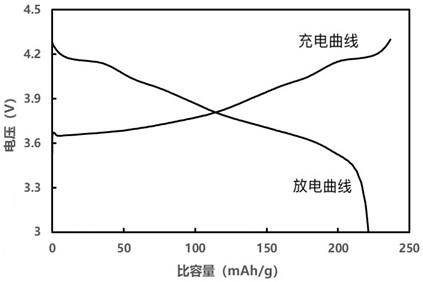
1.本发明涉及锂电池技术领域,具体而言,涉及一种四元正极材料及其制备方法和应用。
背景技术:
2.锂离子电池已经成为目前应用最为广泛的电化学动力源,这种电池中最具代表性的就是正极和负极中的锂离子在嵌入与脱嵌时化学电位的变化而产生电能的锂二次电池(libs)。正极材料对 libs的性能有直接主导的作用,因此许多研究人员致力于实现容量大、充电/放电速度快、循环寿命长的可进行锂离子可逆的嵌入与脱嵌的正极材料。目前,高镍材料被认为是最有望的候选材料之一,因为其可以通过增加镍含量来提高锂离子电池的比容量。但是,由此产生的锂离子电池不良循环稳定性可能会阻碍这种方法的成功。
3.此外,高镍材料中四元多晶材料相比三元正极材料在安全性和循环稳定性上更有优势,是目前最有发展前景的材料之一。但是高镍四元正极材料目前降低残碱的方式主要是靠水洗工艺,但是水洗之后,锂残渣被去除,晶格中的锂离子因为与晶格外的锂离子具有更大的浓度差,材料更倾向于发生无电子转移的脱锂反应,继而更倾向于发生ni
3
/ni
2
的转变,水洗后的材料表面粗糙,比表面积变大,与电解液接触面积大,副反应更加剧烈。为了解决这一问题,常用的改性方式是材料表面包覆,但是对于高镍四元正极材料而言,干混包覆会导致材料表面包覆不均匀,而且加了一步工艺,增加了生产成本。
4.有鉴于此,特提出本发明。
技术实现要素:
5.本发明涉及一种四元正极材料的制备方法,包括以下步骤:将正极基材、可溶性钴盐、沉淀剂、络合剂和水进行混合,对混合后的体系进行液固分离,收集固相并进行干燥和煅烧;所述正极基材的化学通式为lini
x
co
y
mn
z
al
(1
‑
x
‑
y
‑
z)
o2,其中,0.9 ≤ x<1,0<y<0.07,0<z<0.03。
6.本发明提供一种四元正极材料的制备方法,以解决现有技术中的高镍四元正极材料水洗后的材料表面粗糙,比表面积变大,与电解液接触面积大,副反应更加剧烈的问题。本发明将可溶性钴盐、沉淀剂、络合剂、水与正极基材进行混合,对正极基材进行水洗包覆,在正极基材的表面均匀包覆一层钴的化合物,既可以提高材料导电性还可以起到保护层的作用,减少正极材料与电解液的副反应发生;除此之外,加入沉淀剂可以把残存的锂源沉降下来,防止后期匀浆过程中因ph过高出现果冻状情况,严重影响正极材料容量的发挥以及循环保持率;该方法可促进锂离子嵌入脱出,减少正极材料表面副反应。
7.根据本发明的另一个方面,本发明还涉及所述的四元正极材料的制备方法得到的四元正极材料。
8.本发明的正极材料在正极基材的表面均匀包覆一层钴的化合物,既可以提高材料
导电性还可以起到保护层的作用,减少正极材料与电解液的副反应发生。
9.根据本发明的另一个方面,本发明还涉及一种锂电池正极,包括如上所述的四元正极材料。
10.本发明的锂电池正极可赋予锂电池优异的容量、首效和循环稳定性能。
11.根据本发明的另一个方面,本发明还涉及一种锂电池,包括如上所述的锂电池正极。
12.本发明的锂电池具有优异的容量、首效和循环稳定性能。
13.与现有技术相比,本发明的有益效果为:(1)本发明将可溶性钴盐、沉淀剂、络合剂、水与正极基材进行混合,对正极基材进行水洗包覆,在正极基材的表面均匀包覆一层钴的化合物,既可以提高材料导电性还可以起到保护层的作用,减少正极材料与电解液的副反应发生;除此之外,加入沉淀剂可以把残存的锂源沉降下来,防止后期匀浆过程中因ph过高出现果冻状情况,严重影响正极材料容量的发挥以及循环保持率;本发明的制备方法简单,周期短,易合成;(2)本发明的正极材料在正极基材的表面均匀包覆一层钴的化合物,既可以提高材料导电性还可以起到保护层的作用,减少正极材料与电解液的副反应发生。
