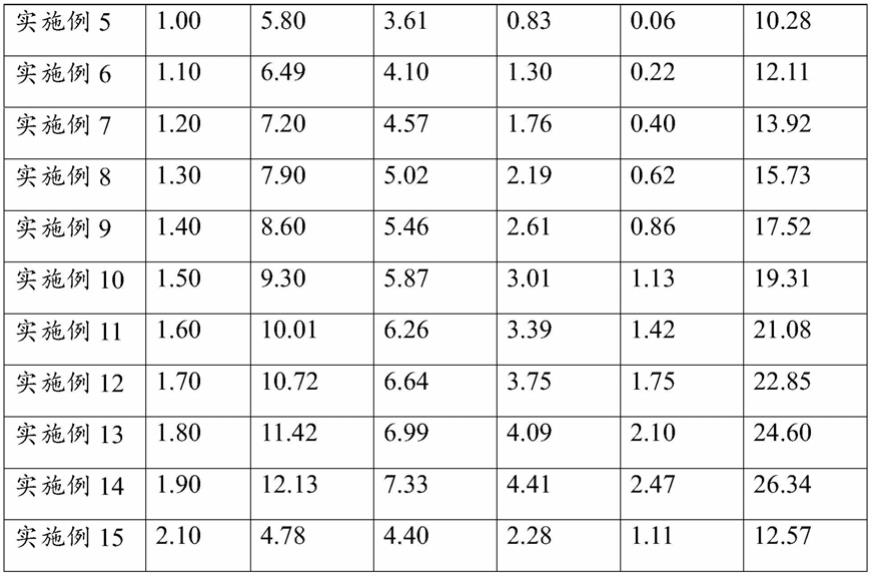
1.本发明涉及钢铁冶炼技术领域,具体而言,涉及一种改善中碳钢表面凹坑麻面的保护渣和方法。
背景技术:
2.中碳钢为c含量在0.25~0.60%之间的钢种,现有技术中,由于中碳钢热收缩系数相对较低、凝固坯壳收缩量较小,现有的保护渣无法有效地控制铸坯与结晶器之间的传热,容易导致铸坯表面凹坑麻面缺陷的形成。
3.鉴于此,特提出本发明。
技术实现要素:
4.本发明的目的之一在于提供一种改善中碳钢表面凹坑麻面的保护渣和方法,其通过优化保护渣的成分,以降低保护渣的熔化速度,提高保护渣的整体粘度,从而充分降低结晶器的卷渣几率,进而有效地降低中碳钢表面凹坑麻面缺陷率。
5.本发明的实施例是这样实现的:
6.第一方面,本发明提供一种改善中碳钢表面凹坑麻面的保护渣,中碳钢含碳量0.25%~0.60%,改善中碳钢表面凹坑麻面的保护渣包括按照重量比的如下成分:
7.sio2:27~32.45,al2o3:12~18,cao:25~29.25,mgo:3.5~6.5,na2o:3.05~3.95,t.c:21~26,f:4~6,其余为水分和不可避免的杂质。
8.在可选的实施方式中,保护渣的熔点为1150℃~1200℃。
9.在可选的实施方式中,保护渣的粘度为0.70~0.80pa.s。
10.在可选的实施方式中,保护渣的碱度r为0.70~0.85,且r=w(cao)/w(sio2);
11.和/或,
12.保护渣的含水量为0.10~0.35%;
13.和/或,
14.保护渣的熔重为0.65~0.70g/ml。
15.第二方面,本发明提供一种改善中碳钢表面凹坑麻面的方法,包括:
16.在连铸过程中采用前述实施方式中任一项的改善中碳钢表面凹坑麻面的保护渣。
17.在可选的实施方式中,中碳钢的化学成分按照质量百分比计包括c:0.25~0.60%,si:0.15~0.35%,mn:0.4~1.25%,p≤0.02%,s≤0.02%,cu ni as sn pb≤0.7%,余量为铁和不可避免的杂质;
18.改善中碳钢表面凹坑麻面的方法还包括在连铸过程中调整二次冷却区的参数,二次冷却区包括足辊区、一区、二区以及三区,调整二次冷却区的参数包括使二次冷却区各区冷却水量q满足公式a
×v2
b
×
v c,其中v为拉速,v的范围为1.0m/min~2.1m/min,a、b以及c按照如下规则选择:
19.足辊区:a:-0.363
±
0.005,b:5.48
±
0.005,c:-2.399
±
0.005;
20.一区:a:-0.377
±
0.005,b:4.606
±
0.005,c:-1.478
±
0.005;
21.二区:a:-0.295
±
0.005,b:3.883
±
0.005,c:-3.793
±
0.005;
22.三区:a:-0.316
±
0.005,b:3.616
±
0.005,c:-4.884
±
0.005。
23.在可选的实施方式中,二次冷却区的二次冷却水比水量:0.55~0.75l/kg;且二次冷却区的各区冷却水量分配满足:
24.足辊区:40~45%、一区:25~27%、二区:14~20%、三区:6~11%;
25.和/或,
26.足辊区的水量≥3m3/h、一区的水量≥2m3/h、二区的水量≥1m3/h、三区的水量≥0.5m3/h。
27.在可选的实施方式中,还包括在连铸过程中调整结晶器的参数,且调整结晶器的参数的过程包括:
