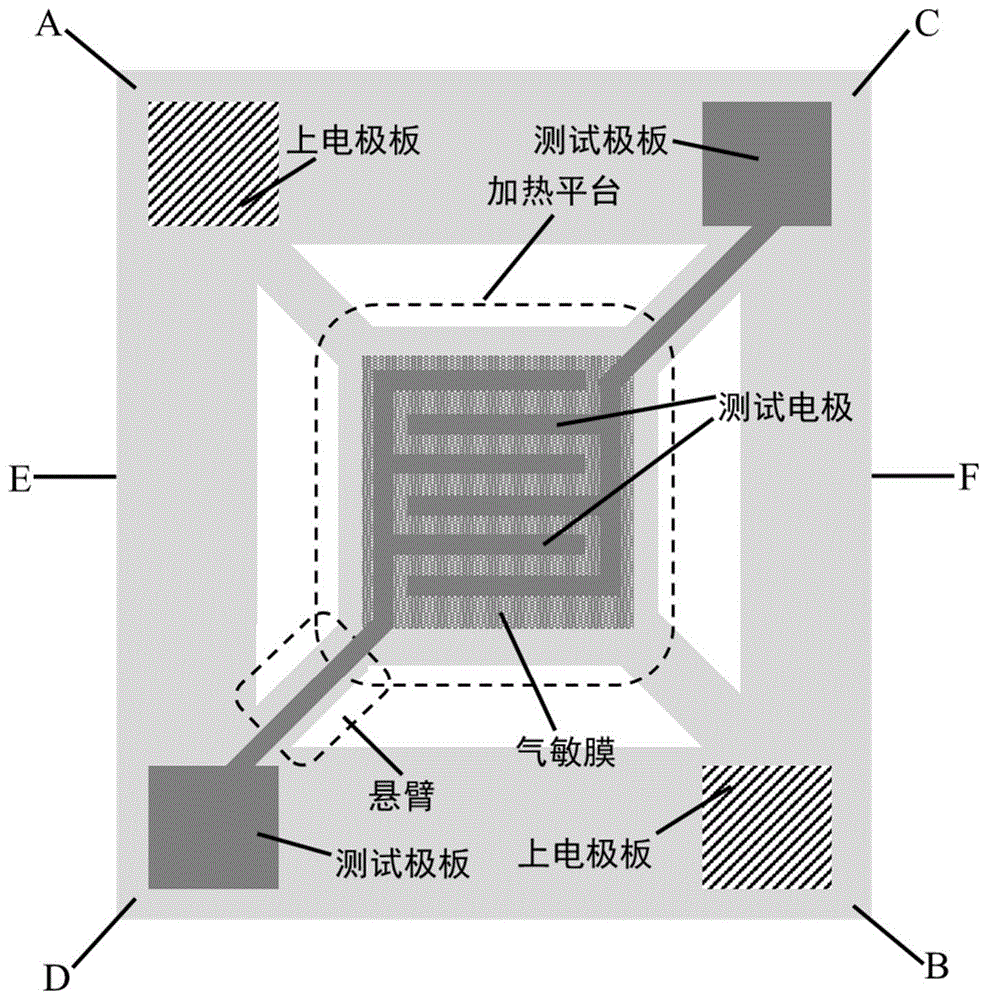
本发明属于微电子器件技术领域,特别涉及一种气体传感器,可用于对化学气体的检测,保证生产安全。
技术背景
当前,mems气体传感器以其高灵敏度、低功耗、小体积、易集成等众多优势,在人工智能、物联网、空气质量监测、化工生产和安全家居等领域发挥着极其重要的作用。mems气体传感器通常由mems微热板和气敏膜两部分组成,其中mems微热板发挥着至关重要的作用,它用于提供一个稳定且恒定的工作温度,以确保气敏膜可以准确地检测被测气体浓度变化,参见赵如如,mems集成甲醛传感器设计及性能检测研究,哈尔滨理工大学,2014。
传统mems气体传感器结构如图1所示,其中图1a为传统mems气体传感器的俯视图,图1b为传统mems气体传感器的ab剖面,图1c为传统mems气体传感器的cd剖面,图1d为传统mems气体传感器的ef剖面,图1e为传统mems气体传感器中加热电极的俯视图。该传统mems气体传感器自下而上包括:硅衬底、下绝缘层、加热电极、下电极板、上绝缘层、测试电极、上电极板、测试极板和气敏膜,该硅衬底通过腐蚀形成空气绝热槽,所述下电极板和上电极板之间设有接触孔,且下电极板和上电极板电气连接,所述下绝缘层和上绝缘层通过腐蚀形成加热平台和悬臂,所述加热电极各处金属厚度均相同。然而,传统mems气体传感器中的mems微热板,尤其是大尺寸mems微热板上的温度分布并不均匀,mems微热板中心温度与边缘温度差异大的问题依然十分显著,这导致mems微热板上部各处气敏膜的气敏响应存在较大差异,最终会影响整个mems气体传感器的气敏特性。
技术实现要素:
本发明的目的在于克服上述已有技术的不足,提出一种基于温度补偿结构的气体传感器,利用温度补偿结构补偿微热板上由中心至边缘的温度梯度,以显著改善微热板上温度分布的均匀性,减小气体传感器的功耗,提高气体传感器的气敏特性。
为实现上述目的,本发明提供了一种基于温度补偿结构的气体传感器,包括:硅衬底1、下绝缘层2、温度补偿结构加热电极3、上电极板9、下电极板4、上绝缘层5、覆盖层6、保护层7、测试电极8、测试极板10、加热平台15、悬臂16和气敏膜17,覆盖层6中间设有通孔阵列12和空气隔热层13,下电极板4与上电极板9之间电气连接,其特征在于:
所述温度补偿结构加热电极3,其在水平方向位于加热平台15的区域内,由自内向外环绕的m圈电极组成,呈“回”字形,各圈的电极由内而外依次命名为e1、e2、…、em,各圈电极的宽度均为w,相邻两圈电极间隔均为s,加热电极最外圈电极em与加热平台边界的水平间距为l,且w、s和l的取值范围均为0.5~10μm,同一圈电极的厚度相同,不同圈电极的厚度按照由内向外方向呈减小趋势,且第i圈电极厚度di由如下公式确定:
di=k-(k-r)×(i-1)/(m-1)
其中,k>r>0,i为整数,且1≤i≤m,m为温度补偿结构加热电极总圈数且m为大于等于2的整数;
所述空气隔热层13,其为长方体空腔,且下界面与上绝缘层5的上界面重合,该长方体空腔在水平方向位于温度补偿结构加热电极3中最外圈电极em所围的区域内,上表面各边与最外圈电极em的水平间距q均相等,q≥0μm;
所述通孔阵列12,其由p行、p列大小相同的正方形通孔组成,p≥2,各正方形通孔的边长u满足0μm<u<1μm,相邻两正方形通孔的间距为j,最外围正方形通孔的边界与温度补偿结构加热电极3中最外圈电极em的水平距离为f,且f>q。
进一步,其特征在于,下绝缘层2位于硅衬底1之上,温度补偿结构加热电极3位于下绝缘层2的上部中间,下电极板4位于下绝缘层2上部左上右下的对角位置,上绝缘层5位于温度补偿结构加热电极3和下电极板4的上部,覆盖层6位于上绝缘层5之上,保护层7位于覆盖层6之上。
进一步,其特征在于,测试电极8位于保护层7的上部中间,上电极板9位于保护层7上部左上右下的对角位置,测试极板10位于保护层7上部左下右上的对角位置,气敏膜17位于测试电极8的上部和间隙内。接触孔14位于下电极板4与上电极板9之间。