14.(3)本发明的锂电池正极可赋予锂电池优异的容量、首效和循环稳定性能。
15.(4)本发明的锂电池具有优异的容量、首效和循环稳定性能。
附图说明
16.为了更清楚地说明本发明具体实施方式或现有技术中的技术方案,下面将对具体实施方式或现有技术描述中所需要使用的附图作简单地介绍,显而易见地,下面描述中的附图是本发明的一些实施方式,对于本领域普通技术人员来讲,在不付出创造性劳动的前提下,还可以根据这些附图获得其他的附图。
17.图1为实施例1中的正极材料的首次充放电曲线图;图2为对比例1中的正极材料的首次充放电曲线图。
具体实施方式
18.下面将结合实施例对本发明的实施方案进行详细描述,但是本领域技术人员将会理解,下列实施例仅用于说明本发明,而不应视为限制本发明的范围。实施例中未注明具体条件者,按照常规条件或制造商建议的条件进行。所用试剂或仪器未注明生产厂商者,均为可以通过市购获得的常规产品。
19.根据本发明的一个方面,本发明涉及一种四元正极材料的制备方法,包括以下步骤:将正极基材、可溶性钴盐、沉淀剂、络合剂和水进行混合,对混合后的体系进行液固分离,收集固相并进行干燥和煅烧;所述正极基材的化学通式为lini
x
co
y
mn
z
al
(1
‑
x
‑
y
‑
z)
o2,其中,0.9 ≤ x<1,0<y<0.07,0<z<0.03。
20.本发明将可溶性钴盐、沉淀剂、络合剂、水与正极基材进行混合,对正极基材进行水洗包覆,在正极基材的表面均匀包覆一层钴的化合物,既可以提高材料导电性还可以起
到保护层的作用,减少正极材料与电解液的副反应发生;除此之外,加入碳酸氢氨溶液可以把残存的锂源沉降下来,防止后期匀浆过程中因ph过高出现果冻状情况,严重影响正极材料容量的发挥以及循环保持率。本发明采用的制备工艺简单,周期短,易合成。
21.优选地,所述络合剂包括nh3·
h2o和/或氯化铵。
22.优选地,所述沉淀剂包括碳酸氢铵。
23.优选地,所述可溶性钴盐包括硫酸钴、硝酸钴和氯化钴中的至少一种。
24.优选地,所述正极基材、所述可溶性钴盐、所述沉淀剂和所述络合剂的质量比为1:(0.006~0.012):(0.004~0.006):(0.15~0.25)。
25.在一种实施方式中,所述正极基材、所述可溶性钴盐、所述沉淀剂和所述络合剂的质量比还可以选择1:0.006:0.004:0.15、1:0.007:0.0045:0.17、1:0.008:0.005:0.19、1:0.009:0.005:0.2、1:0.01:0.005:0.21或1:0.12:0.006:0.25。
26.本发明通过限定正极基材、所述可溶性钴盐、所述沉淀剂和所述络合剂采用适宜的比例,进而使得正极基材的表面可均匀的包覆钴的化合物,并且可有效地沉降残存的锂源。
27.优选地,所述混合的过程中进行搅拌,所述搅拌的转速为100~300r/min,所述搅拌的时间为10~20min。
28.本发明通过采用适宜的搅拌速度和时间,进而使混合液更加均匀,使得钴的化合物更加均匀的包覆于正极基材的表面,进而提高正极材料的电化学性能。
29.在一种实施方式中,所述搅拌的转速为100~300r/min,还可以选择110r/min、120r/min、130r/min、140r/min、150r/min、160r/min、170r/min、180r/min、190r/min、200r/min、210r/min、220r/min、230r/min、240r/min、250r/min、260r/min、270r/min、280r/min或290r/min。
30.优选地,所述混合具体包括以下步骤:向所述正极基材和络合剂溶液的第一混合物中滴加可溶性钴盐溶液,得到第二混合物;向所述第二混合物中滴加沉淀剂溶液。
31.优选地,所述沉淀剂溶液的浓度为4~6mol/l。
