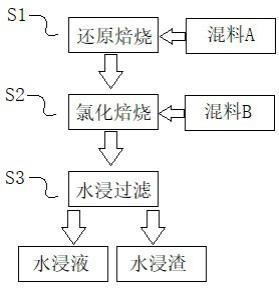
1.本发明属于冶炼废渣的资源化利用,具体涉及一种锰渣协同氯化钙废渣资源化处理方法。
背景技术:
2.在电解二氧化锰的生产过程中,碳酸锰经硫酸浸出后,在石灰中和阶段将产生大量的电解二氧化锰渣(本文简称“锰渣”),每生产1吨二氧化锰将产生约4吨锰渣,锰渣中除主成分硫酸钙和少量的锰氧化物相等。
3.目前锰渣的主要大宗处置方式为填埋,特别是在贵州省等地区,丘陵山区的地理条件有利于百万吨甚至千万吨级填埋场的建设。但填埋法存在渗滤液处理难,渗滤液污染地表地下水源等问题,从本质上而言是一种将污染暂时性掩盖的处理方式,无法从根本上实现锰渣的消纳。
4.由于电解锰渣中含有大量的硅钙成分,可用于回收制备水泥建材,目前国内少数几家企业开展了相关的产业化实践,利用电解锰渣制备成水泥建材材料。但是电解锰渣中含有的金属锰在制备水泥建材存在环境污染风险,并且对水泥建材的强度性能和安全性能存在较大隐患。
5.并且锰含量较高的锰渣中锰资源流失严重,目前尚无理想的处理工艺能将锰渣中的锰物相分离。若能实现上述目标,则既可实现锰渣中金属锰的资源化,又可实现固渣的无害化处理,为后续制备建材奠定基础。
6.申请号为cn201910588744.2的中国专利申请公开了一种高铁锰矿氯化还原焙烧生产碳酸锰和铁粉的方法,将无水氯化镁、无水氯化钙、炭质还原剂与高铁锰矿粉混合均匀得混合物,将所有混合物一次还原焙烧,冷却后得到还原产物,该方法是针对高铁锰物料进行的铁、锰分离回收,最终得到碳酸锰和铁粉,但工艺弃渣为二次废渣,并未实现固废的大宗消纳。并且反应过程将离子型的无水氯盐直接作为氯化反应的反应物与高铁锰原料进行高温强还原反应,由于氯盐结构稳定,氯化反应的效率并不高;并且在还原和氯化混合的高温反应体系中,高铁锰物料中的铁还会优先于锰被迅速氯化成三氯化铁,三氯化铁沸点仅为316℃,低沸点的三氯化铁迅速挥发进入烟气逸散,消耗大量氯化剂,导致锰氯化回收率降低,使得最终得到的二次废渣中仍留存大量的锰。
7.因此该种针对高铁锰矿的锰回收方式在电解锰渣上并不适用。
技术实现要素:
8.本发明解决的技术问题是:针对现有电解锰渣向建材材料进行资源化处理的过程中存在的上述问题,提供一种锰渣协同氯化钙废渣资源化处理方法,既能够将锰渣中的锰物相通过氯化锰的形式进行分离回收,同时能够保证分离后的废渣能够满足建材材料的要求。
9.本发明采用如下技术方案实现:
一种锰渣协同氯化钙废渣资源化处理方法,分别对锰渣和氯化钙废渣分段焙烧进行还原氯化反应,具体包括如下步骤:s1、将锰渣和煤粉混合形成混料a,将混料a加入回转窑中,通入空气进行还原焙烧,通过煤粉中的碳做还原剂,将锰渣中的所有高价锰物相还原成低价锰物相;s2、将氯化钙废渣和石英砂混合形成混料b,将混料b连同s1步骤中的还原焙烧产物一同加入氯化窑中,通入燃气与空气进行氯化焙烧,窑内通过氯化钙废渣中的水蒸气与氯化钙高温转化形成氯化氢气氛,所述还原焙烧产物中的低价锰物相在氯化氢气氛下氯化反应成氯化锰;s3、将氯化焙烧产物冷却后水浸,分离水浸液和水浸渣,其中所述水浸液蒸发结晶得到氯化锰,所述水浸渣干燥后得到用于水泥建材的钙盐和二氧化硅。
10.根据权利要求1所述的一种锰渣协同氯化钙废渣资源化处理方法,所述氯化钙废渣为含水量为15%
‑
30%的膏体。
11.具体的,在本发明的一种锰渣协同氯化钙废渣资源化处理方法中,所述步骤s1中所述锰渣与煤粉按照重量比5~10:1进行混合。
12.具体的,在本发明的一种锰渣协同氯化钙废渣资源化处理方法中,所述步骤s2中所述氯化钙废渣与石英砂的混合比例依据渣中钙含量计算,控制混料b中的氯化钙与石英砂中二氧化硅的质量比为1.5~2:1。
