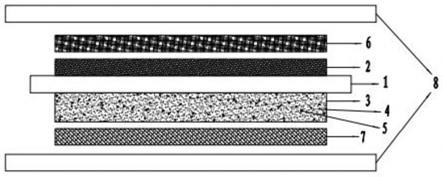
1.本发明涉及一种膜电极组件及制备方法,属于电化学技术领域。
背景技术:
2.氢能源是一种能量密度高并且无污染的理想清洁能源和能源载体,利用可再生能源发电和电解水制氢被认为是未来大规模能源存储的最佳解决方案之一。在已成熟或逐渐商业化的电解水制氢技术中,质子交换膜水电解(pemwe)相比碱性水电解(awe)不使用腐蚀性电解质,具有更加高效、安全、清洁、结构紧凑等优点,其对输入的快速动态响应特性、大的电流密度工作范围、高效率以及可在高压差下工作等特性非常适合与可再生能源联用,为氢储能提供了最理想的前景。但是pemwe成为商业上可行的大规模制氢解决方案仍然面临重大挑战,如:催化剂和质子交换膜的耐久性不足,铂族金属基催化剂的使用成本高,集电器的腐蚀以及兆瓦级功率的制氢设备国产化进程慢等。
3.pemwe使用固体聚合物电解质膜(或质子交换膜)作为离子导体,在阳极处将水氧化产生氧气,在阴极处产生氢。作为pemwe最关键的核心部件,膜电极组件(mea)是进行电化学反应和多相物质传输的场所,对pem电解制氢装置的能耗、寿命、成本至关重要。与质子交换膜燃料电池(pemfc)类似,用于pemwe的mea也具有类似三明治的结构,即包括阴/阳极催化层和质子交换膜的三层mea,也可拓展到包含阴/阳极气体扩散层和密封边框的五层和七层mea。高性能mea制备技术一直是电化学领域的核心技术,除要获得最佳的电解或发电性能外,还必须考虑质子交换膜、催化剂、气体扩散层等材料的耐久性以及气体交叉渗透等实际工程应用问题。因此,研究高活性、低成本、长寿命的mea及其制备工艺对于加快pemwe商业化进程具有十分重要的意义。
4.目前,用于pemwe和pemfc的膜电极制备工艺大多数是通过喷涂法或直接涂布法将催化剂直接涂覆在质子交换膜的两侧,制得催化剂涂层膜(catalyst coated membrane,ccm)膜电极。虽然采用上述方法可以提高质子交换膜和催化层之间的粘附性,但是制备膜电极时会因催化剂浆料中溶剂的使用而导致质子交换膜溶胀起皱,从而影响其表面平整性,且在另一面涂覆催化剂层时更加困难;同时,在大析气量场合及水气的持续剧烈冲刷下,尤其是在高压、高温操作条件下,上述方法难以保证催化层和质子交换膜的紧密贴合,导致催化层的剥离、脱落、流失等情况,从而导致膜电极内阻增加和性能下降。这些对提高膜电极性能、降低制造成本以及规模化生产极为不利。因此,在获得高的电解效率的同时,设法保证膜电极组件的长期运行寿命,降低膜电极组件成本,提高批量化制备效率对于pem电解制氢尤其是mw级大规模pem制氢的市场推广意义重大。
技术实现要素:
5.有鉴于此,本发明的目的在于提供一种膜电极组件及制备方法。
6.为实现上述目的,本发明的技术方案如下:
7.一种膜电极组件,所述组件包括质子交换膜以及位于质子交换膜两侧的阴极催化
剂层和阳极催化剂层;
8.所述阴极催化剂层由阴极第一活性组分和阴极第二活性组分组成,以所述阴极催化剂的总质量为100%计,所述阴极第一活性组分的质量分数为30~100%,所述阴极第二活性组分的质量分数为0~70%;所述阴极第一活性组分为pt、pd、ru、ni、fe、co、mo、ag、re和os中的一种以上;或所述阴极第一活性组分为pt、pd、ru、ni、fe、co、mo、ag、re和os中两种以上元素形成的合金;或所述阴极第一活性组分为负载有pt、pd、ru、ni、fe、co、mo、ag、re和os中的一种以上的负载型催化剂;所述阴极第二活性组分为pt、pd、ru、ir、ag、au、mn、co、ni、fe、mo、ag、re、os或cu的氧化物;或所述阴极第二活性组分为pt、pd、ru、ir、ag、au、mn、co、ni、fe、mo、ag、re、os和cu的两种元素以上的多氧化物;或所述阴极第二组分为负载有pt、pd、ru、ir、ag、au、mn、co、ni、fe、mo、ag、re、os和cu中两种以上的负载型催化剂,且当阴极第一活性组分为负载型催化剂时,阴极第一活性组分和阴极第二活性组分不同;