28.结晶器的振动频率按照公式f=90 60v计算,v为拉速,v的范围为1.0m/min~2.1m/min,结晶器的振动频率在90~210次/min;
29.和/或,
30.结晶器的振动行程为9~11mm;
31.和/或,
32.结晶器冷却水流量控制在125~135nm3/h;
33.和/或,
34.结晶器的水缝控制在4.0~4.5mm;
35.和/或,
36.结晶器的倒锥度控制在0.16~0.20%/m。
37.在可选的实施方式中,调整结晶器的参数的过程还包括:
38.调整结晶器的电磁搅拌参数至250~350a/3hz;
39.调整末端电磁搅拌参数至300~400a/8hz。
40.在可选的实施方式中,还包括:
41.将连铸过程中的浸入式水口调整为整体式,且浸入式水口与结晶器的对中偏差≤
±
5mm,浸入式水口插入深度90~130mm。
42.本发明的实施例至少具备以下优点或有益效果:
43.本发明的实施例提供了一种改善中碳钢表面凹坑麻面的保护渣,中碳钢含碳量0.25%~0.60%,保护渣包括按照重量比的如下成分:sio2:27~32.45,al2o3:12~18,cao:25~29.25,mgo:3.5~6.5,na2o:3.05~3.95,t.c:21~26,f:4~6,其余为水分和不可避免的杂质。
44.一方面,该保护渣通过充分降低na2o的含量,以有效地降低保护渣的熔化速率,可降低卷渣概率;同时,该保护渣通过充分提高游离碳(t.c)的含量,能与降低na2o含量的操作相辅相成,以进一步地降低保护渣的熔化速率,减少钢液热量损失,减少液态渣,以进一步地降低卷渣概率,从而降低中碳钢表面凹坑麻面缺陷率;另一方面,该保护渣还通过提高al2o3的含量,以提高保护渣的粘度,与降低保护渣熔化速率的操作相辅相成,从而充分提高保护渣的表面张力,进而更进一步地降低卷渣概率,继而进一步地降低中碳钢表面凹坑麻面缺陷率。
45.本发明的实施例还提供了一种改善中碳钢表面凹坑麻面的保护渣的方法,其在连铸过程中采用上述的保护渣。因此,该方法也具有能降低结晶器的卷渣几率,从而有效地降低中碳钢表面凹坑麻面缺陷率的优点。
附图说明
46.为了更清楚地说明本发明实施例的技术方案,下面将对实施例中所需要使用的附图作简单地介绍,应当理解,以下附图仅示出了本发明的某些实施例,因此不应被看作是对范围的限定,对于本领域普通技术人员来讲,在不付出创造性劳动的前提下,还可以根据这些附图获得其他相关的附图。
47.图1为利用对比例1提供的保护渣所制得的部分铸坯的外貌图(图片已做灰度处理);
48.图2为利用本发明的实施例1-4提供的保护渣所制得的部分铸坯的外貌图(图片已做灰度处理);
49.图3为利用本发明的改善中碳钢表面凹坑麻面的保护渣的方法改进前后的对比效果图;
50.图4为利用本发明的实施例19-21提供的电磁搅拌参数的方法改进后的部分铸坯的外貌图。
具体实施方式
51.为使本发明实施例的目的、技术方案和优点更加清楚,下面将对本发明实施例中的技术方案进行清楚、完整地描述。实施例中未注明具体条件者,按照常规条件或制造商建议的条件进行。所用试剂或仪器未注明生产厂商者,均为可以通过市售购买获得的常规产品。
52.现有技术中,由于含量在0.25~0.60%之间的钢种的热收缩系数相对较低、凝固坯壳收缩量较小,因而现有的保护渣无法有效地控制铸坯与结晶器之间的传热,容易导致铸坯表面凹坑麻面缺陷的形成。
