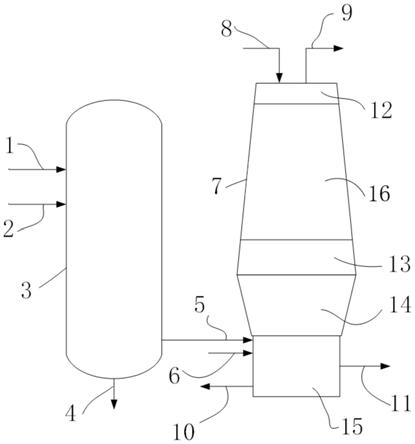
1.本发明涉及一种高炉炼铁的方法。
背景技术:
2.我国钢铁生产的主要流程为高炉-转炉流程,占我国钢铁产量的90%。钢铁产量的高速增长依赖于资源和能源的大量消耗。现有高炉炼铁工艺以焦炭和补吹煤粉为主体燃料的冶炼体系,但该工艺会引起二氧化碳的大量排放与高炉系统的高能耗的问题,极大地影响了炼铁清洁、低碳和高效的发展。作为以碳冶金为本质的钢铁行业,高炉炼铁排放的co2占整个流程的70%。随着我国“碳达峰、碳中和”的实施,钢铁工业在节能、降碳和减排的工作面临着巨大的压力和挑战。
3.传统高炉炼铁操作的研发己发展到相当的高度,传统高炉工艺己趋于成熟,碳消耗与碳排放已接近常规高炉炼铁操作的极限,仅仅依靠现有技术进一步降低能耗、减少co2排放的效果极其有限。全氧高炉的发展提高了高炉煤气热值及冶炼强度,被欧盟“ulcos”项目及日本“course50”项目都列为中长期发展方向。现有的全氧高炉流程有fink、w-k lu、fobf、nkk、ocf和tula等流程,这些流程的主要目的是为解决氧气高炉“上冷下热”问题。全氧高炉主要是将纯氧、煤粉和高品质煤气通过喷嘴喷入到全氧高炉中,高炉的炉顶进料矿石和焦炭。随后,将炉顶煤气的二氧化碳在煤气提质加热炉中转化为co,形成高品质煤气,最后将其再喷入到全氧高炉中。
4.现有的技术也将化工领域常用的气化炉引入氧气高炉冶炼过程。其主要思路是将部分炉顶煤气引入煤气化炉,通过补吹部分粉煤进行煤气重整,再实现煤气加热和再循环。全氧高炉额外增设了煤气提质加热炉,增加了设备消耗和能量消耗。然而,实践结果表明,传统高炉结构在适应全氧冶炼方面仍具有局限性,现有高炉对富氧条件也存在一定上限,目前的煤气化与高炉协同的技术,专利诸如cn200810033923.1、cn201810580363.5、cn201910087997.1等,存在一定的局限性。专利cn201810580363.5公开了一种耦合煤气化实现高炉炼铁工艺碳捕捉的装置及方法,炉膛入口和气化气的入口均被设置于炉腹入口,会导致鼓风动能不足的问题,并且在炉腹部位添加的气化气入口虽能解决热量供给,但是需要较大的能耗提升鼓风动能以及对该部位铁的品质提升效果不明显。此外,传统高炉热风中氧含量的提高会带来热风动能不足的问题,影响高炉炉内分布,而热风量的降低也会带来整体热量不足,出现顶部炉温过低的情况。炉顶温度降低则导致整体还原效率下降,降低了出铁品质,也增加了二氧化碳排放和系统能耗。
5.目前,我国还没有同时对高炉炼铁过程进行降碳、减排及提升煤气品质的技术和工艺,亟需解决该类现状。为了解决上述问题,现有技术在高炉炉身部分增设气体或煤粉喷吹进口,一方面增加了炉身的进口,会增加高炉炉体本身存在的安全风险,另一方面增加了相应的设备和管道,使炉身部位的进口系统变复杂。
技术实现要素:
6.本发明所要解决的技术问题是为了克服现有技术中出铁品质低,能量消耗高、二氧化碳排放量较高的缺陷,而提供了一种高炉炼铁的方法。本发明的高炉炼铁的方法采用气化炉的高温、高压合成气替代热风炉的热风空气和煤粉喷吹,能够提高鼓风动能、有效降低能量消耗、确保出铁品质的同时提升高炉出口煤制品品质并且有效降低高炉吨铁的煤炭消耗量,达到节能减排效果。
7.本发明提供了一种高炉炼铁的方法,所述高炉炼铁的装置包括依次串联的气化炉和高炉;
