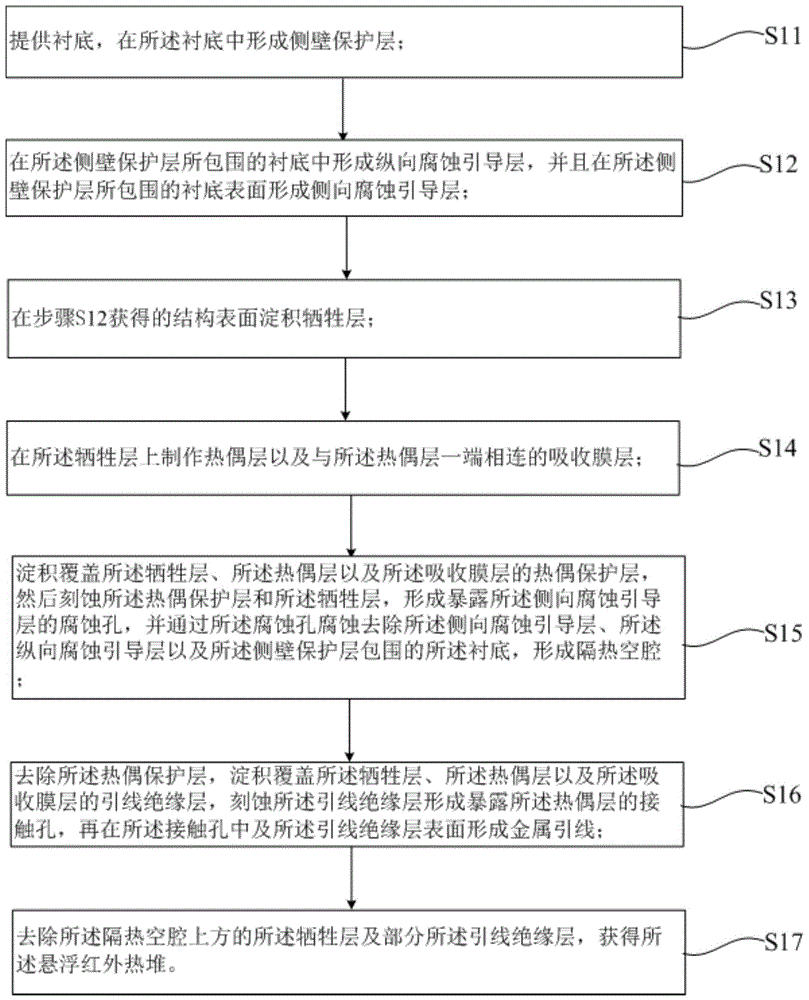
本发明属于硅微机械传感技术领域,特别是涉及一种在衬底上制作悬浮红外热堆的方法。
背景技术:
随着mems技术的迅猛发展,基于mems微机械加工技术制作的红外探测器以其尺寸小、价格低等优势被广泛应用于热电堆红外探测器现已广泛应用于非接触测温、气体传感、安保、卫星姿态控制、红外成像等领域。热堆红外探测器相比于其他类型的红外探测器具有明显的优势,例如可在室温下工作,无需制冷设备;具有自激励产生信号的特点,无需施加额外的偏置电压/电流,避免自加热效应的同时保证了低功耗:可以在不加斩波器的情况在实现对趋于静态的红外信号的直接测量;近年来热堆探测器阵列的发展进一步拓宽了热堆红外探测器的应用范围,同时也促使热堆红外探测器沿着更小型化、更低成本、更高性能方向发展。
传统的热堆探测器通常在介质薄膜上淀积多晶硅/金属制作热偶对,然后通过背面硅各向异性湿法腐蚀的方法在介质薄膜下方形成隔热空腔以增加热阻。但该方案需要双面加工,增加了工艺复杂度,同时器件下方没有了衬底结构,器件的机械强度下降。并且,该方案受制于(100)单晶硅衬底湿法腐蚀的各向异性,器件尺寸较大且热堆结构需要按照晶向排列,限制了热堆探测器性能的提升。
1992年,shie.j等人通过湿法腐蚀在以硅为衬底上的玻璃膜上制造红外探测器。但是受到硅湿法腐蚀的各向异性限制,器件结构的设计必须按照一定规则排列,不能获得性能最优解[shiej,wengp.designconsiderationsofmetal-filmbolometerwithmicromachinedfloatingmembrane[j].sensors&actuatorsaphysical,1992,33(3):183-189.]2006年,calaza.c等人通过采用标准cmos工艺和tmahpost-cmos技术制作了用于红外成像的微机械热电堆红外探测器阵列,并成功获得了室温红外成像效果。但是由于受到硅湿法腐蚀的各向异性限制,单一器件面积较大,最终的探测器阵列为16×16,密度较小,且湿法腐蚀工艺会破坏结构,降低成品率。[calazac,viaranin,pedrettig,etal.anuncooledinfraredfocalplanearrayforlow-costapplicationsfabricatedwithstandardcmostechnology[j].sensorsandactuatorsa(physical),2006,132(1):129-138.]。
因此,提供一种新的在衬底上制作悬浮红外热堆的方法是本领域技术人员需要解决的课题。
技术实现要素:
鉴于以上所述现有技术的缺点,本发明的目的在于提供一种在衬底上制作悬浮红外热堆的方法,用于解决现有技术的方法所制作的悬浮红外热堆存在工艺复杂、机械强度低、器件尺寸大、红外探测性能不佳等问题。
为实现上述目的及其他相关目的,本发明提供一种在衬底上制作悬浮红外热堆的方法,所述方法至少包括:
1)提供衬底,在所述衬底中形成侧壁保护层;
2)在所述侧壁保护层所包围的衬底中形成纵向腐蚀引导层,并且在所述侧壁保护层所包围的衬底表面形成侧向腐蚀引导层;
3)在步骤2)获得的结构表面淀积牺牲层;
4)在所述牺牲层上制作热偶层以及与所述热偶层一端相连的吸收膜层;
