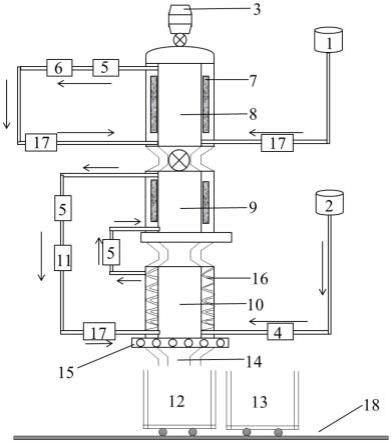
1.本发明涉及高磷铁矿处理技术领域,特别涉及一种高磷铁矿氢还原-自粉碎提铁除磷方法及装置。
背景技术:
2.我国高磷铁矿石占总铁矿资源的10%以上,开发和利用高磷矿是资源战略的必然选择。高炉炼铁过程矿石中的磷基本上全部进入铁水从而对钢材性能产生极大危害,此外炼钢产生的高磷钢渣资源循环使用困难,冶金流程循环使用会造成整个钢铁生产过程中磷的恶性富集,直接用于原料生产磷肥则磷含量太低,限制了其高效使用。因此针对高磷铁矿开发高效提铁除磷技术是实现其高效利用的必然选择。
3.研究人员已经对高磷铁矿脱磷工艺进行了大量研究并取得了一定成果,目前较热门的脱磷方法有选矿法、微生物法、化学浸出-浮选法等。但由于高磷铁矿复杂的矿物结构,氧化铁晶粒嵌布粒度细,并且与磷灰石、鲕绿泥石相互夹杂分布,呈现层状相同的鲕粒结构,使得现有选矿工艺无法高效实现铁、磷元素的有效分离。微生物脱磷有较好的效果,但由于培养微生物时间较长,且需要较长的脱磷周期限制了该工艺的工业化应用。化学脱磷法结合浮选工艺脱磷,可实现磷元素的脱除,但铁元素富集程度较低,而且处理过程中会产生大量环境问题。由于无法得到有效提铁脱磷的工艺方法,使得我国对于高磷赤铁矿一直没有综合利用。因此,到目前为止研究并开发能够实现工业化应用的高效提铁除磷技术仍是钢铁生产流程亟待解决的技术难题。
技术实现要素:
4.本发明的目的是至少克服现有技术不足之一,提供了一种高磷铁矿氢还原-自粉碎提铁除磷方法及装置,利用高磷矿粉搭配生石灰进行造球,通过严格控制配矿中各组分的比例, 在一定的温控制度下,控制还原过程中铁的聚集和渣相中硅酸钙的晶型转变,确保急冷过程矿石中的磷灰石与炉渣一起粉碎实现磷铁分离,从而为实现高磷铁矿的高效利用提供一种新方法。
5.本发明采用如下技术方案:一方面,本发明提供了一种高磷铁矿氢还原-自粉碎提铁除磷方法,包括:s1、造球:将高磷铁矿配入适量膨润土、生石灰或转炉粉尘充分混匀后造球,干燥后焙烧得到成品球团;s2、氢还原:将焙烧好的成品球团在氢氛围下还原,还原温度为1538-1700℃,还原时间15-20min;s3、恒温处理:对经步骤s2处理后的炉料在惰性气氛保护下进行恒温处理,恒温处理温度为1100℃-1150℃,处理时间不小于60min,促进硅酸钙的晶型转变;s4、快速冷却粉碎:经步骤s3处理后的炉料进行快速冷却处理,炉料在20min之内快速冷却到100℃之下;
s5、磷铁分离:对经步骤s4处理后的金属铁和炉渣进行筛分分离。
6.如上所述的任一可能的实现方式,进一步提供一种实现方式,步骤s1中,生石灰依据高磷铁矿中磷酸钙的含量进行配比,造球过程中维持碱度3.0-3.5。
7.如上所述的任一可能的实现方式,进一步提供一种实现方式,步骤s2中,高磷矿中的铁氧化物被还原成金属铁并熔化聚集成大于5mm的金属小颗粒,得到金属化率大于95%的还原炉料。
8.如上所述的任一可能的实现方式,进一步提供一种实现方式,步骤s3中,惰性气氛为氮气。
9.如上所述的任一可能的实现方式,进一步提供一种实现方式,步骤s4中,快速冷却的方式为:在炉底通入冷却氮气,同时在炉体中设置水冷系统。
