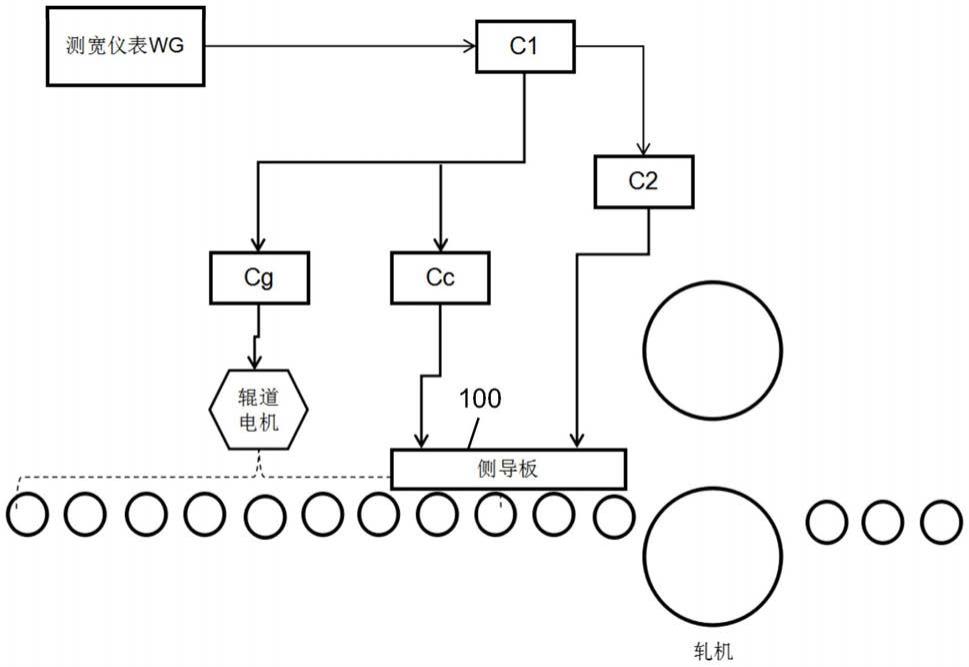
1.本发明涉及中厚板轧制生产线的自动控制技术,更具体地说,涉及一种利用测宽仪对中厚板轧机侧导板自动标定的方法及其装置,尤其涉及测宽仪布置在远离机架位置的中厚板生产线,在换辊结束后,自动利用测宽仪进行轧机侧导板开口度进行标定的控制方法。
背景技术:
2.目前有的现代化中厚板轧制生产线装备有测宽仪(wg),为了保证测宽仪测量环境少受水雾、氧化铁锈尘的影响,不至于过于恶劣,测宽仪有时被安装在距离轧机较远的产线位置上,仅在钢板完成轧制时,进行中间板宽度测量(布置粗轧机和精轧机之间,距离两者都较远),或成品宽度测量(布置在精轧机后较远位置),用于生产产品质量监督检查。
3.现代化中厚板轧机机架前后布置的侧导板,又被称为推床,是钢板进入轧机的导卫装置,其基本作用是通过夹持及引导,将钢板对中(对齐轧机中心线)地导入轧机中,通常情况下,侧导板通过液压控制,会减少钢板长度方向的侧弯(俗称“镰刀弯”)的产生。但在各中厚板厂的生产实践中,因为对中夹持操作的侧导板开口度可以大致表征钢板宽度,所以侧导板又演化出多种附加作用,比如指导后续道次侧导板开口度(cn103962387a,一种轧钢侧导板位置跟随的动态控制方法),又如采用侧导板开口度作为实测宽度校验模型计算宽度,并修正立辊辊缝设定(cn102825072a,侧导板对中测宽修正立辊辊缝设定的方法),再如侧导板开口度作为轧机宽度控制模型的输入值之一,与定宽机前测宽仪数据、上游工序板坯基准值等相互比较,推断出宽度控制模型最终接收的板坯宽度数值(cn105642676a,一种利用侧导板辊缝值进行宽度模型控制的方法)。
4.上述这些侧导板附加功能应用效果的好坏,都依赖于侧导板开口度精度,这引起了人们对侧导板标定过程及精度的关注。具体而言,侧导板的标定精度可以分成两个生产工艺关心的精度指标,一个是开口精度,即两导板间距离的电气显示值与实际值之间的偏差,另一个是对中度精度,表征两导板间中心线与轧机中心线的重合情况。对于与宽度控制相关的侧导板附加功能而言,更关注侧导板开口度标定过程与开口度精度。
5.现有的侧导板开口度标定方法是在生产停机期间,操作人员用卷尺直接测量两导板间距离作为参考开口度,手工记录卷尺测量值,并人工输入到电气程序中,由电气程序把参考开口度与侧导板液压缸位置检测数值比较,保存标定偏差,在标定后,电气程序的侧导板开口度测量值实际为位置检测值与标定偏差之和。
6.目前关于侧导板开口度标定的技术方案涉及不多,主要有几个共同特点:
7.1)在生产停机以后实施,不能在生产过程中实施;
8.2)用精心设计的专用装置代替卷尺,进行两导板间距离测量,有些还能代替笔与纸,直接进行信息传递;
9.3)标定流程需要人工操作或者半自动操作,所谓半自动操作是指需要人工启动标定流程,后续标定过程,由电气系统自动完成。
10.对于中厚板轧机侧导板开口度标定方法而言,常规卷尺测量标定方法的问题点如下:
11.1)如同cn202485591u背景技术部分所言,由于侧导板衬板和高温钢板接触摩擦,会产生逐渐磨损,而为修复磨损进行的缺陷处激光堆焊,又经常使得衬板底部变形,测量基准面确认不易。简而言之,即衬板磨损及修复影响侧导板开口度精度,而且衬板磨损是在整个生产周期中偶发出现,磨损情况在生产周期是变化的;
12.2)如同cn206898071u背景技术部分所言,在轧制过程中,如果侧导板液压缸设备状态不佳,可能会发生缓慢内部泄漏,驱动传动链也会产生磨损,这些都影响侧导板开口度精度,使得侧导板测量宽度值偏小。
