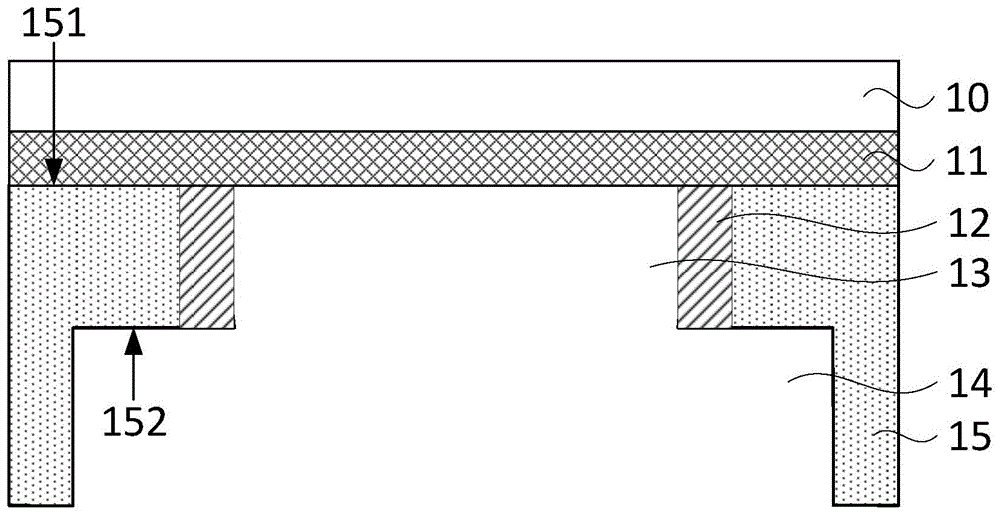
本发明实施例涉及半导体制造技术领域,尤其涉及一种半导体结构及其制作方法。
背景技术:
在半导体工艺中,有些情况需要用到双面加工工艺,例如需要在硅片的正面和反面都制作图形,特别是一些mems器件,比如,在压力传感器、热电堆温度传感器等mems器件的背面需要做深刻蚀,使得最终器件是一层薄膜器件。其中,双面加工工艺需要用到专门的设备双面光刻机,深刻蚀可以使用干法刻蚀或湿法腐蚀等。
双面光刻机采用接近式或接触式曝光,即光学系统将图形以1:1的比例投射到硅片上,因此使用到的掩膜版与硅片的尺寸相同,并且掩膜版上的图形的尺寸和位置也必须和实际情况一致,这样就使得传统的双面光刻工艺中基本上都采用人工方式来放置和对准掩膜版。然而人工方式放置掩膜版普遍存在对位不准确的情况,包括中心偏离,即曝光图形的中心会偏离晶圆的中心,最大偏离会达到十几毫米;还包括旋转偏差,即曝光图形相对晶圆的平边会发生旋转,最大会达到几十度。虽然操作熟练的工程师可以在较大程度上克服这个问题,但对准精度仍然受到操作熟练度的影响。
当硅片正反面图形形成一定的偏差后,深刻蚀后的图形会继续保持这种偏差,甚至放大这种偏差,从而对器件的性能产生不利影响。
技术实现要素:
本发明提供一种半导体结构及其制作方法,以提高深刻蚀器件对准精度。
第一方面,本发明实施例提供了一种半导体结构,包括器件层、隔绝层、腐蚀阻挡层、自限制腐蚀腔、第一腐蚀腔和衬底;
所述器件层位于所述衬底的第一侧,所述自限制腐蚀腔位于所述衬底的第二侧,所述隔绝层和所述腐蚀阻挡层位于所述自限制腐蚀腔靠近所述器件层的一侧,且所述自限制腐蚀腔位于所述隔绝层和所述腐蚀阻挡层所限定的空间内;
所述第一腐蚀腔位于所述自限制腐蚀腔远离所述器件层的一侧,且所述第一腐蚀腔与所述自限制腐蚀腔连通。
可选的,所述隔绝层位于所述器件层靠近所述衬底的一侧,所述腐蚀阻挡层位于所述隔绝层远离所述器件层的一侧。
可选的,所述衬底包括第一衬底分部和第二衬底分部,所述第二衬底分部位于所述第一衬底分部远离所述器件层的一侧;
所述隔绝层位于所述第一衬底分部和所述第二衬底分部之间;
所述腐蚀阻挡层位于所述器件层靠近所述第一腐蚀腔的一侧,且所述腐蚀阻挡层贯穿所述第一衬底分部、所述隔绝层以及至少部分所述第二衬底分部。
可选的,所述自限制腐蚀腔在所述器件层所在平面的垂直投影位于所述第一腐蚀腔在所述器件层所在平面的垂直投影内,且所述第一腐蚀腔在所述器件层所在平面的垂直投影的面积大于所述自限制腐蚀腔在所述器件层所在平面的垂直投影的面积。
可选的,所述隔绝层的材料包括氧化硅或氮化硅,所述腐蚀阻挡层的材料包括氧化硅。
第二方面,本发明实施例还提供了一种半导体结构的制备方法,用于制备第一方面所述的任一半导体结构,该方法包括:
提供一衬底;
在所述衬底上形成隔绝层和腐蚀阻挡层;
在所述衬底的第一侧制备器件层;
在所述衬底的第二侧制备第一腐蚀腔;
