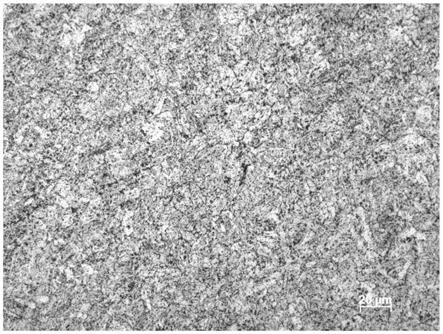
1.本发明涉及一种油套管及其制造方法,尤其涉及一种耐腐蚀的油套管及其制造方法。
背景技术:
2.在油气田生产过程中,注水作业是一种比较常用且高效的工艺,其通过注水井向油层注水,以保持或恢复油层压力,使油藏有较强的驱动力,从而提高油藏的开采速度和采收率。在页岩气井开采中,可以借助高压将大量水、沙子以及化学物质的混合物通过钻孔打入地下,压裂页岩层,使其出现更大更多裂缝,将其中的石油或天然气储备释放出来。
3.从便捷性和经济性考虑,注水作业中大量使用的水一般均是油田附近河水、湖泊水,且采出水经常用来回注重复作业。通常来讲,河水、湖泊水以及采出水中含有较高含量的微生物,尤其是硫酸盐还原菌、腐生菌等。
4.微生物通过附着在材料表面的生物膜中依靠自身生命活动及其代谢产物直接或间接地加速金属材料的腐蚀或破坏,造成很多油气田油套管破漏事故。
5.据报道,美国油井77%以上的腐蚀与微生物腐蚀有关。因此,微生物腐蚀已经严重威胁油气田的管柱服役安全,尤其注水井、页岩气井等。目前,微生物腐蚀防治方法主要有:(1)物理方法,如使用紫外线照射杀菌或对生物膜进行外力刮擦;(2)化学方法,如使用杀菌剂;(3)防护性涂层,如在金属材料表面涂覆抗菌涂层,涂覆防附着的超滑或超疏水涂层使其表面不易被微生物附着;(4)生物防治法,即通过微生物之间的竞争和拮抗等关系来防止微生物腐蚀。化学方法和防护性涂层是油田比较常用的两种方法。采用方法(2)中的杀菌剂,虽然可直接杀死介质中的微生物,但大量使用杀菌剂一方面会污染环境和破坏生态平衡,另一方面会导致微生物的耐药性,导致效果不佳。此外,杀菌剂对浮游的微生物效果较好,对生物膜内的微生物效果欠佳。而方法(3)中的防护性涂层在使用过程中存在两方面问题:(1)油田施工过程中机械损伤、长时间使用老化降解等原因导致涂层脱落,更有助于微生物的附着。同时涂层脱落部位和未脱落部位形成“大阴极-小阳极”电化学腐蚀结构,加速局部腐蚀。(2)油套管是通过螺纹连接,未涂覆涂层的螺纹部位与涂覆涂层的管体之间也会形成“大阴极-小阳极”电化学腐蚀结构,促进腐蚀穿孔。
6.微生物腐蚀主要为硫酸盐还原菌腐蚀,国内外学者已对硫酸盐还原菌腐蚀机理进行了长期研究,其主要腐蚀机理有以下三种:(1)阴极氢去极化:金属在厌氧环境腐蚀过程中阴极会释放大量的氢,但是由于氢的活化电位较高,导致阴极逐渐被一层原子态的氢所覆盖,导致金属的腐蚀发生中断。而硫酸盐还原菌在生命活动过程中,会导致金属表面的氢原子被去除,促进金属继续腐蚀。(2)代谢产物腐蚀:对于金属而言,硫酸盐还原菌在代谢过程中,会产生较多的硫和硫铁化合物,这些都会导致金属表面难以形成有效的保护膜,导致金属的腐蚀速度加快。(3)浓差电池理论:如果油田套管的表面出现了锈蚀之后,其无法与溶解于水中的氧气进行接触,导致管道上被沉积物覆盖的区域呈现阳极,导致金属在水中出现浓差电池,加速了金属上已经存在的腐蚀。以上几种腐蚀机理都有大量证据所支撑。
7.基于硫酸盐还原菌的几种腐蚀机理,生物膜是被业界公认的导致微生物腐蚀的重要因素之一。微生物在材料表面吸附形成的覆盖层称为生物膜。生物膜中的细胞密度比悬浮状态的要高,在较纯的系统中甚至可高出5-6个数量级,相邻位置细胞之间通过长时间接触可能产生生理相互作用,导致协同微生物作用。微生物不仅可将水中组分转变成不溶性的生物质,使之沉积于表面,还可将本身并不沉积的物质带到材料表面形成污垢,为厌氧腐蚀提供场所。此外,生物膜还可以通过分泌促进阴极还原的酶、形成“大阴极-小阳极”电化学腐蚀结构促进微生物腐蚀,进而导致腐蚀穿孔。因此,抑制生物膜在金属表面附着会大大降低局部腐蚀发生,从该角度出发研发具备抑制或消除细菌生物膜附着功能的石油管产品是一种比较好的选择。
