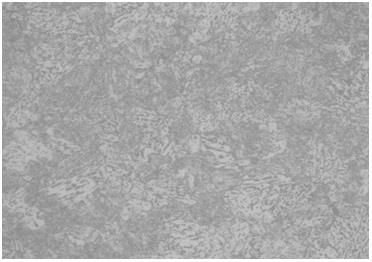
1.55%,p≤0.015%,s≤0.003%,al:0.015-0.035%,nb:0.020-0.035%,ni:0.4-0.5%,b:0.0008-0.0025%,ti:0.008-0.02%,cr:0.4-0.45%,mo:0.4-0.5%,cu:0.25-0.35%, n≤0.0030%,h≤0.00015%,余量为fe和不可避免的杂质,其中,cev≤0.60%。
10.进一步的,所述钢板耐大气腐蚀指数为i,且i≥6.68。
11.本发明还公开了一种大厚度调质q690e/f高强钢板的制造方法,其特征在于:包括冶炼步骤、连铸步骤、加热步骤、轧制及冷却步骤和热处理步骤,其中:1)冶炼:包铁水预处理
→
转炉冶炼
→
lf炉处理
→
rh真空处理;在钢水冶炼过程中,控制p、s、n、h的含量,其质量百分含量为: p≤0.015%,s≤0.003%,n≤0.0030%,h≤0.00015%,lf精炼时间40-50min ,rh真空处理时间为12-18min;2)连铸:控制过热度10-20℃,采用二冷电磁搅拌和凝固末端轻压下,328*2200mm规格铸坯浇铸过程中保持恒拉速,拉速范围为0.6m/min-0.8m/min,中心偏析c类≤1.0;3)加热:加热段温度采用高温1230-1270℃,均热段温度控制在1210-1250℃,铸坯在加热炉内的总加热时间为280-320min,保证铸坯温度均匀;4)轧制及冷却:采用再结晶区 未再结晶区两阶段控轧工艺,第一阶段开轧温度为≥1000℃,累积压下率40-50%且末三道次的单道次压下率15-20%。第二阶段终轧温度为780-820℃,累计压下率为35-45%,末道次采用快速抛钢,抛钢速度2.7-3.2m/s,使钢板快速进入控冷区,避免晶粒长大,采用acc控制冷却方式冷却,钢板终冷温度为600-640℃;5)热处理:淬火加热温度为890-910℃,升温速率为1.5min/mm,在炉时间为230-260min;回火温度为610-630℃,升温速率2.5min/mm,在炉时间310-360min。
12.进一步的:制备的钢板,屈服强度≥750mpa,抗拉强度≥800mpa,延伸率≥17%,-40℃横向冲击功≥150j,
ꢀ‑
60℃横向冲击功≥120j;显微组织为回火索氏体,晶粒度在10级。
13.进一步的:所述钢板的探伤结果满足nb/t 47013-2015标准i级要求。
14.进一步的:所述的cev=c mn/6 (cr mo v)/5 (cu ni)/15, 所述的i=26.01(%cu) 3.88(%ni) 1.20(%cr) 1.49(%si) 17.28(%p)-7.29(%cu)(%ni)-9.10(% ni)(% p)-33.39(%cu)2。
15.本发明的优点在于:1、通过合理的成分体系设计,通过最优的控轧控冷及热处理工艺,所生产100-120mm厚度的q690e及q690 f钢板,各力学性能指标均达到国标gb/t 16270-2009标准要求,其实际生产钢板可达到屈服强度≥750mpa,抗拉强度≥800mpa,延伸率≥17%,-40℃横向冲击功≥150j ,-60℃横向冲击功≥120j;2、该发明所生产的100-120mmq690e/f钢板不仅具有良好的强度和韧性,同时兼具优异的耐大气腐蚀性能,耐大气腐蚀指数为i≥6.68;3、钢板内部组织优良,满足探伤标准nb/t 47013-2015标准i级要求;4、本发明所涉及钢板在工程机械、矿山开采、起重矿车、海洋平台等领域具有较好的应用前景。
附图说明
16.图1 实施例1所述的钢板典型微观组织。
具体实施方式
17.下面结合实施例进一步说明本发明的内容。
18.实施例1一种大厚度调质q690e/f级高强钢板厚度为100mm,钢板的化学成分组成及其质量百分含量为:c:0.11%,si:0.4%,mn:1.4%,p:0.009%,s:0.003%,al:0.015%,nb:0.035%,ni:0.5%,b:0.0008%,ti:0.008%,cr:0.4%,mo:0.5%,cu:0.25%, n:0.002%,h:0.0015%,余量为fe和不可避免的杂质,cev=0.57%。
19.钢板的生产步骤及工艺参数为:1、冶炼:lf精炼时间40min ,rh真空处理时间为15min;2、连铸:过热度10℃,铸坯厚度为328mm,拉速为0.7m/min,中心偏析c类:无;3、加热:加热段最高加热温度1230℃,均热段温度1220℃,铸坯在加热炉内的总加热时间280min;4、轧制及冷却:采用再结晶区 未再结晶区两阶段控轧工艺,第一阶段开轧温度为1050℃,累积压下率40%,末三道次的单道次压下率15%、18%、18%。第二阶段终轧温度为780℃,累计压下率为35%,末道次采用快速抛钢,抛钢速度3.2m/s,钢板终冷温度为640℃;5、热处理:淬火加热温度为890℃,升温速率为1.5min/mm,在炉时间为230min;回火温度为620℃,升温速率2.5min/mm,在炉时间310min。