53.有鉴于此,发明人对问题进行了分析,发明人发现由于现有技术中提供的保护渣的熔点偏低、粘度偏低,使得现有的保护渣的熔化过快,熔渣过早的裸露在大气中,钢液热量损失大,所以才造成了结晶器上部横断面局部钢液过冷的问题,因而才出现了卷渣现象,使对应的坯壳应缩收而形成凹坑麻面。因此,发明人对保护渣的成分进行了改进,从改善保护渣熔点和粘度为出发点,二者协同有效地改善中碳钢凹坑麻面的缺陷。
54.详细地,本发明的实施例提供的保护渣针对含碳量0.25%~0.60%之间的中碳钢,中碳钢的化学成分按照质量百分比计包括c:0.25~0.60%,si:0.15~0.35%,mn:0.4~1.25%,p≤0.02%,s≤0.02%,cu ni as sn pb≤0.7%,余量为铁和不可避免的杂质。例如,具体可选择为c:0.32~0.37%、si:0.15~0.33%、mn:0.65~0.85、p≤0.025%、s≤0.020%、cr≤0.2%、cu≤0.20%、ni≤0.15%、as≤0.08%、pb≤0.15%、sn≤0.10%。
55.与之对应,保护渣包括按照重量比的如下成分:sio2:27~32.45,al2o3:12~18,cao:25~29.25,mgo:3.5~6.5,na2o:3.05~3.95,t.c:21~26,f:4~6,其余为水分和不可避免的杂质。例如,具体可选择为sio2:30.65,al2o3:13,cao:27.61,mgo:5.0,na2o:3.12,
t.c:22.24,f:5.1,h2o:0.35,fe2o3:0.17。
56.发明人发现对于上述成分的中碳钢而言,其保护渣应该减缓铸坯向结晶器的传热,以使得使铸坯坯壳横向结晶器传热的同时自身不产生表面缺陷,从而达到均匀生长和减缓传热的目的,确保生产合格的中碳钢铸坯。因而,发明人认为对于上述成分的中碳钢而言,保护渣应该选择热阻大,洁净率高的保护渣系。因为保护渣结晶温度高,析出的晶体增多,渣的热阻增大,这样可以达到对初生坯壳缓冷的目的,从而可减少卷渣现象出现,以充分改善凹坑麻面的问题。
57.因而,在本实施例中,一方面,该保护渣通过充分降低na2o的含量,以有效地降低保护渣的熔化速率,可降低卷渣概率,从而能一定程度的降低中碳钢表面凹坑麻面缺陷率;同时,该保护渣通过充分提高游离碳(t.c)的含量,能与降低na2o含量的操作相辅相成,以进一步地提高保护渣的熔点,以降低保护渣的熔化速率,减少钢液热量损失,减少液态渣,以进一步地降低卷渣概率,从而降低中碳钢表面凹坑麻面缺陷率;另一方面,该保护渣还通过提高al2o3的含量,以提高保护渣的粘度,与降低保护渣熔化速率的操作相辅相成,从而充分提高保护渣的表面张力,进而更进一步地降低卷渣概率,继而进一步地降低中碳钢表面凹坑麻面缺陷率。
58.也即,本实施例通过优化保护渣的成分,以降低保护渣的熔化速度,提高保护渣的整体粘度,从而充分降低结晶器的卷渣几率,进而有效地降低中碳钢表面凹坑麻面缺陷率。
59.需要说明的是,除了粘度和熔点,发明人还发现连铸生产中提高保护渣碱度能够增强保护渣的吸附能力,从而能保证连铸质量,减少缺陷形成。因而,在本实施例中,通过同时提高保护渣中cao、mgo含量,能有效地提高保护渣碱度,从而保证保护渣具有较强吸附能力,以保证连铸质量。
60.通过对上述保护渣的成分限定,使得本发明的实施例提供的保护渣的熔点能控制在1150℃~1200℃之间,此熔点明显高于现有技术中保护渣的熔点,使得保护渣的熔化速率明显下降,从而能减少钢液的热量损失,从而能充分降低结晶器卷渣几率,进而能有效地改善中碳钢表面凹坑麻面的现象。
