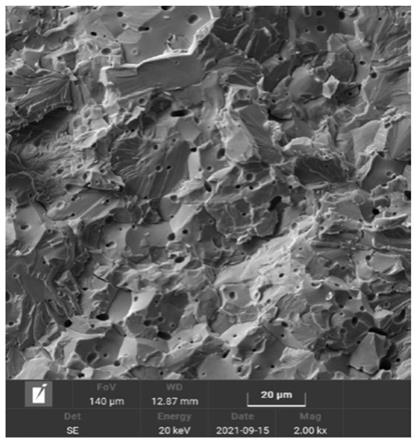
一种wc颗粒增强mo基合金的制备方法及其产品
技术领域
1.本发明属于钼合金材料技术领域,具体涉及一种wc颗粒增强mo基合金的制备方法及其产品。
背景技术:
2.钼合金是一种常用的高温合金,具有许多优异的性能,包括高熔点,高强度,高蠕变和耐腐蚀,低热膨胀系数以及出色的导热性和电子传导性。在航空航天、电子电器、机械加工、军事、冶金等领域都有着非常广泛的应用。随着科学技术的快速发展,因为钼金属材料强度上的不足的原因使其难以满足更高的性能要求。因此,如何制备出高强的新型钼基材料成为必然发展趋势,而通用的手段主要分为成分设计和工艺优化两个方面。
3.目前钼合金研究领域主要有固溶强化钼合金、碳化物掺杂钼合金、氧化物掺杂钼合金和多组元钼合金等。它们在不同的应用领域表现出优越的性能,但同时也存在许多问题,比如成本高、工艺复杂等。所以研究与开发新型钼基材料十分必要和迫切。wc的化学性质稳定,熔点和硬度很高,而且价格相对低廉,来源广泛,已经应用于硬质合金生产领域,但目前尚无研究开发wc增强钼基体复合材料的公开报道。
技术实现要素:
4.本发明的目的是提供一种wc颗粒增强mo基合金的制备方法及其产品,该方法中wc的加入,可以有效地提升钼合金材料的硬度和强度等综合力学性能;而且本发明的方法简单、实用和有效,在钼合金领域有很好的应用前景。
5.本发明这种wc颗粒增强mo基合金的制备方法,包括以下步骤:
6.1)配料:wc颗粒和钼粉按照设定的比例进行称料;
7.2)混料:将步骤1)称量好的原料加入滚筒式罐磨机进行球磨混料,得到混合料;
8.3)压坯:将步骤2)中的混合料置于模具中进行压制,得到坯料;
9.4)烧结:将步骤3)中的坯料置于高温烧结炉中,在氢气气氛下进行烧结,烧结完毕后,随炉冷却至室温,即得wc颗粒增强mo基合金。
10.所述步骤1)中,wc颗粒的质量百分含量为7~14%;余量为钼粉;优选的,wc颗粒的质量百分含量为12%。
11.所述步骤2)中,球磨的球料比为(3~5):1;球磨转速为100~150r/min;混料时间为12~36h。
12.所述步骤3)中,压制压强为150~250mpa。
13.所述步骤4)中,烧结的工艺为:先以14~16℃/min升温至1000℃,高于1000℃时升温速率为8~12℃/min,并在1100℃保温1.5~2.5h,然后继续升温至烧结温度,保温3~5h,烧结完毕后,以8~12℃/min降温至500℃,最后随炉冷却。
14.所述的烧结温度为1700~2000℃。
15.根据上述制备方法制备得到wc颗粒增强mo基合金。
16.本发明的原理:本发明所制造的wc颗粒增强mo基合金,采用常规的烧结方法,在基体材料上添加12%的wc颗粒,具有提高材料硬度和抗拉强度的优点,不同wc颗粒添加量的性能可见具体实施方式中的表1所示。可以明显看到,添加12%的wc颗粒的mo基合金的综合性能较高。不同wc添加量的材料的金相显微组织照片如说明书附图4-8所示,从图中可以看出,随着wc添加量的增多,晶粒逐渐细化。说明在加入wc之后,钼晶粒晶界处分布着的第二相颗粒在烧结过程中,钉扎晶界,阻碍晶界的迁移,防止烧结过程中晶粒进一步长大,从而达到细化晶粒的效果。烧结过程结束后,在钼晶粒晶内或晶界处分布着的第二相颗粒对钼合金还起到第二相强化的作用。因此在细晶强化和第二相强化的双重作用下,位错运动的阻力增大,钼合金的强度得到了显著提高。其中当wc添加量为12%时,晶粒得到了显著的细化而且晶粒大小较为均匀,细小的第二相颗粒均匀地分布在钼基体上,继续增加wc的添加量,晶粒大小均匀程度降低,第二相颗粒变大并且越来越多,对基体的强化效果减弱。
17.本发明的有益效果:1)本发明在mo基体材料上,通过添加不同质量分数的wc颗粒有效提高了材料的硬度和抗拉强度;并且对比性能来优化wc颗粒的加入量,最后确定添加12%wc的mo基合金综合性能最优。2)wc的化学性质稳定,熔点和硬度很高,而且价格相对低廉,来源广泛,但目前尚无研究开发wc增强钼基体复合材料的公开报道。本发明发现wc可以提高钼基体材料的力学性能,起到了明显的强化效果。3)本发明采用的工艺十分简单,适用于工业化的大批量生产,成本得到有效地降低,且材料的性能得到有效的提升,具有良好的经济效益和市场前景。
附图说明
