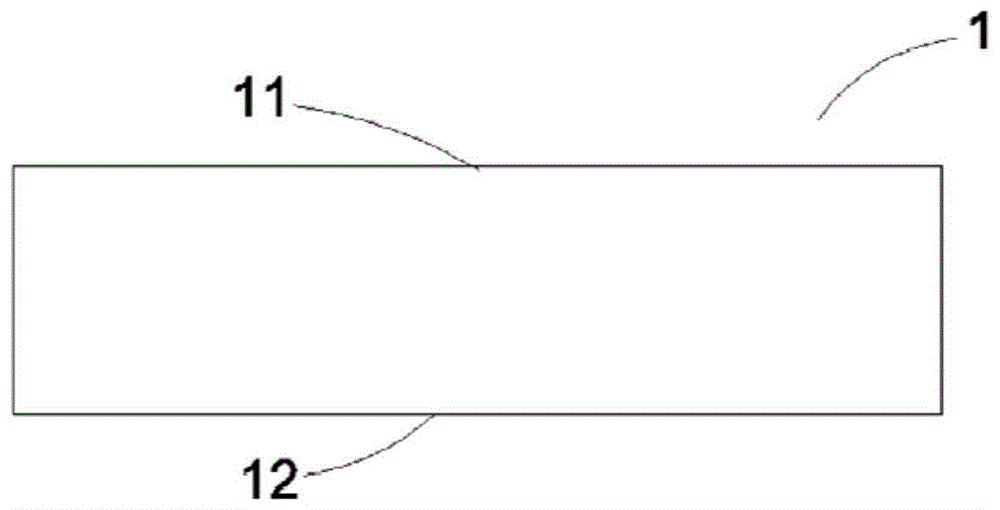
本发明涉及微电子机械系统领域,尤其涉及一种压力传感器及其制造方法。
背景技术:
随着微机电系统技术的不断发展,压力传感器的成本在逐渐减小,压力传感器的应用也已经进入医疗、汽车、气象检测、高度测量、消费电子等众多领域。常用的压力传感器有电容式、压电式、压阻式三种,其中压阻式压力传感器的工艺较为简单,适合批量生产,是压力传感器发展的主流方向。
压阻式压力传感器的感压薄膜是最关键的结构,目前常用于制备压阻式感压薄膜的方法有以下几种。一种是采用碱性溶液各向异性腐蚀的硅片背面的方法,该方法通过时间控制得到背腔的同时也得到一定厚度的感压薄膜,但采用该方法不能保证整片晶圆腐蚀的均匀性,因而很难获得平整度较高的感压薄膜。第二种是电化学腐蚀,该方法需要昂贵的恒电位仪,生产成本较高。第三种是:采用c-soi工艺,先在一片si晶圆(称晶圆1)的正面刻蚀出压力腔外形的凹槽;然后,在另一片si晶圆(称晶圆2)上双面沉积氧化硅,将晶圆1的正面与晶圆2任意一面进行si-sio2键合;减薄晶圆2使其达到一定厚度,进而得到悬空薄膜,同时得到封闭的压力腔;若用于制备表压传感器,则通过深反应离子刻蚀的方式刻蚀晶圆1的背部,使得压力腔与外界连通。这种方法得到的薄膜厚度较大,用于制备小量程压力传感器生产成本较高。
因此,如何获得制造成本低、厚度更薄、平整度更高的感压薄膜成为亟待本领域解决的技术问题。
技术实现要素:
本发明所要解决的技术问题是降低压力传感器的感压薄膜的制造成本,提高感压薄膜的平整度,降低感压薄膜的厚度。
为了解决上述问题,本发明提供了一种压力传感器的制造方法,其包括:提供衬底;在所述衬底的表面形成若干间隔排列的第一孔;进行第一热处理,使得若干所述第一孔合并成悬空的第一真空腔;形成与所述第一真空腔连通的沟槽以及由所述沟槽环绕的感应本体。
可选地,所述第一热处理为快速热退火。
可选地,所述第一热处理的温度不小于1100摄氏度。
可选地,还包括:通过外延工艺形成覆盖所述衬底的器件层。
可选地,还包括:在所述器件层的表面形成若干间隔排列的第二孔;进行第二热处理,使得若干所述第二孔合并成悬空的第二真空腔,所述第二真空腔位于所述感应本体内。
可选地,所述第二热处理为快速热退火。
可选地,所述第二热处理的温度不小于1100摄氏度。
可选的,所述第二孔的直径为0.5微米~1.5微米,所述第一孔的直径为0.5微米~1.5微米。
可选地,所述第二真空腔位于所述第一真空腔的正上方。
可选地,所述沟槽为具有缺口的环状;所述沟槽的数量为两个,分别为第一、二沟槽,所述第一沟槽环绕在所述第二沟槽的外侧,且所述第一沟槽的缺口与第二沟槽的缺口呈180度间隔设置。
另外,本发明还提供了一种压力传感器,其包括:半导体衬底;位于所述半导体衬底内的悬空的第一真空腔,所述第一真空腔由若干间隔排列的第一槽经第一热处理合并而成;位于所述半导体衬底内的沟槽,所述沟槽穿过部分半导体衬底直至与所述第一真空腔连通,所述沟槽与第一真空腔围成感应本体。
可选地,所述半导体衬底包括衬底和位于所述衬底上的器件层,所述器件层为外延层。
可选地,所述器件层内具有悬空的第二真空腔,所述第二真空腔位于所述感应本体内,并由若干间隔排列的第二槽经第二热处理合并而成。
可选地,所述第二真空腔位于所述第一真空腔的正上方。
可选地,所述第二热处理为快速热退火。
