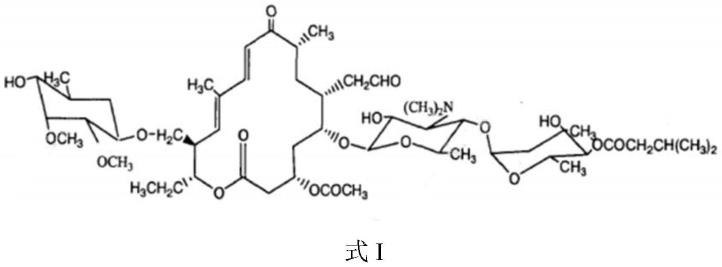
一种改变泰万菌素发酵过程的溶氧以降低4
”‑
氧-异戊酰泰乐菌素组分方法
技术领域
1.本发明涉及一种改变泰万菌素发酵过程的溶氧以降低4
”‑
氧-异戊酰泰乐菌素组分方法,属于发酵技术领域。
背景技术:
2.泰万菌素,又名乙酰异戊酰泰乐菌素(aiv)、3-o-乙酰基-4〞-o-异戊酰基酒石酸盐,其结构如式i所示,是一种禽畜专用的大环内酯类抗生素。作为一种全新的大环内酯类抗生素,泰万菌素克服了其它大环内酯类药物的不足,具有高效、低毒、低残留、不会产生大环内酯类药物间的耐药性等优点,在市场上广受欢迎。
[0003][0004]
现有技术中主要通过添加泰乐菌素和不同的酰基供体的方法己经生产了多种泰乐菌素的衍生物,其中就包括泰乐菌素的第三代升级产品乙酰异戊酰泰乐菌素,即泰万菌素。通过对泰乐菌素的3'-oh和4'-oh位置进行选择性地酰化修饰,合成乙酰异戊酰泰乐菌素基因目前已经阐明包括在泰乐菌素的基础上负责酰化功能的是二个基因acya和acyb,其中acyb包含 bl和b2,其中,基因acya主要负责乙酰基化功能,而基因acyb主要负责异戊酰基化功能, b1基因为负责泰乐菌素4"-oh上的异戊酰化基因,b2为激活b1的正调控基因。其具体的生物合成通路如下所示:
[0005][0006]
aiv的发酵生物合成通路
[0007]
泰万菌素发酵液组分复杂,3-o-乙酰基-4〞-o-异戊酰基泰乐菌素(t2i5)为主要成分,但还含有3-氧-乙酰泰乐菌素(t20)、4
”‑
氧-异戊酰泰乐菌素(t0i5)、3-氧-乙酰-4
”‑
氧-异戊酰雷洛菌素(r2i5)等中间产物,乙酰异戊酰泰乐菌素相关物质如下表所示。
[0008][0009]
目前主要的泰万菌素发酵方法为:发酵罐接种后,ph自然上升到7.50后持续补入酸,控制离线在7.45~7.55之间,当发酵发酵时间在35~45h期间发酵液ph会自然代谢下降至6.9 以下,然后流加补入底物泰乐菌素干粉和l-亮氨酸,再补加葡萄糖溶液使得ph在6.95~7.25 之间,直至发酵完成。现有技术中发酵罐搅拌桨组合一般为三层搅拌,其中底层采用抛物线型搅拌器,中层为直叶圆盘搅拌器,上层采用轴流式搅拌桨。虽然该组合对于能耗、气-液分散效果较高,但不利于发酵的液面控制,当液面表层与上层搅拌接触后容易产生较大泡沫,从进而影响补料和放罐体积。同时现有发酵工艺仅对泰万菌素代谢过程中的t20和t2i5的液相结果进行分析,进而控制下一步的补料速率,但是对于泰万菌素而言,菌丝易受到搅拌等机械应力而断裂产生泡沫,从而影响次级代谢,故体积控制在体积85%以下(上层搅拌附近),随后期发酵液面与上层搅拌接触会加剧发酵液翻滚,造成泡沫快速增大、发酵状态不可控,导致4
”‑
氧-异戊酰泰乐菌素组分含量过高。
技术实现要素:
[0010]
针对现有技术的不足,本发明提供了一种改变泰万菌素发酵过程的溶氧以降低4
”‑
氧
‑ꢀ
异戊酰泰乐菌素组分方法。
[0011]
本发明的技术方案如下:
[0012]
一种改变泰万菌素发酵过程的溶氧以降低4
”‑
氧-异戊酰泰乐菌素组分方法,在以耐热链霉菌为生产菌株在发酵罐中进行泰万菌素的发酵生产,在发酵初期调控发酵液ph至 7.00~7.50,然后流加补入底物泰乐菌素干粉和l-亮氨酸,再补加葡萄糖溶液使得发酵液ph 在6.95~7.25之间,直至发酵完成;