13.具体的,在本发明的一种锰渣协同氯化钙废渣资源化处理方法中,所述步骤s2中进行氯化焙烧的混料b与还原焙烧产物的比例依照焙烧还原产物中的一氧化锰含量计算,控制氯化钙与一氧化锰的质量比为1.5~2:1。
14.具体的,在本发明的一种锰渣协同氯化钙废渣资源化处理方法中,所述步骤s1中的还原焙烧升温至800~1200℃并停留60~150min。
15.具体的,在本发明的一种锰渣协同氯化钙废渣资源化处理方法中,所述步骤s2中的氯化焙烧燃烧加热至600~1000℃并停留30~60min。
16.具体的,在本发明的一种锰渣协同氯化钙废渣资源化处理方法中,所述步骤s3中进行水浸的液固比为2~5:1。
17.具体的,在本发明的一种锰渣协同氯化钙废渣资源化处理方法中,所述步骤s3中水浸流程在窑尾的水冷搅拌槽中进行。
18.具体的,在本发明的一种锰渣协同氯化钙废渣资源化处理方法中,所述水浸液通过与窑尾的高温尾气换热进行蒸发结晶。
19.考虑到锰渣中除开锰之外大量的硫酸钙可作为水泥缓凝剂,本发明通过将氯化钙废渣中大量的氯与锰渣中的锰形成氯化锰。具体反应如下:首先通过还原焙烧将锰渣中的锰物相还原成低价锰物相,主要反应化学方程式如下:mn2o
3 c= mno co
↑
;mn2o
3 c= mno co2↑
;mn2o3 co = mno co2↑
。
20.在氯化焙烧阶段,首先通过氯化钙的高温转化,形成氯化氢气氛,主要方程式如下:
cacl
2 sio
2 h2o = casio
3 hcl
↑
。
21.利用氯化钙转化产生的氯化氢气氛对还原焙烧后的锰渣进行氯化焙烧,使低价锰物相通过如下反应生成氯化锰,主要反应化学方程式如下:mno hcl
↑
= mncl
2 h2o。
22.氯化焙烧之后的产物包括氯化锰、钙盐和二氧化硅混合物,利用氯化锰易溶于水,其他钙盐和二氧化硅不易溶于水的特性,通过水浸分离氯化锰回收锰渣中的锰资源,以及锰含量低的浸出渣用于水泥生产,既实现了锰渣和氯化钙废渣的固废协同资源化,也保证了去除金属锰之后的浸出渣用于水泥材料的安全性能。
23.在本发明的处理工艺中,还利用焙烧过程中的冷却水系统和高温尾气进行水浸以及水浸产物的干燥结晶,降低固废渣资源回收的能耗。
24.本发明具有如下有益效果:(1)本发明针对电解锰渣和氯化钙废渣作为原材料分别混料,并且采用分段还原焙烧和氯化焙烧两个阶段进行,两个流程相互之间不存在干扰,每个流程反应单一,能够更有效地控制反应过程,更有利于整体工艺的实施。
25.(2)本发明先对锰渣进行还原焙烧后,再利用氯化钙废渣进行氯化反应,在s1步骤对电解锰渣的混料a的还原焙烧过程中,只发生将高价锰还原成低价锰的还原反应,保证了锰渣中所有锰能够还原反应完全,然后在s2步骤中将氯化钙废渣的混料b进行二次氯化焙烧,在二次氯化焙烧反应过程中,本发明采用的氯化钙废渣为含水量在15
‑
30%的膏状物料,相比较无水氯化钙,本发明是通过氯化钙、二氧化硅和水分子通过高温转化,形成氯化氢和硅酸钙,将氯化钙中的氯离子置换成氯化氢,氯化氢在高温下为气体,在氯化窑内形成氯化氢反应气氛,还原焙烧后的锰渣产物在氯化氢气氛中进行氯化反应。本发明的锰渣还原反应和氯化反应分成两个阶段进行,在s1步骤中锰还原能够反应更彻底,同时在氯化氢气氛中进行的氯化反应,能够更加高效地将还原后的低价锰物相从锰渣中提炼出来,氯化反应生成的水分子循环与窑内的氯化钙和二氧化硅循环反应,持续提供氯化窑内的氯化氢气氛,还原焙烧产物中的锰被氯化的效率得到进一步提升。
