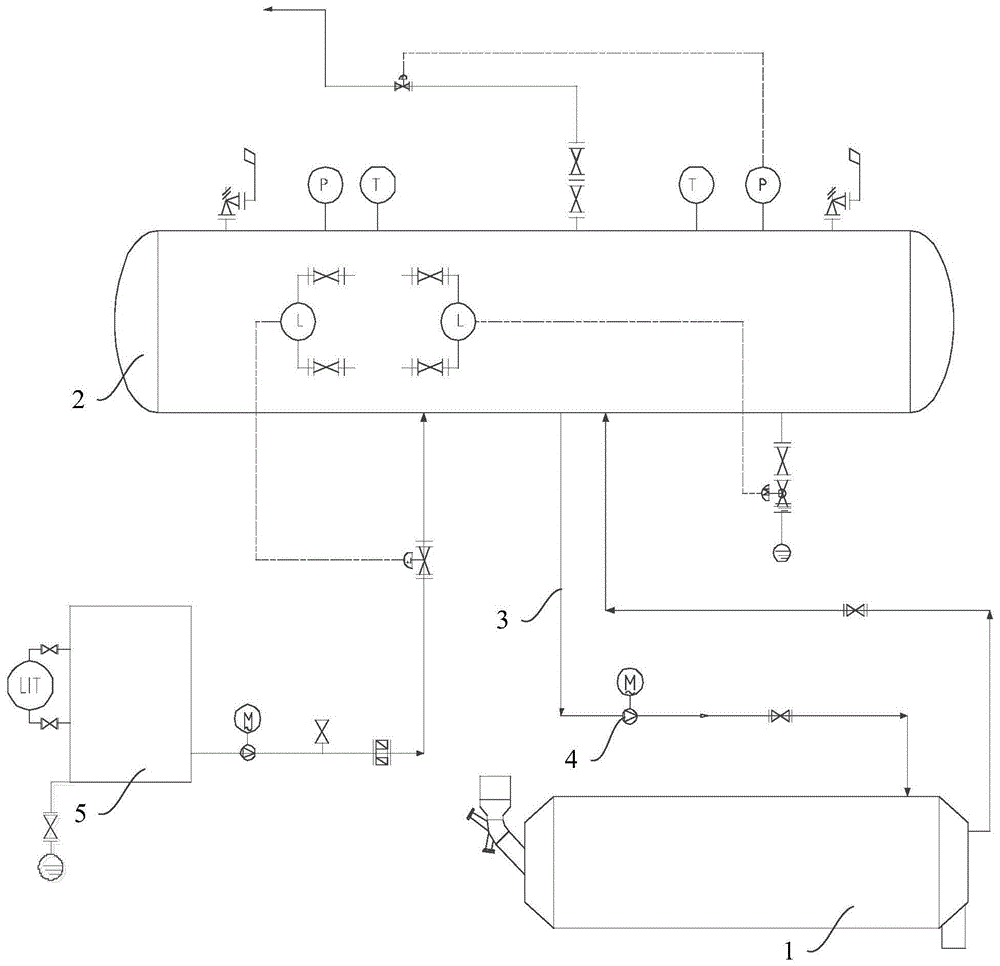
本发明涉及余热回收技术领域,特别涉及一种冶金渣余热回收装置。
背景技术:
冶金废渣是指冶金工业生产过程中产生的各种固体废弃物。目前,冶金渣的余热回收装置和回收方法较少,有热闷余热回收工艺、篦冷式余热回收工艺、竖式余热回收工艺等。
热闷余热回收工艺是将高温态冶金渣放入压力容器内,并在容器内直接打水产生蒸汽,该工艺水耗量及排污量较大,蒸汽中含有大量污染物,无法直接利用该蒸汽。篦冷式余热回收工艺是将高温态冶金渣放入专用篦冷车内,鼓风机从下部送入冷风,与高温态冶金渣换热后的热风从上部排出,送入余热锅炉生产蒸汽。该工艺漏风率较高,换热效率低,且烟风含尘量较大,工业化可行性较低。竖式余热回收工艺是将高温态冶金渣放入竖式容器内,鼓风机或循环风机从下部送入冷风,与高温态冶金渣换热后的热风从上部排出,送入余热锅炉生产蒸汽,该工艺风压损失较大,能耗较高,且烟风含尘量较大,经济效益差,不适合现有工业化生产。
技术实现要素:
为了解决以上冶金渣余热回收时能量回收率低、能耗高和污染严重的技术问题,本发明提供一种冶金渣余热回收装置,该冶金渣余热回收装置包括:
换热设备,所述换热设备具有容纳冶金渣的筒体和多个沿轴向延伸布置于所述筒体内部的换热管;
蒸汽发生器,所述蒸汽发生器设置于所述换热设备的上方;
其中,所述蒸汽发生器开设有进水口、与所述换热管的出口端相连通的热除盐水入口、以及与所述换热管的进口端相连通的下降口;
所述换热管内来自于所述下降口的除盐水与冶金渣换热后通过所述热除盐水入口返回所述蒸汽发生器内,以使得来自所述进水口的除盐水在所述蒸汽发生器和所述换热管之间实现循环;
所述蒸汽发生器还设置有出汽管线,所述出汽管线用于排出除盐水换热后产生的蒸汽。
可选地,多个所述换热管在所述筒体内的内壁面处周向均匀布置。
可选地,所述换热管的外壁面设置有导向片,所述导向片自所述换热管的外壁面向与所述筒体的径向呈预设角度的方向延伸。
可选地,所述下降口与所述换热管的进口端通过下降管相连,所述下降管安装有循环泵,所述循环泵将所述蒸汽发生器内的除盐水泵送至所述换热管内,以实现除盐水在所述蒸汽发生器和所述换热管之间的强制循环。
可选地,还包括除盐水设备,所述除盐水设备通过给水管线连接至所述进水口。
可选地,还包括动力设备;
所述动力设备与所述换热设备的所述筒体传动连接,以带动所述筒体沿自身轴线转动。
可选地,所述动力设备的输出端设置有主动齿轮,所述筒体的外周设置有被动齿轮,所述主动齿轮通过链条带动所述被动齿轮转动。
可选地,还包括用于支撑所述筒体的支座,所述筒体可转动地安装于所述支座。
可选地,所述蒸汽发生器还设置有排水管线和液位变送器,所述给水管线和所述排水管线均设置有水量调节阀;
所述液位变送器联锁调节所述调节阀以及安装于所述给水管线的给水泵。