进一步,其特征在于,空气绝热槽11通过腐蚀硅衬底1形成;加热平台15和悬臂16通过腐蚀下绝缘层2、上绝缘层5、覆盖层6和保护层7同时形成。
进一步,其特征在于,硅衬底1选取p型(100)的硅片,其厚度h为200~500μm;覆盖层6的厚度tb为1~2.5μm;保护层7的厚度tc为2~4μm。
进一步,其特征在于,下绝缘层2的厚度td为1~5μm;上绝缘层5的厚度tu为1~5μm,且tu>k。
进一步,其特征在于,空气绝热槽10的深度g为5~100μm,其上表面在水平方向大于加热平台15区域,且上表面各边在水平方向与加热平台15边界的距离b均相等,20μm≤b≤150μm。
进一步,其特征在于,空气隔热层11的厚度ta为0.5~2.0μm,且ta<tb,其中tb为覆盖层6的厚度。
为实现上述目的,本发明制作基于温度补偿结构的气体传感器的方法,其特征在于,包括如下步骤:
a)在硅衬底上采用热氧化技术制作厚度td为1~5μm的sio2绝缘介质,形成下绝缘层;
b)制作温度补偿结构加热电极和下电极板:
b1)在下绝缘层上制作掩膜,利用该掩膜在下绝缘层上淀积宽度为w的m圈第一层金属,相邻两圈之间的间距为s,形成厚度为dm的第m圈电极em,同时在下绝缘层上淀积金属形成下电极板,w和s的取值范围均为0.5~10μm;
b2)在下绝缘层、下电极板和m圈第一层金属上部制作掩膜,利用该掩膜在第1圈电极至第m-1圈电极的第一层金属上淀积第二层金属,形成厚度为dm-1的第m-1圈电极em-1;以此类推,直至形成厚度为d1的第1圈电极e1,得到由e1至em的m圈电极,完成温度补偿结构加热电极的制作,其中:
m根据器件实际使用要求确定,其值为大于等于2的整数,同一圈电极的厚度相同,不同圈电极的厚度按照由内向外方向呈减小趋势,且第i圈电极ei的厚度di满足公式:
di=k-(k-r)×(i-1)/(m-1)
式中,k>r>0,i为整数,且1≤i≤m;
c)在温度补偿结构加热电极、下电极板和下绝缘层上淀积绝缘介质,并经过平坦化处理后,形成厚度为tu的上绝缘层,tu的取值范围为1~5μm,且tu>k;
d)在上绝缘层上淀积一层厚度为ta的易腐蚀材料层,ta的取值范围为0.5~2.0μm,并在易腐蚀材料层上制作掩膜,利用该掩膜刻蚀出形状为长方体的牺牲层,该牺牲层在水平方向位于温度补偿结构加热电极中最外圈电极em所围区域内,且上表面各边与最外圈电极em的水平间距为q,q≥0μm;
e)在牺牲层和上绝缘层上淀积一层绝缘介质,并进行平坦化处理,形成厚度为tb的覆盖层,tb的取值范围为1~2.5μm,且tb>ta;
f)在覆盖层表面制作掩膜,利用该掩膜进行刻蚀,刻蚀至牺牲层上表面为止,形成通孔阵列,该通孔阵列由p行、p列大小相同的正方形通孔组成,p≥2,各正方形通孔的边长u满足0μm<u<1μm,相邻两正方形通孔的间距为j,最外围正方形通孔的边缘与最外圈电极em的水平距离为f,且f>q;
g)利用f)步骤中形成的通孔阵列,采用湿法腐蚀工艺完全腐蚀掉牺牲层,形成空气隔热层;
h)在覆盖层上淀积厚度为tc的介质材料,tc的取值范围为2~4μm,完全覆盖通孔阵列,并进行平坦化处理,形成保护层;
i)在保护层表面制作掩膜,利用该掩膜进行刻蚀至下电极板上表面为止,形成接触孔;
j)在保护层、接触孔中下电极板的上部制作掩膜,利用该掩膜在接触中淀积金属,该金属完全填充接触孔,形成上电极板,上电极板与下电极板之间电气连接;
k)在保护层、上电极板的上部制作掩膜,利用该掩膜淀积金属,形成测试极板和测试电极;
l)在保护层、上电极板、测试电极和测试极板的上部制作掩膜,利用该掩膜进行刻蚀,且刻蚀至硅衬底表面为止,形成加热平台和悬臂,该加热平台的区域在水平方向大于温度补偿结构加热电极最外圈电极em所围的区域,且加热平台边界与最外圈电极em的水平间距均为l,且0.5μm≤l≤10μm;
