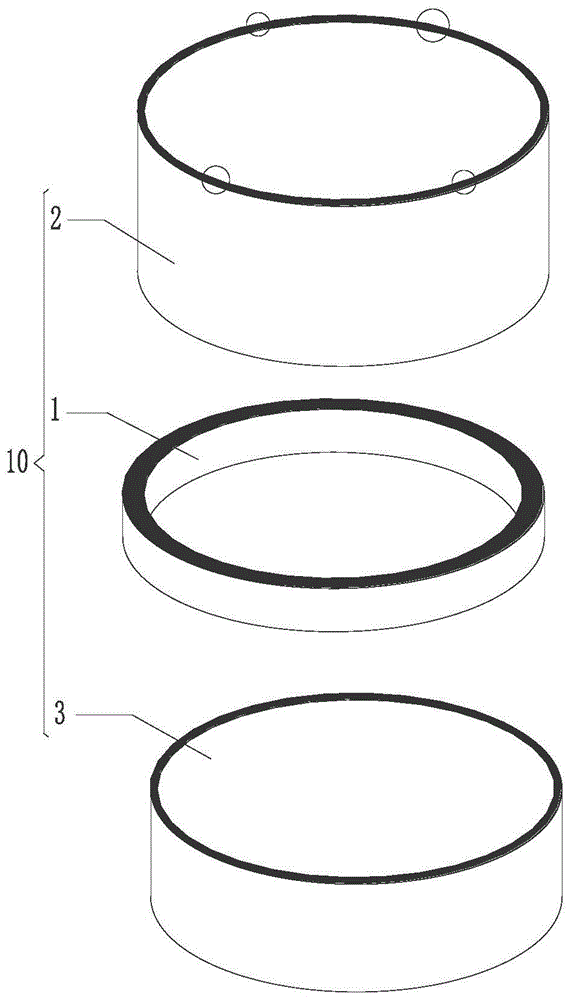
本发明涉及船舶领域,特别涉及一种船舶双角度舵桨法兰与筒体的组装方法。
背景技术:
一般含舵桨装置且舵桨装置具备双角度技术要求的船舶,其舵桨装置的安装精度要求较高。
舵桨装置一般包含舵桨设备与舵桨法兰基座两部分,且舵桨法兰基座由舵桨法兰、上下筒体组成。
舵桨法兰、上下筒体与船体结构相连接,且舵桨法兰、上下筒体必须按照双角度的技术要求先定位、安装,其安装后的精度偏差决定了后续舵桨设备是否能正确安装到位。为了降低舵桨装置安装的精度偏差风险,目前主要采用的安装方法为在船坞阶段船舶轴系拉线望光后,将与船体结构相连接的上筒体、舵桨法兰、下筒体按顺序分别进行吊装并定位安装,每次吊装需对上筒体、舵桨法兰、下筒体轴系中心点以及双角度数值进行多次测量和精度校核,保证法兰、筒体的精度误差控制在工艺要求之内后,才能安装舵桨设备。
船坞阶段作业,由于舵桨法兰、上下筒体尺寸较大,重量较重,在船坞搭载阶段安装舵桨法兰、上下筒体需要高空车、汽车吊、大型门座吊全程配合,安装定位过程需利用船舶外板上的吊码和手工葫芦辅助拉进定位,每安装一个筒体或法兰后,需对其进行精度测量,保证精度基本满足技术要求后才能吊装另外一个,而且需在舵桨装置上方的船体外板上安装临时吊码,且相应的吊码装焊作业需高空车全程配合。舵桨法兰、筒体的吊装作业需汽车吊、高空车、大型门座吊、大量人力投入配合,在船坞阶段操作难度较大,定位安装效率较低。
船坞阶段作业,舵桨法兰、上下筒体附近的空间有限,高空车、汽车吊占据的面积较大,交叉作业复杂,且舵桨法兰、上下筒体较重,作业的危险度相对较高,安全系数差。
船坞阶段作业,由于舵桨法兰、上下筒体的轴系对中精度要求较高,每一个法兰或筒体在船坞内定位、安装都需要花费很长时间,影响舵桨装置安装完整的时间,进而使船坞周期滞后。
技术实现要素:
基于此,有必要提供效率高且安全性好的船舶双角度舵桨法兰与筒体的组装方法。
为解决上述技术问题,本发明提供一种船舶双角度舵桨法兰与筒体的组装方法,包括以下步骤:
取舵桨法兰、上筒体和下筒体,将所述上筒体焊接在所述舵桨法兰的上表面,将所述下筒体焊接在所述舵桨法兰的下表面,焊接后,所述舵桨法兰、上筒体和下筒体形成一个同轴的筒体;
安装划线板,使划线板的下表面与舵桨法兰下表面的中心点c相平齐,并将c点在所述划线板上标记出来;
在所述筒体上划出斜向横剖面线,所述斜向横剖面线为所述筒体的立轴中心线在所述筒体上左侧或者右侧的投影;
找出中心点c在所述斜向横剖面线上的投影点e,以投影点e为转轴,将所述斜向横剖面线的上端向后端旋转角度a°,形成正向横剖线,并在所述筒体的外表面划出正向横剖线;
在所述筒体上划出斜向纵剖面线,所述斜向纵剖面线为所述筒体的立轴中心线在所述筒体上前端或者后端的投影;
找出中心点c在所述斜向纵剖面线上的投影点f,以投影点f为转轴,将所述斜向纵剖面线的上端向左侧旋转角度b°,形成正向纵剖线,并在所述筒体的外表面划出正向纵剖线。
作为上述实施例的进一步改进,取舵桨法兰、上筒体和下筒体,将所述上筒体焊接在所述舵桨法兰的上表面,将所述下筒体焊接在所述舵桨法兰的下表面,焊接后,所述舵桨法兰、上筒体和下筒体形成一个同轴的筒体,包括以下步骤:
在舵桨法兰的上表面划出上筒体安装位置线,在舵桨法兰的下表面划出下筒体安装位置;
取下筒体,将舵桨法兰水平放置,且使其下表面朝上,按照预先划好的下筒体安装位置线,将下筒体焊接在所述舵桨法兰的下表面;