13.对于上述两个问题点,cn206898071u给出了解决方案,即在标定时,考虑从上个停机标定至今的油缸内泄情况,进行补偿。但是,侧导板常规标定周期是以周为单位,也就是说如果发生内泄,需在几周后才能在标定中体现。
14.综上所述,现有技术的不足之处主要体现在:
15.1)在停机时进行侧导板开口度标定,减少了生产时间,降低了轧线有效作业率;
16.2)除用卷尺方法外,常需要额外添置专用测量装置,增加成本投资与设备维护量;
17.3)多是在机旁现场作业,操作人员的安全风险高;
18.4)标定间隔周期长,对于影响开口度精度的衬板磨损、油缸内泄、传动链磨损等设备状态问题,不能及时适应,影响最终输出的侧导板宽度精度。
技术实现要素:
19.针对现有技术中存在的上述缺陷,本发明的目的是提供一种利用测宽仪对中厚板轧机侧导板自动标定的方法及其装置,利用测宽仪测量宽度,在生产周期初期,花费少量的辊道运输及宽度测量时间,自动进行侧导板开口度标定。
20.为实现上述目的,本发明采用如下技术方案:
21.一方面,一种利用测宽仪对中厚板轧机侧导板自动标定的方法:
22.在轧机或侧导板旁边位置安装有测量钢板宽度的测宽仪表wg,所述测宽仪表wg连接协调联动模块c1,所述协调联动模块c1连接执行模块c2,所述执行模块c2用于驱动所述侧导板的开口度标定,所述协调联动模块c1还连接辊道输送模块cg、及侧导板对中操作模块cc;
23.所述方法包括以下过程:
24.所述协调联动模块c1识别出生产周期的第一块钢板,指令所述辊道输送模块cg将所述第一块钢板移动至所述测宽仪表wg下方;
25.所述测宽仪表wg测得宽度测量数据wi;
26.所述协调联动模块c1指令所述辊道输送模块cg将所述第一块钢板移动至侧导板位置;
27.所述协调联动模块c1指令所述侧导板对中操作模块cc,进行所述侧导板自动对中操作,得到侧导板开口度显示值ki;
28.将所述侧导板开口度显示值ki、所述宽度测量数据wi分别引入所述协调联动模块c1;
29.所述协调联动模块c1计算所述宽度测量数据wi与所述侧导板开口度显示值ki之间的偏差pi=wi-ki;
30.将偏差pi作为标定参考量,被引入所述执行模块c2,所述执行模块c2根据偏差pi,自动进行侧导板标定基准数值pz的替换,完成侧导板开口度自动标定过程。
31.所述侧导板标定基准数值pz替换计算如下:
32.pz
新
=α
×
pi (1-α)
×
pz
旧
33.上式中,pz
旧
是在先执行的侧导板标定基准数值,pz
新
是标定后将执行的侧导板标定基准数值,α为系数。
34.α的取值范围在0.1~0.8之间。
35.另一方面,一种利用测宽仪对中厚板轧机侧导板自动标定的装置,包括:
36.设置在轧机或侧导板旁边位置的测宽仪表wg、与所述测宽仪表wg连接的协调联动模块c1、与所述协调联动模块c1连接的执行模块c2,辊道输送模块cg、以及侧导板对中操作模块cc,
37.所述执行模块c2用于驱动所述侧导板的开口度标定;
38.所述协调联动模块c1、执行模块c2、测宽仪表wg、辊道输送模块cg、以及侧导板对中操作模块cc执行以下操作过程:
39.所述协调联动模块c1识别出生产周期的第一块钢板,指令所述辊道输送模块cg将所述第一块钢板移动至所述测宽仪表wg下方;
40.所述测宽仪表wg测得宽度测量数据wi;
41.所述协调联动模块c1指令所述辊道输送模块cg将所述第一块钢板移动至侧导板位置;
42.所述协调联动模块c1指令所述侧导板对中操作模块cc进行所述侧导板自动对中操作,得到侧导板开口度显示值ki;
