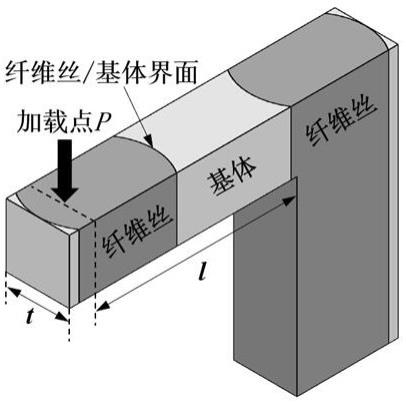
1.本发明属于力学试验技术领域,涉及一种界面力学性能原位测试方法,尤其是一种纤维增强复合材料微纳尺度界面力学性能原位测试方法。
背景技术:
2.纤维增强复合材料是由增强纤维材料,如玻璃纤维、碳纤维、芳纶纤维等,与基体材料经过缠绕、模压或拉挤等成型工艺而形成的复合材料。纤维增强复合材料具有如下特点:(1)比强度高,比模量大;(2)材料性能具有可设计性;(3)抗腐蚀性和耐久性能好;(4)热膨胀系数与混凝土的相近。这些特点使得纤维增强复合材料能满足现代结构向大跨、高耸、重载、轻质高强以及在恶劣条件下工作发展的需要,因此该种材料已被广泛应用于许多领域,例如航空航天领域、民用建筑、风力涡轮机、民用建筑和人体假肢等。
3.界面是纤维增强复合材料的重要组成部分,其性能直接影响复合材料纤维与基体之间的应力传递与分布,从而影响复合材料的力学性能;界面特性还会影响到复合材料使用过程中的内部损伤积累和裂纹传播过程,进而影响复合材料的使用可靠性,因此对界面性能的合理表征是准确预测复合材料性能的必要前提。传统的界面强度试验主要包括:1965年,kelly等设计的纤维断裂试验;1966年,broutman等设计的纤维拔出试验;1980年,mandell等设计的压头顶出试验;1987年,miller等设计的微滴脱粘试验,这四种试验方法均为对界面的剪切强度进行测定。试验的原理是:以一个剪力作用于单根纤维和基体的界面上,当界面发生脱粘时,界面剪切强度即可用极限剪切载荷和界面脱粘面积通过应力分析计算得到。这些试验方法的差异在于所用试件的外形和加载方式的不同,以及试验过程中界面的剪应力分布存在差异。然而,2006年rosso等指出,传统界面剪切试验虽然可以直接测量界面剪切强度,但其所测强度几乎不能与任何包含高体积分数的真实层合复合材料所处的应力状态相关。宏观力学测试可以间接评估界面性能,但是进行宏观力学测试所需的厚板是难以制造的。rosso认为横向纤维束测试可以作为连接微观力学和宏观力学的纽带。2009年,deng等进行了横向纤维束拉伸和v口剪切试验,试验结果显示出这两种试验对于界面性能具有良好的敏感性。2013年,zhang等使用横向纤维拉伸试验研究了纳米二氧化硅颗粒对于复合材料界面性能的影响,试验结果显示纳米粒子对界面影响不大。2014年,qi等提出了基于通用单元法的多尺度破坏分析,模拟了横向纤维拉伸的渐进破坏过程,得到了横向纤维的法向界面强度。2016年,qi等在横向纤维拉伸试验的基础上开发了45度纤维束拉伸试验,用以评估界面的剪切强度,试验发现,横向纤维拉伸与45度横向纤维拉伸试验试件表面的断裂特征是不同的,这可能是由于载荷条件不同导致的。同年,qi等研究了纤维体积分数对横向纤维拉伸测试的影响,试验和有限元结果均表明,横向纤维拉伸强度随纤维体积分数的减少而增加。
4.然而,以上均是对纤维增强复合材料的宏观界面性能测试,尚未发现进行微纳尺度的纤维增强复合材料界面力学性能原位测试方法。
技术实现要素:
5.为了测试纤维增强复合材料的微纳尺度界面力学性能,本发明提供了一种纤维增强复合材料微纳尺度界面力学性能原位测试方法。该方法可以实现对纤维增强复合材料微纳米尺度下的界面力学性能原位测试,可以为纤维增强复合材料在微纳米尺度下的断裂力学试验设计和强度检测提供指导依据。
6.本发明的目的是通过以下技术方案实现的:一种纤维增强复合材料微纳尺度界面力学性能原位测试方法,包括如下步骤:步骤一、含界面微纳米纤维增强复合材料悬臂梁试验件的制备含界面微纳米纤维增强复合材料悬臂梁试验件采用聚焦离子束技术从复合材料薄块中切割而成,具体步骤如下:(1)使用带有高目数砂纸的抛光机对复合材料薄块上垂直于纤维束的表面进行打磨,使其表面光滑;(2)采用聚焦离子束,从纤维增强复合材料薄块上切出一个微米块;(3)利用钨气相沉积技术,在聚焦离子束操作系统中通过一个微米探针机械手将切好的微米块取出;(4)通过钨气相沉积技术,将取出来的微米块粘在金属线的顶端;(5)采用聚焦离子束在微米块上切出微纳米悬臂梁的部分,悬臂梁应至少包含1个纤维丝/基体界面,且界面和基体须靠近悬臂梁根部位置;步骤二、含