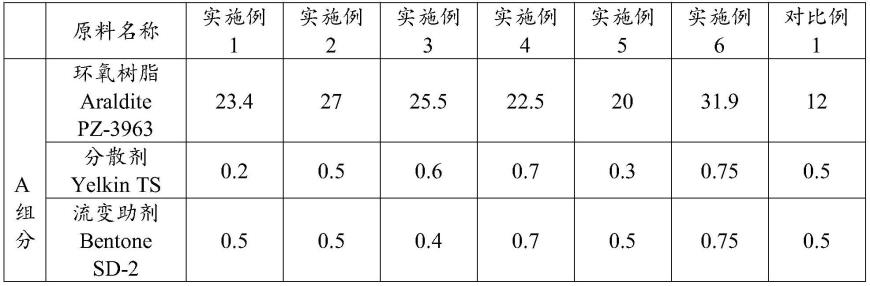
1.本发明属于防腐底漆技术领域,具体涉及一种水性环氧富锌底漆及其制备方法和应用。
背景技术:
2.随着环境保护诉求的加大,水性富锌底漆逐渐被推广起来。由于锌粉比较活泼,会与水发生反应,而水性涂料中含水,因此锌粉在水性涂料中的应用工艺比较特殊。水性环氧富锌底漆的发展历程大致可分为三个阶段:第一阶段:水性环氧富锌底漆由水性化的环氧乳液、水性环氧固化剂和锌粉三个组分组成。此阶段环氧乳液和水性环氧固化剂分别作为涂料的常规a、b组分,一般都已经过水性化改性,形成的产品中也含有水;锌粉作为一个单独的c组分,在施工时,将a、b、c组分混合后在适用期内进行施工。第一阶段的产品是由三组分构成的水性环氧富锌底漆体系,因配漆工艺繁琐、搅拌时间长、粘度大、消泡难和现场锌尘大等问题,已逐渐淡出市场。目前,水性环氧富锌底漆以第二阶段、第三阶段产品为主流体系;其中,第二阶段产品:以含有亲水性基团但不加水的环氧固化剂作为锌粉的载体,配以其他颜填料、助剂等作为主漆a组分,环氧乳液作为b组分,施工时将a、b两组分混合均匀,再加水稀释,在适用期内进行施工。第二阶段的水性环氧富锌底漆体系的环氧固化剂通常亲水性物质的含量比较低,因此固化后涂膜无论耐水、耐盐雾性能都比较优异。但由于主漆中溶剂含量多、亲水程度不够、又需承载大量锌粉,故而对环氧乳液的稳定性要求比较高,水性环氧富锌底漆体系采用少量的固化剂树脂包覆锌粉的方式,要满足锌粉在储存时不沉降,需要更多的分散剂、防沉剂和大量的溶剂稀释,因此主漆的voc含量较高。此外,主漆由碱性较强的环氧固化剂承载锌粉,对长期贮存稳定性不利。基于此,迫切需要开发新的水性环氧富锌底漆体系。
3.为了解决锌粉载体导致涂料长期贮存稳定性不足的问题,以环氧组分作为锌粉载体的第三阶段水性环氧富锌底漆体系应运而生,即水性环氧富锌底漆的发展历程第三阶段:在环氧树脂中引入亲水性物质,但在涂料产品的成分中不加水,而是加入锌粉和助剂等作为涂料的主漆a组分(不含水),水性环氧固化剂作为b组分(含水),进行固化。这一类水性环氧富锌底漆体系较为明显的优点在于采用较多量的环氧树脂包覆锌粉,而环氧树脂本身酸碱性也比较微弱,因此主体树脂对锌粉的分散性、稳定性、防沉等方面都明显优于第二阶段水性环氧富锌底漆。这一类体系中,环氧树脂水性化为关键技术,其引入的亲水物质含量比普通环氧乳液要多,这可以保证主漆配漆加水时相反转流畅,不发生破乳、絮凝、分层、适用期缩短等问题。但过多的亲水性物质会损失涂膜的防腐性能。从实际应用情况看,第二阶段产品涂膜防腐性能更加优异,但贮存和施工稍嫌麻烦;第三阶段产品性能更稳定,施工性好。两种体系各有利弊,需要针对不同工况和实际要求进行设计。
4.水性环氧富锌底漆的防护利用锌粉与基材的氧化还原电势差来起到保护基材的作用。在腐蚀环境中通过牺牲锌粉(阳极)达到保护基体(阴极)的目的,锌粉与氧气、二氧化碳和水形成锌盐,而锌盐被氧化分解后形成氧化锌作为填料沉积在漆膜中,较高的颜料体
积浓度导致防腐性下降,铁质基材开始生锈。富锌底漆要提供阴极(基体)保护性能,必须与基体有充分的接触和形成密集充分的导电网络,而高含量的锌粉中也只有近三分之一的锌粉发挥牺牲阳极的作用,剩余的锌粉并未充分利用。此外,锌粉含量高会导致环氧树脂包裹锌粉的程度变差以至于影响涂料的沉降性、涂层附着力、抗冲击和耐磨性。
