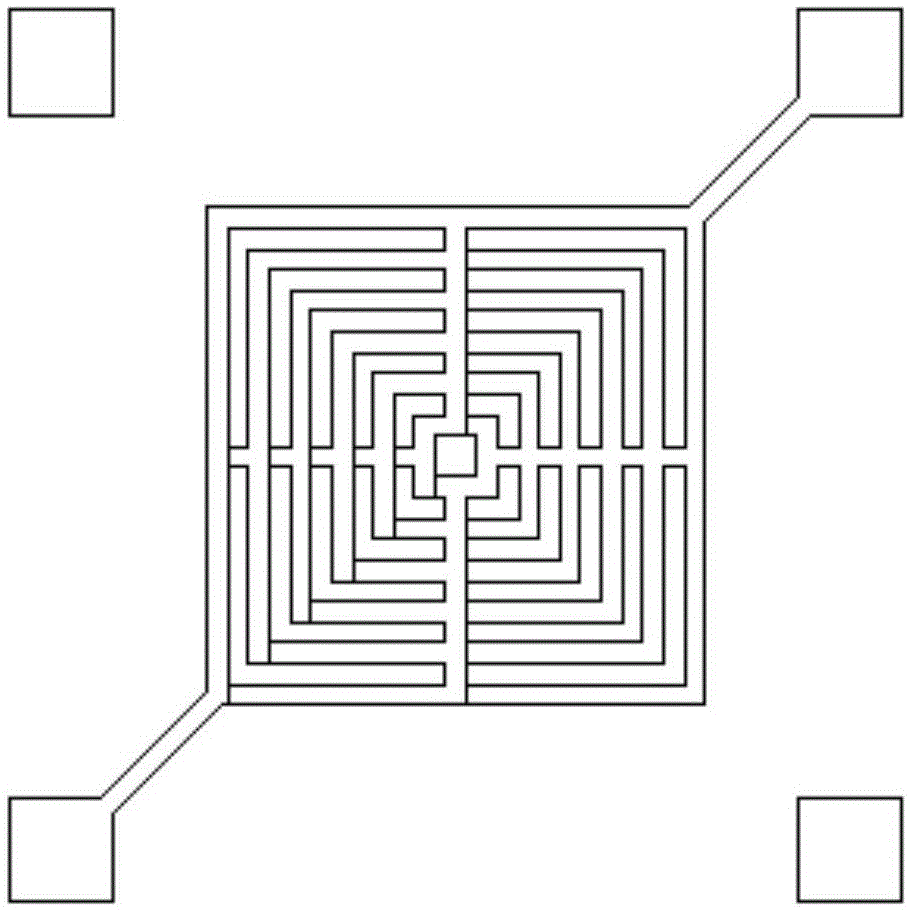
本发明涉及微电子器件及其制备技术领域,特别涉及单片集成的cmos加mems的微加热器及制备方法。
背景技术:
目前,现有的微加热器制备工艺主要采用正面或背面体硅刻蚀工艺,微加热器mems的器件与cmos/asic等读出电路的连接方式主要通过引线键合wire-bonding的封装技术。该工艺制备的微加热器具有尺寸大,功耗大,不易阵列化,及敏感膜应力大、隔热性差和高温热稳定性不理想等缺点。制约了微加热结构传感器如微气体传感器、微热量计、微气压计,微加速度计,以及电子鼻等微器件的发展和应用;mems器件和cmos电路独立制备而后采用引线键合wire-bonding的封装方式,mems cmos整体模块的尺寸无法降低且封装过程延长制备周期和容易在封装过程中导致良率减小。
随着现代微电子的技术日新月异的发展,小体积、低功耗且易与其它材料或器件组合的微热板越来越受到重视,但使用微加热板会带来一定的热功率损耗和器件的不稳定性。
现有技术中,为降低热功耗,实现结构保温普遍采用正面或背面悬空结构的绝热槽。微热板普遍采用的一种结构是:在衬底的上表面沉积一层二氧化硅(sio2)或氮化硅(sin)膜层作为绝缘层,在硅基底的下表面通过干法刻蚀制备绝热槽。在加热丝表面上又沉积一层氮化硅层作为钝化层。例如cn104541161a公开了的硅基微热板的加工方法便采用了在硅基底背面制备绝热槽的工艺;这种方法制备出来的微热板的尺寸600μm~1000μm,但是这种方法蚀刻出绝热槽后加热层仅靠一层薄膜结构的氮化硅层支撑,而该薄膜仅在两端被支撑衬底支撑,这种薄膜结构的应力控制比较差,而且强度不够,在器件受到震动或者碰撞时易发生破裂导致器件失效。另一种方法为:在硅基底的上表面通过湿法刻蚀制备绝热槽。例如,cn104176699a公开的硅基微热板的加工方法便采用了在硅基底正面制备绝热槽的工艺。该专利中描述的微热板是利用绝热沟槽的方式来进行热量的隔离,通过薄膜生长的方式形成一定的绝缘层和隔热层,然后经过溅射、剥离、刻蚀的方式来形成加热电极和测试电极层,然后从正面进行刻蚀形成一定的绝热槽结构。这种正面体硅刻蚀的方法制备的微加热器由于制备工艺的限制,器件尺寸300μm~1000μm,且工艺难度较背面体硅刻蚀制备绝热槽的大。由上可见,两种微加热器的制备过程中,;两种微加热器均具有较大的功耗,正面体硅刻蚀工艺制备的微加热器大约20mw,背面体硅刻蚀工艺制备的微加热器70mw~80mw;另外,由于在加工过程中,主要还是采用了单面薄膜复合的方式来实现隔热层、绝缘层、加热电极层、测试电极层的制备,因此会由于薄膜层次太多,容易产生应力而造成器件失效。综上,两种微加热器均存在尺寸达到几百至上千微米,功耗大,薄膜应力大、厚度不够的缺陷,难以做到同时具备小尺寸、低功耗、易于实现阵列化、械强度高、产品良率好等方面优点。另外,mems与cmos一体式集成制备的结构设计和制备工艺不仅可以减少后期mems器件和cmos封装过程,缩短mems cmos模块制备周期和避免在此过程导致下降的产品良率,显然地,还具有降低mems cmos模块的尺寸。
