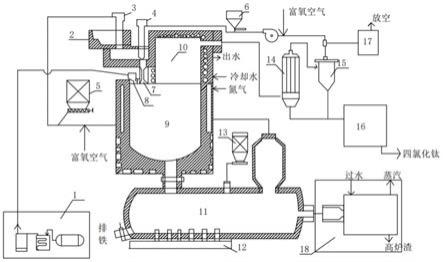
1.本发明涉及固废冶金渣资源利用化领域,具体为含钛高炉渣液态氯化制取四氯化钛的系统及工艺。
背景技术:
2.含钛高炉渣中tio2含量为22~26%,由于tio2弥散分布在多种矿物中,很难用选矿的方法分离富集,若利用酸、碱处理技术分离提钛,因tio2的品位低,使工艺耗酸碱量大,工艺复杂,生产成本高,钛的富集效果不理想,对环境的污染大。而作为水泥混合材使用,其tio2的含量又太高,基本没有活性,只能用作砂石料,因此,至今未找到大量利用的合适途径。
3.含钛高炉渣的高温碳化—低温选择性氯化工艺,是目前最具产业化前景的工艺路线。液态熔融含钛高炉渣直接流入密闭电炉中加热到1600℃~1800℃与碳混合进行碳化,碳化后的液态高炉渣在空气中自然冷却,然后经破碎、细磨,颗粒状的碳化高炉渣在400~550℃的流化床中经氯气氯化,生成四氯化钛蒸汽,经除尘冷凝分离得到粗四氯化钛产品与氯化渣。
4.含钛高炉渣的高温碳化—低温选择性氯化工艺的问题是,一、需要对含钛高炉渣高温碳化,虽然充分利用熔渣物理热,但碳化过程电耗过高问题依然明显,碳化电耗成本可占总成本的80%,且存在电炉涨炉底以及有较严重的泡沫渣,造成碳粉损失大,电极断裂,碳化时间长等问题。二、需要对碳化后的液态高炉渣进行冷却,然后经破碎、细磨,对1650℃~1770℃液态渣直接冷却,造成大量的冷却水消耗和大量的热量损失,且由于碳化钛的存在,使磨碎的动力消耗和设备损耗较大。三、采用700℃以下低温氯化存在反应速度较慢、产能较低的问题;而700℃以上氯化,在氯化过程中会形成氯化钙和氯化镁,钙、镁氯化后的液相析出,极易造成床层熔融粘结,从而使氯化过程无法进行;且碳化钛氯化过程放出的大量热量回收利用及热平衡控制,也是低温氯化过程必须解决的关键问题。四、低温氯化的氯化残渣中,钙、镁氯化率仍在7%左右,氯离子含量远高于水泥允许标准;水洗除氯,而水洗残渣属非活性混合材,按国家规定,非活性混合材掺量不得大于水泥质量15%,所以氯化残渣的用途问题仍然没解决。
技术实现要素:
5.为解决现有技术中的不足,本发明提供具有含钛高炉渣液态氯化制取四氯化钛的系统及工艺,可以大幅降低电耗,解决钙、镁氯化后的液相析出黏结,碳化钛氯化过程放出大量热量回收利用以及炉内热平衡控制的关键难题,兼顾了提钛和大量二次废渣及余热的综合利用。
6.本发明为实现上述目的,通过以下技术方案实现:含钛高炉渣液态氯化制取四氯化钛的系统,包括双层中间包,所述双层中间包下端连接液态氯化炉,所述液态氯化炉底端连通碳热还原炉,所述碳热还原炉侧边连通干法粒化和余热回收装置,所述液态氯化炉通
过管道连接氯气供给装置。
7.所述双层中间包包括错位设置的上层中间包和下层中间包,上层中间包和下层中间包之间通过水口连通,所述下层中间包通过设置在下层中间包底端的喷射水口与液态氯化炉连通,所述水口内设置上层中空塞棒,所述喷射水口内设置下层中空塞棒。
8.所述液态氯化炉包括炉顶、炉体、炉底,所述液态氯化炉内层炉壁分为上下两段,上段为气流段,下部为熔池段,气流段包括夹套结构,所述炉顶顶端连通喷射水口,喷射水口一侧设置与喷射水口中心线呈30
°
-60
°
的氯气喷嘴。