18.图1实施例1中12%wc添加量的钼基合金材料的拉伸试样断口扫描电子显微镜照片。
19.图2实施例1中12%wc添加量的钼基合金材料的拉伸试样断口w元素分布图。
20.图3实施例1中12%wc添加量的钼基合金材料的拉伸试样断口c元素分布图。
21.图4对比例2中3%wc添加量的钼基合金材料的金相显微组织照片。
22.图5实施例2中7%wc添加量的钼基合金材料的金相显微组织照片。
23.图6实施例1中12%wc添加量的钼基合金材料的金相显微组织照片。
24.图7实施例3中14%wc添加量的钼基合金材料的金相显微组织照片。
25.图8对比例3中28%wc添加量的钼基合金材料的金相显微组织照片。
26.图9对比例1中0%wc添加量的纯钼材料的金相显微组织照片。
具体实施方式
27.实施例1
28.按以下比例进行配料:按质量百分比计,碳化钨添加量为12%,余量为钼粉;
29.在滚筒式罐磨机中进行混料,用混料瓶装配好的粉,球料比是4:1,然后以120r/min的转速,混粉24h,得到混合料。
30.将混合料装入模具中,采用电子万能试验机压制成型,压制压力为200mpa,得到压坯。
31.将压坯置于高温烧结炉进行烧结,烧结气氛为氢气;烧结工艺为先以15℃/min升
温至1000℃,高于1000℃时升温速率为10℃/min,在1100℃保温2小时,在1900℃保温4小时,然后以10℃/min降温至500℃,最后随炉冷却;得到wc颗粒增强mo基合金。
32.本实施例制备的wc颗粒增强mo基合金拉伸试样断口微观形貌图如图1所示:可以看出试样断口属于沿晶脆性断裂,晶界轮廓清晰,晶粒均为不规则的多面体状,有少量细小的球形孔洞;本实施例制备的wc颗粒增强mo基合金断口w和c元素分布图分别如图2和3所示:从元素分布图中可以看出元素分布较为均匀弥散,说明在烧结过程中,元素扩散的较为均匀。
33.实施例2
34.与实施例1一致,区别点在于:碳化钨添加量为7%。
35.实施例3
36.与实施例1一致,区别点在于:碳化钨添加量为14%。
37.对比例1
38.所有制备过程中工艺参数与实施例1基本一致,烧结纯钼,不掺杂任何物质。
39.对比例2
40.与实施例1一致,区别点在于:碳化钨添加量为3%。
41.对比例3
42.与实施例1一致,区别点在于:碳化钨添加量为28%。
43.对比例4
44.与实施例1一致,区别点在于:添加物质为金属钨,钨添加量为12%。
45.本发明实施例和对比例制备的钼基合金材料的金相图如图4~9所示,从图中可以看出,随着wc添加量的增多,晶粒逐渐细化。说明在加入wc之后,钼晶粒晶界处分布着的第二相颗粒在烧结过程中,钉扎晶界,阻碍晶界的迁移,防止烧结过程中晶粒进一步长大,从而达到细化晶粒的效果。烧结过程结束后,在钼晶粒晶内或晶界处分布着的第二相颗粒对钼合金还起到第二相强化的作用。因此在细晶强化和第二相强化的双重作用下,位错运动的阻力增大,钼合金的强度得到了显著提高。其中当wc添加量为12%时,晶粒得到了显著的细化而且晶粒大小较为均匀,细小的第二相颗粒均匀地分布在钼基体上,继续增加wc的添加量,晶粒大小均匀程度降低,第二相颗粒变大并且越来越多,对基体的强化效果减弱。
46.上述实施例和对比例制备的钼基合金材料的力学性能如表1所示,从表1可以看出,当wc含量为12%时,获得wc颗粒增强mo基合金性能最优,实施例1与对比例1相比,实施例1中的添加12%wc的mo基合金与纯钼相比,硬度提升约50%,抗拉强度提升约20%;实施例1与对比例2(wc 3%)制备的合金相比,硬度提升约43%,抗拉强度提升约17%;当wc的添加量小于12%时,随着wc含量的增加,钼合金的强度逐渐增加。但是随着wc添加量的继续增加,钼合金的强度反而下降。wc的添加量为12%时,钼合金的综合性能最优。
47.实施例1与对比例4相比,实施例1中的添加12%wc的mo基合金与添加12%w的mo基合金相比,前者的硬度和强度都优于后者。
48.表1 不同wc添加量的材料的性能对比
49.名称wc添加量(%)硬度(hv)抗拉强度(mpa)对比例10162.30488对比例23169.63502
实施例27200.10540实施例112242.74585.5实施例314258.82515.33对比例328343.92506对比例4添加w,12%192.83544
再多了解一些
本文用于企业家、创业者技术爱好者查询,结果仅供参考。