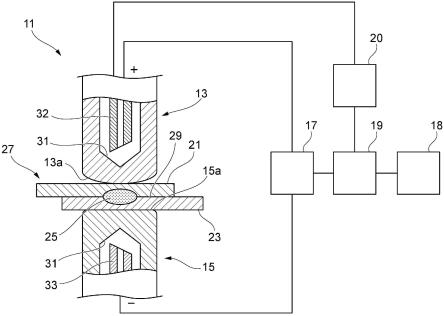
1.本发明涉及点焊方法。
背景技术:
2.铝材具有机械强度,且轻量,因此被应用为机动车的门等各种结构体的部件。该铝材存在轧制板、挤压材料或者锻造材料等延展材料、铝铸件等,根据所要求的刚性或强度以适当分开使用的方式用于结构体的各部位。
3.在组装由铝材构成的结构体时,需要将这些由铝材构成的构件彼此接合,作为能够最廉价地接合的方法,广泛采用点焊。
4.该点焊用于将由延展材料构成的铝材彼此接合,例如,由延展材料构成的铝材与由铸件构成的铝材的接合一般通过使用螺栓等的机械紧固连结方法而进行。
5.若能够通过点焊将由延展材料构成的铝材与由铸件构成的铝材接合,则能够实现结构体的紧凑化、轻量化、成本降低。然而,由延展材料构成的铝材与由铸件构成的铝材的电阻值以及熔点较大不同,因此在点焊时形成的焊核形成于相对于构件的重叠面偏向的位置,并有可能在焊核还未充分发展时产生飞溅。
6.在专利文献1中,示出了使相对于被接合的构件上下配置的电极的一方的接触面积比另一方的接触面积大,而修正在点焊时形成的焊核的偏向。另外,在专利文献2中,公开了在铝材的接合中,使正极侧的电极的面积比负极侧的电极大,从而提高点焊的焊接点数的方法。
7.现有技术文献
8.专利文献
9.专利文献1:日本国特开2017-177112号公报
10.专利文献2:日本国特开平5-50260号公报
技术实现要素:
11.发明要解决的课题
12.然而,专利文献1所记载的技术例如在对不同的板厚的板材进行点焊时,以使其焊核达到各个板材的对合面的方式修正焊核的形成位置,并不抑制对延展材料的铝材与铸件的铝材进行了点焊时的焊核的偏向与飞溅的产生。
13.另外,对延展材料的铝材与铸件的铝材进行了点焊时的焊核的偏向与飞溅的产生也难以通过延长电极的寿命而提高点焊的焊接点数的专利文献2所述的技术来抑制。
14.本发明解决了上述的问题,并提供能够抑制飞溅的产生并且将适度的大小的焊核形成于适当的位置的点焊方法。
15.用于解决课题的方案
16.本发明由下述结构构成。
17.(1)一种点焊方法,其中,
18.所述点焊方法包括:
19.重叠工序,在所述重叠工序中,将铝延展材料与铝铸件材料重叠;
20.配置工序,在所述配置工序中,将重叠了的所述铝延展材料以及所述铝铸件材料插入配置于对置位置的第一电极与第二电极之间,在所述铝延展材料侧配置第一电极并且在所述铝铸件材料侧配置所述第二电极;以及
21.通电工序,在所述通电工序中,一边利用所述第一电极与所述第二电极将重叠了的所述铝延展材料以及所述铝铸件材料夹入而进行加压,一边向所述第一电极与所述第二电极之间通电,
22.在所述通电工序中,使所述第二电极相对于所述铝铸件材料的接触面积比所述第一电极相对于所述铝延展材料的接触面积大。
23.(2)一种点焊方法,其中,
24.所述点焊方法包括:
25.重叠工序,在所述重叠工序中,将铝延展材料与铝铸件材料重叠;
26.配置工序,在所述配置工序中,将重叠了的所述铝延展材料以及所述铝铸件材料插入配置于对置位置的第一电极与第二电极之间,在所述铝延展材料侧配置第一电极并且在所述铝铸件材料侧配置所述第二电极;以及
27.通电工序,在所述通电工序中,一边利用所述第一电极与所述第二电极将重叠了的所述铝延展材料以及所述铝铸件材料夹入而进行加压,一边向所述第一电极与所述第二电极之间通电,
28.在所述通电工序中,将电极加压力设为7.0kn以上且10kn以下。
29.发明效果
30.根据本发明,能够抑制飞溅的产生并且将适度的大小的焊核形成于适当的位置。
附图说明
31.图1是点焊机的概要结构图。
32.图2a是将用作铝铸件材料的压力铸造材料成形的模具的剖视图。
33.图2b是压力铸造材料的立体图。
34.图3是示出点焊方法中的重叠工序以及配置工序的示意图。
35.图4是示出焊接电流以及加压力的赋予的定时的时序图。
36.图5是示出通过点焊方法的通电工序而形成的焊核的形成状态的示意图。
37.图6是示出参考例的通过点焊方法的通电工序而形成的焊核的形成状态的示意图。
38.图7是示出变形例1的通过点焊方法的通电工序而形成的焊核的形成状态的示意图。
39.图8是示出变形例2的通过点焊方法的通电工序而形成的焊核的形成状态的示意图。
40.图9a是示出试验例1中的焊核的熔入量的图表。
41.图9b是示出试验例1中的焊接耳垂(weld lobe)的图表。
42.图10a是示出试验例2中的焊核的熔入量的图表。
43.图10b是示出试验例2中的焊接耳垂的图表。
44.图11a是示出试验例3中的焊核的熔入量的图表。
45.图11b是示出试验例3中的焊接耳垂的图表。
46.图12a是示出试验例4中的焊核的熔入量的图表。
47.图12b是示出试验例4中的焊接耳垂的图表。
48.图13a是示出以焊接电流25ka进行了焊接时的焊核的状态的试验例1中的截面图像。
49.图13b是示出以焊接电流25ka进行了焊接时的焊核的状态的试验例2中的截面图像。
50.图13c是示出以焊接电流25ka进行了焊接时的焊核的状态的试验例3中的截面图像。