8.所述高炉炼铁的方法包括以下步骤:
9.s1:通过载气将含碳物料通入所述气化炉中,再将气化剂通入所述气化炉中,发生气化反应,得到合成气;
10.所述含碳物料为煤粉、生物质、天然气、油、含碳的固体废弃物、石油焦和兰炭中的一种或多种;
11.s2:将s1中所述的合成气和纯氧通入高炉中,与燃料和铁矿发生炼铁反应,得到渣水、铁水和气体产物;
12.所述炼铁反应的温度为900~1800℃;所述炼铁反应的压力为0.1~0.4mpa;
13.所述合成气和所述纯氧的通入位置为所述高炉的炉缸和炉腹之间。
14.本发明中,所述的高炉为本领域常规,其由上往下依次包括:炉喉、炉身、炉腰、炉腹和炉缸。
15.s1中,所述载气优选为惰性气体、n2和co2中的一种或多种;进一步优选为n2和/或co2。本发明未使用h2o输送物料,而使用所述载气输送物料,可避免水吸热带走的热量,确保气化的效率并且减少合成气中h2o的含量。
16.s1中,所述含碳物料优选为煤粉,所述煤粉由原料煤经过研磨后得到。
17.s1中,所述含碳物料优选为生物质。
18.s1中,所述气化炉的直径优选为1~5m;进一步优选为1.5~2.0m,例如1.5m或2.0m。
19.s1中,所述气化剂优选为o2,co2,空气和水蒸气中的一种或多种,进一步优选为o2。
20.s1中,所述气化反应的温度一般为900~1500℃,优选为1300~1500℃,例如1450℃或1500℃。
21.s1中,所述气化反应的压力优选为0.5~6.5mpa,进一步优选为常压~6.5mpa;更进一步优选为3.0~6.5mpa,例如3.0mpa或4.0mpa。
22.s1中,所述合成气一般地包括co、h2、co2、载气、含碳固体颗粒和飞灰;所述含碳固体颗粒未经过气化。
23.其中,所述co的体积含量优选占合成气的40~50%。
24.其中,所述h2的体积含量优选占合成气的20~30%。
25.其中,所述co2的体积含量优选占合成气的5~10%。
26.s1中,所述合成气的出口温度优选为900~1500℃,进一步优选为1300~1500℃,例如为1450℃或1500℃。
27.s1中,所述气化反应后一般产生灰渣;使用本领域常规方法,将所述灰渣从所述气
化炉底部的出渣口排出。
28.s2中,所述燃料优选为焦炭和/或粉煤,进一步优选为焦炭和粉煤。
29.其中,当所述燃料为焦炭和粉煤时,所述焦炭和粉煤的质量比优选为1:1。
30.s2中,所述铁矿优选为球团矿、烧结矿和块矿中的一种或多种,进一步优选为烧结矿、球团矿和块矿的混合物。
31.其中,当所述铁矿为烧结矿、球团矿和块矿的混合物时,所述烧结矿、球团矿和块矿的质量比优选为7:2:1。
32.s2中,所述燃料和所述铁矿均可从所述高炉的顶部通入所述高炉中。
33.s2中,所述纯氧的体积分数优选为99.6%。
34.s2中,所述炼铁反应的压力优选为0.15mpa。
35.s2中,所述反应的能量可通过所述纯氧与所述合成气或所述燃料的燃烧提供。
36.s2中,所述渣水可从所述高炉的底部的出渣口排出。
37.s2中,所述铁水可从所述高炉的底部的出铁口排出。
38.s2中,所述铁水优选包括铁和碳。
39.其中,所述铁水的铁含量可为95%以上,例如97%。
40.其中,所述铁水的碳含量可为小于等于3%,例如3%。
41.s2中,所述气体产物可从所述高炉的顶部排出。
42.s2中,所述气体产物可为煤气。
