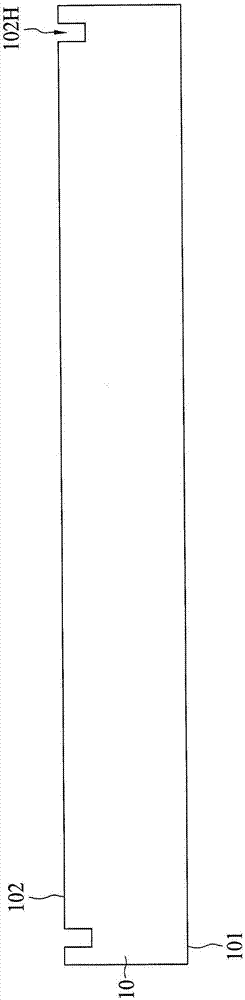
本发明涉及微机电系统(mems)结构和其制造方法。
背景技术:
微机电系统(mems)装置为微尺寸装置,通常尺寸范围为从小于1微米到数毫米。mems装置包含形成于衬底(例如,晶片)上的机械元件(固定元件和/或可移动元件)以感测物理状态,例如力、加速度、压力、温度或振动,以及电子元件以处理电信号。mems装置广泛用于例如音响系统(acousticsystem)、汽车系统(automotivesystem)、惯性引导系统(inertialguidancesystem)、家用电器(householdappliance)、许多装置的保护系统之应用中,以及用于许多其它的产业、科学、与工程系统中。
随着技术进展,由于尺寸与厚度越来越小,mems装置与半导体装置的设计变得越来越复杂。在此小且薄的装置中,实施许多制造操作。以微小化规模制造mems装置与半导体装置变得更加复杂,制造复杂度的增加可能造成缺陷,例如产量下降、晶片破裂、以及其它问题。
技术实现要素:
本发明的一些实施例为提供一种制造结构的方法,其包括:接收装置衬底,所述装置衬底具有彼此对置的第一表面与第二表面;接收载体衬底,所述载体衬底具有彼此对置的第三表面与第四表面;在所述载体衬底的所述第三表面与所述装置衬底的所述第二表面之间,形成中间层;将所述装置衬底的所述第二表面附接到所述载体衬底的所述第三表面;从所述第一表面薄化所述装置衬底;在所述装置衬底的所述第一表面上方形成装置;以及从所述第四表面图案化所述载体衬底与所述装置衬底,以在所述载体衬底、所述中间层、以及所述装置衬底中形成空腔。
本发明的一些实施例为提供一种制造mems结构的方法,其包括:接收衬底,所述衬底具有载体衬底、装置衬底、以及插于其间的中间层,其中所述中间层具有多个凹部;薄化所述装置衬底;在所述装置衬底上方形成mems装置,其中所述mems装置包括隔膜、重叠于所述隔膜上的板、以及包围所述薄膜与所述板的至少一介电层;蚀刻所述衬底,以形成暴露所述介电层的空腔;以及蚀刻所述介电层的一部分以暴露所述隔膜与所述板,并且同时蚀刻所述中间层的一部分。
本发明的一些实施例为提供一种mems结构,其包括:衬底,其具有第一表面与第二表面;板,其位于所述衬底的所述第一表面上方;隔膜,其位于所述衬底的所述第一表面上方;空腔,其形成于所述衬底中并且暴露所述板与所述隔膜;以及凸块,其位于所述衬底的所述第二表面上。
附图说明
为协助读者获得最佳理解效果,建议在阅读本发明的同时参考附图和其详细文字描述。应注意,为遵循业界标准作法,本专利说明书中的图式不一定按照正确的比例绘制。在某些图式中,尺寸可能刻意放大或缩小,以协助读者清楚了解其中的讨论内容。
图1为根据本发明的各方面说明制造结构的方法的流程图。
图2a、2b、2c、2d、2e、2f、2g、2h、2i和2j为根据本发明的一些实施例说明制造结构的各种操作之一的横截面图。
图3a、3b和3c为根据本发明的一些实施例说明制造结构的各种操作之一的横截面图。
图4a和4b为根据本发明的一些实施例说明制造结构的各种操作之一的横截面图。
符号说明
10装置衬底
10a通路孔
10c空腔
20载体衬底
20a沟槽
22中间层
22h开口
22t凹部
24凸块
26薄膜
30装置
31电介质层
32导电层
34连接垫
36蚀刻停止层
41第一板
41h通气孔
42隔膜
42h孔洞
43第二板
43h通气孔
50装置结构
60装置结构
70装置结构
101第一表面
102第二表面
102h凹槽
203第三表面
204第四表面
204h凹槽
具体实施方式