可选地,所述沟槽为具有缺口的环状;所述沟槽的数量为两个,分别为第一、二沟槽,所述第一沟槽环绕在所述第二沟槽的外侧,且所述第一沟槽的缺口与第二沟槽的缺口呈180度间隔设置。
可选地,所述第一热处理为快速热退火。
本发明先在衬底的表面形成若干间隔排列的第一孔,再对衬底进行第一热处理,使得若干第一孔合并成悬空的第一真空腔且第一孔之间的部分结合在一起形成感压薄膜(也成为悬空薄膜),简化了感压薄膜的制造工艺。与此同时,通过这种热处理工艺形成的感压薄膜平整度高、厚度较薄,可以薄至1微米。再者,经热处理工艺形成的第一真空腔的侧壁比较平滑,边角均为圆角,使得感压薄膜基本无应力存在。
进一步地,在进行第一热处理之后,可以通过外延工艺在衬底上形成器件层,该器件层的材料与感压薄膜的材料相同,可以作为感压薄膜的一部分。由于该器件层的厚度很容易控制,故压力传感器的感压薄膜的整体厚度可以在较大范围内调整。
附图说明
图1至图15是本发明的一实施例中压力传感器在不同制造阶段的截面图;
图16是本发明的一实施例中压力传感器的平面图。
具体实施方式
下面结合附图先对本发明提供的压力传感器制造方法的具体实施方式做详细说明。
如图1所示,提供衬底1,衬底1包括上表面11和下表面12。在本实施例中,衬底1为单晶硅衬底。当然,在其他实施例中,衬底1也可以选用其他合适的半导体材料。
如图2所示,在衬底1的上表面上形成具有若干图形14(即为窗口)的保护层13。保护层13的制造方法包括:采用低压化学气相沉积、等离子体化学气相沉积或热氧化等工艺在衬底1的上表面形成保护材料层(未图示)之后,然后采用光刻和湿法腐蚀工艺,或者光刻和干法刻蚀工艺去除部分保护材料层,形成具有图形14的保护层13。该具体实施方式中,保护层13的材料为氧化硅,在本发明的其他具体实施方式中,保护层13的材料还可以为氮化硅、碳化硅、氮氧化硅等介质材料,可以为单层或多层复合结构。
如图3所示,以保护层13为掩膜,刻蚀衬底1,在衬底1内形成若干第一孔15。由于第一孔15位于衬底1的表面,故也可以将其称之为第一槽。该具体实施方式中,采用各向异性刻蚀工艺,例如深反应离子硅刻蚀(drie)工艺,刻蚀衬底1得到若干第一孔15,定义相邻两第一孔15之间的部分为图形15a。在本实施例中,若干第一孔15呈阵列排布,第一孔15为圆孔,该圆孔的深度为几微米,直径约为0.5微米~1.5微米,例如可以为1微米,各个圆孔之间的间隔约为0.5微米。当然,在其他实施例中,第一孔15也可以设置为其他形状的孔,该孔可以是矩形、圆形、五边形、六边形或其他多边形,第一孔的尺寸以及间隔可以根据光刻机的光刻能力做出相适应调整。
如图4所示,去除保护层13。在具体实施例中,采用干法刻蚀或湿法腐蚀工艺,如用缓冲氢氟酸(boe)去除保护层13。
如图5所示,对衬底1进行第一热处理,使得若干第一孔15(参考图4)合并成悬空的第一真空腔16,所谓悬空是指第一真空腔16位于衬底1的内部,与衬底1的上表面11存在一定的间隔。衬底1中位于上表面11与第一真空腔16之间的部分定义为第一悬空薄膜17。
结合图4至图5所示,在所述第一热处理的作用下,第一孔15会沿水平方向扩大,使得各个第一孔15之间相互连通,从而合并为一个完整的大孔,即为第一真空腔16。与此同时,在所述第一热处理的作用下,衬底1的上表面能量降低,使得衬底1的上表面发生迁移,各个图形15a的端部得以相互结合为一个整体,从而在第一真空腔16的上方形成第一悬空薄膜17。通过该第一热处理工艺形成的第一悬空薄膜17很平整,且厚度较薄,可以薄至1微米。在具体实施例中,第一真空腔16位于衬底1内部的中心偏上位置。而且,利用第一热处理工艺形成的第一真空腔16的侧壁比较平滑,且如图5所示,第一真空腔16的边角均为圆角,使得第一悬空薄膜17基本无应力存在。由于真空腔与悬空薄膜利用热处理工艺形成,避免了传统的体硅刻蚀、牺牲层刻蚀、晶圆键合所带来的一系列不良影响。