技术实现要素:
5.有鉴于此,本发明的目的在于提供一种水性环氧富锌底漆及其制备方法和应用,本发明提供的水性环氧富锌底漆在具有优异的防腐性能的同时能减少锌粉的使用量。
6.为了实现上述目的,本发明提供了以下技术方案:
7.本发明提供了一种水性环氧富锌底漆,包括a组分和b组分;
8.以质量份数计,所述a组分包括环氧树脂10~35份、助剂0.5~4.5份、锌粉65~80份和有机溶剂0.2~3.5份;所述助剂包括导电助剂;所述导电助剂包括单壁碳纳米管;
9.所述b组分包括水性环氧固化剂20~45份和水55~80份。
10.优选的,所述a组分和b组分的质量比为(8.5~12.5):1。
11.优选的,所述环氧树脂包括可用水稀释的双酚a型水性环氧树脂。
12.优选的,所述锌粉的平均粒径为2~9μm;所述水性环氧固化剂包括胺类固化剂。
13.优选的,所述助剂还包括分散剂和/或流变助剂。
14.优选的,所述分散剂包括卵磷脂;所述流变助剂包括有机膨润土。
15.本发明还提供了上述技术方案所述水性环氧富锌底漆的制备方法,包括以下步骤:
16.将环氧树脂、助剂、锌粉和有机溶剂混合,得到a组分;
17.将水性环氧固化剂和水混合,得到b组分。
18.本发明还提供了上述技术方案所述水性环氧富锌底漆或上述技术方案所述制备方法制备得到的水性环氧富锌底漆在防腐领域中的应用。
19.本发明还提供了一种利用水性环氧富锌底漆防腐的方法,包括以下步骤:
20.将a组分和b组分混合后,涂覆在基体表面,进行固化;
21.所述a组分和b组分为上述技术方案所述水性环氧富锌底漆中的a组分和b组分或上述技术方案所述制备方法制备得到的a组分和b组分。
22.优选的,所述固化的温度》5℃。
23.本发明提供了一种水性环氧富锌底漆,包括a组分和b组分;以质量份数计,所述a组分包括环氧树脂10~35份、助剂0.5~4.5份、锌粉65~80份和有机溶剂0.2~3.5份;所述助剂包括导电助剂;所述导电助剂包括单壁碳纳米管;所述b组分包括水性环氧固化剂20~45份和水55~80份。
24.本发明提供的水性环氧富锌底漆的a组分采用单壁碳纳米管作为导电助剂。单壁碳纳米管的结构是一个原子厚度的单层石墨薄片卷成的空心长管,单壁碳纳米管嵌入到涂料的基质中,分散良好的单壁碳纳米管使涂料在锌粉含量较低的情况下也能形成良好的三维导电网络,起到传递电子的作用来保护待防护基体;单壁碳纳米管的空心长管结构也能延长腐蚀介质进入基体的通道,延缓腐蚀介质深入至基体的时间,从而提高涂料的防腐蚀性能,而且单壁碳纳米管的加入可以使体系中更多的锌粉发挥牺牲阳极的作用。因此,本发
明采用单壁碳纳米管作为导电助剂,取代部分锌粉,而不损失涂料的防腐性能,使涂料不挥发分中金属锌含量降低至65~75%,仍能使涂料形成导电网络,确保水性环氧富锌底漆具有超越不挥发分中金属锌含量达到80%才能具有的优越的阴极保护性能、防腐蚀性能(如耐湿热性、耐盐雾性和耐化学介质性)、涂层附着力、柔韧性和耐冲击性。
25.此外,锌粉含量的降低会降低成本,也会减少切割等工艺产生的氧化锌烟尘量,从而有利于工作人员的健康和环境保护。
具体实施方式
26.本发明提供了一种水性环氧富锌底漆,包括a组分和b组分;以质量份数计,所述a组分包括环氧树脂10~35份、助剂0.5~4.5份、锌粉65~80份和有机溶剂0.2~3.5份;所述助剂包括导电助剂;所述导电助剂包括单壁碳纳米管;所述b组分包括水性环氧固化剂20~45份和水55~80份。
