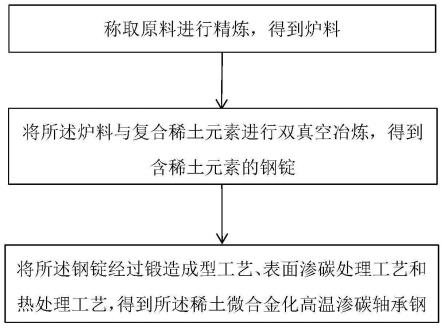
1.本发明属于高温渗碳轴承钢领域,尤其涉及一种稀土微合金化高温渗碳轴承钢及其制备方法。
背景技术:
2.轴承是装备制造业中重要的、关键的基础零部件,随着航空、航天、高铁等高端工业领域的迅速发展,对轴承的要求越来越高。用于制造轴承的钢称为轴承钢,轴承钢水平的高低直接决定了轴承的服役寿命。高碳铬轴承钢gcr15,其典型的化学成分(质量百分数,下同)为1%碳和1.5%铬,一部分碳固溶基体产生固溶强化,使钢具有较高的硬度,另一部分与铁和铬结合形成碳化物分布在基体上,满足轴承对耐磨性的需求。由于gcr15具有较高的硬度和耐磨性,并且价格便宜,自从20世纪初被发明至今,其一直占据了绝大部分的轴承领域。然而gcr15由于含碳量高,容易形成大尺寸碳化物,严重影响了钢的韧性,并且其只能在室温或低温(<150℃)下使用,因此限制了其使用范围。在某些高温服役环境下,如航空发动机,轴承需要保证具有较好的耐高温性能,因此借鉴高速工具钢得到了采用二次硬化设计8cr4mo4v(m50),其典型化学成分为0.8%碳、4%铬、4%钼和1%钒,该钢在高温回火后析出稳定的mo2c碳化物,从而满足350℃以下高温环境使用的要求。随着航空发动机轴承转速增加,dn值不断加大,除了需要轴承钢具有耐高温、高硬度、耐磨性、高抗疲劳性等性能,还要求其具备良好的耐冲击性能。因此,在8cr4mo4v的基础上,通过降碳增镍开发出了高温渗碳轴承钢g13cr4mo4ni4v(m50nil)。降低碳含量,可以提高钢的韧性;增加镍含量,可以降低表面吸收碳原子能力,加速碳原子在奥氏体中的扩散,有利于渗碳热处理,同时镍还可提高钢的韧性。
3.由于高温渗碳轴承钢性能不稳定,因此其至今还未被普遍应用。影响性能波动的根源在于钢的洁净度不高,即钢中存在较高的气体元素和杂质元素,进而影响钢中夹杂物尺寸、分布和形状等。随着冶炼工艺的不断发展,通过真空感应熔炼(vim)和真空电弧重熔(var)可以将高温渗碳轴承钢的气体元素和杂质元素含量控制在较低的水平,但是夹杂物形状仍是制约性能稳定性的瓶颈。通过在轴承钢加入微量稀土是一种变质夹杂物、改善性能有效的方法,但目前此方法多数用于高碳铬轴承钢中,在高温渗碳轴承钢鲜有报道。针对上述问题,本专利提出一种稀土微合金化高温渗碳轴承钢及其制备方法,达到提高钢洁净度和力学性能的目的。
技术实现要素:
4.为了克服上述现有技术存在的缺陷,本发明的目的在于提供一种洁净度高、表面硬度高、耐磨性好、芯部基体韧性好、耐高温、优良的抗疲劳性能的适用于高端关键轴承的采用稀土微合金化的高温渗碳轴承钢及其超纯净化制备方法。为实现上述目的,本发明提供如下技术方案:
5.一种稀土微合金化高温渗碳轴承钢的制备方法,所述方法包括如下步骤:
6.称取原料进行精炼,得到炉料;
7.将所述炉料与复合稀土元素进行双真空冶炼,得到含稀土元素的钢锭;
8.将所述钢锭经过锻造成型工艺、表面渗碳处理工艺和热处理工艺,得到所述稀土微合金化高温渗碳轴承钢。
9.具体地,所述炉料与复合稀土元素的各组分及其重量百分含量为:
10.碳含量为0.11-0.15wt%,铬含量为4.00-4.25wt%,钼含量为4.00-4.50wt%,钒含量为1.13-1.33wt%,镍含量为3.20-3.60wt%,锰含量为0.15-0.35wt%,硅含量为0.10-0.25wt%,复合稀土元素含量为0.05-0.2wt%,其余组分为铁;
11.具体地,所述复合稀土元素为铼-铈复合稀土元素。
12.进一步地,所述称取原料进行精炼,得到炉料的具体步骤为:
13.将碳、铬、钼、镍和铁按重量百分比称重,得到原料;
14.依次将钒、锰和硅加入到所述原料中进行精炼,得到炉料。
15.进一步地,所述将所述炉料与复合稀土元素进行双真空冶炼,得到含稀土元素的钢锭的具体步骤为:
16.在所述炉料出钢前5分钟加入铼-铈复合稀土元素,得到钢液;