m)采用湿法腐蚀工艺腐蚀硅衬底,形成深度g为5~100μm空气绝热槽,该空气绝热槽上表面在水平方向大于加热平台的区域,且加热平台边界在水平方向与空气绝热槽上表面各边的距离b均相等,且20μm≤b≤150μm;
n)在测试电极上部及测试电极间隙内涂覆气敏材料,形成气敏膜,完成整个传感器的制作。
本发明与现有技术相比具有以下优点:
1、温度分布均匀性好
本发明采用了自内向外环绕的m圈电极组成的“回”字形的温度补偿结构加热电极,同一圈电极的厚度相同,不同圈电极的厚度按照由内向外方向呈减小趋势,这种温度补偿结构加热电极的设置方式,可以实现不同圈电极的电阻按照由内向外方向逐渐增加,从而可以补偿微热板上由中心至边缘的温度梯度,确保微热板获得更好的温度分布均匀性。
2、功耗低
本发明由于采用了空气隔热层,可实现对温度补偿结构加热电极所提供的热量的有效存储,减小热量的散失,因此可显著减小所需加热功耗。
仿真结果表明,本发明的基于温度补偿结构的气体传感器的温度分布均匀性明显优于传统mems气体传感器。
附图说明
图1为传统mems气体传感器的结构图;
图2是本发明中基于温度补偿结构的气体传感器结构的俯视图;
图3是图2横向ab的剖面图;
图4是图2横向cd的剖面图;
图5是图2横向ef的剖面图;
图6是温度补偿结构加热电极的俯视图;
图7是图6温度补偿结构加热电极俯视图的放大图;
图8是温度补偿结构加热电极图形的剖面图;
图9是本发明中的通孔阵列分布图;
图10是本发明制作基于温度补偿结构的气体传感器的工艺流程图;
图11是本发明与传统mems气体传感器的温度分布仿真对比图。
具体实施方式
以下结合附图对本发明的实施例和效果作进一步详细描述。
参照图2、图3、图4、图5和图6,本发明基于温度补偿结构的气体传感器包括:硅衬底1、下绝缘层2、温度补偿结构加热电极3、下电极板4、上绝缘层5、覆盖层6、保护层7、测试电极8、上电极板9、测试极板10和气敏膜17。下绝缘层2位于硅衬底1之上,温度补偿结构加热电极3位于下绝缘层2的上部中间,下电极板4位于下绝缘层2上部的左上右下对角位置,上绝缘层5位于温度补偿结构加热电极3和下电极板4的上部,覆盖层6位于上绝缘层5之上,保护层7位于覆盖层6之上。测试电极8位于保护层7的上部中间,上电极板9位于保护层7上部的左上右下对角位置,测试极板10位于保护层7上部的左下右上对角位置,气敏膜17位于测试电极8的上部和间隙内。硅衬底1通过腐蚀形成空气绝热槽11,下电极板4与上电极板9之间设有接触孔14,覆盖层6中间设有通孔阵列12和空气隔热层13,下绝缘层2、上绝缘层5、覆盖层6和保护层7通过腐蚀同时形成加热平台15和悬臂16。
参照图7和图8,该温度补偿结构加热电极3,其在水平方向位于加热平台15的区域内,由自内向外环绕的m圈电极组成,呈“回”字形,各圈的电极由内而外依次命名为e1、e2、…、em,各圈电极的宽度均为w,相邻两圈电极间隔均为s,加热电极最外圈电极em与加热平台边界的水平间距为l,且w、s和l的取值范围均为0.5~10μm,同一圈电极的厚度相同,不同圈电极的厚度按照由内向外方向呈减小趋势,且第i圈电极厚度di由如下公式确定:
di=k-(k-r)×(i-1)/(m-1)
其中,k>r>0,i为整数,且1≤i≤m,m为温度补偿结构加热电极总圈数且m为大于等于2的整数;
该空气隔热层13,其为长方体空腔,厚度ta为0.5~2.0μm,且下界面与上绝缘层5的上界面重合,该长方体空腔在水平方向位于温度补偿结构加热电极3中最外圈电极em所围的区域内,上表面各边与最外圈电极em的水平间距q均相等,q≥0μm;
参照图9,该通孔阵列12,其由p行、p列大小相同的正方形通孔组成,p≥2,各正方形通孔的边长u满足0μm<u<1μm,相邻两正方形通孔的间距为j,最外围正方形通孔的边界与温度补偿结构加热电极3中最外圈电极em的水平距离为f,且f>q;