具体的,所述第一热处理在不含氧、低压(低于大气压)的环境下进行,以防止衬底1被氧化。在一实施例中,该不含氧的环境为纯氢气环境。当然,在其他实施例中,该不含氧的环境也可以为惰性气体环境。所述第一热处理的环境压强可以小于1个大气压,使得形成的第一真空腔16内气压小于1个大气压。
在本实施例中,所述第一热处理的温度1100摄氏度。当然,在其他实施例中,所述第一热处理的温度也可以高于1100摄氏度。进一步的,在本实施例中,所述第一热处理为快速热退火。
如图6所示,通过外延工艺形成覆盖衬底1的器件层18。由于采用外延工艺,故器件层18的材料与衬底1的材料相同,在本实施例中,器件层18的材料为单晶硅。
如图7所示,在器件层18上形成具有若干图形20(即为窗口)的保护层19。保护层19的制造方法包括:采用低压化学气相沉积、等离子体化学气相沉积或热氧化等工艺在器件层18的上表面形成保护材料层(未图示)之后,然后采用光刻和湿法腐蚀工艺,或者光刻和干法刻蚀工艺去除部分保护材料层,形成具有图形20的保护层19。该具体实施方式中,保护层19的材料为氧化硅,在本发明的其他具体实施方式中,保护层19的材料还可以为氮化硅、碳化硅、氮氧化硅等介质材料,可以为单层或多层复合结构。
如图8所示,以保护层19为掩膜,刻蚀具有器件层18的衬底1,在衬底1内形成若干第二孔21。由于第二孔21位于器件层18的表面,故也可以将第二孔21称之为第二槽。该具体实施方式中,采用各向异性刻蚀工艺,例如深反应离子硅刻蚀(drie)工艺,刻蚀衬底1得到若干第二孔21,定义相邻两第二孔21之间的部分为图形21a。在本实施例中,若干第二孔21呈阵列排布,第二孔21为圆孔,该圆孔的深度为几微米,直径可以为0.5微米~1.5微米,例如可以为1微米,各个圆孔之间的间隔约为0.5微米。当然,在其他实施例中,第二孔21也可以设置为其他形状的孔,该孔可以是矩形、圆形、五边形、六边形或其他多边形。进一步的,在本实施例中,若干第二孔21均位于第一真空腔16的正上方。
如图9所示,去除保护层19。在具体实施例中,采用干法刻蚀或湿法腐蚀工艺,如用缓冲氢氟酸(boe)去除保护层19。
如图10所示,对衬底1进行第一热处理,使得若干第二孔21(参考图9)合并成悬空的第二真空腔7,所谓悬空是指第二真空腔7位于具有器件层18的衬底1的内部,与器件层18的上表面存在一定的间隔。器件层18的上表面11与第二真空腔7之间的部分定义为第二悬空薄膜8(也称之为感压薄膜)。在本实施例中,第二真空腔7位于第一真空腔16的正上方,且第二真空腔7的宽度(水平方向尺寸)小于第一真空腔16的宽度。
结合图9至图10所示,在所述第二热处理的作用下,第二孔21会沿水平方向扩大,使得各个第二孔21之间相互连通,从而合并为一个完整的大孔,即为第二真空腔7。与此同时,在所述第二热处理的作用下,器件层18的上表面能量降低,使得器件层18的上表面发生迁移,各个图形21a的端部得以相互结合为一个整体,从而在第二真空腔7的上方形成第二悬空薄膜8。通过该第二热处理工艺形成的第二悬空薄膜8很平整,且厚度较薄,可以薄至1微米。而且,利用第一热处理工艺形成的第二真空腔7的侧壁比较平滑,且如图10所示,第二真空腔7的边角均为圆角,第二悬空薄膜8基本无应力存在。
