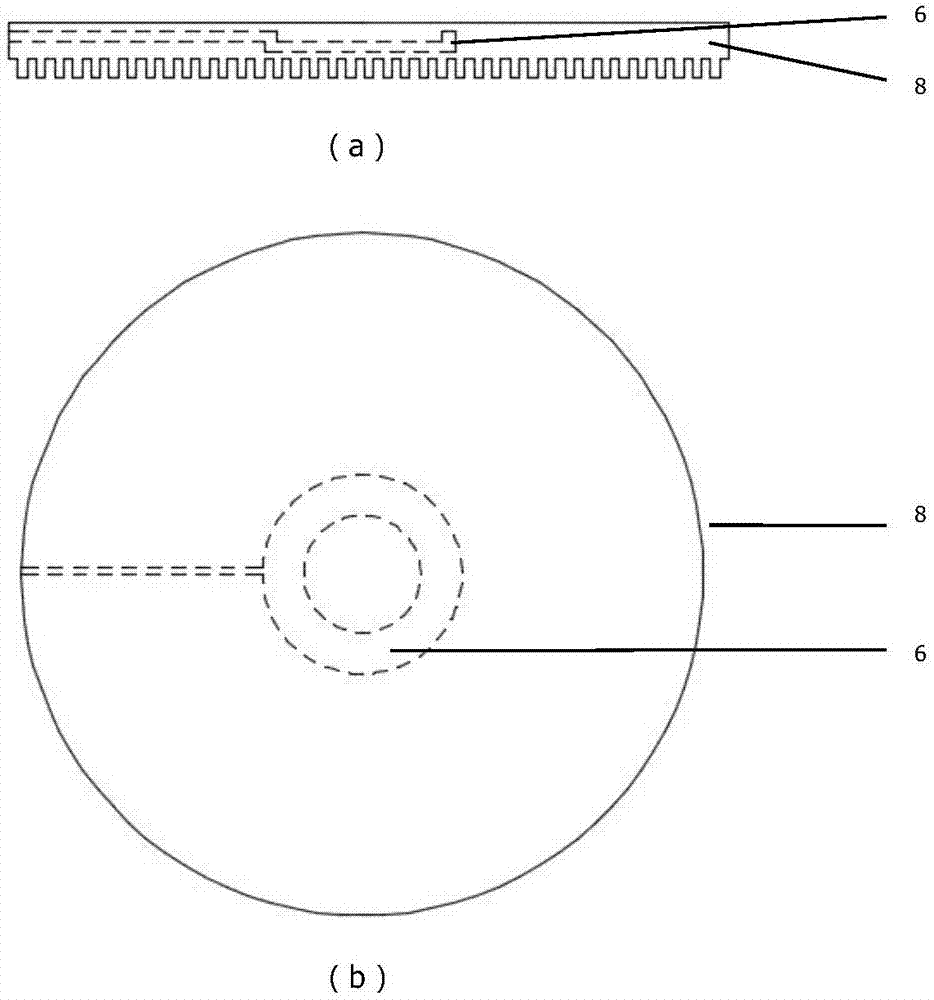
本发明属于微纳制造领域,尤其涉及复杂腔体内表面微纳结构的自适应随形制造方法。
背景技术:
随着微纳米技术的发展,微纳米技术不但推动着科技的进步,而且造就了现代知识经济的物质基础。例如,微纳米加工技术促使集成电路按照摩尔定律发展。在非平面上制造微纳结构也有很多重要的应用,尤其在航空航天设备的超轻量化、飞机表面减阻降温、雷达反射面、潜艇减阻,曲面衍射光栅等方面都有潜在的应用。腔体内表面微纳结构的制造也有较多的应用,例如,有“v”字形沟槽微结构的天然气管道相对于无沟槽的管道,其空气阻力明显减小。有沟槽的管子可使气体、液体输运效率提高10%,并可节约管输成本10%;气缸工作表面制备独立微坑结构,更易于达到气缸-活塞环摩擦副的工作要求。
目前微纳制造工艺主要有光刻工艺、激光直写技术和纳米压印技术等,这些技术对于在曲面衬底上制造微纳结构来说存在很大的局限性。光刻工艺主要是在平面上做微纳结构,难以实现曲面上微纳结构的制造;激光直写技术,既可在平面上做微纳结构,又可在复杂外曲面上做微纳结构,但其成本高,效率低,而且对于复杂腔体内表面的微纳结构的制造存在较大的难度;纳米压印技术可以采用拼接的方法在曲面上制作微纳结构,但存在拼接误差,难以实现大幅面曲面上连续微纳结构的精确制造,并且,模具在腔室内表面的拼接难度较大,也使得制造过程效率低,不适于快速制造。
技术实现要素:
为了克服现有技术的缺点,本发明提出了复杂腔体内表面微纳结构的自适应随形制造方法,具有制备工艺简单、成本低、制备周期短、模具可重复利用、模具自适应内表面形状、以及可在复杂腔体内表面上制作复杂微纳结构等优点。
为了实现上述目的,本发明采取的技术方案如下:
复杂腔体内表面微纳结构的自适应随形制造方法,包括以下步骤:
1)制备带有微纳结构的弹性体薄膜:首先,在平面衬底上制作微纳结构图案;其次,将上述平面衬底平放在加热台上,待加热台温度升高至弹性体材料的熔化温度时,在平面衬底上均匀的放置一层热塑性弹性体颗粒;然后,待热塑性弹性体颗粒受热吸附在平面衬底表面上后,用圆柱形物体滚压热塑性弹性体颗粒使其黏附在一起并呈第一薄膜状态;在第一薄膜上制作预设的气道,气道的位置布置由仿真模型得出,再将事先制备的无微纳结构的第二薄膜覆盖在有气道的第一薄膜上,使其粘合为一体;将平面衬底转移到常温环境下,待其冷却到室温后,翻模即得到有微纳结构图案的弹性体薄膜;
2)制备弹性体模具:将第一步制备的弹性体薄膜折叠成球状,并在其接口处和气道6入口分别插入第一气体管道和第二气体管道,并将弹性体薄膜和预设的气体管道做密封处理,得到弹性体模具;