10.另一方面,本发明还提供了一种高磷铁矿氢还原-自粉碎提铁除磷装置,包括自上而下依次连通设置的还原炉、恒温炉、粉碎炉;所述还原炉顶部设置装料口,还原炉的内壁设置电加热单元,还原炉底部连通储氢罐;所述还原炉内的还原温度为1538-1700℃;所述恒温炉的顶部与还原炉的底部连通,恒温炉的内壁设置电加热单元;所述恒温炉内的温度为1100℃-1150℃;所述粉碎炉的顶部与所述恒温炉底部连通,粉碎炉底部设置振动筛网,粉碎炉底部连通储氮罐,粉碎炉底部设置卸料口;所述粉碎炉顶部设置有与所述恒温炉底部连通的氮气管道,氮气经储氮罐进入粉碎炉内并通过所述氮气管道进入恒温炉底部。
11.如上所述的任一可能的实现方式,进一步提供一种实现方式,所述粉碎炉底部设置有收铁罐和收渣罐。
12.如上所述的任一可能的实现方式,进一步提供一种实现方式,收铁罐和收渣罐均设置在导轨上,收铁罐和收渣罐可轮流运行到粉碎炉下。
13.如上所述的任一可能的实现方式,进一步提供一种实现方式,所述装置还包括还原炉煤气再利用系统,所述还原炉煤气再利用系统包括净化除尘器、压缩处理机和风机;还原炉顶部设置煤气出口,所述煤气出口通过管道依次连接净化除尘器、压缩处理机和风机,并再次通过管道与还原炉底部连通。
14.如上所述的任一可能的实现方式,进一步提供一种实现方式,所述装置还包括氮气循环及余热利用系统,所述氮气循环及余热利用系统包括净化除尘器、余热发电单元和风机;恒温炉顶部设置高温氮气出口,所述高温氮气出口通过管道依次连接净化除尘器、余热发单单元和风机,并再次通过管道与粉碎炉底部连通。
15.如上所述的任一可能的实现方式,进一步提供一种实现方式,所述振动筛网为孔径为不大于5mm的圆孔振动筛,实验证明孔径为5mm时最佳。
16.本发明的有益效果为:通过本发明方法可实现高磷铁矿中铁和磷的高效分离,铁收得率90%,铁中磷含量0.08%,分离收集到的金属铁可直接用于炼钢,筛分得到的含磷渣主要成分是含有大量cao、sio2,可作为原料用于生产水泥、磷肥、混凝土、陶瓷材料、微晶玻璃、耐火保温纤维等,实现高磷矿的绿色、高效利用。
附图说明
17.图1所示为本发明实施例一种高磷铁矿氢还原-自粉碎提铁除磷装置的结构示意图。
18.图中:1-储氢罐,2-储氮管,3-装料口,4-冷却风机,5-净化除尘器,6-压缩处理机,7-电加热棒,8-还原炉,9-恒温炉,10-粉碎炉,11-余热发电单元,12-收渣罐,13-收铁罐,14-卸料口,15-振动筛网,16-水冷系统,17-风机,18-导轨。
具体实施方式
19.下文将结合具体附图详细描述本发明具体实施例。应当注意的是,下述实施例中描述的技术特征或者技术特征的组合不应当被认为是孤立的,它们可以被相互组合从而达到更好的技术效果。在下述实施例的附图中,各附图所出现的相同标号代表相同的特征或者部件,可应用于不同实施例中。
20.如图1所示,本发明实施例一种高磷铁矿氢还原-自粉碎提铁除磷装置,包括自上而下依次连通设置的还原炉8、恒温炉9、粉碎炉10;所述还原炉8顶部设置装料口3,还原炉8的内壁设置电加热单元(电加热棒)7,还原炉8底部连通储氢罐1;所述还原炉8内的还原温度为1538-1700℃;所述恒温炉9的顶部与还原炉8的底部连通,恒温炉9的内壁设置电加热单元(电加热棒)7;所述恒温炉9内的温度为1100℃-1150℃;所述粉碎炉10的顶部与所述恒温炉9底部连通,粉碎炉10底部设置振动筛网15,振动筛网15优选为孔径为5mm的圆孔振动筛,粉碎炉10底部连通储氮罐2,粉碎炉10底部设置卸料口14;所述粉碎炉10顶部设置有与所述恒温炉9底部连通的氮气管道,氮气经储氮罐2进入粉碎炉10内并通过所述氮气管道进入恒温炉9底部,所述粉碎炉10底部设置有收铁罐13和收渣罐12,收铁罐13和收渣罐12均设置在导轨18上。