51.图13d是示出以焊接电流25ka进行了焊接时的焊核的状态的试验例4中的截面图像。
52.图14a是示出以焊接电流35ka进行了焊接时的焊核的状态的试验例1中的截面图像。
53.图14b是示出以焊接电流35ka进行了焊接时的焊核的状态的试验例3中的截面图像。
54.图15是示出试验例5中的基于电极加压力的焊接推荐范围的变化的图表。
55.图16是示出试验例6中的焊接电流与通电时间的关系的图表。
56.图17是示出试验例7中的焊接电流与通电时间的关系的图表。
57.图18是示出试验例8中的基于电极加压力的焊接推荐范围的变化的图表。
58.图19是示出试验例9中的焊接电流与通电时间的关系的图表。
59.图20是示出试验例10中的焊接电流与通电时间的关系的图表。
60.图21是示出将试验例11的电极加压力设为7kn的情况下的焊核直径相对于焊接电流的分布的图表。
61.图22是示出试验例12中的基于电极加压力的焊接推荐范围的变化的图表。
62.图23是用于说明压痕的深度的定义的截面照片。
63.图24是示出求出焊核直径为5√t时的压痕深度的结果的图表。
具体实施方式
64.以下,参照附图对本发明的实施方式详细进行说明。
65.<点焊机>
66.图1是示出对铝材进行焊接的点焊机的主要部分的概要结构图。
67.如图1所示那样,点焊机11具备:第一电极13及第二电极15;焊接变压器部17,其与第一电极13及第二电极15连接;电源部18;控制部19,其向焊接变压器部17供给来自电源部18的焊接电力;以及电极驱动部20,其使第一电极13及第二电极15沿轴向移动。控制部19统一控制电流值、通电时间、电极的加压力、通电定时、加压定时。
68.第一电极13是具有由曲面构成的前端面13a的半径形(r形)或圆顶半径形(dr形)的电极。与此相对,第二电极15是具有由平面构成的前端面15a的平面形(f形)的电极。第一
电极13以及第二电极15分别将前端面13a、15a设为平滑面。焊接变压器部17将第一电极13作为正极,将第二电极15作为负极,而在第一电极13与第二电极15之间通电。
69.这些第一电极13以及第二电极15在各自的内部具备冷却部。冷却部的冷却方式没有特别限定,但在图示例的结构中,在分别形成于第一电极13以及第二电极15的凹部31配置有冷却用管32、33,通过从冷却用管32、33供给水等冷却介质,从而冷却第一电极13以及第二电极15。
70.点焊机11在第一电极13与第二电极15之间重叠而夹入铝延展材料21与铝铸件材料23。此时,将重叠了的铝延展材料21以及铝铸件材料23以在铝延展材料21侧配置第一电极13、并在铝铸件材料23侧配置第二电极15的方式夹入第一电极13与第二电极15之间。
71.并且,通过由电极驱动部20进行的第一电极13以及第二电极15的驱动,而对铝延展材料21与铝铸件材料23在板厚方向上加压。在该加压状态下,基于来自控制部19的指令,焊接变压器部17在第一电极13与第二电极15之间通电。由此,在被正极的第一电极13与负极的第二电极15夹着的铝延展材料21与铝铸件材料23的边界部29形成焊核(点焊部)25,得到铝延展材料21与铝铸件材料23一体化了的铝焊接接头(接合体)27。
72.<铝延展材料>
73.作为铝延展材料21,例如使用2000系、3000系、5000系、6000系、7000系的铝合金、或由1000系的纯铝构成的轧制材料、挤压材料或者锻造材料。
74.<铝铸件材料>
75.作为铝铸件材料23,例如使用由ac4c、ac4ch、ac2b(jis h 5202)、或adc12(jis h 5302)等构成的板状的压力铸造材料或铸造材料。
76.图2a是将用作铝铸件材料的压力铸造材料成形的模具的剖视图,图2b是压力铸造材料的立体图。
77.板状的铝铸件材料23如图2a所示那样例如使用具备薄壁腔室51的压力铸造模具53而制作。该压力铸造模具53例如将薄壁腔室51的间隙设为2mm,并具有与薄壁腔室51相连的浇口55以及溢流浇口57。在该压力铸造模具53中,从浇口55向薄壁腔室51加压注入铝熔液59,并从在薄壁腔室51中的液流动方向fl的延长线上设置的溢流浇口57排出。
78.如图2a所示那样,由具有薄壁腔室51的压力铸造模具53成形的压力铸造材料61在形成于浇口55的部分的浇口部63与形成于溢流浇口57的部分的溢流部65之间具有利用薄壁腔室51形成的薄壁部67。在本例中,作为铝铸件材料23,使用压力铸造材料61的薄壁部67中的除浇口部63以及溢流部65的附近以外的部分。通过利用加压注入的铝熔液59朝向溢流浇口57流动的主流成形薄壁部67,从而即使产生气泡也被向溢流部65挤压并排除。由此,在压力铸造材料61的薄壁部67中,气孔的产生被充分抑制,能够良好地实施点焊。因此,通过使用压力铸造材料61的薄壁部67作为铝铸件材料23,能够良好地进行点焊。
79.<点焊方法>
80.接着,对利用点焊机11将铝延展材料21与铝铸件材料23点焊而接合的情况进行说明。需要说明的是,本发明的点焊方法并不限定于以下的方案。