取上筒体,将所述舵桨法兰水平放置,使其上表面朝上,按照预先划好的上筒体安装位置线,将所述上筒体焊接在所述舵桨法兰的上表面。
作为上述实施例的进一步改进,在将舵桨法兰、上筒体和下筒体焊接固定之前,先在舵桨法兰的上表面和下表面划出十字线,用于确定舵桨法兰的中轴线,以及筒体的左侧、右侧、前端和后端。
作为上述实施例的进一步改进,焊接所述舵桨法兰、上筒体和下筒体时,先将所述舵桨法兰的下表面朝上,将所述下筒体焊接在所述舵桨法兰的下表面,然后,再将所述舵桨法兰和所述下筒体翻身,使所述舵桨法兰的上表面朝上,再将所述上筒体焊接在所述舵桨法兰的上表面。
作为上述实施例的进一步改进,焊接所述舵桨法兰下筒体时,将舵桨法兰放置在组装平台上进行组装,并使用码板和铁锲对所述舵桨法兰进行定位;
焊接所述舵桨法兰上筒体时,将焊接好的舵桨法兰和下筒体放置在组装平台上,并使用码板固定所述下筒体。
作为上述实施例的进一步改进,在所述筒体内固定工装架,并将所述划线板固定在所述工装架上。
作为上述实施例的进一步改进,所述上筒体的上表面固定有加强件,所述下筒体的下表面也固定有加强件,所述加强件为由多个槽钢焊接而成的“米”字形框架。
作为上述实施例的进一步改进,将所述筒体固定到船体上,所述船体上固定有动力装置;
安装时,找到投影点e的重力垂线,使所述重力垂线与所述斜向横剖面线相重合;
找到找到投影点f的重力垂线,使所述重力垂线与所述斜向纵剖面线相重合。
作为上述实施例的进一步改进,将所述筒体固定在所述船体上之前,进行以下步骤:
以舵桨法兰的下表面所在的面为基准面,所述基准面与所述筒体形成的线为斜向水线;
所述斜向水线以中心点c为转轴尾端向下倾斜a°,形成正向水线,并在筒体外表面划出正向水线;
所述斜向水线以中心点c为转轴向右端向下倾斜b°,形成正向水线,并在筒体外表面划出正向水线。
作为上述实施例的进一步改进,将所述筒体固定到船体上,所述船体上固定有动力装置,所述筒体与所述动力装置固定连接,固定后,所述正向水线呈水平状态;所述动力装置包括动力输出轴,所述中心点c位于所述动力输出轴的中轴线的延长线上。
该方法相对现有的技术有以下优点:
1、舵桨装置的安装流程简单化,节省了舵桨法兰、筒体在船坞阶段吊装作业所需的汽车吊、高空车、大型门座吊等资源投入,对后续船坞阶段的轴系工程和下水工程周期及成本有很大的影响,大大减少的人力资源的投入;
2、有限空间作业地面完成,增加了作业的安全性;
3、减少轴系工程和下水工程的周期及工作量,工序真正前移,缩短了船坞建造周期。
附图说明
通过附图中所示的本发明优选实施例更具体说明,本发明上述及其它目的、特征和优势将变得更加清晰。在全部附图中相同的附图标记指示相同的部分,且并未刻意按实际尺寸等比例缩放绘制附图,重点在于示出本的主旨。
图1为本发明的上筒体、舵桨法兰及下筒体的整体结构图;
图2为本发明优选实施例的上筒体或者下筒体安装加强件后的示意图;
图3为本发明优选实施例的舵桨法兰的俯视(或者仰视)图;
图4为本发明优选实施例的焊接上筒体、舵桨法兰及下筒体的流程示意图;
图5为本发明优选实施例的划出正向横剖线的方法示意图;
图6为本发明优选实施例的划出正向纵剖线的方法示意图;
图7为本发明优选实施例的划出正向水线的方法示意图;
图8为本发明优选实施例船舶的纵向剖面图;
图9为本发明优选实施例的船舶的横向剖线图。