5)淀积覆盖所述牺牲层、所述热偶层以及所述吸收膜层的热偶保护层,然后刻蚀所述热偶保护层和所述牺牲层,形成暴露所述侧向腐蚀引导层的腐蚀孔,并通过所述腐蚀孔腐蚀去除所述侧向腐蚀引导层、所述纵向腐蚀引导层以及所述侧壁保护层包围的所述衬底,形成隔热空腔;
6)去除所述热偶保护层,淀积覆盖所述牺牲层、所述热偶层以及所述吸收膜层的引线绝缘层,刻蚀所述引线绝缘层形成暴露所述热偶层的接触孔,再在所述接触孔中及所述引线绝缘层表面形成金属引线;
7)去除所述隔热空腔上方的所述牺牲层及部分所述引线绝缘层,获得所述悬浮红外热堆。
作为本发明在衬底上制作悬浮红外热堆的方法的一种优化的方案,步骤1)中形成所述侧壁保护层的步骤包括:
1-1)在所述衬底表面形成中间薄外围厚的第一薄层,刻蚀中间薄的所述第一薄层区域形成第一窗口,刻蚀外围厚的所述第一薄层区域形成第二窗口并继续刻蚀下方的所述衬底形成第一槽体;
1-2)在步骤1-1)获得的结构表面淀积第二薄层,淀积在所述第一槽体侧壁上的所述第二薄层形成所述侧壁保护层。
作为本发明在衬底上制作悬浮红外热堆的方法的一种优化的方案,步骤2)中,形成所述纵向腐蚀引导层和所述引导层的步骤包括:
2-1)刻蚀所述第一窗口中的所述第二薄层并继续刻蚀下方的所述衬底形成第二槽体;
2-2)去除所述中间薄的所述第一薄层暴露出所述衬底;
2-3)在所述第二槽体中淀积形成所述纵向腐蚀引导层,在暴露的所述衬底表面淀积形成所述侧向腐蚀引导层。
作为本发明在衬底上制作悬浮红外热堆的方法的一种优化的方案,所述衬底包括(100)单晶硅衬底,所述侧壁保护层包括氧化硅及氮化硅中的一种。
作为本发明在衬底上制作悬浮红外热堆的方法的一种优化的方案,所述纵向腐蚀引导层包括多晶硅及非晶硅中的一种,所述侧向腐蚀引导层包括多晶硅及非晶硅中的一种。
作为本发明在衬底上制作悬浮红外热堆的方法的一种优化的方案,所述牺牲层包括是氧化硅及氮化硅中的一种。
作为本发明在衬底上制作悬浮红外热堆的方法的一种优化的方案,所述热偶层包括n型多晶硅条、p型多晶硅条及n型多晶硅条-热偶绝缘层-p型多晶硅条叠加结构中的一种。
作为本发明在衬底上制作悬浮红外热堆的方法的一种优化的方案,所述吸收膜层包括氮化硅。
作为本发明在衬底上制作悬浮红外热堆的方法的一种优化的方案,步骤5)中,所述隔热空腔通过xf2气体进行各向同性腐蚀或者碱性溶液各向异性腐蚀,去除所述侧向腐蚀引导层以及所述侧向腐蚀引导层下方的所述衬底后获得。
作为本发明在衬底上制作悬浮红外热堆的方法的一种优化的方案,所述热偶保护层包括氧化硅,所述引线绝缘层包括氧化硅及氮化硅中的一种,所述金属引线包括al、au、及pt中的一种或多种的组合。
作为本发明在衬底上制作悬浮红外热堆的方法的一种优化的方案,步骤7)中,通过气相hf腐蚀或者hf溶液腐蚀的方式去除所述隔热空腔上方的所述牺牲层及部分所述引线绝缘层。
如上所述,本发明的在衬底上制作悬浮红外热堆的方法,具有以下有益效果:
1、本发明利用牺牲层,保证了隔热空腔释放时悬浮结构的机械强度,提高了生产良率。
2、本发明避免了硅片的背面刻蚀,实现悬浮梁膜结构红外热堆的硅片单面加工,且工艺条件和步骤与标准cmos工艺兼容,可用于实现微传感器与集成电路的单片集成,有利于小尺寸、低成本、大批量生产。