技术实现要素:
通过上述描述过程中,可以总结出传统的微加热器制备工艺具有如下缺点:通过正面体硅工艺制备的微加热器和通过背面体硅工艺制备的的微加热器尺寸均达到几百至上千微米,且结构保温性能不好,具有较大功耗;传统正面/背面体硅刻蚀工艺制备的微加热器,因制备过程中由于薄膜间应力而容易导致器件失效,无法同时实现保温隔热及机械强度大、产品良率高等优点;在工艺制备和封装过程中,正面体硅刻蚀技术制备微加热器的工艺难度较大,背面体硅刻蚀方法制备的微加热器在封装过程中因背面空腔结构容易产生损耗,两种微加热器均具有较低良率的特点。即,传统制备方法的微加热器具有尺寸大、功耗高、工艺难度大、良率低、薄膜应力大、机械强度低等缺点。另外,显然地,mems器件和cmos/asic读出电路分立制备后期引线键合的封装方法具有不仅产品实现周期较长,过程复杂,mems cmos模块尺寸较大的缺点。
针对以上传统工艺制备的微加热器的缺点,本申请通过另外提供的一种集成cmos加mems的热膜结构微加热器及其制备方法与电子鼻阵列,优化结构及加工工艺,此外,本申请提供的集成cmos加mems的热膜结构微加热器及其制备方法与电子鼻阵列,通过mems cmos集成制备可以减少封装过程,过程集成化,可以缩短制备周期,使制备/封装过程简单化,及减少mems cmos模块尺寸。实现以下特点:小尺寸(悬空微加热结构可达到17μm)、保温隔热性能好、低功耗(达到几微瓦)、工艺简单、结构强度高、可阵列化,从而实现电子鼻阵列,mems cmos集成制备可以实现过程集成化,缩短周期,制备过程简单化等特点。
为了达到上述目的,本发明提供的单片集成的cmos加mems的微加热器及制备方法,包括以下步骤:
步骤s1:在制备好的cmos/asic电路上制备绝热层,并在绝热层使用干法刻蚀打开用于与电极柱子连接的在cmos上的pad的开口。
步骤s2:在绝热层上制备绝缘层ⅰ,并在绝缘层ⅰ使用干法刻蚀打开用于与电极柱子连接的在cmos上的pad的开口。
步骤s3:涂覆第一层al层所需的第一光阻层并图形化。
步骤s4:蒸镀/溅射第一层al层。
步骤s5:通过lift-off工艺剥离第一光阻层并制备第一层电极柱子。
步骤s6:涂覆第二层al层所需的第二光阻层并图形化。
步骤s7:蒸镀/溅射第一层al层。
步骤s8:通过lift-off工艺剥离第二光阻层并制备第二层电极柱子,制成最终所需的电极柱子。
步骤s9:在含有所述步骤s8的电极柱子的硅基底表面制备牺牲层。
步骤s10:在电极柱子和牺牲层表面上,采用化学气相沉积cvd方法制备支撑层。
步骤s11:在支撑层上采用化学气相沉积cvd方法制备绝缘层ⅱ。
步骤s12:在绝缘层ⅱ上面制备具有应力释放的台阶结构层。
步骤s13:在含有所述支撑层、绝缘层ⅱ、台阶结构层的复合结构表面制备加热层、该加热层覆盖电极柱子的上表面。
步骤s14:在加热层上制备钝化层。
步骤s15:采用各向同性的湿法刻蚀或干法刻蚀方法释放牺牲层,形成空腔,制成集成cmos加mems的热膜结构微加热器。