本发明提供了数个不同的实施方法或实施例,可用于实现本发明的不同特征。为简化说明起见,本发明也同时描述了特定零组件与布置的范例。应注意,提供这些特定范例的目的仅在于示范,而非予以任何限制。举例来说,在以下说明第一特征如何在第二特征上或上方的叙述中,可能会包括某些实施例,其中第一特征与第二特征为直接接触,而叙述中也可能包括其它不同实施例,其中第一特征与第二特征中间另有其它特征,以致于第一特征与第二特征并不直接接触。此外,本发明中的各种范例可能使用重复的参考数字和/或文字注记,以使文件更加简单化和明确,这些重复的参考数字与注记不代表不同的实施例与配置之间的关联性。
另外,本发明在使用与空间相关的叙述词汇,如“在...之下”,“低”,“下”,“上方”,“之上”,“下”,“顶”,“底”和类似词汇时,为便于叙述,其用法均在于描述图示中一个元件或特征与另一个(或多个)元件或特征的相对关系。除了图示中所显示的角度方向外,这些空间相对词汇也用来描述所述装置在使用中以及操作时的可能角度和方向。所述装置的角度方向可能不同(旋转90度或其它方位),而在本发明所使用的这些空间相关叙述可以同样方式加以解释。
在本文中所使用的“第一”、“第二”、“第三”以及“第四”词语为描述各种元件、组件、区域、层和/或区段,这些元件、组件、区域、层和/或区段应不受限于这些词语。这些词语可仅用于一元件、组件、区域、层、或区段与另一元件、组件、区域、层、或区段。除非内文中清楚指明,否则当于本文中使用例如“第一”、“第二”、“第三”以及“第四”词语时,并非意指序列或顺序。
在本文中,“装置衬底”一词为半导体材料或其它材料形成的晶片或衬底,其上形成装置,例如半导体装置、mems装置、或其它装置。
在本文中,“载体衬底”一词是指由半导体材料或其它材料形成的晶片或衬底作为载体或支撑体,以于运送或制造过程中携载或支撑装置衬底。载体衬底的尺寸、材料或特性与装置晶板的尺寸、材料或特性可相同或不同。在一些实施例中,载体衬底可重复使用。
在本文中,“附接”一词为以直接接触方式或间接接合方式,结合一物体到另一物体。在直接接触方式中,所述物体彼此实体接触。在间接接合方式中,可使用中间层结合所述物体。
在本发明中,提供制造结构的方法。将装置衬底附接到载体衬底,而后将装置衬底的厚度薄化到一预定厚度。而后,在薄化的装置衬底上,形成包含mems装置和/或半导体装置的装置。所述薄化的装置衬底受到载体衬底支撑,因而可与标准的半导体工艺与设备相容。
图1为根据本发明的各方面说明制造结构的方法的流程图。所述方法100始于操作110,在操作110中接收具有彼此对置的第一表面和第二表面的装置衬底。所述方法100继续进行操作120,在操作120中接收具有彼此对置的第三表面和第四表面的载体衬底。所述方法100继续进行操130,在操作130中,在载体衬底的第三表面与装置衬底的第二表面之间,形成中间层。所述方法100继续进行操作140,在操作140中,装置衬底的第二表面附接到载体衬底的第三表面。所述方法100继续进行操作150,其中从第一表面薄化装置衬底。所述方法100继续进行操作160,其中在装置衬底的第一表面上方,形成装置。所述方法100继续进行操作170,其中从第四表面图案化载体衬底与装置衬底,以于载体衬底、中间层以及装置衬底中形成空腔(cavity)。
所述方法100仅为一范例,且并非用于限制本发明超出记载于权利要求书的内容。可在方法100之前、期间、以及之后,提供其它操作,以及关于所述方法的其它实施例,可替换、排除、或移动所描述的一些操作。
图2a、2b、2c、2d、2e、2f、2g、2h、2i和2j为根据本发明的一些实施例说明制造结构的各种操作之一的横截面图。如图2a与图1的操作100所示,方法100始于操作110,在操作110中,接收装置衬底10,所述衬底10具有彼此对置的第一表面101和第二表面102。装置衬底10为晶片或衬底,其上形成装置,例如半导体装置、mems装置或其它装置。在一些实施例中,装置衬底10包含半导体衬底,例如块状半导体衬底。块状半导体衬底包含元素半导体,例如硅或锗;化合物半导体,例如硅锗、碳化硅、砷化镓、磷化镓、磷化铟、或砷化铟;或其组合物。在一些实施例中,衬底包含多层衬底,例如绝缘体上硅(silicon-on-insulator,soi)衬底,其包含底部半导体层、包埋的氧化物层(buriedoxidelayer,box)以及顶部半导体层。在其它的一些实施例中,衬底包含绝缘衬底,例如玻璃衬底、导电衬底、或任何其它合适的衬底。
