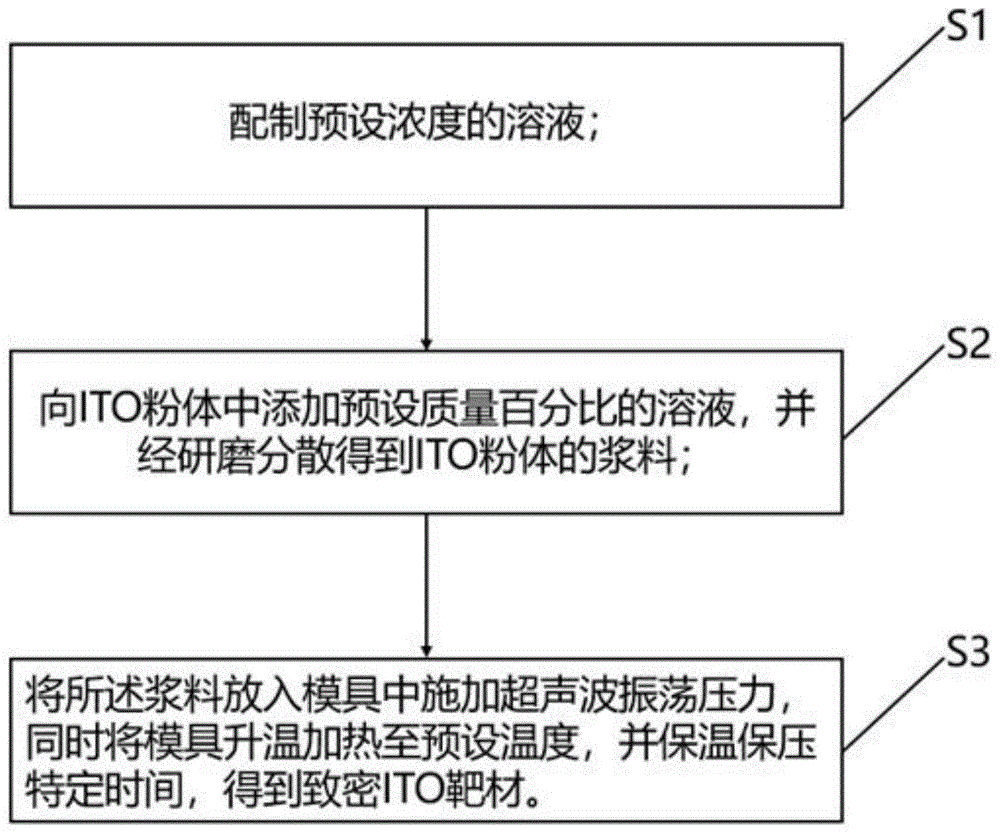
本发明涉及低温陶瓷烧结技术领域,尤其涉及一种高密度ITO靶材的制备方法。
背景技术
近几十年来,氧化铟锡(ITO)作为一种透明的导电氧化物,以其优异的光电性能引起了人们的不断关注。ITO薄膜广泛应用于生物传感技术、液晶平板显示器、衬底、太阳能电池和电极等领域。ITO薄膜具有导电性能好,可见光透过率高,能吸收紫外光,能反射红外光,对微波衰减率高,膜层硬度高、耐磨性能好,加工性能好,易于刻蚀等特点。ITO薄膜玻璃作为面发热体,用在汽车、火车、飞机挡风玻璃,飞船眩窗,坦克激光测距仪、机载光学侦察仪,潜望镜观察窗等,不仅起隔热降温作用,而且通电后可以除冰霜,因此也得到了广泛的应用。
目前,ITO靶材的烧结方法有常压固相烧结、热压烧结、火花等离子烧结等,但是工厂生产靶材的烧结方法通常是常压固相烧结,并在烧结过程中通氧。常压固相烧结的烧结温度通常为1450~1600℃,烧结时长7-14天,长时间的高温烧结导致晶粒粗大,高温烧结的能耗也非常大。随着平板显示向高清大尺寸的方向发展要求ITO靶材具有更细的晶粒尺寸,以便获得光电性能更优异的ITO薄膜。鉴于此提供一种降低烧结温度,并能够制备出晶粒细小均匀且相对密度大的高密度ITO靶材的制备方法是十分有必要的。
技术实现要素:
本发明的目的在于提供一种高密度ITO靶材的制备方法,能够降低烧结温度,且制备出的晶粒细小均匀且相对密度大,节约能耗。
为实现上述目的,本发明采用的一种高密度ITO靶材的制备方法,包括如下步骤:
配制预设浓度的溶液;
向ITO粉体中添加预设质量百分比的所述溶液,并经研磨分散得到ITO粉体的浆料;
将所述浆料放入模具中施加超声波振荡压力,同时将模具升温加热至预设温度,并保温保压特定时间,得到致密ITO靶材。
其中,所述酸溶液为甘氨酸、丙氨酸、乙酸、草酸、柠檬酸、乙二胺四乙酸、酒石酸、柠檬酸铵溶液中的一种或者多种的混合溶液。
其中,所述酸溶液的预设浓度为:甘氨酸0.1-250g/L、丙氨酸0.1-20g/L、乙酸1-6mol/L、草酸0.1-2mol/L、柠檬酸0.1-2mol/L、乙二胺四乙酸0.1-0.5g/L、酒石酸0.1-1390g/L、柠檬酸铵0.1-1mol/L。
其中,向ITO粉体中添加预设质量百分比的所述溶液的步骤中,所述预设质量百分比为所述ITO粉体总量的5~50%。
其中,保温保压特定时间,得到致密ITO靶材的步骤中:
保压时采用的压力为80~530Mpa。
其中,保温保压特定时间,得到致密ITO靶材的步骤中:
特定时间为0.5~4小时。
其中,将模具升温加热至预设温度的步骤中:
所述预设温度为100~400℃。
其中,将模具升温加热至预设温度的步骤中:
升温速率为5~20℃/min。
其中,所述ITO粉体采用水热合成的ITO粉体、共沉淀合成的ITO粉体、球磨合成的ITO粉体或者以SnO为锡源的球磨混合粉体。
本发明的有益效果体现在:通过配制预设浓度的溶液;向ITO粉体中添加预设质量百分比的所述溶液,并经研磨分散得到ITO粉体的浆料;将所述浆料放入模具中施加超声波振荡压力,同时将模具升温加热至预设温度,并保温保压特定时间,得到致密ITO靶材。上述工艺在≤400℃下制备出相对密度高于93%的靶材,较传统常压烧结降低了烧结的温度,有利于得到晶粒细小的靶材,降低了能源的消耗。
附图说明
为了更清楚地说明本发明实施例或现有技术中的技术方案,下面将对实施例或现有技术描述中所需要使用的附图作简单地介绍,显而易见地,下面描述中的附图仅仅是本发明的一些实施例,对于本领域普通技术人员来讲,在不付出创造性劳动的前提下,还可以根据这些附图获得其他的附图。
