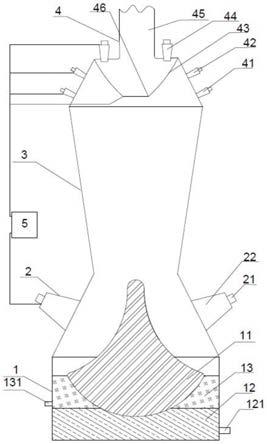
1.本发明属于冶金的技术领域,涉及一种含铁粉料在还原性气氛中直接炼钢装置及使用方法。
背景技术:
2.炼焦 烧结/球团
→
高炉
→
转炉是目前粗钢生产的主要流程,该流程集烧结(或球团)、炼焦、高炉炼铁和转炉氧化炼钢四个工艺环节,具有生产流程长、能耗高、依赖焦炭资源而对环境污染严重等缺点。在当前全球环境污染和资源、能源短缺问题愈演愈烈之际,实行节能减排、推行清洁生产已成为全球钢铁工业持续发展的必由之路。
3.传统炼钢工艺采用氧气转炉和电炉炼钢工艺。氧气转炉采用高炉铁水为原料进行吹炼获得合格钢水,生产单元多,规模庞大,生产周期长。氧气转炉采用的高炉铁水含碳量高(通常为2.5
‑
4.3%),含有较多的硅、锰、磷、硫等杂质,不仅仅需要造渣熔剂,还需要高纯度氧气吹炼,铁水转运亦会损失热量。电炉炼钢主要采用回收再利用的废钢,在电炉中利用电能作为热源进行冶炼获得合格钢水的工艺,工艺流程简单,生产环节和周期少。由于需要熔化废钢,需要耗费大量的电能,两者均需建设独立的炼钢设备,投入资金巨大。
4.针对传统高炉炼铁流程高污染、高能耗问题,熔融还原炼铁技术因可降低对造块、烧结、炼焦等高污染、高耗能工序的依赖,近年来得以发展,成为钢铁工业实现节能减排和清洁生产的重要技术途径,如corex、finex和hismelt等工艺。corex法采用上部预还原竖炉进行铁矿预还原,得到金属化率为70%
‑
90%的金属化球团(dri),然后将dri送入下部熔化气化炉进行终还原。该工艺生产过程中仍需依靠块矿、球团矿、烧结矿和部分焦炭来维持炉况顺行。finex工艺以粉矿为原料,采用多级流化态反应器完成铁矿预还原,获得金属化率为90%左右的还原铁粉,还原铁粉和粉煤经热压块后作为炉料加入熔化气化炉进行熔融终还原。hismelt工艺以粉矿为主要原料,采用旋风熔化炉对粉矿进行闪速熔炼,粉矿、熔剂、煤粉以氧气为载体沿炉体切线方向喷吹到旋风熔化炉内,粉矿在运动过程中被还原熔化,进而沿着炉壁流淌、滴落到熔融还原炉内进行终还原。
5.上述的工艺显然都是通过不同的装置进行还原炼铁和熔融终还原炼钢,其中的先还原含铁粉料然后压块,之后还原炼钢,显然工艺复杂,装置利用率低。虽然闪速熔炼效率高,但是其中的旋风熔化炉和熔融还原炉也是不同的装置结构,沿炉体切线方向喷吹到旋风熔化炉对喷吹性能的要求非常高,耐火材料侵蚀严重,炉衬寿命短,不能够进行工业大规模生产和推广。
6.而专利cn106086280a、cn102690919a、cn103993115a等公开的闪速炼铁技术,把还原、熔化、造渣等过程集于一体,具有设备简化,易于生产的大规模生产的优点,但产物铁水的碳含量高(>2.0%),si、mn、p、s等杂质无法有效去除,不能直接生产粗钢。其他的专利cn101906501a、cn108374067a提出用粉矿和煤氧直接炼钢的工艺,铁矿粉经预还原后,与煤粉、氧气喷入炼钢炉内进行炼钢。特别是cn108374067a中的飞速还原直接炼钢的装置包括铁矿粉预处理系统、飞速还原炉系统和炼钢炉系统,显然也是通过不同的装置进行还原炼
铁和熔融终还原炼钢。
