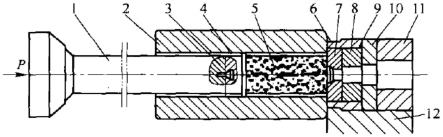
一种t型型材加工方法
技术领域
1.本发明属于铝型材加工技术领域,尤其是一种t型型材加工方法。
背景技术:
2.铝型材采用铝合金为原料,经过模具挤出成型,其具有重量轻的优点,而且在空气、水以及很多化学体系中均具有优良的抗腐蚀性,又因为铝型材优良的可加工性、可成型性等特点,其被广泛的应用在多个领域中。铝型材中的t型型材是一种常用的结构,可用于吊顶龙骨、收边、收口、压条、压缝、导轨等处,传统型材生产多采用符合国标要求的铸锭、普通模具和常规的生产工艺,普通模具为平面模具,使用时通过模具工作带尺寸控制流速,修模难度大,常规的生产工艺包括非恒速等温挤压、热处理单级淬火等一般工艺。现有技术会造成产品组织不均匀,产生粗大晶粒,最终导致性能不均且较低;在挤压过程中变形、扭拧严重,后期无法实现高精度尺寸控制。
技术实现要素:
3.本发明的目的在于克服现有技术的不足之处,提供一种t型型材加工方法。该方法中,使用模具进行挤压、结合水冷淬火、冷加工、深冷处理后,得到质量良好、尺寸稳定、力学性能高且组织均匀的成品。
4.本发明解决技术问题所采用的技术方案是:
5.一种t型型材加工方法,其特征在于:包括以下步骤:
6.⑴
在挤压筒内安装模具;
7.⑵
对模具和铸锭加热;
8.⑶
挤压铸锭,模具孔中挤出型材;
9.⑷
对步骤
⑶
的型材进行淬火和冷加工后得到成品。
10.进一步的:在模具本体上径向均布设置四个t字型挤出孔,每个t字型挤出孔的模具本体端面上设置有导流坑。
11.进一步的:步骤
⑵
所述的模具加热的步骤是:将挤压模具和挤压筒预热至400-440℃;升温速率80-200℃/h。
12.进一步的:步骤
⑵
所述的铸锭加热步骤是:将铸锭梯度加热至400-440℃,控制铸锭头尾温差≤30℃;升温速率30-50℃/min。
13.进一步的:步骤
⑶
所述的挤出型材的速度为0.1-0.5mm/s。
14.进一步的:步骤
⑷
所述的淬火过程是:型材挤出后升温至488-492℃,保温30min;继续升温至495-499℃,保温10min;使用温水进行淬火。
15.进一步的:步骤
⑷
所述的冷加工的过程是:
16.拉伸型材,采用1.0-3.0%的永久塑性变形率。
17.进一步的:拉伸速度为5-10mm/s,型材装夹时保证型材平面部分对正;拉伸时调整扭拧头,消除型材在挤压时产生的应力和扭拧变形。
18.进一步的:拉伸的拉力取值范围是:拉力大于材料的屈服强度与材料横截面面积的乘积且拉力小于材料的抗拉强度与材料横截面积的乘积。
19.进一步的:冷加工后对型材进行深冷处理,过程是:将冷加工后的型材放入液氮中一段时间。
20.本发明取得的技术效果是:
21.本发明中,在模具本体的径向方向均布设置四个挤出孔,每个挤出孔所在的模具本体端面上设置有导流坑,利用导流坑实现挤压过程中金属流速控制,保证制品组织和外形尺寸;通过铸锭加热温度、工模具加热温度、挤压速度等配合控制,实现恒温等速挤压,保证制品组织均匀;挤出后淬火采用双级保温制度,高温的升温温度更接近过烧温度,能获得更高过饱和度,使固溶更充分,温水淬火可有效防止淬火变形;冷加工产生塑形变形,提高内部位错密度,消除前期产生的应力和扭拧变形;深冷处理提高去应力效果及提高抗晶间腐蚀能力,晶间腐蚀深度能降低30%。
附图说明
22.图1是本发明的模具装配图;
23.图2是导流坑的示意图;
24.图3是晶间腐蚀深度对比图。
具体实施方式
25.下面通过具体实施例对本发明作进一步详述,以下实施例只是描述性的,不是限定性的,不能以此限定本发明的保护范围。
26.一种t型型材加工方法,如图所示,本发明的创新在于:
27.挤压筒和模具如图1所示:
28.挤压筒内套2内部设置挤压轴1,挤压轴前部通过连接销3设置挤压垫片4,挤压垫片将加热后的铸锭5向挤压模具7方向挤压。挤压模具和模垫8设置在模套6内,在模套前部通过定位销9设置前环10和后环11。
29.加工方法包括以下步骤:
30.⑴
在挤压筒内安装模具;
31.⑵
对模具和铸锭加热;
32.⑶
挤压铸锭,模具孔中挤出型材;