21.优选的,所述装置还包括还原炉煤气再利用系统,所述还原炉煤气再利用系统包括净化除尘器5、压缩处理机6和风机17;还原炉8顶部设置煤气出口,所述煤气出口通过管道依次连接净化除尘器5、压缩处理机6和风机17,并再次通过管道与还原炉8底部连通。
22.优选的,所述装置还包括氮气循环及余热利用系统,所述氮气循环及余热利用系统包括净化除尘器5、余热发电单元11和风机17;恒温炉9顶部设置高温氮气出口,所述高温氮气出口通过管道依次连接净化除尘器5、余热发单单元11和风机17,并再次通过管道与粉碎炉10底部连通。
23.本发明实施例一种高磷铁矿氢还原-自粉碎提铁除磷方法,使用上述的高磷铁矿氢还原-自粉碎提铁除磷装置,所示方法包括:s1、造球:将高磷铁矿配入适量膨润土、生石灰(或转炉粉尘)充分混匀后造球,干燥去除水分后采用三段式焙烧方法得到成品球。特别的造球过程中需严格控制生石灰的配比,其配比区间需依据磷酸钙的含量和混合料碱度进行约束,这主要是因为反应过程矿物中的磷酸钙与生成的β-2cao
·
sio2结合能力较强形成固熔体,这会抑制β-2cao
·
sio2的粉化,因此为确保反应生成足够的2cao
·
sio2使得粉化炉中生成的炉渣更好的粉碎从而为磷铁分离提供有利基础,造球过程中生石灰的配比范围遵循以下原则。最高配比由混合料碱度决定,应确保添加生石灰后混合料碱度应低于3.5(碱度=cao/sio2),过高的碱度会减缓硅酸钙的晶型转变速度从而使得炉渣粉碎率降低。最低添加量由矿石中磷酸钙的含量进行
确定,生石灰含量过低生成的硅酸钙被磷酸钙完全固结,粉碎段中炉渣中没有足量的硅酸钙使得炉渣粉碎,其最低添加量如式1所示,y =112x/155
ꢀꢀꢀꢀꢀꢀꢀꢀꢀꢀꢀꢀꢀꢀꢀꢀꢀꢀꢀꢀꢀꢀꢀꢀ
式1其中y:混合料中生石灰的最低添加量(质量百分数,%)x:高磷矿中磷酸三钙含量(质量百分数,%)综上生石灰添加量调控范围:112x/155<y<3.5z其中z:混合料中sio2含量(质量百分数,%);高磷铁矿磷和铁分离炉体采用设计的三段式还原-恒温-粉碎炉,还原炉8,恒温炉9和粉碎炉10串联分布;s2、氢还原:将焙烧好的球团通过炉顶装料口3加入还原炉8,还原炉底部进气口通过管道与储氢罐1连接,炉料在与氢气的逆向运动中被还原。其中还原炉8采用电加热方式,两侧埋有电加热棒7,炉内温度可稳定在1538℃,为铁的熔化温度(当然也可以选择1538-1700℃中的任一温度),在此温度下铁氧化物可被快速还原为金属铁,同时该温度下铁会被熔化聚集。球团从上至下在还原段还原15-20min,在此时间段内铁氧化物被快速还原为金属铁。实验研究表明还原时间过短铁氧化物还原不完全会使得金属铁无法聚集,还原时间过长还原生成的液态金属铁过度流动会包裹炉渣从而使得粉碎的炉渣无法被筛分去除,因此最终确定控制还原时间为15-20min。此时高磷矿中的铁氧化物被还原成金属铁并熔化聚集成大于5mm的金属小颗粒,得到金属化率大于95%的还原炉料,由于氢气还原气氛中,磷灰石开始还原温度较高(>1538℃),因此还原炉8内磷灰石未被还原被固定在渣相中。此外,由于高磷铁矿渣相中sio2含量高,cao和sio2结合生成大量正硅酸钙(2cao