在一些实施例中,装置衬底10为具有标准直径与厚度的晶片。例如,装置衬底10为八英寸晶片、十二英寸晶片、或其它尺寸的晶片。例如,装置衬底10的厚度为约725微米,但并不以此为限。
在一些实施例中,可从第二表面102任选地将装置衬底10图案化以形成凹槽(notch)120h。可通过蚀刻、激光钻孔、或任何其它图案化技术,形成凹槽102h。凹槽102h为第二表面102中的凹部、沟槽、或凹痕(indent),并且不穿过装置衬底10。在一些实施例中,凹槽102h位于预定的切割线,装置衬底10沿着所述预定的切割线待切割。凹槽102h为用于确保在切割操作(也称为单粒化(singulation)操作)过程中,装置衬底10基本沿着凹槽102h被切割而不沿着其它方向破裂。
如图2b与图1的操作120所示,方法100继续进行操作120,在操作120中,接收载体衬底20,其具有彼此对置的第三表面203和第四表面204。载体衬底20为晶片或衬底作为载体或支撑体,以在运送或制造过程中携载、支撑、或握持装置衬底10。载体衬底20的尺寸、材料或特性与装置衬底10的尺寸、材料或特性可相同或不同。在一些实施例中,载体衬底20可重复使用。
在一些实施例中,可从第四表面204任选地图案化载体衬底20,以形成凹槽204h。在一些实施例中,形成对应于凹槽102h的凹槽204h,并且凹槽204h具有与凹槽102h相同的功能性。
如图2c与图1的操作130所示,方法100继续进行操作130,在操作130中,在载体衬底20的第三表面203与装置衬底10的第二表面102之间,形成中间层22。在一些实施例中,在将装置衬底10的第二表面102附接到载体衬底20的第三表面203之前,在载体衬底20的第三表面203上方,形成中间层22。在一些其它的实施例中,在将装置衬底10的第二表面102附接到载体衬底20的第三表面203之前,在装置衬底10的第二表面102上,形成中间层22。在一些实施例中,中间层22为图案化的中间层,其具有开口22h以暴露载体衬底20的第三表面203的一部分。在一些其它的实施例中,中间层22未被图案化,并且基本覆盖载体衬底20的整个第三表面203与装置衬底10的第二表面102。
如图2d与图1的操作140所示,方法100继续进行操作140,在操作140中,将装置衬底10的第二表面102附接到载体衬底20的第三表面203。例如,通过熔融接合或任何其它合适的直接或间接接合技术,可接合装置衬底10与载体衬底20。在一些实施例中,中间层22是有粘着性的,且通过中间层22接合装置衬底10与载体衬底20。中间层22位于装置衬底10与载体衬底20之间,并且作为载体衬底20与装置衬底10之间的牺牲释放层。牺牲释放层暂时粘附于载体衬底20与装置衬底10之间,因而装置衬底10可受到载体衬底20支撑并且被薄化到预定厚度,以满足所要形成的装置的需求。在薄化装置衬底10且在装置衬底10上方形成装置之后,接着将自载体衬底20和/或装置衬底10脱离牺牲释放层。在一些实施例中,中间层22为电介质材料,例如氧化硅、氮化硅、氮氧化硅、或任何其它合适的材料。在一些实施例中,中间层22的材料以及载体衬底20与装置衬底10的材料具有不同的蚀刻选择性。