该硅衬底1,其厚度h为200~500μm,选取p型(100)的硅片;
该空气绝热槽11,其深度g为5~100μm,且上表面在水平方向大于加热平台15区域,上表面各边与加热平台15边界的水平间距b均相等,20μm≤b≤150μm;
该下绝缘层2,其厚度td为1~5μm;
该上绝缘层5,其厚度tu为1~5μm;
该覆盖层6,其厚度tb为1~2.5μm;
该保护层7,其厚度tc为2~4μm。
参照图10,本发明制作基于温度补偿结构的气体传感器给出如下三种实施例:
实施例一:制作p型(100)硅片厚度h为200μm,温度补偿结构加热电极的圈数m为3,第3圈电极e3厚度d3为0.2μm,第2圈电极e2厚度d2为0.6μm,第1圈电极e1厚度d1为1μm的基于温度补偿结构的气体传感器。
步骤1,在硅衬底上制作下绝缘层,如图10a。
在硅衬底上采用热氧化技术生长出一层厚度td为1μm的sio2绝缘介质,形成下绝缘层。
步骤2,在下绝缘层上制作温度补偿结构加热电极和下电极板,如图10b。
2a)在下绝缘层上第一次制作掩膜,采用电子束蒸发技术,即在真空度小于1.8×10-3pa,功率为220w,蒸发速率小于
2b)在下绝缘层上与金属pt上第二次制作掩膜,使用与2a)相同的电子束蒸发技术工艺条件,利用该掩膜在第1圈电极至第2圈电极的第一层金属pt上淀积厚度为0.4μm的第二层金属pt,形成厚度d2为0.6μm的第2圈电极e2;
2c)在下绝缘层上和金属pt上第三次制作掩膜,使用与2a)相同的电子束蒸发技术工艺条件,利用该掩膜在第1圈电极的第二层金属pt上淀积厚度为0.4μm的第三层金属pt,形成厚度d1为1μm的第1圈电极e1,完成温度补偿结构加热电极的制作。
步骤3,在温度补偿结构加热电极、下电极板和下绝缘层上制作上绝缘层,如图10c。
在温度补偿结构加热电极、下电极板和下绝缘层上,采用等离子体增强化学气相淀积技术,即在n2o流量为800sccm,sih4流量为200sccm,温度为250℃,rf功率为25w,压力为1100mt的工艺条件下,淀积sin绝缘介质,并进行平坦化处理,形成厚度tu为1μm的上绝缘层。
步骤4,在上绝缘层上制作牺牲层,如图10d。
在上绝缘层上,采用化学气相淀积技术,即在反应室温度为1200℃,sicl4流量在h2中的摩尔百分比为5%,薄膜生长速率为2.2μm/min条件下,淀积一层厚度ta为0.5μm的多晶硅;
采用反应离子刻蚀技术在多晶硅的表面制作掩膜,即在cf4流量为15sccm,压强为10mt,功率为100w的条件下,将多晶硅刻蚀成长方体的牺牲层,该牺牲层在水平方向位于温度补偿结构加热电极中最外圈电极e3所围区域内,且牺牲层上表面各边与最外圈电极e3的水平间距q为0.1μm。
步骤5,在牺牲层与上绝缘层上制作覆盖层,如图10e。
在牺牲层与上绝缘层上采用等离子体增强化学气相淀积技术,即在n2o流量为800sccm,sih4流量为200sccm,温度为250℃,rf功率为25w,压力为1100mt的工艺条件下,淀积一层sin绝缘介质,并进行平坦化处理,形成厚度tb为1μm的覆盖层。
步骤6,刻蚀覆盖层形成通孔阵列,如图10f。
在覆盖层表面制作掩膜,采用反应离子刻蚀技术,即在cf4流量为20sccm,o2流量为2sccm,压强为20mt,偏置电压为100v的工艺条件下,刻蚀至牺牲层上表面为止,形成通孔阵列。该通孔阵列由2行、2列大小相同的正方形通孔组成,各正方形通孔的边长u=0.2μm,相邻两正方形通孔的间距j为3.8μm,最外围正方形通孔的边界与最外圈电极e3的水平距离f为0.3μm。
步骤7,腐蚀牺牲层形成空气隔热层,如图10g。
采用湿法腐蚀工艺,即在四甲基氢氧化铵tmah溶液浓度为15%,温度为80℃的湿法腐蚀条件下,通过通孔阵列完全腐蚀掉牺牲层,形成空气隔热层。
步骤8,在覆盖层上制作保护层,如图10h。