可选地,所述蒸汽发生器的顶部设置有压力变送器;
所述压力变送器联锁调节设置于所述出汽管线的汽量调节阀。
由以上技术方案可知,本发明的冶金渣余热回收装置包括换热设备和蒸汽发生器,换热设备筒体内的冶金渣与换热管内的除盐水热交换,冶金渣温度降低被排出进入下级工序,而换热管内的除盐水进入蒸汽发生器,通过蒸汽发生器的出汽管线输送至用户,该余热回收过程不需要外加能耗,仅仅消耗冶金渣本身的热量,也不会产生污水或者粉尘等污染物,冶金渣中的能量回收利用率高,实现了能量的循环利用。
附图说明
以下附图仅对本发明做示意性说明和解释,并不限定本发明的范围。
图1为本发明实施例的冶金渣余热回收装置整体结构示意图。
图2为本发明实施例的蒸汽发生器示意图。
图3为本发明实施例的换热设备示意图。
图4为本发明实施例的换热设备纵截面剖视图。
图5为本发明实施例的换热设备侧视图。
图6为本发明实施例的除盐水设备示意图。
其中:
1换热设备
101筒体;101a冶金渣入口;101b冶金渣出口
102换热管;103导向片;104支座;105滚轮
2蒸汽发生器
201热除盐水入口;202出汽管线;203进水口;204下降口;205排水管线;206液位变送器;207水量调节阀;208压力变送器;209汽量调节阀;210安全阀
3下降管
4循环泵
5除盐水设备
501给水管线;502给水泵;503给水流量变送器;504排污阀
6动力设备
601主动齿轮;602被动齿轮;603链条
p压力变送器;t温度表;l液位变送器或液位计;m泵;f流量计
具体实施方式
为了对发明的技术特征、目的和效果有更加清楚的理解,现对照附图说明本发明的具体实施方式,在各图中相同的标号表示相同的部分。
在本文中,“示意性”表示“充当实例、例子或说明”,不应将在本文中被描述为“示意性”的任何图示、实施方式解释为一种更优选的或更具优点的技术方案。
为使图面简洁,各图中的只示意性地表示出了与本发明相关部分,而并不代表其作为产品的实际结构。另外,以使图面简洁便于理解,在有些图中具有相同结构或功能的部件,仅示意性地绘示了其中的一个,或仅标出了其中的一个。
在本文中,“上”、“下”、“前”、“后”、“左”、“右”等仅用于表示相关部分之间的相对位置关系,而非限定这些相关部分的绝对位置。
在本文中,“第一”、“第二”等仅用于彼此的区分,而非表示重要程度及顺序、以及互为存在的前提等。
在本文中,“相等”、“相同”等并非严格的数学和/或几何学意义上的限制,还包含本领域技术人员可以理解的且制造或使用等允许的误差。除非另有说明,本文中的数值范围不仅包括其两个端点内的整个范围,也包括含于其中的若干子范围。
为了解决现有技术中对冶金渣余热回收时能量回收率低、能耗高和污染严重的技术问题,如图1所示,本发明的实施例提供了一种冶金渣余热回收装置,该冶金渣余热回收装置包括换热设备1和蒸汽发生器2。