81.图3是示出点焊方法中的重叠工序以及配置工序的示意图。图4是示出焊接电流以及加压力的赋予的定时的时序图。图5是示出通过点焊方法的通电工序而形成的焊核的形成状态的示意图。
82.(重叠工序、配置工序)
83.如图3所示那样,将铝延展材料21与铝铸件材料23重叠,并将该重叠了的铝延展材料21以及铝铸件材料23插入第一电极13与第二电极15之间。由此,相对于重叠了的铝延展材料21以及铝铸件材料23,在铝延展材料21侧配置正极的第一电极13并且在铝铸件材料23侧配置负极的第二电极15。
84.(通电工序)
85.一边将重叠了的铝延展材料21以及铝铸件材料23用第一电极13和第二电极15夹入而进行加压,一边利用焊接变压器部17向由正极构成的第一电极13与由负极构成的第二电极15之间通电焊接电流。
86.需要说明的是,作为通电工序中的通电的方法,例如如图4所示那样,利用控制部19,在从由第一电极13与第二电极15进行的加压开始到加压结束的加压时间tp的期间向第一电极13与第二电极15之间通电焊接电流iw。向该第一电极13与第二电极15之间通电的焊接电流iw设为单一的脉冲电流。焊接电流iw在从由第一电极13与第二电极15进行的加压开始起时间ta后开始通电,并在时间ti的期间维持通电。并且,由第一电极13与第二电极15进行的加压在焊接电流iw的通电结束后的时间tb后停止。
87.在此,第一电极13为具有由曲面构成的前端面13a的r形或dr形的电极,第二电极15为具有由平面构成的前端面15a的f形的电极。因此,第二电极15相对于铝铸件材料23的接触面积比第一电极13相对于铝延展材料21的接触面积大。即,在使第二电极15相对于铝铸件材料23的接触面积比第一电极13相对于铝延展材料21的接触面积大的状态下,向第一电极13与第二电极15之间通电。
88.若像这样向第一电极13与第二电极15之间通电,则如图5所示那样,在铝延展材料21以及铝铸件材料23的边界部29开始熔融,形成分别熔入铝延展材料21以及铝铸件材料23的焊核25。
89.并且,通过上述的工序,得到铝延展材料21与铝铸件材料23通过点焊而一体化了的铝焊接接头27。
90.<参考例>
91.在此,对参考例进行说明。
92.图6是示出参考例的通过点焊方法的通电工序而形成的焊核的形成状态的示意图。
93.如图6所示那样,在参考例中,例如,作为第一电极以及第二电极,使用具有由相同曲率半径的曲面构成的相同形状的前端面103a、105a的r形或dr形的第一电极103以及第二电极105对铝延展材料21与铝铸件材料23进行点焊。
94.在该参考例中,第一电极103以及第二电极105的前端面103a、105a的形状相同,因此第二电极105相对于铝铸件材料23的接触面积与第一电极103相对于铝延展材料21的接触面积相同。即,在参考例中,在使第二电极105相对于铝铸件材料23的接触面积与第一电极103相对于铝延展材料21的接触面积相同的状态下向第一电极103与第二电极105之间通电。
95.在此,铝铸件材料23与铝延展材料21相比电阻较高,因此在点焊时与铝延展材料21相比容易发热。并且,铝铸件材料23与铝延展材料21的熔点较大不同。
96.因此,若如参考例那样,使第二电极105相对于铝铸件材料23的接触面积与第一电极103相对于铝延展材料21的接触面积相同的状态下向第一电极103与第二电极105之间通电,焊核25形成于与铝延展材料21以及铝铸件材料23的边界部29相比偏向铝铸件材料23侧的位置。这样,有时焊核25相对于铝延展材料21以及铝铸件材料23的熔入深度产生偏向。另外,有可能在铝延展材料21与铝铸件材料23的接合部位产生飞溅,并导致接合强度以及焊接品质的降低。
97.与此相对,根据本实施方式的点焊方法,在通电工序中,使第二电极15相对于铝铸件材料23的接触面积比第一电极13相对于铝延展材料21的接触面积大。由此,在通电工序中,降低与铝延展材料21相比容易发热的铝铸件材料23的电流密度,能够抑制发热集中在铝铸件材料23侧的情况。即,能够取得电阻值以及熔点较大不同的铝延展材料21以及铝铸件材料23的焊接时的电阻发热的平衡,能够抑制飞溅的产生并且能够在适当的位置无偏向地形成焊核25。
98.因此,能够通过点焊将铝延展材料21与铝铸件材料23以较高的焊接品质接合,能够实现由铝材构成的结构体的紧凑化、轻量化以及成本降低。
99.尤其是,通过使用具有由曲面构成的前端面13a的电极来作为第一电极13,并使用具有由平面构成的前端面15a的电极来作为第二电极15,能够容易使第二电极15相对于铝铸件材料23的接触面积比第一电极13相对于铝延展材料21的接触面积大。
100.另外,在通电工序中,将第一电极13作为正极并且将第二电极15作为负极,而向重叠了的铝延展材料21以及铝铸件材料23通电。由此,能够通过所谓的极性效应,而使与作为正极的第一电极13相接的铝延展材料21侧的发热比与作为负极的第二电极15相接的铝铸件材料23侧的发热大。因此,能够进一步良好地取得铝延展材料21以及铝铸件材料23的焊接时的电阻发热的平衡。
101.接着,对变形例进行说明。
102.(变形例1)