9.所述喷射水口另一侧设置上升烟道,上升烟道为水冷壁结构,上升烟道顶部设有气体导出管道,上升烟道水冷壁涂有耐火耐酸涂层。
10.所述上升烟道顶部设置出口,通过出口连通设置冷凝器,所述冷凝器顶部与气液分离器相连,所述冷凝器与气液分离器底部的液体出口通过管道相连,且一并连通四氯化钛分离回收装置,气液分离器顶部的气体出口通过管道连通三通分配阀,所述三通分配阀通过管道分配部分气体通过风机加压并连通下层中空塞棒,压力为0.8~1.0mpa,管道上接入石油焦储仓,石油焦粉细度为200—300目,所述三通分配阀通过管道分配部分气体进入尾气处理排放装置。
11.所述炉底为锥底结构,所述炉底设有滑动水口与碳热还原炉相通。
12.碳热还原炉底部设置底吹喷管,碳热还原炉上部设有碳材料入口和炉气出口管道,所述碳材料入口连接碳材料储仓,所述炉气出口管道通过连通管连通上层中空塞棒,所述连通管接入富氧空气和添加剂储罐,所述碳热还原炉侧边设有渣液出口,所述渣液出口连通干法粒化器余热回收装置。
13.所述夹套结构内部设置通气孔,通过通气孔向夹套内部通入氮气。
14.含钛高炉渣液态氯化制取四氯化钛的工艺,包括以下步骤:
15.s1、高炉排放的1350℃~1450℃含钛高炉渣液流入上层中间包,同时通过气力输送加入添加剂,添加剂通过上层中空塞棒加入渣液,提起上层中空塞棒,渣液流入下层中间包;
16.s2、向下层中空塞棒中通入富氧空气,计量加入石油焦,给含钛高炉渣液配碳,提起下层中空塞棒,渣液与配碳在水口的收缩段和直管段混合流入液态氯化炉;
17.s3、渣液从水口喷出,受到高速高浓度氯气冲击,形成分散的液滴,气液充分接触,fe2o3、tio2被氯化,氯化的fe2o3、tio2气化,随反应后的烟气进入上升烟道,未氯化或气化的渣液落入炉底;
18.s4、渣液通过炉底水口流入设置在下部的碳热还原炉,碳热还原炉内加入碳质材料,底部通入烟气搅拌,添加剂被碳热还原从渣液中气化脱出,渣液从碳热还原炉一侧进入干法粒化和余热回收装置,渣液被粒化冷却成具有潜在水硬性的高炉矿渣;
19.s5、液态氯化炉炉气,经上升烟道上升并冷却降温,同时低沸点气体凝固,与气体携带的液滴一起沉降落入液面,初步冷却的炉气进入四氯化钛分离回收装置,四氯化钛冷凝成液态从炉气中分离,进一步净化、过滤形成四氯化钛溶液,分离从四氯化钛后的炉气经三通分流阀,一部分被加压输送至下层中空塞棒,作为气力输送气体,且炉气中未反应的氯气循环利用,多余的炉气通过吸收器、分离器,分离出hcl经烟囱排空;
20.s6、碳热还原炉炉气经加压进入上层中空塞棒,进入渣液循环利用,向夹套通入氮
气,夹套内气压略大于液态氯化炉炉腔内气压,氮气透过夹套内壁通气孔,在液态氯化炉炉腔内壁形成氮气气膜,防止高温氯气的腐蚀。
21.s2中,石油焦固定碳含量>95%,挥发分2%
‑
4%,粒度≤0.075mm,配碳比为完全反应的理论量的140%
‑
160%,富氧空气压力为0.8~1.0mpa。
22.对比现有技术,本发明的有益效果在于:
23.1、液态高炉渣在高速氯气的冲击下,气液两相剧烈混合,液态状态下氯化,相比于高温碳化—低温氯化制取四氯化钛工艺,省略了高温碳化阶段,省去高温碳化能耗和进入低温氯化炉前的破碎磨细电耗,简化了工艺流程、设备,生产实施和控制操作相对简单。