9.所述阳极催化剂层由阳极第一活性组分和阳极第二活性组分组成,以所述阳极催化剂的总质量为100%计,所述阳极第一活性组分的质量分数为30~90%,所述阳极第二活性组分的质量分数为10~70%;所述阳极第一活性组分为ir、rh、ru、pt、pd、ag或au的氧化物;或所述阳极第一活性组分为ir、rh、ru、pt、pd、ag和au的两种元素以上的多元氧化物;所述阳极第二活性组分为ir、ru、pd、ag、pt、au、ti、sn、co、ni、v、sr、zr、nb、mo、tc、sb、mn、hf、ta、w、ge和bi中的一种以上,或所述阳极第二活活性组分为ir、ru、pd、ag、pt、au、ti、sn、co、ni、v、sr、zr、nb、mo、tc、sb、mn、hf、ta、w、ge和bi中两种以上元素形成的合金,或所述阳极第二活活性组分为ir、ru、pd、ag、pt、au、ti、sn、co、ni、v、sr、zr、nb、mo、tc、sb、mn、hf、ta、w、ge和bi中两种以上元素且至少包含一种贱金属元素的多元氧化物。
10.优选的,所述负载型催化剂的载体为炭黑、碳纳米纤维、碳纳米管、碳纳米线、碳纳米棒、石墨烯、乙炔黑、科琴黑、tac、tic、tin、mof、聚苯胺、聚吡咯、聚噻吩或过渡金属氧化物。
11.优选的,所述阴极催化剂层中阴极第一活性组分和阴极第二活性组分均匀混合或第一活性组分和第二活性组分交替叠层分布。
12.优选的,所述阳极催化剂层中阳极第一活性组分和阳极第二活性组分均匀混合或第一活性组分和第二活性组分交替叠层分布。
13.优选的,所述质子交换膜为长支链全氟磺酸膜、短支链全氟磺酸膜、复合膜或增强型复合膜,厚度为5
‑
300微米。
14.优选的,所述组件还包括分别位于阴极催化剂层和阳极催化剂层外的阴极气体扩散层和阳极气体扩散层。所述阴极气体扩散层和阳极气体扩散层外设有密封边框。
15.一种膜电极组件的制备方法,所述方法步骤如下:
16.(1)质子交换膜的预处理:将质子交换膜依次用h2o2溶液、h2so4溶液在50~120℃温度下进行热处理,然后放入真空吸附加热平台上50~100℃下烘干0.5~2h,得到预溶胀的质子交换膜;
17.(2)催化剂浆料的制备:将所述阴极催化剂和阳极催化剂分别与粘结剂、分散剂、添加剂混合均匀,在150~1000w功率下超声震荡0.5~1h,形成均匀分散的阴极催化剂浆料和阳极催化剂浆料;
18.所述粘结剂为全氟磺酸树脂、聚四氟乙烯、聚偏氟乙烯、聚苯胺、环糊精串接聚苯
胺预聚体、聚苯胺聚氧化乙烯和聚苯胺/聚丙烯酸中的一种以上;
19.所述分散剂为电阻率大于等于10mω.cm的水、乙醇、乙二醇、异丙醇、正丙醇、正丁醇、n,n
‑
二甲基甲酰胺、氯仿和丙酮中的一种以上;
20.所述添加剂为聚四氟乙烯、聚乙烯吡咯烷酮、聚乙烯醇、聚苯胺、聚吡咯、聚噻吩、聚对苯二胺、聚邻苯二胺、聚间苯二胺、果胶、树胶、乙酸乙酯、甲基纤维素和羟甲基纤维素中的一种以上;
21.所述催化剂与粘结剂、分散剂、添加剂的质量比为1:0.1~0.8:1~200:0~1;