图中:10、筒体;101、斜向横剖面线;102、正向横剖线;103、斜向纵剖面线;104、正向纵剖线;105、斜向水线;106、正向水线;1、舵桨法兰;11、上筒体安装线;2、上筒体;3、下筒体;4、划线板;5、加强件;6、工装架;7、动力装置;71、垂直中心线;72、立轴中心线;8、组装平台;81、码板;82、铁锲。
具体实施方式
为了便于理解本发明,下面将参照相关附图对本进行更全面的描述。
需要说明的是,当一个元件被认为是“连接”另一个元件,它可以是直接连接到另一个元件并与之结合为一体,或者可能同时存在居中元件。本文所使用的术语“安装”、“一端”、“另一端”以及类似的表述只是为了说明的目的。
除非另有定义,本文所使用的所有的技术和科学术语与属于本技术领域的技术人员通常理解的含义相同。本文中说明书中所使用的术语只是为了描述具体的实施例的目的,不是旨在于限制本发明。本文所使用的术语“及/或”包括一个或多个相关的所列项目的任意的和所有的组合。
参考图1-9,本发明提供一种船舶双角度舵桨法兰与筒体的组装方法,包括以下步骤:
参考图1,取舵桨法兰1、上筒体2和下筒体3,将所述上筒体2焊接在所述舵桨法兰1的上表面,将所述下筒体3焊接在所述舵桨法兰1的下表面,焊接后,所述舵桨法兰1、上筒体2和下筒体3形成一个同轴的筒体10;
安装划线板4,使划线板4的下表面与舵桨法兰1下表面的中心点c相平齐,并将c点在所述划线板4上标记出来,作为基准点,安装时,方便校准。
参考图5,在所述筒体10上划出斜向横剖面线101,所述斜向横剖面线101为所述筒体10的立轴中心线72在所述筒体10上左侧或者右侧的投影;优选地,将所述斜向横剖面线101划在所述筒体10的右侧,安装在船舶上时,右侧朝外,方便校准。将筒体10放置于水平面上时,斜向横剖面线101与水平线垂直。
找出中心点c在所述斜向横剖面线101上的投影点e,以投影点e为转轴,将所述斜向横剖面线101的上端向筒体的后端旋转角度a°,形成正向横剖线102,并在所述筒体10的外表面划出正向横剖线102。组装完成后,根据舵桨法兰1表面上标记的前后左右中心线,拉出十字线并引至划线板4上,标记为c点并划在划线板4上,中心点c点即为舵桨法兰1基座定位基点。
参考图6,在所述筒体10上划出斜向纵剖面线103,所述斜向纵剖面线103为所述筒体10的立轴中心线72在所述筒体10上前端或者后端的投影;将筒体10放置于水平面上时,斜向纵剖面线103与水平线垂直。
找出中心点c在所述斜向纵剖面线103上的投影点f,以投影点f为转轴,将所述斜向纵剖面线103的上端向左侧旋转角度b°,形成正向纵剖线104,并在所述筒体10的外表面划出正向纵剖线104。
参考图8和图9,因双角度舵桨装置在舵桨法兰1基座基准点c点位置的纵、横方向均有倾斜角度要求,即纵向倾斜角度为a°,横向倾斜角度为b°,为以斜向横剖线与法兰下端理论基点面的交点为原点,将斜向横剖线的上端向尾旋转角度a°,并将调整后的斜向横剖线堪划在筒体10外围上(即为中心线横向结构安装位置线),定义为正向横剖线102。同样以斜向纵剖线与法兰下端理论基点面的交点为原点,将斜向纵剖线的上端向外侧(左舷筒体10向左侧,右舷筒体10向右侧)旋转角度b°,并将调整后的斜向纵剖线堪划在筒体10外围上(即为中心线纵向结构安装位置线),定义为正向纵剖线104,如图7所示。并做好样冲标记,作为后续舵桨法兰1与筒体10组合体的基准点以及双角度粗定位参考数据。
参考图7,根据正向纵剖线104、正向横剖线102安装预装结构(船体肘板),预装结构的上下位置依据结构图确定;预装结构与筒体10及法兰间仅点焊固定,便于后续法兰精定位后再做调整装焊。
