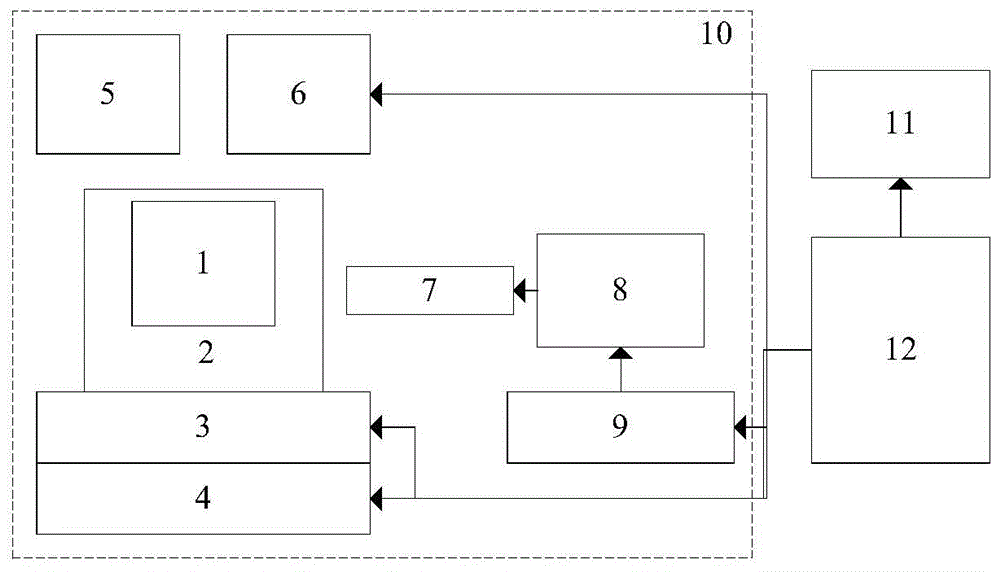
本发明属于纳米孔加工技术领域,具体涉及一种自动精确定位制备固态纳米孔阵列的系统及方法。
背景技术:
随着纳米科学技术的发展,纳米孔单分子技术已成为生命科学领域应用研究最强有力的工具之一。固态纳米孔因其性能稳定,孔径可控等优点被诸多研究者应用于dna测序,rna测序和蛋白结构测试的实验中,其制备材料多以二维薄膜材料为主。现有的固态纳米孔加工方法主要有透射电镜加工,聚焦离子束加工以及电击穿加工方法等,前两者因其设备昂贵,实验室条件要求苛刻,其加工低于2nm的纳米孔仍然存在技术瓶颈等问题,限制了该方法的适用范围。
固态纳米孔电击穿制备方法因其设备简单,具有原位制备纳米孔的优势广泛适用于纳米孔技术研究团队。随着该技术的发展,主要从恒压源击穿法,电压脉冲击穿法,电流脉冲击穿法,基于玻璃微管的电流击穿法以及基于z-score的恒电压源击穿法等。其中恒压源击穿法具有击穿速度快的优点,但由于需要预设击穿电流值会导致制备假纳米孔和打破纳米薄膜的问题逐渐被淘汰;电压脉冲击穿法和电流脉冲击穿法是现在的主流打孔方法,具备纳米孔孔径,孔型可控的优点,但因为其纳米孔孔径测试与电脉冲穿插执行,导致了孔径测试不准确和制备耗时的缺点;基于玻璃微管的电流击穿法和基于z-score恒压源击穿法是近来研究组提出的新的纳米孔制备方法,前者具有纳米孔位置可控的优点,后者具有纳米孔孔径可控的优点,但基于玻璃微管的电流击穿法所使用的采用接近电容控制位移的方法需要额外的设备以及离线电容的计算等繁琐程序,不利于该设备的广泛使用;基于z-score恒压源击穿法很好的解决了恒压源电击穿法需要预设击穿电流值以及存在的打假孔和打破薄膜的问题,并且可以将纳米孔的打孔精度控制在0.5nm以内,但是其仍然需要研究者探索打孔电压参数,并且因为固定了扩孔电压持续时间以及扩孔电压,严重的影响了打孔精度和扩孔时间。
技术实现要素:
基于存在的上述问题,本发明提供一种自动精确定位制备固态纳米孔阵列的系统及方法,其能够精确控制固态纳米孔制备位置、实现纳米孔阵列的自动化快速制备,有效提高了纳米孔制备的稳定性,进而提高纳米孔检测的实验效率。
依据本发明的第一方面,提供一种自动精确定位制备固态纳米孔阵列的系统,其整个过程采用自动化系统控制,实现固态纳米孔的自动化制备,固态纳米孔阵列制备,进而实现固态纳米孔相关检测应用。
进一步地,所述自动精确定位制备固态纳米孔阵列的系统包括纳米薄膜芯片1,缓冲池2,纳米操控台3,第一三维微操控平台4,光源5,显微镜6,玻璃微管7,玻璃微管夹持器8,第二三维微操控平台9,法拉第屏蔽罩10,iv扫描模块11及控制系统12,其特征在于,所述纳米薄膜芯片1安放在缓冲池2中,并构成上下结构的腔室;缓冲池2设置有接入下腔室的氯化银/银电极接口;缓冲池2固定在纳米操控台3上;所述纳米操控台3为采用压电陶瓷控制的高精度纳米操控台,通过电路连接到控制系统12,通过设置参数进行实时控制;所述纳米操控台3固定在第一三维微操控平台4上;所述第一三维微操控平台及第二三维微操控平台电路上连接到控制系统12,通过设置参数实时控制;所述第一三维微操控平台及第二三维微操控平台机