换热设备1具有容纳冶金渣的筒体101和多个沿轴向延伸布置于筒体101内部、并用于与冶金渣热交换的换热管102,可以理解的是,换热管102内部有除盐水,外部则为高温的冶金渣,并且冶金渣与除盐水是相互隔绝的,二者通过换热管102进行热交换,换热完成后,冶金渣温度降低,同时换热管102内的除盐水吸热。
蒸汽发生器2设置于换热设备1的上方,具体可以是正上方,也可以是侧上方,总之,蒸汽发生器2的位置高于换热设备1的位置。如图2所示,蒸汽发生器2开设有与换热管102的出口端相连通的热除盐水入口201、以及设置于顶部的出汽管线202,除盐水自热除盐水入口201进入蒸汽发生器2内部汽化产生水蒸气,水蒸气经顶部的出汽管线202输送至用户处。
蒸汽发生器2开设有进水口203、与换热管102的出口端相连通的热除盐水入口201、以及与换热管102的进口端相连通的下降口204;
换热管102内来自于下降口204的除盐水与冶金渣换热后通过热除盐水入口201返回所述蒸汽发生器2内,以使得来自进水口203的除盐水在蒸汽发生器2和换热管102之间实现循环;
蒸汽发生器2还设置有出汽管线202,出汽管线202用于排出除盐水换热后产生的蒸汽。
蒸汽发生器2还开设有用于除盐水进入的进水口203、以及与换热管102的进口端相连通的下降口204,以使得来自进水口203的除盐水在蒸汽发生器2和换热管102之间实现循环,具体该循环是指除盐水自进水口203进入蒸汽发生器2,并通过下降口204进入换热管102,除盐水在换热管102内与冶金渣热交换吸热,吸热后的除盐水通过热除盐水入口201进入蒸汽发生器2内汽化为水蒸气,水蒸气通过顶部的出汽管线202输送至用户处。
如图3所示,该筒体101开设有冶金渣入口101a和冶金渣出口101b,高温冶金渣自冶金渣入口101a进入筒体101内,在筒体101内与换热管102内的除盐水热交换后温度降低,通过冶金渣出口101b排出。
本发明所指的冶金渣为高炉渣、转炉渣和电炉渣中的一种或者多种的混合物,并且来自上级工序的冶金渣为高温颗粒状固体,固体颗粒在换热设备内部换热后形态不变,自冶金渣出口101b排出进入下级工序。
本发明的冶金渣余热回收装置包括换热设备和蒸汽发生器,换热设备筒体内的冶金渣与换热管内的除盐水热交换,冶金渣温度降低被排出进入下级工序,而换热管内的除盐水进入蒸汽发生器,通过蒸汽发生器的出汽管线输送至用户,该余热回收过程不需要外加能耗,仅仅消耗冶金渣本身的热量,也不会产生污水或者粉尘等污染物,冶金渣中的能量回收利用率高,实现了能量的循环利用。该冶金渣余热回收装置热回收效率高,处理时间短,不消耗水资源,不产生大气污染,生产的动力蒸汽可为工业企业其它工序提供热能或直接用于发电。