43.其中,所述煤气一般包括co2、co、h2、载气、细铁和飞灰。
44.其中,所述co2的体积含量优选占煤气的50%以上。
45.其中,所述co的体积含量优选占煤气的30%以上。
46.其中,所述h2的体积含量优选占煤气的2%以上。
47.s2中,所述合成气的入口与所述纯氧的入口可水平设置或上下设置。所述水平设置是指设定在同一平面上,合成气的入口与纯氧的入口依次间隔排列;所述上下设置是指合成气的入口与纯氧的入口分层设定。
48.其中,所述纯氧的入口优选设于所述合成气的入口的下方。
49.一较佳的实施例中,所述合成气的入口与所述纯氧的入口水平设置;所述合成气和所述纯氧以间隔式通入所述高炉中。所述间隔式是指合成气的入口与纯氧的入口依次间隔水平排列。
50.s2中,所述合成气和所述纯氧的进料量均可调节。不仅可解决鼓风动能不足的问题,还可以合理调节炉缸和炉腹的热量供给,并确保出铁品质。
51.s2中,所述炉缸的上部设有纯氧入口和合成气入口;所述纯氧入口的氧气量可依据所述合成气入口的合成气量设定,通过调节纯氧入口的氧气量和合成气入口的合成气量来调节合成气温度和纯氧温度。
52.本发明中,所述合成气和所述纯氧均从炉缸和炉腹之间通入高炉中,通过高温高压合成气直接喷入高炉内部,一方面减少了设备数量和降低了设备要求,另一方面解决了鼓风动能不足的问题。若所述合成气和所述纯氧从炉身或炉腰通入,会发生鼓风动能较低,铁矿石还原不充分的问题。
53.本发明中,高炉的进料气体的位置越靠下,进料气体所需的动能越大,从高炉炉缸
和炉腹的位置进料需要较大的鼓风动能,利用气化过程的高温高压合成气,解决了鼓风动能不足的问题。
54.本发明中,所述的高炉炼铁的方法可不使用热风炉。
55.本领域常识的基础上,上述各优选条件,可任意组合,即得本发明各较佳实例。
56.本发明所用试剂和原料均市售可得。
57.本发明的积极进步效果在于:
58.(1)本发明通过高效的气化反应生产高温高压的合成气,既解决了鼓风动能不足的问题,满足高炉鼓风所需的动能,又将高温合成气的能量直接带入气化炉,确保了高炉下部热量以及还原性气体的供给,无需增加额外的煤粉进料口。相同处理能力下,降低能耗。
59.(2)通过本发明的高炉炼铁的方法,利用煤气化合成气替代煤粉喷吹的低能耗高炉炼铁的方法,有效地分离了粉煤纯氧气化和传统高炉冶炼,利用工艺耦合的方式降低流程重构的难度。
60.(3)本发明通过高温合成气和纯氧直接替代热风与粉煤喷吹参与冶炼后,由于入口热风氮气含量降低,出口煤气中的co含量提升显著,对应的煤气热值大幅度上升,煤气利用的回收节能增长。
61.(4)本发明可以不使用热风炉,工艺综合能耗下降显著,高温合成气能够满足高炉炉内温度分布,提升整体还原效率,降低了二氧化碳排放和系统能耗。
62.(5)本发明采用高炉与气化炉耦合,大大简化了设备和系统,减少了高炉炉身入口。另外,本发明采用生物质、含碳固废、石油焦等含碳物料能够大量替代煤炭消耗,确保出铁品质的同时提升煤气品质,降低二氧化碳排放和能耗。
附图说明
63.图1为实施例1的高炉炼铁的方法的装置图。
64.附图标记说明
65.1-含碳物料和载气进口,2-气化剂进口;3-气化炉;4-出渣口;5-合成气通道;6-氧气进口;7-高炉;8-铁矿石和焦炭进口;9-气体产物出口;10-出铁口;11-出渣口;12-炉喉;13-炉腰;14-炉腹;15-炉缸;16-炉身。