32.在一种实施方式中,沉淀剂溶液的浓度还可以选择4.5mol/l、5mol/l或5.5 mol/l。
33.优选地,所述可溶性钴盐溶液的浓度为1~3mol/l。
34.在一种实施方式中,可溶性钴盐溶液的浓度还可以选择1.5mol/l、2mol/l或2.5mol/l。
35.优选地,所述络合剂溶液为nh3·
h2o溶液,所述nh3·
h2o的质量浓度为20%~30%。
36.在一种实施方式中,将正极基材、浓度为25%的nh3·
h2o溶液和蒸馏水混合,在搅拌机中以100~300r/min的转速搅拌5~10min后滴加硫酸钴溶液;再搅拌5~10min后滴加碳酸氢铵溶液。
37.优选地,所述干燥的温度为80~150℃,所述干燥的时间为5~15h。
38.本发明将包覆钴的化合物的正极材料在真空干燥箱中进行干燥处理,通过采用适宜的干燥温度和时间,以去除正极材料中的水分,又不会损害甄姬材料的性能。
39.在一种实施方式中,所述干燥的温度为80~150℃,还可以选择85℃、90℃、95℃、
100℃、105℃、110℃、115℃、120℃、125℃、130℃、135℃、140℃或145℃。
40.在一种实施方式中,所述干燥的时间为5.5h、6h、6.5h、7h、7.5h、8h、8.5h、9h、9.5h、10h、10.5h、11h、11.5h、12h、12.5h、13h、13.5h、14h或14.5h。
41.优选地,所述煅烧的温度为300~500℃,所述煅烧的时间为7~9h。
42.本发明通过适宜的煅烧温度和煅烧时间,进而获得四元正极材料。
43.在一种实施方式中,所述煅烧的温度为300~500℃,还可以选择310℃、320℃、330℃、340℃、350℃、360℃、370℃、380℃、390℃、400℃、410℃、420℃、430℃、440℃、450℃、460℃、470℃、480℃或490℃。
44.在一种实施方式中,煅烧的时间为7~9h,还可以选择7.1h、7.2h、7.3h、7.4h、7.5h、7.6h、7.7h、7.8h、7.9h、8h、8.1h、8.2h、8.3h、8.4h、8.5h、8.6h、 8.7h、8.8h或8.9h。
45.优选地,所述正极基材的制备方法,包括以下步骤:将镍钴锰铝氢氧化物与锂源的混合物进行煅烧处理;所述锂源和所述镍钴锰铝氢氧化物分别以锂元素和混合金属元素计的摩尔比为(1~1.05):1,所述混合金属元素为镍元素、钴元素、锰元素和铝元素,所述镍钴锰铝氢氧化物中,镍元素、钴元素、锰元素和铝元素的摩尔比为(89~91):(6.8~7.1):(1.8~2.1):1。
46.本发明中的锂源为氢氧化锂(lioh)。
47.在一种实施方式中,所述锂源和所述镍钴锰铝氢氧化物分别以锂元素和混合金属元素计的摩尔比为(1~1.05):1,还可以选择1:1、1.01:1、1.02:1、1.03:1或1.04:1。
48.在一种实施方式中,所述镍钴锰铝氢氧化物中,镍元素、钴元素、锰元素和铝元素的摩尔比为90:7:2:1。
49.优选地,所述煅烧处理的温度为650~800℃,时间为7~9h。
50.在一种实施方式中,所述煅烧处理的温度为650~800℃,还可以选择660℃、670℃、680℃、690℃、700℃、710℃、720℃、730℃、740℃、750℃、760℃、770℃、780℃或790℃。
51.在一种实施方式中,所述煅烧处理的时间为7~9h,还可以选择7.1h、7.2h、7.3h、7.4h、7.5h、7.6h、7.7h、7.8h、7.9h、8h、8.1h、8.2h、8.3h、8.4h、8.5h、8.6h、 8.7h、8.8h或8.9h。
52.优选地,在含有氧气的气氛下进行所述煅烧处理。