优选的,所述牺牲层材料为:聚酰亚胺pi/氧化硅sio2/氮化硅sin/非晶硅a-si/多晶硅poly-si/金属cu/al。
本发明另提供一种集成cmos加mems的热膜结构微加热器,包括:在cmos/asic电路上表面形成的绝热层、绝缘层ⅰ,并刻蚀出用于与电极柱子连接的pad的开口;在绝缘层ⅰ表面形成的电极柱子;在电极柱子之间形成空腔及悬空加热结构;加热结构由下到上依次为支撑层、绝缘层ⅱ、台阶结构层、加热层及钝化层;其中,绝缘层ⅱ覆盖支撑层;台阶结构层位于在绝缘层ⅱ正上方区域内;加热层覆盖在含所述支撑层,绝缘层ⅱ、台阶结构层的复合结构上、并覆盖电极柱子的上表面;钝化层覆盖所述加热层;绝缘层ⅰ、电极柱子、支撑层共同形成集成cmos加mems的热膜结构微加热器的空腔,微加热器成悬空结构。
优选的,所述加热层位于空腔、所述支撑层、绝缘层ⅱ以及台阶结构层的正上方区域,并覆盖电极柱子的上表面。
优选的,所述绝热层的材料是多孔硅,厚度为10μm~100μm,孔隙率为50%~90%;制备cmos/asic电路使用的硅片为单晶硅片,厚度为200μm~500μm;所述绝缘层ⅰ的材料是氧化硅,厚度为50nm~2μm;所述绝缘层ⅱ的材料是氮化硅sin/氧化硅sio2/陶瓷三氧化二铝al2o3,厚度为50nm~500m。
优选的,所述台阶结构层的台阶深度100nm~1000nm、台阶线条宽度为1μm~50μm、台阶间隙宽度为0.5μm~50μm。材料是氧化硅sio2/氮化硅sin。
优选的,所述支撑层的材料是多孔硅/氧化硅sio2/陶瓷三氧化二铝al2o3,厚度为200nm~5μm;采用多孔硅时,其孔隙率为50%~90%。
优选的,所述加热层的材料是taaln/多晶硅poly-si/w/tin/mo/pt薄膜,厚度为50nm~500nm;
优选的,所述钝化层的材料是氮化硅sin/氧化硅sio2/聚酰亚胺pi,厚度为50nm~3μm。
本发明另提供了一种所述电子鼻阵列,将多个上述的集成cmos加mems的热膜结构微加热器在硅片表面上不同区域排布制备,各微加热器通过电极柱子及cmos/asic电路上的连接pad与微加热器下面的cmos/asic电路连接。
有益效果:本发明的集成cmos加mems的热膜结构微加热器采用支撑层 绝缘层ⅱ 台阶结构层,提高了微加热器隔热保温性能并多重复合结构增强了微加热器的结构强度;结构设计上,cmos/asic电路表面的绝热层和绝缘层ⅱ进一步增强器件的隔热性能,进一步提高了热保温、低功耗的性能;台阶结构层具有应力释放的作用,在加热过程中,有类似弹簧的效果,增强了微加热器的结构强度;桥式热膜微加热器中通过表面硅技术制备,微加热结构可达到17μm,相比使用体硅刻蚀技术制备的微加热器(尺寸为几百至上千微米),大大减少了结构尺寸,具有极大的尺寸优势,同时具有易于阵列化的特点,在制备电子鼻方面具有尺寸缩小,易实现化的极大的优势。分步镀膜技术克服目前一步镀膜(电极柱子一次镀膜具有高度限制),增加电极柱子的高度,可提高电学导通率和良率;集成cmos加mems的热膜结构微加热器空腔制备通过制备牺牲层及后期释放而实现,相比体硅刻蚀的方法,桥式热膜架构微加热器制备过程中选择的牺牲层材料及相应的刻蚀技术具有工艺成熟、刻蚀工艺简单等特点,因而表面体硅技术的微加热器具有极易实现,工艺简单的优势,相比正面/背面体硅刻蚀技术的微加热器的制备工艺,工艺难度大大减少,提高微加热器产品良率。具有实用性和可实现的优势。