17.将所述钢液采用双真空冶炼,得到含稀土元素的钢锭。
18.具体地,所述双真空冶炼包括真空感应熔炼和真空电弧重熔。
19.进一步地,所述热处理工艺的具体步骤包括:
20.冷处理步骤:将所述表面渗碳处理工艺后的试样进行淬火、保温,油冷至室温,再进行低温处理、保温,再恢复至室温;
21.回火步骤:将所述恢复至室温后的试样进行回火处理、保温,再空冷;
22.重复一次所述冷处理步骤和所述回火步骤,即得到所述稀土微合金化高温渗碳轴承钢。
23.具体地,所述冷处理步骤中,所述试样的淬火温度为1040-1080℃,保温时间为1小时。
24.具体地,所述冷处理步骤中,所述低温处理温度为-78℃,保温时间为2小时。
25.具体地,所述回火步骤中,所述回火温度为500-550℃,保温时间为2小时。
26.进一步地,所述稀土微合金化高温渗碳轴承钢在热处理工艺后,表面硬度≥57.3hrc,抗拉强度≥1300mpa,延伸率≥15%,芯部硬度≥42hrc,断裂韧性≥45mpa
·m1/2
,晶粒度≥5级。
27.一种稀土微合金化高温渗碳轴承钢,所述一种稀土微合金化高温渗碳轴承钢包含以下组分及重量百分含量:
28.碳含量为0.11-0.15wt%,铬含量为4.00-4.25wt%,钼含量为4.00-4.50wt%,钒含量为1.13-1.33wt%,镍含量为3.20-3.60wt%,锰含量为0.15-0.35wt%,硅含量为0.10-0.25wt%,复合稀土元素含量为0.05-0.2wt%,其余组分为铁。
29.本发明的技术效果和优点:
30.本发明采用一种稀土微合金化的适用于高端关键轴承的高温渗碳轴承钢具有优良强韧匹配性能和抗疲劳性能,这是由于稀土元素的加入降低了偏析、细化了晶粒、净化了晶界、使夹杂物变质。微量稀土的加入,提高了高温渗碳轴承钢的纯净度和均质性,不仅使
碳化物球化、细化、均匀分布,还使有害夹杂物变质为小尺寸近球状夹杂物,从而改善钢的力学性能、提高钢的抗疲劳性能。添加的微量稀土也有利于提高钢的抗氧化性能,而且有利于调整钢的热膨胀系数,改善了加工的高端关键轴承零件的尺寸稳定性和耐磨性。本发明高温渗碳轴承钢具有表面硬度高、芯部韧性好、抗疲劳性能优异,适用于航空航天等高端装备制造业中的高温、高转速、磨损等环境中,并且便于加工制造滚动轴承、滑动轴承、主轴等轴类零件。
31.本发明的其它特征和优点将在随后的说明书中阐述,并且,部分地从说明书中变得显而易见,或者通过实施本发明而了解。本发明的目的和其他优点可通过在说明书、权利要求书以及附图中所指出的结构来实现和获得。
附图说明
32.图1为本发明一种稀土微合金化高温渗碳轴承钢的制备方法流程图;
33.图2为本发明一种稀土微合金化高温渗碳轴承钢的双真空冶炼钢锭铸态组织;
34.图3为本发明一种稀土微合金化高温渗碳轴承钢均质化热处理后的显微组织。
具体实施方式
35.下面将结合本发明实施例中的附图,对本发明实施例中的技术方案进行清楚、完整地描述,显然,所描述的实施例仅仅是本发明一部分实施例,而不是全部的实施例。基于本发明中的实施例,本领域普通技术人员在没有做出创造性劳动前提下所获得的所有其他实施例,都属于本发明保护的范围。
36.为解决现有技术的不足,本发明公开了一种稀土微合金化高温渗碳轴承钢及其制备方法,具体为:
37.本发明的一种采用稀土微合金化的高端关键轴承的高温渗碳轴承钢的主要特点是高硬度和高韧性相结合,从而满足在高温高速环境下轴承服役的性能要求。而这个特点的关键技术在于化学成分的设计稀土元素净化钢的作用与热处理工艺的配合。本发明的一种采用稀土微合金化的适用于高端关键轴承的高温渗碳轴承钢为马氏体钢,形成马氏体组织的基本条件是在淬火温度时,必须形成奥氏体,为此钢中要含有一定量的奥氏体形成元素。本发明钢中是通过控制碳、镍、锰等元素来促成形成奥氏体的。
38.碳:碳是形成奥氏体的最强有效元素之一,同时也是提高硬度的有效元素,但要控制适当的含量,碳含量太高易生成过量的碳化物,对钢的韧性和疲劳性能产生不利影响;碳含量太低,钢的芯部硬度达不到要求。本发明轴承钢中碳的含量应控制在0.11-1.15wt%为宜。
