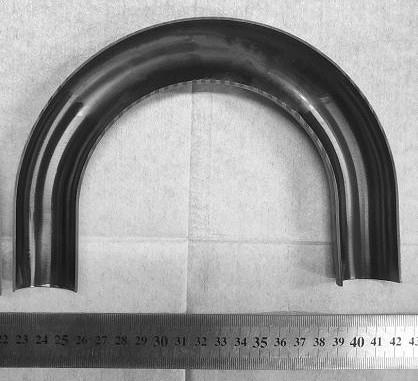
1.本发明涉及管类工件内壁表面改性领域,尤其涉及一种弯管内壁类金刚石碳基涂层沉积方法。
背景技术:
2.弯管系列管道配件产品广泛应用于石油、化工、医药、电力、航天、消防、军工、冶金、造船、燃气、核电、城建、水暖及环境保护等行业建设和检验的需要。弯管的质量直接影响到这些行业的产品的结构合理性、安全性和可靠性。通常,在弯管加工过程中,由于工艺条件和操作等原因会使得弯管产生各种程度不同的缺陷,同时由于其通常服役于高强度、腐蚀与摩擦共存的工况环境,而这些缺陷往往会成为起始失效点,并且向四周扩散从而直接影响产品的安全性,同时也会降低其服役寿命。
3.表面处理技术是一种减弱这些缺陷对弯管性能影响的有效手段。例如热喷涂、电镀和堆焊等技术。但喷涂内壁涂层技术对管道内径有要求,如采用先进等离子喷涂设备的内孔喷枪在管道内壁喷涂耐磨涂层,该技术适合长度小于600mm、内径大于160mm 的管道。另外,由于等离子喷涂涂层结合强度较低,不适合短管道组焊成长管道的情况,在焊接时,由于局部高温涂层容易脱落。超音速火焰喷涂和电弧喷涂都只能适用于更大口径的管道。中国专利cn104611665a公开的一种在大尺寸弯管类工件上热喷涂制备涂层的方法,需要采用特殊设计的弯管喷涂工装进行夹持固定,通用性较差,工艺复杂;另外仅适用于曲率半径大于或等于2m弯管件,而弯管通常曲率半径为0.5 m以下。弯管半径减小意味着其曲率半径减小,同时也表明在径向的弯曲应力的增加;另外管径越细也就意味着在弯曲过程中能达到的轴向曲率半径就会越小,也会导致弯曲应力的增加,从而大大增加类金刚石碳膜的沉积难度。
4.类金刚石碳基涂层因其高的机械强度、高的化学惰性、低的摩擦系数和磨损率以及优异的抗腐蚀能力而常被用于表面防护材料。据报道,直管内壁的类金刚石碳基涂层具有高硬度和优异耐蚀性能及摩擦学性能,能效地延长管道的使用寿命。而弯管内壁类金刚石碳基涂层沉积的技术难点在于:一是弯管具有双重应力(轴向和径向)使得类金刚石碳基涂层生长难度大大增加;二是通入的氩气、硅烷和乙炔混合气从进气口沿管道再到出气口,这个过程气体的流动方向改变180
°
,由于受到外管壁的阻力,气体的流速会逐渐减小,致使产生的等离子体密度在管内发布不均匀,很难实现类金刚石碳基涂层的均匀沉积。
技术实现要素:
5.本发明所要解决的技术问题是提供一种方法简单、工艺稳定的弯管内壁类金刚石碳基涂层沉积方法。
6.为解决上述问题,本发明所述的一种弯管内壁类金刚石碳基涂层沉积方法,包括以下步骤:
⑴
将弯管工件抛光处理并清洗后,装入等离子体化学气相沉积室的真空腔内;
⑵
通入氩气,在弯管内壁进行氩等离子体轰击清洗和预热管内壁;
⑶
引入硅烷,在弯管内壁进行原位等离子体浸没注入硅元素,沉积得到厚度为50~1000 nm的硅中间层;
⑷
将弯管作为阴极,在管件上施加负脉冲偏压,保持氩气、硅烷气流量不变,交替通入不同流量的乙炔,最终在弯管内壁获得厚度为10~20 μm的掺硅类金刚石碳基涂层。
7.所述步骤
⑴
中弯管的形状包含直角管和u型管,且其直径为10~100 mm。
8.所述步骤
⑵
中清洗条件是指对弯管施加5~10 kv的负脉冲偏压,脉冲频率为1~2khz,氩气流量为100~500 sccm,辉光放电真空压力为4~8 pa,清洗时间为10~120 min。
9.所述步骤
⑶
中硅中间层的沉积条件是指在弯管内壁上施加10~20 kv的负脉冲偏压,脉冲频率为1~2 khz,氩气流量为100~500 sccm,硅烷气流量为50~150 sccm,辉光放电真空压力为10~20 pa,硅元素注入时间为10~60 min。
10.所述步骤
⑷
中掺硅类金刚石碳基涂层的沉积条件是指在管件上施加负脉冲偏压为500~1500v,脉冲频率为100~1500hz,氩气流量为100~500 sccm,硅烷气流量为50~150 sccm,乙炔气流量为50~500 sccm,辉光放电真空压力为12~20 pa,沉积时间为30~300min。