附图说明
图1为本发明集成cmos加mems的热膜结构微加热器俯视图。
图2为本发明集成cmos加mems的热膜结构微加热器的台阶应力释放结构(环形)。
图3为本发明集成cmos加mems的热膜结构微加热器的台阶应力释放结构(回形)。
图4为本发明电子鼻阵列结构图。
图5为本发明电子鼻阵列俯视图。
图6为本发明cmos/asic电路示意图。
图7为本发明集成cmos加mems的热膜结构微加热器制备方法步骤s1示意图。
图8为本发明集成cmos加mems的热膜结构微加热器制备方法步骤s2示意图。
图9为本发明集成cmos加mems的热膜结构微加热器制备方法步骤s3示意图。
图10为本发明集成cmos加mems的热膜结构微加热器制备方法步骤s4示意图。
图11为本发明集成cmos加mems的热膜结构微加热器制备方法步骤s5示意图。
图12为本发明集成cmos加mems的热膜结构微加热器制备方法步骤s6示意图。
图13为本发明集成cmos加mems的热膜结构微加热器制备方法步骤s7示意图。
图14为本发明集成cmos加mems的热膜结构微加热器制备方法步骤s8示意图。
图15为本发明集成cmos加mems的热膜结构微加热器制备方法步骤s9示意图。
图16为本发明集成cmos加mems的热膜结构微加热器制备方法步骤s10示意图。
图17为本发明集成cmos加mems的热膜结构微加热器制备方法步骤s11示意图。
图18为本发明集成cmos加mems的热膜结构微加热器制备方法步骤s12示意图。
图19为本发明集成cmos加mems的热膜结构微加热器制备方法步骤s13示意图。
图20为本发明集成cmos加mems的热膜结构微加热器制备方法步骤s14示意图。(牺牲层释放前)
图21为本发明集成cmos加mems的热膜结构微加热器制备方法步骤s15示意图。(牺牲层释放后)。
附图标识:
1、cmos/asic电路;2、绝热层;3、绝缘层ⅰ;4、电极柱子;41、第一层al层;42、第二层al层;5、牺牲层;51、第一光阻层;52、第二光阻层;6、支撑层;7、绝缘层ⅱ;8、台阶结构层;9、加热层;10、钝化层;12、空腔。
具体实施方式
为使本发明解决的技术问题、采用的技术方案和达到的技术效果更加清楚,下面结合附图和实施例对本发明作进一步的详细说明。可以理解的是,此处所描述的具体实施例仅仅用于解释本发明,而非对本发明的限定。另外还需要说明的是,为了便于描述,附图中仅示出了与本发明相关的部分而非全部内容。
实施例
一、结构