7.综上所述,现阶段熔融还原炼铁/直接炼钢方法可在一定程度上解决钢铁生产流程长、能耗高、污染严重的问题,然而上述工艺依然采用传统的还原炼铁和氧化炼钢二步过程;还原工序和氧化工序在不同设备或容器中实施,存在设备投资大、连接设备故障多的弊端。
技术实现要素:
8.本发明解决的技术问题是传统高炉炼铁和转炉炼钢能耗大,环境污染严重,需要两步进行;虽然有熔融还原炼铁技术,但是其是通过不同的装置进行还原炼铁和氧化炼钢,生产流程长,能耗高,污染严重,不同设备占地面积大,协同率低。
9.为解决上述技术问题,本发明提供如下技术方案:
10.一种含铁粉料在还原性气氛中直接炼钢装置,所述装置包括炼钢池、造气塔、快速还原区、矿料投放区和控制系统;
11.其中:所述炼钢池设置在所述装置最底部,所述炼钢池包括造渣熔剂堆,所述炼钢池底部设置有钢水层,所述钢水层上设置有液态渣层;
12.所述炼钢池的上方设置有快速还原区;
13.所述快速还原区下部的旁侧设置有造气塔,所述快速还原区的上方设置有矿料投放区;
14.所述矿料投放区顶部的中央部位设有尾气排放口,所述尾气排放口的外侧沿圆周设置有若干造渣熔剂投放口,所述矿料投放区的侧面均匀设置有若干冷气口和若干矿粉投放口,所述矿料投放区的内部设有造渣熔剂仓和造渣熔剂投放机构;
15.所述控制系统设置在炼钢池、造气塔、快速还原区或矿料投放区的旁侧,通过传感器和控制部件与所述装置电连接。
16.优选地,所述炼钢池为圆筒或多边形棱柱筒,所述炼钢池的上部和所述快速还原区直接连接,所述炼钢池的钢水层靠近底部的一侧开设有出钢口,所述液态渣层的靠近所述钢水层的另一侧开设有出渣口。
17.优选地,所述造渣熔剂堆为圆弧锥形的固态造渣熔剂料堆;所述固态造渣熔剂料堆为圆锥堆状,由包括粒径为5
‑
50mm的粒状或块状石灰石、生石灰、兰炭、萤石、白云石和块煤的一种或几种混合后自然下落而成;所述固态造渣熔剂料堆穿过液态渣层,底部悬浮在钢水层中。
18.优选地,所述造气塔内置造气枪和还原气流道,呈圆锥台或棱锥台;所述造气枪外部连接有氧气供应装置和造气原料供应装置,所述造气枪口火焰高温达1800
‑
2400℃,所述造气枪向内喷射造气原料燃烧的火焰,通过不完全燃烧产生高温还原气,直接喷射到造渣熔剂堆的侧面;所述造气塔的还原气流道出口与快速还原区下部连接。
19.优选地,所述造气原料供应装置供应造气原料,造气原料为包含但不限于粉煤、天然气、氢气、生物质燃料等。
20.优选地,所述造气枪产生的还原气,含有一定比例的co,h2,少量的h2o,co2和n2。
21.优选地,快速还原区域的主要反应为:
22.[feo] h2(g)=[fe] h2o(g)
[0023]
[feo] co(g)=[fe] co2(g)
[0024]
造渣熔剂堆区域主要反应为:
[0025]
(sio2) 2(cao)=(2cao
·
sio2)
[0026]
[fes] (cao)=(cas) [feo]
[0027]
(p2o5) 4(cao)=(4cao
·
p2o5)。
[0028]
优选地,所述还原气流道为喇叭口状,与水平面向下倾斜角为30
°‑
60
°
;与向心轴线倾角在北半球为右倾1
°‑
16
°
,在南半球为左倾1
°‑
16
°
。
[0029]