在所述衬底的第二侧制备自限制腐蚀腔,其中,所述隔绝层和所述腐蚀阻挡层位于所述自限制腐蚀腔靠近所述器件层的一侧,所述自限制腐蚀腔位于所述隔绝层和所述腐蚀阻挡层所限定的空间内,所述第一腐蚀腔位于所述自限制腐蚀腔远离所述器件层的一侧,且所述第一腐蚀腔与所述自限制腐蚀腔连通。
可选的,所述衬底为单层硅衬底;
在所述衬底上形成隔绝层和腐蚀阻挡层,包括:
在所述衬底的第一侧刻蚀第一空腔,在所述第一空腔内填充氧化硅或氮化硅,形成腐蚀阻挡层;
在所述衬底的第一侧以及所述腐蚀阻挡层远离所述衬底的一侧制备所述隔绝层。
可选的,所述衬底为soi硅片,所述soi硅片包括第一衬底分部、所述隔绝层和第二衬底分部,所述隔绝层位于所述第一衬底分部和所述第二衬底分部之间;
在所述衬底上形成隔绝层和腐蚀阻挡层,包括:
在所述衬底的第一侧刻蚀第二空腔,在所述第二空腔内填充氧化硅或氮化硅,形成腐蚀阻挡层,其中,所述腐蚀阻挡层贯穿所述第一衬底分部、所述隔绝层以及至少部分所述第二衬底分部。
可选的,通过各向异性湿法腐蚀工艺或深硅干刻法刻蚀工艺在所述衬底的第二侧制备第一腐蚀腔;
通过各向同性湿法腐蚀工艺或各向异性湿法腐蚀工艺在所述衬底的第二侧制备自限制腐蚀腔。
可选的,通过各向异性湿法腐蚀工艺在所述衬底的第二侧制备自限制腐蚀腔,所述衬底的腐蚀面为(100)晶面。
本发明实施例提供的半导体结构,通过设置器件层位于衬底的第一侧,自限制腐蚀腔位于衬底的第二侧,隔绝层和腐蚀阻挡层位于自限制腐蚀腔靠近器件层的一侧,且自限制腐蚀腔位于隔绝层和腐蚀阻挡层所限定的空间内,第一腐蚀腔位于自限制腐蚀腔远离器件层的一侧,且第一腐蚀腔与自限制腐蚀腔连通,使得衬底的第二侧的自限制腐蚀腔由衬底的第一侧形成腐蚀阻挡层所限定,从而使得衬底的第一侧和第二侧的图案均可在衬底的第一侧进行定位和对准,其工艺简单可控,通过衬底的第一侧制备的腐蚀阻挡层所形成的自限制腐蚀腔不受双面光刻的误差影响,其主要受单面光刻的误差影响,而单面光刻的误差在现代半导体工艺中可以控制的很小,解决了现有技术中双面光刻工艺采用人工方式来放置和对准掩膜版造成的对位不准确的问题,大大提高了深刻蚀器件中衬底第二侧的自限制腐蚀腔和衬底第一侧的器件层的对准精度。
附图说明
图1为本发明实施例提供的一种半导体结构的剖面结构示意图;
图2为本发明实施例提供的一种半导体结构的仰视结构示意图;
图3为本发明实施例提供的另一种半导体结构的剖面结构示意图;
图4为本发明实施例提供的一种半导体结构的制备方法的流程示意图;
图5为本发明实施例提供的另一种半导体结构的制备方法的流程示意图;
图6为本发明实施例提供的又一种半导体结构的制备方法的流程示意图;
图7为本发明实施例提供的又一种半导体结构的制备方法的流程示意图;
图8为本发明实施例提供的又一种半导体结构的制备方法的流程示意图;
图9为本发明实施例提供的又一种半导体结构的制备方法的流程示意图。
具体实施方式
下面结合附图和实施例对本发明作进一步的详细说明。可以理解的是,此处所描述的具体实施例仅仅用于解释本发明,而非对本发明的限定。另外还需要说明的是,为了便于描述,附图中仅示出了与本发明相关的部分而非全部结构。