27.如无特殊说明,本发明对所用原料的来源没有特殊要求,采用本领域技术人员所熟知的市售商品即可。
28.本发明提供的水性环氧富锌底漆包括a组分;以质量份数计,所述a组分包括环氧树脂10~35份,优选为12~34份,更优选为15~33份。在本发明中,所述环氧树脂优选包括可用水稀释的双酚a型环氧树脂,更优选包括环氧树脂araldite pz-3963(亨斯迈先进化工材料(广东)有限公司)、环氧树脂hongli 3075(弘利)、环氧树脂stw600/75wa(上海华谊精细化工有限公司)、自乳化环氧树脂2ee166b(广东彤德新材料有限公司)和环氧树脂aers 6075m(无锡洪汇新材料科技股份有限公司)中的一种或几种,进一步优选为环氧树脂araldite pz-3963(亨斯迈先进化工材料(广东)有限公司)。当环氧树脂为上述几种时,本发明对不同种类环氧树脂的配比没有特殊限定,任意配比均可。
29.本发明采用的双酚a型改性环氧树脂可用水稀释,具有很好的锌粉相容性。
30.以所述a组分中环氧树脂的质量份数为基准,本发明提供的水性环氧富锌底漆的a组分包括助剂0.5~4.5份,优选为0.7~3份,更优选为0.8~2份。在本发明中,所述助剂包括导电助剂;所述导电助剂包括单壁碳纳米管,优选包括tuball
tm
单壁碳纳米管matrix 201(ocsiai)和/或bc-xg230(上海君江科技有限公司),更优选为bc-xg230。当导电助剂为tuball
tm
单壁碳纳米管matrix 201(ocsiai)和bc-xg230(上海君江科技有限公司)时,本发明对不同种类导电助剂的配比没有特殊限定,任意配比均可。
31.本发明所用导电助剂是结构为一个原子厚度的单层石墨薄片卷成的空心长管的单壁碳纳米管,单壁碳纳米管嵌入到涂料的基质中,分散良好的单壁碳纳米管会形成三维导电网络,起到传递电子的作用来保护基体;单壁碳纳米管的空心长管结构也能延长腐蚀介质进入基体的通道,延缓腐蚀介质深入至基体的时间,从而提高涂料的防腐蚀性能。而且单壁碳纳米管作为全新纳米导电材料,添加量少,漆膜电阻值稳定,漆膜厚度适应力强,分散简便,且对环氧富锌底漆原来的颜色或其他主要性能影响极小。
32.在本发明中,所述导电助剂的质量优选为所述a组分总质量的0.01~0.15%,更优选为0.02~0.10%。本发明仅需在a组分中占极少份量的导电助剂就能在明显降低锌粉含量的前提下仍形成导电网络,确保水性环氧富锌底漆的阴极保护性能。
33.在本发明中,所述助剂优选还包括分散剂和流变助剂;所述分散剂优选包括卵磷
脂,更优选为大豆卵磷脂yelkin ts。本发明在水性环氧富锌底漆加入助剂可以改善涂料的分散性、贮存稳定性和施工性。
34.在本发明中,所述流变助剂优选包括有机膨润土,更优选为bentone sd-2有机膨润土(海明斯)或yh-s34有机膨润土(浙江宇宏)。
35.在两种不互溶的液相存在的情况下卵磷脂可降低原料的表面张力,并起到乳化作用;在固相和液相(速溶)之间使用时,卵磷脂起到润湿和分散的作用。因为锌粉密度大,容易沉降,对涂料的贮存和施工时的短期防沉性能提出了更高的要求,本发明采用流变助剂在低搅拌速率下即可有效分散锌粉,而且流变助剂具有良好的颜料悬浮性,良好的贮存稳定性以及良好的抗流挂性和防沉性,不会影响涂料的流动和流平,不需制备预凝胶,不需另外添加活化剂的优点,可在涂料生产过程中任一阶段中使用。在本发明提供的水性环氧富锌底漆中加入分散剂和流变助剂可使涂料分散更均匀,从而提高涂料的贮存稳定性和施工性。