61.同理,通过对上述保护渣的成分限定,使得本发明的实施例提供的保护渣的粘度0.70~0.80pa.s之间,此粘度也明显高于现有技术中保护渣的粘度,使得保护渣的表面张力明显增加,从而能与提高熔点的操作相互相成,以充分降低结晶器卷渣几率,进而能有效地改善中碳钢表面凹坑麻面的现象。
62.可选地,在本发明的实施例中,保护渣的碱度r为0.70~0.85,且r=w(cao)/w(sio2)。将碱度控制在此范围内,使得保护渣具有较强吸附能力,从而能辅助熔点和粘度的操作,以充分保证连铸质量,减少表面缺陷的形成。
63.进一步地,在本发明的实施例中,还可以将保护渣的含水量控制在0.10~0.35%之间。同时,也可以将保护渣的熔重控制在0.65~0.70g/ml之间,以进一步地将保护渣的成分和参数调整为与中碳钢适配,以有效地改善中碳钢表面凹坑麻面的缺陷,保证成品质量。
64.本发明的实施例还提供了一种改善中碳钢表面凹坑麻面的方法,其包括依次进行的转炉——lf精炼——rh或vd——小方坯连铸步骤。其中,转炉终点c含量>0.08%,出钢过程配c含量至目标c含量的85~92%。并且,在连铸过程中可以采用前述实施方式中任一项的改善中碳钢表面凹坑麻面的保护渣作为结晶器的保护渣,以充分减少凹坑麻面缺陷的
形成。
65.可选地,在本发明的实施例提供的改善中碳钢表面凹坑麻面的方法中,除了能利用保护渣的成分进行改善,还能通过对结晶器冷却水量以及二次冷却水量进行优化,以进一步地改善凹坑麻面的缺陷。
66.详细地,可以通过在连铸过程中调整二次冷却区的参数以改善凹坑麻面的缺陷。具体地,二次冷却区包括足辊区、一区、二区以及三区,调整二次冷却区的参数包括使二次冷却区各区冷却水量q满足公式a
×v2
b
×
v c,其中v为拉速,v的范围为1.0m/min~2.1m/min,a、b以及c按照如下规则选择:足辊区:a:-0.363
±
0.005,b:5.48
±
0.005,c:-2.399
±
0.005;一区:a:-0.377
±
0.005,b:4.606
±
0.005,c:-1.478
±
0.005;二区:a:-0.295
±
0.005,b:3.883
±
0.005,c:-3.793
±
0.005;三区:a:-0.316
±
0.005,b:3.616
±
0.005,c:-4.884
±
0.005。
67.在上述过程中,通过对二次冷却区各区冷却水量的控制,能够保证中碳钢拉速控制在1.0m/min~2.1m/min之间,当拉速在此范围内时,能保证铸坯表面无明显裂纹,无明显凹坑麻面,能充分保证铸坯质量。
68.需要说明的是,还可以通过合理分离冷却水量以进一步地改善凹坑麻面的问题,例如可将二次冷却区的二次冷却水比水量控制在0.55~0.75l/kg;且二次冷却区的各区冷却水量分配满足:足辊区:40~45%、一区:25~27%、二区:14~20%、三区:6~11%;足辊区的水量≥3m3/h、一区的水量≥2m3/h、二区的水量≥1m3/h、三区的水量≥0.5m3/h。
69.另外,在本发明的实施例中,还可以通过调整结晶器的参数,以进一步地改善中碳钢铸坯表面凹坑麻面缺陷。例如,在本发明的实施例中,可以将结晶器的振动频率按照公式f=90 60v计算,其中,v为拉速,v的范围为1.0m/min~2.1m/min,结晶器的振动频率在90~210次/min。同时,结晶器的振动行程为9~11mm;结晶器冷却水流量控制在125~135nm3/h;结晶器的水缝控制在4.0~4.5mm;结晶器的倒锥度控制在0.16~0.20%/m。通过这样设置,能辅助保护渣的设计,以充分改善中碳钢铸坯表面凹坑麻面缺陷。