22.(3)催化剂涂层(ccm)膜电极的制备:将所述预溶胀的质子交换膜放入真空吸附加热平台上,加热台温度恒定在50~90℃,吸附压力恒定在0.2~0.8mpa;将所述阴极催化剂浆料和阳极催化剂浆料分别喷涂到所述预溶胀的质子交换膜两侧,烘干5~30min,得到ccm膜电极;其中,真空吸附加热平台与质子交换膜接触的部分附有多孔介质;
23.优选的,所述粘结剂为长侧链的nafion树脂或短侧链的aquivion树脂,将树脂加入醇溶液中,树脂含量为2.5wt%~20wt%。
24.优选的,喷涂时采用超声喷涂;超声喷涂时采用辐照光源进行辅助,所述辐照光源为红外线。
25.优选的,所述多孔介质为微孔陶瓷、碳纸、碳毡、钛毡、多孔钛板、钛网或多孔聚四氟乙烯板。
26.(4)膜电极组件的制备:在ccm膜电极的两侧分别放置聚四氟乙烯薄片或聚偏氟乙烯薄片,然后放置于两块金属板之间,进行三阶段热压:第一阶段在50~130℃、0.1~3mpa下压制1~60min;第二阶段在温度大于130℃小于等于150℃,且第二阶段与第一阶段温差为10~30℃,压力大于3mpa小于等于7mpa下,压制0.5~10min;第三阶段在温度大于130℃小于等于150℃,压力大于7mpa小于等于15mpa下,且第三阶段与第二阶段压差大于等于0.5mpa,压制0.1~5min;压制结束后冷却至室温,揭下聚四氟乙烯或聚偏氟乙烯薄片,得到一种膜电极组件。
27.有益效果
28.本发明所述膜电极组件中通过在催化剂层中添加多种活性组分,有助于降低活化过电势,大大提升催化析氢和析氧的活性;阴极第二活性组分和阳极第二活性组分可分别对阴极第一活性组分和阳极第一活性组分起到稀释作用,增加阴极第一活性组分和阳极第一活性组分的分散度和稳定性,防止阴极第一活性组分和阳极第一活性组分的迁移、团聚和流失,从而可大大减少贵金属的使用量;此外,可消除或减缓金属阳离子欠电位沉积和气体交叉
‑
渗透尤其是在高压、高温操作条件下对膜电极的损害,同时提高产品气的纯度,保障设备的安全性,并大大拓宽了质子交换膜的选用范围。
29.本发明所述方法中在喷涂前将质子交换膜进行了预处理,可除去原材料中的有机、无机污染物,同时使质子交换膜发生一定程度的预溶胀,使喷涂过程中可能发生的溶胀变形程度大大降低,并辅以多孔介质接触层的真空吸加热系统和红外辐照,防止传统真空加热板对质子膜的污染以及喷涂时催化层起皮、膜电极褶皱等情况,大大提高了喷涂效率,尤其适用于大尺寸膜电极的制备。
30.本发明所述方法将喷涂与三级热压有机结合,喷涂后首先通过在较低温度下预先施加较低压力的预压制过程使温度和压力均匀地传递到催化层和质子交换膜上,保证各处
的均匀一致性,通过压制过程使催化层与质子交换膜形成一体化结构,再通过加压压制进一步提高了催化层与质子交换膜的结合力,减小了膜电极的内阻,防止液体冲刷和强析气环境造成的催化层脱落、剥离等情况,从而延长膜电极的寿命。
31.本发明可精准制备所需尺寸、各种催化剂担载量的高活性一体化膜电极组件,系统操作简单、工艺灵活、浆料浪费率低、废品率低,显著提高了生产效率,降低了生产成本,适用于膜电极组件的批量化制备,在电解水、燃料电池等领域的产业化发展中展现出了良好的应用前景。
附图说明
32.图1为本发明所述膜电极组件的结构示意图;
33.图2为实施例和对比例所述电解池的性能测试图;
34.图3为实施例1
‑
2和对比例1的所述电解池中氧中氢含量曲线;
35.其中,1
‑
质子交换膜,2
‑
阴极催化剂层,3
‑
阳极催化剂层,4
‑
阳极第一活性组分,5
‑
阳极第二活性组分,6
‑
阴极气体扩散层,7
‑
阳极气体扩散层,8
‑