械上固定在常用的防震平台上;所述的光源5和显微镜6电路上连接到控制系统,通过设置参数调节光源亮度,观察显微镜图像;所述的光源5和显微镜6机械上固定在与第一三维微操控平台及第二三维微操控平台同样的防震平台上;所述的玻璃微管7夹持在玻璃微管夹持器8上,位于纳米薄膜芯片1的正上方;所述玻璃微管7中注有缓冲池2下腔室同样的缓冲溶液licl,并连接有氯化银/银电极,与缓冲池2下腔室的电极一起连接到iv扫描模块11;所述玻璃微管夹持器机械上固定在第二三维微操控平台9上;所述法拉第屏蔽罩10安放在防震平台上,并保证与防震平台金属导电面的电气连接,将自动精确定位制备固态纳米孔阵列的系统置于该屏蔽罩所构建的空间中。
优选地,所述纳米操控台3通过螺丝固定在第一三维微操控平台4上。
优选地,所述法拉第屏蔽罩10采用铝合金材料制造。所述系统的屏蔽罩尺寸为500mm*700mm*500mm的长方体壳。缓冲池2通过螺丝固定在纳米操控台3上。
依据本发明的第二方面,提供一种使用上述系统的方法,其包括以下步骤:
(1)准备纳米薄膜芯片1,将纳米薄膜芯片安装在缓冲池2中,注入缓冲溶液;
所述纳米薄膜芯片1为氮化硅薄膜、石墨烯薄膜、二硫化钼薄膜、二硫化钨薄膜或者其他厚度在0.35~30nm的纳米薄膜;在纳米薄膜上先加工200nm左右的孔,再将二维材料薄膜转移到该纳米薄膜上,形成一个开窗为200nm的二维材料薄膜;
所述缓冲池2采用pmma,特氟龙等材料制得;所述缓冲池与纳米薄膜芯片匹配,将纳米薄膜芯片固定,并形成纳米薄膜芯片两端完整接触的缓冲池;所述缓冲池的纳米薄膜面采用低外沿设计,留有玻璃微管的操作空间和显微镜的观察空间;所述缓冲池固定在纳米操控台3上;
(2)选择闭环控制精度高于1nm、行程大于3um的压电陶瓷器件及控制器,搭建z轴方向的纳米操控台3,其与缓冲池2以及第一三维微操台匹配安装,在微操台对纳米薄膜芯片位置粗定位的基础上,实现纳米薄膜芯片与玻璃微管尖端位置的纳米级定位;
(3)选择闭环控制精度为0.5um、行程大于15mm的步进电机及控制器,控制第一,第二三维为操控台,其中第一三维微操控台4与纳米操控台匹配安装,第二三维微操控台9与玻璃微管夹持器8匹配安装;
所述三维微操台为选择的精度为0.5um、行程大于15mm的三维操纵台,其控制电机采用5相步进电机,电机与步进电机驱动器和控制器连接,受整机控制系统的控制;
所述第一三维微操台与纳米操控台匹配安装,并控制纳米薄膜芯片窗口位于显微镜的焦面位置,控制纳米薄膜芯片与玻璃微管尖端的相对位置;
所述第二三维微操台与玻璃微管夹持器匹配安装,控制玻璃微管位于纳米薄膜芯片窗口的具体位置,控制精度为0.5um。
(4)搭建能实时观察纳米薄膜芯片窗口的显微镜系统;
(5)采用玻璃微管拉制仪,其尖端内径为200nm~3um;
(6)根据玻璃微管的尺寸,制造可拆卸的v型结构的玻璃微管夹持器8;
所述玻璃微管夹持器8用于夹持玻璃微管8,所述玻璃微管夹持器8与第二三维微操台9匹配安装;
(7)根据整机仪器的尺寸,制造长方体壳的铝合金屏蔽罩10;所述屏蔽罩具有电磁屏蔽和光屏蔽的作用,屏蔽外界环境对系统带来的电磁干扰以及光干扰;