界面微纳米纤维增强复合材料悬臂梁的原位加载与观测(1)利用微纳米悬臂梁的原位加载与观测系统对含界面微纳米纤维增强复合材料悬臂梁进行原位加载,其中:所述微纳米悬臂梁的原位加载与观测系统集成在扫描电子显微镜的样品架上,断裂试验在扫描电子显微镜内完成,且金刚石加载头须置于远离界面的悬臂梁远端纤维丝上表面处;所述微纳米悬臂梁的原位加载与观测系统包含一个可以三轴平移的试样台和一个带有载荷传感器的金刚石加载头,通过电脑端可以观察到整个原位加载的过程;(2)在原位加载过程中,弯曲载荷通过金刚石加载头施加在远离纤维丝/基体界面的悬臂梁远端纤维丝上表面处,试验台由压电驱动器驱动进行平移,借助扫描电子显微镜内的电子束探头实现对整个断裂过程的原位观测,进行重复试验,最终得到含界面微纳米纤维增强复合材料悬臂梁的原位加载试验结果曲线;步骤三、含界面微纳米纤维增强复合材料悬臂梁界面裂纹启裂行为分析结合原位观测试验和有限元方法进一步分析含界面微纳米纤维增强复合材料悬臂梁试验件界面端裂纹启裂时的应力分布情况,并采用内聚力模型确定纤维丝/基体界面力学参数,具体步骤如下:(1)建立微纳米悬臂梁试验件的二维有限元模型,所述二维有限元模型采用平面应变状态;(2)对界面端附近的有限元网格进行细化处理;(3)针对二维有限元模型根据试验件的真实边界条件,对悬臂梁的基部远端施加完全固定约束;
(4)采用内聚力模型表征纤维增强复合材料中纤维丝/基体界面的开裂行为,通过将模拟载荷
‑
位移曲线与试验载荷
‑
位移曲线进行对比得到合理的特征长度值和内聚力强度值,最后得到纤维丝/基体界面的断裂能g
c
;步骤四、含界面微纳米纤维增强复合材料试验件尺寸效应探究步骤一、步骤二、步骤三仅是针对于特定尺寸的试验件进行的试验件制备及原位加载与观测的说明,在此基础上通过改变试验件的尺寸重复步骤一~步骤三可以进行其他尺寸试验件的探究试验,以探究含界面微纳米纤维增强复合材料试验件的尺寸大小对试验结果的影响。
7.相比于现有技术,本发明具有如下优点:1、本发明提供了一种在扫描电子显微镜环境下通过微纳米悬臂梁弯曲原位加载观测试验测得纤维增强复合材料界面力学性能的测试方法,对研究纤维增强复合材料的界面力学问题具有重要意义;2、本发明提供了一种含界面微纳米纤维增强复合材料悬臂梁试验件的制备方法,解决了纤维增强复合材料微纳米悬臂梁试验件制备困难的问题;3、本发明为纤维增强复合材料的微纳尺度界面力学性能测试提供了可信的试验手段,在此基础上可以进行不同尺寸试验件的探究试验,以探究含界面微纳米纤维增强复合材料试验件的尺寸大小对试验结果的影响。
附图说明
8.图1是含界面微纳米纤维增强复合材料悬臂梁试验件示意图;图2是含界面微纳米纤维增强复合材料悬臂梁试验件聚焦离子束制备流程图;图3是含界面微纳米复合材料悬臂梁试验件的扫描电子显微镜照片;图4是含界面微纳米纤维增强复合材料悬臂梁试验件的原位加载与观测系统;图5是含界面微纳米纤维增强复合材料悬臂梁的原位加载试验结果曲线;图6是含界面微纳米纤维增强复合材料悬臂梁试验件的二维有限元模型。
具体实施方式
9.下面结合附图对本发明的技术方案作进一步的说明,但并不局限于此,凡是对本发明技术方案进行修改或者等同替换,而不脱离本发明技术方案的精神和范围,均应涵盖在本发明的保护范围中。
10.本发明提供了一种纤维增强复合材料微纳尺度界面力学性能原位测试方法,所述方法借助聚焦离子束技术制备了一系列不同尺寸(5 μm、3 μm、1 μm、500 nm、300 nm、100 nm等)的微纳米悬臂梁试件,以微纳米尺度下含界面的纤维增强复合材料为研究对象,在扫描电子显微镜环境下开展了微纳米悬臂梁弯曲原位加载观测试验,原位观测到微纳米复合材料界面启裂、扩展的整个过程,从而测得纤维增强复合材料的界面力学参数。通过进行不同尺寸试验件的原位加载试验,可以进一步探究试验件尺寸对实验结果的影响。具体包括如下步骤:步骤一、含界面微纳米纤维增强复合材料悬臂梁试验件的制备图1中的含界面微纳米纤维增强复合材料悬臂梁试验件采用聚焦离子束技术从复