在覆盖层上采用等离子体增强化学气相淀积技术,即在n2o流量为800sccm,sih4流量为200sccm,温度为250℃,rf功率为25w,压力为1100mt的工艺条件下,淀积一层sin绝缘介质,完全填充通孔阵列,并对其进行平坦化处理,形成厚度tc为2μm的保护层。
步骤9,制作接触孔,如图10i。
采用反应离子刻蚀技术在保护层表面制作掩膜,即在cf4流量为20sccm,o2流量为2sccm,压强为20mt,偏置电压为100v的工艺条件下,刻蚀至下电极板上表面为止,形成接触孔。
步骤10,制作上电极板,如图10j。
采用电子束蒸发技术在保护层、接触孔中下电极板的上部制作掩膜,即在真空度小于1.8×10-3pa,功率为220w,蒸发速率小于
步骤11,在保护层上制作测试电极和测试极板,如图10k。
采用电子束蒸发技术在保护层和上电极板的上部制作掩膜,即在真空度小于1.8×10-3pa,功率为220w,蒸发速率小于
步骤12,制作加热平台和悬臂,如图10l。
采用反应离子刻蚀技术在保护层、上电极板、测试电极和测试极板的上部制作掩膜,即在cf4流量为20sccm,o2流量为2sccm,压强为20mt,偏置电压为100v的工艺条件下,刻蚀至硅衬底表面为止,形成加热平台和悬臂,该加热平台的区域在水平方向上大于加热电极最外圈电极e3所围的区域,且最外圈电极e3与加热平台边界的水平间距l为0.5μm。
步骤13,制作空气绝热槽,如图10m。
在四甲基氢氧化铵tmah溶液浓度为15%,温度为80℃的湿法腐蚀条件下腐蚀硅衬底,形成深度g为5μm的空气绝热槽,该空气绝热槽上表面在水平方向大于加热平台的区域,且加热平台边界与空气绝热槽上表面各边的水平间距b为20μm。
步骤14,制作气敏膜,如图10n。
采用丝网印刷技术,在测试电极上部及测试电极间隙内涂覆氧化锡气敏材料,形成气敏膜,完成整个传感器的制作。
实施例二:制作p型(100)硅片厚度h为300μm,温度补偿结构加热电极的圈数m为4,第4圈电极e4厚度d4为0.5μm,第3圈电极e3厚度d3为0.8μm,第2圈电极e2厚度d2为1.1μm,第1圈电极e1厚度d1为1.4μm的基于温度补偿结构的气体传感器。
步骤一,在硅衬底上制作下绝缘层,如图10a。
在硅衬底上采用热氧化技术生长出一层厚度td为2μm的sio2绝缘介质,形成下绝缘层。
步骤二,在下绝缘层上制作温度补偿结构加热电极和下电极板,如图10b。
2.1)在下绝缘层上第一次制作掩膜,采用电子束蒸发技术,在下绝缘层上淀积厚度为0.5μm、宽度w为7μm的4圈第一层金属pt,相邻两圈之间的间距s为7μm,形成厚度d4为0.5μm的第4圈电极e4,同时在下绝缘层上淀积金属pt形成下电极板;
2.2)在下绝缘层上和金属pt上第二次制作掩膜,采用电子束蒸发技术,在第1圈电极至第3圈电极的第一层金属pt上淀积厚度为0.3μm的第二层金属pt,形成厚度d3为0.8μm的第3圈电极e3;
2.3)在下绝缘层上和金属pt上第三次制作掩膜,采用电子束蒸发技术,在第1圈电极至第2圈电极的第二层金属pt上淀积厚度为0.3μm的第三层金属pt,形成厚度d2为1.1μm的第2圈电极e2;
2.4)在下绝缘层上和金属pt上第四次制作掩膜,采用电子束蒸发技术,在第1圈电极的第三层金属pt上淀积厚度为0.3μm的第四层金属pt,形成厚度d1为1.4μm的第1圈电极e1,完成温度补偿结构加热电极的制作。
所述电子束蒸发技术的工艺条件为:真空度小于1.8×10-3pa,功率为230w,蒸发速率小于
步骤三,制作上绝缘层,如图10c。
采用等离子体增强化学气相淀积技术在温度补偿结构加热电极、下电极板和下绝缘层上淀积绝缘介质sin,并进行平坦化处理,形成厚度tu为2μm的上绝缘层,其中等离子体增强化学气相淀积技术的工艺条件为:n2o流量为850sccm,sih4流量为250sccm,温度为250℃,rf功率为35w,压力为1200mt。
步骤四,制作牺牲层,如图10d。