103.图7是示出变形例1的通过点焊方法的通电工序而形成的焊核的形成状态的示意图。
104.如图7所示那样,在变形例1中,使用具有由曲面构成的前端面13a的电极来作为第一电极13,使用具有由比第一电极13的前端面13a大的曲率半径的曲面构成的前端面15a的电极来作为第二电极15。
105.在该变形例1中,相对于第一电极13的前端面13a的曲率半径,第二电极15的前端面15a的曲率半径较大。因此,在利用这些第一电极13与第二电极15将重叠了的铝延展材料21与铝铸件材料23夹入了时,第二电极15相对于铝铸件材料23的接触面积比第一电极13相对于铝延展材料21的接触面积大。
106.因此,在变形例1中,也降低与铝延展材料21相比容易发热的铝铸件材料23的电流密度,也能够抑制发热集中在铝铸件材料23侧的情况。由此,能够取得铝延展材料21以及铝铸件材料23的焊接时的电阻发热的平衡,能够抑制飞溅的产生并且在适当的位置无偏向地形成焊核25。
107.(变形例2)
108.图8是示出变形例2的通过点焊方法的通电工序而形成的焊核的形成状态的示意
图。
109.如图8所示那样,在变形例2中,例如,使用具有由相同曲率半径的曲面构成的前端面13a、15a的电极来作为第一电极13以及第二电极15,对铝延展材料21与铝铸件材料23进行点焊。另外,使用前端面15a被粗糙面化了的电极来作为第二电极15。为了将前端面15a粗糙面化,例如,通过带式砂光机等研磨机对第二电极15的前端面15a实施研磨处理。
110.在该变形例2中,第二电极15的前端面15a被粗糙面化。因此,在利用这些第一电极13与第二电极15将重叠了的铝延展材料21与铝铸件材料23夹入了时,第二电极15相对于铝铸件材料23的接触面积比第一电极13相对于铝延展材料21的接触面积大。
111.因此,在变形例2中,也降低与铝延展材料21相比容易发热的铝铸件材料23的电流密度,也能够抑制发热集中在铝铸件材料23侧的情况。由此,能够取得铝延展材料21以及铝铸件材料23的焊接时的电阻发热的平衡,能够抑制飞溅的产生并且在适当的位置无偏向地形成焊核25。
112.需要说明的是,作为将第二电极15的前端面15a粗糙面化的方法,并不限于利用研磨机的研磨处理,也可以实施喷砂处理或蚀刻处理等各种表面处理、或切削加工处理。
113.<其他点焊方法>
114.作为本发明的点焊方法,也可以使电极加压力增加。在该情况下,在通电时形成于铝延展材料21与铝铸件材料23的界面的熔融金属通过由电极进行的加压而被封入电极间的区域内。由此,能够防止熔融金属的飞散(飞溅),得到必要且充分的尺寸的焊核,而能够稳定地维持较高的接合强度。
115.通过电极加压力设为7kn以上且10kn以下,从而形成适当的焊核。若将电极加压力设为10kn以下,则形成于铝延展材料21以及铝铸件材料23的压痕深度在将板厚设为t(mm)的情况下,被抑制为0.1t以下,优选被抑制为0.09t以下。
116.实施例
117.[a]变更电极的接触面积
[0118]
使用相互配置于对置位置的各种第一电极以及第二电极,对相互重叠了的相同尺寸的铝延展材料与铝铸件材料进行点焊,求出焊核向铝延展材料以及铝铸件材料的熔入深度以及通电时间与焊接电流的关系即焊接耳垂,并且观察焊核部分的截面状态。
[0119]
<试验片>
[0120]
(铝延展材料)
[0121]
材质:6k21-t4(6000系铝合金的延展材料)
[0122]
形状:宽度40mm、长度100mm的板状
[0123]
厚度:2mm
[0124]
(铝铸件材料)
[0125]
材质:adc12(由铝合金构成的压力铸造材料)
[0126]
形状:宽度40mm、长度100mm的板状
[0127]
厚度:2mm
[0128]
<试验条件>
[0129]
(1)焊接条件
[0130]
电极加压力:5.0kn
[0131]
焊接电流:20ka、25ka、30ka、33ka、35ka、37ka
[0132]
(2)焊接方法
[0133]
将第一电极作为正极,将第二电极作为负极,使重叠了的铝延展材料与铝铸件材料夹入第一电极与第二电极之间,在铝延展材料侧配置作为正极的第一电极并且在铝铸件材料侧配置作为负极的第二电极。
[0134]
利用第一电极与第二电极对铝延展材料以及铝铸件材料进行加压,在从加压开始起100ms后以通电时间200ms通电焊接电流,在电流通电结束后使加压保持200ms而结束加压。
[0135]
<使用电极>
[0136]
(试验例1)
[0137]
1)第一电极(正极侧电极)
[0138]
类别:半径形(r形)电极
[0139]
电极前端直径:19mm
[0140]
前端曲率半径:100mm
[0141]
前端面:平滑面
[0142]
2)第二电极(负极侧电极)
[0143]
类别:平面形(f形)电极
[0144]
电极前端直径:19mm
[0145]
前端面:平滑面
[0146]
(试验例2)
[0147]
1)第一电极(正极侧电极)
[0148]
类别:圆顶半径形(dr形)电极
[0149]
电极前端直径:8mm
[0150]
前端曲率半径:40mm