图1为本发明实施例提供的一种半导体结构的剖面结构示意图,图2为本发明实施例提供的一种半导体结构的仰视结构示意图,如图1和图2所示,本发明实施例提供的半导体结构包括器件层10、隔绝层11、腐蚀阻挡层12、自限制腐蚀腔13、第一腐蚀腔14和衬底15。器件层10位于衬底15的第一侧151,自限制腐蚀腔13位于衬底15的第二侧152,隔绝层11和腐蚀阻挡层12位于自限制腐蚀腔13靠近器件层10的一侧,且自限制腐蚀腔13位于隔绝层11和腐蚀阻挡层13所限定的空间内,第一腐蚀腔14位于自限制腐蚀腔13远离器件层10的一侧,且第一腐蚀腔14与自限制腐蚀腔13连通。
具体的,如图1和图2所示,器件层10位于衬底15的第一侧151,其中,器件层10可以为mems器件的最终功能层的部分,器件层10可以是一层或者是多层,每一层的器件层10可构成一个子功能层,各子功能层之内可以是单一类型器件,也可以是各种类型器件的混合,本领域技术人员可根据预设的功能对器件层10进行设置。
继续参考图1和图2,隔绝层11和腐蚀阻挡层12位于自限制腐蚀腔13靠近器件层10的一侧,隔绝层11和腐蚀阻挡层12可由衬底15的第一侧151制备,自限制腐蚀腔13和第一腐蚀腔14可由衬底15的第二侧152制备,且自限制腐蚀腔13位于隔绝层11和腐蚀阻挡层13所限定的空间内,从而通过在衬底15的第一侧151设计隔绝层11和腐蚀阻挡层12的图案,来限定衬底15的第二侧152的图案。
具体的,制备半导体结构时,在衬底15的第一侧151制备腐蚀阻挡层12和器件层10,并利用腐蚀阻挡层12在衬底15的第二侧152形成第一腐蚀腔和自限制腐蚀腔,使得衬底15的第二侧152的自限制腐蚀腔13由衬底15的第一侧151形成腐蚀阻挡层13所限定,从而使得衬底15的第一侧151和第二侧152的图案均可在衬底15的第一侧151进行定位和对准,其工艺简单可控,通过衬底15的第一侧151制备的腐蚀阻挡层12所形成的自限制腐蚀腔13不受双面光刻的误差影响,其主要受单面光刻的误差影响,而单面光刻的误差在现代半导体工艺中可以控制的很小,这大大提高了深刻蚀器件中衬底15第二侧152的自限制腐蚀腔13和衬底15第一侧151的器件层10的对准精度。
本发明实施例提供的半导体结构,通过设置器件层10位于衬底15的第一侧151,自限制腐蚀腔13位于衬底15的第二侧152,隔绝层11和腐蚀阻挡层12位于自限制腐蚀腔13靠近器件层10的一侧,且自限制腐蚀腔13位于隔绝层11和腐蚀阻挡层13所限定的空间内,第一腐蚀腔14位于自限制腐蚀腔13远离器件层10的一侧,且第一腐蚀腔14与自限制腐蚀腔13连通,使得衬底15的第二侧152的自限制腐蚀腔13由衬底15的第一侧151形成腐蚀阻挡层13所限定,从而使得衬底15的第一侧151和第二侧152的图案均可在衬底15的第一侧151进行定位和对准,其工艺简单可控,通过衬底15的第一侧151制备的腐蚀阻挡层12所形成的自限制腐蚀腔13不受双面光刻的误差影响,其主要受单面光刻的误差影响,而单面光刻的误差在现代半导体工艺中可以控制的很小,解决了现有技术中双面光刻工艺采用人工方式来放置和对准掩膜版造成的对位不准确的问题,大大提高了深刻蚀器件中衬底15第二侧152的自限制腐蚀腔13和衬底15第一侧151的器件层10的对准精度。
