128sccm,直流功率为5000~8000w,射频功率为0~90w,处理时间为60~180s。
18.步骤d中,所述通入气体为高纯氩气和氮气,氩气流量为25~40sccm,氮气流量为
80~128sccm,所述直流功率为5000~8000w,所述射频功率为0~90w。
19.所述掺钪氮化铝薄膜的厚度为100~1500nm。
20.本发明的有益效果如下:
21.1、本发明采用磁控反应溅射技术制备掺钪氮化铝薄膜,薄膜厚度均匀性好,钪元素分布均匀,同时对靶材的要求容易掌握,可实现多次重复制备。
22.2、本发明通过调节气体流量、直流功率、射频功率值可获得近零应力的掺钪氮化铝薄膜,有利于提高产品的可靠性。
23.3、本发明不增加额外工艺步骤以及额外设备改造,通过对溅射靶材的两次等离子体轰击处理,获得稳定的掺钪氮化铝生长状态,避免了靶材中毒现象的发生,提高了生产效率,节约了成本。
附图说明
24.图1为本发明的一种近零应力掺钪氮化铝薄膜制备方法流程图。
25.图2为本发明的掺钪氮化铝薄膜应力随直流功率变化曲线图。
26.图3为本发明的工艺时靶电压随时间变化曲线示意图。
27.图4为本发明的掺钪氮化铝薄膜应力随射频功率变化曲线图。
28.图5为本发明的掺钪氮化铝薄膜应力随工艺压力变化曲线图。
29.图6为本发明的实施例中制备的掺钪氮化铝薄膜厚度分布测试结果图。
30.图7为本发明的实施例中制备的掺钪氮化铝薄膜应力测试结果图。
31.图8为本发明的实施例中制备的掺钪氮化铝薄膜横截面形貌图。
具体实施方式
32.下面结合附图对本发明技术方案进行详细说明,但是本发明的保护范围不局限于所述实施例。
33.本发明提供了一种近零应力掺钪氮化铝薄膜制备方法,参阅图1,该方法包括以下步骤:
34.步骤a.将硅衬底传入烘烤腔进行除气烘烤,去除硅衬底表面水汽和有机物沾污;
35.步骤b.对硅衬底进行等离子体预清洗,去除硅衬底表面自然氧化层;
36.步骤c.对溅射合金靶材进行等离子体预处理,获得稳定的掺钪氮化铝生长状态;
37.步骤d.向腔体内通入高纯氩气和氮气,调节气体流量、直流功率、射频功率对掺钪铝靶进行溅射,在硅衬底上形成低应力的掺钪氮化铝薄膜。
38.下面结合实施例对本发明作进一步的详细说明。
39.实施例1
40.本实施例中所采用的硅衬底厚度为400μm,直径为150mm。溅射靶材为铝钪合金靶,铝材料纯度为99.9%,钪原子比例为8%,靶材直径为344mm,厚度为14mm,靶基距为48mm。工艺前工艺腔的真空度抽至3.0
×
10
‑8torr。
41.在步骤a中,对传入的硅衬底进行300℃烘烤,烘烤时间为90s,使硅衬底表面尽可能的干燥,从而增加掺钪氮化铝薄膜与硅衬底之间的粘附性。
42.在步骤b中,对硅衬底进行等离子体清洗,通入清洗腔的气体为氩气,流量是
5sccm,加载到射频线圈的功率范围为150w,加载到下电极的功率为300w,此时对应的sio2刻蚀速率为左右。而硅衬底表面的自然氧化层厚度通常为因此本实施例中将预清洗时间设置为60s。
43.在步骤c中,对靶材进行两次等离子体清洗,第一次清洗的目的是去除铝钪合金靶表面生成的掺钪氮化铝薄膜,在正式溅射工艺前获得一个靶材的稳定状态;第二次清洗是使工艺腔达到一个稳定的掺钪氮化铝生长状态。
44.对靶材采用第一次等离子体清洗,通入的气体是高纯氩气,流量为50sccm,直流功率为8000w,处理时间为60s。