24.2、本发明含钛高炉渣液态氯化方法,与沸腾氯化工艺相比,解决了氯化生成cacl2和mgcl2两种熔点低而沸点高的氯化物,在沸腾氯化炉(800~1000℃)中熔融成液相黏附炉料,使炉料结块,沸腾层遭到破坏的问题,从而解决了高钙镁盐的含钛高炉渣不能直接进行流态化氯化,而必须高温碳化,碳化渣再低温氯化的问题。
25.3、本发明含钛高炉渣液态氯化方法,解决了沸腾氯化和低温氯化需要导出氯化过程的大量反应热能,较难控制温度及炉内热平衡的问题。
26.4、本发明含钛高炉渣液态氯化方法,使渣液中的cao不被氯化或很少氯化,冷却的氯化残渣可以不用洗涤,具有高炉矿渣的活性,解决了含钛高炉渣资源化利用问题。
27.5、本发明含钛高炉渣液态氯化装置,利用惰性气膜防止氯气在高温下,对炉壁强烈的腐蚀,增强设备的寿命和安全性。
附图说明
28.附图1是本发明含钛高炉渣液态氯化制取四氯化钛的系统装置图。
29.附图中所示标号:1、氯气供给装置;2、双层中间包;3、上层中空塞棒;4、下层中空塞棒;5、添加剂储罐;6、石油焦储仓;7、喷射水口;8、氯气喷嘴;9、液态氯化炉;10、上升烟道;11、碳热还原炉;12、底吹喷管;13、碳材料储仓;14、冷凝器;15、气液分离器;16、四氯化钛分离回收装置;17、尾气处理排放装置;18、干法粒化和余热回收装置。
具体实施方式
30.下面结合具体实施例,进一步阐述本发明。应理解,这些实施例仅用于说明本发明而不用于限制本发明的范围。此外应理解,在阅读了本发明讲授的内容之后,本领域技术人员可以对本发明作各种改动或修改,这些等价形式同样落于本技术所限定的范围。
31.实施例一:
32.如图1所示含钛高炉渣液态氯化制取四氯化钛的系统,包括双层中间包2,所述双层中间包2下端连接液态氯化炉9,所述液态氯化炉9底端连通碳热还原炉11,所述碳热还原炉11侧边连通干法粒化和余热回收装置,所述液态氯化炉9通过管道连接氯气供给装置1,氯气供给装置1包括液氯罐、汽化器、和缓冲罐,所述缓冲罐压力控制在0.4mpa。
33.进一步的,所述双层中间包2包括错位设置的上层中间包和下层中间包,上层中间包和下层中间包之间通过水口连通,所述下层中间包通过设置在下层中间包底端的喷射水口7与液态氯化炉9连通,所述水口内设置上层中空塞棒3,所述喷射水口7内设置下层中空塞棒4。
34.进一步的,所述液态氯化炉9包括炉顶、炉体、炉底,所述液态氯化炉9内层炉壁分为上下两段,上段为气流段,下部为熔池段,炉壁由水冷管、数层耐火和保温材料砌成,炉腔内壁可挂渣形成耐火材料保护层,气流段包括夹套结构,夹套内壁由不锈钢材料和氮化硅陶瓷构成,不锈钢材料和氮化硅陶瓷上均匀密布通气孔,形成内壁防腐蚀惰性气体气膜,所述炉顶顶端连通喷射水口7,喷射水口7一侧设置与喷射水口7中心线呈45
°
的氯气喷嘴8,液态氯化炉9的外层是钢材焊成的炉壳。
35.进一步的,所述喷射水口7另一侧设置上升烟道10,上升烟道10为水冷壁结构,上升烟道10顶部设有气体导出管道,上升烟道10水冷壁涂有耐火耐酸涂层。