具体实施方式
66.下面通过实施例的方式进一步说明本发明,但并不因此将本发明限制在所述的实施例范围之中。下列实施例中未注明具体条件的实验方法,按照常规方法和条件,或按照商品说明书选择。
67.图1为实施例1的高炉炼铁的方法的装置图。
68.实施例1-3中高炉炼铁的方法是在下述装置中进行的:
69.该装置包括:气化炉3和高炉7;气化炉3与高炉7之间通过合成气通道5串联连接,气化炉3设有含碳物料和载气进口1、气化剂进口2和4-出渣口;高炉7设有氧气进口6,铁矿石和焦炭进口8,气体产物出口9,出铁口10和出渣口11。高炉7由上往下依次设有炉喉12、炉身16、炉腰13、炉腹14和炉缸15。合成气通道5的出口与氧气入口均设于炉腹之间,且氧气入口设于合成气入口下方。
70.本发明实施例1-3和对比例1-2使用的原料组成和铁矿成分如表1和表2所示。
71.表1 原料煤的化学组成
[0072][0073]
表2 铁矿的化学成分
[0074][0075]
实施例1
[0076]
s1:载气将含碳物料通过含碳物料和载气进口1进入气化炉3,气化剂通过气化剂进口2进入气化炉3,与含碳物料进行高温高压气化反应,得到高温合成气和灰渣。所得灰渣由出渣口4排出。
[0077]
s2:焦炭和铁矿由铁矿石和焦炭进口8送入高炉7。
[0078]
s3:将s1中的高温合成气由合成气通道5间隔式进入高炉7,氧气通过氧气进口6间隔式进入高炉7中,氧气与合成气或焦炭进行燃烧反应,生成热量供给于铁矿石的还原反应。高温合成气和焦炭与铁矿石发生氧化还原反应,得到渣水、铁水和气体产物,即煤气。所得渣水由出渣口11排出,所得铁水由出铁口10排出,所得煤气由气体产物出口9排出。
[0079]
实施例2
[0080]
采用实例1的高炉炼铁的方法:
[0081]
(1)原料煤经过研磨后得到煤粉,并通过n2输送至气化炉反应,气化炉直径为2.0m。气化反应的压力为4.0mpa,气化反应的温度控制在1500℃,对表1所示的原料煤进行气化。煤粉和氧气在气化炉内反应生成高温合成气和灰渣,合成气包括co、h2和co2,合成气出口温度为1500℃。
[0082]
(2)步骤(1)中得到的高温合成气与体积分数为99.6%的纯氧也通入高炉中,高炉的有效容积为750m3。质量比为7:2:1的烧结矿、球团矿和块矿,燃料(焦炭与粉煤的质量比为1:1)与高温合成气和氧气在高炉中发生氧化还原反应,高炉温度为900-1800℃,高炉压力为0.15mpa,得到煤气、铁水和渣水。
[0083]
本实施例制备得到铁水,其中铁含量为97.0wt.%,碳含量为3.0wt.%,具体成分见表2。
[0084]
实施例3
[0085]
采用实例1的高炉炼铁的方法:
[0086]
(1)将生物质进行气化,并通过n2输送至气化炉反应,气化炉直径为1.5m。气化反应的压力为3.0mpa,气化反应的温度控制在1450℃,对表1所示的原料煤进行气化。煤粉和氧气在气化炉内反应生成高温合成气和灰渣,合成气包括co、h2和co2,合成气出口温度为
1450℃。
[0087]
(2)步骤(1)中得到的高温合成气与体积分数为99.6%的纯氧也通入高炉中,高炉的有效容积为750m3。质量比为7:2:1的烧结矿、球团矿和块矿,燃料(焦炭与粉煤的质量比为1:1)与高温合成气和氧气在高炉中发生氧化还原反应,高炉温度为900-1800℃,高炉压力为0.15mpa,得到煤气、铁水和渣水。
