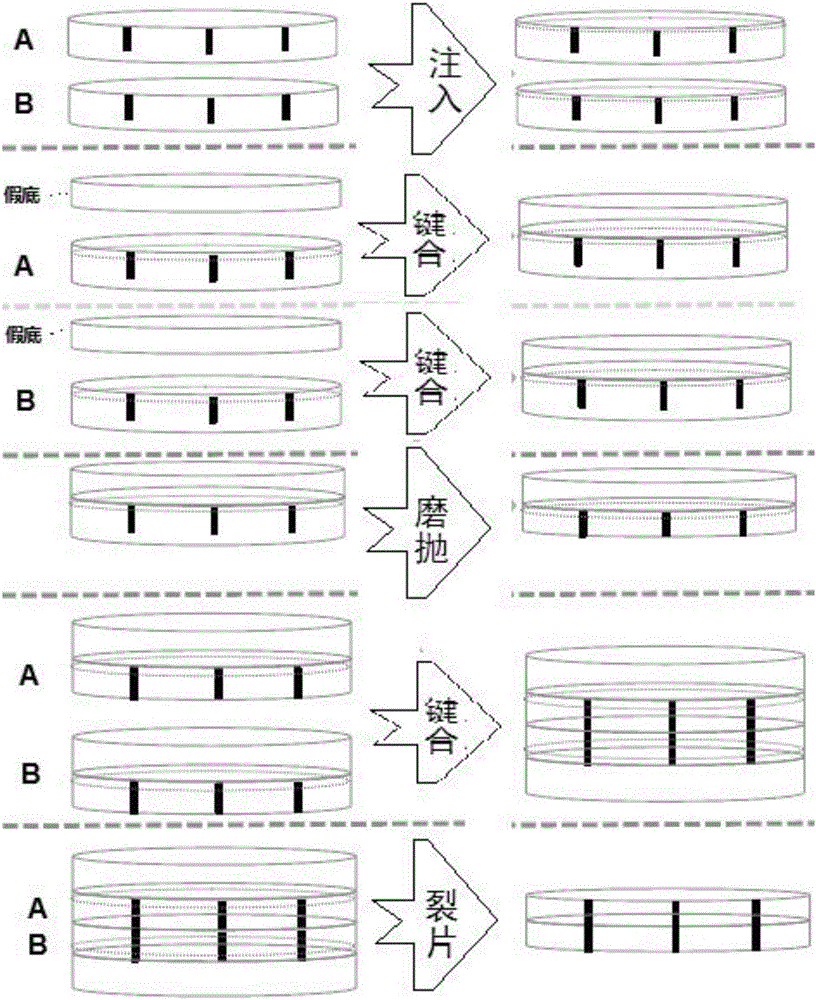
本发明涉及硅片加工技术领域,特别提供了一种贯穿空腔结构硅片的加工方法。
背景技术:
随着mems技术的蓬勃发展,产生出愈来愈多的mems新结构需求,但受加工硬件设备的制约,许多结构面临着无法被制造的窘境。在硬件无法满足要求的情况下就需要工程技术人员开发出新的技术克服这种尴尬的矛盾。
贯穿空腔的mems就是特殊结构中的一种。区别普通mems空腔在最终结构中被埋在硅片之中,贯穿空腔需要最终暴露在外,当前硅片加工的设备大部分使用真空抓取和加工硅片,贯穿硅片整体的空腔将破坏真空,直接影响设备完成动作,例如常规加工最终需要使用磨抛机进行两次研磨将原本在图形片中未漏出的部分完全暴露出来形成贯穿结构,但在第二次研磨时图形的干扰会影响真空的密封,打通空腔后真空被彻底破坏,磨抛机台不能在固定硅片也无法传递硅片,造成研磨不能按要求完成加工甚至危害机台。
为处理贯穿空腔带来的漏真空问题,我们开发出一种假底植入剥离的mems加工技术,用来解决漏真空和剥离最终结构不需要的假底。假底植入剥离技术由键合技术,离子注入技术和微波裂片技术构成。假底在形成最终结构之前起到封装空腔避免漏真空的发生,通过键合技术在常温或高温的温场和常压或真空的气压环境下,将普通硅片与图形片键合为一片实现对图形空腔的封装。由于假底是不被需要的部分,最终需要从最终结构中剥离,假底的剥离是通过键合前对普通硅片或图形片进行离子注入的预处理,常用氢离子氦原子最为分离用注入剂,最后通过微波裂片技术,提高注入离子的动能使离子发生汇聚产生小气泡,小气泡受硅片的挤压将倾向沿着键合面方向运动,小气泡汇聚在注入层形成完整的大气泡,是假底与主体结构形成宏观的分离,实现假底被剥离的效果,贯穿结构不需要研磨机实现。
技术实现要素:
本发明的目的是提供一种技术效果优良的贯穿空腔结构硅片的加工方法。
本发明提供了一种贯穿空腔结构硅片的加工方法,其特征在于:其依次按照下述要求进行操作:
①对硅片或图形片进行离子注入;步骤①的处理是为了假底在最后可以通过微波裂片技术被剥离进行预处理;
②植入假底,使用硅片与图形片键合;被键合的硅片即为假底,在以后步骤中起到密封图形,保证机台能够加工的作用;步骤②通过硅片直接键合技术,实现假底引入的目的;
②通过机械研磨或/和化学抛光方法进行磨抛,以被键合的硅片即假底为衬底,减薄图形片,研磨到露出图形的深度,暴露出原本未露出的空腔;磨抛使用机械研磨和化学抛光可以将硅片加工到设计需求的指定厚度及优良粗糙度,保证后续过程使用的是状态优良的表面;
③键合,将完成①②两步骤的两片硅片,进行图形对图形的键合;假底处于整体结构上、下两侧;
④剥离假底,通过低温退火和微波裂片操作将完成保护作用的假底剥离掉,实现贯穿结构的硅片。退火可以同时提升键合界面的键合力,保证图形键合界面优良的键合状态保证后续使用的可靠性。退火处理有助于增强图形图形键合界面的键合力,避免形成贯穿结构后在进行设备上的加工又产生漏真空问题;微波裂片是通过微波增加离子的动能,运动的离子彼此碰撞汇聚形成小气泡,硅片的挤压将限制气泡在垂直键合界面方向的运动,更倾向沿键合界面方向运动,小气泡因此汇聚成大气泡,最终在注入层形成硅片的分离,假底被剥离出主体结构。