20.本实施例所得钢板力学性能:屈服强度760mpa,抗拉强度800mpa,延伸率18%,-40℃横向冲击功均值168j ,-60℃横向冲击功均值128j;耐大气腐蚀指数为i=6.6;钢板显微组织为回火索氏体(如图1),晶粒度10级(实施例2-6钢板显微组织图与图1类似,故省略);标准按照nb/t 47013-2015标准探伤i级合格。
21.实施例2一种大厚度调质q690e/f级高强钢板厚度为110mm,钢板的化学成分组成及其质量百分含量为:c:0.12%,si:0.38%,mn:1.45%,p:0.010%,s:0.002%,al:0.020%,nb:0.025%,ni:0.45%,b:0.0008%,ti:0.02%,cr:0.45%,mo:0.4%,cu:0.35%, n:0.001%,h:0.0014%,余量为fe和不可避免的杂质,cev=0.58。
22.钢板的生产步骤及工艺参数为:1、冶炼:lf精炼时间45min ,rh真空处理时间为12min;2、连铸:过热度12℃,铸坯厚度为328mm,拉速为0.7m/min,中心偏析c类:0.5;3、加热:加热段最高加热温度1240℃,均热段温度1210℃,铸坯在加热炉内的总加热时间300min;4、轧制及冷却:采用再结晶区 未再结晶区两阶段控轧工艺,第一阶段开轧温度为1000℃,累积压下率42%,末三道次的单道次压下率16%、18%、18%。第二阶段终轧温度为790℃,累计压下率为38%,末道次采用快速抛钢,抛钢速度2.8m/s,钢板终冷温度为620℃;5、热处理:淬火加热温度为900℃,升温速率为1.5min/mm,在炉时间为235min;回火温度为610℃,升温速率2.5min/mm,在炉时间320mi。
23.本实施例所得钢板力学性能:屈服强度770mpa,抗拉强度860mpa,延伸率17.5%,-40℃横向冲击功均值170j ,-60℃横向冲击功均值125j;耐大气腐蚀指数为i=6.8;标准按照nb/t 47013-2015标准探伤i级合格。
24.实施例3一种大厚度调质q690e/f级高强钢板厚度为120mm,钢板的化学成分组成及其质量百分含量为:c:0.13%,si:0.35%,mn:1.5%,p:0.008%,s:0.002%,al:0.025%,nb:0.028%,ni:0.42%,b:0.0025%,ti:0.01%,cr:0.42%,mo:0.42%,cu:0.28%, n:0.002%,h:0.0012%,余量为fe和不可避免的杂质,cev=0.59。
25.钢板的生产步骤及工艺参数为:1、冶炼:lf精炼时间48min ,rh真空处理时间为15min;2、连铸:过热度18℃,铸坯厚度为328mm,拉速为0.7m/min,中心偏析c类:1.0;3、加热:加热段最高加热温度1240℃,均热段温度1230℃,铸坯在加热炉内的总加热时间310min;4、轧制及冷却:采用再结晶区 未再结晶区两阶段控轧工艺,第一阶段开轧温度为1020℃,累积压下率48%,末三道次的单道次压下率18%、18%、19%。第二阶段终轧温度为790℃,累计压下率为42%,末道次采用快速抛钢,抛钢速度2.7m/s,钢板终冷温度为630℃;5、热处理:淬火加热温度为905℃,升温速率为1.5min/mm,在炉时间为250min;回火温度为620℃,升温速率2.5min/mm,在炉时间350min。
26.本实施例所得钢板力学性能:屈服强度780mpa,抗拉强度890mpa,延伸率21%,-40℃横向冲击功均值180j ,-60℃横向冲击功均值140j;耐大气腐蚀指数为i=6.6;标准按照nb/t 47013-2015标准探伤i级合格。
27.实施例4一种大厚度调质q690e/f级高强钢板厚度为120mm,钢板的化学成分组成及其质量百分含量为:c:0.14%,si:0.25%,mn:1.55%,p:0.012%,s:0.002%,al:0.035%,nb:0.02%,ni:0.4%,b:0.0015%,ti:0.009%,cr:0.4%,mo:0.41%,cu:0.3%, n:0.002%,h:0.0015%,余量为fe和不可避免的杂质,cev=0.60%。
28.钢板的生产步骤及工艺参数为:1、冶炼:lf精炼时间46min ,rh真空处理时间为18min;2、连铸:过热度17℃,铸坯厚度为328mm,拉速为0.7m/min,中心偏析c类:无;3、加热:加热段最高加热温度1260℃,均热段温度1250℃,铸坯在加热炉内的总加热时间310min;4、轧制及冷却:采用再结晶区 未再结晶区两阶段控轧工艺,第一阶段开轧温度为1080℃,累积压下率50%,末三道次的单道次压下率15%、18%、20%。第二阶段终轧温度为820℃,累计压下率为43%,末道次采用快速抛钢,抛钢速度2.8m/s,钢板终冷温度为640℃;5、热处理:淬火加热温度为900℃,升温速率为1.5min/mm,在炉时间为260min;回火温度为630℃,升温速率2.5min/mm,在炉时间360min。