70.除此之外,还能调整结晶器的电磁搅拌参数至250~350a/3hz;调整末端电磁搅拌参数至300~400a/8hz,以保证结晶器处于较优状态,保证铸坯质量,以进一步地改善凹坑麻面的缺陷。同时,还可以将连铸过程中的浸入式水口调整为整体式,且浸入式水口与结晶器的对中偏差≤
±
5mm,浸入式水口插入深度90~130mm,以辅助结晶器参数调整,从而进一步地改善中碳钢铸坯表面凹坑麻面缺陷。
71.下面通过具体地实施例对上述改善中碳钢表面凹坑麻面的保护渣和方法进行详细地说明:
72.实施例1-4以及对比例1
73.实施例1-4以及对比例1提供了一种相同成分的中碳钢,中碳钢的熔炼成分为按照质量百分比计的c:0.32~0.37%、si:0.15~0.33%、mn:0.65~0.85、p≤0.025%、s≤0.020%、cr≤0.2%、cu≤0.20%、ni≤0.15%、as≤0.08%、pb≤0.15%、sn≤0.10%;中碳钢小方坯的连铸生产流程包括转炉——lf精炼——rh或vd——小方坯连铸,转炉终点c含量>0.08%,出钢过程配c含量至目标c含量的85~92%。
74.实施例1-4还提供了一种改善中碳钢表面凹坑麻面的方法,其具体包括在小方坯连铸过程中采用表1所示的保护渣,且表1中的实施例1-4的保护渣的物理指标如表2所示。
对比例1采用的保护渣也如表1所示,物理指标如表2所示。
75.表1.实施例1-4以及对比例1的保护渣的成分
76.成分实施例1实施例2实施例3实施例4对比例1sio2(%)2727.0527.1227.4834al2o3(%)121314122.5cao(%)2525.0326.0525.5824.8mgo(%)3.53.63.53.7/na2o(%)3.053.123.083.058fe2o3(%)0.150.170.160.150.21t.c(%)2121.0521.252215f(%)444.534.124.5h2o(%)0.350.350.30.30.3
77.表2.实施例1-4以及对比例1的保护渣的物理指标
78.指标实施例1实施例2实施例3实施例4对比例1碱度r0.850.860.840.850.43熔点(℃)11501165116011581050容重(g/ml)0.680.690.680.700.60粘度(pa
·
s)0.750.760.750.780.65
79.图1为对比例1提供的保护渣所制得的部分铸坯的外貌图(图片已做灰度处理);图2为利用本发明的实施例2提供的保护渣所制得的部分铸坯的外貌图(图片已做灰度处理);图3为利用本发明的改善中碳钢表面凹坑麻面的保护渣的方法改进前后的对比效果图。根据图1至3可知,利用图1制备得到的铸坯表面存在较多的凹坑麻面,存在较大缺陷,凹坑麻面缺陷率为45%。,从图2与图1的对比可看出铸坯表面无明显裂纹,凹坑麻面显著改善,将0.25%~0.60%钢种表面凹坑麻面缺陷率由之前的45%降低至0.5%以内。
80.实施例5-15以及对比例2
81.实施例5-15提供了一种与实施例1-4成分相同的中碳钢,其区别在于,实施例5-提供的改善中碳钢表面凹坑麻面的方法,具体包括在连铸工艺中,调整二冷区的参数条件,使其处于不同拉速下。其中,实施例5-15中二冷区各区冷却水量q按照a
×v2
b
×
v c,其中v为拉速,a、b以及c表3所示进行选择,实施例5-15中二冷区的拉速以及二冷水量如表4所示。同时,对比例2提供的连铸工艺中,并未进行各区冷却水参数的明确划分,且冷却水140~150m3/h,且二冷水比水量为0.65~0.80l/kg。
