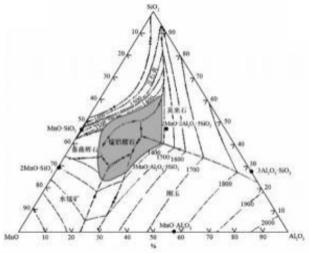
1.本发明属于转炉冶炼技术领域,具体涉及一种45#钢精炼造渣方法。
背景技术:
2.45#钢是一种优质碳素结构钢,对应日标s45c,美标1045,德标c45。应用广泛,涉及交通运输、机械制造、国防工业等重要行业,具有良好的综合机械性能,广泛应用于各种重要的结构零件,特别是那些在交变负荷下工作的连杆、螺栓、齿轮及轴类等。由于终端产品拉拔,加工工艺流程复杂,因此,对45#钢的品质要求严格,尤其是拉拔性能。因此对钢的纯净度、化学成分、夹杂物控制等提出了严格的要求。在钢铁行业持续低迷的市场下,为了开拓市场突破建材生产基地的产品单一问题,提高市场竞争力和产品质量,促进产品的升级换代,提高产品附加值,开始研发45#钢,但由于国内多家钢厂相继开发出的45#钢使利润空间下降,因此迫切需要突破惯性思维,达到低本高质的研发目标。
技术实现要素:
3.本发明的目的在于提供一种45#钢精炼造渣方法。
4.本发明解决其技术问题所采用的技术方案是:一种45#钢精炼造渣方法,包括以下步骤:
5.1)造渣操作,石灰总量1000~1200kg,精炼炉补加500~600kg与适量萤石球,石灰与萤石总量配比在8:1~6:1;
6.2)进站后先破顶,根据实际渣况确定精炼石灰加入时机与批量,其中单批石灰加入200kg~300kg/次,萤石根据实际渣况配加,一次送电完毕后石灰加入总量≥1000kg;
7.3)供电操作,起弧档位5~7档,功率5档,化渣、埋弧趋于良好后可视进站温度及成分需求情况选择4~6档,功率选择3~5档,换档时间间隔》5s,化渣时间≥5min;
8.4)正常炉次若需提温时采用5~3档,功率选择为2~4档进行提温,以电弧稳定,噪音较小为原则调整功率;
9.5)除每次起弧时段外,正常加热期间埋弧声响尖锐及电流波动上下差值≥10000a时,及时降低档位与底吹强度,保证埋弧效果;
10.6)底吹制度,底吹流量档位与钢水裸露直接匹配流量,1档进行软吹,<40nl/min对应渣液面微动钢水不裸露,2档进行供电,100~200nl/min钢水裸露直径不大于200m,3档进行调整成分,600~1000nl/min控制钢水裸露直径不大于600m;
11.7)炉内微正压控制,减少炉门开动次数与时长,且根据不同时段产生烟气量与浓度,及时调整侧吸的开度,在保证顶吸除尘烟气不外泄的前提下,把侧吸开度降至最低,保持炉内微正压的还原气氛;
12.8)定氧操作,进站与软吹前进行定氧操作,定氧操作时定氧探头要插入钢液面内≥400mm,在进行定氧操作前关闭底吹渣面平静后在开始;
13.9)扩散脱氧,观察烟尘颜色来判定脱氧程度,炉渣脱氧不良时,烟尘呈深黄、黄、浅
黄,并且黄烟与白烟频繁转换时说明脱氧不完全;当烟尘颜色转变为灰白、白色、乳白色且持续保持说明炉渣脱氧相对完全,及时粘取渣样进行确认;
14.10)根据脱氧实际情况,分批少量,扩散脱氧剂按照20~30kg/次加入,中前期使用sic达脱氧与发泡,后期不具备发泡条件后使用sife,均匀撒在渣面上,进行造白渣操作,保持终渣feo mno不大于1%,扩散脱氧剂加入时机与频次根据烟尘颜色变化与渣杆渣样颜色灵活调整;
15.11)喂钙线操作,喂钙线先放下喂丝导管,采用软吹氩模式,严禁钢液面裸露,喂钙线速度4.5m/s~5m/s,在喂线时看到渣面上有白色ca火焰,调整喂丝速度和/或进行小氩气流量搅拌;为促进钢液中夹杂物上浮,钙处理后保证软吹12~15min。
16.本发明具有以下有益效果:根据45#钢脱氧合金化合金化夹杂物特点与使用性能需求,进站炉渣碱度2.0~1.7,软吹前炉渣碱度1.0~1.5,渣中al2o3≤12%的渣系,仅使用sic与sife进行扩散脱氧与炉渣改质,吨钢成本降低3.9元/t,确保钢中夹杂物处于低熔点区域、具有良好变形能力、塑性、可浇性。
附图说明