密封边框。
具体实施方式
36.下面结合具体实施例对本发明作进一步详细的说明。
37.如图1所示,一种膜电极组件,所述组件包括质子交换膜1以及位于质子交换膜两侧的阴极催化剂层2和阳极催化剂层3;
38.所述阴极催化剂层2由阴极第一活性组分和阴极第二活性组分组成,以所述阴极催化剂的总质量为100%计,所述阴极第一活性组分的质量分数为30~100%,所述阴极第二活性组分的质量分数为0~70%;所述阴极第一活性组分为pt、pd、ru、ni、fe、co、mo、ag、re和os中的一种以上;或所述阴极第一活性组分为pt、pd、ru、ni、fe、co、mo、ag、re和os中两种以上元素形成的合金;或所述阴极第一活性组分为负载有pt、pd、ru、ni、fe、co、mo、ag、re和os中的一种以上的负载型催化剂;所述阴极第二活性组分为pt、pd、ru、ir、ag、au、mn、co、ni、fe、mo、ag、re、os或cu的氧化物;或所述阴极第二活性组分为pt、pd、ru、ir、ag、au、mn、co、ni、fe、mo、ag、re、os和cu的两种元素以上的多氧化物;或所述阴极第二组分为负载有pt、pd、ru、ir、ag、au、mn、co、ni、fe、mo、ag、re、os和cu中两种以上的负载型催化剂,且当阴极第一活性组分为负载型催化剂时,阴极第一活性组分和阴极第二活性组分不同;
39.所述阳极催化剂层3由阳极第一活性组分4和阳极第二活性组分5组成,以所述阳极催化剂的总质量为100%计,所述阳极第一活性组分4的质量分数为30~90%,所述阳极第二活性组分5的质量分数为10~70%;所述阳极第一活性组分4为ir、rh、ru、pt、pd、ag或au的氧化物;或所述阳极第一活性组分4为ir、rh、ru、pt、pd、ag和au的两种元素以上的多元氧化物;所述阳极第二活活性组分5为ir、ru、pd、ag、pt、au、ti、sn、co、ni、v、sr、zr、nb、mo、tc、sb、mn、hf、ta、w、ge和bi中的一种以上,或所述阳极第二活活性组分5为ir、ru、pd、ag、pt、au、ti、sn、co、ni、v、sr、zr、nb、mo、tc、sb、mn、hf、ta、w、ge和bi中两种以上元素形成的合金,或所述阳极第二活活性组分5为ir、ru、pd、ag、pt、au、ti、sn、co、ni、v、sr、zr、nb、mo、tc、sb、mn、hf、ta、w、ge和bi中两种以上元素且至少包含一种贱金属元素的多元氧化物。
40.所述负载型催化剂的载体为炭黑、碳纳米纤维、碳纳米管、碳纳米线、碳纳米棒、石
墨烯、乙炔黑、科琴黑、tac、tic、tin、mof、聚苯胺、聚吡咯、聚噻吩或过渡金属氧化物。
41.所述阴极催化剂层2中阴极第一活性组分和阴极第二活性组分均匀混合或第一活性组分和第二活性组分交替叠层分布。
42.所述阳极催化剂层3中阳极第一活性组分4和阳极第二活性组分5均匀混合或阳极第一活性组分4和阳极第二活性组分5交替叠层分布。
43.所述质子交换膜1为长支链全氟磺酸膜、短支链全氟磺酸膜、复合膜或增强型复合膜,厚度为5
‑
300微米。
44.所述组件还包括分别位于阴极催化剂层2和阳极催化剂层3外的阴极气体扩散层6和阳极气体扩散层7,所述阴极气体扩散层6和阳极气体扩散层7外设有密封边框8。
45.实施例1
46.将商品化的nafion(全氟磺酸)117膜裁剪成所需尺寸,依次浸入5wt%h2o2溶液和0.5mol/lh2so4溶液中,在80℃下分别处理0.5h,除去膜表面的有机和无机杂质,并促使膜充分溶胀和质子化,之后将膜放入洁净的真空吸附加热平台上80℃下烘干0.5h,蒸出部分水分,得到预溶胀的nafion膜;