33.⑷
对步骤
⑶
的型材进行淬火和冷加工后得到成品。
34.步骤
⑴
所述的模具结构是:在模具本体上径向均布设置四个t字型挤出孔15,t字型挤出孔上设置有直径1.50毫米的工艺孔14。每个t字型挤出孔的模具本体端面上设置有导流坑13。导流坑的宽度为型材厚度加10到15mm,深15mm,入口锥角3-10
°
(不同角度控制流速);模具工作带有效尺寸3-5mm(不同尺寸控制流速),挤出孔尺寸收缩率0.6-1.5%(收缩率即挤出孔尺寸在制品尺寸基础上增加的比率。不同合金和规格采用收缩率不同,发明中型材厚度部分为0.7%,外形部分为1.2%。)。
35.①
对模具进行预热加热,将模具和挤压筒加热至400-440℃;升温速率80-200℃/h。
36.②
对铸锭进行梯度加热;将铸锭梯度加热至400-440℃,控制铸锭头尾温差≤30℃;升温速率30-50℃/min。
37.③
将预热后的铸锭装入挤压筒中进行挤压,挤压轴通过挤压垫推动铸锭向前运动完成镦粗,继续向前运动,将铸锭从四个挤出孔中挤出,挤压速度为0.1-0.5mm/s,得到四支t字型铝合金型材。
38.在模具本体上开设导流坑,可以实现挤压过程中金属流速控制,同时制品前端与上一根制品尾端连接。前端与尾端连接是:前一根挤压完成后,切掉压余,导流坑中余有金属。接着挤压下一根时,新的金属会与导流坑中的金属混合焊接,从而实现两根相连制品的首尾相接。由于制品首尾相接,前一根制品的重量会限制后一根制品头端的自由活动,包括扭拧、弯曲等,从而提高制品的外形尺寸,减少制品前端扭拧变形,提高成品率和制品组织均匀性。
39.步骤
⑷
所述的淬火过程是:型材挤出后匀速升温20min,升温至488-492℃,保温30min;继续匀速升温5min,升温至495-499℃,保温10min;使用温水(30-38℃)进行淬火。型材挤出后的升温温度更接近过烧温度,能获得更高过饱和度,使固溶更充分,温水淬火可有效防止淬火变形。
40.步骤
⑷
所述的冷加工的过程是:
41.通过对制品施加拉力,拉力大于(材料的屈服强度)r
p0.2
×
(横截面面积)f且拉力小于(材料的抗拉强度)rm×
(横截面面积)f。
42.拉伸变形超过金属的屈服极限,拉伸变形超过金属的屈服极限:一般规定为发生0.2%永久变形,拉力超过(材料的屈服强度)r
p0.2
×
(横截面面积)f,并达到1.0-3.0%的永久塑性变形程度,使各条纵向纤维的弹复能力趋于一致,在弹复后各处的残余弯曲量不超过允许值(允许值一般分为普通级、高精级和超高精级,每个级别所要求的弯曲度又与制品的外接圆直径和型材最小壁厚有关)。
43.采用2.2-2.4%的永久塑性变形率,控制拉伸的平衡移动、保持拉伸速度为5-10mm/s的慢速拉伸,装夹料时保证型材平面部分对正,拉伸时观察型材扭拧变化并旋转调节扭拧头,消除型材在挤压和淬火时产生的应力和扭拧变形,显著提升晶间腐蚀性能,根据型材的扭拧程度确定旋转的量,每根型材的扭拧程度不同,所以旋转的量也不一样。冷加工产生塑形变形,提高内部位错密度,消除前期产生的应力和扭拧变形。
44.冷加工后对型材进行深冷处理,过程是:将冷加工后的型材放入﹣150~﹣180℃液氮中,保温30min。深冷处理后材料的内部应力可以得到显著改善,其去应力效果和提高抗晶间腐蚀能力明显,如图3所示,本发明(图3a)晶间腐蚀深度最大0.097mm,比技术要求值0.150mm (图3b)降低30%以上。
45.制得的成品进行综合力学性能检测,表1为本发明产品与标准比较,表2为本发明产品与其他产品比较。抗拉强度rm,屈服强度r
p0.2
,断后伸长率a。
46.对照标准:性能指标r
p0.2
/mparm/mpaa/%gjb 2507a-2015≥290≥395≥10本发明36647213
47.表1:本发明与标准比较
48.从表1可知,本发明与国军标相比抗拉强度提高19%,规定非比例延伸长度提高
26%,延伸率提高30%。
[0049][0050]
表2:本发明与其他产品比较。
再多了解一些
本文用于创业者技术爱好者查询,仅供学习研究,如用于商业用途,请联系技术所有人。