8.综上所述,目前油气田采用的微生物腐蚀防治方法有效性均不佳,而通过材料优化开发出耐微生物腐蚀的油套管产品是一种兼顾有效性和便捷性的方法。为避免或减缓微生物腐蚀引起的油套管服役风险,油气田行业迫切希望能获得一种耐微生物腐蚀优异的油套管产品。
9.公开号为cn107400835a,公开日为2017年11月28日,名称为“一种耐硫酸盐还原菌腐蚀用钢、其应用及其制备方法”的中国专利文献,公开了一种耐硫酸盐还原菌腐蚀采油用管产品,其化学元素组成为:c≤0.04%,si 0.1~0.5%,mn≤0.50%,cr 16~24%,cu 0.15~1.5%,al 1.5~3.5%,ce 0.01~0.1%,其余为fe和不可避免的杂质。该专利制造的钢材能有效抵抗外部环境srb腐蚀,且屈服强度大于380mpa,满足j55钢级的要求。该钢材虽具有耐耐硫酸盐还原菌腐蚀性能,但强度较低,不能达到80-95ksi钢级要求;另一方面合金含量较高,成本较高,经济性方面欠佳。
10.公开号为cn109234615a,公开日为2019年1月18日,名称为“一种耐微生物腐蚀油井管用不锈钢及其制造方法”的中国专利文献,公开了一种具有耐微生物腐蚀性能的油井管用不锈钢及其制造方法,其化学元素组成为:c≤0.03%,si 0.1~0.3%,mn≤0.50%,cr 12~14%,ni:4.0~6.0%,mo 1.5~2.5%,cu 1.0~2.0%,ga 0.1~0.8%,ce 0.1~0.2%,s≤0.02%,p≤0.03%,其余为fe和不可避免的杂质。该发明钢可获得较好的强韧性和优异的耐微生物腐蚀性能,可应用于油井管用钢的生产。该专利发明钢材合金含量较高,成本较高,油气田在油套管采购成本方面压力较大。
技术实现要素:
11.本发明的目的之一在于提供一种耐微生物腐蚀的油套管,该耐微生物腐蚀的油套管强度高且耐微生物腐蚀性能优异,其可以有效应用于油气田行业,具有良好的推广前景和应用价值。
12.为了实现上述目的,本发明提供了一种耐微生物腐蚀的油套管,其除了fe以外还含有质量百分比如下的下述化学元素:
13.c:0.12~0.3%,si:0.1~1.5%,mn:0.20~2.5%,ni:0.5~2.0%,cu:0.5~2.5%,mo:0.10~1.0%,v:0.02~0.15%,re:0.05~0.1%。
14.进一步地,在本发明所述的耐微生物腐蚀的油套管中,其各化学元素质量百分比为:
15.c:0.12~0.3%,si:0.1~1.5%,mn:0.20~2.5%,ni:0.5~2.0%,cu:0.5~
2.5%,mo:0.10~1.0%,v:0.02~0.15%,re:0.05~0.1%,余量为fe和其他不可避免的杂质元素。
16.在本发明所述的耐微生物腐蚀的油套管中,各化学元素的设计原理如下所述:
17.c:在本发明所述的耐微生物腐蚀的油套管中,c是保证钢管室温强度和淬透性所必需的成分,适量的c元素可以有效保证钢管的强度和淬透性。若钢中c元素含量低于0.12%时,则钢管的淬透性和强度不够;而当钢管中c元素含量高于0.3%时,会使韧性会变坏。因此,在本发明所述的耐微生物腐蚀的油套管中控制c的质量百分比在0.12~0.3%之间。
18.si:在本发明所述的耐微生物腐蚀的油套管中,si是炼钢过程中重要的脱氧剂,si元素可以有效提高钢管的高温抗氧化和耐酸性能,但若钢管中si元素含量过多,则会降低钢管的韧性和塑性。因此,在本发明所述的耐微生物腐蚀的油套管中控制si的质量百分比在0.1~1.5%之间。
19.mn:在本发明所述的耐微生物腐蚀的油套管中,mn是改善钢的强韧性必需的元素。若钢中mn元素含量低于0.20时,则mn的作用不够明显;而当钢管中mn元素含量高于2.5%时,则易发生偏析,造成最终产品中的明显带状组织,会影响钢管的力学性能。因此,在本发明所述的耐微生物腐蚀的油套管中控制mn的质量百分比在0.20~2.5%之间。