继续参考图1和图2,可选的,隔绝层11位于器件层10靠近衬底15的一侧,腐蚀阻挡层12位于隔绝层11远离器件层10的一侧。
其中,如图1和图2所示,衬底15可选用单层硅衬底,先在衬底15的第一侧151制备腐蚀阻挡层12,再在衬底15的第一侧151以及腐蚀阻挡层12远离衬底15的一侧制备隔绝层11,从而在衬底15的第一侧151形成限定衬底15第二侧152的自限制腐蚀腔13的结构,使得自限制腐蚀腔13不受双面光刻的误差影响,解决了现有技术中双面光刻工艺采用人工方式来放置和对准掩膜版造成的对位不准确的问题,提高深刻蚀器件中衬底15第二侧152的自限制腐蚀腔13和衬底15第一侧151的器件层10的对准精度。
图3为本发明实施例提供的另一种半导体结构的剖面结构示意图,如图3所示,可选的,衬底15包括第一衬底分部21和第二衬底分部22,第二衬底分部22位于第一衬底分部21远离器件层10的一侧。隔绝层11位于第一衬底分部21和第二衬底分部22之间,腐蚀阻挡层12位于器件层10靠近第一腐蚀腔14的一侧,且腐蚀阻挡层12贯穿第一衬底分部21、隔绝层11以及至少部分第二衬底分部22。
其中,如图3所示,衬底15可选用soi硅片,soi硅片包括第一衬底分部21、隔绝层11和第二衬底分部22,且隔绝层11位于第一衬底分部21和第二衬底分部22之间,先在衬底15的第一侧151制备腐蚀阻挡层12,且腐蚀阻挡层12贯穿第一衬底分部21、隔绝层11以及至少部分第二衬底分部22,从而在衬底15的第一侧151形成限定衬底15第二侧152的自限制腐蚀腔13的结构,使得自限制腐蚀腔13不受双面光刻的误差影响,解决了现有技术中双面光刻工艺采用人工方式来放置和对准掩膜版造成的对位不准确的问题,提高深刻蚀器件中衬底15第二侧152的自限制腐蚀腔13和衬底15第一侧151的器件层10的对准精度。
此外,采用soi硅片可省去制备隔绝层11的工艺步骤,从而进一步简化工艺制程。
继续参考图1-3,可选的,自限制腐蚀腔13在器件层10所在平面的垂直投影位于第一腐蚀腔14在器件层10所在平面的垂直投影内,且第一腐蚀腔14在器件层10所在平面的垂直投影的面积大于自限制腐蚀腔13在器件层10所在平面的垂直投影的面积。
其中,如图1-3所示,先在衬底15的第二侧152制备第一腐蚀腔14,通过设置第一腐蚀腔14的面积较大,将腐蚀阻挡层12露出,从而使得衬底15第二侧152的图形化工艺可利用露出的腐蚀阻挡层12进行光刻对准,形成自限制腐蚀腔13,进而使得自限制腐蚀腔13不受双面光刻的误差影响,解决了现有技术中双面光刻工艺采用人工方式来放置和对准掩膜版造成的对位不准确的问题,提高深刻蚀器件中衬底15第二侧152的自限制腐蚀腔13和衬底15第一侧151的器件层10的对准精度。