26.(3)本发明在对电解锰渣和氯化钙废渣资源化处理后,得到的产物中,电解锰渣中的锰与氯化钙废渣中的氯离子结合形成溶于水的氯化锰进行回收,其余固渣成分为除锰后剩余的硅酸钙和二氧化硅,由于硅酸钙是水泥的主要成分,二氧化硅是生产水泥的必要原材料,从而使固渣达到制备水泥建材的标准,可以直接用于水泥建材原料,解决两种废渣回用于建材存在的锰、氯含量高的问题,因此本发明最终实现两种废渣的全量化消纳,不会产生二次废弃物。
27.综上所述,本发明提出的一种锰渣协同氯化钙废渣资源化处理方法中,通过锰渣与氯化钙废渣两段焙烧实现协同资源化的方法,利用氯化钙可与二氧化硅、空气中的水蒸气在高温下形成硅酸钙与氯化氢气体的反应特点,将预先还原完全的含有低价锰物相的锰渣与上述物料混合进行高温氯化焙烧,焙烧产物分离得到氯化锰,并得到硅酸钙、硫酸钙、二氧化硅混合物组成的水浸固渣,实现锰渣和氯化钙废渣的协同资源化利用,既提高了上述固废的资源价值,具有较高的经济效益,也降低了对两种固废单独处理造成的环境污染,整个处理工艺步骤简单易行,回收效率高,可在电解锰行业广泛推广应用。
附图说明
28.图1为本发明的工艺流程示意图。
29.图2为实施例1中的锰渣xrd物相图谱。
30.图3为实施例1中的水浸渣xrd物相图谱。
具体实施方式
31.以下结合实施例对本发明加以说明,但本发明的保护范围不局限于所述实施例。
32.实施例1如图1所示,本实施例的步骤s1称取锰渣1吨,配入标煤煤粉200kg均匀混合成混料a,将混料a通过螺旋给料机加入还原焙烧窑,窑内通入空气升温至1200℃并在该温度区间停留保持时间150min。
33.本实施例治理的锰渣主要成分为硫酸钙、二氧化硅及少量三氧化二锰等,如图2中的锰渣xrd物相图谱所示,锰渣中各成分的元素含量如表1所示,表中通过氧化物来表达锰渣中各个成分相应元素含量(其中钙通过cao形式表达,硫通过so3形式表达,锰通过mno形式来表示)。
34.表1 电解锰渣主要成分(%)物相sio2al2o3caomgoso3mno其他含量30.604.8317.100.9424.505.4516.58步骤s2称取700kg含水率在15%的氯化钙废渣与56kg石英砂均匀混合成混料b,混料b中氯化钙比石英砂中二氧化硅的质量比为1.5:1,将还原焙烧产物直接加入到氯化焙烧窑中,将混料b同时加入到氯化焙烧窑中,混料b中的氯化钙与还原焙烧产物体系中的一氧化锰质量比为2:1,氯化焙烧窑中通入空气和天然气作为燃气燃烧加热,控制焙烧温度为1000℃,停留时间为60min。
35.本实施例中选取协同的氯化钙废渣主要成分的元素含量如表2所示,氯化钙废渣中氯化钙的质量含量为15.52%,渣整体呈碱性。
36.表2 氯化钙废渣主要成分(%)物相caco3caso4fe2o3al2o3sio2cacl2mg(oh)2caoloss含量40.233.940.71.32.115.528.065.4722.68步骤s3将氯化焙烧产物冷却后,直接倒入窑尾的水冷搅拌槽中进行水浸,控制搅拌槽内料浆液固比为5:1,料浆通过料浆泵泵入压滤机中进行水渣分离过滤,其中压滤出的水浸液泵送至换热蒸发系统中蒸发结晶,得到的产物为氯化锰晶体,干燥后的水浸渣物相如图3所示。
37.通过测算,本实施例最终得到纯度为95%的氯化锰94.2kg,较电解锰渣中的锰含量,锰回收率达92.56%,水浸渣烘干后滤渣1.3吨,经检测最终渣中含有51.67%的硅酸钙、2.46%的二氧化硅和33.15%的硫酸钙,均可直接用于水泥建材材料。
38.实施例2本实施例选取与实施例1相同成分的锰渣和氯化钙。
39.本实施例的步骤s1称取锰渣1吨,配入标煤煤粉100kg均匀混合成混料a,将混料a通过螺旋给料机加入还原焙烧窑,窑内通入空气升温至800℃并在该温度区间停留保持时
