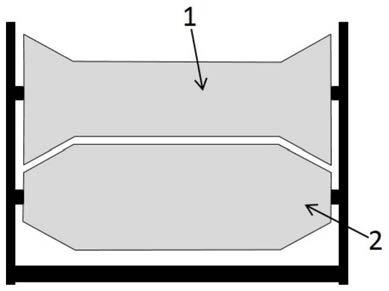
1.本发明属于金属基层状复合材料制备技术领域,特别是提供了一种利用接触反应制备金属层状复合板的方法。
背景技术:
2.金属复合板因兼具不同金属的物理、化学、力学或价格优势而广泛应用于散热、通讯、电力等行业。目前制备金属复合板的方法主要由轧制复合、爆炸复合、固液铸轧复合等。轧制复合法因工艺简单、生产效率高、成本低等特点而广泛应用于工业生产,但是为提高界面结合强度,一般所需轧制变形量较大,对设备能力要求高。爆炸复合法是利用炸药爆炸产生的巨大能量使双金属间瞬间产生高温高压,实现被焊金属的牢固结合。该方法工艺简单,产品尺寸不受限制,但对实验场地的限制较大。固液铸轧复合法是一种以双辊铸轧技术为基础的新技术,利用转动的轧辊对液态金属迅速冷却,使液态金属在固态基板表面形成扩散流动,然后在轧制力的作用下使液态金属在凝固过程中同时发生塑性变形从而制备出双金属复合板。该方法制备出的复合板界面结合强度高,工艺流程短,需要专用设备。综上所述,采用现有方法制备金属层状复合板存在设备要求高、工艺复杂、界面结合强度低等问题,极大影响了金属层状复合板的推广和应用。
3.因此,针对传统工艺方法存在的不足,提出一种利用接触反应制备金属层状复合板的方法,对于制备高界面结合强度金属层状复合板具有重要意义。
技术实现要素:
4.本发明的目的是:提出了一种利用接触反应制备金属层状复合板的方法,通过利用特制冷轧机对板材进行冷轧复合,随后加热中间金属粉末与基层和覆层发生接触反应实现同种/异种金属板的高强度连接。
5.本发明的解决方案如下:在待复合金属板材之间铺覆一层能与待复合金属板材发生共晶反应并生成脆性金属间化合物的金属粉末,然后对组合好的金属板才进行冷轧复合,最后进行加热,金属粉末与基层金属发生接触反应,实现待复合板材间的有效连接。
6.一种利用接触反应制备金属层状复合板的方法,通过在冷轧复合前预置中间层金属粉末获得高界面结合强度金属层状复合板,其包括如下步骤:
7.步骤1:将金属粉末平铺置于真空加热炉中进行加热保温去除粉末表面氧化层,加热时金属粉末应平铺放置,防止金属粉末在加热过程中发生粘结。在室温条件下对待复合的基层金属板和覆层金属板进行清洗,随后打磨待复合表面,使复合表面出现带有凹痕的硬化层,打磨完成后表面呈现出金属亮色,形成的硬化层厚度为10~100μm。
8.步骤2:将金属粉末铺覆在基层金属板表面,铺覆厚度为0.1mm~1mm,随后将覆层金属板置于基层金属板上方进行叠合组坯;
9.步骤3:对组坯进行加压烧结处理,加压方式为配重加压或液压装置加压,在压力和热的作用下金属粉末之间和金属粉末与基层金属板和覆层金属板表面发生粘结,可有效
防止后续冷轧复合时金属粉末在轧辊挤压作用下被挤出复合界面;
10.步骤4:组坯送入凹凸匹配的特制双辊冷轧机进行冷轧复合,使得基层金属板和覆层金属板表面硬化层龟裂,中间层金属粉末嵌入冷轧复合板表面硬化层内,由于铺覆的金属粉末厚度较小,不超过1mm,在冷轧复合时金属粉末因板材长度的增加而分散分布在界面内,得到金属粉末钉扎在界面内的复合界面;
11.步骤5:对冷轧复合板进行加热并保温,使得金属粉与基层金属板和覆层金属板表面发生共晶反应,所产生的共晶金属间化合物的硬度高于基层金属板和覆层金属板,最终形成具有金属间化合物钉扎结构的高界面结合强度金属层状复合板。
12.进一步的,步骤1中所述金属粉末为能与待复合金属板材发生共晶反应并生成高硬度金属间化合物的的单种或多种金属粉末,所述金属粉末粒度≤150目,能够有效防止金属粉末与金属板过度反应而影响金属层状复合板的功能。
13.进一步的,步骤1中所述金属粉末加热温度为其熔点温度的60%~80%,保温时间为30~60min,加热时真空度为10-2
pa及以下,所述金属粉末在上述真空加热时,通过低氧分压和高温使氧化膜分解而去除。
14.进一步的,基层金属和覆层金属为同种或异种的纯金属材料或合金材料,基层金属和覆层金属板宽度≥特制轧辊平行端10mm。