17.图1为mno-al2o3-sio2系夹杂物示意图。
18.图2为cao-al2o3-sio2系夹杂物示意图。
具体实施方式
19.现在结合附图对本发明作进一步详细的说明。
20.一、低成本转炉增碳新工艺:终点碳高低,直接对应着冶炼用氧量的多少,即决定着钢水中氧含量的高低,终点碳过高,钢水温度难于达到要求,增加lf精炼炉的压力,钢中的磷含量不易达标;终点碳过低,钢水氧性过高,脱氧产物较多,钢质较差。根据实践总结,终点碳控制在0.20
±
0.05%较宜。但为了确保成分均匀,有效避免增碳剂加入对成品碳偏析及钢中氮含量等控制影响、避免部分增碳剂进入钢种中使炉渣变稠,导致精炼造渣过程脱氧难以控制,这就要求钢包进入lf工位后增大底吹流量并且延长处理时间。
21.因此经过多次现场试验,采用出钢完毕向钢包折铁进行增碳新工艺,完全替代原有出钢过程使用增碳剂增碳操作模式,基本操作流程为:放钢过程中不加增碳剂;放钢完毕钢包车开至东侧(挡火门与炉壳之间)折铁专用位;炉长记录好钢包车称显示的钢水实际重量;根据转炉出钢碳含量、铁水实际碳含量,按照目标成分要求,计算折铁量,折铁量计算公式为:(目标碳含量-出钢碳含量-合金碳量)*钢水量/铁水碳含量;利用溅渣时间指挥天车将铁包吊运至准备折铁位置;指挥天车缓慢起副钩,小流慢折,折铁时关注钢包车重量增值,当达到计算折铁量停止折铁;指挥天车降铁包吊至兑铁等待位后进行加废钢在兑铁流程,折铁完毕在加入顶渣。
22.二、低成本转炉、精炼夹杂物控制新工艺
23.45#钢线材中非金属夹杂物的存在,破坏了基体组织的连续性与均匀性,起到了显微裂纹的作用。当受到外力作用时,在夹杂物处首先产生应力集中,当应力集中达到一定程度时,就会使该处开裂以至造成拉拔断裂。夹杂物对中45#钢线材性能的影响因素主要有以下3种。
24.(1)尺寸的影响。夹杂物的尺寸增大对45#钢线材的不利影响也会逐步增大。生产经验表明夹杂物大于被加工钢丝直径的2%就会导致在冷拉或合股过程中脆性断裂。
25.(2)几何形态的影响。长条状、多角形及其他不规则形状的夹杂物对中高碳钢线材性能的影响要大于球形的夹杂物,铝脱氧产生的al2o3夹杂在钢中呈尖角、块状或链串状这对中高碳线材制品的抗疲劳性能非常有害。
26.(3)钢基体与夹杂物变形能力差异的影响。在钢的热加工温度下非金属夹杂物与钢基体的变形能力差别很大,轧制过程在钢基体—夹杂物界面上可能会形成微裂纹、间隙等这些裂纹、间隙在随后的冷拉或使用过程中会成为破坏源,尤其是al2o3对45#钢线材危害最大因为氧化铝不具备塑性变形能力。
27.非金属夹杂物的存在严重影响45#钢线材的性能,尤其是al2o3类夹杂,因此在45#钢冶炼过程中必须采取一些措施来抑制非金属夹杂物对45#钢线材的危害,这有利于提高中高碳钢线材的冷拉性能和抗疲劳性能从而提高中高碳钢线材制品的产品质量。
28.2.1低成本转炉脱氧合金化工艺
29.根据硅锰镇静钢脱氧特点,[o]<10ppm,sio2析出水口堵塞;[o]>20ppm铸坯气孔增加;[o]=10~20ppm最佳范围。而单独采用si mn脱氧工艺无法完成上述效果,因此采用si mn al脱氧工艺,但als小于0.002%时,钢水脱氧不良,铸坯形成针孔;als大于0.005%时,有单独al2o3析出,可浇性差,在0.002~0.005%时既不堵水口,铸坯又不产生皮下针孔,而夹杂物具有良好的塑性。如何精准控制钢中als是含量既达到高质效果,又降低als对al2o3,重新优化脱氧合金化新工艺,采用钢芯铝与硅钡钙符合沉淀脱氧新工艺,脱氧合金化顺序:出钢见钢流先加入钢芯铝(预沉淀脱氧)
→
出钢1/4左右先加入硅铁再加入硅锰
→