具体的,所述第二热处理在不含氧、低压(低于大气压)的环境下进行,以防止衬底1被氧化。在一实施例中,该不含氧的环境为纯氢气环境。当然,在其他实施例中,该不含氧的环境也可以为惰性气体环境。所述第二热处理的环境压强可以小于1个大气压,使得形成的第二真空腔7内气压小于1个大气压。
在本实施例中,所述第二热处理的温度1100摄氏度。当然,在其他实施例中,所述第二热处理的温度也可以高于1100摄氏度。进一步的,在本实施例中,所述第二热处理为快速热退火。
如图11所示,在器件层18上形成第一介质层23,其作为阻挡层,材料可以为氧化硅、氮化硅、氮氧化硅等,形成工艺可以为低压化学气相沉积、等离子体化学气相沉积或热氧化等工艺。
继续参考图11所示,形成若干压阻10,压阻10位于第二真空腔7的正上方。在本实施例中,压阻10的形成工艺为离子注入,即通过对器件层18表层的特定区域进行离子注入以获得压阻10。
继续参考图11所示,形成覆盖于第一介质层23的第二介质层22。第二介质层22的材料可以为氧化硅、氮化硅、氮氧化硅等,形成工艺可以为低压化学气相沉积、等离子体化学气相沉积或热氧化等工艺。
如图12所示,去除部分第二介质层22和第一介质层23,以形成若干窗口24,各个窗口24露出对应的部分压阻10。窗口24的形成方法为先光刻再进行反应离子刻蚀。
如图13所示,在第二介质层22上形成若干金属电极9,金属电极9的一部分填充至窗口24内并与压阻10形成欧姆接触。在本实施例中,金属电极9的形成方法包括:形成覆盖第二介质层22的金属材料层,该金属材料层的一部分填充至窗口24内,并与下方的压阻10形成欧姆接触;该金属材料层的形成方法可以为淀积或电镀;在该金属材料层的上方形成图形化掩膜层,以该图形化掩膜层为掩膜对该金属材料层进行刻蚀,以形成金属电极9,该刻蚀工艺可以为干法刻蚀或湿法刻蚀,该图形化掩膜层可以为光刻胶层。
如图14所示,在金属电极9上形成一具有图形27的保护层26,保护层26覆盖于第二介质层22之上,图形27位于金属电极9的外围。
保护层26的制造方法包括:采用低压化学气相沉积、等离子体化学气相沉积或热氧化等工艺在第二介质层22和金属电极9的上表面形成保护材料层(未图示)之后,然后采用光刻和湿法腐蚀工艺,或者光刻和干法刻蚀工艺去除部分保护材料层,形成具有图形27的保护层26。该具体实施方式中,保护层26的材料为氧化硅,在本发明的其他具体实施方式中,保护层26的材料还可以为氮化硅、碳化硅、氮氧化硅等介质材料,可以为单层或多层复合结构。
如图15所示,以保护层26为掩膜,刻蚀第二介质层22、第一介质层23至衬底1,以形成沟槽25以及由沟槽25环绕的感应本体6,沟槽25与第一真空腔16连通构成收容腔(未标识)。在本实施例中,该刻蚀工艺为干法刻蚀,具体为深反应离子硅刻蚀(drie)工艺。
具体地,第二真空腔7位于感应本体6内,压阻10和金属电极9均位于感应本体6内。感应本体6由沟槽25以及第一真空腔16围成,并可以沿着垂直于衬底1的方向运动,以在受到外力的作用时发生形变从而根据压阻10的阻值变化检测压力。