[0013]
整个发酵过程中控制不同发酵时间的溶氧量,在0~35h内控制发酵液的溶氧量在50%以上,在35~70h内控制发酵液溶氧量为20~30%,在70h至放罐期间控制发酵液的溶氧量在70%以上。
[0014]
根据本发明优选的,所述发酵罐包括发酵罐罐体,发酵罐罐体内设置有搅拌装置,搅拌装置下方设置有环形空气分布器;所述环形空气分布器包括环形管和进气管,所述环形管与进气管连通,所述环形管上均匀设置有4个大出气孔,30个小出气孔;所述进气管伸出发酵罐罐体外,发酵罐罐体底部设置有排料口。
[0015]
进一步优选的,所述搅拌装置固定在发酵罐罐体顶端的电机座,电机座上设置有电机,电机侧面连接有减速器,减速器下方依次连接有密封圈、穿过发酵罐顶盖的搅拌轴、联轴器、直叶圆盘搅拌器、中间轴承和抛物线型搅拌器。
[0016]
进一步优选的,所述抛物线型搅拌器和环形空气分布器之间的距离为5~20cm,抛物线型搅拌器宽度和环形空气分布器的直径相同。
[0017]
进一步优选的,所述环形管壁厚φ125*4mm,通过法兰固定在发酵罐上。
[0018]
进一步优选的,所述大出气孔尺寸为φ22mm*4个,小出气孔尺寸为φ18mm*30个。
[0019]
进一步优选的,所述大出气孔和小出气孔的面积之和≤环形管截面积的80%。
[0020]
根据本发明优选的,所述发酵生产中采用的物料培养基配比为:淀粉10~20g/l,酵母膏 1~10g/l,鱼肉浸膏0.1~0.8g/l,k2hpo
4 0.01~0.5g/l。
[0021]
根据本发明优选的,所述发酵初期为采用甘油和柠檬酸的混合物调节ph;
[0022]
进一步优选的,甘油和柠檬酸的质量比为1:1。
[0023]
根据本发明优选的,所述泰乐菌素干粉和l-亮氨酸的质量比为(5~6):1,其中泰乐菌素干粉用量按照800~1000μg/ml加入。
[0024]
有益效果:
[0025]
1、本发明改变了泰乐菌素发酵过程的空气分布形式,有效地控制了不同发酵时间段的溶氧量,解决了泰万菌素因单独搅拌机提高压力造成菌丝老化自溶和泡沫大的问题,有效地降低了发酵液中4
”‑
氧-异戊酰泰乐菌素组分比例,进而提高了发酵液中泰万菌素的组分比例,实现发酵液中泰万菌素组分比例在84%以上。
[0026]
2、本发明改变了传统发酵过程中以直管从发酵罐底部通入空气的方式,去除发酵罐内上层的轴流式搅拌桨,并将直管空气分布器改为环形空气分布器,空气分流后喷射压力提高,空气经过设置有大出气孔和小出气孔的空气分布器出来后,气泡直径要远小于直管喷射型。同时将空气出口向下喷射,当与下层搅拌接触后,会被搅拌桨打碎并在桨叶背面形成“气穴”,当气穴破碎后会形成富集的小气泡区,进一步增加气体与液体的接触面积,提高后期发酵液中溶氧含量。
[0027]
3、本发明去除了上层搅拌,实现单批发酵罐用电量下降5-10%,有效的降低了生产成本。
附图说明
[0028]
图1是本发明发酵罐的结构示意图。
[0029]
图2是本发明环形空气分布器的结构示意图。
[0030]
图3是不同搅拌频次对泰万菌素4
”‑
氧-异戊酰泰乐菌素(t0i5)组分的影响。
[0031]
图4是不同溶氧条件下菌体浓度变化。
[0032]
图5是不同溶氧条件下4
”‑
氧-异戊酰泰乐菌素(t0i5)变化。
[0033]
图6是相同溶氧条件下3-o-乙酰基-4
”‑
o-异戊酰基泰乐菌素(t2i5)变化。
[0034]