11.本发明与现有技术相比具有以下优点:1、本发明利用高压直流脉冲电源对管内壁进行ar等离子体去杂质、油污分子、氧化层和活化,从而改善界面状态,有助于增强膜基结合力。
12.2、本发明利用高能离子注入、空心阴极高密度等离子体化学气相沉积一体化技术,从沉积的涂层的结构入手,在基底与涂层之间沉积一层si中间层;用于缓解界面失配,并且通过改变通入的气体前驱体的成分沉积压应力与拉应力交替的多层结构减小涂层内应力;通过工艺优化降低涂层的沉积速率从而实现弯管内壁类金刚石碳基涂层的沉积。另一方面,通过增大前驱体气体流量和干泵抽速来实现气体在u型管中均匀的填充。
13.3、本发明能够在管内形成均匀稳定、高密度的辉光等离子体,在较低的真空度下均匀沉积高机械强度、低摩擦系数、优异抗磨性能和优异耐腐蚀性能的类金刚石碳基涂层,从而解决了在弯管在加工过程中由于弯曲产生的裂纹和缺陷导致其服役寿命大大缩短的技术难题。同时通过设计压应力与拉引力交替的多层结构以及工艺优化解决了弯管由于双重应力存在难以沉积类金刚石碳基涂层的难题。
14.4、采用本发明方法,成功在弯管内壁沉积了具有高强度,低摩擦,高耐磨和高耐腐蚀的类金刚石碳基涂层,解决了小曲率半径的弯管内壁类金刚石碳基涂层的沉积问题。
15.5、本发明方法简单,操作灵活,工艺稳定,可重复性好。且无需特殊的固定装置,部件更换方便,加工成本低,易于推广应用。
附图说明
16.下面结合附图对本发明的具体实施方式作进一步详细的说明。
17.图1为本发明获得的内径30 mm,管壁厚1.5mm,曲率半径80 mm,管高130 mm304不锈钢u型管内壁超厚类金刚石碳基涂层。
18.图2为本发明获得的内径45 mm,管壁厚1.5 mm,曲率半径85 mm,管高150 mm 304不锈钢u型管内壁类金刚石碳基涂层。
19.图3为本发明获得的内径15 mm,管壁厚1.5 mm,304不锈钢直角管管内壁类金刚石
碳基涂层。
20.图4为本发明获得的内径15 mm,管壁厚1.5 mm,曲率半径65 mm,管高200 mm 铸铁u型管内壁类金刚石碳基涂层。
具体实施方式
21.一种弯管内壁类金刚石碳基涂层沉积方法,包括以下步骤:
⑴
将弯管工件抛光处理并清洗后,装入等离子体化学气相沉积室的真空腔内。该沉积室具有等离子体浸没注入、空心阴极等离子体化学气相沉积等技术功能。
22.弯管的形状包含直角管和u型管,且其直径为10~100 mm。弯管的材质包含不锈钢、铸铁、铝等大多数常用金属。
23.⑵
通入氩气,在弯管内壁进行氩等离子体轰击清洗和预热管内壁。即:对弯管施加5~10 kv的负脉冲偏压,脉冲频率为1~2khz,氩气流量为100~500 sccm,辉光放电真空压力为4~8 pa,清洗时间为10~120 min。操作人员可按照弯管材质和表面状态选择清洗时长和工艺参数。
24.⑶
引入硅烷,在弯管内壁进行原位等离子体浸没注入硅元素,沉积得到厚度为50~1000 nm的硅中间层。
25.其中:硅中间层的沉积条件是指在弯管内壁上施加10~20 kv的负脉冲偏压,脉冲频率为1~2 khz,氩气流量为100~500 sccm,硅烷气流量为50~150 sccm,辉光放电真空压力为10~20 pa,硅元素注入时间为10~60 min。依据弯管材质与类金刚石碳基涂层的界面差异适当选择。
26.利用高压直流脉冲电源在管内壁实施硅元素注入,高能离子注入这一关键技术能够显著提高后续类金刚石碳基涂层与管内壁基底的结合强度。
27.⑷
将弯管作为阴极,在管件上施加负脉冲偏压,保持氩气、硅烷气流量不变,交替通入不同流量的乙炔,最终在弯管内壁获得厚度为10~20 μm的掺硅类金刚石碳基涂层。
28.其中:掺硅类金刚石碳基涂层的沉积条件是指在管件上施加负脉冲偏压为500~1500v,脉冲频率为100~1500hz,氩气流量为100~500 sccm,硅烷气流量为50~150 sccm,乙炔气流量为50~500 sccm,辉光放电真空压力为12~20 pa,沉积时间为30~300min。
29.步骤
⑵
~
⑷
在弯管中前驱体气体的引入必须增大气流量和气体抽速并且保持压强恒定。