结合图15和图16所示,在本实施例中,沟槽25呈具有缺口(未标识)的环状,沟槽25的数量为两个,分别为外侧沟槽和内侧沟槽,其中,外侧沟槽的缺口与内侧沟槽的缺口呈180度间隔设置。更具体的,沟槽25为矩形,其中一条边设置有缺口。衬底1中位于外侧沟槽与内侧沟槽之间的部分构成一支撑梁5,衬底1中位于该沟槽25的缺口的部分也构成另一支撑梁,该两个支撑梁均与感应本体6连接,使得感应本体6可以悬空。
需说明的是,参考图15所示,在本发明的实施例中,沟槽25的数量并不应局限于两个,其数量可以任意设置,例如,沟槽25可以仅为一个。每个沟槽25的缺口数量可以任意设置,例如可以为两个。另外,沟槽25的形状也不应局限于矩形,还可以设置为圆形、五边形、六边形等多边形。
另外,第一真空腔16的数量并不应局限于一个,其还可以为两个,两个第一真空腔16沿水平方向间隔设置,第二真空腔7位于两个第一真空腔16之间,各个第一真空腔均与垂直延伸的沟槽连通,在这种情况下,所有第一真空腔与所有沟槽围成感应本体。
再者,在本实施例的变换例中,形成第一真空腔16之后,可以省略形成器件层、第二真空腔的步骤,直接进行形成压阻、金属电极、沟槽的步骤,依据该变换方法形成的感应本体内没有第二悬空薄膜,根据第一热处理步骤形成的第一悬空薄膜即为感压薄膜。
下面结合附图接着对本发明提供的压力传感器的具体实施方式做详细说明。
如图15所示,该压力传感器包括衬底1。在本实施例中,衬底1为单晶硅衬底。当然,在其他实施例中,衬底1也可以选用其他合适的半导体材料。
衬底1内形成有悬空的第一真空腔16,所谓悬空是指第一真空腔16位于衬底1的内部,与衬底1的上表面(未标识)存在一定的间隔。第一真空腔16由若干间隔排列的第一槽经第一热处理合并而成,该第一槽位于衬底1的表面。换言之,通过先在衬底1的表面形成若干间隔排列的第一槽,再进行第一热处理,可以使得该些第一槽合并成悬空的第一真空腔16。
在所述第一热处理的作用下,该第一槽会沿水平方向扩大,使得各个第一槽之间相互连通,从而合并为一个完整的大孔,即为第一真空腔16。与此同时,在所述第一热处理的作用下,衬底1的上表面能量降低,使得衬底1的上表面发生迁移,各个第一槽之间的部分的端部得以相互结合为一个整体,从而在第一真空腔16的上方形成第一悬空薄膜(未标识)。通过该第一热处理工艺形成的第一悬空薄膜很平整,且厚度较薄,可以薄至1微米。在具体实施例中,第一真空腔16位于衬底1内部的中心偏上位置。
具体的,所述第一热处理在不含氧、低压(低于大气压)的环境下进行,以防止衬底1被氧化。在一实施例中,该不含氧的环境为纯氢气环境。当然,在其他实施例中,该不含氧的环境也可以为惰性气体环境。所述第一热处理的环境压强可以小于1个大气压,使得形成的第一真空腔16内气压小于1个大气压。
在本实施例中,所述第一热处理的温度1100摄氏度。当然,在其他实施例中,所述第一热处理的温度也可以高于1100摄氏度。进一步的,在本实施例中,所述第一热处理为快速热退火。
在本实施例中,衬底1上形成有器件层18,器件层18通过外延生长的方式形成,即为外延层,具有与衬底1相同的材料,衬底1与器件层18构成半导体衬底(未标识)。
器件层18上形成有第一介质层23,其作为阻挡层,材料可以为氧化硅、氮化硅、氮氧化硅等,形成工艺可以为低压化学气相沉积、等离子体化学气相沉积或热氧化等工艺。
第一介质层23上形成有第二介质层22。第二介质层22的材料可以为氧化硅、氮化硅、氮氧化硅等,形成工艺可以为低压化学气相沉积、等离子体化学气相沉积或热氧化等工艺。
沟槽25穿过第一真空腔16上方的半导体衬底、第一介质层23以及第二介质层22,并与第一真空腔16连通。沟槽25与第一真空腔16围成感应本体6。