图7是不同溶氧条件下效价对比。
[0035]
图中:1、发酵罐罐体,2、电机座,3、电机,4、减速器,5、密封圈,6、发酵罐顶盖, 7、搅拌轴,8、联轴器,9、直叶圆盘搅拌器,10、中间轴承,11、抛物线型搅拌器,12、进气管,13,环形空气分布器,14、出料口,15,环形管,16、大出气孔,17、小出气孔。
具体实施方式
[0036]
下面结合实施例和附图对本发明的技术方案作进一步说明,但是本发明的保护范围并不仅限于此。实施例中涉及的试剂及药品,若无特殊说明,均为普通市售产品;实施例中涉及的实验操作,若无特殊说明,均为本领域常规操作。
[0037]
实施例所用设备均为常规现有设备。
[0038]
实施例中使用的原料,淀粉购自内蒙古托县金河有限公司,葡萄糖购自内蒙古阜丰生物科技有限公司,鱼肉浸膏购自济南亚康力诺生物工程有限公司,泰乐菌素干粉为齐鲁制药(内蒙古)有限公司。
[0039]
如图1~2所示,本发明发酵过程中所使用的发酵罐包括发酵罐罐体1,发酵罐罐体1内设置有搅拌装置,所述搅拌装置包括固定在发酵罐罐体1顶端的电机座2,电机座2上设置有电机3,电机3侧面连接有减速器4。
[0040]
所述减速器4下方依次连接有密封圈5、穿过发酵罐顶盖6的搅拌轴7、联轴器8、直叶圆盘搅拌器9、中间轴承10和抛物线型搅拌器11。所述抛物线型搅拌器11下方10cm处设置有环形空气分布器13;所述环形空气分布器13包括环形管15和进气管12,所述环形管15 与进气管12连通,所述环形管15上均匀设置有4个大出气孔16,30个小出气孔17;所述进气管12伸出发酵罐罐体1外,发酵罐罐体1底部设置有排料口14。
[0041]
所述环形空气分布器13壁厚φ125*4mm,通过法兰固定在发酵罐上。所述大出气孔16 尺寸为φ22mm,小出气孔17尺寸为φ18mm。所述大出气孔16和小出气孔17的面积之和≤环形管15截面积的80%。
[0042]
实施例1
[0043]
一种改变泰万菌素发酵过程的溶氧以降低4
”‑
氧-异戊酰泰乐菌素组分方法,在以耐热链霉菌为生产菌株在发酵罐中进行泰万菌素的发酵生产,在发酵初期采用甘油和柠檬酸的混合物调节调控ph至7.0,流加补入底物泰乐菌素干粉和l-亮氨酸,由于底物的补加,造成代谢改变,发酵ph开始升高,再补加葡萄糖溶液使得发酵液ph至7.2,直至发酵完成;
[0044]
整个发酵过程中结合菌丝生长状况,调节搅拌频次分步控制不同发酵时间的溶氧代谢,其中在0~35h内控制搅拌频次为0-30赫兹,控制发酵液的溶氧量为55%,在35~70h内控制搅拌频次为50赫兹以维持发酵液溶氧量为30%,在70h至放罐期间控制搅拌频次为40-50赫兹发酵液的溶氧量为75%。
[0045]
所述发酵生产中采用的物料培养基配比为:淀粉15g/l,酵母膏5g/l,鱼肉浸膏0.5g/l, k2hpo
4 0.3g/l。所述甘油和柠檬酸的质量比为1:1。
[0046]
所述泰乐菌素干粉和l-亮氨酸的质量比为5:1,其中泰乐菌素干粉用量按照900μg/ml加入。
[0047]
取样测定发酵完成的发酵液,效价为24265μg/ml,泰万菌素(t2i5)的组分比例为84.17%, 4
”‑
氧-异戊酰泰乐菌素(t0i5)的组分比例为4%。
[0048]
实施例2
[0049]
一种改变泰万菌素发酵过程的溶氧以降低4
”‑