4.1)采用化学气相淀积技术在上绝缘层上淀积一层厚度ta为1μm的多晶硅;
4.2)在多晶硅的表面制作掩膜,采用反应离子刻蚀技术将易腐蚀材料层刻蚀成长方体的牺牲层,该牺牲层在水平方向位于加热电极中最外圈电极e4所围区域内,且上表面各边与最外圈电极e4的水平间距q为0.5μm。
所述化学气相淀积技术的工艺条件为:反应室温度为1200℃,sicl4流量在h2中的摩尔百分比为5%,薄膜生长速率为2.2μm/min。
所述反应离子刻蚀技术的工艺条件为:cf4流量为15sccm,压强为10mt,功率为100w。
步骤五,制作覆盖层,如图10e。
采用等离子体增强化学气相淀积技术在多晶硅和上绝缘层上淀积一层绝缘介质sin,并平坦化,形成厚度tb为2μm的覆盖层。
所述等离子体增强化学气相淀积技术的工艺条件为:n2o流量为850sccm,sih4流量为250sccm,温度为250℃,rf功率为35w,压力为1200mt。
步骤六,在覆盖层表面制作掩膜,利用该掩膜刻蚀出通孔阵列,如图10f。
在覆盖层表面制作掩膜,采用反应离子刻蚀技术在覆盖层表面进行刻蚀,刻蚀至牺牲层上表面为止,形成通孔阵列,该通孔阵列由3行、3列大小相同的正方形通孔组成,各正方形通孔的边长u为0.5μm,相邻两正方形通孔的间距j为43μm,最外围正方形通孔边缘与最外圈电极e4的水平距离f为1μm。
所述反应离子刻蚀技术的工艺条件为:cf4流量为20sccm,o2流量为2sccm,压强为20mt,偏置电压为100v。
步骤七,利用通孔腐蚀牺牲层,形成空气隔热层,如图10g。
采用湿法腐蚀技术腐蚀牺牲层形成空气隔热层。
所述湿法腐蚀技术的工艺条件为:四甲基氢氧化铵tmah溶液浓度为20%,温度为90℃。
步骤八,淀积介质材料覆盖覆盖层且填充通孔,形成保护层,如图10h。
采用等离子体增强化学气相淀积技术在覆盖层和通孔上淀积介质材料sin,完全填充通孔阵列,并进行平坦化处理,形成厚度tc为3μm的保护层。
所述等离子体增强化学气相淀积技术的工艺条件为:n2o流量为850sccm,sih4流量为250sccm,温度为250℃,rf功率为35w,压力为1200mt。
步骤九,在保护层表面制作掩膜,利用该掩膜刻蚀出接触孔,如图10i。
在保护层表面制作掩膜,采用反应离子刻蚀技术刻蚀至下电极板上表面为止,形成接触孔。其中反应离子刻蚀技术的工艺条件为:cf4流量为20sccm,o2流量为2sccm,压强为20mt,偏置电压为100v。
步骤十,在接触孔中淀积金属完全填充接触孔,形成上电极板,且与下电极板之间电气连接,如图10j。
在保护层、接触孔中下电极板的上部制作掩膜,采用电子束蒸发技术在接触孔中淀积金属au,该金属au完全填充接触孔,形成上电极板,且与下电极板之间电气连接。
所述电子束蒸发技术的工艺条件为:真空度小于1.8×10-3pa,功率为230w,蒸发速率小于
步骤十一,在保护层和上电极板表面制作掩膜,利用该掩膜淀积金属形成测试电极和测试极板,如图10k。
在保护层和上电极板表面制作掩膜,采用电子束蒸发技术淀积金属au形成测试极板和测试电极。其中电子束蒸发技术的工艺条件为:真空度小于1.8×10-3pa,功率为230w,蒸发速率小于
步骤十二,刻蚀形成加热平台和悬臂,如图10l。
在保护层、上电极板、测试电极和测试极板的上部制作掩膜,采用反应离子刻蚀技术进行刻蚀,且刻蚀至硅衬底表面为止,形成加热平台和悬臂,该加热平台的区域在水平方向大于温度补偿结构加热电极最外圈电极e4所围的区域,且加热平台边界与最外圈电极e4的水平间距l为5μm。
所述反应离子刻蚀技术的工艺条件为:cf4流量为20sccm,o2流量为2sccm,压强为20mt,偏置电压为100v。
步骤十三,采用湿法腐蚀工艺腐蚀硅衬底,形成空气绝热槽,如图10m。
采用湿法腐蚀技术在硅衬底中间刻蚀形成深度g为40μm的空气绝热槽,该空气绝热槽上表面在水平方向大于加热平台的区域,且加热平台边界在水平方向与空气绝热槽上表面各边的距离b为100μm,其中湿法腐蚀技术的工艺条件为:四甲基氢氧化铵tmah溶液的浓度为20%,温度为90℃。