·
sio2,熔点2130℃),硅酸三钙(3cao
·
sio2,熔点1900℃))。还原炉炉顶煤气中含有未利用的氢气,通过净化除尘器5、压缩处理机6后在风机17的作用下重新返回至炉中;s3、恒温处理:还原炉8的炉料向下运动进入恒温炉9,与还原炉8采取同样的加热方式,两侧埋有电加热棒7,炉内温度稳定在1100℃-1150℃区间内(晶型转变温度),恒温炉9底部通过管道与经过粉碎炉10预热并净化除尘器5处理过的氮气连接,整个恒温段通氮气进行保护。在此阶段内通过恒温处理60min(要求时间不小于60min,过长时间则浪费能量,建议可选取60-65min为宜)促进硅酸钙的晶型转变(3cao
·
sio2分解为α-2cao
·
sio2),经过晶型转变使得所有硅酸钙的晶型转变为为α-2cao
·
sio2。在此阶段时间过短无法使得所有硅酸钙转变为α-2cao
·
sio
2,
时间过长造成能耗的提高和生产率的下降。此外,利用炉顶流出的高温氮气通过净化除尘器5可进行余热发电,降温之后通入粉碎炉10中实现氮气的循环利用;s4、快速冷却粉碎:恒温炉9处理的炉料向下运动进入粉碎炉10,炉底进气口通过管道与储氮罐2连接,从粉碎炉10底部通入经过冷却风机4冷却的氮气,同时炉体两侧埋有水冷系统16,进入此阶段的炉料被快速冷却,可在20min内将炉料温度迅速冷却到100℃以下,急冷过程液相中析出的矿物来不及结晶或者来不及长大生成没有结晶或结晶不完全的脆性的玻璃质,此外急冷过程中正硅酸钙发生三种晶形转变,由α-2cao
·
sio2转变为β-2cao
·
sio2,由β-2cao
·
sio2转变向γ-2cao
·
sio2晶型,晶型转变过程中体积膨胀,产生内应力,导致炉渣粉碎掉落至底部;s5、磷铁分离:高磷矿中的磷酸钙随炉渣一起被筛分实现磷铁分离。粉碎炉10底部
安装有孔径为5mm的圆孔振动筛网15,金属铁和炉渣采取分批回收方式,卸料口14下方铺设有导轨18,收渣罐12和收铁罐13可来回移动实现分批卸料,其中振动筛网的选择是由生成的金属铁颗粒的直径决定的,研究表明还原炉中生成的金属小颗粒直径大于5mm,过小的筛子不利于快速筛分,过大的筛子会使得金属颗粒被筛下进入炉渣中从而使得生产率降低。首先粉碎的炉渣筛分至收渣罐12中,筛上物金属铁则通过卸料口14收集至收铁罐13,完成磷铁分离;本方法使用能够在零碳、零固废的基础上实现高磷铁矿中磷和铁的高效分离,符合国家倡导的节能减排,且整体工艺流程简单、生产效率高,可实现高磷铁矿大规模工业化利用,使经济、低碳应用高磷铁矿成为可能。
24.本发明提供的高磷铁矿氢还原-自粉碎提铁除磷方法,具有较强的原料适应性强,除高磷铁矿外还可适用于其他低品位铁矿的提铁操作。
25.本文虽然已经给出了本发明的几个实施例,但是本领域的技术人员应当理解,在不脱离本发明精神的情况下,可以对本文的实施例进行改变。上述实施例只是示例性的,不应以本文的实施例作为本发明权利范围的限定。
再多了解一些
本文用于企业家、创业者技术爱好者查询,结果仅供参考。