步骤③是步骤④的预处理,目的是将两片图形片的空腔连接到一起做准备。磨抛使用机械研磨和化学抛光可以将硅片加工到设计需求的指定厚度及优良粗糙度,保证后续过程使用的是状态优良的表面。
所述贯穿空腔结构硅片的加工方法,优选内容要求是:
对硅片或图形片进行离子注入的要求是:注入深度在距表面1μm~0.001μm范围内;氢离子注入的参数要求是:10~120kev能量,1e15~9e16剂量,1-20ma束流;通过参数控制可以保证经过注入的硅片表面状态良好,对后段加工没有影响;
使用硅片与图形片键合的具体要求是:硅片的粗糙度小于等于5nm;使用硅片与图形片直接接触,借助于二者表面的分子间作用力实现将两者结合为一体。
硅片与图形片键合使用等离子增强的直接键合方法。具体地:使用一枚普通硅片与图形片进行0~90s的等离子增强,将普通硅片与带图形的表面进行键合,普通硅片即为假底。
随着工业多键合力及降低热预算的需求,后续发展出等离子增强的直接键合技术,可以实现更快的加工速度和更低后续退火温度。
剥离假底时对键合片进行退火处理的温度要求是:150~450℃。
对硅片或图形片进行离子注入之前进行下述操作:对图形片进行化学湿法清洗,去除沾污,以降低金属和有机物污染;然后进行氧化处理,在800-1150℃下在图形片的正背面、边缘和空腔内均匀生长0.1-0.5μm厚度的氧化层;
使用微波裂片技术将两侧的假底剥离之后,对具有贯穿空腔结构的硅片使用hf进行氧化层的去净漂洗,去除分离界面,形成表面状态优良的表面。
相对于现有技术而言,本发明操作规范,产品质量能够得到有效保证;且产品的性价比高,综合技术效果优良;其具有可预期的较为巨大的经济价值和社会价值。
附图说明:
图1为贯穿空腔结构硅片的加工方法原理示意简图。
具体实施方式:
实施例1
一种贯穿空腔结构硅片的加工方法,其依次按照下述要求进行操作:
①对硅片或图形片进行离子注入;步骤①的处理是为了假底在最后可以通过微波裂片技术被剥离进行预处理;
②植入假底,使用硅片与图形片键合;被键合的硅片即为假底,在以后步骤中起到密封图形,保证机台能够加工的作用;步骤②通过硅片直接键合技术,实现假底引入的目的;
②通过机械研磨或/和化学抛光方法进行磨抛,以被键合的硅片即假底为衬底,减薄图形片,研磨到露出图形的深度,暴露出原本未露出的空腔;磨抛使用机械研磨和化学抛光可以将硅片加工到设计需求的指定厚度及优良粗糙度,保证后续过程使用的是状态优良的表面;
③键合,将完成①②两步骤的两片硅片,进行图形对图形的键合;假底处于整体结构上、下两侧;
④剥离假底,通过低温退火和微波裂片操作将完成保护作用的假底剥离掉,实现贯穿结构的硅片。退火可以同时提升键合界面的键合力,保证图形键合界面优良的键合状态保证后续使用的可靠性。退火处理有助于增强图形图形键合界面的键合力,避免形成贯穿结构后在进行设备上的加工又产生漏真空问题;微波裂片是通过微波增加离子的动能,运动的离子彼此碰撞汇聚形成小气泡,硅片的挤压将限制气泡在垂直键合界面方向的运动,更倾向沿键合界面方向运动,小气泡因此汇聚成大气泡,最终在注入层形成硅片的分离,假底被剥离出主体结构。