参照图1、图21,本实施例的微加热器包括:在cmos/asic电路1上表面形成的绝热层2、绝缘层ⅰ3,并在绝热层2及绝缘层ⅰ3上干法刻蚀出用于与电极柱子4连接的pad的开口;在绝缘层ⅰ3表面形成的电极柱子4;在电极柱子之间形成空腔12及悬空加热结构;加热结构由下到上依次为支撑层6、绝缘层ⅱ7、台阶结构层8、加热层9及钝化层10;其中,绝缘层ⅱ7覆盖支撑层6;台阶结构层8位于在绝缘层ⅱ7正上方区域内;加热层9覆盖在含所述支撑层6,绝缘层ⅱ7、台阶结构层8的复合结构上、并覆盖电极柱子4的上表面;;钝化层10覆盖所述加热层9;绝缘层ⅰ3、电极柱子4、支撑层6共同形成集成cmos加mems的热膜结构微加热器的空腔12,使加热器形成悬空结构。
其中所述加热层9位于所述支撑层6、绝缘层ⅱ7以及台阶结构层8的正上方区域内,所述支撑层6、绝缘层ⅱ7以及台阶结构层8能够更稳定地支撑加热层9,有效防止微加热器(简称器件)受到震动碰撞时因为没有有效支撑而发生的破裂。同时,前述台阶结构层8还可以有效减缓微加热器在使用碰撞时或温度急剧变化时产生的应力,避免导致加热层9因变形翘曲而导致的破裂脱落,有效提高器件使用期间的稳靠性和使用寿命,同时所述加热层9位于所述空腔12的正上方区域内,还能保证良好的隔热效果。
所述台阶结构层8的台阶状结构减缓应力和提高强度的效果与其材料的选择、宽度及台阶间距有关。在保证工艺实现的前提下,台阶越深、宽度越小、间距越小,减缓应力和提高强度效果越好。
为了保证台阶结构层8能产生较好的支撑强度和绝热效果,所述台阶结构层8的下表面覆盖一层支撑层6,材料为多孔硅,其厚度为200nm~5μm,孔隙率为50%~90%,也可以是氧化硅/陶瓷三氧化二铝,但不限于此。
对空腔12内填充的牺牲层5,材料为多孔硅/聚酰亚胺pi/氧化硅sio2/氮化硅si3n4/非晶硅a-si/多晶硅poly-si/金属cu/al等,但不限于此。其中,选用多孔硅的孔隙率为50%~90%。
为了保证台阶状结构具有较好的减缓应力和提高强度的效果,所述台阶结构层的台阶深度为100nm~1000nm,台阶间隙为0.5μm~50μm,宽度为1μm~50μm,本实施例中台阶间隙优选为1μm,台阶宽度优选为1μm。
由于加热层一般电导率较高,为了保证安全,优选在所述支撑层6上设置绝缘层ⅱ7,绝缘层ⅱ7可以为氧化硅sio2/氮化硅sin,厚度为50nm~500nm。
所述加热层9可以是taaln薄膜,厚度为50nm~500nm。
所述加热层9也可以是多晶硅poly-si/w/tin/mo/pt等,但不限于此。
同样的,由于加热层一般电导率较高,为了保证安全,优选在所述加热层9上设置钝化层10,所述钝化层10可以是sin,厚度为50nm~3μm。
优选的,所述钝化层10也可以氧化硅sio2/聚酰亚胺pi。
所述加热层9和钝化层10均具有台阶结构;优选的,所述台阶状结构层8、加热层9和钝化层10均具有台阶状类弹簧结构。
为了便于加热层9引线,在绝热层9上制备连接电极11、并与电极柱子4连接,用来与asic/cmos等读出电路连接。
为了便于制备空腔12,空腔12的形成是通过释放原先填充空腔12的牺牲层5来实现的;该牺牲层5可以是聚酰亚胺pi,也可以是氧化硅sio2/氮化硅sin/非晶硅a-si/多晶硅poly-si等,但不限于此。