36.本发明对所述分散剂和流变助剂的配比没有特殊的限定,采用任意配比,能够保证助剂的质量份数满足上述要求即可。
37.以所述a组分中环氧树脂的质量份数为基准,本发明提供的水性环氧富锌底漆的a组分包括锌粉65~80份,优选为65~78份,更优选为68~75份。在本发明中,所述锌粉优选包括zmp 4p16(umicore)、fh325锌粉(优美科富虹锌业)或zmp 4p645(umicore),更优选为fh325锌粉;所述锌粉的平均粒径优选为2~9μm,更优选为6~9μm。在本发明提供的平均粒径范围内的锌粉具有减少沉降、减小涂层孔隙率以及提高涂层屏蔽性的效果,不会因锌粉过粗导致整个干膜充满毛刺,影响屏蔽效应和防腐性能。
38.以所述a组分中环氧树脂的质量份数为基准,本发明提供的水性环氧富锌底漆的a组分包括有机溶剂0.2~3.5份,优选为0.8~3.5份;所述有机溶剂优选包括乙二醇单丁醚、异丙醇和丙二醇单甲醚中的一种或几种,更优选为乙二醇单丁醚、异丙醇和丙二醇单甲醚。当溶剂为上述几种时,本发明对不同种类溶剂的配比没有特殊限定,任意配比均可。
39.本发明提供的水性环氧富锌底漆包括b组分;以质量份数计,所述b组分包括水性环氧固化剂20~45份,优选为25~40份。在本发明中,所述水性环氧固化剂优选包括胺类固化剂;更优选包括水性环氧固化剂aradur 38-1(亨斯迈先进化工材料(广东)有限公司)、水性环氧固化剂hongli gh60(弘利)、水性环氧固化剂stw703b(上海华谊精细化工有限公司)、水性环氧固化剂3ec163w(广东彤德新材料有限公司)和水性环氧固化剂aers7013(无锡洪汇新材料科技股份有限公司)中的一种或几种,更优选为水性环氧固化剂aradur 38-1(亨斯迈先进化工材料(广东)有限公司)。本发明所用水性环氧固化剂为多胺加成物的水溶液,不含溶剂,适用于配制金属基材的防腐涂料,具有优异的性能。
40.以所述b组分中水性环氧固化剂的质量份数为基准,所述b组分包括水55~80份,优选为60~75份。
41.在本发明中,所述a组分和b组分的质量比优选为(8.5~12.5):1,更优选为(10.5~12):1。
42.本发明还提供了上述技术方案所述水性环氧富锌底漆的制备方法,包括以下步骤:
43.将环氧树脂、助剂、锌粉和有机溶剂混合,得到a组分;
44.将水性环氧固化剂和水混合,得到b组分。
45.在本发明中,所述环氧树脂、助剂、锌粉和有机溶剂的混合过程优选将助剂加入搅拌状态下的环氧树脂中,分散均匀,然后加入锌粉,分散至细度小于50μm后,用溶剂调整粘度,得到a组分;所述搅拌的速率优选为2000~4000rpm,更优选为3000~3500rpm。
46.在本发明中,所述a组分的粘度优选为100~125ku,更优选为110~125ku。本发明对所述分散的过程没有特殊限定,采用本领域熟知的分散过程即可。
47.本发明对所述水性环氧固化剂和水的混合过程没有特殊限定,采用本领域熟知的混合过程使水性环氧固化剂与水混合均匀即可。
48.本发明提供了上述技术方案所述水性环氧富锌底漆在防腐领域中的应用。
49.在本发明中,所述防腐领域优选包括电力工业领域、海洋工程领域、石油化工领域或基础设施领域。