如图2e与图1的操作150所示,方法100继续进行操作150,在操作150中,从第一表面101薄化装置衬底10。在一些实施例中,将装置衬底10薄化到一预定厚度,以符合装置的需求,所述装置例如欲形成的mems装置。在一些实施例中,薄化的装置衬底10之预定厚度范围大致为从约50微米到约400微米。如果没有载体衬底20,那么在标准的半导体设备中,难以握持如此薄厚度的装置衬底10,晶片破裂的风险增加。然而,由于受到载体衬底20支撑,装置衬底10可与标准半导体设备与制造相容。可通过任何机械和/或化学薄化技术,例如研磨、抛光或蚀刻,薄化装置衬底10。
如图2f与图1的操作160所示,方法100继续进行操作160,在操作160中,在装置衬底20的第一表面101上方,形成装置30。装置30可为mems装置、半导体装置、电子装置、机械装置、主动装置、被动装置、其组合、或任何其它的装置。在一些实施例中,装置30包含mems装置,例如音响装置(acousticdevice)。在一些实施例中,装置30包含mems装置,例如音响装置(acousticdevice),以及主动装置,例如cmos装置,以用于处理mems装置产生的信号。例如,音响装置为麦克风装置或超音波装置,其为用于感测声波并且将声波转换为电子信号。
在一些实施例中,在装置衬底10的第一表面101上方形成装置30包含形成多个电介质层31与导电层32的薄膜堆叠。电介质层31与导电层32可交替形成。在一些实施例中,导电层32至少包含板与隔膜(diaphragm),且板与隔膜之间由至少一电介质层31相隔。在本发明中,导电层32包含第一板41、隔膜42、以及第二板43,其中隔膜42插在第一板41与第二板43之间。第一板41与第二板43作为电极。在一些实施例中,可省略第一板41或第二板43其中之一。隔膜42也称为膜(membrane)。
在一些实施例中,隔膜42为导电性或半导体性。例如,隔膜42由半导体材料形成,例如多晶硅或任何其它合适的半导体材料并且掺杂p型、n型掺质、或具导电性的类似者。在一些实施例中,隔膜42由电介质材料或以导电材料覆盖之半导体材料形成。在一些实施例中,隔膜42包含孔洞42h以调节隔膜42的共振形式和/或防止隔膜42因过大的压力而破裂。
第一板41与第二板43为导电性的或半导体性的。在一些实施例中,第一板41或第二板43由半导体材料形成,例如多晶硅与掺杂p型、n型掺质、或具导电性的类似者。在一些实施例中,第一板41或第二板43由电介质材料或导电材料覆盖之半导体材料形成。在一些实施例中,第一板41或第二板43可为单层结构。在一些实施例中,第一板41或第二板43可为多层结构,其包含导电材料层与至少一绝缘层。例如,多层结构包含氮化硅层与硅层(sin/si)的薄膜堆叠,或氮化硅层、硅层、以及另一氮化硅层(sin/si/sin)的薄膜堆叠。
在一些实施例中,第一板41包含通气孔41h,且/或第二板43包含通气孔43h。通气孔41h与43h用于调节隔膜42的共振形式和/或防止隔膜42因过大的压力而破裂。
电介质层31用作牺牲结构层。牺牲结构层经形成以用以支撑或包围包含隔膜42与板的导电层32,所述板例如第一板41和第二板43。牺牲结构层暂时形成于导电层32之间,因而在制造过程中,导电层32可受支撑。而后,移除各个牺牲结构层的一部分,因而隔膜42与第一板41和第二板43的各者之间存在空气间隙。电介质层31的材料包含半导体氧化物(例如氧化硅)、半导体氮化物(例如氮化硅)、半导体氮氧化物(氮氧化硅)、或任何其它合适的电介质材料。在一些实施例中,电介质层31的材料以及载体衬底20与装置衬底10的材料具有不同的蚀刻选择性。在一些实施例中,电介质层31与中间层22可包含相同的电介质材料。