为了便于形成隔热的空腔12,优选在cmos/asic电路1上制备多孔硅层,即前述绝热层2,厚度为10μm~100μm,孔隙率为50%~90%。cmos/asic电路1优选为硅片(特别是单晶硅基底),厚度为200μm~500μm。
参照图2、图3,所述应力释放台阶为环形或回形。
本实施例的集成cmos加mems的热膜结构微加热器结构的尺寸可达到长度17μm。
二、参数要求
本实施例的集成cmos加mems的热膜结构微加热器各层参数如下:
1、cmos/asic电路:厚度200μm~500μm。
2、绝热层:多孔硅,厚度为10μm~100μm,50%-90%孔隙率。
3、绝缘层ⅰ:氧化硅sio2,厚度为50nm~2μm。
4、电极柱子:分步镀膜的方法镀al层,厚度为2μm~20μm。
5、牺牲层:聚酰亚胺(pi)/氧化硅sio2/氮化硅sin/非晶硅a-si/多晶硅poly-si/金属cu/al等,厚度为1μm~20μm。
6、支撑层:多孔硅/氧化硅sio2/陶瓷三氧化二铝al2o3,厚度为5μm~200μm,使用多孔硅时孔隙率为50%-90%。
7、绝缘层ⅱ:氮化硅sin/氧化硅sio2/陶瓷三氧化二铝al2o3,厚度50nm~500nm。
8、台阶结构层:氮化硅sin/氧化硅sio2,厚度100nm~3μm,台阶线条line宽度:100nm~1000nm,间隙space宽度:0.5μm~50μm。
9、加热层:taaln/多晶硅poly-si/w/tin/mo/pt等,厚度50nm~500nm。
10、钝化层:氮化硅sin/氧化硅sio2/聚酰亚胺pi,厚度50nm~3μm
三、电子鼻阵列
如图4、图5所示,应用表面硅技术的加热器阵列电子鼻,电子鼻中各微加热器通过电极柱子及cmos/asic电路上的连接pad与微加热器下面的cmos/asic电路相连。
四、制备方法
本实施例的集成cmos加mems的热膜结构微加热器制备方法包括以下步骤:
请参照图7,步骤s1:在制备好的cmos/asic电路1,(结构参照图6所示)上制备绝热层2,并在绝热层2上使用干法刻蚀打开用于与电极柱子4连接的在cmos上的pad的开口。
请参照图8,步骤s2:在绝热层2上制备绝缘层ⅰ3,并在绝缘层ⅰ3使用干法刻蚀打开用于与电极柱子4连接的在cmos上的pad的开口。
请参照图9,步骤s3:涂覆第一层al层41所需的第一光阻层51并图形化。
请参照图10,步骤s4:蒸镀/溅射第一层al层41。
请参照图11,步骤s5:通过lift-off工艺剥离第一光阻层51并制备第一层电极柱子。
请参照图12,步骤s6:涂覆第二层al层42所需的第二光阻层52并图形化。
请参照图13,步骤s7:蒸镀/溅射第一层al层42。
请参照图14,步骤s8:通过lift-off工艺剥离第二光阻层52并制备第二层电极柱子,制成最终所需的电极柱子。
请参照图15,步骤s9:在含有所述步骤s8的电极柱子的硅基底表面制备牺牲层5。