参考图1和图4,作为上述实施例的进一步改进,取舵桨法兰1、上筒体2和下筒体3,将所述上筒体2焊接在所述舵桨法兰1的上表面,将所述下筒体3焊接在所述舵桨法兰1的下表面,焊接后,所述舵桨法兰1、上筒体2和下筒体3形成一个同轴的筒体10,包括以下步骤:
在舵桨法兰1的上表面划出上筒体2安装位置线,在舵桨法兰1的下表面划出下筒体3安装位置;具体地,在舵桨法兰1的上表面划出上筒体2外表面(即外壁)安装位置,并做好样冲标记。焊接上筒体2时可以容易校对位置,减少出现偏差的概率。
取下筒体3,将舵桨法兰1水平放置,且使其下表面朝上,按照预先划好的下筒体3安装位置线,将下筒体3焊接在所述舵桨法兰1的下表面;具体地,在舵桨法兰1的下表面划出下筒体3外表面(即外壁)安装位置,并做好样冲标记。焊接下筒体3时可以容易校对位置,减少出现偏差的概率。
取上筒体2,将所述舵桨法兰1水平放置,使其上表面朝上,按照预先划好的上筒体2安装位置线,将所述上筒体2焊接在所述舵桨法兰1的上表面。焊接结束后,调整焊缝的平整度。
作为上述实施例的进一步改进,在将舵桨法兰1、上筒体2和下筒体3焊接固定之前,先在舵桨法兰1的上表面和下表面划出十字线,用于确定舵桨法兰1的中轴线,以及筒体10的左侧、右侧、前端和后端,避免划线时出现误差。
作为上述实施例的进一步改进,焊接所述舵桨法兰1、上筒体2和下筒体3时,先将所述舵桨法兰1的下表面朝上,将所述下筒体3焊接在所述舵桨法兰1的下表面,然后,再将所述舵桨法兰1和所述下筒体3翻身,使所述舵桨法兰1的上表面朝上,再将所述上筒体2焊接在所述舵桨法兰1的上表面。
作为上述实施例的进一步改进,焊接所述舵桨法兰1下筒体3时,将舵桨法兰1放置在组装平台8上进行组装,并使用码板81和铁锲82对所述舵桨法兰1进行定位。具体地,将舵桨法兰1放置在钢制平台上,下表面朝上,调整水平后用码板81及铁楔固定舵桨法兰1。钢制平台要求平整,确保使舵桨法兰1平整放置。
焊接所述舵桨法兰1上筒体2时,将焊接好的舵桨法兰1和下筒体3放置在组装平台8上,并使用码板81固定所述下筒体3。
作为上述实施例的进一步改进,在所述筒体10内固定工装架6,并将所述划线板4固定在所述工装架6上。具体地,工装架6由20b槽钢组成,用于固定划线板4。
参考图2,作为上述实施例的进一步改进,所述上筒体2的上表面固定有加强件5,所述下筒体3的下表面也固定有加强件5,所述加强件5为由多个槽钢焊接而成的“米”字形框架。具体地,上筒体2、下筒体3材质均为钢结构,需要安装加强件5防止筒体10堆放、运输变形,即分别在上筒体2的上端口和下筒体3的下端口按“米”字交叉形式安装20b槽钢。
参考图8和图9,作为上述实施例的进一步改进,将所述筒体10固定到船体上,所述船体上固定有动力装置7;
安装时,找到投影点e的重力垂线,使所述重力垂线与所述斜向横剖面线101相重合;
找到找到投影点f的重力垂线,使所述重力垂线与所述斜向纵剖面线103相重合。需要说明的是,重力垂线是指将一个具有重量的物体绑在绳子上,绳子的一端固定在某一点上,让物体在重力的作用下自然下垂,绳子所在的线即为崇礼垂线。
作为上述实施例的进一步改进,将所述筒体10固定在所述船体上之前,进行以下步骤:
以舵桨法兰1的下表面所在的面为基准面,所述基准面与所述筒体10形成的线为斜向水线105;
所述斜向水线105以中心点c为转轴尾端向下倾斜a°,形成正向水线106,并在筒体10外表面划出正向水线106;
