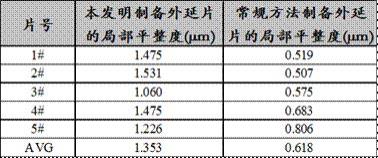
1.本发明属于硅外延生长技术领域,具体涉及一种改善硅外延片背面边缘长硅的方法。
背景技术:
2.硅外延片属于高端装备制造中的印刷电路、电气元件组件领域,是半导体元器件不可缺少的必备元件。
3.受益于市场环境的改变,近两年国内半导体市场发展迅速,半导体相关材料需求日益旺盛。硅外延片是半导体制造链当中极为重要的基础材料,硅外延片的外延层掺杂量、掺杂厚度的控制精度高,硅外延层的金属、氧等杂质含量低,缺陷密度小,电学性能优异。
4.现在,硅外延片制备工艺发展较为成熟,硅外延片的外延层厚度、外延层电阻率的均匀性等控制技术可靠。但是,硅外延片外观方面的问题依然比较严重,主要包括表面颗粒问题、背面长硅问题、表面滑移线问题等。其中,背面长硅问题会严重影响后道的光刻工序,造成光刻聚焦不良,影响后道工序正常流转,严重者会造成硅片报废。
5.硅外延片背面边缘长硅主要在于以下几个方面:第一,硅外延片通过在单晶硅衬底上沉积一层硅外延层得到。单晶硅衬底预先放入高纯石墨基座的片坑中(参见图1及图2、图4及图5),置于耐高温的外延反应腔室。由于石墨基座片坑略大于衬底直径,在沉积过程中,反应气氛不可避免的流入衬底与片坑的间隙当中,硅片边缘以及硅片背面边缘部分区域与反应气氛接触,在高温下沉积一层硅。其中,硅片背面边缘区域沉积的硅会影响硅片边缘的局部平整度,引起后道光刻聚焦不良。
6.第二,石墨基座片坑底部并非一个平面,一般带有向下的弧度设计,硅外延片在生长过程中,由于重力作用,硅片中心部分会发生下沉,参见图3及图8,边缘部分由于石墨基座的支撑作用不会发生下沉,但是边缘部分与基座的接触位置会发生一定位移,硅片与基座接触位置的位移,导致硅片背面裸露在反应气氛中的面积增大,硅片背面边缘长硅的面积相应增大。
7.第三,每一次外延沉积完成之后,都会对反应腔室做一次hcl清洗,通过hcl的高温刻蚀作用,刻蚀掉反应腔室以及基座上沉积的硅。但是,基座上各个位置hcl的刻蚀速率不同,基座表面以及基座片坑内中心区域的刻蚀速率较快,基座片坑内边缘区域的刻蚀速率较慢,基座片坑内边缘区域沉积的硅往往不能刻蚀干净。随着外延沉积过程/反应腔室和基座刻蚀过程的不断重复进行,石墨基座片坑内边缘区域残留硅越来越多(参见图9及图10)。基座片坑内边缘区域残留硅(图10中d为残留硅),高温下与硅片背面接触时,发生化学转移,由基座上转移到硅片背面,也造成了硅片背面边缘长硅。
技术实现要素:
8.本发明实施例提供一种改善硅外延片背面边缘长硅的方法,旨在改善外延片背面边缘长硅的问题,提高后序光刻的质量。
9.为实现上述目的,本发明采用的技术方案是:提供一种改善硅外延片背面边缘长硅的方法,所述方法包括:选用具有特定弯曲度的衬底,所述特定弯曲度为:0μm <bow<30μm ;外延生长前,向外延反应腔室内通入大流量的气态hcl,刻蚀去除外延反应腔室以及基座内沉积的硅;外延生长采用化学气相沉积法,将具有特定弯曲度的衬底放入基座的片坑内,且衬底向远离基座的方向弯曲;外延生长之后,将外延片取出,再次向外延反应腔室通入大流量的气态hcl。
10.在一种可能的实现方式中,所述衬底为重掺sb衬底,晶向《100》,电阻率0.01~0.02ohm.cm。
11.在一种可能的实现方式中,所述衬底背面包覆有sio2层,sio2层的厚度为450-550nm,sio2层边缘去除宽度在1.5-2mm之间。