15.进一步的,步骤3所述加压烧结时,压力为1~5mpa,烧结温度为共晶反应温度的60%~90%,保温时间为10~60min,烧结完成后要求金属粉末之间、金属粉末与基层金属和覆层金属之间发生粘接,通过控制上述烧结时的压力和共晶反应温度,以及保温时间,以控制粘接强度,并避免超过冷轧复合变形时的应力,保证板材冷轧复合变形时金属粉末可以发生分离实现分散分布。
16.进一步的,所述特制凹凸匹配的特制双辊冷轧机轧辊两端头为斜面型、波纹型或其他可以实现封边的结构形式。组坯进行冷轧时应居中送入,两侧有宽度≥5mm的组坯位于轧辊封边区,有效防止金属粉末在冷轧时从两侧溢出。
17.进一步的,步骤4中,冷轧速度小于0.1m/s、冷轧变形量大于临界复合变形量,在冷轧复合时,组坯均匀伸长变形,基层和覆层金属板伸长变形表面发生龟裂,同时金属粉末会发生分离,形成金属粉末分散嵌入金属板的复合界面。
18.进一步的,步骤5中加热温度为共晶反应温度至低熔点元素熔化温度,保温时间为15~60min,加热完成后要求金属粉末与基体金属和覆层金属共晶反应生成单层金属间化合物。某些金属之间发生共晶反应时,会生成多种金属间化合物,在加热时一般是优先生成其中一种金属间化合物,随着保温时间的延长,其余种类金属间化合物逐渐在上述金属间化合物与其中一种金属之间生成,金属间化合物为脆性相,且不同金属间化合物之间晶格常数不同,导致金属间化合物层之间的结合强度很低,所以当生成两层或多层金属间化合物时,会显著降低所述金属间化合物钉扎复合界面的结合强度。
19.进一步的,步骤3的覆层金属板上方增加金属粉,并加盖基层金属板,并如此反复叠合,组成复层组坯,所述组坯结构为2~10层。
20.一种金属层状复合板,其由上述的利用接触反应制备金属层状复合板的方法制备而成。
21.本发明具有的优点和有益效果
22.本发明具有的优点和有益效果是:本发明提出了待复合金属板之间预置中间金属粉末后进行特制轧机冷轧 加热的工艺,加热时金属粉与母材金属发生接触共晶反应,在结合界面形成多个焊点及高硬度金属间化合物钉扎结构形式,并通过各环节工艺参数的控制,使得上述界面形式将大大提高复合板界面结合强度,可用于两层或多层板材复合连接,材料适用范围广,操作简单,设备要求低。
附图说明
23.图1为本发明所述高界面结合强度金属层状复合板的制备工艺流程图。其中1为钢丝刷,2为待复合金属,3为中间金属粉末,4为冷轧复合板,5为加热炉。
24.图2为斜面式凹凸匹配轧辊,1为凹辊,2为凸辊。
具体实施方式
25.下面将结合本发明实施例中的附图,对本发明实施例中的技术方案进行清楚、完整地描述,显然,所描述的实施例仅仅是本发明一部分实施例,而不是全部实施例。基于本发明中的实施例,本领域普通技术人员在没有做出创造性劳动前提下所获得的所有其他实施例,都属于本发明保护的范围。
26.本发明提出的金属层状复合板制备方法,利用在待复合金属板之间预置中间金属粉末后进行特制轧机冷轧冷轧 热处理的工艺,在结合界面形成多个焊点及高硬度化合物钉扎结构形式,从而获得高界面结合强度金属层状复合板。相对于传统冷轧复合工艺,所需轧制变相量较低,对设备要求低,界面结合强度高。
27.实施例1:
28.制备3a21铝合金/6063铝合金复合板。
29.步骤1:将粒度为150目的纯铜粉末平铺置于真空加热炉中进行加热保温去除氧化膜,加热温度为1050℃,保温时间为30min,加热时真空度小于1.0
×
10-3
pa。使用在手持式激光清洗设备对3a21铝合金板(长
×
宽
×
厚=200mm
×
50mm
×
1mm)和6063铝合金板(长
×
宽
×
厚=200mm
×
50mm
×
3mm)待复合表面进行清洗,去除表面油污,随后使用丝径为0.3mm的钢丝刷打磨待复合表面形成厚度为10μm的表面硬化层;
30.步骤2:在6063铝合金板待复合表面铺覆厚度为0.2mm的铜粉,随后将3a21铝合金板置于6063铝合金板上方对齐叠合组坯;
31.步骤3:将组坯放入真空扩散焊炉中进行加压加热烧结处理,压力为1mpa,加热温度为400℃,保温时间为20min,加热后得到金属粉末与铝合金板位置相对固定的组坯;
32.步骤4:将叠合后的组坯送入轧速为0.05m/s的装有两端为斜面形轧辊的两辊轧机进行单道次冷轧复合,冷轧变形量为45%,获得铜粉嵌入铝合金板内的冷轧复合界面;