[0151]
前端面:平滑面
[0152]
2)第二电极(负极侧电极)
[0153]
类别:半径形(r形)电极
[0154]
电极前端直径:19mm
[0155]
前端曲率半径:100mm
[0156]
前端面:平滑面
[0157]
(试验例3)
[0158]
1)第一电极(正极侧电极)
[0159]
类别:半径形(r形)电极
[0160]
电极前端直径:19mm
[0161]
前端曲率半径:100mm
[0162]
前端面:平滑面
[0163]
2)第二电极(负极侧电极)
[0164]
类别:半径形(r形)电极
[0165]
电极前端直径:19mm
[0166]
前端曲率半径:100mm
[0167]
前端面:利用具备粒度z60的氧化锆磨石的带式砂光机进行研磨而粗糙面化。
[0168]
(试验例4)
[0169]
1)第一电极(正极侧电极)
[0170]
类别:半径形(r形)电极
[0171]
电极前端直径:19mm
[0172]
前端曲率半径:100mm
[0173]
前端面:平滑面
[0174]
2)第二电极(负极侧电极)
[0175]
类别:半径形(r形)电极
[0176]
电极前端直径:19mm
[0177]
前端曲率半径:100mm
[0178]
前端面:平滑面
[0179]
<试验结果>
[0180]
(1)熔入深度
[0181]
在图9a、图10a、图11a以及图12a中,示出试验例1~3以及试验例4中的焊核的熔入深度的试验结果。需要说明的是,在各图中,各曲线图表示n=3的平均值以及标准偏差的值。另外,箭头ha表示焊核向铝延展材料侧的熔入方向,箭头hb表示焊核向铝铸件材料侧的熔入方向。
[0182]
(试验例1)
[0183]
如图9a所示那样,在试验例1中,在将焊接电流设为20ka时,焊核偏向铝铸件材料侧一些而形成,但在将焊接电流设为25ka、30ka、33ka、35ka、37ka时,能够形成平衡良好地熔入到铝延展材料侧以及铝铸件材料侧这两方的焊核。
[0184]
(试验例2)
[0185]
如图10a所示那样,在试验例2中,在将焊接电流设为20ka时,焊核向铝铸件材料侧较多地熔入,但在将焊接电流设为25ka、30ka、33ka、35ka时,能够形成平衡良好地熔入到铝延展材料侧以及铝铸件材料侧这两方的焊核。
[0186]
(试验例3)
[0187]
如图11a所示那样,在试验例3中,在将焊接电流设为20ka、25ka、30ka、33ka、35ka、37ka时,能够形成平衡良好地熔入到铝延展材料侧以及铝铸件材料侧这两方的焊核。但是,在任意焊接电流,焊核也稍微偏向铝铸件材料侧而形成。
[0188]
(试验例4)
[0189]
如图12a所示那样,在试验例4(比较例)中,在将焊接电流设为30ka、33ka、35ka时,能够形成平衡良好地熔入到铝延展材料侧以及铝铸件材料侧这两方的焊核。然而,在将焊接电流设为20ka、25ka时,焊核偏向铝铸件材料侧而形成。
[0190]
(2)焊接耳垂
[0191]
在图9b、图10b、图11b以及图12b示出试验例1~3以及试验例4中的焊接耳垂。需要说明的是,在各图中,由5√t(t:板厚)表示成为基准的焊核直径。(试验例1)
[0192]
如图9b所示那样,在试验例1中可知,焊接电流在28ka以上能够形成适度的焊核直
径(5√t)的焊核,另外,在37ka以下能够抑制飞溅(内飞溅)的产生。即,在试验例1中,能够形成适度的直径的焊核的焊接推荐范围(形成5√t的焊核到产生飞溅的焊接电流的范围。以下相同。)为28ka以上且37ka以下。
[0193]
(试验例2)
[0194]
如图10b所示那样,在试验例2中可知,焊接电流在31ka以上能够形成适度的焊核直径(5√t)的焊核,另外,在35ka以下能够抑制飞溅(内飞溅)的产生。即,在试验例2中,能够形成适度的直径的焊核的焊接推荐范围为31ka以上且35ka以下。
[0195]
(试验例3)
[0196]
如图11b所示那样,在试验例3中可知,焊接电流在27ka以上能够形成适度的焊核直径(5√t)的焊核,另外,在37ka以下能够抑制飞溅(内飞溅)的产生。即,在试验例3中,能够形成适度的直径的焊核的焊接推荐范围为27ka以上且37ka以下。
[0197]
(试验例4)
[0198]
如图12b所示那样,在试验例4(比较例)中可知,焊接电流在28ka以上能够形成适度的焊核直径(5√t)的焊核,另外,在35ka以下能够抑制飞溅(内飞溅)的产生。即,在试验例4中,能够形成适度的直径的焊核的焊接推荐范围为28ka以上且35ka以下。
[0199]
(3)截面状态
[0200]
图13a~图13d是示出以焊接电流25ka进行了焊接时的焊核的状态的图像,图13a是试验例1中的截面图像,图13b是试验例2中的截面图像,图13c是试验例3中的截面图像,图13d是试验例4中的截面图像。图14a、图14b是示出以焊接电流35ka进行了焊接时的焊核的状态的图像,图14a是试验例1中的截面图像,图14b是试验例3中的截面图像。
[0201]