3、本发明创新性地利用牺牲层和纵向腐蚀引导层,在(100)单晶硅衬底上获得具有深隔热空腔的悬浮红外热堆,打破了(100)单晶硅片上器件面积与隔热空腔深度的制约关系,在减小红外热堆单个器件面积的同时获得了更深的隔热空腔,并且热堆排布不再受各向异性腐蚀的限制,这能大大提高器件的红外传感性能。
附图说明
图1为本发明实施例中在衬底上制作悬浮红外热堆的方法的流程示意图。
图2~图16为本发明实施例中在衬底上制作悬浮红外热堆的方法所呈现的结构剖视图。
图17为本发明实施例中在衬底上制作悬浮红外热堆的方法所获的器件俯视图。
图18为本发明实施例中在衬底上制作悬浮红外热堆的方法所获的器件结构立体图。
图19为本发明实施例中在衬底上制作悬浮红外热堆的方法所获的器件结构立体半剖视图。
元件标号说明
1衬底
2侧壁保护层
3纵向腐蚀引导层
4侧向腐蚀引导层
5牺牲层
6热偶层
7吸收膜层
8热偶保护层
9腐蚀孔
10隔热空腔
11引线绝缘层
12接触孔
13金属引线
201第一薄层
2011外围厚的第一薄层
2012中间薄的第一薄层
202第一窗口
203第一槽体
204第二薄层
205第二槽体
具体实施方式
以下通过特定的具体实例说明本发明的实施方式,本领域技术人员可由本说明书所揭露的内容轻易地了解本发明的其他优点与功效。本发明还可以通过另外不同的具体实施方式加以实施或应用,本说明书中的各项细节也可以基于不同观点与应用,在没有背离本发明的精神下进行各种修饰或改变。
请参阅附图。需要说明的是,本实施例中所提供的图示仅以示意方式说明本发明的基本构想,遂图式中仅显示与本发明中有关的组件而非按照实际实施时的组件数目、形状及尺寸绘制,其实际实施时各组件的型态、数量及比例可为一种随意的改变,且其组件布局型态也可能更为复杂。
本实施例提供一种在衬底上制作悬浮红外热堆的方法,如图1所示,所述方法包括如下步骤:
首先执行步骤s11,提供衬底,在所述衬底中形成侧壁保护层。
作为优选的方案,本步骤形成侧壁保护层的步骤包括:
s111,所述衬底表面形成中间薄外围厚的第一薄层,刻蚀中间薄的所述第一薄层区域形成第一窗口,刻蚀外围厚的所述第一薄层区域形成第二窗口并继续刻蚀下方的所述衬底形成第一槽体。
具体地,如图2~图4所示,提供硅衬底1,先在所述衬底1表面淀积薄层2011并刻蚀中间区域暴露出衬底1,然后继续淀积薄层2012,所述薄层2012部分形成在衬底1表面,一部分覆盖在薄层2011表面,薄层2011和薄层2012最好为同一材质,两者合并为一体形成中间薄外围厚的第一薄层201,并刻蚀出第一窗口202与第一槽体203。
s112,在步骤s111获得的结构表面淀积第二薄层,淀积在所述第一槽体侧壁上的所述第二薄层形成所述侧壁保护层。
具体地,如图15所示,淀积第二薄层204,第二薄层204将第一窗口202、第一槽体203以及第一薄层201覆盖。其中,附着在所述第一槽体203内侧的第二薄层204被用作所述侧壁保护层2。
作为示例,所述衬底1包括(100)单晶硅衬底,所述侧壁保护层2包括氧化硅及氮化硅中的一种。
优选地,所述衬底1可以为n型或者p型(100)单面(或者双面)抛光单晶硅硅片。所述第一薄层201和第二薄层204为由低压化学气相淀积(lpcvd)制备得到的氧化硅。所述第一窗口202可以使用光刻胶做掩膜,运用反应离子刻蚀技术(rie)刻蚀形成。所述第一槽体203可以使用光刻胶做掩膜,运用深反应离子刻蚀技术(deep-rie)刻蚀形成。