图1是本发明的一种高密度ITO靶材的制备方法的步骤流程图。
图2是高密度ITO靶材的SEM图。
具体实施方式
下面详细描述本发明的实施例,所述实施例的示例在附图中示出,其中自始至终相同或类似的标号表示相同或类似的元件或具有相同或类似功能的元件。下面通过参考附图描述的实施例是示例性的,旨在用于解释本发明,而不能理解为对本发明的限制。
在本发明的描述中,需要理解的是,术语“长度”、“宽度”、“上”、“下”、“前”、“后”、“左”、“右”、“竖直”、“水平”、“顶”、“底”“内”、“外”等指示的方位或位置关系为基于附图所示的方位或位置关系,仅是为了便于描述本发明和简化描述,而不是指示或暗示所指的装置或元件必须具有特定的方位、以特定的方位构造和操作,因此不能理解为对本发明的限制。此外,在本发明的描述中,“多个”的含义是两个或两个以上,除非另有明确具体的限定。
请参阅图1和图2,本发明提供了一种高密度ITO靶材的制备方法,包括如下步骤:
配制预设浓度的溶液;
向ITO粉体中添加预设质量百分比的所述溶液,并经研磨分散得到ITO粉体的浆料;
将所述浆料放入模具中施加压力,同时将模具升温加热至预设温度,并保温保压特定时间,得到致密ITO靶材。
其中所述酸溶液的配制选用去离子水或纯水,在乙酸溶液的配制中,优选电阻率大于18MΩ的去离子水,确保ITO陶瓷靶材的相纯度。另外可以选用蒸馏水来配制溶液,也可以选用有机溶剂来配制,例如,乙醇、丙酮等。另外所述溶液的加入量对靶材的致密度有重大的影响。在向ITO粉体中添加预设质量百分比的所述溶液,并经研磨分散得到ITO粉体的浆料的过程中,所述ITO粉体采用水热合成的ITO粉体、共沉淀合成的ITO粉体、球磨合成的ITO粉体或者以SnO为锡源的球磨混合粉体。在将溶液均匀的滴加到ITO粉体中时,并采用研磨、球磨的方式将其混合成均匀的ITO浆料,其中浆料的粘度、ITO的固含量等是由溶液的种类、溶液的浓度及加入量决定。将ITO浆料放入成型的模具中,其中模具的材质通常为钢制的,也可以是石墨、陶瓷等材质,同时都附带加热功能。加热方式可采用电加热精确控制加热温度及升温速率,也可以选择红外加热、微波加热、中频加热等方式,另外向所述模具施加压力的方式可以选择双向轴压、单向轴压或者超声波振荡的方式,升温方式可选择分段加热。另外在所述ITO粉体中锡的掺杂量为粉体总质量的5~35%。
实施例1,一种高密度ITO靶材的制备方法,包括如下步骤:
S1:配制2mol/L的乙酸溶液;
S2:称取15g水热ITO粉体(质量比In2O3:SnO2=9:1)置于研钵中,再称取粉体质量的30%的上述乙酸溶液滴加到ITO粉体中并研磨均匀,形成浆料;
S3:选用带加热功能的模具,模具的内孔直径为12mm,使用超声波振荡压力机对模具施加350MPa的压力,并以5℃/min的升温速率将模具加热至350℃保温1小时,冷却至室温脱模得到ITO靶材。
其中,模具使用前需要使用工业酒精对模具内壁、模芯、顶杆、垫块清洗干净,待模具干燥后,再称取适量的浆料放入模具中。通过实施例1的方式测试出ITO靶材的相对密度为90.36%。
实施例2,一种高密度ITO靶材的制备方法,包括如下步骤:
S1:配制2mol/L的草酸溶液;
S2:称取50g以SnO为锡源的球磨混合粉体(质量比In2O3:SnO2=9:1)置于研钵中,再称取粉体质量的50%的上述草酸溶液滴加到ITO粉体中并研磨均匀,形成浆料;