36.进一步的,所述上升烟道10顶部设置出口,通过出口连通设置冷凝器14,所述冷凝器14顶部与气液分离器15相连,所述冷凝器14与气液分离器15底部的液体出口通过管道相连,且一并连通四氯化钛分离回收装置16,四氯化钛分离回收装置16包括冷凝器、气液分离器、过滤器、泡沫塔和四氯化钛贮罐,气液分离器15顶部的气体出口通过管道连通三通分配阀,所述三通分配阀通过管道分配部分气体通过风机加压并连通下层中空塞棒4,压力为0.9mpa,管道上接入石油焦储仓6,石油焦粉细度为260目,所述三通分配阀通过管道分配部分气体进入尾气处理排放装置17,尾气处理排放装置17包括收器、气液分离器、稀盐酸贮槽和烟囱。
37.进一步的,所述炉底为锥底结构,所述炉底设有滑动水口与碳热还原炉11相通,水口为耐高温陶瓷并有保温层,水口设计为滑动水口,调整液态氯化炉9的液位,碳热还原炉11为圆筒形或方筒形或长方筒形,本实施例中选用卧式圆筒形。
38.进一步的,碳热还原炉11底部设置底吹喷管12,碳热还原炉11上部设有碳材料入口和炉气出口管道,所述碳材料入口连接碳材料储仓13,所述炉气出口管道通过连通管连通上层中空塞棒3,所述连通管接入富氧空气和添加剂储罐5,所述碳热还原炉11侧边设有渣液出口,所述渣液出口连通干法粒化器余热回收装置18,所述干法粒化器余热回收装置18包括气泡雾化喷嘴或气力雾化喷嘴、余热锅炉和粒化渣收集系统。
39.进一步的,所述夹套结构内部设置通气孔,通过通气孔向夹套内部通入氮气。
40.含钛高炉渣液态氯化制取四氯化钛的工艺,包括以下步骤:
41.s1、高炉排放的1400℃含钛高炉渣液流入上层中间包,同时通过气力输送加入添加剂,添加剂通过上层中空塞棒3加入渣液,提起上层中空塞棒3,渣液流入下层中间包;
42.s2、向下层中空塞棒4中通入富氧空气,计量加入石油焦,给含钛高炉渣液配碳,提起下层中空塞棒4,渣液与配碳在水口的收缩段和直管段混合流入碳热还原炉11;
43.s3、渣液从水口喷出,受到高速高浓度氯气冲击,形成分散的液滴,气液充分接触,fe2o3、tio2被氯化,氯化的fe2o3、tio2气化,随反应后的烟气进入上升烟道10,未氯化或气化的渣液落入炉底;
44.s4、渣液通过炉底水口流入设置在下部的碳热还原炉11,碳热还原炉11内加入碳质材料,底部通入烟气搅拌,添加剂被碳热还原从渣液中气化脱出,渣液从碳热还原炉一侧进入干法粒化和余热回收装置18,渣液被粒化冷却成具有潜在水硬性的高炉矿渣;
45.s5、液态氯化炉9炉气,经上升烟道上升并冷却降温,同时低沸点气体凝固,与气体携带的液滴一起沉降落入液面,冷却的炉气进入四氯化钛分离回收装置16,四氯化钛冷凝成液态从炉气中分离,进一步净化、过滤形成四氯化钛溶液,分离从四氯化钛后的炉气经三
通分流阀,一部分被加压输送至下层中空塞棒4,作为气力输送气体,且炉气中未反应的氯气循环利用,多余的炉气通过吸收器、分离器,分离出hcl经烟囱排空;
46.s6、碳热还原炉11炉气经加压进入上层中空塞棒3,进入渣液循环利用,向夹套通入氮气,夹套内气压略大于液态氯化炉9炉腔内气压,氮气透过夹套内壁通气孔,在液态氯化炉9炉腔内壁形成氮气气膜,防止高温氯气的腐蚀。
47.s2中,石油焦固定碳含量为96%,挥发分为3%,粒度为0.075mm,配碳比为完全反应的理论量的150%,富氧空气压力为0.9mpa。
48.实施例二:
49.含钛高炉渣液态氯化制取四氯化钛的工艺,包括以下步骤:
50.s1、高炉排放的1380℃含钛高炉渣液流入上层中间包,同时通过气力输送加入添加剂,添加剂通过上层中空塞棒3加入渣液,提起上层中空塞棒3,渣液流入下层中间包;
51.s2、向下层中空塞棒4中通入富氧空气,计量加入石油焦,给含钛高炉渣液配碳,提起下层中空塞棒4,渣液与配碳在水口的收缩段和直管段混合流入碳热还原炉11;
52.s3、渣液从水口喷出,受到高速高浓度氯气冲击,形成分散的液滴,气液充分接触,fe2o3、tio2被氯化,氯化的fe2o3、tio2气化,随反应后的烟气进入上升烟道10,未氯化或气化的渣液落入炉底;
53.s4、渣液通过炉底水口流入设置在下部的碳热还原炉11,碳热还原炉11内加入碳质材料,底部通入烟气搅拌,添加剂被碳热还原从渣液中气化脱出,渣液从碳热还原炉一侧进入干法粒化和余热回收装置18,渣液被粒化冷却成具有潜在水硬性的高炉矿渣;
54.s5、液态氯化炉9炉气,经上升烟道上升并冷却降温,同时低沸点气体凝固,与气体携带的液滴一起沉降落入液面,冷却的炉气进入四氯化钛分离回收装置16,四氯化钛冷凝成液态从炉气中分离,进一步净化、过滤形成四氯化钛溶液,分离从四氯化钛后的炉气经三通分流阀,一部分被加压输送至下层中空塞棒4,作为气力输送气体,且炉气中未反应的氯气循环利用,多余的炉气通过吸收器、分离器,分离出hcl经烟囱排空;
55.s6、碳热还原炉11炉气经加压进入上层中空塞棒3,进入渣液循环利用,向夹套通入氮气,夹套内气压略大于液态氯化炉9炉腔内气压,氮气透过夹套内壁通气孔,在液态氯化炉9炉腔内壁形成氮气气膜,防止高温氯气的腐蚀。
56.s2中,石油焦固定碳含量为97%,挥发分为3.8%,粒度为0.07mm,配碳比为完全反应的理论量的155%,富氧空气压力为0.95mpa。
57.本发明系统的工作原理为:
58.对系统进行烘烤升温,待双层中间包2、液态氯化炉9、碳热还原炉11烘烤温度达到1000℃时,将高炉排放的1400℃液态高炉渣流入上层中间包,待上层中间包液位到运行位置,将添加剂储罐5的添加剂加入上层中空塞棒3;同时通入富氧空气,把添加剂通过气力喷出上层中空塞棒3,进入含钛高炉渣渣液,添加剂与渣液中的氧化钙、氧化镁优先结合成无机盐,提起上层中空塞棒3,含钛高炉渣渣液通过中间水口流入下层中间包,过程中渣液均匀混入添加剂。添加剂的加入量根据渣液钙镁含量调整,是理论配入量的1.1倍;富氧空气压力2000pa。
59.含钛高炉渣渣液结合添加剂进入下层中间包,下层中空塞棒4计量加入石油焦粉、富氧空气,提升下层中空塞棒4的棒头到水口的圆筒中间位置,石油焦粉在富氧空气的作用
下,由下层中空塞棒4的棒头上的导气通孔高速喷出,与渣液一起经水口缩口加速在直管段剧烈混合,并喷入液态氯化炉9,此处所用的石油焦粉固定碳含量为96%,挥发分为3%,粒度为0.075mm,配碳比为完全反应的理论量的150%,富氧空气压力为0.9mpa。
60.进入液态氯化炉9的渣液,在混合石油焦粉的压力气体加速冲击下,形成液滴,液态氯化炉9上的氯气喷嘴8喷出高速气流,高速氯气流与喷入的渣液相遇,被粉碎成更加细小液滴,反应表面积迅速扩大造成良好的元素氯化动力学条件,渣液中tio2及其它易氯化的元素随即氯化,沸点低于炉温氯化物气化进入炉气,高于炉温的氯化物随氯化残渣渣液落入炉底。