可选的,隔绝层11的材料包括氧化硅或氮化硅,腐蚀阻挡层12的材料包括氧化硅。
其中,隔绝层11采用氧化硅或氮化硅等抗腐蚀的材料,腐蚀阻挡层12采用氧化硅等抗腐蚀的材料,从而实现限定自限制腐蚀腔13的范围。
在其他实施例中,隔绝层11和腐蚀阻挡层12也可采用其他抗腐蚀的材料,本领域技术人员可根据实际需求进行设置,本发明实施例对此不作限定。
基于同样的发明构思,本发明实施例还提供了一种半导体结构的制备方法,用于制备上述实施例提供的任一半导体结构,与上述实施例相同或相应的结构以及术语的解释在此不再赘述,图4为本发明实施例提供的一种半导体结构的制备方法的流程示意图,如图4所示,该方法包括如下步骤:
步骤110、提供一衬底。
其中,衬底可采用硅材料,也可采用其他材料,本发明实施例对此不作限定。
步骤120、在所述衬底上形成隔绝层和腐蚀阻挡层。
其中,隔绝层和腐蚀阻挡层可由衬底的第一侧制备。
步骤130、在所述衬底的第一侧制备器件层。
其中,器件层可以为mems器件的最终功能层的部分,器件层可以是一层或者是多层,每一层的器件层可构成一个子功能层,各子功能层之内可以是单一类型器件,也可以是各种类型器件的混合,本领域技术人员可根据预设的功能对器件层进行设置。
步骤140、在所述衬底的第二侧制备第一腐蚀腔。
其中,第一腐蚀腔可由衬底的第二侧制备。
步骤150、在所述衬底的第二侧制备自限制腐蚀腔,其中,所述隔绝层和所述腐蚀阻挡层位于所述自限制腐蚀腔靠近所述器件层的一侧,所述自限制腐蚀腔位于所述隔绝层和所述腐蚀阻挡层所限定的空间内,所述第一腐蚀腔位于所述自限制腐蚀腔远离所述器件层的一侧,且所述第一腐蚀腔与所述自限制腐蚀腔连通。
其中,自限制腐蚀腔可由衬底的第二侧制备,且自限制腐蚀腔位于隔绝层和腐蚀阻挡层所限定的空间内,从而通过在衬底的第一侧设计隔绝层和腐蚀阻挡层的图案,来限定衬底的第二侧的图案,从而使得衬底的第一侧和第二侧的图案均可在衬底的第一侧进行定位和对准,其工艺简单可控,通过衬底的第一侧制备的腐蚀阻挡层所形成的自限制腐蚀腔不受双面光刻的误差影响,其主要受单面光刻的误差影响,而单面光刻的误差在现代半导体工艺中可以控制的很小,这大大提高了深刻蚀器件中衬底第二侧的自限制腐蚀腔和衬底第一侧的器件层的对准精度。
图5为本发明实施例提供的另一种半导体结构的制备方法的流程示意图,如图5所示,可选的,衬底为单层硅衬底。
在所述衬底上形成隔绝层和腐蚀阻挡层,包括:
在所述衬底的第一侧刻蚀第一空腔,在所述第一空腔内填充氧化硅或氮化硅,形成腐蚀阻挡层。
在所述衬底的第一侧以及所述腐蚀阻挡层远离所述衬底的一侧制备所述隔绝层。