在一些实施例中,在薄膜堆叠上方,形成多个连接垫34与蚀刻停止层36。连接垫34用作装置30外部或内部的连接部件。在一些实施例中,连接垫34分别电连接到第一板41与第二板43。连接垫34也可电连接到另一结构,例如防护环(guardring)。连接垫34的材料可包含金属,例如金(au)、合金,例如铝铜(alcu)、或任何其它导电材料。蚀刻停止层36用于当蚀刻电介质层31时,保护连接垫34免于受到蚀刻或破坏。在一些实施例中,蚀刻停止层36分别覆盖连接垫34的横侧。
如图2g与图1的操作170所示,方法100继续进行操作170,在操作170中,从第四表面204图案化载体衬底20与装置衬底10,以于载体衬底20、中间层22、以及装置衬底10中形成空腔10c(也称为背腔室)。在一些实施例中,装置20包含电容式麦克风装置或电容式超音波装置,以及空腔10c用作共振腔室。可基于不同考量,例如灵敏性、信噪比、频率响应以及其它因素,而修改形状、尺寸与深度。在一些实施例中,空腔10c的侧壁基本垂直于装置衬底10的第二表面102,也就是说,载体衬底20中的空腔10c与装置衬底10中的空腔10c具有相同尺寸。在一些其它的实施例中,空腔10c的侧壁相对于装置衬底10的第二表面102倾斜。例如,装置衬底10中的空腔10c的尺寸小于载体衬底20中的空腔10c的尺寸。可通过蚀刻,例如干式蚀刻和/或湿式蚀刻,形成空腔10c。在一些实施例中,在相同的蚀刻操作中,蚀刻去除空腔10c所暴露的中间层22。
方法100可继续进行以下操作。如图2h所示,经由空腔10c以及经由装置30的顶部表面(与空腔10c对置的表面),蚀刻各个电介质层31的一部分以悬挂(suspend)隔膜42。在移除所述部分的电介质层31之后,在隔膜42与板41之间以及隔膜42与第二板43之间,形成空气间隙。据此,隔膜42与第一板41和第二板43相隔,因而可相对于第一板41和/或第二板43移动。因此,隔膜42可受到声压而共振。在一些实施例中,沿着各个电介质层31的所述部分,同时蚀刻去除部分的中间层22。在此例子中,中间层22与载体衬底20之间的接触面积减少,因而可轻易地从载体衬底20拾取装置衬底10。
如图2i所示,载体衬底20的第四表面204附接到薄膜(film)26。在一些实施例中,薄膜26为粘性膜,例如胶带,其可粘附到载体衬底20。在一些实施例中,薄膜26为与载体衬底20的第四表面204基本齐平。而后,进行切割操作以沿着切割线切割装置衬底10,因而装置衬底10分为数片,而装置衬底10的各片仍附接到载体衬底20而无散落。
在一些实施例中,未沿着装置衬底10切割载体衬底20。在一些其它的实施例中,也沿着装置衬底10切割载体衬底20,因而载体衬底20被分为数片。在一些实施例中,通过激光切割或任何合适的切割技术,达成装置衬底10与载体衬底20的切割。装置衬底10的凹槽102h与载体衬底20的凹槽204h为用于在切割操作中防止装置衬底10与载体衬底20沿着其它横向破裂。
如图2j所示,装置30与装置衬底10的各片在载体衬底20被拾取并且与载体衬底20分隔。据此,制造出装置结构50,例如mems结构。在一些实施例中,中间层22或部分的中间层22保留在装置衬底10的第二表面102上,因而在装置衬底10的第二表面102上形成凸块24。凸块24的图案可规则或不规则分布。
本发明的制造结构的方法并不限于上述实施例,并且可具有其它不同的实施例。为了简化说明并且便于比较本发明的各个实施例,以下实施例中相同的元件以相同的元件符号标示。为了使其更容易比较实施例之间的差异,以下说明将详述不同实施例之间的相异之处,并且不再冗余描述相同的特征。
图3a、3b和3c为根据本发明的一些实施例说明制造结构的各种操作中的一者的横截面图。如图3a所示,不同于图2a到2j的实施例,在附接装置衬底10的第二表面102到载体衬底20的第三表面203之前,图案化中间层22以形成凹部22t。凹部22t为用于预先调节中间层22与载体衬底20之间的接触面积。