优选地,所述快速还原区为含铁粉料还原的区域,结构为中间细、上下两端粗的变截面的圆筒状或多边形筒状;所述快速还原区下部沿圆周设置有至少3个造气塔。
[0030]
优选地,所述矿料投放区为下大上小的锥台型,所述矿料投放区的顶部中央部位开设有尾气排放口;所述尾气排放口外侧沿圆周设置有至少1个造渣熔剂投放口;所述矿料投放区的外侧均匀设置有至少2个矿粉投放口,所述矿料投放区的外侧均匀设置有至少2个冷气口,所述矿料投放区的内部设置有造渣熔剂存储仓和造渣熔剂投放机构。
[0031]
优选地,所述控制系统由硬件系统和控制软件组成,通过传感器和控制部件与所述装置电连接。
[0032]
优选地,所述控制系统与所述造气塔、所述冷气口、所述矿粉投放口、所述造渣熔剂投放口和所述造渣熔剂投放机构电连接。
[0033]
一种含铁粉料在还原性气氛中直接炼钢装置的使用方法,所述使用方法包括如下步骤:
[0034]
步骤一、通过控制系统打开造渣熔剂投放口,将造渣熔剂材料混合后装入造渣熔剂存储仓,造渣熔剂材料从造渣熔剂存储仓进入炼钢池,在底部形成1
‑
3m高的造渣熔剂堆;
[0035]
步骤二、把平均粒径小于0.1mm的造气原料干燥到水分≤1wt.%后装入造气原料供应装置;
[0036]
步骤三、通过造气枪的点火装置启动造气枪,调节氧气供应装置和造气原料供应装置使所造气体成分中co h2>90%,温度>1800℃;
[0037]
步骤四、把含铁粉料干燥到水分≤1wt.%后启动矿粉投放口投放,所述含铁粉料的粒径<1mm,平均粒径为0.074mm,全铁tfe含量为50
‑
70wt.%;
[0038]
步骤五、含铁粉料在所述装置下落中,在快速还原区与上升的造气枪产生的还原性气体发生传热和传质反应,之后落入炼钢池中的造渣熔剂堆表面,含铁粉料在快速还原区未还原的部分在造渣熔剂堆表面与造气枪产生的还原性气体进一步还原;
[0039]
步骤六、铁水与还原气完成终还原,与造渣熔剂堆完成脱杂质反应,生成终渣,进而渣钢分离;
[0040]
步骤七、钢水和渣液定期从出钢口和出渣口排出,产生的废气通过尾气排放口及时排出。
[0041]
优选地,所述步骤一的造渣熔剂堆表面为内凹弧面,软熔的钢渣混合物在重力作用下自堆顶沿弧面向堆底缓慢流动,与高温还原气逆向对流,进行热质交换;钢渣混和物向下流动时,与造渣熔剂堆表面的造渣熔剂反应,脱除钢液中的硫、磷等杂质,生成高碱度终渣。
[0042]
优选地,所述步骤七中的钢水为c:<0.5wt.%,s:<0.02wt.%,p:<0.02wt.%的粗
钢;所述渣液的二元碱度为1.3
‑
2.0。
[0043]
本发明实施例提供的上述技术方案,至少具有如下有益效果:
[0044]
上述方案中,含铁粉料在还原性气氛中直接炼钢,摒弃了传统高炉的炼焦、烧结、球团的工艺流程和转炉炼钢的方法,直接采用含铁粉料为原料,在快速还原区中与还原气发生还原反应,少量未还原铁氧化物在造渣熔剂堆完成终还原,同时完成脱硫、脱磷等脱杂质反应,从而在一个装置内能够直接高效生产粗钢,不再依赖焦炭资源,降低了高耗能的工序;不需要大量的炼钢装置,工厂占地少,节省大量资金投入。
[0045]