82.表3.实施例5-15的二冷区各区冷却水参数
83.二冷各区足辊区一区二区三区a-0.363
±
0.005-0.377
±
0.005-0.295
±
0.005-0.316
±
0.005b5.48
±
0.0054.606
±
0.0053.883
±
0.0053.616
±
0.005c-2.399
±
0.005-1.478
±
0.005-3.793
±
0.005-4.884
±
0.005
84.表4.实施例5-15的二冷区各区拉速以及二冷水量(m3/h)
[0085][0086][0087]
请参阅表3、4以及图3,将对比例2采用对比例1中的保护渣,配套使用结晶器冷却水140~150m3/h,制备得到的铸坯凹坑麻面缺陷率高达45%,漏钢发生率达5%。而采用本实施例5-15所提供的分区参数涉及,能将凹坑麻面缺陷率从45%降至32%左右。若配套本实施例提供的保护渣使用,效果更佳,本实施例不再赘述。
[0088]
实施例16-18以及对比例3
[0089]
实施例16-18以及对比例3提供了一种与实施例1-4成分相同的中碳钢,其区别在于,实施例16-18提供的改善中碳钢表面凹坑麻面的方法,具体包括在连铸工艺中,调整结晶器的参数,调节方式如表5所示。对比例3也采用表5中的数据进行调整。
[0090]
表5.实施例16-18以及对比例3的结晶器参数
[0091][0092]
请参阅表5以及图3,采用本实施例16-18所示的振动参数,能将对比文件3的45%的凹坑麻面缺陷率降至40%左右。若配套本实施例提供的保护渣使用,效果更佳,本实施例不再赘述。
[0093]
实施例19-21以及对比例4
[0094]
实施例19-21以及对比例4提供了一种与实施例1-4成分相同的中碳钢,其区别在于,实施例19-21提供的改善中碳钢表面凹坑麻面的方法,具体包括在连铸工艺中,调整结晶器电磁搅拌的参数,调节方式如表6所示。对比例3也采用表5中的数据进行调整。
[0095]
表6.实施例19-21以及对比例4的电磁搅拌参数
[0096] 结晶器的电磁搅拌参数末端电磁搅拌参数实施例19250a/3hz300a/8hz实施例20300a/3hz350a/8hz实施例21350a/3hz400a/8hz对比例4200a/3hz250a/8hz
[0097]
图4为利用本发明的实施例19-21提供的电磁搅拌参数的方法改进后的部分铸坯的外貌图。请参阅图4、表6以及图3可知,本发明通过调整电磁搅拌参数可以将铸坯表面凹坑麻面发生率从45%降至32%左右,若配套实施例1-15中提供的改善方法,改善效果更佳,此处不再赘述。
[0098]
综上所述,根据图1-4,以及表1-6的数据可知,一方面本发明的实施例通过优化保护渣成分,提高保护渣熔点,降低保护渣熔化速率,提高保护渣粘度,提高保护渣的表面张力,减少钢液热量损失,能有效地降低结晶器卷渣几率,从而改善中碳钢表面凹坑麻面的缺陷。另一方面,本发明的实施例还通过对连铸工艺中的水冷参数,结晶器振动参数以及电磁搅拌参数进行优化,也能有效地改善中碳钢表面凹坑麻面的缺陷,使得小方坯连铸在生产含碳量0.25%~0.60%钢种表面凹坑麻面缺陷率由之前的45%降低至0.5%以内。
[0099]
以上仅为本发明的优选实施例而已,并不用于限制本发明,对于本领域的技术人员来说,本发明可以有各种更改和变化。凡在本发明的精神和原则之内,所作的任何修改、等同替换、改进等,均应包含在本发明的保护范围之内。
再多了解一些
本文用于企业家、创业者技术爱好者查询,结果仅供参考。