需要说明的是,图2~图16是沿图17和图18的虚线aa’方向的剖视图。其中,图17是俯视图,图18是立体图。为了更好的展示器件的内部结构,图19示出了立体的半剖视图。
其次执行步骤s12,在所述侧壁保护层所包围的衬底中形成纵向腐蚀引导层,并且在所述侧壁保护层所包围的衬底表面形成侧向腐蚀引导层。
作为优选的方案,本步骤形成所述纵向腐蚀引导层和所述侧向腐蚀引导层的步骤包括:
s121,如图6所示,刻蚀所述第一窗口202中的所述第二薄层204并继续刻蚀下方的所述衬底1形成第二槽体205;
s122,如图7所示,去除所述中间薄的所述第一薄层201暴露出所述衬底1;
s123,如图8所示,在所述第二槽体205中淀积形成所述纵向腐蚀引导层3,在暴露的所述衬底1表面淀积形成所述侧向腐蚀引导层4。
需要说明的是,步骤s121在刻蚀所述第一窗口202中的第二薄层204时采用的是无掩膜工艺,因此其余部分表平面的第二薄层204也会被减薄,接下来以剩余的第一薄层201为掩膜刻蚀形成第二槽体205,在形成第二槽体205的同时,第一槽体203的底部会被继续刻蚀,深度变深,如图6所示;步骤s122中,在去除所述中间薄的所述第一薄层201的同时,周围厚的第一薄层201也会有所减薄,如图7所示;步骤s123中,在淀积形成所述纵向腐蚀引导层3和所述侧向腐蚀引导层4的过程中,所述第一槽体203中也会同时填充进腐蚀引导材料,如图8所示,这些材料可以使衬底1表面变得平坦,有利于后续工艺的进行。
所述纵向腐蚀引导层3包括多晶硅及非晶硅中的一种,所述侧向腐蚀引导层4包括多晶硅及非晶硅中的一种。本实施例中,所述纵向腐蚀引导层3和所述侧向腐蚀引导4层均为多晶硅。
通过所述纵向腐蚀引导层3和所述侧向腐蚀引导层4可以引导后续步骤的腐蚀液或者腐蚀气体往横向和纵向方向腐蚀衬底,从而控制隔热空腔10的广度和深度。
在需要说明的是,所述纵向腐蚀引导层3的深度不能大于所述侧壁保护层2的深度,因为纵向腐蚀引导层3在引导腐蚀溶液或腐蚀气体向下腐蚀的同时也会向两侧推进,直到遇到所述侧壁保护层2才会停止,如果所述纵向腐蚀引导层3的深度比侧壁保护层2的深度深,腐蚀溶液或腐蚀气体就会突破所述侧壁保护层2的阻挡,腐蚀过程就会变得不可控。
然后执行步骤s13,如图9所示,在步骤s12获得的结构表面淀积牺牲层5。
作为示例,所述牺牲层5包括是氧化硅及氮化硅中的一种。本实施例中,所述牺牲层5为氧化硅,且所述牺牲层5采用低压化学气相淀积(lpcvd)制备得到,厚度为1μm。
接着执行步骤s14,在所述牺牲层上制作热偶层以及与所述热偶层一端相连的吸收膜层。
如图10所示,可以先淀积热偶材料,然后使用光刻胶作为掩膜,运用rie工艺刻蚀出所需形状的热偶层6。作为示例,所述热偶层6包括n型多晶硅条、p型多晶硅条及n型多晶硅条-热偶绝缘层-p型多晶硅条叠加结构中的一种。本实施例中,所述热偶层6为掺磷n型多晶硅,厚度为1μm。
如图11所示,可以先使用lpcvd淀积吸收膜材料,然后使用光刻胶作为掩膜,刻蚀出所需形状的吸收膜层7。作为示例,所述吸收膜层7可以为氮化硅,厚度范围为0.5μm~2μm。