合材料薄块中切割而成,如图2所示,具体的制作步骤如下:(1)使用带有高目数(4000目)砂纸的抛光机对复合材料薄块上垂直于纤维束的表面进行打磨,使其表面光滑;(2)采用聚焦离子束,从纤维增强复合材料薄块上切出一个大小约为10 μm的微米块,如图2(a)所示;(3)利用钨气相沉积技术,在聚焦离子束操作系统中通过一个微米探针机械手将切好的微米块取出,如图2(b)所示;(4)通过钨气相沉积技术,将取出来的微米块粘在一个直径约为0.25 mm的金属线的顶端,如图2(c)所示;(5)采用聚焦离子束在微米块上切出微纳米悬臂梁的部分,悬臂梁包含2个纤维丝/基体界面,基体位于2根纤维丝中间,且界面靠近悬臂梁根部位置,如图2(d)所示。
11.整个制备过程中,ga离子束的能量设置为40 kv,离子束电流根据切割的精度要求在1.13 na ~ 0.01 na之间调整。
12.图3给出了最终制备而成的含界面微纳米复合材料悬臂梁试验件的扫描电子显微镜照片。如图3所示,微纳米悬臂梁试件的界面端(也就是发生裂纹启裂的位置)非常光滑,并没有在聚焦离子束处理过程中引入缺陷或损伤。
13.步骤二、含界面微纳米纤维增强复合材料悬臂梁的原位加载与观测为了实现对界面端启裂过程的原位观测,本发明提供了一种适用于微纳米悬臂梁的原位加载与观测系统,原位加载试验是在扫描电子显微镜内完成。微纳米悬臂梁的原位加载与观测系统如图4所示,加载装置包含了一个可以三轴平移的试样平台和一个带有微机电系统(mems)载荷传感器的金刚石加载头。为了实现对整个试验过程得原位观测,该加载装置被集成到扫描电子显微镜的样品架上。由于纤维丝比基体硬度大,因此在加载过程中弯曲载荷p通过金刚石加载头施加在远离纤维丝/基体界面的悬臂梁远端纤维丝上表面处。试验台由一个压电驱动器以1 nm/s的速度平移。加载系统的精度为放大倍数的
±
5%。试验过程中,借助扫描电子显微镜内的电子束探头实现对整个断裂过程得原位观测,进行3~5组重复试验,最终得到的含界面微纳米纤维增强复合材料悬臂梁的原位加载试验结果曲线,如图5所示。
14.步骤三、含界面微纳米纤维增强复合材料悬臂梁界面裂纹启裂行为分析通过步骤二中的微纳米尺度原位观测试验能直接得到的试验结果非常有限,比如施加在微纳米悬臂梁试验件远端的载荷信息p以及试验件的变形信息d。鉴于此本发明提出了一种含界面微纳米纤维增强复合材料悬臂梁界面裂纹启裂行为分析方法,此方法结合原位观测试验和有限元方法(finite element method,fem)进一步分析含界面微纳米纤维增强复合材料悬臂梁试验件界面端裂纹启裂时刻p
c
的应力分布情况。如图6所示,建立了微纳米悬臂梁试验件的二维有限元模型。考虑到界面端附近会出现应力集中,对界面端附近的有限元网格进行了细化处理。由于悬臂梁试验件的厚度方向的尺寸足够大,有限元模型采用了平面应变状态。根据试验件的真实边界条件,有限元模型的右端和底端施加完全固定约束。采用指数形式的内聚力模型表征纤维增强复合材料中纤维丝/基体界面的开裂行为,为了得到合理的特征长度值,首先初步预设纤维丝/基体界面的内聚力强度初始值,并尝试多个不同的值,通过对比模拟载荷
‑
位移曲线和试验载荷
‑
位移曲线的斜率使其误差在5%以
内,从而得到最佳的值作为内聚力模型的特征长度参数。然后尝试若干不同的内聚力强度值,通过对比模拟载荷
‑
位移曲线和试验
‑
载荷位移曲线的峰值点使其误差在5%以内,从而确定最佳的值作为内聚力模型的内聚力强度值。最后通过公式(其中,e = 2.71828)得到纤维丝/基体界面的断裂能g
c
。
15.步骤四、含界面微纳米纤维增强复合材料试验件尺寸效应探究需要说明的是,本发明还提供了一种含界面微纳米纤维增强复合材料试验件尺寸效应探究方法。上述方法(步骤一~步骤三)仅是针对于特定尺寸(5 μm)的试验件进行的试验件制备及原位加载与观测的说明。由于纤维丝的直径约为6 μm,因此在进行含界面微纳米纤维增强复合材料试验件尺寸效应探究时,悬臂梁横截面的边长不能超过5 μm。因此在此基础上可以进行其他尺寸(5 μm、3 μm、1 μm、500 nm、300 nm、100 nm等)试验件的探究试验,通过改变试验件的尺寸重复以上步骤1~步骤3,以探究含界面微纳米纤维增强复合材料试验件的尺寸大小对试验结果的影响。
再多了解一些
本文用于企业家、创业者技术爱好者查询,结果仅供参考。