出钢2/3~3/4左右加入硅钡钙(终沉淀脱氧)。有效降低钢中als含量,促进大颗粒al2o3夹杂上浮。钢芯铝与硅钡钙配加数量为:出钢前利用tco投弹式副枪进行定氧,根据实际[o]含量按照动态调整钢芯铝加入量定量配加硅钡钙新模式,按照[(tco定氧值-0.008)*1000*0.02/铝脱氧利用系数)]kg/炉,进行吨钢芯铝用量确定。后补加0.3kg/t硅钡钙,按照此模式精炼进站[o]含量0.002
±
0.0005%确定精准脱氧效果降低后续控制难度。
[0030]
2.2低成本精炼造渣工艺
[0031]
在采用cao-al2o3-sio2精炼渣系的钢中,als随精炼渣碱度、渣中al2o3含量的升高而升高,选择低碱度和低al2o3含量的精炼渣系可以进一步降低als,满足形成塑性夹杂物的要求。研究表明,此渣系下钢中的夹杂物主要为mno-al2o3-sio2系夹杂物和cao-al2o3-sio2系夹杂物,对于mno-al2o3-sio2三元夹杂物,组成分布在锰铝榴3mno
·
al2o3·
sio2及其周围的低熔点区域时具有良好变形能力,如图1中阴影区域所示,该区域内al2o3质量分数在15%~30%;对于mno-al2o3-sio2三元夹杂物,图2中的钙斜长石\钙黄长石、磷石英和假硅灰石交界的阴影区域为夹杂物塑性良好的成分区,在此范围内的夹杂物碱度cao/sio2为0.2~1.0,al2o3质量分数在8%~25%。但由于45#钢,其成品尺寸大,对夹杂物形态和尺寸要求不如帘线钢高,因此,lf终渣碱度可以提高,cao/sio2=0.8~1.5,al2o3《15%。
[0032]
2.2.1精炼低成本造渣工艺实施关键点
[0033]
(1)造渣操作
[0034]
1)配电工每炉钢水进站时到现场观察渣况。
[0035]
2)石灰总量控制1000~1200kg(转炉顶渣配加500~600kg 100kg萤石球),精炼炉补加500~600kg与适量萤石球,石灰与萤石总量配比在8:1~6:1左右。
[0036]
3)进站后先破顶,根据实际渣况决定精炼石灰加入时机与批量(单批石灰加入200~300/次,萤石根据实际渣况配加,正常情况下一次送电完毕后石灰加入总量≥1000kg,达到早化渣、早变渣、早成渣目标。
[0037]
4)每次送电结束及送电过程埋弧声响异常等情况下,及时粘取渣样,后根据实际渣形貌进行针对性调渣操作。根据渣杆渣样形貌调渣技巧为:
[0038]
①
玻璃态——渣中酸性氧化物或caf2含量高,碱度偏低,在这种渣况加入石灰后通电化渣,每次加入量不超200kg/炉(调渣过程做到少调精调,严禁调渣过度出现补加萤石二次调渣现象)。化透后在粘取渣样观察。
[0039]
②
渣面平滑、厚度适宜(渣杆粘渣厚度在4
±
1mm)——这种渣冷却后应碎裂(较脆)是比较理想的。
[0040]
③
渣况表面粗糙不平,厚薄不均——石灰量过大或石灰熔化不好甚至出现未熔化的石灰颗粒。渣子发粘,加入caf2进行调整,每次加入量50~80kg左右,后再根据渣况调渣。
[0041]
表1精炼渣系控制要求
[0042][0043]
(2)供电操作
[0044]
1)起弧档位5~7档,功率5档。化渣、埋弧趋于良好后可视进站温度及成分需求情况选择4~6档,功率选择3~5档,换档时间间隔》5s,化渣时间≥5min。
[0045]
2)冶炼过程视温度与节奏,正常炉次若需提温时采用5~3档,功率选择为2-4档进行提温,以电弧稳定,噪音较小为原则调整功率。
[0046]
3)除每次起弧时段外,正常加热期间埋弧声响尖锐及电流波动上下差值≥10000a等异常情况及时降低档位与底吹强度,保证埋弧效果。
[0047]
4)底吹制度——底吹流量档位与钢水裸露直接匹配流量:
[0048]
1档(软吹)<40nl/min对应渣液面微动钢水不裸露,
[0049]
2档(供电)100~200nl/min钢水裸露直径不大于200m,
[0050]
3档(调整成分)600~1000nl/min控制钢水裸露直径不大于600m。透气性差可使用旁通吹堵,待透气良好时恢复正常档位操作。
[0051]