含铁粉料在还原性气氛中直接炼钢,造气原料需要通过造气枪喷射高温还原气,该高温还原气先直接作用于造渣熔剂堆和沿造渣熔剂堆向下流动的钢渣混合物,为钢渣混合物和造渣熔剂堆提供热量,有利于提高钢渣混合物的温度,有利于石灰的熔化,缩短滞止期,加速造渣的进程,热量少损失;然后高温还原气通过快速还原区上升,在快速还原区与下落的含铁粉料发生逆流相遇,同时进行传热和传质反应,接触反应充分,反应效率高。
[0046]
含铁粉料在还原性气氛中直接炼钢,在炉体底部设置有炼钢池,经过还原反应后下落的铁及铁矿软熔物均一起落在造渣熔剂堆的表面,含铁粉料在快速还原区未还原的部分能够与高温还原气进一步还原,完成终还原的钢渣混合料,与造渣熔剂完成脱磷、脱硫等脱杂质反应,生成终渣,进而渣钢分离,实现在一个装置中就能够直接炼钢,不需要炼钢设备的大量单独投入,极大地节省了资金和场地面积。
[0047]
故而本发明基于在快速还原区和造渣熔剂堆的含铁粉料一体化还原和造渣,对直接炼钢设备结构和工艺进行独有的设计,创造出装置内利于传热和传质的流场和温度场,从而在还原性气氛下,基于装置内造渣熔剂堆,达成一体化直接炼钢的目的。
[0048]
总之,本发明的冶炼过程是围绕在炼钢池内的造渣熔剂堆开展,整个冶炼过程造渣熔剂是充足的、过量的;需要脱除的硫、磷等杂质和酸性氧化物在过量的造渣熔剂(碱性氧化物)堆表面完成各类化学反应,生成低熔点终渣,排炼钢池。
附图说明
[0049]
为了更清楚地说明本发明实施例中的技术方案,下面将对实施例描述中所需要使用的附图作简单地介绍,显而易见地,下面描述中的附图仅仅是本发明的一些实施例,对于本领域普通技术人员来讲,在不付出创造性劳动的前提下,还可以根据这些附图获得其他的附图。
[0050]
图1为本发明的含铁粉料在还原性气氛中直接炼钢装置的结构示意图。
[0051]
附图标记说明如下:
[0052]
1、炼钢池;11、造渣熔剂堆;12、钢水层;121、出钢口;13、液态渣层;131、出渣口;
[0053]
2、造气塔;21、造气枪;22、还原气流道;
[0054]
3、快速还原区;
[0055]
4、矿料投放区;41、冷气口;42、矿粉投放口;43、造渣熔剂存储仓;44、造渣熔剂投放口;45、尾气排放口;46、造渣熔剂投放机构;
[0056]
5、控制系统。
具体实施方式
[0057]
为使本发明要解决的技术问题、技术方案和优点更加清楚,下面将结合附图及具体实施例进行详细描述。
[0058]
如图1所示,本发明实施例提供一种含铁粉料在还原性气氛中直接炼钢装置,所述装置包括炼钢池1、造气塔2、快速还原区3、矿料投放区4和控制系统5,所述炼钢池1设置在所述装置的最底部,所述炼钢池1包括中心设置的造渣熔剂堆11,所述造渣熔剂堆11底部设置有钢水层12,所述钢水层12的上层设置有液态渣层13,所述造渣熔剂堆11的上方设置有快速还原区3,所述快速还原区3下部的旁侧设置有造气塔2,所述快速还原区3的上方设置有矿料投放区4,所述控制系统5通过电连接控制分布在不同部位的测控单元。
[0059]
所述炼钢池1为圆筒或多边形棱柱筒,所述炼钢池1的上部和所述快速还原区3直接连接,所述炼钢池1的钢水层12靠近底部的一侧开设有至少1个出钢口121,所述液态渣层13的靠近所述钢水层121的另一侧开设有至少1个出渣口131。
[0060]