47.以pt/c(pt:20wt%)作为阴极催化剂,加入5wt%nafion树脂溶液作为粘结剂,去离子水和乙醇作为分散剂(去离子水和乙醇质量比为1:1)混合均匀,其中阴极催化剂与nafion树脂、分散剂的质量比例为1:0.3:20,将混合后的浆料在300w功率下超声0.5h,形成均匀分散的阴极催化剂浆料;
48.以irox作为阳极第一活性组分,并添加ruir合金(原子比ru:ir=8:2)作为阳极第二活性组分,阳极第一活性组分和阳极第二活性组分的质量比为6:4,加入5wt%nafion树脂溶液作为粘结剂,去离子水和乙醇作为分散剂(去离子水和乙醇质量比为1:1)混合均匀,其中阳极催化剂与nafion树脂、分散剂的质量比例为1:0.1:15,将混合后的浆料在300w功率下超声0.5h,形成均匀分散的阳极催化剂浆料。
49.将所述预溶胀的nafion膜吸附到50℃真空吸附加热台上,在红外辐照辅助下,将阴极和阳极催化剂浆料分别超声喷涂到nafion膜两侧,喷涂流量均为8ml/min,加热烘干5min后,得到ccm膜电极。阴极催化剂层的贵金属载量为0.2mg/cm2,阳极催化剂层的贵金属载量为1.5mg/cm2。其中,真空吸附加热平台与质子交换膜接触的部分附有多孔介质,所述多孔介质为多孔聚四氟乙烯板;
50.将所述ccm膜电极用两片聚四氟乙烯薄片夹住,并放置于两块金属板夹具之间,在110℃、1mpa压力下预压制5min,然后在140℃、3.5mpa压力下压制10min,最后在145℃、10mpa压力下加压压制3min,冷却至室温,揭下聚四氟乙烯薄片,得到一种膜电极组件。
51.在所述膜电极组件两侧分别加装气体扩散层(本实施例中气体扩散层采用多孔钛板)和密封边框,然后加装流场板和极板,用不锈钢夹具组装成电解池,并在50℃下进行极化曲线测试,结果如图2所示,电解池性能达到1.75v@1a/cm2,2.05v@2a/cm2。
52.采用氢分析仪测试所述电解池氧气侧氢气含量,结果如图3所示,氧气中氢气体积百分比在0.2%上下波动,且随时间推移未有升高迹象。
53.实施例2
54.将商品化的nafion117膜裁剪成所需尺寸,依次浸入5wt%h2o2溶液和0.5mol/l h2so4溶液中,在80℃下分别处理0.5h,除去膜表面的有机和无机杂质,并促使膜充分溶胀和
质子化,之后将膜放入洁净的真空吸附加热平台上80℃下烘干0.5h,蒸出部分水分,得到预溶胀的nafion膜;
55.将pt/c(pt:20wt%)作为阴极催化剂,加入5wt%nafion树脂溶液作为粘结剂,去离子水和乙醇作为分散剂(去离子水和乙醇质量比为1:1)混合均匀,其中阴极催化剂与nafion树脂、分散剂的质量比例为1:0.3:20,将混合后的浆料在300w功率下超声0.5h,形成均匀分散的阴极催化剂浆料;
56.将irox作为阳极第一活性组分,加入5wt%nafion树脂溶液作为粘结剂,去离子水和乙醇作为分散剂(去离子水和乙醇质量比为1:1)混合均匀,其中阳极第一活性组分与nafion树脂、分散剂的质量比例为1:0.1:1015,将混合后的浆料在300w功率下超声0.5h,形成均匀分散的阳极第一活性组分浆料;将ruir合金(原子比ru:ir=8:2)作为阳极第二活性组分,加入5wt%nafion树脂溶液作为粘结剂,去离子水和乙醇作为分散剂(去离子水和乙醇质量比为1:1),其中阳极第二活性组分与nafion树脂、分散剂的质量比例为1:0.1:15,将混合后的浆料在300w功率下超声0.5h,形成均匀分散的阳极第二活性组分浆料,阳极第一活性组分和阳极第二活性组分的质量比为6:4。