上述的多个换热管102可以是在筒体101内的内壁面处周向均匀布置,附图中换热管102仅仅设置了一圈,当然,换热管102可以不仅仅是设置一圈,分层次设置多圈也是可以的,换热管102的外壁面并不与筒体101的内壁面接触,具体换热管102如何固定,本领域技术人员可以选择管板安装,并且管板可以将换热管102内的除盐水与冶金渣分开。筒体101的冶金渣入口101a由耐热钢制成,冶金渣出口101b与下序工艺密封对接,可将换热后的冶金渣在密闭状态排出。
进一步地,换热管102的外壁面设置有导向片103,如图4所示,该导向片103固定于换热管102的外壁面,具体可以是导向片103竖立于换热管的外壁面,并且导向片103自换热管102的外壁面向与筒体101的径向呈预设角度倾斜的方向延伸,即导向片103并不是自换热管102的外壁面沿筒体101的径向向筒体101的轴线处延伸,导向片103的延伸方向与筒体101的径向存在一定夹角。导向片103可以增加冶金渣在筒体101内的轴向流动,增加换热管102与冶金渣的换热接触时间,提高换热系数,进而提高冶金渣的能量回收利用率。
此外,导向片103也可以是以规律曲折延伸的形式设置于换热管102的外壁面,具体导向片103可以是通过焊接固定于换热管102的外表面。
具体地,蒸汽发生器2的下降口204与换热管102的进口端通过下降管3相连,下降管3安装有循环泵4,循环泵4将蒸汽发生器2内的除盐水泵送至换热管102内,换热管102内压力增加,使得除盐水压力增大,可以使得除盐水顺利进入蒸汽发生器,以实现除盐水在蒸汽发生器2和换热管102之间的强制循环。
在可选示例中,如图5所示,该冶金渣余热回收装置还可以包括动力设备6。动力设备6与换热设备1的筒体101传动连接,以带动筒体101沿自身轴线转动。动力设备6可以是并列设置的多套,并且均与筒体101传动连接,使得筒体101自转,在筒体101自转时可以增加内部冶金渣的流动,增大冶金渣与换热管102之间的换热系数,提高冶金渣与除盐水的换热效果。
该动力设备6与筒体101可以是通过齿轮链条传动连接。具体地,动力设备6的输出端设置有主动齿轮601,筒体101的外周设置有被动齿轮602,主动齿轮601通过链条603带动被动齿轮602转动。使用时,动力设备6带动主动齿轮601转动,主动齿轮601带动链条603移动,链条603带动被动齿轮602转动,筒体101随被动齿轮602同步转动。当然,筒体101可以是小角度转动。该动力设备6可以是电机。
该换热设备1还包括用于支撑筒体101的支座104,筒体101可转动地安装于支座104,具体可以是筒体101通过轴承安装于支座104,筒体101可相对支座104转动。也可以是支座104设置滚轮105,筒体101支撑于滚轮105,并可相对于滚轮105滚动。
如图6所示,该冶金渣余热回收装置还可以包括除盐水设备5,并且除盐水设备5通过给水管线501连接至进水口203,除盐水设备5通过给水管线501向蒸汽发生器2供给除盐水。