(8)组建iv扫描模块11;所述iv扫描模块提供精度为0.1pa的恒定电流输出,输出功率大于42w。
相对于现有技术,本发明的有益效果为:(1)能快速制备低于1nm的纳米孔;(2)单孔制备时间控制在300ms以内;(3)纳米孔加工位置精确可控。
本发明申请与现行技术相比,通过本专利所描述的系统及方法能够在各种类型的薄膜上快速制备位置精确,孔径精确的固态纳米孔,尤其能够自动制备阵列纳米孔,进而实现固态纳米孔相关检测应用,尤其可以用于dna测序,rna测试以及蛋白测试等领域。
附图说明
图1是依据本发明的自动精确定位制备固态纳米孔阵列的系统结构示意图。
图2是本发明的玻璃微管图片及电镜图片。
图3是本发明的纳米薄膜的iv测试曲线图。
图4是本发明的制备完成的纳米孔的iv曲线图。
图5是本发明的制备完成的纳米孔的iv曲线图。
图6是依据本发明的纳米孔制备操作流程示意图。
附图标记具体指示如下:
图1中1:纳米薄膜芯片,2:缓冲池,3:纳米操控台,4:第一三维微操台,5:光源,6:显微镜,7:玻璃微管,8:玻璃微管夹持器,9:第二三维微操台,10:法拉第屏蔽罩,11:iv扫描模块,12:控制系统;
图2中:pipette-b1、b2拉制参数:p=200,heat=529,pull=30,vel=40,time=250,pipette-s1、s2拉制参数:p=200,heat=530,pull=80,vel=70,del=80;
图3中:m1:厚度为10nm,开窗面积130um*100um的氮化硅薄膜;
图4中:b1,b2,s1,s2:用图2中b1,b2,s1,s2的玻璃微管打孔并实时测试的iv曲线图;null:在薄膜两端注满溶液测试的iv曲线图;纳米孔的孔径为4.5nm;
图5中:使用尖端直径为1um的b1玻璃微管加工纳米孔,打孔电压20v,膜厚20nm,缓冲溶液参数为:1mlicl:ph=9.04σ=6.54,计算得知该纳米孔孔径为0.4nm;此为测得的用b1玻璃微管打孔并实时测试的iv曲线图,此时纳米孔的孔径为0.4nm(限制电压20v1um玻璃微管)。
具体实施方式
下面将结合本发明实施例中的附图,对本发明实施例中的技术方案进行清楚、完整地描述。显然,所描述的实施例仅仅是本发明的一部分实施例,而不是全部的实施例。基于本发明中的实施例,本领域普通技术人员在没有做出创造性劳动前提下所获得的所有其他实施例,都属于本发明保护的范围。另外地,不应当将本发明的保护范围仅仅限制至下述具体实验方法或具体参数。
为了能实现固态纳米孔的自动化制备和精确制备,本发明所提出的自动精确定位制备固态纳米孔阵列的系统及方法,能够在各种类型的薄膜上制备位置精确,孔径精确的固态纳米孔,整个过程采用自动化系统控制,实现固态纳米孔的自动化制备,固态纳米孔阵列制备,进而实现固态纳米孔相关检测应用,尤其可以用于dna测序,rna测试以及蛋白测试等领域。该自动精确制备系统包括纳米薄膜芯片1,缓冲池2,纳米操控台3,第一三维微操控平台4,光源5,显微镜6,玻璃微管7,玻璃微管夹持器8,第二三维微操控平台9,法拉第屏蔽罩10,iv扫描模块11及控制系统12。