12.在一种可能的实现方式中,外延生长前,气态hcl刻蚀流量20-40slm,hcl刻蚀时间为常规刻蚀时间的1.5倍-2倍。
13.在一种可能的实现方式中,外延生长过程中,通过感应线圈将反应腔室温度提高到生长温度1040-1050℃,通入硅源以及掺杂源。
14.在一种可能的实现方式中,硅源为sihcl3,纯度99.99%;掺杂源为ph3与h2的混合气,ph3纯度99.9995%。
15.在一种可能的实现方式中,外延生长后,气态hcl刻蚀流量20-40slm,hcl刻蚀时间为常规刻蚀时间的1.5倍-2倍。
16.在一种可能的实现方式中,外延生长采用lpe 3061型多片式外延生长设备。
17.在一种可能的实现方式中,所述基座包覆有sic涂层。
18.在一种可能的实现方式中,所述气态hcl的纯度为99.999%。
19.本发明提供的改善硅外延片背面边缘长硅的方法,与现有技术相比,有益效果在于:选用具有特定弯曲度的衬底,采用多片式外延生长设备,固定合适的外延生长温度区间,外延生长前,通入大流量的气态hcl,刻蚀上次外延生长残留的硅,以保证本次外延生长在比较理想的基座上,改善外延片背面边缘长硅问题;外延生长完成之后,再向外延腔室内通入大流量的气态hcl,清洗外延腔室以及基座,通过大流量的hcl刻蚀作用,将基座片坑内沉积的硅充分去除,再进行下一次外延生长。
20.本发明制备的硅外延片,由于采用了具有特定弯曲度的衬底,及外延生长前后均采用大流量的气体刻蚀清洗,因此可以明显改善硅外延片背面边缘长硅问题,减小硅外延片边缘局部平整度,避免后道光刻聚焦不良问题,满足光刻要求,从而能够提高光刻图形的位置准确性,提高产品的质量。
附图说明
21.图1为常规技术采用的衬底/外延片在基座片坑内的外延前的结构示意图;图2为图1提供的衬底/外延片在基座片坑内的外延前的局部放大图;图3为图1提供的外延生长后的外延片结构示意图;图4为常规技术提供的衬底的主视结构示意图;
图5为图4提供的衬底的侧面结构示意图;图6为本发明实施例采用的衬底/外延片在基座片坑内的结构示意图;图7为图6提供的衬底/外延片在基座片坑内的外延前的局部放大图;图8为图6提供的外延生长后的外延片结构示意图;图9为基座片坑边缘无残留硅的结构示意图;图10为基座片坑边缘有残留硅的结构示意图;图11为常规技术与本发明两种方法获得的边缘硅对比图;图12为常规技术与本发明制备的外延片的边缘硅对比实物图;附图标记说明:1、基座;2、衬底;21、sio2层;22、背面边缘。
具体实施方式
22.为了使本发明所要解决的技术问题、技术方案及有益效果更加清楚明白,以下结合附图及实施例,对本发明进行进一步详细说明。应当理解,此处所描述的具体实施例仅仅用以解释本发明,并不用于限定本发明。
23.请一并参阅图6至图8,现对本发明提供的改善硅外延片背面边缘长硅的方法进行说明。所述改善硅外延片背面边缘长硅的方法,所述方法包括:步骤一,选用具有特定弯曲度的衬底2,特定弯曲度为:0μm <bow<30μm ;(参见图6及图7)步骤二,外延生长前,向外延反应腔室内通入大流量的气态hcl,刻蚀去除外延反应腔室以及基座1内沉积的硅;步骤三,外延生长采用化学气相沉积法,将具有特定弯曲度的衬底2放入基座1的片坑内,且衬底2向远离基座1的方向弯曲;步骤四,外延生长之后,将外延片取出,再次向外延反应腔室通入大流量的气态hcl。