需要说明的是,在图13a~图13d以及图14a、图14b的各图像中,上侧为铝延展材料w,下侧为铝铸件材料c。
[0202]
如图13a所示那样,在试验例1中能够确认,在以焊接电流25ka进行了点焊的情况下,焊核n不仅平衡良好地熔入铝铸件材料c还平衡良好地熔入铝延展材料w。同样地,如图13b所示那样,在试验例2也能够确认,在以焊接电流25ka进行了点焊的情况下,焊核n不仅平衡良好地熔入铝铸件材料c还平衡良好地熔入铝延展材料w。并且,如图13c所示那样,在试验例3中也能够确认,在以焊接电流25ka进行了点焊的情况下,焊核n不仅平衡良好地熔入铝铸件材料c还平衡良好地熔入铝延展材料w。
[0203]
尤其是,如图14a所示那样,在试验例1中能够确认,在以焊接电流35ka进行了点焊的情况下,焊核n相对于铝铸件材料c以及铝延展材料w平衡良好地充分熔入。同样地,如图14b所示那样,在试验例3中也能够确认,在以焊接电流35ka进行了点焊的情况下,焊核n相对于铝铸件材料c以及铝延展材料w平衡良好地充分熔入。
[0204]
与此相对,如图13d所示那样,在作为比较例的试验例4中能够确认,在焊接电流25ka下,焊核n仅偏向铝铸件材料c侧而形成,向铝延展材料w的熔入不充分。另外,在试验例4中,在以焊接电流35ka进行了点焊时产生了飞溅。
[0205]
根据上述的试验结果,在试验例1~3中可知,能够相对于铝铸件材料以及铝延展材料形成抑制飞溅的产生并且平衡良好地熔入的焊核。
[0206]
在试验例1、2中,通过使第一电极以及第二电极的前端面的形状不同,另外,在试验例3中通过将第二电极的前端面粗糙面化,从而第二电极相对于铝铸件材料的接触面积
比第一电极相对于铝延展材料的接触面积大。
[0207]
即,认为通过使第二电极相对于与铝延展材料相比容易发热的铝铸件材料的接触面积比第一电极相对于铝延展材料的接触面积大,从而在通电工序中铝铸件材料的电流密度变低,发热集中在铝铸件材料侧的情况被抑制。
[0208]
[b]变更电极加压力
[0209]
接着,对提高电极压力而进行点焊的方案进行说明。
[0210]
与上述的点焊条件同样地,利用一对第一电极以及第二电极夹入相互重叠了的相同尺寸的铝延展材料与铝铸件材料,并在包括比前述的5kn高的加压力的各种加压力的条件下进行了点焊。并且,分别求出从形成于铝延展材料与铝铸件材料之间的焊核成为5√t的最低电流到产生飞溅的焊接电流的焊接推荐范围的宽度。
[0211]
<试验片>
[0212]
(铝延展材料)
[0213]
材质:6k21-t4(6000系铝合金的延展材料)
[0214]
形状:宽度40mm、长度100mm的板状
[0215]
厚度:2mm
[0216]
(铝铸件材料:试验例5~7、11、12)
[0217]
材质:adc12(由铝合金构成的压力铸造材料)
[0218]
形状:宽度40mm、长度100mm的板状
[0219]
厚度:2mm
[0220]
(铝铸件材料:试验例8~10)
[0221]
材质:ac4ch(由铝合金构成的压力铸造材料)
[0222]
形状:宽度40mm、长度100mm的板状
[0223]
厚度:2mm
[0224]
<试验条件>
[0225]
(1)焊接条件
[0226]
电极加压力:3.0kn、4.0kn、5.0kn、6kn、7kn
[0227]
焊接电流:20ka、25ka、30ka、33ka、35ka、40ka、43ka
[0228]
(2)焊接方法
[0229]
将第一电极作为正极,将第二电极作为负极,使重叠了的铝延展材料与铝铸件材料夹入第一电极与第二电极之间,在铝延展材料侧配置作为正极的第一电极并且在铝铸件材料侧配置作为负极的第二电极。
[0230]
利用第一电极与第二电极对铝延展材料以及铝铸件材料进行加压,在从加压开始100ms后以通电时间200ms通电焊接电流,并在电流通电结束后使加压保持200ms而结束加压。
[0231]
(3)使用电极第一电极(正极侧电极)、第二电极(负极侧电极)
[0232]
类别:半径形(r形)电极
[0233]
电极前端直径:19mm
[0234]
前端曲率半径:100mm
[0235]
前端面:平滑面
[0236]
图15是示出试验例5中的基于电极加压力的焊接推荐范围的变化的图表。在各焊接电流中,由
“○”
表示得到5√t的焊核直径的焊接电流的最小值,由
“▲”
表示产生了内飞溅的焊接电流的最小值。
[0237]
在电极加压力为3kn~6kn的范围内,焊接推荐范围为5~7ka程度的宽度,但在将电极加压力设为7kn时,焊接推荐范围扩大为约10ka的宽度。
[0238]
在试验例6(比较例)中,求出将试验例5的电极加压力设为5kn(通电时间:200ms)的将条件变更为各种通电时间的情况下的焊接推荐范围。
[0239]
图16是示出试验例6中的焊接电流与通电时间的关系的图表。
[0240]
在将通电时间设为50ms、100ms、150ms以及试验例5的200ms的情况下,焊接推荐范围成为3~5ka程度的宽度。
[0241]
在试验例7中,求出将试验例5的电极加压力设为7kn(通电时间:200ms)的将条件变更为各种通电时间的情况下的焊接推荐范围。