如图1所示。所述纳米薄膜芯片1可以是氮化硅薄膜,石墨烯薄膜,二硫化钼薄膜,二硫化钨薄膜或者其他厚度在0.35nm~30nm的纳米薄膜;所述纳米薄膜芯片1安放在缓冲池2中,并构成上下结构的腔室,并在下腔室中注入缓冲溶液licl;缓冲池2采用pmma,特氟龙等材料设计,并留有接入下腔室的氯化银/银电极接口;缓冲池2固定在纳米操控台3上,通过螺丝固定;所述纳米操控台3为采用压电陶瓷控制的高精度纳米操控台,其电路上连接到控制系统12,通过设置参数进行实时控制;所述纳米操控台3机械上通过螺丝固定在第一三维微操控平台4上;所述第一三维微操控平台及第二三维微操控平台电路上连接到控制系统12,通过设置参数实时控制;所述第一三维微操控平台及第二三维微操控平台机械上固定在常用的防震平台上;所述的光源5,显微镜6电路上连接到控制系统,通过设置参数调节光源亮度,观察显微镜图像;所述的光源5和显微镜6机械上固定在与第一三维微操控平台及第二三维微操控平台同样的防震平台上;所述的玻璃微管7夹持在玻璃微管夹持器8上,位置上位于纳米薄膜芯片1的正上方;所述玻璃微管7中注有缓冲池2下腔室同样的缓冲溶液licl,并连接有氯化银/银电极,与缓冲池2下腔室的电极一起连接到iv扫描模块11;所述玻璃微管夹持器机械上固定在第二三维微操控平台9上;所述法拉第屏蔽罩10采用铝合金材料设计,安放在防震平台上,并保证与防震平台金属导电面的电气连接,将整套系统置于该屏蔽罩所构建的空间中,减少外界的干扰,并发明所设计样机的屏蔽罩尺寸为500mm*700mm*500mm的长方体壳。
进一步地,本发明是通过以下步骤来实现的:
(1)准备纳米薄膜芯片1,将纳米薄膜芯片安装在缓冲池2中,注入缓冲溶液;
所述纳米薄膜芯片1可以是氮化硅薄膜,石墨烯薄膜,二硫化钼薄膜,二硫化钨薄膜或者其他厚度在0.35~30nm的纳米薄膜。所述碳化硅纳米薄膜采用掩模刻蚀硅衬底的方式制得,形成开窗面积为5um-200um的矩形纳米薄膜窗口;所述石墨烯,二硫化钼,二硫化钨等薄膜是在氮化硅薄膜的基础上转移而来:在氮化硅薄膜上先加工200nm左右的孔,再将二维材料薄膜转移到该氮化硅薄膜上,形成一个开窗为200nm的二维材料薄膜;
所述缓冲池2为采用pmma,特氟龙等材料制得。所述缓冲池与纳米薄膜芯片匹配,将纳米薄膜芯片固定,并形成纳米薄膜芯片两端完整接触的缓冲池;所述缓冲池的纳米薄膜面采用低外沿设计,留有玻璃微管的操作空间和显微镜的观察空间;所述缓冲池固定在纳米操控台3上。
(2)选择闭环控制精度高于1nm,行程大于3um的压电陶瓷器件及控制器,搭建z轴方向的纳米操控台3,其与缓冲池2以及第一三维微操台匹配安装,在微操台对纳米薄膜芯片位置粗定位的基础上,实现纳米薄膜芯片与玻璃微管尖端位置的纳米级定位;也可以用于dna等待测分子的纳米操控。
(3)选择闭环控制精度为0.5um,行程大于15mm的步进电机及控制器,进一步通过设计三维微操台结构和程序,其中第一三维微操控台4与纳米操控台匹配安装,第二三维微操控台9与玻璃微管夹持器8匹配安装;
所述三维微操台为选择的精度为0.5um,行程大于15mm的三维操纵台,其控制电机采用5相步进电机,电机与步进电机驱动器和控制器连接,受整机控制系统的控制;
所述第一三维微操台与纳米操控台匹配安装,并控制纳米薄膜芯片窗口位于显微镜的焦面位置,控制纳米薄膜芯片与玻璃微管尖端的相对位置;