20.ni:在本发明所述的耐微生物腐蚀的油套管中,ni可以明显改善钝化膜性能,提升钢种的耐腐蚀作用。此外,ni还会改善材料的热加工性能。为了使ni元素在本发明中有效发挥其作用,在本发明所述的耐微生物腐蚀的油套管中控制ni的质量百分比在0.5~2.0%之间。
21.在一些优选的实施方式中,为了得到更好的实施效果,ni的质量百分比可以控制在:0.8~2.0%之间。
22.cu:在本发明所述的耐微生物腐蚀的油套管中,cu对微生物具有生物毒性,其能有效提升钢的耐微生物腐蚀性能。在微生物环境中cu离子和富cu相源源不断的释放出,可以保证钢材持久的耐微生物腐蚀性能。但需要注意的是,过量的cu会使得钢在热加工时易产生裂纹。因此,在本发明所述的耐微生物腐蚀的油套管中控制cu的质量百分比在0.5~2.5%之间。
23.在一些优选的实施方式中,为了得到更好的实施效果,cu的质量百分比可以控制在1.0~2.5%之间。
24.mo:在本发明所述的耐微生物腐蚀的油套管中,mo元素可以有效增加钢耐点蚀能力,同时mo元素具有较好的固溶强化效果,有利于提升钢的强度。因此,在本发明所述的耐微生物腐蚀的油套管中控制mo的质量百分比在0.10~1.0%之间。
25.在一些优选的实施方式中,为了得到更好的实施效果,mo的质量百分比可以控制在0.40~1.0%之间。
26.v:在本发明所述的耐微生物腐蚀的油套管中,v元素能够起到细化晶粒,提高钢管强度和韧性的作用。因此,为使v元素有效发挥其有益效果,在本发明所述的耐微生物腐蚀的油套管中控制v的质量百分比在0.02~0.15%之间。
27.在一些优选的实施方式中,为了得到更好的实施效果,v的质量百分比可以控制在0.08~0.15%之间。
28.re:在本发明所述的耐微生物腐蚀的油套管中,稀土元素的添加能够有效提高钢种的韧性,大大改善钢的耐腐蚀性能。但需要注意的是,钢中也不宜添加过量的稀土元素。因此,在本发明所述的耐微生物腐蚀的油套管中控制re的质量百分比在0.05~0.1%之间。
29.进一步地,在本发明所述的耐微生物腐蚀的油套管中,其各化学元素质量百分含量同时满足:1.0%≤[cu%] 2[mo%]≤4.2%。其中,式中的cu和mo均表示相应元素质量百分含量的百分号前的数值。
[0030]
在上述技术方案中,在本发明所述的耐微生物腐蚀的油套管中,在控制单一元素含量的同时,通过控制1.0%≤[cu%] 2[mo%]≤4.2%,可以有效保证本发明所述的耐微生物腐蚀的油套管的优异耐微生物腐蚀性能。
[0031]
进一步地,在本发明所述的耐微生物腐蚀的油套管中,在其他不可避免的杂质中,p≤0.015%,并且/或者s≤0.007%。
[0032]
上述技术方案中,在本发明所述的耐微生物腐蚀的油套管中,p和s均是钢中不可避免的杂质元素,在钢中p和s元素含量越低越好。p是钢中的有害元素,其会对钢的韧性和热加工性能产生不利影响。s元素同样也是使得热加工性能降低并对冲击韧性产生不良影响的有害元素。若钢中s元素的含量超过0.007%,则不能正常制造钢管。因此,在本发明所述的耐微生物腐蚀的油套管中,控制p的质量百分比为p≤0.015%,控制s的质量百分比为s≤0.007%。
[0033]
进一步地,在本发明所述的耐微生物腐蚀的油套管中,其各化学元素质量百分含量满足下述各项的至少其中之一:
[0034]
ni:0.8~2.0%,
[0035]
cu:1.0~2.5%,
[0036]
mo:0.40~1.0%,
[0037]
v:0.08~0.15%。
[0038]