所述造渣熔剂堆11为圆弧锥形的固态造渣熔剂料堆;所述固态造渣熔剂料堆为1
‑
3m高的圆锥堆状,由包括粒径为5
‑
50mm的粒状或块状石灰石、生石灰、兰炭、萤石、白云石和块煤的一种或几种混合后自然下落而成。固态造渣熔剂料堆优选粒径为20mm的粒状石灰石,优选粒径为30mm的块状生石灰,优选粒径为15mm的粒状兰炭,优选粒径为40mm的块状兰炭、萤石、白云石和块煤,优选粒径为33mm的粒状石灰石、生石灰、兰炭和萤石;圆锥堆状锥堆的高度优选为1.5m、2.5m、1m、3m。
[0061]
所述造气塔2内置造气枪21和还原气流道22,呈圆锥台;所述造气枪21外部连接有氧气供应装置和造气原料供应装置;所述造气枪21枪口火焰高温达1800
‑
2400℃,优选为1800℃、2000℃、2200℃、2400℃;所述造气枪21向内喷射造气原料燃烧的火焰,通过不完全燃烧产生高温还原气,直接喷射到造渣熔剂堆11的侧面;所述造气塔2的还原气流道22出口与快速还原区3下部连接。
[0062]
所述造气原料供应装置供应造气原料,造气原料为包含但不限于粉煤、天然气、氢气、生物质燃料等。
[0063]
所述造气枪21产生的还原气,含有一定比例的co,h2,少量的h2o,co2和n2。
[0064]
所述还原气流道22为喇叭口状,与水平面向下倾斜角为30
°‑
60
°
,优选为45
°
、40
°
、50
°
、30
°
、60
°
;与向心轴线倾角在北半球为右倾1
°‑
16
°
,在南半球为左倾1
°‑
16
°
,优选为8
°
、11
°
、5
°
。
[0065]
所述快速还原区3为含铁粉料还原的区域,结构为中间细、上下两端粗的变截面的圆筒状,变截面的形状用于控制流场按设定参数运行;所述快速还原区3下部沿圆周均匀设置3
‑
36个造气塔。
[0066]
所述矿料投放区4为下大上小的锥台型,所述矿料投放区4的顶部中央部位开设有尾气排放口45;所述尾气排放口外侧沿圆周设置有1
‑
3个造渣熔剂投放口44,所述矿料投放区4的外侧均匀设置有2
‑
16个矿粉投放口42,所述矿料投放区4的外侧均匀设置有2
‑
18个冷气口41,用于通入冷却气体,控制尾气温度在设定范围,所述矿料投放区4的内部设置有造渣熔剂存储仓43和造渣熔剂投放机构46。
[0067]
所述控制系统5由硬件系统和控制软件组成,通过传感器和控制部件与所述装置电连接。
[0068]
本发明实施例提供一种含铁粉料在还原性气氛中直接炼钢装置的使用方法,所述使用方法包括如下步骤:
[0069]
步骤一、通过控制系统5打开造渣熔剂投放口44,将造渣熔剂材料混合后装入造渣熔剂存储仓43,并控制造渣熔剂投放机构46使造渣熔剂材料从造渣熔剂存储仓43进入炼钢池1,在底部形成造渣熔剂堆11;
[0070]
步骤二、把平均粒径小于0.1mm的造气原料干燥到水分≤1wt.%后装入造气原料供应装置;
[0071]
步骤三、通过造气枪21的点火装置启动造气枪21,调节氧气供应装置和造气原料供应装置使所造气体成分中co h2>90%,温度>1800℃;
[0072]
步骤四、把含铁粉料干燥到水分≤1wt.%后启动矿粉投放口42投放,所述含铁粉料的粒径<1mm,平均粒径为0.074mm,全铁tfe含量为50