具体的,如图5所示,提供的衬底15为单层硅衬底,在衬底15的第一侧151光刻形成腐蚀阻挡层12的窗口,然后深硅刻蚀该窗口,形成腐蚀阻挡层12对应的第一空腔23,在第一空腔23内填充氧化硅或氮化硅,从而形成腐蚀阻挡层12。在衬底15的第一侧151以及腐蚀阻挡层12远离衬底15的一侧制备隔绝层11,然后在隔绝层11远离衬底15的一侧制作器件层10,通过双面光刻在衬底15的第二侧152形成第一腐蚀腔14的腐蚀窗口,从而形成第一腐蚀腔14,然后继续腐蚀形成自限制腐蚀腔13。其中,通过在衬底15的第一侧151设计隔绝层11和腐蚀阻挡层12的图案,来限定衬底15的第二侧152的自限制腐蚀腔13,从而使得衬底15第一侧151的器件层10和第二侧152的自限制腐蚀腔13均可在衬底15的第一侧151进行定位和对准,其工艺简单可控,通过腐蚀阻挡层12所形成的自限制腐蚀腔13不受双面光刻的误差影响,其主要受单面光刻的误差影响,而单面光刻的误差在现代半导体工艺中可以控制的很小,这大大提高了深刻蚀器件中衬底15第二侧152的自限制腐蚀腔13和衬底15第一侧151的器件层10的对准精度。
图6为本发明实施例提供的又一种半导体结构的制备方法的流程示意图,如图6所示,可选的,衬底15为soi硅片,soi硅片包括第一衬底分部21、隔绝层11和第二衬底分部22,隔绝层11位于第一衬底分部21和第二衬底分部22之间。
在所述衬底上形成隔绝层和腐蚀阻挡层,包括:
在所述衬底的第一侧刻蚀第二空腔,在所述第二空腔内填充氧化硅或氮化硅,形成腐蚀阻挡层,其中,所述腐蚀阻挡层贯穿所述第一衬底分部、所述隔绝层以及至少部分所述第二衬底分部。
具体的,如图6所示,提供的衬底15为soi硅片,soi硅片包括第一衬底分部21、隔绝层11和第二衬底分部22。在衬底15的第一侧151光刻形成腐蚀阻挡层12的窗口,然后深硅刻蚀该窗口,形成腐蚀阻挡层12对应的第二空腔24,在第二空腔24内填充氧化硅或氮化硅,从而形成腐蚀阻挡层12,其中,腐蚀阻挡层12贯穿第一衬底分部21、隔绝层11以及至少部分第二衬底分部22。在第一衬底分部21和腐蚀阻挡层12远离衬底15的一侧制作器件层10,通过双面光刻在衬底15的第二侧152形成第一腐蚀腔14的腐蚀窗口,从而形成第一腐蚀腔14,然后继续腐蚀形成自限制腐蚀腔13。其中,通过在衬底15的第一侧151设计隔绝层11和腐蚀阻挡层12的图案,来限定衬底15的第二侧152的自限制腐蚀腔13,从而使得衬底15第一侧151的器件层10和第二侧152的自限制腐蚀腔13均可在衬底15的第一侧151进行定位和对准,其工艺简单可控,通过腐蚀阻挡层12所形成的自限制腐蚀腔13不受双面光刻的误差影响,其主要受单面光刻的误差影响,而单面光刻的误差在现代半导体工艺中可以控制的很小,这大大提高了深刻蚀器件中衬底15第二侧152的自限制腐蚀腔13和衬底15第一侧151的器件层10的对准精度。
继续参考图5和图6,可选的,通过各向异性湿法腐蚀工艺或深硅干刻法刻蚀工艺在衬底15的第二侧152制备第一腐蚀腔14,通过各向同性湿法腐蚀工艺或各向异性湿法腐蚀工艺在衬底15的第二侧152制备自限制腐蚀腔13。
示例性的,如图5和图6所示,以通过深硅干刻法刻蚀工艺在衬底15的第二侧152制备第一腐蚀腔14,通过各向同性湿法腐蚀工艺在衬底15的第二侧152制备自限制腐蚀腔13为例,其中,各向同性湿法腐蚀工艺使用的腐蚀溶液是可以腐蚀硅的酸性溶液,比如硝酸和氢氟酸的混合液等,本领域技术人员可根据实际需求进行设置。