61.液态氯化炉9炉体上部夹套通入惰性气体氮气,夹套压力略高于炉内压力,氮气透过通气孔在炉膛内壁形成气膜,防止高温氯化物腐蚀;炉体下部水冷铜套通入冷却水,使炉膛内壁黏结冷却结成渣层,护住炉壁防止渣液高温侵蚀。
62.混有氮气的炉气上升至上升烟道10,上升烟道10冷却壁和冷却挂件通入冷却水,炉气冷却至220℃,沸点低于240℃的氯化物重新凝结,沉降落入炉底渣液;未凝结的炉气进入冷凝器14,冷却器14中冷凝液是采用冷却后的粗ticl4液,自器顶喷淋而下,和底部上升的炉气逆向接触,炉气中的ticl4和其他一些杂质凝集成液体,气液混合物经气液分离器15分离,液体流入四氯化钛分离回收装置16,得到初步提纯,即为工业(粗)四氯化钛液体;而其它气体则从分离器15中逸出,逸出气体含有较多的co、co2、cl2、hcl等气体,气体通过三通分配阀使大部分气体经加压通入下层中空塞棒4,重新进入液态氯化炉9循环利用,剩余的残气通过三通分配阀进入尾气处理排放装置17,在尾气处理排放装置17中cl2、hcl被吸收后再排空。
63.由于液态氯化炉9内加入了co、co2、cl2、hcl气体,操作中适当减少石油焦粉的加入量,同时降低富氧空气量。
64.液态氯化炉9炉底渣液通过水口流入碳热还原炉11,调节设在水口中间的滑动插板,调整液态氯化炉9内液位,液位要起到液封作用,液面进一步进行氯化反应。
65.碳热还原炉11内加入碳质材料,炉底喷入co2气体和空气,渣液中结合了cao、mgo添加剂,在碳热还原条件和炉底气体搅拌下被还原,脱除cao、mgo进入炉气,碳热还原炉11卧式圆筒设置,渣液与碳质材料接触面积大,炉底喷出气体造成渣液液面翻腾,强化了渣液与碳质材料的接触,使还原反应快速彻底;碳热还原后的炉气,通过管道进入上层中空塞棒3,喷入新加入的渣液中,循环利用;碳热还原后的渣液流入干法粒化和余热回收装置18,渣液被气力粒化,并被余热锅炉冷却至150℃排出,形成粒化矿渣。
66.循环利用的炉气是还原气氛,循环利用气体的加入后,操作中适当减少添加剂的加入量,降低富氧空气量。还原气氛一方面使含钛高炉渣的高价钛还原为低价钛,另一方面对渣液加热,增加渣液的流动性。
67.本发明与现有技术不同点在于,现有的技术是气固氯化,富钛渣或高温碳化的含钛高炉渣,经破碎、磨细成细颗粒,悬浮在氯气中或漂浮在氯盐熔液上,加碳进行氯化反应,由于cao、mgo有优先tio2氯化的趋势,且cacl2、mgocl2熔点较低,钙、镁氯化后的液相析出,造成床层黏结,所以钙、镁氯化形成液相是绕不过去的坎;因此,采用富钛渣,严格控制cao mgo/%≤1.5%,但这样的高品质的富钛矿很少;或采用在高温下用碳对含钛高炉渣进行深度还原,使渣中的tio2转化为tic,在700℃以下进行“低温选择性氯化”,但氯化试验时,钙
镁氯化较为严重,选择性不强。且碳化渣氯化放热量较大,控制氯化温度在700℃以下,必须排出多余的热量,在大型氯化设备上如何导出如此巨大的反应热是采用tic低温选择性氯化的一个非常棘手的技术难题。而本发明是气液氯化,采用液态的含钛高炉渣,在液态下利用氯气喷吹氯化,化解了上述技术的制约因素,提高了氯化反应速率,简化流程,减少设备投资,大幅减低能耗。
再多了解一些
本文用于企业家、创业者技术爱好者查询,结果仅供参考。