50.本发明还提供了一种利用水性环氧富锌底漆防腐的方法,包括以下步骤:
51.将a组分和b组分混合后,涂覆在基体表面,进行固化;
52.所述a组分和b组分为上述技术方案所述水性环氧富锌底漆中的a组分和b组分或上述技术方案所述制备方法制备得到的a组分和b组分。
53.在本发明中,所述a组分和b组分混合的方式优选为搅拌,本发明对搅拌的过程没有特殊限定,采用本领域熟知的搅拌过程使a组分和b组分混合均匀即可。
54.本发明优选在进行喷涂前,对所述a组分和b组分混合所得混合物进行稀释来达到施工粘度;所述稀释所用溶液优选为水;所述施工粘度优选为60~80ku,更优选为65~75ku。
55.在本发明中,所述涂覆的方式优选为喷涂;本发明对所述喷涂的过程没有特殊限定,采用本领域熟知的喷涂过程即可。
56.在本发明中,所述固化的温度优选》5℃,更优选为20~30℃;所述固化的时间优选为7d。
57.下面将结合本发明中的实施例,对本发明中的技术方案进行清楚、完整地描述。
58.实施例1~6
59.按照表1的配比,将助剂加入搅拌(3000~3500rpm)状态下的环氧树脂中,分散均匀,加入锌粉,分散至细度小于50μm,用溶剂调整粘度至110~125ku,分散均匀,得到a组分;将水性环氧固化剂与水混合,分散均匀,得到b组分。
60.使用前,按照表1所示的质量比将a组分和b组分混合后,得到水性环氧富锌底漆。
61.对比例1
62.按照表1的配比,将助剂加入搅拌状态下的环氧树脂中,分散均匀,加入锌粉,高速分散至细度小于50μm,用溶剂调整粘度至130ku,分散均匀,得到a组分;将水性环氧固化剂与水混合,分散均匀,得到b组分。
63.使用前,按照表1所示的质量比将a组分和b组分混合,制备得到水性环氧富锌底漆。
64.性能测试
65.将实施例1~6和对比例1得到的水性环氧富锌底漆用水稀释至施工粘度65~75ku,喷涂在钢铁基材的表面,在23℃下固化7d后,进行性能测试。实施例1~6和对比例1提
供的水性环氧富锌底漆的组成、物理参数和漆膜性能见表1。
66.表1实施例1~6和对比例1的水性环氧富锌底漆的原料用量以及涂料性能
67.[0068][0069]
由表1可知,与对比例1相比,本发明通过添加少量的导电助剂,从而降低锌粉的含量,实施例中水性环氧富锌底漆形成的漆膜与对比例相比具有更优异的附着力和耐盐雾性,而耐湿热性和耐化学介质性与对比例一致,由此说明,虽然本发明降低了底漆中锌粉的含量,但在导电助剂与锌粉配合作用下,有利于提高涂层的防腐性能,而不会受到降低锌粉含量的影响。
[0070]
在本发明的水性环氧富锌底漆中,以可用水稀释的双酚a型环氧树脂为基体树脂,配以优化的助剂及锌粉的种类和含量,可明显地改善涂层的物理性能和防腐性能,例如附着力,抗冲击性、耐盐雾性,同时降低锌粉含量。上述原料及配比的优化使得本发明提供的水性环氧富锌底漆具有优越的物理性能和防腐性能,在降低涂料中锌粉含量的同时,提高涂料的贮存稳定性和施工性,提高涂层附着力和耐冲击性,降低能源消耗、减少锌尘造成的环境污染。
[0071]
尽管上述实施例对本发明做出了详尽的描述,但它仅仅是本发明一部分实施例而不是全部实施例,人们还可以根据本实施例在不经创造性前提下获得其他实施例,这些实施例都属于本发明保护范围。
再多了解一些
本文用于企业家、创业者技术爱好者查询,结果仅供参考。