S3:选用带加热功能的模具,模具的内孔直径为15mm,使用超声波振荡压力机对模具施加300MPa的压力,并以5℃/min的升温速率将模具加热至150℃,并保温30min,随后以10℃/min的升温速率加热至350℃保温1小时,冷却至室温脱模得到ITO靶材。
其中,模具使用前需要使用工业酒精对模具内壁、模芯、顶杆、垫块清洗干净,待模具干燥后,再称取适量的浆料放入模具中。通过实施例2的方式测试出ITO靶材的相对密度为98.58%。
实施例3,一种高密度ITO靶材的制备方法,包括如下步骤:
S1:配制20g/L的甘氨酸酸溶液;
S2:称取80g水热ITO粉体(质量比In2O3:SnO2=9:1)置于研钵中,再称取粉体质量的35%的上述甘氨酸溶液滴加到ITO粉体中并研磨均匀,形成浆料;
S3:选用带加热功能的模具,模具的内孔直径为60mm,使用超声波振荡压力机对模具施加350MPa的压力,并以5℃/min的升温速率将模具加热至150℃,并保温30min,随后以10℃/min的升温速率加热至400℃保温1小时,冷却至室温脱模得到ITO靶材。
其中,模具使用前需要使用工业酒精对模具内壁、模芯、顶杆、垫块清洗干净,待模具干燥后,再称取适量的浆料放入模具中。通过实施例3的方式测试出ITO靶材的相对密度为81.63%。
实施例4,一种高密度ITO靶材的制备方法,包括如下步骤:
S1:配制15g/L的丙氨酸溶液;
S2:称取50g球磨ITO粉体(质量比In2O3:SnO2=8:2)置于研钵中,再称取粉体质量的40%的上述丙氨酸溶液滴加到ITO粉体中并研磨均匀,形成浆料;
S3:选用带加热功能的模具,模具的内孔直径为80mm,使用超声波振荡压力机对模具施加350MPa的压力,并以5℃/min的升温速率将模具升温至350℃,并保温30min,冷却至室温脱模得到ITO靶材。
其中,模具使用前需要使用工业酒精对模具内壁、模芯、顶杆、垫块清洗干净,待模具干燥后,再称取适量的浆料放入模具中。通过实施例4的方式测试出ITO靶材的相对密度为88.58%。
实施例5,一种高密度ITO靶材的制备方法,包括如下步骤:
S1:配制1mol/L的柠檬酸溶液;
S2:称取50g水热ITO粉体(质量比In2O3:SnO2=9.5:0.5)置于研钵中,再称取粉体质量的50%的上述柠檬酸溶液滴加到ITO粉体中并研磨均匀,形成浆料;
S3:选用带加热功能的模具,模具的内孔直径为80mm,使用超声波振荡压力机对模具施加350MPa的压力,并以10℃/min的升温速率将模具升温至150℃,并保温20min,随后以10℃/min的升温速率加热至350℃保温1小时,冷却至室温脱模得到ITO靶材。
其中,模具使用前需要使用工业酒精对模具内壁、模芯、顶杆、垫块清洗干净,待模具干燥后,再称取适量的浆料放入模具中。通过实施例5的方式测试出ITO靶材的相对密度为89.24%。
实施例6,一种高密度ITO靶材的制备方法,包括如下步骤:
S1:配制2mol/L的乙酸溶液;
S2:称取50g球磨ITO粉体(质量比In2O3:SnO2=7:3)置于研钵中,再称取粉体质量的50%的上述乙酸溶液滴加到ITO粉体中并研磨均匀,形成浆料;
S3:选用带加热功能的模具,模具的内孔直径为80mm,使用超声波振荡压力机对模具施加300MPa的压力,并以10℃/min的升温速率将模具升温至150℃,并保温10min,随后以10℃/min的升温速率加热至350℃保温1小时,冷却至室温脱模得到ITO靶材。
其中,模具使用前需要使用工业酒精对模具内壁、模芯、顶杆、垫块清洗干净,待模具干燥后,再称取适量的浆料放入模具中。通过实施例6的方式测试出ITO靶材的相对密度为84.17%。
实施例7,一种高密度ITO靶材的制备方法,包括如下步骤:
S1:配制50g/L的酒石酸溶液;
S2:称取50g球磨ITO粉体(质量比In2O3:SnO2=6.5:3.5)置于研钵中,再称取粉体质量的45%的上述酒石酸溶液滴加到ITO粉体中并研磨均匀,形成浆料;
S3:选用带加热功能的模具,模具的内孔直径为80mm,使用超声波振荡压力机对模具施加350MPa的压力,并以10℃/min的升温速率将模具升温至150℃,并保温30min,随后以5℃/min的升温速率加热至350℃保温1小时,冷却至室温脱模得到ITO靶材。
其中,模具使用前需要使用工业酒精对模具内壁、模芯、顶杆、垫块清洗干净,待模具干燥后,再称取适量的浆料放入模具中。通过实施例7的方式测试出ITO靶材的相对密度为76.32%。
实施例8,一种高密度ITO靶材的制备方法,包括如下步骤:
S1:配制1mol/L的乙酸溶液;
S2:称取50g水热ITO粉体(质量比In2O3:SnO2=9.5:0.5)置于研钵中,再称取粉体质量的50%的上述乙酸溶液滴加到ITO粉体中并研磨均匀,形成浆料;
S3:选用带加热功能的模具,模具的内孔直径为80mm,使用超声波振荡压力机对模具施加250MPa的压力,并以10℃/min的升温速率将模具升温至350℃保温2小时,冷却至室温脱模得到ITO靶材。
其中,模具使用前需要使用工业酒精对模具内壁、模芯、顶杆、垫块清洗干净,待模具干燥后,再称取适量的浆料放入模具中。通过实施例8的方式测试出ITO靶材的相对密度为84.84%。
实施例9,一种高密度ITO靶材生的制备方法,包括如下步骤:
S1:配制1mol/L的乙酸溶液;
S2:称取50g共沉淀合成的ITO粉体(质量比In2O3:SnO2=7.5:2.5)置于研钵中,再称取粉体质量的50%的上述乙酸溶液滴加到ITO粉体中并研磨均匀,形成浆料;
S3:选用带加热功能的模具,模具的内孔直径为80mm,使用超声波振荡压力机对模具施加400MPa的压力,并保温20min,随后以5℃/min的升温速率加热至400℃保温1小时,冷却至室温脱模得到ITO靶材生。
其中,模具使用前需要使用工业酒精对模具内壁、模芯、顶杆、垫块清洗干净,待模具干燥后,再称取适量的浆料放入模具中。通过实施例9的方式测试出ITO靶材的相对密度为93.91%。
综上所述:本发明提供一种高密度ITO靶材的制备方法,实现在低于400℃的条件下制备出晶粒细小均匀且相对密度大于93%的ITO靶材。相比于传统的生坯制备技术,具有降低烧结温度和烧结时间、易于获得ITO纳米晶陶瓷靶材等特点。
具体的获得的效果为:本发明的优点和积极效果:
本发明的高密度ITO靶材的制备方法,其工艺简单,用时短,制备出的靶材具有高密度且均匀,变形小的优点。
本发明的高密度ITO靶材的制备方法,在≤400℃和≤530MPa下制备出相对密度高于93%的靶材。相对于传统的靶材制备方法,该方法不用加入粘结剂,同时也省略了排胶的工艺。
本发明的高密度ITO靶材的制备方法,在≤400℃下制备出相对密度高于93%的靶材,降低了烧结工艺的温度,有利于得到晶粒细小的靶材,降低了能源的消耗。
本发明的高密度ITO靶材制备方法,在在≤400℃下制备出相对密度高于93%的靶材,相较于传统烧结降低了1000℃的烧结温度,不发生铟、锡的挥发,保证了准确的铟锡比,并省略了通氧的过程,降低了能源的消耗。
以上所揭露的仅为本发明一种较佳实施例而已,当然不能以此来限定本发明之权利范围,本领域普通技术人员可以理解实现上述实施例的全部或部分流程,并依本发明权利要求所作的等同变化,仍属于发明所涵盖的范围。
本文用于企业家、创业者技术爱好者查询,结果仅供参考。