53.在一种实施方式中,所述正极基材的制备方法,包括以下步骤:将镍钴锰铝氢氧化物与lioh按照一定摩尔比进行干法混合,得到干混物,然后将干混物在650~800℃,氧气气氛中,煅烧7~9h,冷却、过筛后得到正极基材。
54.根据本发明的另一个方面,本发明还涉及所述的四元正极材料的制备方法得到的四元正极材料。
55.本发明的正极材料具有优异的容量、首效和循环稳定性能。
56.根据本发明的另一个方面,本发明还涉及一种锂电池正极,包括如上所述的四元正极材料。
57.本发明的锂电池正极片的制备方法,包括以下步骤:将所述四元正极材料、炭黑导电剂、粘结剂聚偏氟乙烯(pvdf)和n
‑
甲基吡咯烷酮(nmp)混合均匀制备电池正极浆料,其中,四元正极材料、炭黑导电剂、粘结剂pvdf和nmp的质量比为(94~96):(2~3):(2~3):(4~6);将上述正极浆料涂布在厚度为20~40um的铝箔上,
经过真空干燥和辊压做成正极极片。
58.根据本发明的另一个方面,本发明还涉及一种锂电池,包括如上所述的锂电池正极。
59.本发明的锂电池包括上述正极片、锂金属负极片和电解液;电解液的组成为:六氟磷酸锂(lipf6)、碳酸乙烯酯(ec)和碳酸二甲酯(dmc);其中,lipf6为1.15m,ec和dmc的体积比为1:1。
60.本发明的锂电池具有优异的容量、首效和循环稳定性能。
61.下面将结合具体的实施例和对比例对本发明作进一步地解释说明。
62.实施例1一种四元正极材料的制备方法,包括以下步骤:(a)将镍钴锰铝氢氧化物和lioh在混料机里干法混合,将干法混合后的物料在普通箱式炉700℃氧气气氛下煅烧8h后,冷却、粉碎并过筛得到正极基材;其中,镍钴锰铝氢氧化物与lioh分别按照金属元素计的摩尔比为1:1.025(li/metal(ni、co、mn和al)=1.025) ;镍钴锰铝氢氧化物中,ni、co、mn和al 的摩尔比为90 : 7 : 2 : 1;(b)将上述得到的正极基材、氨水、蒸馏水按照1: 0.2:100的质量比进行混合,在200r/min下搅拌5分钟后得到第一混合体系;再向得到的第一混合体系中滴加硫酸钴溶液,正极基材与硫酸钴的质量比为1:0.01,在200r/min搅拌10分钟后得到第二混合体系,再向第二混合体系中滴加碳酸氢铵溶液,正极基材与碳酸氢铵的质量比为1:0.005,搅拌均匀后抽滤,在100℃真空干燥箱放置10h,烘干后取出;其中,硫酸钴溶液的浓度为2mol/l;碳酸氢铵溶液的浓度为5mol/l;(c)最后将干燥后得到的材料在400℃氧气气氛下煅烧8h后,冷却、过筛得到包覆的正极材料;实施例1中的正极材料的首次充放电曲线图如图1所示。
63.实施例2一种四元正极材料的制备方法,包括以下步骤:(a)将镍钴锰铝氢氧化物和lioh在混料机里干法混合,将干法混合后的物料在普通箱式炉700℃氧气气氛下煅烧8h后,冷却、粉碎并过筛得到正极基材;其中,镍钴锰铝氢氧化物与lioh分别按照金属元素计的摩尔比为1:1.025(li/metal(ni、co、mn和al)=1.025) ;镍钴锰铝氢氧化物中,ni、co、mn和al 的摩尔比为90 : 7 : 2 : 1;(b)将上述得到的正极基材、氨水、蒸馏水按照1: 0.15:100的质量比进行混合,在200r/min下搅拌5分钟后得到第一混合体系;再向得到的第一混合体系中滴加硫酸钴溶液,正极基材与硫酸钴的质量比为1:0.006;在200r/min搅拌10分钟后得到第二混合体系,再向第二混合体系中滴加碳酸氢铵溶液,正极基材与碳酸氢铵的质量比为1:0.004,搅拌均匀后抽滤,在80℃真空干燥箱放置15h,烘干后取出;其中,硫酸钴溶液的浓度为2mol/l;碳酸氢铵溶液的浓度为5mol/l;(c)最后将干燥后得到的材料在300℃氧气气氛下煅烧9h后,冷却、过筛得到包覆的正极材料。
64.实施例3一种四元正极材料的制备方法,包括以下步骤:
(a)将镍钴锰铝氢氧化物和lioh在混料机里干法混合,将干法混合后的物料在普通箱式炉700℃氧气气氛下煅烧8h后,冷却、粉碎并过筛得到正极基材;其中,镍钴锰铝氢氧化物与lioh分别按照金属元素计的摩尔比为1:1.025(li/metal(ni、co、mn和al)=1.025) ;镍钴锰铝氢氧化物中,ni、co、mn和al 的摩尔比为90 : 7 : 2 : 1;(b)将上述得到的正极基材、氨水、蒸馏水按照1: 0.25:100的质量比进行混合,在200r/min下搅拌5分钟后得到第一混合体系;再向得到的第一混合体系中滴加硫酸钴溶液,正极基材与硫酸钴的质量比为1:0.012;在200r/min搅拌10分钟后得到第二混合体系,再向第二混合体系中滴加碳酸氢铵溶液,正极基材与碳酸氢铵的质量比为1:0.006,搅拌均匀后抽滤,在150℃真空干燥箱放置5h,烘干后取出;其中,硫酸钴溶液的浓度为2mol/l;碳酸氢铵溶液的浓度为5mol/l;(c)最后将干燥后得到的材料在500℃氧气气氛下煅烧7h后,冷却、过筛得到包覆的正极材料。
65.对比例1一种正极材料的制备方法,包括以下步骤:(a)正极基材的制备:方法同实施例1中的步骤(a);(b)将得到的正极基材与蒸馏水按照质量比为1:1的比例混合,200r/min搅拌10分钟后抽滤,在100℃真空干燥箱放置10h,烘干后取出;(c)将(b)中干燥后的材料在400℃氧气气氛下煅烧8h后,冷却、过筛得到正极材料;本对比例中的正极材料的首次充放电曲线图如图2所示。
66.对比例2一种正极材料的制备方法,包括以下步骤:(a)正极基材的制备:方法同实施例1中的步骤(a);(b)将得到的正极基材与蒸馏水按照质量比为1:1的比例混合,再向混合体系中滴加碳酸氢铵溶液,正极基材与碳酸氢铵的质量比为1:0.006,搅拌均匀后抽滤,200r/min搅拌10分钟后抽滤,在100℃真空干燥箱放置10h,烘干后取出;其中碳酸氢铵溶液的浓度为5mol/l。
67.(c)将(b)中干燥后的材料在400℃氧气气氛下煅烧8h后,冷却、过筛得到正极材料;实验例分别利用实施例和对比例得到的正极材料制备扣式电池,包括以下步骤:将质量比为95:2.5:2.5:5的正极材料、炭黑导电剂、粘结剂pvdf和nmp混合均匀制备电池正极浆料;将正极浆料涂布在厚度为12μm的铝箔上,经过真空干燥和辊压做成正极极片,以锂金属片为负极,电解液组成为:1.15m lipf6,ec和dmc的体积比为1:1;并组装扣式电池。
68.材料的电性能测试采用蓝电电池测试系统在45℃下进行测试,测试电压范围为3v~4.3v;测试1周容量以及50周容量保持率。
69.本发明将可溶性钴盐溶液、沉淀剂溶液、络合剂与正极基材按照一定的顺序进行混合,对正极基材进行水洗包覆,在正极基材的表面均匀包覆一层钴的化合物,既可以提高材料导电性还可以起到保护层的作用,减少正极材料与电解液的副反应发生,同时沉淀剂可以把残存的锂源沉降下来,防止后期匀浆过程中因ph过高出现果冻状情况,严重影响正极材料容量的发挥以及循环保持率;由表1可知,本发明实施例的方法得到的正极材料用于制备锂电池,可获得优异的电化学性能。而采用对比例1或对比例2中的方法得到的正极材料,其制备得到的锂电池在充电比容量、放电比容量、首效和50圈循环保持率方面均差于本发明实施例得到的正极材料所制备的锂电池。
70.最后应说明的是:以上各实施例仅用以说明本发明的技术方案,而非对其限制;尽管参照前述各实施例对本发明进行了详细的说明,但本领域的普通技术人员应当理解:其依然可以对前述各实施例所记载的技术方案进行修改,或者对其中部分或者全部技术特征进行等同替换;而这些修改或者替换,并不使相应技术方案的本质脱离本发明各实施例技术方案的范围。
再多了解一些
本文用于企业家、创业者技术爱好者查询,结果仅供参考。