图7为本发明实施例提供的又一种半导体结构的制备方法的流程示意图,如图7所示,示例性的,以通过各向异性湿法腐蚀工艺在衬底15的第二侧152制备第一腐蚀腔14,通过各向同性湿法腐蚀工艺在衬底15的第二侧152制备自限制腐蚀腔13为例,各向异性湿法腐蚀工艺使用的腐蚀溶液是可以腐蚀硅的碱性溶液,比如koh溶液,tmah溶液等;各向同性湿法腐蚀工艺使用的腐蚀溶液是可以腐蚀硅的酸性溶液,比如硝酸和氢氟酸的混合液等,本领域技术人员可根据实际需求进行设置。
图8为本发明实施例提供的又一种半导体结构的制备方法的流程示意图,如图8所示,示例性的,以通过深硅干刻法刻蚀工艺在衬底15的第二侧152制备第一腐蚀腔14,通过各向异性湿法腐蚀工艺在衬底15的第二侧152制备自限制腐蚀腔13为例,各向异性湿法腐蚀工艺使用的腐蚀溶液是可以腐蚀硅的碱性溶液,比如koh溶液,tmah溶液等,本领域技术人员可根据实际需求进行设置。
图9为本发明实施例提供的又一种半导体结构的制备方法的流程示意图,如图9所示,示例性的,以通过各向异性湿法腐蚀工艺在衬底15的第二侧152制备第一腐蚀腔14,通过各向异性湿法腐蚀工艺在衬底15的第二侧152制备自限制腐蚀腔13为例,各向异性湿法腐蚀工艺使用的腐蚀溶液是可以腐蚀硅的碱性溶液,比如koh溶液,tmah溶液等,本领域技术人员可根据实际需求进行设置。
继续参考图8和图9,可选的,通过各向异性湿法腐蚀工艺在衬底15的第二侧152制备自限制腐蚀腔13,衬底15的腐蚀面为(100)晶面。
其中,衬底15可采用单层硅衬底或soi硅片,如图8和图9所示,以衬底15为单层硅衬底为例,当通过各向异性湿法腐蚀工艺在衬底15的第二侧152制备自限制腐蚀腔13时,可选取衬底15的(100)晶面为腐蚀面,从而获得断面为“v”形的自限制腐蚀腔13。
在其他实施例中,本领域技术人员可根据实际需求选取不同制备自限制腐蚀腔13的方法,本发明实施例对此不作限定。
本发明实施例提供的半导体结构的制备方法,通过在衬底的第一侧设计隔绝层和腐蚀阻挡层的图案,来限定衬底的第二侧的自限制腐蚀腔,从而使得衬底第一侧的器件层和第二侧的自限制腐蚀腔均可在衬底的第一侧进行定位和对准,其工艺简单可控,通过腐蚀阻挡层所形成的自限制腐蚀腔不受双面光刻的误差影响,其主要受单面光刻的误差影响,而单面光刻的误差在现代半导体工艺中可以控制的很小,这大大提高了深刻蚀器件中衬底第二侧的自限制腐蚀腔和衬底第一侧的器件层的对准精度。
注意,上述仅为本发明的较佳实施例及所运用技术原理。本领域技术人员会理解,本发明不限于这里所述的特定实施例,对本领域技术人员来说能够进行各种明显的变化、重新调整和替代而不会脱离本发明的保护范围。因此,虽然通过以上实施例对本发明进行了较为详细的说明,但是本发明不仅仅限于以上实施例,在不脱离本发明构思的情况下,还可以包括更多其他等效实施例,而本发明的范围由所附的权利要求范围决定。
本文用于企业家、创业者技术爱好者查询,结果仅供参考。