进一步地,在本发明所述的耐微生物腐蚀的油套管中,其微观组织为回火索氏体。
[0039]
进一步地,在本发明所述的耐微生物腐蚀的油套管中,其性能满足下述各项的至少其中之一:其屈服强度为552mpa~758mpa,至少0℃下的全尺寸冲击功≥140j;其在硫酸盐还原菌和腐生菌环境下的均匀腐蚀速率<0.08mm/a,局部腐蚀速率<0.2mm/a。
[0040]
相应地,本发明的另一目的在于提供一种耐微生物腐蚀的油套管的制造方法,采用该制造方法制得的耐微生物腐蚀的油套管的屈服强度为552mpa~758mpa,至少0℃下的全尺寸冲击功≥140j;其在硫酸盐还原菌和腐生菌环境下的均匀腐蚀速率<0.08mm/a,局部腐蚀速率<0.2mm/a,具有优异的耐微生物腐蚀的特性。
[0041]
为了实现上述目的,本发明提出了上述的耐微生物腐蚀的油套管的制造方法,包括步骤:
[0042]
(1)制得管坯;
[0043]
(2)轧制荒管;
[0044]
(3)淬火 回火:将钢管加热到920~980℃,保温0.5~1.5h,再进行水冷或油冷;控制回火温度为615℃~680℃;
[0045]
在本发明所述的耐微生物腐蚀的油套管的制造方法中,通过对工艺条件尤其是热处理工艺参数的控制,使得采用本发明所述的制造方法所制得的耐微生物腐蚀的油套管微
观组织为回火索氏体,以保证本发明的耐微生物腐蚀的油套管具有优异的性能。
[0046]
进一步地,在本发明所述的制造方法中,在步骤(2)中,将管坯加热到1100~1280℃,保持1~3h后,经穿孔、连轧、张力减径或张力定径制得荒管。
[0047]
进一步地,在本发明所述的制造方法中,在步骤(2)中,控制终轧温度为900℃以上,以使得终轧结束时管子为全奥氏体组织。
[0048]
本发明所述的耐微生物腐蚀的油套管及其制造方法相较于现有技术具有如下所述的优点以及有益效果:
[0049]
综上所述可以看出,本发明所述的耐微生物腐蚀的油套管通过合理的化学成分设计,配合特定的变形和热处理工艺获得具有一定强度的回火索氏体组织。该耐微生物腐蚀的油套管屈服强度为552mpa~758mpa,至少0℃下的全尺寸冲击功≥140j;其在硫酸盐还原菌和腐生菌环境下的均匀腐蚀速率<0.08mm/a,局部腐蚀速率<0.2mm/a,具有较高的强度以及优异的耐生物腐蚀性能。
[0050]
此外,本发明所述的耐微生物腐蚀的油套管钢化学成分简单,且经济成本低廉,具有良好的推广前景和应用价值。
附图说明
[0051]
图1为实施例1的耐微生物腐蚀的油套管的金相组织图。
具体实施方式
[0052]
下面将结合具体的实施例和说明书附图对本发明所述的耐微生物腐蚀的油套管及其制造方法做进一步的解释和说明,然而该解释和说明并不对本发明的技术方案构成不当限定。
[0053]
实施例1-7和对比例1-4
[0054]
实施例1-7的耐微生物腐蚀的油套管和对比例1-4的油套管均采用以下步骤制得:
[0055]
(1)按照表1所示的化学成分进行冶炼并制得φ300mm圆管坯;
[0056]
(2)轧制荒管:将管坯加热到1100~1280℃,保持1~3h后,经穿孔、连轧、张力减径或张力定径制得荒管。控制终轧温度为900℃以上,以保证终轧结束时管子为全奥氏体组织;
[0057]
(3)淬火 回火:将钢管加热到920~980℃,保温0.5~1.5h,再进行水冷或油冷;控制回火温度为615℃~680℃。
[0058]
表1列出了实施例1-7的耐微生物腐蚀的油套管和对比例1-4的油套管中各化学元素质量百分比。
[0059]
表1.(wt%,余量为fe和其他除了p、s以外的不可避免的杂质)
[0060]
[0061][0062]
表2列出了实施例1-7的耐微生物腐蚀的油套管和对比例1-4的油套管的具体工艺参数。
[0063]
表2.