所述第二三维微操台与玻璃微管夹持器匹配安装,控制玻璃微管位于纳米薄膜芯片窗口的具体位置,控制精度为0.5um。
(4)搭建能实时观察纳米薄膜芯片窗口的显微镜系统;
所述显微镜系统包括显微镜光源5,显微镜6两个部分;
所述光源5为普通白光光源,具有光斑大小调节和亮度调节功能;
所述显微镜6包括目镜,镜筒和数码相机,其中目镜选用长工作距离的2~28x的可调焦目镜;所述数码相机采用高分辨率的数码相机,其与物镜结合后可以达到1000x的放大倍数;所述显微镜光源,纳米薄膜平面与显微镜目镜构成反射光路,可实现同时清晰观察玻璃微管尖端与纳米薄膜窗口;
(5)采用玻璃微管拉制仪,如sutter-2000等,拉制玻璃微管7,所述玻璃微管采用玻璃毛细管拉制的,其尖端内径为200nm~3um;如图2所示,所述玻璃毛细管的管径根据需求进行选择;所述玻璃微管的拉制采用suter-97或者suter-2000等拉制仪拉制,通过控制拉制参数实现尖端内外径的控制;所述玻璃微管需要注入缓冲溶液并保证导通;所述玻璃微管也可以直接采用stm针尖或者其他微纳导电针尖代替;
(6)根据玻璃微管的尺寸,制造可拆卸的v型结构的玻璃微管夹持器8,并设计有与第二三维微操台衔接的安装螺丝孔,玻璃微管夹持器8选用铝合金或者pmma等硬质塑料;
所述玻璃微管夹持器8用于夹持玻璃微管8,方便玻璃微管的固定与玻璃微管内电极的固定;所述玻璃微管夹持器8与第二三维微操台9匹配安装,并最终实现精确控制玻璃微管在纳米薄膜窗口上的具体位置,其接近方向的精度控制到nm级,另外两个维度的精度分别达到0.5um;
(7)根据整机仪器的尺寸(500mm*700mm*500mm),制造长方体壳的铝合金屏蔽罩10;所述屏蔽罩具有电磁屏蔽和光屏蔽的作用,屏蔽外界环境对系统带来的电磁干扰以及光干扰;
(8)组建iv扫描模块11;所述iv扫描模块可选用成熟的商用的宽范围高精度的源表;也可以选用高精度的电源表和pa表;还可以根据需求自行设计;
所述的iv扫描模块可以提供精度为0.1pa的恒定电流输出,输出功率大于42w,所述恒定电流输出模式下可以灵活设置限定电压,即输出功率可控。
(9)采用labview等软件系统,结合各模块控制器,构建控制系统12;控制系统包括微米操纵台控制,纳米操控台控制,iv模块控制和其他外围接口控制等;具体操作流程根据具体的实施流程设计。
所述微米操纵台控制系统包括:控制装置,运动控制卡(插入电脑pci卡槽),步进电机驱动器,步进电机和微米操纵台机械结构及传感器。控制流程为:通过设置移动位移,通过运动控制卡装置包发送命令,运动控制卡接收命令后向步进电机驱动器发送脉冲,进而控制步进电机转动,转动的位置经传感器实时反馈回运动控制卡,构成闭环控制系统,控制精度为0.5um。
所述纳米操控台控制系统包括:控制装置,压电陶瓷控制器,压电陶瓷结构和传感器。控制流程为:根据需求在装置控制装置中设置参数,将参数发送给压电陶瓷控制器,压电陶瓷控制器接收命令并把相应命令转化为控制压电陶瓷位置的电压,进而实现纳米级的运动,运动位移通过电容传感器实时检测并反馈给压电控制器,构成闭环控制系统,控制精度为1nm。