所述斜向水线105以中心点c为转轴向右端向下倾斜b°,形成正向水线106,并在筒体10外表面划出正向水线106。
参考图2和图7,将法兰理论下端面基准点c点的水平线引至上、下筒体3外表面上,分别作出斜向水线105。在基准点横剖面(a-a)将斜向水线105以c点为转轴右端向下倾斜b°,作出正向水线106;同时在基准点纵剖面(b-b)将斜向水线105以c点为转轴后端向下倾斜a°,作出正向水线106。正向水线106需做好样冲标记,作为后续舵桨法兰1与筒体10组合体的基准点以及双角度粗定位参考,如图8所示,用以校准安装位置是否准确。
作为上述实施例的进一步改进,将所述筒体10固定到船体上,所述船体上固定有动力装置7,所述筒体10与所述动力装置7固定连接,固定后,所述正向水线106呈水平状态。所述动力装置7包括动力输出轴,所述中心点c位于所述动力输出轴的中轴线的延长线上。
该方法相对现有的技术有以下优点:
1、舵桨装置的安装流程简单化,节省了舵桨法兰1、筒体10在船坞阶段吊装作业所需的汽车吊、高空车、大型门座吊等资源投入,对后续船坞阶段的轴系工程和下水工程周期及成本有很大的影响,大大减少的人力资源的投入;
2、有限空间作业地面完成,增加了作业的安全性;
3、减少轴系工程和下水工程的周期及工作量,工序真正前移,缩短了船坞建造周期。
当前的造船形势下,能够缩短船坞周期,特别是轴系工程周期,具有重要的现实意义。减少水下工程的工作量,高空作业地面做,工序真正前移,实现了降本增效和技术创新,提高了船舶制造企业的整体造船能力及竞争力。
实际生产过程中,该方法产生的经济效益如下:
1、船坞作业改为地面作业,有限空间空作业转地面作业,节省搭拆架费用。省去船坞脚手架搭设,按宽10米,高6米,长8米的空间区域搭架,省去船坞阶段反复搭拆架,节省人工费用约1万元。
2、舵桨法兰1、筒体10于船坞阶段定位安装过程中需大量施工人员、葫芦配合,其中1个法兰或筒体10的定位、安装以及反复测量精度要求等需消耗时间至少2天,包含后续大量的装配、电焊、打磨作业,节省人工费用约1.6万元。
3、缩短船坞建造(水下工程)周期至少16天。
在本申请中,除非另有明确的规定和限定,第一特征在第二特征“上”或“下”可以是第一和第二特征直接接触,或第一和第二特征通过中间媒介间接接触。而且,第一特征在第二特征“之上”、“上方”和“上面”可是第一特征在第二特征正上方或斜上方,或仅仅表示第一特征水平高度高于第二特征。第一特征在第二特征“之下”、“下方”和“下面”可以是第一特征在第二特征正下方或斜下方,或仅仅表示第一特征水平高度小于第二特征。
在本说明书的描述中,参考术语“优选实施例”、“再一实施例”、“其他实施例”或“具体示例”等的描述意指结合该实施例或示例描述的具体特征、结构、材料或者特点包含于本申请的至少一个实施例或示例中。在本说明书中,对上述术语的示意性表述不必须针对的是相同的实施例或示例。而且,描述的具体特征、结构、材料或者特点可以在任一个或多个实施例或示例中以合适的方式结合。此外,在不相互矛盾的情况下,本领域的技术人员可以将本说明书中描述的不同实施例或示例以及不同实施例或示例的特征进行结合和组合。
尽管上面已经示出和描述了本申请的实施例,可以理解的是,上述实施例是示例性的,不能理解为对本申请的限制,本领域的普通技术人员在本申请的范围内可以对上述实施例进行变化、修改、替换和变型。
本文用于企业家、创业者技术爱好者查询,结果仅供参考。