氧-异戊酰泰乐菌素组分方法,在以耐热链霉菌为生产菌株在发酵罐中进行泰万菌素的发酵生产,在发酵初期采用甘油和柠檬酸的混合物调节调控ph至7.0,流加补入底物泰乐菌素干粉和l-亮氨酸,然后ph开始升高,再补加葡萄糖溶液使得发酵液ph为7.1,直至发酵完成;
[0050]
整个发酵过程中结合菌丝生长状况,调节搅拌频次分步控制不同发酵时间的溶氧代谢,其中在0~35h内控制搅拌频次为0-30赫兹,控制发酵液的溶氧量为60%,在35~70h内控制搅拌频次为50赫兹以维持发酵液溶氧量为20%,在70h至放罐期间控制搅拌频次为40-50赫兹发酵液的溶氧量为80%。
[0051]
所述发酵生产中采用的物料培养基配比包括:淀粉15g/l,酵母膏5g/l,鱼肉浸膏0.5g/l, k2hpo
4 0.3g/l。所述甘油和柠檬酸的质量比为1:1。
[0052]
所述泰乐菌素干粉和l-亮氨酸的质量比为6:1,其中泰乐菌素干粉用量按照800μg/ml加入。
[0053]
实施例3
[0054]
一种改变泰万菌素发酵过程的溶氧以降低4
”‑
氧-异戊酰泰乐菌素组分方法,在以耐热链霉菌为生产菌株在发酵罐中进行泰万菌素的发酵生产,在发酵初期采用甘油和柠檬酸的混合物调节调控ph至7.2,流加补入底物泰乐菌素干粉和l-亮氨酸,再补加葡萄糖溶液使得发酵液ph为7.0,直至发酵完成;
[0055]
整个发酵过程中结合菌丝生长状况,调节搅拌频次分步控制不同发酵时间的溶氧代谢,其中在0~35h内控制搅拌频次为0-30赫兹,控制发酵液的溶氧量为65%,在35~70h内控制搅拌频次为50赫兹以维持发酵液溶氧量为25%,在70h至放罐期间控制搅拌频次为40-50赫兹发酵液的溶氧量为85%。
[0056]
所述发酵生产中采用的物料培养基配比包括:淀粉15g/l,酵母膏5g/l,鱼肉浸膏0.5g/l, k2hpo
4 0.3g/l。所述甘油和柠檬酸的质量比为1:1。
[0057]
所述泰乐菌素干粉和l-亮氨酸的质量比为6:1,其中泰乐菌素干粉用量按照1000μg/ml 加入。
[0058]
对比例1
[0059]
一种改变泰万菌素发酵过程的溶氧以降低4
”‑
氧-异戊酰泰乐菌素组分方法,具体方法同实施例1,其不同之处在于,保留现有技术中的上层轴流式搅拌桨。
[0060]
取样测定发酵完成的发酵液,效价为20116μg/ml,泰万菌素(t2i5)的组分比例为81.98%, 4
”‑
氧-异戊酰泰乐菌素(t0i5)的组分比例为6.59%。
[0061]
对比例2
[0062]
一种改变泰万菌素发酵过程的溶氧以降低4
”‑
氧-异戊酰泰乐菌素组分方法,具体方法同实施例1,其不同之处在于,调整搅拌频使得发酵过程的0~35h和70h至放罐期间的的溶氧量均为40-60%。
[0063]
取样测定发酵完成的发酵液,效价为22018μg/ml,泰万菌素(t2i5)的组分比例为83.52%, 4
”‑
氧-异戊酰泰乐菌素(t0i5)的组分比例为4.42%。
[0064]
对比例3
[0065]
一种改变泰万菌素发酵过程的溶氧以降低4
”‑
氧-异戊酰泰乐菌素组分方法,具体方法同实施例1,其不同之处在于,调整搅拌频使得发酵过程中全程溶氧量均为20~40%。
[0066]
取样测定发酵完成的发酵液,效价为10708μg/ml,泰万菌素(t2i5)的组分比例为72.25%, 4
”‑
氧-异戊酰泰乐菌素(t0i5)的组分比例为8.24%
[0067]
对比例4
[0068]
一种改变泰万菌素发酵过程的溶氧以降低4
”‑