3)弹性模具的形状控制:首先,将第二步制备的弹性体模具浸泡在压印胶里,使压印胶黏附在弹性体模具上;其次,将附有压印胶的弹性体模具放入物体内腔,将充气装置与第一气体管道、第二气体管道相接,并用控制器控制充气装置给弹性体薄膜及其气道充气,使得弹性体薄膜逐渐膨胀,逐渐排出腔体内空气;最后,给弹性体薄膜及其气道继续充气,并通过控制气道的压力,使得弹性模具的形状达到预定形状,与腔体内壁随形接触,并具有一定的压力;
4)固化压印胶,实现图形转移:首先,通过热或紫外光,使得固化胶固化;然后,将第一气体管道、第二气体管道和充气装置分离,排出弹性体模具内的气体,弹性模具回复充气前状态,与腔体内壁脱离;最后,从物体内腔取出弹性体模具,即得到内表面有微纳结构图案的物体;
5)刻蚀腔体内表面:以转移的微纳结构化压印胶为掩膜,对腔体内表面进行刻蚀;刻蚀完成后,将压印胶清洗移除。
所述的步骤1)中的气道的形状与布局经过预设计:通过弹塑性力学模型,建立气道的形状与布局在弹性体模具气道模型和弹性体模具气道的映射关系,使得弹性体模具充气后能够与腔体内表面随形贴合。
所述的步骤1)中的微纳结构的形状与布局经过预设计:第一步,通过弹塑性力学模型,建立微纳结构的形状与布局在弹性体模具充气前后的映射关系;第二步,根据该映射关系,将待制造的微纳结构形状与布局,即弹性模具充气后与腔体内壁随形贴合时的微纳结构形状与布局,进行数学转换,得到弹性模具充气前的微纳结构形状与布局;第三步,按照弹性模具充气前的微纳结构形状与布局进行制造。
所述的步骤1)中的热塑性弹性体材料为tpe、橡胶或pbt。
所述的步骤1)中的气道根据物体内表面复杂程度设有多个。
所述的步骤1)中的微纳结构的线宽为10nm-0.5mm。
所述的步骤3)中的压印胶为卡夫特、noa81或epg535。
本发明的有益效果为:由于本发明是将平面微纳结构图案转移到弹性体模具上,并采用气体控制弹性体模具及其内置气道压强的方式驱动弹性体模具逐渐变形,使得弹性体模具贴合物体内表面,所以具有弹性体模具可重复使用、弹性体模具自适应物体内表面形状以及可在复杂内表面或凹面上制作复杂微纳结构的优点。
附图说明
图1是制备带有微纳结构的弹性体薄膜的示意图,图1(a)是平面衬底;图1(b)和(c)是在加热台上将微纳结构图案复制到弹性体薄膜及制作气道的示意图;图1(d)将气道密封的示意图。
图2是制备好的弹性体薄膜示意图,图2(a)是弹性体薄膜正视图;图2(b)是弹性体薄膜俯视图。
图3是弹性体模具的示意图。
图4是将黏附压印胶的弹性体模具放置在物体内腔的示意图。
图5是弹性体模具自适应物体内表面形状的示意图。
图6是压印胶附在物体内表面的示意图。
图7是物体内表面被刻蚀后的示意图。
图8是弹塑性力学模拟仿真确定气道位置的示意图。
图9是弹塑性力学模拟仿真确定微纳结构形状与布局的示意图,图9(a)弹性体模具充气前微纳结构简图;图9(b)弹性体模具充气后贴合物体内表面的微纳结构简图。