本发明样机iv扫描模块采用keithley2450源表搭建,通过设置扫描参数,控制keithley2450源表进行iv扫描。纳米孔加工过程中,通过设置打孔电流和打孔电压,结合纳米操控系统进行纳米孔制备。
下面以在氮化硅薄膜上自动加工阵列纳米孔为例:来描述纳米孔的制备方法,如图6所示,纳米孔的制备方法分为两个步骤:开机准备工作和自动化制备。
开机准备工作:
(1)开机准备:准备氮化硅薄膜芯片,并将薄膜芯片安装在缓冲池上,加入缓冲溶液;在玻璃微管中注入缓冲溶液,并将该玻璃微管安装在玻璃微管夹持器上;连接好缓冲池溶液和玻璃微管溶液的电极;调节玻璃微管位置和薄膜芯片位置,使其位于显微镜视场下,并能进行实时观察。
(2)位置初定位:通过系统上的微调按钮,调节两个三维微操台,将玻璃微管调节至需要加工纳米孔的xy坐标位置,当需要加工阵列纳米孔时,选择第一个纳米孔的xy坐标位置;调节两个三维微操台,使得玻璃微管位于薄膜芯片xy坐标平面的上方4um以内。
(3)打孔参数设置:如果该类型的薄膜是第一次在该平台上制备纳米孔时,需要对纳米薄膜的耐压性能进行测试,扫描出图3中的iv曲线图,再根据图3中的iv曲线设置打孔电流和打孔电压值,并将该类型的打孔参数存入薄膜材料性能list里,供该类型的纳米薄膜打孔使用;如果不是第一次使用,即可以在薄膜材料list里面直接选择相应类型的参数;设置需要加工的目标孔径参数值;设置使用缓冲溶液的电导率值。
自动化制备:参数设置完成后,点击开始按钮程序即进入自动运行状态,自动运行的过程又分为玻璃微管逼近自动控制;纳米孔成孔判断;纳米孔孔径判断;纳米孔孔径扩展;纳米孔阵列制备5个阶段,其流程如图5所示。
(1)玻璃微管逼近自动控制:该部分采用纳米操控台控制,控制玻璃微管尖端溶液逐渐逼近纳米薄膜,采用电压检测法实时检测相对位移,当产生接触突变时及时停止逼近;
(2)纳米孔成孔判断:玻璃微管与纳米薄膜接触的瞬间,通过z-score打分机制判断纳米孔是否形成,即是否产生电压的突变现象。通过计算z-score的值与系统预设值(通常设置为10)进行比较,当计算值大于预设值时,表明纳米孔形成。
(3)判断纳米孔孔径:利用如图4中所示的iv曲线测试纳米孔的孔径,并与设置的目标孔径进行比较,当小于目标孔径时进入孔径扩展程序;当等于或大于目标孔径时则进入下一个纳米孔的制备周期或者结束制备;
(4)纳米孔孔径扩展:实时计算纳米孔孔径值与目标孔径值的差值,通过该差值计算对应的扩孔时间和扩孔电压,该孔径差值和扩孔时间和扩孔电压的对应关系用pid算法进行计算,使得扩孔时间和扩孔电压更加细化,大大的提高了纳米孔的加工精度;当纳米孔孔径扩展到目标孔径后,进入下一个纳米孔的制备周期或者结束制备;
(5)纳米孔阵列制备:当完成上一个纳米孔的制备后,自动导入下一个纳米孔的xy位置参数和目标孔径参数,开始下一个纳米孔的制备,直到完成所有纳米孔的制备工作,结束打孔程序。
本发明具有如下的特点:
该自动精确制备固态纳米孔的系统包括纳米薄膜芯片1,缓冲池2,纳米操控台3,第一三维微操控平台4,光源5,显微镜6,玻璃微管7,玻璃微管夹持器8,第二三维微操控平台9,法拉第屏蔽罩10,iv扫描模块11及控制系统12几个部分。该系统采用纳米操控玻璃微管精确定位制备纳米孔,使得纳米孔的位置精确可控;采用z-score打分作为打孔的判据,大大提高了成孔效率,并且为制备小孔径纳米孔提供了可能;纳米孔的扩孔程序采用pid等控制算法控制扩孔电压和扩孔时间的变化,提高了打孔效率和孔径精度;整个纳米孔制备过程采用原位在线的方式,与后期纳米孔测试无缝链接。
更进一步地,本发明采用纳米操控玻璃微管精确定位制备纳米孔,使得纳米孔的位置可控,纳米孔的位置精度为1um。
采用限电压方式打孔,采用z-score打分机制作为成孔判据,将纳米孔初次成孔时间缩短到300ms以内,并为制备小孔径纳米孔提供了可能,可制备低于1nm的固态纳米孔;
纳米孔扩孔程序采用pid算法控制,大大的提高了打孔精度,纳米孔制备精度高达0.3um;
原位精确纳米孔阵列自动化制备,即实现了程序自动化。
所述的纳米操控系统以玻璃微管尖端与纳米薄膜直接的距离为控制对象,以实时检测到的电压信号作为反馈信号,构建具有100nm控制精度的纳米操控系统。
所述z-score打分依据为统计算法z-score统计算法,其计算公式如下:
其中,μ为前多项(申请人选择10项)测试数据的平均值,σ为前多项测试数据的标准差。x为当前测试数据,通过以上公式计算出z-score的数值,进而表征变化的大小,用于纳米孔形成的判据。
更进一步地,图2是本发明中使用的玻璃微管的实物图片和电镜图片,分为尖端为1um(b)和尖端为0.3um(s)两种尺寸,其拉制参数如下:pipette-b1、b2拉制参数:p=200,heat=529,pull=30,vel=40,time=250,pipette-s1、s2拉制参数:p=200,heat=530,pull=80,vel=70,del=80;所采用的拉制仪器为sutter-97光纤拉制仪。两种类型pipette均适用于本发明的纳米孔加工需求。
图3是采用kcl和licl两种溶液在厚度为10nm,开窗面积为130um*100um氮化硅薄膜(m1)上进行iv扫描(各3次)的iv曲线图。该图证明了同一电流下,两种溶液所形成的测量电压是不同的,即要达到同样的击穿电场,licl溶液需要设置更大的电流。进一步的,该图可以扫描到薄膜击穿的电场临界值,就氮化硅而言是1v/nm,这也是其他电击穿法加工纳米孔的临界值,即其他方法均在该值以下加工。而本发明采用的限电压瞬间接触法可以将加工电场设置到5v/nm,并且能加工孔形较好的纳米孔。这是在已有技术中从未见过公开报道的。
图4是本发明制备完成的纳米孔的iv曲线图,该图是采用两种尺寸的4根(b1,b2,s1,s2)玻璃微管与不加玻璃微管直接测试4.5nm纳米孔孔径的曲线图。证明了该系统中通过玻璃微管测试纳米孔孔径是靠近于真实的纳米孔孔径值的,可以直接用于纳米孔加工的实时反馈信号,进而构建自动化的纳米孔阵列加工系统。
图5是本发明制备完成的纳米孔的iv曲线图,该图是采用膜片钳系统axon200b测试的iv曲线,根据膜厚,电导率等参数计算出纳米孔的孔径为0.4nm,证明了本发明可以加工低于1nm的固态纳米孔。具体加工情况:使用尖端直径为1um的b1玻璃微管加工纳米孔,打孔电压20v,膜厚20nm,缓冲溶液参数为:1mlicl:ph=9.04电导率=6.54s/m,计算得知该纳米孔孔径为0.4nm。