29.本实施例所得钢板力学性能:屈服强度750mpa,抗拉强度815mpa,延伸率20%,-40℃横向冲击功均值150j ,-60℃横向冲击功均值120j;耐大气腐蚀指数为i=6.5;标准按照nb/t 47013-2015标准探伤i级合格。
30.实施例5一种大厚度调质q690e/f级高强钢板厚度为120mm,钢板的化学成分组成及其质量百分含量为:c:0.13%,si:0.3%,mn:1.52%,p:0.015%,s:0.002%,al:0.03%,nb:0.024%,ni:
0.41%,b:0.002%,ti:0.011%,cr:0.41%,mo:0.42%,cu:0.32%, n:0.003%,h:0.001%,余量为fe和不可避免的杂质,cev=0.59%。
31.钢板的生产步骤及工艺参数为:1、冶炼:lf精炼时间50min ,rh真空处理时间为15min;2、连铸:过热度20℃,铸坯厚度为328mm,拉速为0.7m/min,中心偏析c类:1.0;3、加热:加热段最高加热温度1270℃,均热段温度1240℃,铸坯在加热炉内的总加热时间320min;4、轧制及冷却:采用再结晶区 未再结晶区两阶段控轧工艺,第一阶段开轧温度为1080℃,累积压下率50%,末三道次的单道次压下率16%、18%、20%。第二阶段终轧温度为800℃,累计压下率为45%,末道次采用快速抛钢,抛钢速度2.8m/s,钢板终冷温度为600℃;5、热处理:淬火加热温度为910℃,升温速率为1.5min/mm,在炉时间为260min;回火温度为630℃,升温速率2.5min/mm,在炉时间360min。
32.本实施例所得钢板力学性能:屈服强度775mpa,抗拉强度863mpa,延伸率17%,-40℃横向冲击功均值195j ,-60℃横向冲击功均值166j;耐大气腐蚀指数为i≥6.7;标准按照nb/t 47013-2015标准探伤i级合格。
33.实施例6一种大厚度调质q690e/f级高强钢板厚度为120mm,钢板的化学成分组成及其质量百分含量为:c:0.12%,si:0.32%,mn:1.48%,p:0.011%,s:0.003%,al:0.028%,nb:0.026%,ni:0.42%,b:0.001%,ti:0.015%,cr:0.4%,mo:0.5%,cu:0.27%, n:0.002%,h:0.0009%,余量为fe和不可避免的杂质,cev=0.59%。
34.钢板的生产步骤及工艺参数为:1、冶炼:lf精炼时间48min ,rh真空处理时间为13min;2、连铸:过热度13℃,铸坯厚度为328mm,拉速为0.7m/min,中心偏析c类:0.5;3、加热:加热段最高加热温度1260℃,均热段温度1240℃,铸坯在加热炉内的总加热时间320min;4、轧制及冷却:采用再结晶区 未再结晶区两阶段控轧工艺,第一阶段开轧温度为1080℃,累积压下率46%,末三道次的单道次压下率16%、18%、18%。第二阶段终轧温度为810℃,累计压下率为40%,末道次采用快速抛钢,抛钢速度2.8m/s,钢板终冷温度为620℃;5、热处理:淬火加热温度为900℃,升温速率为1.5min/mm,在炉时间为255min;回火温度为620℃,升温速率2.5min/mm,在炉时间350min。
35.本实施例所得钢板力学性能:屈服强度790mpa,抗拉强度859mpa,延伸率21%,-40℃横向冲击功均值182j ,-60℃横向冲击功均值129j;耐大气腐蚀指数为i≥6.5;标准按照nb/t 47013-2015标准探伤i级合格。
36.综上,本发明所述的方案,具有如下优点:1、通过合理的成分体系设计,通过最优的控轧控冷及热处理工艺,所生产100-120mm厚度的q690e及q690 f钢板,各力学性能指标均达到国标gb/t 16270-2009标准要求,其实际生产钢板可达到屈服强度≥750mpa,抗拉强度≥800mpa,延伸率≥17%,-40℃横向冲击功≥150j ,-60℃横向冲击功≥120j;2、该发明所生产的100-120mmq690e/f钢板不仅具有良好的强度和韧性,同时兼具
优异的耐大气腐蚀性能,耐大气腐蚀指数为i≥6.68;3、钢板内部组织优良,满足探伤标准nb/t 47013-2015标准i级要求;4、本发明所涉及钢板在工程机械、矿山开采、起重矿车、海洋平台等领域具有较好的应用前景。
再多了解一些
本文用于企业家、创业者技术爱好者查询,结果仅供参考。