进一步地,给水管线501设置有水量调节阀207,用于调节除盐水的供应流量。此外,蒸汽发生器2还设置有排水管线205和液位变送器206,排水管线205设置于蒸汽发生器2的底部,用于配合调节蒸汽发生器2内的总水量,当蒸汽发生器2内的水量超过预设水位时,可以通过给水管线205排出多余的水,该预设水位可以是蒸汽发生器2总容积的百分之六十,当然,排水管线205也设置有水量调节阀207,用于调节蒸汽发生器2的给水量。
除盐水设备5的给水管线501还设置有给水流量变送器503,给水流量变送器503实时监测给水管线501内的水流量,联锁控制除盐水设备的制水量,保证除盐水的稳定供给。当然,除盐水设备5也可以装设有液位计。
除盐水设备5还可设置排污阀504,用于排出其内部的残余污水。
液位变送器206用于实时监控测量蒸汽发生器2内的水位,并联锁调节调节阀207以及安装于给水管线501的给水泵502。当液位变送器206监测到蒸汽发生器2内的水位超过预设阈值范围时,通过联锁调节调节阀207和给水泵502调节蒸汽发生器2内的进出水量,保证蒸汽发生器2内的水位处于预设阈值范围。
在蒸汽发生器2的顶部设置有压力变送器208,用于实时监测蒸汽发生器2内的压力波动;蒸汽发生器2的出汽管线202设置有汽量调节阀209,用于调节蒸汽发生器2内的蒸汽输出量。该压力变送器208联锁调节汽量调节阀209,即当压力变送器208监测到蒸汽发生器2内的压力变化超过预设阈值范围时,压力变送器208通过调节汽量调节阀209的开度调整蒸汽输出速率,进而调整蒸汽发生器2内的压力。
蒸汽发生器2的顶部还设置有安全阀210,当蒸汽发生器2内的压力高于预设压力时,该安全阀210可自行打开泄压。
此外,蒸汽发生器2还可以设置测温口和加药口,这些都是本领域技术人员根据常规选择可以实现的,此处不再赘述。
工作时,高温态冶金渣通过冶金渣入口进入筒体101内,筒体101的轴向旋转可使内部设置的导向片将冶金渣从筒体101的一端缓慢的运送到另一端,在这一过程中,冶金渣与换热管102充分接触,与换热管102内逆向流动的除盐水进行热交换;下降管3的循环泵4将上述换热后的除盐水送入蒸汽发生器2,实现在蒸汽发生器2内产生蒸汽,释放蒸汽后的除盐水被再次送入换热管102,实现换热的下一次循环;蒸汽发生器2内产生的饱和蒸汽送至相关用户,以实现余热的再利用。
应当理解,虽然本说明书是按照各个实施方式描述的,但并非每个实施方式仅包含一个独立的技术方案,说明书的这种叙述方式仅仅是为清楚起见,本领域技术人员应当将说明书作为一个整体,各实施方式中的技术方案也可以经适当组合,形成本领域技术人员可以理解的其他实施方式。
上文所列出的一系列的详细说明仅仅是针对本发明的可行性实施方式的具体说明,而并非用以限制本发明的保护范围,凡未脱离本发明技艺精神所作的等效实施方案或变更,如特征的组合、分割或重复,均应包含在本发明的保护范围之内。
本文用于企业家、创业者技术爱好者查询,结果仅供参考。