步骤③是步骤④的预处理,目的是将两片图形片的空腔连接到一起做准备。磨抛使用机械研磨和化学抛光可以将硅片加工到设计需求的指定厚度及优良粗糙度,保证后续过程使用的是状态优良的表面。
对硅片或图形片进行离子注入的要求是:注入深度在距表面1μm~0.001μm范围内;氢离子注入的参数要求是:10~120kev能量,1e15~9e16剂量,1-20ma束流;通过参数控制可以保证经过注入的硅片表面状态良好,对后段加工没有影响;
使用硅片与图形片键合的具体要求是:硅片的粗糙度小于等于5nm;使用硅片与图形片直接接触,借助于二者表面的分子间作用力实现将两者结合为一体。
硅片与图形片键合使用等离子增强的直接键合方法。具体地:使用一枚普通硅片与图形片进行0~90s的等离子增强,将普通硅片与带图形的表面进行键合,普通硅片即为假底。随着工业多键合力及降低热预算的需求,后续发展出等离子增强的直接键合技术,可以实现更快的加工速度和更低后续退火温度。
剥离假底时对键合片进行退火处理的温度要求是:150~450℃。
对硅片或图形片进行离子注入之前进行下述操作:对图形片进行化学湿法清洗,去除沾污,以降低金属和有机物污染;然后进行氧化处理,在800-1150℃下在图形片的正背面、边缘和空腔内均匀生长0.1-0.5μm厚度的氧化层;
使用微波裂片技术将两侧的假底剥离之后,对具有贯穿空腔结构的硅片使用hf进行氧化层的去净漂洗,去除分离界面,形成表面状态优良的表面。
相对于现有技术而言,本实施例操作规范,产品质量能够得到有效保证;且产品的性价比高,综合技术效果优良;其具有可预期的较为巨大的经济价值和社会价值。
实施例2
一种贯穿空腔结构硅片的加工方法,其依次按照下述要求进行操作:
①对图形片进行化学湿法清洗,去除沾污,降低金属和有机物污染,然后进行氧化处理,在800-1150℃下在图形片的正背面,边缘,和空腔内均匀生长0.1-0.5μm厚度的氧化层。
②对图形片进行10~120kev能量,1e15~9e16剂量,1-20ma束流的氢离子注入。
③使用一枚普通硅片与图形片进行0~90s的等离子增强,将普通硅片与带图形的表面进行键合,普通硅片即为假底。
④将完成步骤③的键合片,对图形片的进行研磨,以假底为衬底,减薄图形片,研磨到露出图形的深度。
⑤将完成步骤④的两片进行0~90s的等离子增强的键合,密封露出的图形,假底出于整体结构上下两侧。
⑥对完成步骤⑤的键合片进行150~450℃的退火处理,增强图形图形键合界面的键合力,避免形成贯穿结构后在进行设备上的加工又产生漏真空问题。
⑦使用微波裂片技术将两侧的假底剥离。
⑧对具有贯穿空腔结构的硅片使用hf进行氧化层的去净漂洗,去除分离界面,形成表面状态优良的表面。
本文用于企业家、创业者技术爱好者查询,结果仅供参考。