45.对靶材采用第二次等离子体清洗,通入的气体与第一次清洗不同,同时通入35sccm的高纯氩气和112sccm的高纯氮气,直流功率和射频功率与主溅射工艺中参数一致,目的是避免在主溅射开始阶段由于靶材状态与工艺阶段的差异而导致沉积的掺钪氮化铝薄膜组分不稳定。通过第二次等离子体清洗,相当于在主溅射时已经直接过渡到稳定的掺钪氮化铝薄膜生长状态,处理时间为80s。
46.本发明中掺钪氮化铝薄膜中的应力(stress)随溅射直流功率(dc power)的增大而减小,并存在由张应力向压应力转换的趋势,参阅图2。
47.根据掺钪氮化铝中应力与直流功率之间的关系,将直流功率设置为8000w,射频偏置功率设置为0w,工艺时间为600s,同时通入35sccm的高纯氩气和112sccm的高纯氮气,制备的掺钪氮化铝厚度为710nm,测得应力为264mpa,如要制备近零应力的掺钪氮化铝薄膜,需进一步增加直流溅射功率。
48.对靶材进行两次等离子体清洗还具有延长工艺腔体内防着备件使用寿命的优点。原因是通过两次清洗,会在工艺腔体内壁上交替生成铝薄膜和掺钪氮化铝薄膜,由于铝薄膜为金属,与内壁的粘附性较好,掺钪氮化铝薄膜不易脱落,若是内壁上完全由掺钪氮化铝薄膜覆盖,由于薄膜本身应力较大,易脱落,大大缩短工艺腔体的清洗维护保养周期。
49.本发明采用的是反应溅射法制备掺钪氮化铝薄膜,通过调节直流功率、射频功率、氩气和氮气的流量可以有效避免靶中毒情况的发生。在步骤d中,如果工艺参数选取不合适,会造成靶中毒情况,即靶材表面生成的掺钪氮化铝薄膜不断增加,刻蚀速率与生长速率达不到平衡,随着靶材表面掺钪氮化铝进一步持续增加,无掺钪氮化铝沉积到硅衬底上,靶中毒现象发生。
50.本发明中可以通过观测靶电压(voltage)随时间(time)变化关系来进行是否发生靶中毒的判断,参阅图3,正常工艺时,靶电压几乎维持不变;发生靶中毒时,工艺初始阶段靶电压会和正常工艺时一致,随着工艺的进行,靶电压会快速增大,稳定在一恒定值,这是因为靶材表面完全被掺钪氮化铝覆盖,无法继续生长,即靶材与衬底之间的阻抗不再变化,而直流功率也未发生变化,故靶电压不再变化。
51.实施例2
52.本实施例中所采用的硅衬底厚度为400μm,直径为150mm。溅射靶材为铝钪合金靶,铝材料纯度为99.9%,钪原子比例为8%,靶材直径为344mm,厚度为14mm,靶基距为48mm。工艺前工艺腔的真空度抽至3.0
×
10
‑8torr。
53.在步骤a中,对传入的硅衬底进行300℃烘烤,烘烤时间为90s。
54.在步骤b中,对硅衬底进行等离子体清洗,通入清洗腔的气体为氩气,流量是
5sccm,加载到射频线圈的功率范围为150w,加载到下电极的功率为300w,预清洗时间设置为60s。
55.在步骤c中,对靶材进行两次等离子体清洗。
56.对靶材采用第一次等离子体清洗,通入的气体是高纯氩气,流量为50sccm,直流功率为8000w,处理时间为60s。
57.对靶材采用第二次等离子体清洗,同时通入35sccm的高纯氩气和112sccm的高纯氮气,直流功率和射频功率与主溅射工艺中参数一致,处理时间为80s。
58.本发明中,掺钪氮化铝薄膜中的应力(stress)随射频偏置功率(rf bias)变化的曲线参阅图4,当射频功率<40w时,应力几乎不变,当射频功率>40w时,应力随射频功率增加而减小,并存在由张应力向压应力转换的趋势。
59.在步骤d中,通入35sccm的高纯氩气和112sccm的高纯氮气,直流功率为8000w,射频偏置功率为60w,工艺时间为610s,制备的掺钪氮化铝薄膜厚度为697nm,测得应力为
‑
1.5mpa,应力接近于0mpa。
60.实施例3