接着执行步骤s15,淀积覆盖所述牺牲层、所述热偶层以及所述吸收膜层的热偶保护层,然后刻蚀所述热偶保护层和所述牺牲层,形成暴露所述侧向腐蚀引导层的腐蚀孔,并通过所述腐蚀孔腐蚀去除所述侧向腐蚀引导层、所述纵向腐蚀引导层以及所述侧壁保护层包围的所述衬底,形成隔热空腔。
如图12所示,可以先淀积热偶保护层8,然后使用光刻胶作为掩膜,运用rie工艺刻蚀出所述腐蚀孔9。
作为示例,所述热偶保护层8包括氧化硅。本实施例中,所述热偶保护层8为厚度1μm由lpcvd制备得到的氧化硅。
作为示例,所述隔热空腔10通过xf2气体进行各向同性腐蚀或者碱性溶液各向异性腐蚀,去除所述侧向腐蚀引导层4、所述纵向腐蚀引导层3以及所述侧壁保护层2包围的所述衬底1后获得。本实施例中,可以使用tmah(四甲基氢氧化铵)或者koh(氢氧化钾)腐蚀液蚀去除所述侧向腐蚀引导层4、所述纵向腐蚀引导层3以及所述侧壁保护层2包围的所述衬底1,形成隔热空腔10,如图13所示。
由此可见,通过所述侧向腐蚀引导层4和所述纵向腐蚀引导层3可以在(100)单晶硅衬底1上获得具有深隔热空腔10的悬浮红外热堆,打破了(100)单晶硅片上器件面积与隔热空腔深度的制约关系,在减小红外热堆单个器件面积的同时获得了更深的隔热空腔,并且热堆排布不再受各向异性腐蚀的限制,这能大大提高器件的红外传感性能。
另外,通过所述牺牲层5可以保证隔热空腔(深槽)释放时悬浮结构的机械强度,提高了生产良率。
再执行步骤s16,去除所述热偶保护层,淀积覆盖所述牺牲层、所述热偶层以及所述吸收膜层的引线绝缘层,刻蚀所述引线绝缘层形成暴露所述热偶层的接触孔,再在所述接触孔中及所述引线绝缘层表面形成金属引线。
如图14所示,可以先使用lpcvd淀积引线绝缘层11,然后使用光刻胶作为掩膜,运用rie工艺刻蚀出所述接触孔12。
作为示例,所述引线绝缘层11包括氧化硅及氮化硅中的一种,所述金属引线13包括al、au、及pt中的一种或多种的组合。本实施例中,所述引线绝缘层11为氧化硅,厚度200nm;所述金属引线13为au。形成的金属引线13,如图15所示。
最后执行步骤s17,去除所述隔热空腔上方的所述牺牲层及部分所述引线绝缘层,获得所述悬浮红外热堆。
如图16所示,可以通过气相hf腐蚀或者hf溶液腐蚀的方式去除所述隔热空腔10上方的所述牺牲层5及部分所述引线绝缘层11。本实施例中,通过气相hf腐蚀去除所述隔热空腔10上方的所述牺牲层及部分所述引线绝缘层11。
需要说明的是,在去除所述隔热空腔10上方的所述牺牲层及部分所述引线绝缘层11的同时,还可以去除侧壁保护层2及部分第一薄层201,如图16所示。
总之,本实施例提供了一种在衬底上制作悬浮红外热堆的方法,该方法使用单面工艺,在减小器件尺寸的同时,提供更深的隔热空腔以增加热阻,提高红外探测性能,克服了基于(100)硅衬底的传统热堆探测器尺寸大、需要双面加工以及隔热空腔不够深引发器件红外探测性能下降的问题,同时本方法的工艺步骤和条件与标准ic工艺兼容。
上述实施例仅例示性说明本发明的原理及其功效,而非用于限制本发明。任何熟悉此技术的人士皆可在不违背本发明的精神及范畴下,对上述实施例进行修饰或改变。因此,举凡所属技术领域中具有通常知识者在未脱离本发明所揭示的精神与技术思想下所完成的一切等效修饰或改变,仍应由本发明的权利要求所涵盖。
本文用于企业家、创业者技术爱好者查询,结果仅供参考。