57.将所述预溶胀的nafion膜吸附到6050℃真空吸附加热台上,在红外辐照辅助下,将阴极催化剂浆料超声喷涂到nafion膜一侧,之后将第一阳极催化剂浆料和第二阳极催化剂浆料依次喷涂到nafion膜的另一侧,喷涂流量均为8ml/min,加热烘干5min后,得到ccm膜电极。阴极催化层的贵金属载量为0.2mg/cm2,阳极催化层的贵金属载量为1.5mg/cm2。其中,真空吸附加热平台与质子交换膜接触的部分附有多孔扩散层介质,所述多孔扩散层介质为多孔聚四氟乙烯板;
58.将所述ccm膜电极用两片聚四氟乙烯薄片夹住,并放置于两块金属板夹具之间,在110℃、1mpa压力下预压制5min,然后在140℃、3.5mpa压力下压制10min,最后在145℃、10mpa压力下加压压制3min,冷却至室温,揭下聚四氟乙烯薄片,得到一种膜电极组件。
59.在所述膜电极组件两侧分别加装气体扩散层(本实施例中气体扩散层采用多孔钛板)和密封边框,然后加装流场板和极板,用不锈钢夹具组装成电解池,并在50℃下进行极化曲线测试,结果如图2所示,电解池性能达到1.79v@1a/cm2,2.11v@2a/cm2。
60.采用氢分析仪测试所述电解池氧气侧氢气含量,结果如图3所示。氧气中氢气体积百分比在0.4%上下波动,且随时间推移未有升高迹象。
61.实施例3:
62.将商品化的nafion117膜裁剪成所需尺寸,依次浸入5wt%h2o2溶液和0.5mol/l h2so4溶液中,在80℃下分别处理0.5h,除去膜表面的有机和无机杂质,并促使膜充分溶胀和质子化,之后将膜放入洁净的真空吸附加热平台上80℃下烘干0.5h,蒸出部分水分,得到预溶胀的nafion膜;
63.将pt/c(pt:20wt%)作为阴极第一活性组分,并添加ptru/c(ptru:20wt%,原子比pt:ru=1:1)作为阴极第二活性组分,阴极第一活性组分和阴极第二活性组分的质量比为9:1,加入5wt%nafion树脂溶液作为粘结剂,去离子水和乙醇作为分散剂(去离子水和乙醇质量比为1:1)混合均匀,其中阴极催化剂与nafion树脂、分散剂的质量比例为1:0.1:20,将混合后的浆料在300w功率下超声0.5h,形成均匀分散的阴极催化剂浆料;
64.以irox作为阳极第一活性组分,并添加ruir合金(原子比ru:ir=8:2)作为阳极第
二活性组分,阳极第一活性组分和阳极第二活性组分的质量比为6:4,加入5wt%nafion树脂溶液作为粘结剂,去离子水和乙醇作为分散剂(去离子水和乙醇质量比为1:1)混合均匀,其中阳极催化剂与nafion树脂、分散剂的质量比例为1:0.1:15,将混合后的浆料在300w功率下超声0.5h,形成均匀分散的阳极催化剂浆料。
65.将所述预溶胀的nafion膜吸附到50℃真空吸附加热台上,在红外辐照辅助下,将阴极和阳极催化剂浆料分别超声喷涂到nafion膜两侧,喷涂流量均为8ml/min,加热烘干5min后,得到ccm膜电极。阴极催化剂层的贵金属载量为0.2mg/cm2,阳极催化剂层的贵金属载量为1.5mg/cm2。其中,真空吸附加热平台与质子交换膜接触的部分附有多孔介质,所述多孔介质为多孔聚四氟乙烯板。
66.将所述ccm膜电极用两片聚四氟乙烯薄片夹住,并放置于两块金属板夹具之间,在110℃、1mpa压力下预压制5min,然后在140℃、3.5mpa压力下压制10min,最后在145℃、10mpa压力下加压压制3min,冷却至室温,揭下聚四氟乙烯薄片,得到一种膜电极组件。