30.实施例1u型管件为内径30 mm,管壁厚1.5 mm,曲率半径80 mm,管高130 mm的304不锈钢管。
31.⑴
将u型管用丙酮、无水乙醇超声清洗后,置于等离子体化学气相沉积室的真空腔中,抽本底真空至3
×
10
‑3pa。
32.⑵
通入300 sccm氩气,利用高压直流脉冲电源在管壁上施加6 kv的负脉冲偏压,脉冲频率为1.5 khz,保持真空腔压力为5 pa,对管内壁实施40 min的氩等离子体清洗和预热管内壁。
33.⑶
通入300 sccm氩气和100 sccm硅烷,负脉冲偏压调至15 kv,高压直流脉冲频率为1.5 khz,保持真空腔压力为15 pa,对管内壁实施30 min的硅元素注入。
34.⑷
保持氩气、硅烷气流量不变,交替通入300 sccm和100 sccm乙炔,利用低压直流脉冲电源在管件上施加650 v的负偏压,脉冲频率为500 hz,保持真空腔压力为20 pa和13 pa,沉积180 min后,最终在管内壁获得约为10 μm厚的类金刚石碳基涂层,如图1所示。
35.实施例2管件为内径45 mm,管壁厚1.5 mm,曲率半径85 mm,管高150 mm的304不锈钢管。
36.步骤
⑴
~
⑵
同实施例1。
37.⑶
通入200 sccm氩气和50 sccm硅烷,负脉冲偏压调至15 kv,高压直流脉冲频率为1.5 khz,保持真空腔压力为20 pa,对管内壁实施20 min的硅元素注入。
38.⑷
保持氩气、硅烷气流量不变,交替通入150 sccm和50 sccm乙炔,利用低压直流脉冲电源在管件上施加800 v的负偏压,脉冲频率为1000 hz,保持真空腔压力为20 pa和13 pa,沉积240 min后,最终在管内壁获得约为15 μm厚的类金刚石碳基涂层,如图2所示。
39.实施例3管件为内径15 mm,管壁厚1.5 mm的304不锈钢直角管。
40.步骤
⑴
~
⑵
同实施例1。
41.⑶
通入400 sccm氩气和150 sccm硅烷,负脉冲偏压调至15 kv,高压直流脉冲频率为1.5 khz,保持真空腔压力为10 pa,对管内壁实施30 min的硅元素注入。
42.⑷
保持氩气、硅烷气流量不变,交替通入450 sccm和150 sccm乙炔,利用低压直流脉冲电源在管件上施加650 v的负偏压,脉冲频率为100 hz,保持真空腔压力为20 pa和13 pa,沉积120 min后,最终在管内壁获得约为6 μm厚的类金刚石碳基涂层,如图3所示。
43.实施例4管件为内径15 mm,管壁厚1.5 mm,曲率半径65 mm,管高200 mm的铸铁管。
44.步骤
⑴
~
⑵
同实施例1。
45.⑶
通入400 sccm氩气和150 sccm硅烷,负脉冲偏压调至15 kv,高压直流脉冲频率为1.5 khz,保持真空腔压力为10 pa,对管内壁实施30 min的硅元素注入。
46.⑷
保持氩气、硅烷气流量不变,交替通入450 sccm和150 sccm乙炔,利用低压直流脉冲电源在管件上施加650 v的负偏压,脉冲频率为100 hz,保持真空腔压力为20 pa和13 pa,沉积120 min后,最终在管内壁获得约为6 μm厚的类金刚石碳基涂层,如图4所示。
47.采用摩擦磨损试验机对实施例1~4所得弯管内壁超厚类金刚石碳基涂层进行性能评价,摩擦条件采用球
‑
盘往复模式,往复滑动行程为5mm,往复频率为5hz,法向载荷为5 n,摩擦对偶为φ6 mm的gcr15钢球,测试环境为大气。
48.采用纳米压痕仪对弯管内壁类金刚石碳基涂层的机械性能进行评价。
49.采用电化学工作站在3.5 wt% nacl溶液中评价弯管内壁的电化学腐蚀行为,极化测试扫速为10 mv/s,阻抗的振幅为10 mv。
50.测试结果见表1。
51.表1
ꢀꢀꢀꢀꢀ
测试结果
由表1可以看出:弯管内壁类金刚石碳基涂层摩擦系数稳定在0.06~0.04,磨损率低至2.5
×
10
‑7,硬度均在12 gpa以上,并且其腐蚀电流密度相较于裸基底降低了两个数量级。
再多了解一些
本文用于企业家、创业者技术爱好者查询,结果仅供参考。