[0088]
本实施例制备得到铁水,其中铁含量为97.0wt.%,碳含量为3.0wt.%,具体成分见表2。
[0089]
实施例2和实施例3的气化炉与高炉的规格、气化炉与高炉的操作参数及效果见数据表3和表4。对比例1为传统高炉工艺。实施例2、实施例3和对比例1均使用有效容积为750m3的高炉。实施例2的气化温度1500℃,压力4.0mpa,采用纯氧。实施例3的气化温度1450℃,压力3.0mpa,采用纯氧。
[0090]
对比例1
[0091]
本对比例不同于实施例2的气化炉制气高炉炼铁的流程,采用表1所示的煤为原料,再采用传统高炉炼铁流程,传统的高炉包含热风炉。高炉的有效容积为750m3。质量比为7:2:1的烧结矿、球团矿和块矿,通过送料车和送料带将矿石与焦由顶部入口送入高炉。采用喷煤与热风方式,将质量比为1:1的焦炭与粉煤送入高炉。空气通过热风炉加热后通过热风炉管与煤粉一起进入高炉,反应生成煤气,后与焦炭、铁矿石料反应,得到粗煤气、铁水和渣水。粗煤气由炉顶煤气管进入净化单元,部分净化煤气用于热风炉加热空气。所得铁水由出铁口排出,所得渣水由出渣口排出。
[0092]
对比例2
[0093]
参照申请公开文本cn108949245a的炼铁工艺,见说明书第[0038]-[0055]段,具体操作如下:
[0094]
(1)空气经过空气分离器,分离产生纯氧,经过预热后的纯氧通入气化炉,将煤通入气化炉中,发生气化反应,气化炉直径为1.5m,气化反应温度1450℃,气化反应压力1.0mpa,得到合成气。
[0095]
(2)将步骤(1)中的纯氧从炉腰通入炼铁高炉,将步骤(1)中的合成气从炉身通入炼铁高炉,再将质量比为7:2:1的烧结矿、球团矿和块矿从高炉顶部加入,将生物质从炼铁高炉的炉腔入口喷入,发生炼铁反应,炼铁反应的温度为900~1800℃,炼铁反应的压力为0.15mpa。
[0096]
表3为实施例2-3和对比例1-2的反应器规格和操作参数。
[0097]
表3 气化炉与高炉的规格以及气化炉与高炉的操作参数
[0098][0099]
[0100]
表4为实施例2-3和对比例1-2的炼铁的产品、产量及能耗。
[0101]
表4 高炉炼铁的产品、产量及能耗
[0102]
煤气成分,vol.%实施例2实施例3对比例1对比例2co37.4625.3024.4424.89co255.1153.3819.2855.38h22.682.351.832.05n20.280.4252.900.32有效气(co h2),vol.%40.1427.6526.2726.94煤气量,nm3804.751147.051703.741297.05铁水含铁量,wt.%97.0097.0097.0097.00铁水含碳量,wt.%3.003.003.003.00铁水产量,ton/天2000.002000.002000.002000.00折算标准煤耗,kj/tfe480.46488.27508.55498.34考虑脱碳后能耗,kj/tfe514.45526.09569.55536.12
[0103]