具体实施方式
下面结合附图和实施例对本发明进行详细描述。
复杂腔体内表面微纳结构的自适应随形制造方法,包括以下步骤:
1)制备带有微纳结构的弹性体薄膜:首先,在平面衬底2上制作微纳结构1;其次,将平面衬底2平放在加热台4上,待加热台4温度升高至tpe的熔化温度190℃时,在平面衬底2上均匀的放置一层热塑性弹性体颗粒3;然后,待热塑性弹性体颗粒3受热吸附在平面衬底2表面上后,用圆柱形物体滚压热塑性弹性体颗粒3使其黏附在一起并呈第一薄膜5状态;最后,在第一薄膜5上制作气道6,再将事先制备的无微纳结构的第二薄膜7覆盖在有气道的第一薄膜5上,使其粘合为一体;将平面衬底转移到常温环境下,待其冷却到室温后,翻模即得到有微纳结构图案的弹性体薄膜8,如图1、图2所示;
2)制备弹性体模具:将第一步制备的弹性体薄膜8折叠成球状并在其接口处和气道6入口分别插入第一气体管道9和第二气体管道10,用绳线11将弹性体薄膜8的接口紧紧的系在第一气体管道9上使其接口和第一气体管道9的结合处密封,得到弹性体模具,如图3所示;
3)弹性模具的形状控制:首先,将第二步制备的弹性体模具浸泡在压印胶里,使压印胶黏附在弹性体模具上;其次,将附有压印胶的弹性体模具放入物体12内腔,将充气装置与第一气体管道9相接,用控制器控制充气装置从第一气体管道9给弹性体模具8充气,使其膨胀直至弹性体模具8基本充满物体12的整个内腔,再用控制器控制充气装置从第二气体管道10给弹性体模具8的气道6充气,使其膨胀直至弹性体模具8完全充满物体12的整个内腔,如图4、图5所示;
4)固化压印胶:首先,通过紫外光照射固化胶2min使固化胶固化;然后,将第一气体管道9、第二气体管道10和充气装置分离,排出弹性体模具8内的气体,并从物体12内腔取出弹性体模具8即得到内表面有微纳结构图案的物体13,如图6所示;
5)刻蚀腔体内表面:以转移的微纳结构化压印胶为掩膜,对腔体内表面进行刻蚀;刻蚀完成后,将压印胶清洗移除,如图7所示。
所述的气道6的形状与布局经过预设计:通过弹塑性力学模型,即腔体模型15和弹性体模具模型14,建立气道6的形状与布局在弹性体模具气道模型16和弹性体模具气道6的映射关系17,使得弹性体模具8充气后能够与腔体内表面随形贴合,如图8所示。
所述的微纳结构1的形状与布局经过预设计:通过弹塑性力学模型,即腔体模型15和弹性体模具模型14,建立微纳结构1的形状与布局在弹性体模具8充气前后的映射关系21,使得弹性体模具由充气前微纳结构19变化为充气后贴合在物体12内表面的最终微纳结构20,如图9所示。
所述的步骤1)中的热塑性弹性体材料为tpe。
所述的步骤3)中的压印胶为卡夫特。
本文用于企业家、创业者技术爱好者查询,结果仅供参考。