24.本实施例提供的改善硅外延片背面边缘长硅的方法,与现有技术相比,选用具有特定弯曲度的衬底2,采用多片式外延生长设备,固定合适的外延生长温度区间,外延生长前,通入大流量的气态hcl,刻蚀上次生长残留的硅,以保证本次外延生长在比较理想的基座1上,改善外延片背面边缘22长硅问题;外延生长完成之后,再向外延腔室内通入大流量的气态hcl,清洗外延腔室以及基座1,通过大流量的hcl刻蚀作用,将基座1片坑内沉积的硅充分去除,再进行下一次外延生长。
25.本发明制备的硅外延片,由于采用了具有特定弯曲度的衬底2,及外延生长前后均采用大流量的气体刻蚀清洗,因此可以明显改善硅外延片背面边缘22长硅问题,减小硅外延片边缘局部平整度,避免后道光刻聚焦不良问题,满足光刻要求,从而能够提高光刻图形的位置准确性,提高产品的质量。
26.参见图6至图8,这种衬底2向背离基座1方向弯曲的放置方式,在初始生长时,就能够降低衬底2背面边缘22外露的面积;在外延生长过程中,随着外延反应腔室温度的升高以及外延片重量的增大,衬底2的中间部分因自重向下位移,外延片逐渐趋于水平,而衬底2初始水平放置,在外延生长中因自重向下位移,衬底2的中间呈向下凸,而背面边缘22会翘起,
因此,初始向远离基座1方向弯曲的衬底2,相比初始水平放置的衬底2,不会增大衬底2背面边缘22的空间,因此也不会增大背面边缘22长硅的面积,从而避免外延前后硅片形变导致的硅片边缘裸露过多从而引起的背面边缘22长硅。
27.进一步说明的是,由于外延片的背面边缘22长硅,会导致外延片表面边缘的高度不平,产生高度差,高度差的存在,影响光刻聚光的效果,例如,不能聚光,聚光位置不准确,从而导致光刻图形位置的不准确,进而会导致光刻产品的报废,造成严重的后果。
28.本发明主要通过减小硅片边缘裸露量,调整工艺参数,减小硅片形变量,减小基座1内边缘硅残留量的方法,进而减小硅片背面边缘22长硅,本发明改善长硅的方法与与常规方法明显不同。本发明通过控制衬底2的弯曲度,选取合适的外延生长温度,通过大流量的hcl刻蚀基座1,成功避免了外延片背面边缘22长硅问题,减小了外延片边缘的局部平整度,满足了客户光刻的要求。
29.为了更清楚的理解现有技术的衬底2与本发明的具有特定弯曲度的衬底2,针对图示一一对比说明如下:第一、图1提供的现有技术衬底2与基座1的位置关系与图6本发明提供的衬底2与基座1的位置关系对比,可以看出,现有技术衬底2边缘的空间大于特定弯曲衬底2边缘的空间。
30.第二、图2为现有技术给出的局部放大图,图7为本发明给出的局部放大图,通过图2中的b1与图7中的b2做对比,可以看出,外延前现有技术衬底2边缘的空间大于特定弯曲衬底2边缘的空间。
31.第三、图3为现有技术外延后的外延片边缘空间局部放大图,图8为本发明外延后外延片边缘空间的局部放大图,通过图3中的c1与图8中的c2对比,可以看出,外延后现有技术衬底2边缘的空间仍大于弯曲衬底2边缘的空间。
32.第四、图11为常规技术与本发明外延方法制备的外延片的边缘硅对比,图11中常规技术制备的外延片边缘硅密度大,本发明制备的外延片边缘硅密度小。为了便于理解,本发明还提供了常规技术与本发明外延方法制备的外延片的边缘硅实物对比图片,见图12所示,沿常规外延片的边缘是密集分布的边缘硅,沿本发明外延片的边缘是稀疏分布的边缘硅,其中,边缘硅为图12中的亮点,或图11中的黑点。还需要说明的是,图12中的亮色的区域是反光所致,是强光灯照射的反光区域,而如果不对光拍照,则无法照出实物图中的边缘硅对比。