61.本实施例中所采用的硅衬底厚度为400μm,直径为150mm。溅射靶材为铝钪合金靶,铝材料纯度为99.9%,钪原子比例为8%,靶材直径为344mm,厚度为14mm,靶基距为48mm。工艺前工艺腔的真空度抽至3.0
×
10
‑8torr。
62.在步骤a中,对传入的硅衬底进行300℃烘烤,烘烤时间为90s。
63.在步骤b中,对硅衬底进行等离子体清洗,通入清洗腔的气体为氩气,流量是5sccm,加载到射频线圈的功率范围为150w,加载到下电极的功率为300w,预清洗时间设置为60s。
64.在步骤c中,对靶材进行两次等离子体清洗。
65.对靶材采用第一次等离子体清洗,通入的气体是高纯氩气,流量为50sccm,直流功率为8000w,处理时间为60s。
66.对靶材采用第二次等离子体清洗,通入的气体与第一次清洗不同,同时通入高纯氩气高纯氮气,气体流量与主溅射工艺中参数一致,直流功率为8000w,射频偏置功率为0w,处理时间为80s。
67.本发明中,掺钪氮化铝薄膜中的应力(stress)随工艺气压(pressure)增大而增大,并存在由压应力向张应力转换的趋势,参阅图5。工艺时腔体气压主要与参与反应的氩气和氮气的流量相关,对应关系参阅表1。
68.表1
[0069] 氩气流量(sccm)氮气流量(sccm)工艺气压(mtorr)120643.18225803.95330964.854351125.575401286.37
[0070]
在步骤d中,通入25sccm的高纯氩气和80sccm的高纯氮气,直流功率为8000w,射频偏置功率为0w,工艺时间为555s,制备的掺钪氮化铝薄膜厚度为700nm,测得应力为
‑
33mpa,
如要制备近零应力的掺钪氮化铝薄膜,需稍微增加高纯氩气和氮气的流量。
[0071]
实施例4
[0072]
本实施例中所采用的硅衬底厚度为400μm,直径为150mm。溅射靶材为铝钪合金靶,铝材料纯度为99.9%,钪原子比例为8%,靶材直径为344mm,厚度为14mm,靶基距为48mm。工艺前工艺腔的真空度抽至3.0
×
10
‑8torr。
[0073]
在步骤a中,对传入的硅衬底进行300℃烘烤,烘烤时间为90s。
[0074]
在步骤b中,对硅衬底进行等离子体清洗,通入清洗腔的气体为氩气,流量是5sccm,加载到射频线圈的功率范围为150w,加载到下电极的功率为300w,预清洗时间设置为60s左右。
[0075]
在步骤c中,对靶材进行两次等离子体清洗。
[0076]
对靶材采用第一次等离子体清洗,通入的气体是高纯氩气,流量为50sccm,直流功率为8000w,处理时间为60s。
[0077]
对靶材采用第二次等离子体清洗,同时通入35sccm的高纯氩气和112sccm的高纯氮气,直流功率为8000w,射频偏置功率为70w,处理时间为80s。在步骤d中,通入35sccm的高纯氩气和112sccm的高纯氮气,直流功率为8000w,射频偏置功率为70w,工艺时间为600s,制备的掺钪氮化铝厚度平均值为均匀性为0.2%,测试结果参阅图6。根据测试的薄膜厚度,测试薄膜中的应力,应力(stress)大小为
‑
0.4591mpa,测试结果参阅图7,测得掺钪氮化铝薄膜的半峰宽(fwhm)为1.428
°
,横截面形貌图参阅图8,从图中可以看出薄膜由大量的柱状结构组成,这些柱状结构多垂直于衬底表面生长,直观地说明了掺钪氮化铝薄膜沿c轴方向生长,有利于提高fbar器件性能。
再多了解一些
本文用于企业家、创业者技术爱好者查询,结果仅供参考。