(3)炉内微正压控制
[0052]
1)减少炉门开动次数与时长,且根据不同时段产生烟气量与浓度,及时调整侧吸的开度,在保证顶吸除尘效果烟气不外泄的前提下,把侧吸开度降至最低,保持炉内微正压的还原气氛。
[0053]
2)每次测温、取样前,先在炉门关闭搅拌后在进行测温取样后及时关闭炉门,有效
控制炉门开启时长。
[0054]
(4)定氧操作
[0055]
进站与软吹前进行定氧操作,定氧操作时定氧探头要插入钢液面内≥400mm,在进行定氧操作前关闭底吹渣面平静后在开始确保定氧成功率100%。
[0056]
(5)扩散脱氧
[0057]
1)随时观察烟尘颜色来判定脱氧程度,炉渣脱氧不良时,烟尘呈深黄、黄、浅黄。并且黄烟与白烟频繁转换时说明脱氧不完全。当烟尘颜色转变为灰白、白色、乳白色且持续保持说明炉渣脱氧相对完全,及时粘取渣样进行确认。
[0058]
2)根据脱氧实际情况,分批少量(扩散脱氧剂按照20~30kg/次加入,中前期使用sic达脱氧与发泡,后期不具备发泡条件后使用sife)均匀撒在渣面上,严禁投入钢水裸露面上,进行造白渣操作,保持终渣feo mno不大于1%,扩散脱氧剂加入时机与频次根据烟尘颜色变化与渣杆渣样颜色灵活调整。
[0059]
3)看渣判定脱氧效果技巧:
[0060]
碱性渣随着炉渣氧化性的高低呈现不同颜色,所以渣色是炉渣与钢液脱氧程度的标志,炉渣氧化性强,炉渣呈黑色,随着炉渣氧化性减弱即渣的还原,颜色也逐渐变浅黑色(feo mno>5%)——褐色(feo mno在2~5%)——黄色——黄白——乳白/白色(feo mno<1%)目标脱氧效果。
[0061]
(6)喂钙线操作(选用)
[0062]
1)钙处理主要目的是改善钢水流动性,起到夹杂物变性,促进夹杂物上浮的作用,但要注意ca/al太高,会造成滑动水口及滑板侵蚀严重,控制ca/als=0.11~0.15;
[0063]
2)喂线前温度、成分必须满足要求,并且白渣形成及脱氧良好的情况下进行;
[0064]
3)喂钙线先放下喂丝导管,采用软吹氩模式严禁钢液面裸露;
[0065]
4)喂钙线速度4.5~5m/s;
[0066]
5)在喂线时看到渣面上有白色ca火焰,说明喂丝速度太慢或喂线时没有小氩气流量搅拌;
[0067]
6)为更好的促进钢液中夹杂物上浮,钙处理后保证软吹15min下限不低于12min,软吹过程保持连续稳定,渣面微动严禁钢水面裸露。
[0068]
1.创新采用出钢完毕向钢包折铁进行增碳新工艺,完全替代原有出钢过程使用增碳剂增碳操作模式,确保成分均匀,有效避免增碳剂加入对成品碳偏析及钢中氮含量等控制影响、避免部分增碳剂进入钢种中使炉渣变稠,导致精炼造渣过程脱氧难以控制。
[0069]
2.出钢前利用tco投弹式副枪进行定氧,根据实际[o]含量按照动态调整钢芯铝加入量定量配加硅钡钙新沉淀脱氧性模式,按照此模式精炼进站[o]含量0.002
±
0.0005%确定精准脱氧效果,并杜绝钢中als大于0.005%时,有单独al2o3析出导致连铸可浇性差的瓶颈问题。
[0070]
3.根据45#钢脱氧合金化合金化夹杂物主要为mno-al2o3-sio2系夹杂物和cao-al2o3-sio2系夹杂物特点与使用性能需求,采用进站进站炉渣碱度2.0~1.7,软吹前炉渣碱度1.0~1.5,渣中al2o3≤12%的渣系,采用sic与sife进行扩散脱氧与炉渣改质,并采用轻ca变性处理工艺,12~15min有效软吹时间保证,确保钢中夹杂物处于低熔点区域、具有良好变形能力与塑性。
[0071]
本发明不局限于上述实施方式,任何人应得知在本发明的启示下作出的结构变化,凡是与本发明具有相同或相近的技术方案,均落入本发明的保护范围之内。
[0072]
本发明未详细描述的技术、形状、构造部分均为公知技术。
再多了解一些
本文用于创业者技术爱好者查询,仅供学习研究,如用于商业用途,请联系技术所有人。