间60min。
40.步骤s2称取520kg含水率在20%的氯化钙废渣与32kg石英砂均匀混合成混料b,混料b中氯化钙比石英砂中二氧化硅的质量比为2:1,将还原焙烧产物直接加入到氯化焙烧窑中,将混料b同时加入到氯化焙烧窑中,混料b中的氯化钙与还原焙烧产物体系中的一氧化锰质量比为1.5:1,氯化焙烧窑中通入空气和天然气作为燃气燃烧加热,控制焙烧温度为600℃,停留时间为30min。
41.步骤s3将氯化焙烧产物冷却后,直接倒入窑尾的水冷搅拌槽中进行水浸,控制搅拌槽内料浆液固比为2:1,料浆通过料浆泵泵入压滤机中进行水渣分离过滤,其中压滤出的水浸液泵送至换热蒸发系统中蒸发结晶,得到的产物为氯化锰晶体,本实施例干燥后的水浸渣物相虽然通过化学物相分析方法得出各成分含量虽略有差异,但受限于xrd分析对低结晶度物相的低灵敏度,本实施例的水浸渣xrd图谱与实施例1并无明显差异,可参考实施例1的水浸渣xrd图谱。
42.通过检测,本实施例最终得到纯度为95%的氯化锰26.37kg,较电解锰渣中的锰含量,锰回收率为25.91%,水浸渣烘干后滤渣1.5吨,经检测,其主要成分包括39.82%的硅酸钙、3.91%的氯化钙、2.98%的二氧化硅和28.70%硫酸钙。此外,由于锰物相未充分氯化,渣中锰含量高达2.08%,氯化钙由于外层硅酸钙的包裹,难以在水浸流程被浸出,最终进入水浸渣相。
43.本实施例中的锰回收率低的原因为氯化焙烧阶段温度降低,虽然从热力学角度,氯化钙的分解在600℃下可自发进行,但由于石英砂在此温度下反应活性较低,导致氯化氢产生量不足,造成锰未充分氯化。但在本实施例中的反应条件下进行电解锰渣中的锰回收的回收收益能够与成本基本持平,如进一步降低反应参数则会导致回收成本超过回收收益,失去资源化回收的意义。
44.实施例3本实施例选取与实施例1相同成分的锰渣和氯化钙。
45.如图1所示,本实施例的步骤s1称取锰渣1吨,配入标煤煤粉150kg均匀混合成混料a,将混料a通过螺旋给料机加入还原焙烧窑,窑内通入空气升温至1000℃并在该温度区间停留保持时间120min。
46.步骤s2称取630kg含水率在30%的氯化钙废渣与50kg石英砂均匀混合成混料b,混料b中氯化钙比石英砂中二氧化硅的质量比为1.5:1,将还原焙烧产物直接加入到氯化焙烧窑中,将混料b同时加入到氯化焙烧窑中,混料b中的氯化钙与还原焙烧产物体系中的一氧化锰质量比为1.8:1,氯化焙烧窑中通入空气和天然气作为燃气燃烧加热,控制焙烧温度为800℃,停留时间为45min。
47.步骤s3将氯化焙烧产物冷却后,直接倒入窑尾的水冷搅拌槽中进行水浸,控制搅拌槽内料浆液固比为4:1,料浆通过料浆泵泵入压滤机中进行水渣分离过滤,其中压滤出的水浸液泵送至换热蒸发系统中蒸发结晶,得到的产物为氯化锰晶体,本实施例干燥后的水浸渣物相虽然通过化学物相分析方法得出各成分含量虽略有差异,但受限于xrd分析对低结晶度物相的低灵敏度,本实施例的水浸渣xrd图谱与实施例1并无明显差异,可参考实施例1的水浸渣xrd图谱。
48.通过检测,本实施例最终得到纯度为95%的氯化锰87.26kg,较电解锰渣中的锰含
量,锰回收率达85.74%,水浸渣烘干后得滤渣1.4吨,其主要成分包括47.05%的硅酸钙、2.37%的二氧化硅和31.06%的硫酸钙,均可直接作为水泥建材材料。
49.从实施例1
‑
3可以得出,本发明通过氯化钙废渣协同对锰渣进行锰的回收以及处理固废后作为水泥建材材料的资源化处理,降低了单独对锰渣和氯化钙废渣进行处理的成本,并且提高了冶金废渣的资源回收利用。
再多了解一些
本文用于企业家、创业者技术爱好者查询,结果仅供参考。