43.将所述侧导板开口度显示值ki、所述宽度测量数据wi分别引入所述协调联动模块c1;
44.所述协调联动模块c1计算所述宽度测量数据wi与所述侧导板开口度显示值ki之间的偏差pi=wi-ki;
45.将偏差pi作为标定参考量,被引入所述执行模块c2,所述执行模块c2根据偏差pi,自动进行侧导板标定基准数值pz的替换,完成侧导板开口度自动标定过程。
46.所述侧导板标定基准数值pz替换计算如下:
47.pz
新
=α
×
pi (1-α)
×
pz
旧
48.上式中,pz
旧
是在先执行的侧导板标定基准数值,pz
新
是标定后将执行的侧导板标定基准数值,α为系数。
49.α的取值范围在0.1~0.8之间。
50.在上述的技术方案中,本发明所提供的一种利用测宽仪对中厚板轧机侧导板自动标定的方法,还具有以下几点有益效果:
51.1)节省了侧导板标定时间,从而缩短了生产停机时间,可增加日有效生产作业时间约3分钟,折合日产量约增加0.21%;
52.2)因不需要操作人员在轧机现场操作作业,从本质上保证了操作人员的生产安全
性;
53.3)利用高精度的测宽仪表数据,提高了侧导板宽度精度。
附图说明
54.图1是本发明方法实施例的现场布置示意图;
55.图2是本发明方法实施例的流程示意图;
56.图3是本发明方法实施例的时序示意图。
具体实施方式
57.下面结合附图和实施例进一步说明本发明的技术方案。
58.请结合图1所示,本发明所提供的一种利用测宽仪对中厚板轧机侧导板自动标定的方法,在距离轧机或侧导板较远位置安装有测量钢板宽度的测宽仪表wg,测宽仪表wg连接协调联动模块c1,协调联动模块c1连接执行模块c2,执行模块c2用于驱动侧导板100的开口度标定,协调联动模块c1还连接辊道输送模块cg、及侧导板对中操作模块cc。
59.请结合图2至图3所示,本发明方法具体包括以下过程:
60.当轧机换辊后,在该生产周期的第一块钢板开始轧制时,且在未开始实际轧制前,过程控制l2计算机识别出这是换辊后第一块钢板,于是通知协调联动模块c1,启动自动标定功能。
61.协调联动模块c1通知使轧机打开辊缝,让第一块钢板顺利通过,不进行轧制,协调辊道输送模块cg,将第一块钢板移动至测宽仪表wg下方,协调联动模块c1通知测宽仪表wg开始测量,测得的宽度测量数据wi。
62.然后,协调联动模块c1再协调辊道输送模块cg输送第一块钢板移动至侧导板100位置。
63.然后,协调联动模块c1再协调侧导板对中操作模块cc,开始进行侧导板自动对中操作,自动对中操作结束受,得到侧导板开口度显示值ki。第一块钢板移动、对中操作合计所需时间在1~2分钟。
64.然后,将侧导板开口度显示值ki、宽度测量数据wi分别引入协调联动模块c1,协调联动模块c1计算宽度测量数据wi与侧导板开口度显示值ki之间的偏差pi=wi-ki。
65.然后,将偏差pi作为标定参考量,被协调联动模块c1引入执行模块c2,执行模块c2根据偏差pi,自动进行侧导板标定基准数值pz的替换,侧导板标定基准数值pz替换计算如下:
66.pz
新
=α
×
pi (1-α)
×
pz
旧
67.上式中,pz
旧
是在先执行的侧导板标定基准数值,pz
新
是标定后将执行的侧导板标定基准数值,α的取值范围在0.1~0.8之间。
68.最后,执行模块c2执行现有的标定数据更新程序,自动完成后续的侧导板开口度标定过程,使得此后的侧导板开口度显示值基于新更新的标定基准数值。
69.再结合图1所示,本发明还提供了一种利用测宽仪对中厚板轧机侧导板自动标定的装置,包括:
70.在距离轧机或侧导板100较远位置安装有测量钢板宽度的测宽仪表wg、与测宽仪
表wg连接的协调联动模块c1、与协调联动模块c1连接的执行模块c2,辊道输送模块cg、以及侧导板对中操作模块cc;
71.执行模块c2用于驱动侧导板100的开口度标定;
72.协调联动模块c1、执行模块c2、测宽仪表wg、辊道输送模块cg、以及侧导板对中操作模块cc执行以下操作过程:
73.协调联动模块c1识别出生产周期的第一块钢板,指令辊道输送模块cg将第一块钢板移动至测宽仪表wg下方;
74.测宽仪表wg测得宽度测量数据wi;
75.协调联动模块c1指令辊道输送模块cg将第一块钢板移动至侧导板100位置;
76.协调联动模块c1指令侧导板对中操作模块cc进行侧导板100自动对中操作,得到侧导板开口度显示值ki;
77.将侧导板开口度显示值ki、宽度测量数据wi分别引入协调联动模块c1;
78.协调联动模块c1计算宽度测量数据wi与侧导板开口度显示值ki之间的偏差pi=wi-ki;
79.将偏差pi作为标定参考量,被引入执行模块c2,执行模块c2根据偏差pi,自动进行侧导板标定基准数值pz的替换,完成侧导板开口度自动标定过程。
80.侧导板标定基准数值pz替换计算如下:
81.pz
新
=α
×
pi (1-α)
×
pz
旧
82.上式中,pz
旧
是在先执行的侧导板标定基准数值,pz
新
是标定后将执行的侧导板标定基准数值,α的取值范围在0.1~0.8之间。
83.实施例
84.对于粗轧机、精轧机之间安装有测宽仪wg的中厚板产线。
85.当换辊后,在该生产周期的第一块钢板开始轧制后,过程控制l2计算机,识别出这是换辊后第一块钢板,于是通知协调联动模块c1,启动自动标定功能。
86.协调联动模块c1通知轧机打开辊缝,让钢板能顺利通过,不进行轧制,而且通过辊道输送模块cg控制轧机辊道转动,直到钢板移动到测宽仪wg下。
87.协调联动模块c1通知测宽仪wg开始测量,得到测量结果wi=2353mm。
88.然后,协调联动模块c1通过辊道输送模块cg控制辊道输送钢板到侧导板100位置。
89.然后,协调联动模块c1通知侧导板对中控制模块cc,开始自动对中操作,自动对中结束后,获得侧导板开口度显示值ki=2343mm。移动及对中操作合计需要时间约1~2分钟。
90.然后,协调联动模块c1计算宽度测量值wi与开口度显示值ki之间的偏差pi=wi-ki=2353-2343=10mm。
91.然后,pi作为标定参考量,被协调联动模块c1送到执行模块c2,得到新的侧导板标定基准数值pz的公式如下:
92.pz
新
=α
×
pi (1-α)
×
pz
旧
93.pz
旧
的数值为6mm,取α=0.5,则:
94.pz
新
=10
×
0.5 (1-0.5)
×
6=8mm。
95.最后,执行模块c2执行已有标定数据更新程序,用8mm替换原有6mm,自动完成后续的侧导板开口度标定过程,使得此后的侧导板开口度显示值ki基于新更新的标定基准数值
8mm。
96.综上所述,本发明方法适应面广,且使用方便,充分利用现有装备,不需要增加投资,适合在具有自动化控制的侧导板辊道上方安装有测宽仪表的中厚板轧机生产线上
97.本技术领域中的普通技术人员应当认识到,以上的实施例仅是用来说明本发明,而并非用作为对本发明的限定,只要在本发明的实质精神范围内,对以上所述实施例的变化、变型都将落在本发明的权利要求书范围内。
再多了解一些
本文用于企业家、创业者技术爱好者查询,结果仅供参考。