步骤十四,采用丝网印刷技术,制作气敏膜,如图10n。
采用丝网印刷技术,在测试电极上部及测试电极的间隙内涂覆气敏材料氧化锡,形成气敏膜,完成整个传感器的制作。
实施例三:制作p型(100)硅片厚度h为500μm,温度补偿结构加热电极的圈数m为5,第5圈电极e5厚度d5为1.2μm、第4圈电极e4厚度d4为1.4μm,第3圈电极e3厚度d3为1.6μm,第2圈电极e2厚度d2为1.8μm,第1圈电极e1厚度d1为2μm的基于温度补偿结构的气体传感器。
步骤a,在硅衬底上制作下绝缘层,如图10a。
采用热氧化在硅衬底上生长出一层厚度td为5μm的sio2绝缘介质,形成下绝缘层。
步骤b,在下绝缘层上制作温度补偿结构加热电极和下电极板,如图10b。
首先,在下绝缘层上第一次制作掩膜,使用电子束蒸发技术,在下绝缘层上淀积厚度为1.2μm、宽度w为10μm的5圈第一层金属pt,相邻两圈之间的间距s为10μm,形成厚度d5为1.2μm的第5圈电极e5,同时在下绝缘层上淀积金属pt形成下电极板;
接着,在下绝缘层上和金属pt上第二次制作掩膜,使用电子束蒸发技术,在第1圈电极至第4圈电极的第一层金属pt上淀积厚度为0.2μm的第二层金属pt,形成厚度d4为1.4μm的第4圈电极e4;
接着,在下绝缘层上和金属pt上第三次制作掩膜,使用电子束蒸发技术,在第1圈电极至第3圈电极的第二层金属pt上淀积厚度为0.2μm的第三层金属pt,形成厚度d3为1.6μm的第3圈电极e3;
接着,在下绝缘层上和金属pt上第四次制作掩膜,使用电子束蒸发技术,在第1圈电极至第2圈电极的第三层金属pt上淀积厚度为0.2μm的第四层金属pt,形成厚度d2为1.8μm的第2圈电极e2;
最后,在下绝缘层上和金属pt上第五次制作掩膜,使用电子束蒸发技术,在第1圈电极的第四层金属pt上淀积厚度为0.2μm的第五层金属pt,形成厚度d1为2μm的第1圈电极e1,完成温度补偿结构加热电极的制作。
其中,电子束蒸发技术的工艺条件为:真空度小于1.8×10-3pa,功率为40w,蒸发速率小于
步骤c,在温度补偿结构加热电极、下电极板和下绝缘层上制作上绝缘层,如图10c。
采用等离子体增强化学气相淀积技术在n2o流量为900sccm,sih4流量为300sccm,温度为250℃,rf功率为40w,压力为1300mt的工艺条件下在温度补偿结构加热电极、下电极板和下绝缘层上淀积一层绝缘介质sin,并进行平坦化处理,形成厚度tu为5μm的上绝缘层。
步骤d,在上绝缘层上制作牺牲层,如图10d。
首先,采用化学气相淀积技术在反应室温度为1200℃,sicl4流量在h2中的摩尔百分比为5%,薄膜生长速率为2.2μm/min条件下在上绝缘层上淀积一层厚度ta为2μm的多晶硅;
然后,在多晶硅的表面制作掩膜,采用反应离子刻蚀技术在cf4流量为15sccm,压强为10mt,功率为100w的条件下将多晶硅刻蚀成长方体的牺牲层,该牺牲层在水平方向位于温度补偿结构加热电极中最外圈电极e5所围区域内,且上表面各边与最外圈电极e5的水平间距q为10μm。
步骤e,在牺牲层和上绝缘层上制作覆盖层,如图10e。
采用等离子体增强化学气相淀积技术在n2o流量为900sccm,sih4流量为300sccm,温度为250℃,rf功率为40w,压力为1300mt的工艺条件下在牺牲层和上绝缘层上淀积一层绝缘介质sin,并进行平坦化处理,形成厚度tb为2.5μm的覆盖层。
步骤f,在覆盖层表面制作掩膜,利用该掩膜刻蚀出通孔阵列,如图10f。
在覆盖层表面制作掩膜,采用反应离子刻蚀技术在cf4流量为20sccm,o2流量为2sccm,压强为20mt,偏置电压为100v的工艺条件下刻蚀至牺牲层上表面为止,形成通孔阵列,该通孔阵列由5行、5列大小相同的正方形通孔组成,各正方形通孔的边长u为1μm,相邻两正方形通孔的间距j为34μm,最外围正方形通孔边缘与最外圈电极em的水平距离f为15μm。