[0242]
图17是示出试验例7中的焊接电流与通电时间的关系的图表。
[0243]
在将通电时间设为50ms、100ms、150ms以及试验例5的200ms的情况下,与电极加压力为5kn的情况比较,焊核尺寸达到5√t的焊接电流值增加,但产生内飞溅的焊接电流值特别大,通电时间为100ms以上时焊接推荐范围扩大为10ka程度的宽度。
[0244]
在试验例8中,材料将试验例5的铝铸件材料替换为ac4ch以外,设为与试验例5相同的条件。
[0245]
图18是示出试验例8中的基于电极加压力的焊接推荐范围的变化的图表。
[0246]
此时的通电时间为200ms。在试验例8中,电极加压力到5kn时焊接推荐范围为约5ka以下的宽度,但在将电极加压力设为6kn以上时,焊接推荐范围扩大到约10kn以上的宽度。
[0247]
在试验例9(比较例)中,除了将试验例6的铝铸件材料替换为ac4ch以外,设为与试验例6相同的条件。
[0248]
图19是示出试验例9中的焊接电流与通电时间的关系的图表。
[0249]
在将电极加压力设为5kn,并将通电时间设为50ms、100ms、150ms以及200ms的情况下,焊接推荐范围在100ms~200ms之间成为2~5ka程度的宽度。
[0250]
在试验例10中,除了将试验例7的铝铸件材料替换为ac4ch以外,设为与试验例7相同的条件。
[0251]
图20是示出试验例10中的焊接电流与通电时间的关系的图表。
[0252]
在将电极加压力设为7kn,并将通电时间设为50ms、100ms、150以及200ms的情况下,与电极加压力为5kn的情况相比,焊核尺寸达到5√t的焊接电流值增加。另外,产生内飞溅的焊接电流值特别大,通电时间为100ms以上时焊接推荐范围扩大为10ka以上的宽度。
[0253]
根据试验例5~7以及试验例8~10可知,与铝铸件材料的种类无关,电极加压力的增加有助于焊接推荐范围的扩大。
[0254]
在试验例11中确认了,使用粗糙面化了的电极使电极加压力增加了的情况的焊接推荐范围。所使用的电极如以下那样。(第一电极:正极侧电极)
[0255]
类别:半径形(r形)电极
[0256]
电极前端直径:19mm
[0257]
前端曲率半径:100mm
[0258]
前端面:平滑面
[0259]
(第二电极:负极侧电极)
[0260]
类别:半径形(r形)电极
[0261]
电极前端直径:19mm
[0262]
前端曲率半径:100mm
[0263]
前端面:利用具备粒度z60的氧化锆磨石的带式砂光机进行研磨而粗糙面化。
[0264]
图21是示出将试验例11的电极加压力设为7kn的情况下的焊核直径相对于焊接电流的分布的图表。
[0265]
在将电极加压力设为7kn时,焊接推荐范围扩大为为10ka的宽度,因此可知即使在变更了电极的接触面积的情况下,也对焊接推荐范围的扩大有效果。
[0266]
在试验例12中,确认了变更板厚而增加了电极加压力的情况下的焊接推荐范围的变化。所使用的铝延展材料21与铝铸件材料如以下所示那样。(铝延展材料)
[0267]
材质:6k21-t4(6000系铝合金的延展材料)
[0268]
形状:宽度40mm、长度100mm的板状
[0269]
厚度:1mm
[0270]
(铝铸件材料:)
[0271]
材质:adc12(由铝合金构成的压力铸造材料)
[0272]
形状:宽度40mm、长度100mm的板状
[0273]
厚度:2mm
[0274]
图22是示出试验例12中的基于电极加压力的焊接推荐范围的变化的图表。
[0275]
如图22所示那样,即使在铝延展材料的厚度设为1.0mm的情况下,当电极加压力成为7kn以上时焊接推荐范围也扩大。即,可知即使铝延展材料与铝铸件的板厚比变化,电极加压力的增加也有助于焊接推荐范围的扩大。
[0276]
图23是用于说明压痕的深度的定义的截面照片。图24是示出求出焊核直径为5√t时的压痕深度的结果的图表。
[0277]
当使电极加压力增加时,在试验片的表面产生的电极的压痕变深。在此所说的压痕的深度是指如图23所示那样,铝延展材料的表面的压痕深度t1与铝铸件的表面的压痕深度t2的平均值(=(t1 t2)/2)。
[0278]
将电极加压力3kn、5kn、7kn的压痕深度的分布分别近似为直线,并根据求出的近似直线算出焊核直径相当于5√t的7.1mm时的压痕深度。其结果绘制于图24。具体而言,电极加压力为3kn、5kn、7kn时的压痕深度为0.134mm、0.154mm、0.168mm。
[0279]
当对图24的图表所绘制的各点进行直线近似,并求出压痕深度不超过板厚t的10%(t=2mm因此为0.2mm)的电极加压力时,成为该界限的电极加压力为约10kn。即,通过将电极加压力设为10kn以下,从而维持适当的加压力。
[0280]
这样,本发明并不限定于上述的实施方式,将实施方式的各结构相互组合、本领域技术人员基于说明书的记载以及公知的技术而进行变更、应用也是本发明所预定的,并包括在请求保护的范围。
[0281]
如以上那样,在本说明书中公开了如下事项。