33.步骤5:在空气气氛下对冷轧复合板进行加热,加热温度为500℃,保温时间为30min,铜粉与铝合金板发生共晶反应生成硬度高于铝合金板的金属间化合物cual2,最后空冷至室温获得cual2钉扎在铝合金板内结构形式的高界面结合强度3a21/6063铝合金层状复合板。
34.通过上述步骤获得的3a21铝合金/6063铝合金复合板具有良好的耐腐蚀性,界面结合强度为82mpa,界面结合率为100%。
35.实施例2:
36.制备1060铝合金/6061铝合金/1060铝合金复合板。
37.步骤1:将粒度为200目的纯铜粉末平铺置于真空加热炉中进行加热保温去除氧化膜,加热温度为1100℃,保温时间为20min,加热时真空度小于1.0
×
10-3
pa。使用去油剂清洗1060铝合金板(长
×
宽
×
厚=500mm
×
50mm
×
1mm)和6061铝合金板(长
×
宽
×
厚=500mm
×
50mm
×
3mm)待复合表面油污,随后使用丝径为0.5mm的钢丝刷打磨待复合表面形成厚度为15μm的表面硬化层;
38.步骤2:在1060铝合金板待复合表面铺覆厚度为0.1mm的铜粉,随后将6061铝合金板置于1060铝合金板上方对齐叠合,再在6061铝合金板表面铺覆厚度为0.1mm的铜粉,再将1060铝合金板置于上方对齐叠合组成1060/6061/1060组坯;
39.步骤3:将组坯放入真空扩散焊炉中进行加压加热烧结处理,压力为1mpa,加热温度为350℃,保温时间为30min,加热后得到金属粉末与铝合金板位置相对固定的组坯;
40.步骤4:将叠合后的组坯送入轧速为0.02m/s的装有两端为波纹型轧辊的两辊轧机进行单道次冷轧复合,冷轧变形量为50%,获得铜粉嵌入铝合金板内的冷轧复合界面;
41.步骤5:在空气气氛下对冷轧复合板进行加热,加热温度为500℃,保温时间为30min,铜粉与铝合金板发生共晶反应生成硬度高于铝合金板的金属间化合物cual2,最后空冷至室温获得cual2钉扎在铝合金板内结构形式的高界面结合强度1060/6061/1060铝合金层状复合板。
42.通过上述步骤获得的1060/6061/1060铝合金层状复合板具有优异的的成形性和耐腐蚀性,界面结合强度为75mpa,界面结合率为100%。
43.实施例3:
44.制备304不锈钢/q235碳钢复合板。
45.步骤1:将粒度为150目的钛粉平铺置于真空加热炉中进行加热保温去除氧化膜,加热温度为1100℃,保温时间为60min,加热时真空度小于1.0
×
10-3
pa。使用丙酮清洗304不锈钢板(长
×
宽
×
厚=200mm
×
40mm
×
0.5mm)和q235碳钢板(长
×
宽
×
厚=200mm
×
40mm
×
2mm)待复合表面油污,随后使用丝径为0.5mm的钢丝刷打磨待复合表面形成厚度为10μm的表面硬化层;
46.步骤2:在q235碳钢板待复合表面铺覆厚度为0.5mm的钛粉,随后将304不锈钢板置于对齐叠合组坯;
47.步骤3:将组坯放入真空扩散焊炉中进行加压加热烧结处理,压力为2mpa,加热温度为1000℃,保温时间为30min,加热后得到金属粉末与钢板位置相对固定的组坯;
48.步骤4:将叠合后的组坯送入轧速为0.01m/s的装有两端为波纹型轧辊的两辊轧机进行单道次冷轧复合,冷轧变形量为60%,获得钛粉嵌入钢板内的冷轧复合界面;
49.步骤5:在空气气氛下对冷轧复合板进行加热,加热温度为1200℃,保温时间为30min,钛粉与钢板发生共晶反应生成硬度高于钢板的金属间化合物feti,最后空冷至室温获得feti钉扎在钢板内结构形式的高界面结合强度304不锈钢/q235碳钢层状复合板。
50.通过上述步骤获得的304不锈钢/q235碳钢层状复合板具有优异的的成形性和耐腐蚀性,界面结合强度为102mpa,界面结合率为100%。
51.以上所述,仅为本发明的具体实施例,对本发明进行详细描述,未详尽部分为常规
技术。但本发明的保护范围不局限于此,任何熟悉本技术领域的技术人员在本发明揭露的技术范围内,可轻易想到的变化或替换,都应涵盖在本发明的保护范围之内。本发明的保护范围应以所述权利要求的保护范围为准。
再多了解一些
本文用于企业家、创业者技术爱好者查询,结果仅供参考。