[0064][0065]
将制得的规格为φ127*12.7的实施例1-7的耐微生物腐蚀的油套管和对比例1-4的油套管进行各项性能测试,所得的测试结果列于表3中,具体测试方式如下:
[0066]
(1)测试屈服强度:
[0067]
将制成的实施例和对比例的油套管加工成api弧形试样,按api标准检验后取平均数得出各油套管屈服强度的数据。
[0068]
(2)测试全尺寸夏比v型冲击吸收功:
[0069]
在制成的实施例和对比例的油套管上取截面积为10*10*55全尺寸v型冲击试样,按gb/t 229标准检验后取平均数得出各油套全尺寸夏比v型冲击吸收功数据。
[0070]
(3)测试腐蚀速率:
[0071]
在硫酸盐还原菌环境进行腐蚀试验,将试样浸入容器中液体,控制温度为35℃,硫酸盐还原菌浓度为50000个/ml,腐生菌浓度10000个/ml,控制试验时间为240h,试验完成后,对比试验前后的试样重量,通过计算便可以得出均匀腐蚀速率。再对点蚀坑进行截面分析计算便可得到局部腐蚀速率。
[0072]
表3列出了实施例1-7的耐微生物腐蚀的油套管和对比例1-4的油套管的性能测试
结果。
[0073]
表3.
[0074][0075]
由表3可看出,相较于对比例1-4,本发明各实施例的性能更优,各实施例的屈服强度rt
0.5
均在552mpa~758mpa范围之间,至少0℃下的全尺寸冲击功均≥140j,各实施例在硫酸盐还原菌和腐生菌环境下的均匀腐蚀速率均<0.08mm/a,局部腐蚀速率均<0.2mm/a。各实施例的耐微生物腐蚀的油套管的各项性能十分优异,不仅具有较高的强度,还具有优异的耐微生物腐蚀性能。
[0076]
图1为实施例1的耐微生物腐蚀的油套管的金相组织图。
[0077]
如图1所示,在实施例1的耐微生物腐蚀的油套管中,其微观组织为其微观组织为回火索氏体。
[0078]
综上所述可以看出,本发明所述的耐微生物腐蚀的油套管通过合理的化学成分设计,配合特定的变形和热处理工艺获得具有一定强度的回火索氏体组织,不仅具有较高的强度,还具有优异的耐生物腐蚀性能。
[0079]
此外,本发明所述的耐微生物腐蚀的油套管化学成分简单,且经济成本低廉,具有良好的推广前景和应用价值。
[0080]
需要说明的是,本发明的保护范围中现有技术部分并不局限于本技术文件所给出的实施例,所有不与本发明的方案相矛盾的现有技术,包括但不局限于在先专利文献、在先公开出版物,在先公开使用等等,都可纳入本发明的保护范围。
[0081]
此外,本案中各技术特征的组合方式并不限本案权利要求中所记载的组合方式或是具体实施例所记载的组合方式,本案记载的所有技术特征可以以任何方式进行自由组合或结合,除非相互之间产生矛盾。
[0082]
还需要注意的是,以上列举的仅为本发明的具体实施例,显然本发明不限于以上实施例,随之有着许多的类似变化。本领域的技术人员如果从本发明公开的内容直接导出或联想到的所有变形,均应属于本发明的保护范围。
再多了解一些
本文用于企业家、创业者技术爱好者查询,结果仅供参考。