39.镍:镍是形成奥氏体和稳定奥氏体的最佳元素,也是提高钢韧性的主要添加元素。镍降低钢中的位错阻力,提高钢的韧性;使“碳”曲线右移,提高钢的淬透性;降低钢的ms点(martensitefinish,指马氏体转变终了温度),增加钢中的残余奥氏体。但镍添加过多会促进钢中的有害元素偏聚,增加钢的回火脆性。另外镍资源短缺,价格较贵,应尽量节约使用。本发明轴承钢中控制镍的含量应控制在3.20-3.60wt%为宜。
40.锰:锰扩大奥氏体区的作用较大,且在奥氏体中无限固溶,所以在钢中加入一定量的锰时,可以使钢更易得到奥氏体。本发明轴承钢中锰的含量应控制在0.15-0.35wt%为
宜。
41.本发明轴承钢中还含有铬、钼等元素,这两种元素是铁素体形成元素。它和铁素体形成元素相结合,便于产生平衡组织。通过调节铁素体形成元素和奥氏体形成元素含量来控制轴承钢的组织和性能。
42.铬:铬能增加钢的淬透性并有二次硬化的作用,可提高碳钢的硬度和耐磨性而不使钢变脆,在马氏体钢中含量太高易出现铁素体,又降低马氏体转变点,使钢难以淬硬。本发明轴承钢中铬的含量应控制在4.00-4.25wt%为宜。
43.钼:钼能有效提高钢的淬透性,提高钢的抗回火性或回火稳定性,钼是较强的碳化物形成元素,与碳结合形成稳定的小尺寸碳化物,提高钢的硬度和保持一定的耐磨性。但过量的钼易出现铁素体和降低马氏体转变点,使钢难以淬硬。本发明轴承钢中钼的含量应控制在4.00-4.50wt%为宜。
44.微量稀土元素的加入可变质夹杂物和改善优化钢的组织及晶粒度,本发明轴承钢中稀土元素含量应控制在0.05-0.2wt%为宜。
45.一方面,本实施例一种稀土微合金化轴承钢的制备方法,所述制备方法如附图1所示,包括如下步骤:
46.称取原料进行精炼,得到炉料;
47.将所述炉料与复合稀土元素进行双真空冶炼,得到含稀土元素的钢锭;
48.将所述钢锭经过锻造成型工艺、表面渗碳处理工艺和热处理工艺,得到所述稀土微合金化高温渗碳轴承钢。
49.进一步地,所述炉料与复合稀土元素的各组分及其重量百分含量为:
50.碳含量为0.11-0.15wt%,铬含量为4.00-4.25wt%,钼含量为4.00-4.50wt%,钒含量为1.13-1.33wt%,镍含量为3.20-3.60wt%,锰含量为0.15-0.35wt%,硅含量为0.10-0.25wt%,复合稀土元素含量为0.05-0.2wt%,其余组分为铁。
51.进一步地,称取原料进行精炼,得到炉料,将所述炉料与稀土元素进行真空感应熔炼(vim)和真空电弧重熔(var)冶炼,得到含稀土元素的钢锭,具体步骤为:
52.按一定的重量百分含量称取上述含碳、铬、钼、镍和铁组分的炉料放入真空感应炉中,然后抽真空至5pa以下,预热15分钟后开始对真空感应炉加热使炉料熔化,炉料熔清后加入钒再继续精炼20分钟,然后充入氩气至13000pa后加入锰和硅精炼10分钟,最后加入铼-铈复合稀土元素之后5分钟出钢,即可得到真空感应铸锭。将真空感应铸锭去掉头尾、车光表面后进行真空电弧重熔(var)冶炼,控制熔化速度在1.2-2kg
·
min-1
,即可得到所述含稀土元素的钢锭,其双真空铸态组织图如附图2所示,发明钢采用双真空冶炼后,得到的钢锭组织致密,部分晶界上存在高温铁素体。
53.进一步地,将所述含稀土元素的钢锭进行均质化处理,其均质化处理后的显微组织图如附图3所示,发明钢经过高温均质化处理后,晶界上的高温铁素体被消除,对发明钢的综合力学性能的提升具有重要作用。
54.进一步地,将所述含稀土元素的钢锭均质化处理后经过锻造成型工艺、表面渗碳处理工艺和热处理工艺,具体步骤为:
55.将真空电弧重熔(var)得到的含稀土元素的钢锭进行锻造成型,将锻造成型的棒料采用真空渗碳炉进行真空低压脉冲渗碳,然后进行常规的热处理工艺。
56.具体地,整个渗碳工艺流程如下:
57.将零件表面清洗干净后装入真空渗碳炉中,抽真空后升温,然后通入渗碳气氛进行脉冲渗碳。真空炉中气压为400pa,渗碳剂为乙炔(c2h2),同时加入适当氮气(n2),并间歇式通入渗碳剂,渗碳及扩散温度为880-930℃,时间11-13h,油冷,渗碳后重复进行两次高温回火处理。
58.具体地,整个热处理工艺流程如下:
59.将经过表面渗碳处理工艺后的半成品钢进行淬火,淬火温度为1040-1080℃,保温时间为1小时,油冷至室温,然后进行-78℃的低温处理,保温时间为2h,恢复至室温后进行回火处理,回火温度选择500-550℃,回火时间为2h,再进行空冷。重复一次上述冷处理步骤和回火步骤,即可得到所述稀土微合金化高温渗碳轴承钢。
60.经过热处理工艺后的轴承钢,其表面硬度≥57.3hrc,芯部硬度≥42hrc,抗拉强度≥1300mpa,延伸率≥15%,断裂韧性≥45mpa
·m1/2
,晶粒度≥5级。
61.由本发明的一种采用稀土微合金化的适用于高端轴承的高温渗碳轴承钢按照不同的热处理工艺进行试验,所得结果列于表1。
62.表1热处理工艺过程及其硬度测试结果
[0063][0064]
如表1所示,本发明的一种采用稀土微合金化的适用于高端关键轴承的高温渗碳轴承钢经过热处理工艺后,其芯部硬度均大于42hrc。
[0065]
经上述热处理工艺以后,本发明轴承钢的芯部基体组织由马氏体,弥散分布在马氏体的细小碳化物和少量残余奥氏体组成。
[0066]
另一方面,本实施例一种稀土微合金化高温渗碳轴承钢,包含以下组分及重量百分含量:
[0067]
碳含量为0.11-0.15wt%,铬含量为4.00-4.25wt%,钼含量为4.00-4.50wt%,钒含量为1.13-1.33wt%,镍含量为3.20-3.60wt%,锰含量为0.15-0.35wt%,硅含量为0.10-0.25wt%,复合稀土元素含量为0.05-0.2wt%,其余组分为铁。
[0068]
具体地,所述复合稀土元素为铼-铈复合稀土元素。
[0069]
进一步地,将所述高温渗碳轴承钢采用4wt%硝酸酒精溶液腐蚀,其退火态组织为球状珠光体、铁素体和碳化物。退火态平均硬度为234hv。球状珠光体、铁素体和碳化物组织和234hv硬度使该钢种具有优良的机加工切削性能。
[0070]
本发明的一种采用稀土微合金化的适用于高端关键轴承的高温渗碳轴承钢采用二次硬化的合金化原理,通过添加合金元素和采用合适的热处理工艺实现固溶强化和析出强化。为了达到强度、硬度等性能的要求,通过热处理工艺将钢加热至奥氏体化温度后,采取油冷的冷却方式使其完全转变成马氏体组织,采取冷处理使钢中的奥氏体进一步转变为马氏体,然后经过合适的回火调控钢中碳化物分布和残余奥氏体形态。本发明的核心在于创造性采用真空感应熔炼(vim)和真空电弧重熔(var)冶炼方法,通过添加微量稀土元素提高高温渗碳轴承钢的冶金质量,然后通过通用热处理工艺,调控钢的组织平衡,最终满足适用于高端关键轴承用钢的应用要求。真空感应熔炼(vim)和真空电弧重熔(var)冶炼极大提高钢液纯净度,而高纯度稀土的加入,使钢液有更好的除氢、氧作用,有利于提高钢的洁净度。微量稀土的加入还能控制钢中碳化物分布形态而使钢达到最佳性能。稀土分布在马氏体中形成过饱和固溶体,通过控制过饱和固溶体晶格畸变程度和马氏体组织的分散性,使马氏体轴承钢基体获得较高的硬度。这就是本发明通过创造性添加稀土来提高钢的洁净度,实现固溶强化、析出强化的目的,而非通常意义的优化组织和改善晶粒度。
[0071]
最后应说明的是:以上所述仅为本发明的优选实施例而已,并不用于限制本发明,尽管参照前述实施例对本发明进行了详细的说明,对于本领域的技术人员来说,其依然可以对前述各实施例所记载的技术方案进行修改,或者对其中部分技术特征进行等同替换,凡在本发明的精神和原则之内,所作的任何修改、等同替换、改进等,均应包含在本发明的保护范围之内。
再多了解一些
本文用于创业者技术爱好者查询,仅供学习研究,如用于商业用途,请联系技术所有人。