结合图15和图16所示,在本实施例中,沟槽25呈具有缺口(未标识)的环状,沟槽25的数量为两个,分别为外侧沟槽和内侧沟槽,其中,外侧沟槽的缺口与内侧沟槽的缺口呈180度间隔设置。更具体的,沟槽25为矩形,其中一条边设置有缺口。衬底1中位于外侧沟槽与内侧沟槽之间的部分构成一支撑梁5,衬底1中位于该沟槽25的缺口的部分也构成另一支撑梁,该两个支撑梁均与感应本体6连接,使得感应本体6可以悬空。
需说明的是,参考图15所示,在本发明的实施例中,沟槽25的数量并不应局限于两个,其数量可以任意设置,例如,沟槽25可以仅为一个。每个沟槽25的缺口数量可以任意设置,例如可以为两个。另外,沟槽25的形状也不应局限于矩形,还可以设置为圆形、五边形、六边形等多边形。
在本实施例中,器件层18内形成有悬空的第二真空腔7,所谓悬空是指第二真空腔7位于器件层18的内部,与器件层18的上表面(未标识)存在一定的间隔。第二真空腔7位于感应本体6内,并位于第一真空腔16的正上方。
第二真空腔7由若干间隔排列的第二槽经第二热处理合并而成,该第二槽位于器件层18的表面。换言之,通过先在器件层18的表面形成若干间隔排列的第二槽,再进行第二热处理,可以使得该些第二槽合并成悬空的第二真空腔7。
在所述第二热处理的作用下,该第二槽会沿水平方向扩大,使得各个第二槽之间相互连通,从而合并为一个完整的大孔,即为第二真空腔7。与此同时,在所述第二热处理的作用下,器件层18的上表面能量降低,使得器件层18的上表面发生迁移,各个第二槽之间的部分的端部得以相互结合为一个整体,从而在第二真空腔7的上方形成第二悬空薄膜(未标识)。通过该第二热处理工艺形成的第二悬空薄膜很平整,且厚度较薄,可以薄至1微米。在具体实施例中,第二真空腔7位于器件层18内部的中心偏上位置。
具体的,所述第二热处理在不含氧、低压(低于大气压)的环境下进行,以防止器件层18和衬底1被氧化。在一实施例中,该不含氧的环境为纯氢气环境。当然,在其他实施例中,该不含氧的环境也可以为惰性气体环境。所述第二热处理的环境压强可以小于1个大气压,使得形成的第二真空腔7内气压小于1个大气压。
在本实施例中,所述第二热处理的温度1100摄氏度。当然,在其他实施例中,所述第二热处理的温度也可以高于1100摄氏度。进一步的,在本实施例中,所述第二热处理为快速热退火。
需说明的是,第一真空腔16的数量并不应局限于一个,其还可以为两个,两个第一真空腔16沿水平方向间隔设置,第二真空腔7位于两个第一真空腔16之间,各个第一真空腔均与垂直延伸的沟槽连通,在这种情况下,所有第一真空腔与所有沟槽围成感应本体。
在本发明的变换例中,压力传感器内没有第二真空腔,也没有器件层18(使得半导体衬底仅由单纯的衬底构成),第一介质层23直接覆盖在衬底1的表面,压阻10直接形成在衬底1的表面。
器件层18的表面形成有若干压阻10,压阻10位于第二真空腔7的正上方。在本实施例中,压阻10的形成工艺为离子注入,即通过对器件层18表层的特定区域进行离子注入以获得压阻10。金属电极9位于第二介质层22的上方,且其一端穿过第二介质层22和第一介质层23与下方的压阻10形成欧姆接触。
以上所述仅是本发明的优选实施方式,应当指出,对于本技术领域的普通技术人员,在不脱离本发明原理的前提下,还可以做出若干改进和润饰,这些改进和润饰也应视为本发明的保护范围。
本文用于企业家、创业者技术爱好者查询,结果仅供参考。