33.通过对比,由于现有技术无论在外延前还是外延过程及外延后,外延片的边缘与基座1之间的空间体积均大于本发明采用特定弯曲衬底2的边缘空间体积,而边缘空间的大小也反映出边缘硅生长的空间及面积的大小。由此可知,本发明采用特定弯曲衬底2,能够减少或避免了外延片背面边缘22长硅问题,减小了外延片边缘的局部平整度,满足了客户后道光刻的要求。
34.在一些实施例中,衬底2为6英寸重掺sb衬底2,晶向《100》,电阻率0.01~0.02ohm.cm。
35.在一些实施例中,衬底2背面包覆有sio2层21,sio2层21的厚度为450-550nm,sio2层21边缘去除宽度a在1.5-2mm之间,如图5所示。
36.在一些实施例中,外延生长前,大流量气态hcl刻蚀流量20-40slm,hcl刻蚀时间为
常规刻蚀时间的1.5倍-2倍,对外延系统进行hcl腐蚀,去除外延反应腔室以及基座1上的沉积硅,避免化学转移引起的背面边缘22长硅。
37.在一些实施例中,外延生长过程中,通过感应线圈将反应腔室温度提高到生长温度1040-1050℃,通入硅源以及掺杂源。通过实际生长温度控制在1040-1050℃之间,减小温度过高硅片形变导致的外延片边缘区域与基座1接触位置的位移量,减小硅片边缘裸露过多导致的背面边缘22长硅。
38.在一些实施例中,硅源为sihcl3,纯度99.99%;掺杂源为ph3与h2的混合气,ph3纯度99.9995%。
39.在一些实施例中,外延生长后,气态hcl刻蚀流量20-40slm,hcl刻蚀时间为常规刻蚀时间的1.5倍-2倍。例如,对于外延层厚度50微米的产品,刻蚀时间一般为12-16min。
40.在一些实施例中,外延生长采用lpe 3061型多片式外延生长设备。
41.在一些实施例中,基座1包覆有sic涂层。本实施例采用lpe 3061型多片式外延生长设备,包覆有sic涂层的高纯石墨基座1位于外延反应腔室的中心,通过位于外延反应腔室底部的感应线圈对石墨基座1加热,从而使外延反应腔室达到最终的设定温度。
42.在一些实施例中,所述气态hcl的纯度为99.999%。
43.本发明在外延生长后,采用uih-3c/3d 超高灰度照明装置(简称强光灯)检验外延片背面长硅情况。采用 ade9600平整度测试仪测试硅片边缘的局部平整度。
44.参见图11及图12,本发明制备外延片与常规方法制备外延片背面边缘22长硅对比,本发明制备的外延片背面边缘22长硅轻微,背面边缘22长硅的密度小,面积小,如图11中b1所示,其中a1为本发明生长的外延片;常规方法制备外延片背面边缘22长硅严重,背面边缘22长硅的密度大,面积大,如图11中b2所示,其中,a2为常规生长的外延片。
45.下表为本发明制备外延片与常规外延片局部平整度数据对比,本发明制备外延片的局部平整度明显好于常规方法制备的外延片:本发明制备外延片的局部平整度1.353μm,常规方法制备外延片的局部平整度0.618μm,本发明的平整度更好,平整度的改善,为光刻的质量奠定了基础。
46.在上述实施例中,对各个实施例的描述都各有侧重,某个实施例中没有详述或记载的部分,可以参见其它实施例的相关描述。
47.以上所述仅为本发明的较佳实施例而已,并不用以限制本发明,凡在本发明的精神和原则之内所作的任何修改、等同替换和改进等,均应包含在本发明的保护范围之内。
再多了解一些
本文用于企业家、创业者技术爱好者查询,结果仅供参考。