氧-异戊酰泰乐菌素组分方法,具体
方法同实施例1,保留现有技术中的上层轴流式搅拌桨,调整搅拌频使得发酵过程中全程溶氧量均为0-20%。
[0069]
取样测定发酵完成的发酵液,效价为9164μg/ml,泰万菌素(t2i5)的组分比例为32.36%, 4
”‑
氧-异戊酰泰乐菌素(t0i5)的组分比例为15.11%
[0070]
对比例5
[0071]
采用现有三层搅拌发酵罐发酵生产泰万菌素。
[0072]
具体方法:以耐热链霉菌为生产菌种,在含淀粉、酵母粉、鱼肉浸膏、酵母膏和无机盐的液体发酵培养基中通气搅拌培养,当发酵液ph降7.00~7.20时,开始流加补入底物泰乐菌素干粉以及l-亮氨酸,在发酵过程中后期(100-160h),通过调整搅拌批次40-50赫兹,以调整发酵过程溶氧变化,进行三批次确定发现t0i5的不稳定问题与过程控制降低转速,溶氧不足有直接关系,t0i5与溶氧成负相关性。
[0073]
取样测定01批发酵完成的发酵液,效价为21098μg/ml,泰万菌素(t2i5)的组分比例为82.68%,4
”‑
氧-异戊酰泰乐菌素(t0i5)的组分比例为5.62%
[0074]
实施例1和对比例1~5检测测试结果见下表1和图3~7所示:
[0075]
表1
[0076][0077]
由表1和图3可知,使用现有的三层搅拌发酵罐发酵生产泰万菌素时,在同一个发酵中周期中,空气流量对溶氧的控制效果低,并可能因其泡沫造成发酵控制困难,搅拌转速对溶氧的控制效果最高,通过降低频次会导致溶氧不足,通过三批次实验验证,发现t0i5的不稳定问题与过程控制降低转速,溶氧不足有直接关系,t0i5与溶氧成负相关性。因此控制转速调整发酵过程中溶氧变化可以有效控制异戊酰化途径降低至4.5%以下。本发明实施例1和对比例5相比,采用环管型空气分布器,在不同发酵时间调整空气流量、搅拌速度,以达到控制溶氧水平的方式,并去除上层搅拌叶,有效地降低了4
”‑
氧-异戊酰泰乐菌素组分比例。
[0078]
由图4~7可知,本发明实施例1和对比例2~4相比,通过发酵过程中不同时间段的溶氧量,在不改变补料方式可以明显降低4
”‑
氧-异戊酰泰乐菌素(t0i5)组分、提高3-o-乙酰基
ꢀ‑4”‑
o-异戊酰基泰乐菌素(t2i5)组分和发酵效价。对比例2~4由于过程溶氧控制低,造成泰万菌丝在前期生长较差,整体菌体浓度较低,且可以看出4
”‑
氧-异戊酰泰乐菌素与溶氧控制的明显负相关性。
[0079]
本发明实施例1和对比例1相比,仅更改上层搅拌,但导致在放罐中4
”‑
氧-异戊酰泰乐菌素的组分高出实施例1,也使效价和3-o-乙酰基-4
”‑
o-异戊酰基泰乐菌素的组分均有所下降,其原因为上层搅拌的剪切力使发酵中后期的菌丝破碎较为严重,菌丝出现空泡,并伴随泡沫不可控制的加剧,影响底物的补加。在对比例2中,溶氧的减小控制虽对3-o-乙酰基-4
”‑o‑ꢀ
异戊酰基泰乐菌素组分影响较小,但4
”‑
氧-异戊酰泰乐菌素组分增加,增加了提取工序的难度。
[0080]
因此本发明通过对发酵罐的改造调整,再通过搅拌频次分阶段控制发酵过程的溶氧量,有效地减缓后期菌丝断裂自溶,降低发酵4
”‑
氧-异戊酰泰乐菌素组分含量,提高转化率将放罐总效价提高5%-10%,发酵液aiv组分≥84%,与此同时,上层搅拌叶的去除,实现单批发酵罐用电量下降5-10%,实现经济效益新增。
再多了解一些
本文用于企业家、创业者技术爱好者查询,结果仅供参考。