67.在所述膜电极组件两侧分别加装气体扩散层(本实施例中气体扩散层采用多孔钛板)和密封边框,然后加装流场板和极板,用不锈钢夹具组装成电解池,并在50℃下进行极化曲线测试,结果如图2所示,电解池性能达到1.72v@1a/cm2,1.99v@2a/cm2。
68.实施例4:
69.将商品化的nafion117膜裁剪成所需尺寸,依次浸入5wt%h2o2溶液和0.5mol/l h2so4溶液中,在80℃下分别处理0.5h,除去膜表面的有机和无机杂质,并促使膜充分溶胀和质子化,之后将膜放入洁净的真空吸附加热平台上80℃下烘干0.5h,蒸出部分水分,得到预溶胀的nafion膜;
70.将pt/c(pt:20wt%)作为阴极催化剂,加入5wt%nafion树脂溶液作为粘结剂,去离子水和乙醇作为分散剂(去离子水和乙醇质量比为1:1)混合均匀,其中阴极催化剂与nafion树脂、分散剂的质量比例为1:0.3:20,将混合后的浆料在300w功率下超声0.5h,形成均匀分散的阴极催化剂浆料;
71.将irox作为阳极第一活性组分,并添加sriro3作为阳极第二活性组分,阳极第一活性组分和阳极第二活性组分的质量比为3:7,加入5wt%nafion树脂溶液作为粘结剂,去离子水和乙醇作为分散剂(去离子水和乙醇质量比为1:1)混合均匀,其中阳极催化剂与nafion树脂、分散剂的质量比例为1:0.1:15,将混合后的浆料在300w功率下超声0.5h,形成均匀分散的阳极催化剂浆料。
72.将所述预溶胀的nafion膜吸附到60℃真空吸附加热台上,在红外辐照辅助下,将阴极和阳极催化剂浆料分别超声喷涂到nafion膜两侧,喷涂流量均为8ml/min,加热烘干5min后,得到ccm膜电极。阴极催化层的贵金属载量为0.2mg/cm2,阳极催化层的贵金属载量为1.5mg/cm2。其中,真空吸附加热平台与质子交换膜接触的部分附有多孔介质,所述多孔介质为多孔聚四氟乙烯板。
73.将所述ccm膜电极用两片聚四氟乙烯薄片夹住,并放置于两块金属板夹具之间,在110℃、1mpa压力下预压制5min,然后在140℃、3.5mpa压力下压制10min,最后在145℃、10mpa压力下加压压制3min,冷却至室温,揭下聚四氟乙烯薄片,得到一种膜电极组件。
74.在所述膜电极组件两侧分别加装气体扩散层(本实施例中气体扩散层采用多孔钛板)和密封边框,然后加装流场板和极板,用不锈钢夹具组装成电解池,并在50℃下进行极
化曲线测试,结果如图2所示,电解池性能达到1.72v@1a/cm2,1.95v@2a/cm2。
75.对比例1
76.本对比例中阳极催化剂为irox,其余同实施例1。本对比例制备的膜电极组件电解池性能和气体交叉渗透结果分别如图2和图3所示。从图2可以看出,在相同电流密度下其电解电压明显高于实施例1
‑
4;从图3可以看出,其氧气中氢气体积百分比明显高于实施例1和实施例2,即气体交叉渗透风险较高。采用氢分析仪测试实施例3和实施例4所述电解池氧气侧氢气含量,结果表明,实施例3和实施例4所述电解池中氧气中氢气体积百分比与实施例1类似,氧气中氢气体积百分比在0.2%上下波动,随时间推移未有升高迹象,且明显低于对比例1。
77.对比例2
78.本对比例不进行三级热压,其余同实施例1。从图2可以看出,在相同电流密度下其电解电压明显高于实施例1
‑
4。
79.综上所述,发明包括但不限于以上实施例,凡是在本发明的精神和原则之下进行的任何等同替换或局部改进,都将视为在本发明的保护范围之内。
再多了解一些
本文用于企业家、创业者技术爱好者查询,结果仅供参考。