‑
70wt.%;
[0073]
步骤五、含铁粉料在所述装置下落中,在快速还原区3与上升的造气枪21产生的还原性气体发生传热和传质反应,之后落入炼钢池1中的造渣熔剂堆11表面,含铁粉料在快速还原区3未还原的部分在造渣熔剂堆11表面与造气枪21产生的还原性气体进一步还原;
[0074]
步骤六、完成终还原的钢渣混合料,与造渣熔剂堆11完成脱杂质反应,生成终渣,进而渣钢分离;
[0075]
步骤七、钢水和渣液定期从出钢口121和出渣口131排出,产生的尾气通过尾气排放口45及时排出,尾气温度通过冷气口41通入冷气进行调节。
[0076]
所述步骤一的造渣熔剂堆11表面为内凹弧面,软熔的钢渣混合物在重力作用下自堆顶沿弧面向堆底缓慢流动,与高温还原气逆向对流,进行热质交换;钢渣向下流动时,与造渣熔剂堆11表面的造渣熔剂反应,脱除钢液中的硫、磷等杂质,生成高碱度终渣。
[0077]
所述步骤七中的钢水为c:<0.5wt.%,s:<0.02wt.%,p:<0.02wt.%的粗钢;所述渣液的二元碱度为1.3
‑
2.0。
[0078]
上述方案中,含铁粉料在还原性气氛中直接炼钢,摒弃了传统高炉的炼焦、烧结、球团的工艺流程和闪速熔炼的方法,直接采用含铁粉料为原料,在快速还原区中与还原气发生还原反应,少量未还原铁氧化物在造渣熔剂堆完成终还原,同时完成脱硫、脱磷等脱杂质反应,从而在一个装置内能够直接高效生产粗钢,不再依赖焦炭资源,降低了高耗能的工序;不需要大量的炼钢装置,工厂占地少,节省大量资金投入。
[0079]
含铁粉料在还原性气氛中直接炼钢,造气原料需要通过造气枪喷射高温还原气,该高温还原气先直接作用于造渣熔剂堆,为造渣熔剂堆提供热量,有利于石灰的熔化,缩短滞止期,加速造渣的进程,热量少损失;然后高温还原气通过快速还原区上升,在快速还原区与下落的含铁粉料发生逆流相遇,同时进行传热和传质反应,接触反应充分,反应效率高。
[0080]
含铁粉料在还原性气氛中直接炼钢,在炉体底部设置有炼钢池,经过还原反应后下落的铁及铁矿软熔物均一起落在造渣熔剂堆的表面,含铁粉料在快速还原区未还原的部分能够与高温还原气进一步还原生成铁水,最终所有的铁氧化物与高温还原气则会完成终还原,与造渣熔剂完成脱磷、脱硫等脱杂质反应,生成终渣,进而渣钢分离,实现在一个装置中就能够直接炼钢,不需要炼钢设备的大量单独投入,极大地节省了资金和场地面积。
[0081]
总之,本发明的冶炼过程是围绕在炼钢池内的造渣熔剂堆开展,整个冶炼过程造
渣熔剂是充足的、过量的;需要脱除的硫、磷等杂质和酸性氧化物在过量的造渣熔剂(碱性氧化物)堆表面完成各类化学反应,生成低熔点终渣,排出炼钢池。对直接炼钢设备结构和工艺进行的独有设计,基于在快速还原区和造渣熔剂堆的含铁粉料一体化还原和造渣,创造出装置内利于传热和传质的流场和温度场,从而在还原性气氛下,基于装置内造渣熔剂堆,达成一体化直接炼钢的目的。
[0082]
以上所述是本发明的优选实施方式,应当指出,对于本技术领域的普通技术人员来说,在不脱离本发明所述原理的前提下,还可以做出若干改进和润饰,这些改进和润饰也应视为本发明的保护范围。
再多了解一些
本文用于企业家、创业者技术爱好者查询,结果仅供参考。