步骤g,利用通孔阵列腐蚀牺牲层,形成空气隔热层,如图10g。
采用湿法腐蚀技术在四甲基氢氧化铵tmah溶液浓度为25%,温度为100℃的湿法腐蚀条件下腐蚀牺牲层,形成空气隔热层。
步骤h,在覆盖层和通孔阵列上制作保护层,如图10h。
采用等离子体增强化学气相淀积技术在n2o流量为900sccm,sih4流量为300sccm,温度为250℃,rf功率为40w,压力为1300mt的工艺条件下,在覆盖层和通孔阵列上淀积介质材料sin,完全填充通孔阵列,并进行平坦化处理,形成厚度tc为4μm的保护层;
步骤i,刻蚀保护层制作接触孔,如图10i。
在保护层表面制作掩膜,采用反应离子刻蚀技术在cf4流量为20sccm,o2流量为2sccm,压强为20mt,偏置电压为100v的工艺条件下,刻蚀至牺牲层上表面为止,形成接触孔。
步骤j,在接触孔中淀积金属制作上电极板,如图10j。
在保护层、接触孔中下电极板的上部制作掩膜,采用电子束蒸发技术在真空度小于1.8×10-3pa,功率为240w,蒸发速率小于
步骤k,在保护层表面制作测试电极和测试极板,如图10k。
在保护层和上电极板表面制作掩膜,采用电子束蒸发技术在真空度小于1.8×10-3pa,功率为240w,蒸发速率小于
步骤l,制作加热平台和悬臂,如图10l。
在保护层、上电极板、测试电极和测试极板的上部制作掩膜,采用反应离子刻蚀技术在cf4流量为20sccm,o2流量为2sccm,压强为20mt,偏置电压为100v的工艺条件下,刻蚀至硅衬底表面为止,形成加热平台和悬臂,该加热平台的区域在水平方向大于温度补偿结构加热电极最外圈电极e5所围的区域,且加热平台边界与最外圈电极e5的水平间距l为10μm。
步骤m,腐蚀硅衬底制作空气绝热槽,如图10m。
采用湿法腐蚀技术在四甲基氢氧化铵tmah溶液浓度为25%,温度为100℃的工艺条件下腐蚀硅衬底,以在硅衬底中间形成深度g为100μm的空腔,该空气绝热槽上表面在水平方向大于加热平台的区域,且加热平台边界在水平方向与空气绝热槽上表面各边的距离b为150μm。
步骤n,制作气敏膜,如图10n。
采用丝网印刷技术,在测试电极上部及测试电极的间隙内涂覆气敏材料氧化锡,形成气敏膜,完成整个传感器的制作。
本发明的效果可通过以下仿真进一步说明。
一、仿真参数
设传统mems气体传感器的硅衬底厚度为300μm,空气绝热槽深度为100μm,下绝缘层厚度为3.5μm,加热电极厚度为0.6μm,上绝缘层的厚度为3μm,氧化锡气敏膜厚度为10μm。
本发明传感器中硅衬底的厚度h为300μm,空气绝热槽的深度g为100μm,下绝缘层的厚度td为3.5μm,温度补偿结构加热电极由6圈电极组成,加热电极宽度w和相邻两圈间隔s为5μm,加热电极最外圈电极e6与加热平台边界的水平间距l为5μm。空气隔热层的厚度ta为0.5μm,上绝缘层的厚度tu为1.5μm,保护层的厚度tc为2μm。覆盖层的厚度tb为1μm,加热平台在水平方向与空气绝热槽上面各边的距离b为38μm。氧化锡气敏膜厚度为10μm
二、仿真内容
对传统mems气体传感器和本发明传感器的温度分布情况进行仿真,结果如图11。
结合图11所示的加热平台沿ab剖面的温度分布可以明显地看出,本发明传感器通过利用温度补偿结构加热电极补偿了微热板上由中心至边缘的温度梯度,显著改善了微热板上温度分布的均匀性,表明本发明传感器的温度均匀性远优于传统mems气体传感器。
以上描述仅是本发明的几个具体实施例,并不构成对本发明的限制,显然对于本领域的专业人员来说,在了解了本发明内容和原理后,能够在不背离本发明的原理和范围的情况下,根据本发明的方法进行形式和细节上的各种修正和改变,但是这些基于本发明的修正和改变仍在本发明的权利要求保护范围之内。
本文用于企业家、创业者技术爱好者查询,结果仅供参考。