图6是本发明自动化制备纳米孔的装置系统的设计流程图。纳米孔的制备方法分为两个步骤:开机准备工作和自动化制备。
开机准备工作:
(1)开机准备:准备氮化硅薄膜芯片,并将薄膜芯片安装在缓冲池上,加入缓冲溶液;在玻璃微管中注入缓冲溶液,并将该玻璃微管安装在玻璃微管夹持器上;连接好缓冲池溶液和玻璃微管溶液的电极;调节玻璃微管位置和薄膜芯片位置,使其位于显微镜视场下,并能进行实时观察。
(2)位置初定位:通过系统上的微调按钮,调节两个三维微操台,将玻璃微管调节至需要加工纳米孔的xy坐标位置,当需要加工阵列纳米孔时,选择第一个纳米孔的xy坐标位置;调节两个三维微操台,使得玻璃微管位于薄膜芯片xy坐标平面的上方4um以内。
(3)打孔参数设置:如果该类型的薄膜是第一次在该平台上制备纳米孔时,需要对纳米薄膜的耐压性能进行测试,扫描出图3中的iv曲线图,再根据图3中的iv曲线设置打孔电流和打孔电压值,并将该类型的打孔参数存入薄膜材料性能list里,供该类型的纳米薄膜打孔使用;如果不是第一次使用,即可以在薄膜材料list里面直接选择相应类型的参数;设置需要加工的目标孔径参数值;设置使用缓冲溶液的电导率值。
自动化制备:参数设置完成后,点击开始按钮程序即进入自动运行状态,自动运行的过程又分为玻璃微管逼近自动控制;纳米孔成孔判断;纳米孔孔径判断;纳米孔孔径扩展;纳米孔阵列制备5个阶段,其流程如图5所示。
(1)玻璃微管逼近自动控制:该部分采用纳米操控台控制,控制玻璃微管尖端溶液逐渐逼近纳米薄膜,采用电压检测法实时检测相对位移,当产生接触突变时及时停止逼近;
(2)纳米孔成孔判断:玻璃微管与纳米薄膜接触的瞬间,通过z-score打分机制判断纳米孔是否形成,即是否产生电压的突变现象。通过计算z-score的值与系统预设值(通常设置为10)进行比较,当计算值大于预设值时,表明纳米孔形成。
(3)判断纳米孔孔径:利用如图4中所示的iv曲线测试纳米孔的孔径,并与设置的目标孔径进行比较,当小于目标孔径时进入孔径扩展程序;当等于或大于目标孔径时则进入下一个纳米孔的制备周期或者结束制备;
(4)纳米孔孔径扩展:实时计算纳米孔孔径值与目标孔径值的差值,通过该差值计算对应的扩孔时间和扩孔电压,该孔径差值和扩孔时间和扩孔电压的对应关系用pid算法进行计算,使得扩孔时间和扩孔电压更加细化,大大的提高了纳米孔的加工精度;当纳米孔孔径扩展到目标孔径后,进入下一个纳米孔的制备周期或者结束制备;
(5)纳米孔阵列制备:当完成上一个纳米孔的制备后,自动导入下一个纳米孔的xy位置参数和目标孔径参数,开始下一个纳米孔的制备,直到完成所有纳米孔的制备工作,结束打孔程序。
所述系统的电场设置范围在0.85v/nm~5v/nm的宽范围氮化硅纳米孔制备方法,并将单孔制备时间控制在300ms以内。这是现有其他电击穿法打孔系统做不到的。
本发明未详细阐述部分属于本领域技术人员的公知技术。以上所述仅为本发明的较佳实施例,并不用以限制本发明,凡在本发明的精神和原则之内,所做的任何修改、等同替换、改进等,均应包含在本发明的保护范围之内。
本文用于企业家、创业者技术爱好者查询,结果仅供参考。