如图3b所示,凭借凹部22t(未绘示),随着蚀刻电介质层31,中间层22与载体衬底20之间的接触面积将会减少到所要值。据此,中间层22与载体衬底20之间的粘附降低到所要值以利于后续的脱膜(releasing)操作。而后,在装置衬底10上,形成装置30。
如图3c所示,载体衬底20的第四表面204附接到薄膜26。接着,进行切割操作以切割装置衬底10,因而装置衬底10分为数片,而装置衬底10的各片仍附接到载体衬底20而未散落。装置30与装置衬底10的各片从载体衬底20被拾取并且与载体衬底20分隔。据此,制造装置结构60。在一些实施例中,中间层22或部分的中间层22保留在装置衬底10的第二表面102上,因而在装置衬底10的第二表面102上形成凸块24。凸块24的图案可规则或不规则分布。
图4a和4b为根据本发明的一些实施例说明制造结构的各种操作之一的横截面图。如图4a所示,不同于图2a到2j的实施例,图案化载体衬底20以形成沟槽20a,以及图案化装置衬底10以形成通路孔10a。沟槽20a与通路孔洞10a一起形成空腔10c,并且沟槽20a的尺寸大于通路孔10a的尺寸。在一些实施例中,通过多阶段蚀刻,形成沟槽20a与通路孔10a,以及各个蚀刻阶段可为湿式蚀刻或干式蚀刻。沟槽20a的侧壁可基本垂直于载体衬底20的第四表面204或相对于载体衬底20的第四表面204倾斜。通路孔10a的侧壁可基本垂直于装置衬底10的第二表面102或相对于装置衬底10的第二表面102倾斜。
而后,载体衬底20附接到薄膜26。在一些实施例中,薄膜26的一部分附接到载体衬底20的第四表面204,以及薄膜26的另一部分附接到装置衬底10的第二表面102。
如图4b所示,进行切割操作以切割装置衬底10,因而装置衬底10分为数片,而装置衬底10的各片仍附接到载体衬底20而未散落。装置30与装置衬底10的各片从载体衬底被拾取,并且与载体衬底20分隔。据此,制造装置结构70。
在本发明的方法中,装置结构受到载体衬底支撑,因而可被薄化到预定厚度,满足一些装置的需求,例如mems装置和/或半导体装置。受到载体衬底支撑的薄化的装置衬底与标准半导体工艺与设备可相同,而不增加破裂风险。
在一例示方面,提供制造结构的方法。所述方法包含以下操作。接收具有彼此对置的第一表面与第二表面的装置衬底。接收具有彼此对置的第三表面与第四表面的载体衬底。在载体衬底的第三表面与装置衬底的第二表面之间,形成中间层。装置衬底的第二表面附接到载体衬底的第三表面。从第一表面薄化装置衬底。在装置衬底的第一表面上方,形成装置。从第四表面图案化载体衬底与装置衬底,以于载体衬底、中间层、以及装置衬底中,形成空腔。
在另一例示方面,提供制造mems结构的方法。所述方法包含以下操作。提供衬底,所述衬底具有载体衬底、装置衬底、以及插在其间的中间层。中间层具有多个凹部。薄化装置衬底。在装置衬底上方,形成mems装置,其中mems装置包括隔膜、重叠于所述隔膜的板、以及包围所述隔膜与所述板的至少一电介质层。蚀刻所述衬底,以形成暴露所述电介质层的空腔。蚀刻所述电介质层的一部分以暴露所述隔膜与所述板,并且同时蚀刻所述中间层的一部分。
在另一方面,提供mems结构。mems装置包含衬底、板、隔膜、空腔、以及凸块。所述衬底具有第一表面与第二表面。所述板为位于所述衬底的第一表面上方。所述隔膜为位于衬底的第一表面上方。所述空腔为形成于衬底中并且暴露所述板与所述隔膜。所述凸块为位于衬底的第二表面上。
前述内容概述一些实施方式的特征,因而熟知此技艺的人士可更好地理解本发明的各方面。熟知此技艺的人士应理解可轻易使用本发明作为基础,用于设计或修饰其它工艺与结构而实现与本申请案所述的实施例具有相同目的和/或达到相同优点。熟知此技艺的人士也应理解此均等架构并不脱离本发明揭示内容的精神与范围,并且熟知此技艺的人士可进行各种变化、取代与替换,而不脱离本发明的精神与范围。
本文用于企业家、创业者技术爱好者查询,结果仅供参考。