[0282]
(1)一种点焊方法,其中,
[0283]
所述点焊方法包括:
[0284]
重叠工序,在所述重叠工序中,将铝延展材料与铝铸件材料重叠;
[0285]
配置工序,在所述配置工序中,将重叠了的所述铝延展材料以及所述铝铸件材料插入配置于对置位置的第一电极与第二电极之间,在所述铝延展材料侧配置第一电极并且在所述铝铸件材料侧配置所述第二电极;以及
[0286]
通电工序,在所述通电工序中,一边利用所述第一电极与所述第二电极将重叠了的所述铝延展材料以及所述铝铸件材料夹入而进行加压,一边向所述第一电极与所述第二电极之间通电,
[0287]
在所述通电工序中,使所述第二电极相对于所述铝铸件材料的接触面积比所述第一电极相对于所述铝延展材料的接触面积大。
[0288]
根据该点焊方法,在通电工序中,使第二电极相对于铝铸件材料的接触面积比第一电极相对于铝延展材料的接触面积大。由此,在通电工序中,降低与铝延展材料相比容易发热的铝铸件材料的电流密度,能够抑制发热集中在铝铸件材料侧的情况。即,能够取得电阻值以及熔点较大不同的铝延展材料以及铝铸件材料的焊接时的电阻发热的平衡,能够抑制飞溅的产生并且在适当的位置无偏向地形成焊核。
[0289]
因此,能够通过点焊将铝延展材料与铝铸件材料以较高的焊接品质接合,能够实现由铝材构成的结构体的紧凑化、轻量化以及成本降低。
[0290]
(2)根据(1)所述的点焊方法,其中,
[0291]
使用具有由曲面构成的前端面的电极来作为所述第一电极,使用具有由平面构成的前端面的电极来作为所述第二电极。
[0292]
根据该点焊方法,容易使第二电极相对于铝铸件材料的接触面积比第一电极相对于铝延展材料的接触面积大,能够取得铝延展材料以及铝铸件材料的焊接时的电阻发热的平衡。
[0293]
(3)根据(1)所述的点焊方法,其中,
[0294]
使用具有由曲面构成的前端面的电极来作为所述第一电极,使用具有由比所述第一电极的前端面大的曲率半径的曲面构成的前端面的电极来作为所述第二电极。
[0295]
根据该点焊方法,能够容易使第二电极相对于铝铸件材料的接触面积比第一电极相对于铝延展材料的接触面积大,并取得铝延展材料以及铝铸件材料的焊接时的电阻发热的平衡。
[0296]
(4)根据(1)~(3)中任一项所述的点焊方法,其中,使用前端面被粗糙面化了的电极来作为所述第二电极。
[0297]
根据该点焊方法,第二电极的前端面被粗糙面化了,因此能够高效地增大第二电极相对于铝铸件材料的接触面积。
[0298]
(5)根据(1)~(4)中任一项所述的点焊方法,其中,在所述通电工序中,将所述第一电极作为正极并且将所述第二电极作为负极,而向重叠了的所述铝延展材料以及所述铝铸件材料通电。
[0299]
根据该点焊方法,能够通过所谓的极性效应,而使与作为正极的第一电极相接的铝延展材料侧的发热比与作为负极的第二电极相接的铝铸件材料侧的发热大。由此,能够
进一步良好地取得铝延展材料以及铝铸件材料的焊接时的电阻发热的平衡。
[0300]
(6)根据(1)~(5)中任一项所述的点焊方法,其中,
[0301]
在所述通电工序中,将电极加压力设为7.0kn以上且10kn以下。
[0302]
根据该点焊方法,通过使电极加压力增加,从而将在铝延展材料与铝铸件材料之间形成的熔融金属压入电极间。因此,到较高的焊接电流值时飞溅的产生被抑制,能够提高焊接条件的裕度而形成良好的尺寸的焊核。由此,焊接条件的自由度提高,能够提高焊接施工性。
[0303]
(7)一种点焊方法,其中,
[0304]
所述点焊方法包括:
[0305]
重叠工序,在所述重叠工序中,将铝延展材料与铝铸件材料重叠;
[0306]
配置工序,在所述配置工序中,将重叠了的所述铝延展材料以及所述铝铸件材料插入配置于对置位置的第一电极与第二电极之间,在所述铝延展材料侧配置第一电极并且在所述铝铸件材料侧配置所述第二电极;以及
[0307]
通电工序,在所述通电工序中,一边利用所述第一电极与所述第二电极将重叠了的所述铝延展材料以及所述铝铸件材料夹入而进行加压,一边向所述第一电极与所述第二电极之间通电,
[0308]
在所述通电工序中,将电极加压力设为7.0kn以上且10kn以下。
[0309]
根据该点焊方法,通过使电极加压力增加,从而将在铝延展材料与铝铸件材料之间形成的熔融金属压入电极间。因此,到较高的焊接电流值时飞溅的产生被抑制,能够提高焊接条件的裕度而形成良好的尺寸的焊核。由此,焊接条件的自由度提高,能够提高焊接施工性。
[0310]
需要说明的是,本技术基于2019年12月25日申请的日本专利申请(特愿2019-233663)以及2020年9月30日申请的日本专利申请(特愿2020-166359),其内容在本技术中作为参照而被引用。
[0311]
附图标记说明
[0312]
13 第一电极
[0313]
13a 前端面
[0314]
15 第二电极
[0315]
15a 前端面
[0316]
21 铝延展材料
[0317]
23 铝铸件材料。
再多了解一些
本文用于企业家、创业者技术爱好者查询,结果仅供参考。