请参照图16,步骤s10:在电极柱子4和牺牲层5表面上,采用化学气相沉积cvd方法制备支撑层6。
请参照图17,步骤s11:在支撑层6上采用化学气相沉积cvd方法制备绝缘层ⅱ7。
请参照图18,步骤s12:在绝缘层ⅱ7上面制备具有应力释放的台阶结构层8。
请参照图19,步骤s13:在含有所述支撑层6、绝缘层ⅱ7、台阶结构层8的复合结构表面制备加热层9、该加热层9覆盖电极柱子4的上表面。
请参照图20,步骤s14:在加热层9上制备钝化层10。
请参照图21,步骤s15:采用各向同性的湿法刻蚀或干法刻蚀方法释放牺牲层5,形成空腔12,制成集成cmos加mems的热膜结构微加热器。
所述的方法还包括:在所述第一步前,利用浓硫酸对上cmos/asic电路1煮10~30分钟、之后用去离子水等溶液对所述上cmos/asic电路1进行清洗,然后用氮气吹干。
为了保证较好的隔热效果,所述第一步中多孔硅层的厚度为10μm~100μm,优选100μm;孔隙率为50%~90%,优选50%;采用湿法腐蚀的方法制备。
所述步骤s12中,制备所述台阶结构层8时,所述台阶结构层8落在所述绝缘层ⅱ7正上方区域内,所述台阶结构能够更稳定地支撑加热层9,有效减缓防器件受到震动碰撞或温度急剧变化时产生的比较大的应力,防止发生破裂。
为了保证安全,在所述加热层9上设置钝化层10,步骤s14中制备钝化层10的方法为:在所述加热层9上磁控溅射沉积一层氮化硅sin,厚度可以为50nm~3μm,优选100nm~2μm。
优选的,所述钝化层10也可以是氧化硅sio2/聚酰亚胺pi。
所述步骤s15中的制备所述空腔12的方法为各向同性的湿法刻蚀或干法刻蚀,其中干法刻蚀的方法的具体为:先用光刻胶作为掩模层定义出空腔12的位置及形状,再用各向同性的湿法刻蚀或干法刻蚀工艺制作出空腔12。
五、小结
本发明的特点及优势如下:
1、表面硅制备技术加热结构:工艺简单、性质优势。
2、牺牲层聚酰亚胺pi/氧化硅sio2/氮化硅sin/非晶硅a-si/多晶硅poly-si/金属cu/al:技术成熟,刻蚀工艺简单。
3、分步镀膜技术:分步溅射/蒸镀电极柱子(al柱)增加电极柱子(al柱)的高度,突破单层电极柱子(al柱)制备限制高度,从而增加电学导通率,提高良率。
4、台阶结构层:具有台阶状的薄膜结构,可以释放应力,同时在加热过程中具有类似弹簧的效果,能增加加热器的强度。
5、小尺寸加热结构使小尺寸电子鼻阵列可实现化。
加热层底部的支撑层和绝热层设计:增加薄膜强度,热隔离。
加热层:taaln/多晶硅poly-si/w/tin/mo/pt等。
6、cmos和mems结构单片集成加热式:小体积、低功耗、集成度高,可以直接输出数字信号,可大规模阵列化。
最后应说明的是:以上各实施例仅用以说明本发明的技术方案,而非对其限制;尽管参照前述各实施例对本发明进行了详细的说明,本领域的普通技术人员应当理解:其对前述各实施例所记载的技术方案进行修改,或者对其中部分或者全部技术特征进行等同替换,并不使相应技术方案的本质脱离本发明各实施例技术方案的范围。
本文用于企业家、创业者技术爱好者查询,结果仅供参考。