在相同的铁水产量2000吨/天条件下,本发明实施例2与传统炼铁工艺对比例1均能生产出含铁量97.00wt.%和含碳量3.00wt.%的铁水,但实施例2的气化炉耦合高炉的冶炼系统和冶炼方法大幅提升了煤气中的co含量和h2含量,co含量由24.44%提升至37.46%,h2含量由1.83%提升至2.68%,有效气含量由26.27%提升至40.14%。本发明实施例2的有效气含量较高,由于对比例2的原料用量较大,反应得到的煤气量较高,但该生产工艺得到的有效气含量较低。另外,能耗放折算为标准煤耗由508.55kj/tfe降低至480.46kj/tfe。考虑脱除二氧化碳的能量后,本发明的能耗由569.55kj/tfe降低至514.45kj/tfe。
[0104]
在相同的铁水产量2000吨/天条件下,本发明实施例3与传统炼铁工艺对比例1均能生产出含铁量97.00wt.%和含碳量3.00wt.%的铁水。与对比例1相比,实施例3的气化炉耦合高炉的冶炼系统和冶炼方法提升了煤气中的co含量和h2含量,co含量的24.44%提升至25.30%,h2含量由1.83%提升至2.35%,有效气含量由26.27%提升至27.65%。能耗放折算为标准煤耗由508.55kj/tfe降低至488.27kj/tfe。考虑脱除二氧化碳的能量后,本发明的能耗由569.55kj/tfe降低至526.09kj/tfe。与对比例1相比,实施例3采用的是全部生物质,并没有采用煤炭,确保了铁的产量和有效气的含量、降低了能耗以及达到了较低的碳排放效果。生物质在大自然可以循环,等同于没有在系统里添加化石能源和碳排放。由于采用鼓风炉并通入大量空气,传统高炉生产的煤气中含有大量的n2。
[0105]
在相同的铁水产量2000吨/天条件下,对比例2与传统炼铁工艺对比例1均能生产出含铁量97.00wt.%和含碳量3.00wt.%的铁水。与对比例1相比,对比例2的气化炉耦合高炉的冶炼系统和冶炼方法虽提升了煤气中的co含量和h2含量,co含量的24.44%提升至24.89%,h2含量由1.83%提升至2.05%,有效气含量由26.27%提升至26.94%。能耗放折算为标准煤耗由508.55kj/tfe降低至498.34kj/tfe。考虑脱除二氧化碳的能量后,对比例2降低至536.12kj/tfe。与对比例1相比,对比例2采用的是全部生物质,但与本发明所采用的生物质相比,由于对比例2的操作压力较低,气化的有效气成分降低,且在炉身部位喷入的气化气未能有效提供鼓风动能,所获得的能耗和煤耗较高。本发明实施例3与对比例2在产
出同等品质的铁水时,具有鼓风动能大、折算标煤耗低、排放量低和能耗低的优势。
[0106]
对比例2采用了现有技术的炼铁工艺,该工艺需要先制备高纯氧与气化气,再从炉腰通入纯氧,从炉身通入多股气化气,不但工艺复杂,而且在炉身增加气体入口会增加高炉炉体的安全风险,同时会引起鼓风动能不足。本技术实施例2和实施例3在高炉前增加气化炉,使用气化炉制得的合成气解决了鼓风动能不足的问题,该工艺简单、安全性高,并能达到较好的炼铁效果、提升煤气品质以及降低标准煤耗和脱碳后的能耗。
[0107]
在确保日产钢铁量稳定的同时,本发明的高炉炼铁的方法有效节约了煤炭消耗和降低了能量消耗,并提升了高炉出口的煤气品质及附加值。
[0108]
本发明不局限于上述实施方式,不论在其形状或结构上作任何变化,均落在本发明的保护范围之内。本发明的保护范围是由所附权利要求书限定的,本领域的技术人员在不背离本发明的原理和实质的前提下,可以对这些实施方式做出多种变更或修改,但这些变更和修改均落入本发明的保护范围。
再多了解一些
本文用于企业家、创业者技术爱好者查询,结果仅供参考。